
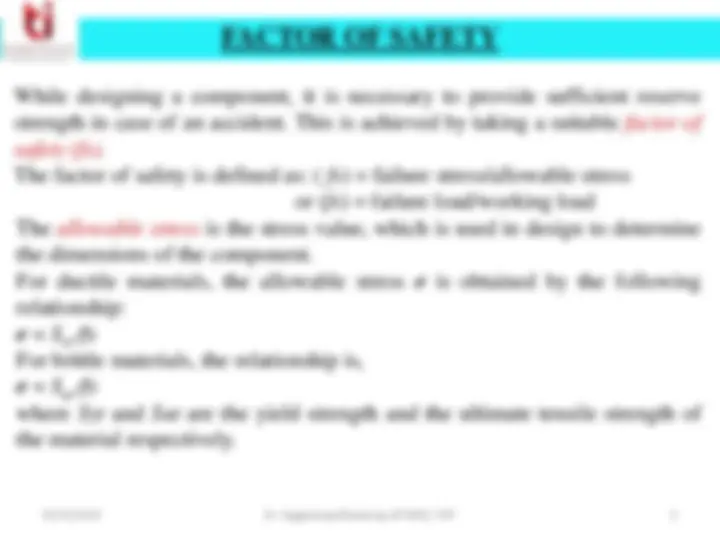
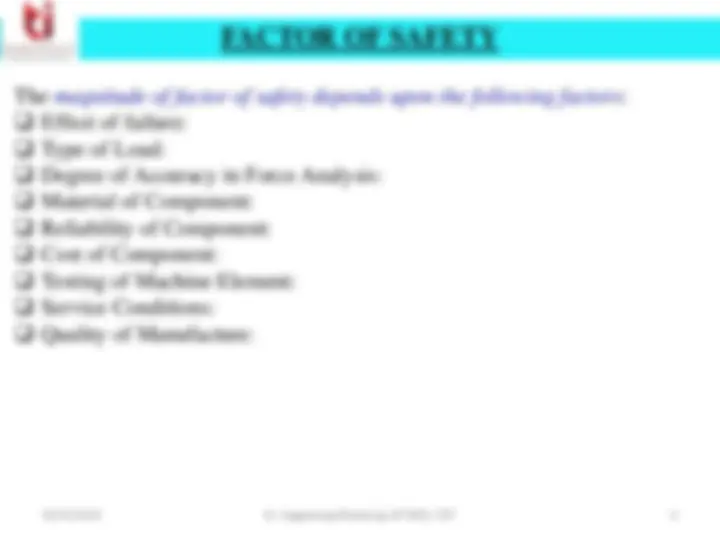
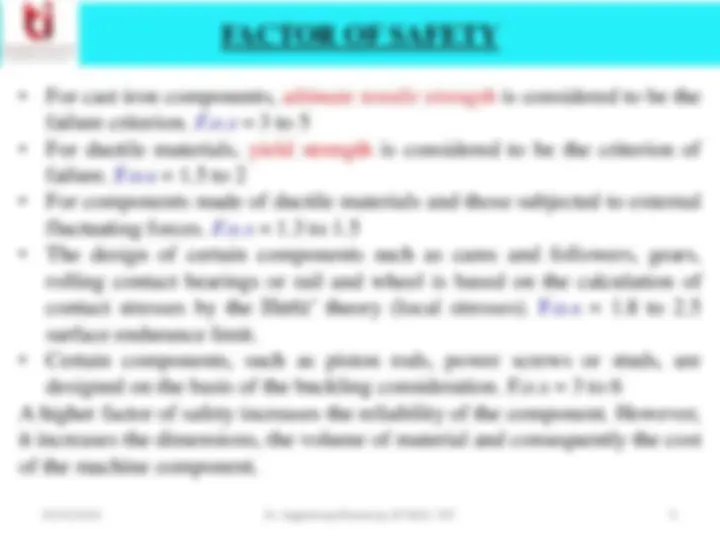
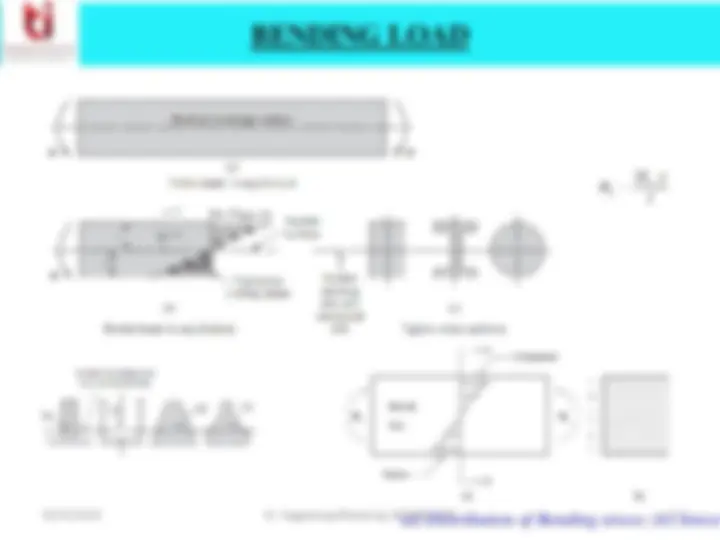
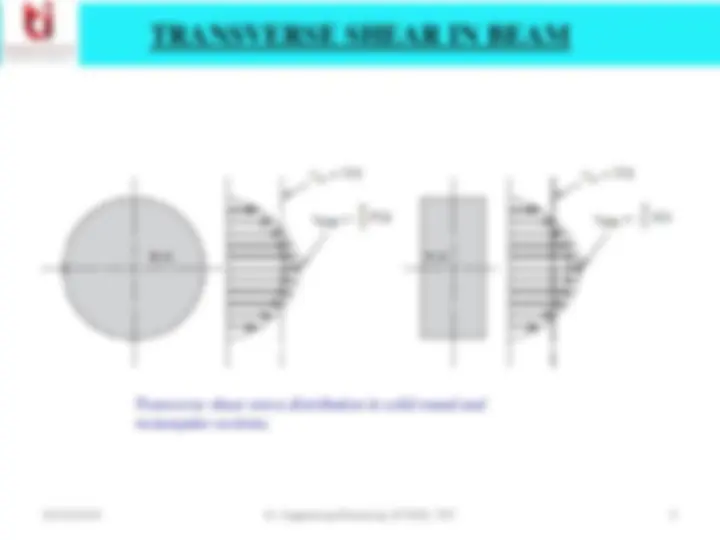
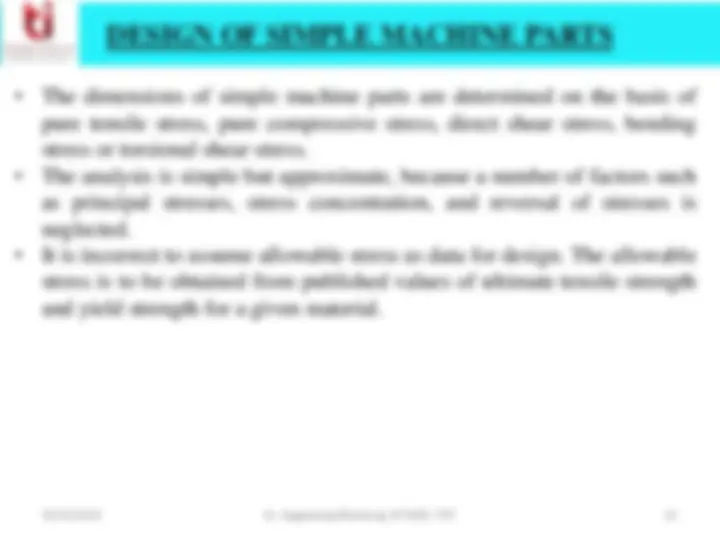
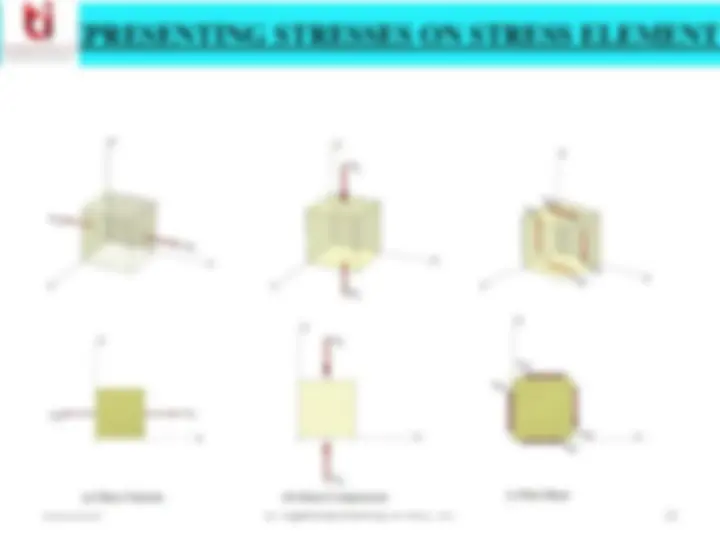
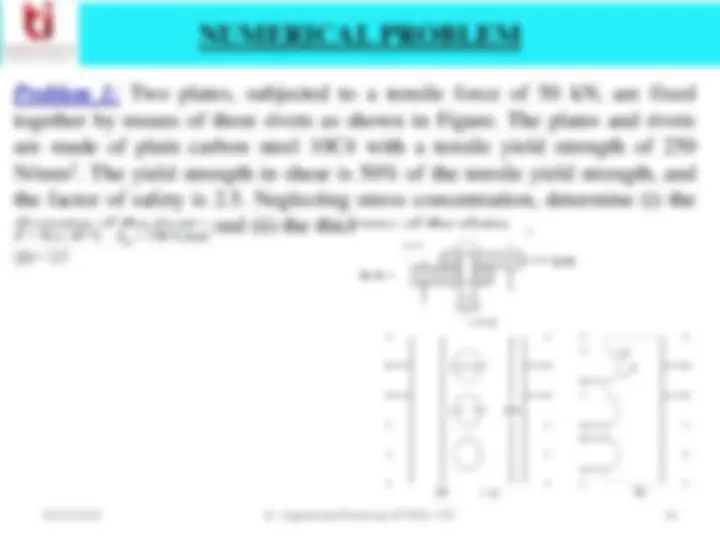
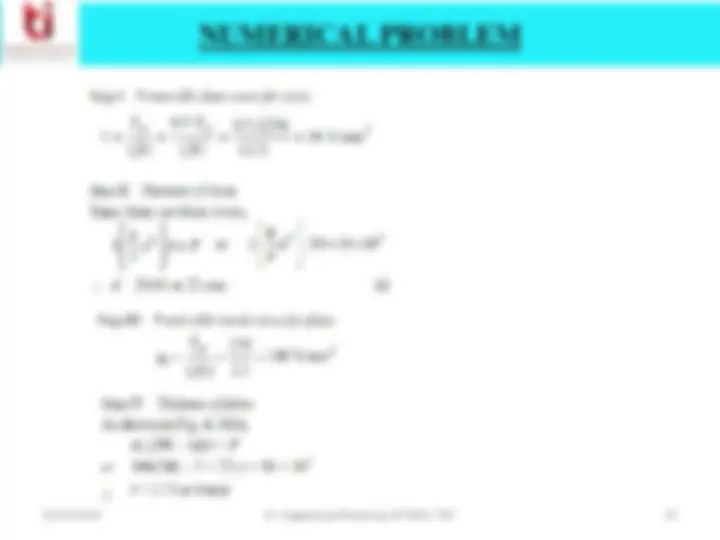
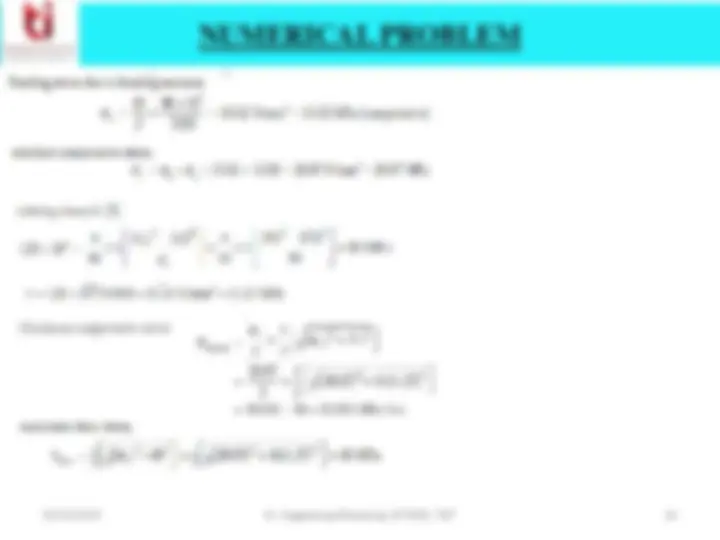
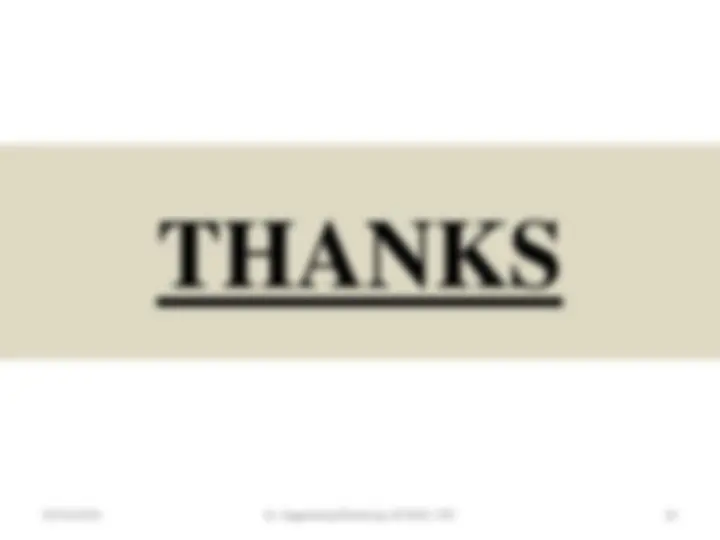
Study with the several resources on Docsity
Earn points by helping other students or get them with a premium plan
Prepare for your exams
Study with the several resources on Docsity
Earn points to download
Earn points by helping other students or get them with a premium plan
Community
Ask the community for help and clear up your study doubts
Discover the best universities in your country according to Docsity users
Free resources
