
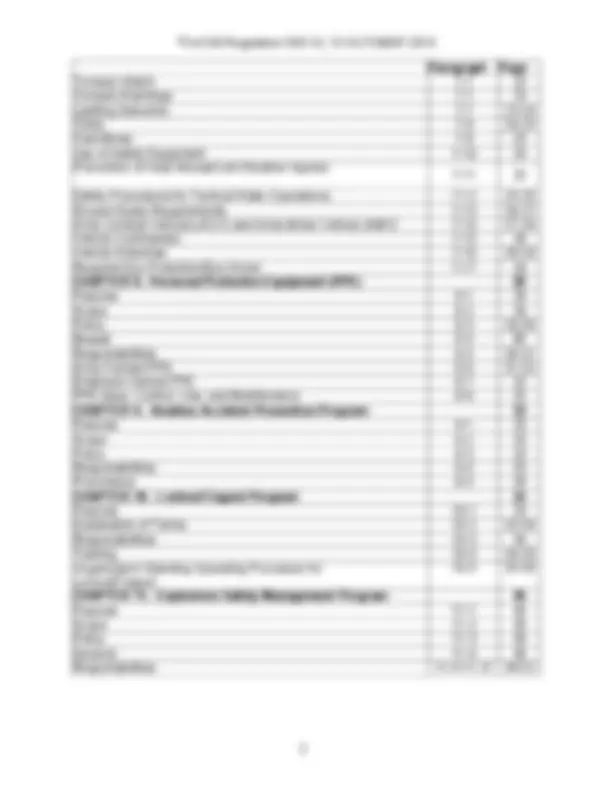
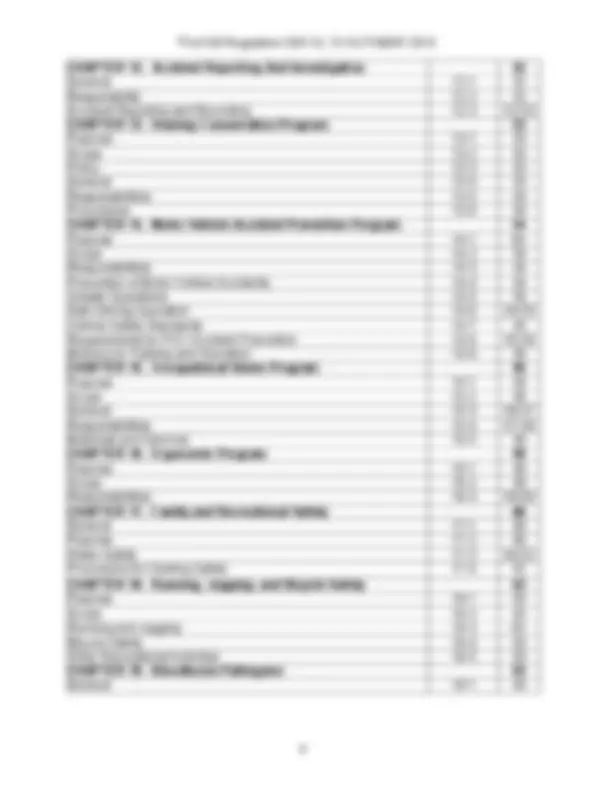
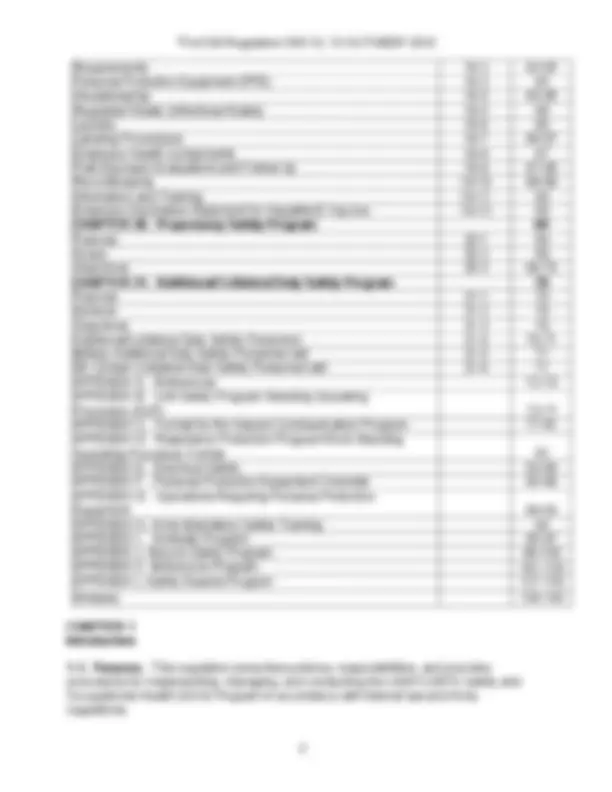
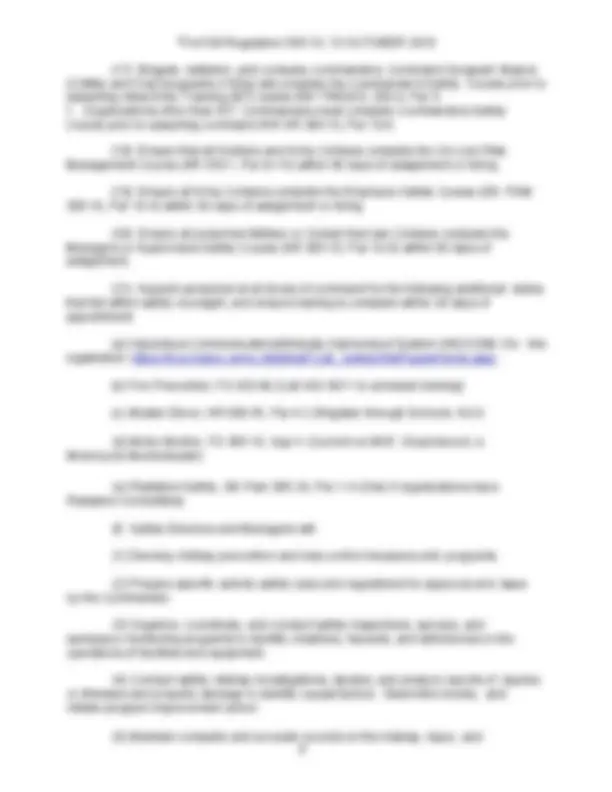
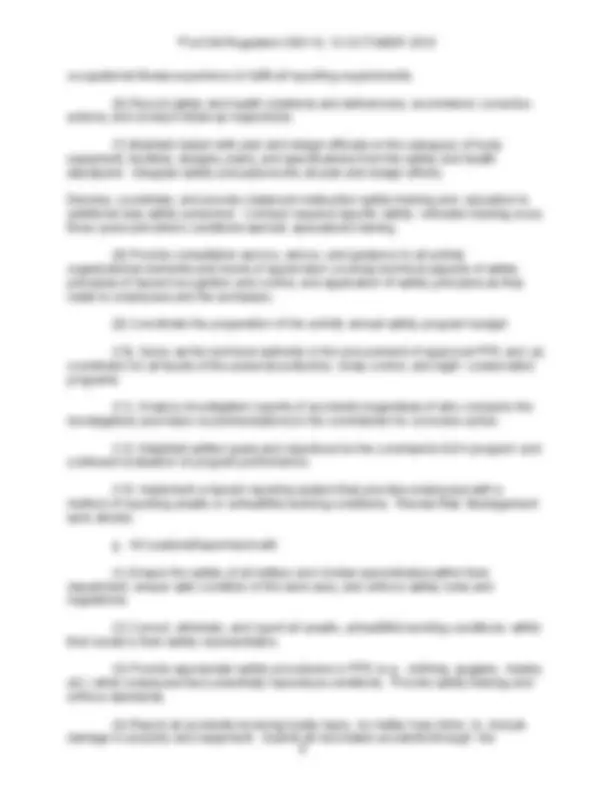
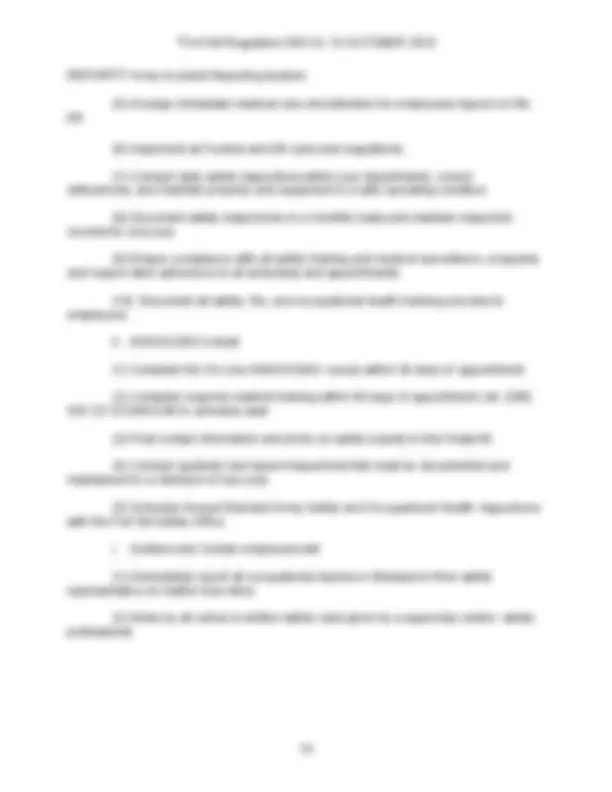