Download our free guides on studying techniques, anxiety management strategies, and thesis advice from Docsity tutors
Basic overview of static loading design
Typology: Lecture notes
1 / 19
This page cannot be seen from the preview
Don't miss anything!
Prepared by: Dr. Gagandeep Bhardwaj, Assistant Professor, MED Email: gagandeep.med@thapar.edu Contact No. 8954388548
05/02/2019 Dr. Gagandeep Bhardwaj, AP MED, TIET 2
A static load is defined as a force, which is gradually applied to a mechanical component and which does not change its magnitude or direction with respect to time.
A mechanical component may fail, that is, may be unable to perform its function satisfactorily, as a result of any one of the following three modes of failure:
The magnitude of factor of safety depends upon the following factors : Effect of failure: Type of Load: Degree of Accuracy in Force Analysis: Material of Component: Reliability of Component: Cost of Component: Testing of Machine Element: Service Conditions: Quality of Manufacture:
05/02/2019 Dr. Gagandeep Bhardwaj, AP MED, TIET 7
Riveted Joint
Shear Deformation
Shear Stress
Elements loaded in pure shear
Shear Strain
Bolted joint, showing three areas of direct shear.
Direct shear loading (showing failure in double shear)
05/02/2019 Dr. Gagandeep Bhardwaj, AP MED, TIET 8
(a) Distribution of Bending stress; (b) Stress
Stresses on an inclined plane:
Principal Plane
Principal Stresses
Plane of max. shear
Max. shear stress Mohr’s^ circle
2-D state of stress
Problem 1: Two plates, subjected to a tensile force of 50 kN, are fixed together by means of three rivets as shown in Figure. The plates and rivets are made of plain carbon steel 10C4 with a tensile yield strength of 250 N/mm^2. The yield strength in shear is 50% of the tensile yield strength, and the factor of safety is 2.5. Neglecting stress concentration, determine (i) the diameter of the rivets; and (ii) the thickness of the plates.
Problem 2: A beam of uniform rectangular cross-section is fixed at one end and carries an electric motor weighing 400 N at a distance of 300 mm from the fixed end. The maximum bending stress in the beam is 40 MPa. Find the width and depth of the beam, if depth is twice that of width.
Solution: W = 400 N; L = 300 mm; σ b = 40 MPa = 40 N/mm^2 ; h = 2 b
Section modulus:
Maximum bending moment (at the fixed end):
Problem 3: A hollow shaft of 40 mm outer diameter and 25 mm inner diameter is subjected to a twisting moment of 120 N-m, simultaneously, it is subjected to an axial thrust of 10 kN and a bending moment of 80 N-m. Calculate the maximum compressive and shear stresses. Solution: do = 40 mm ; di = 25 mm ; T = 120 N-m = 120 × 103 N-mm ; P = 10 kN = 10 × 103 N ; M = 80 N-m = 80 × 103 N-mm We know that cross-sectional area of the shaft,