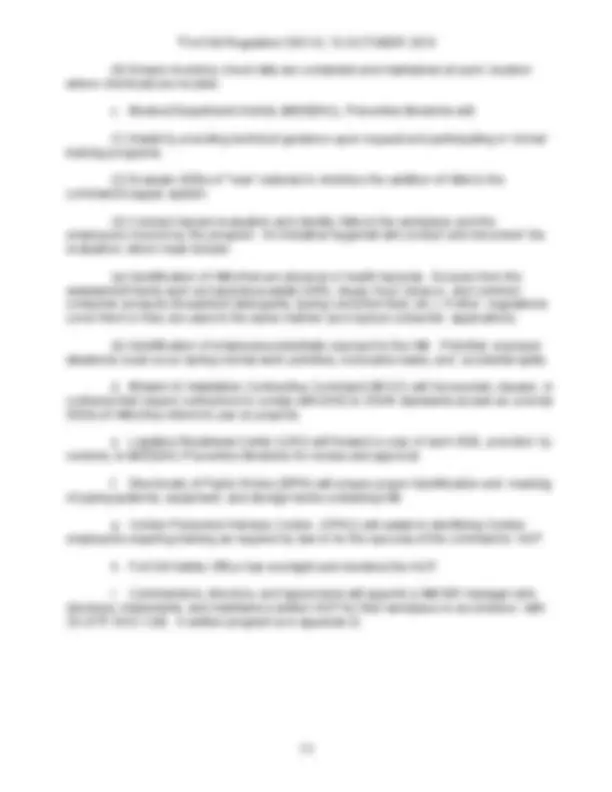
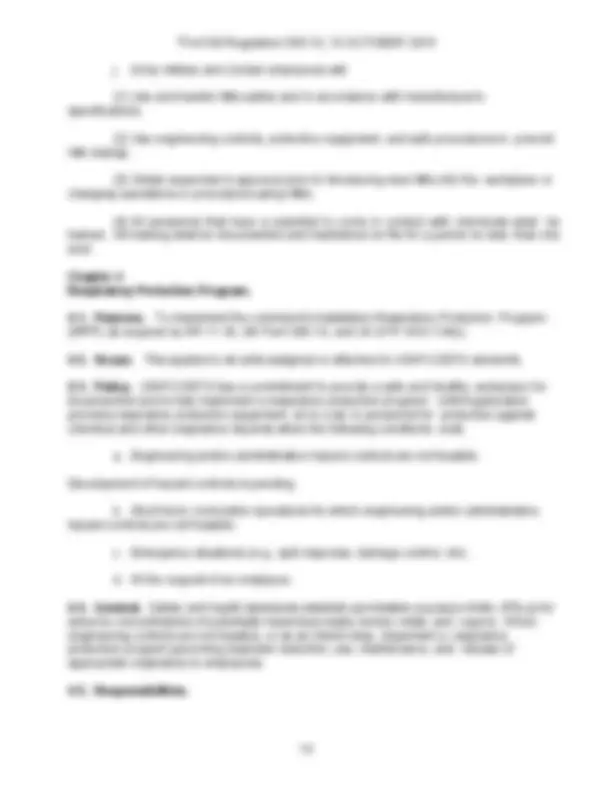
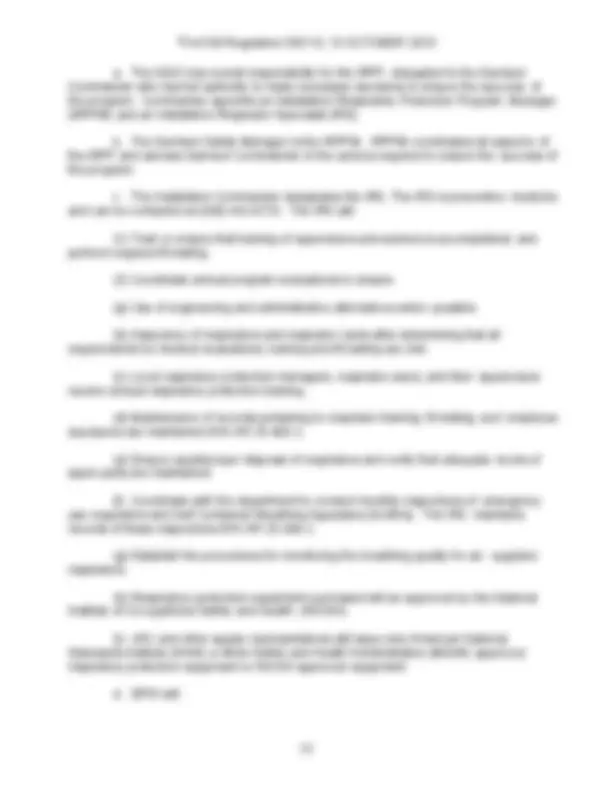
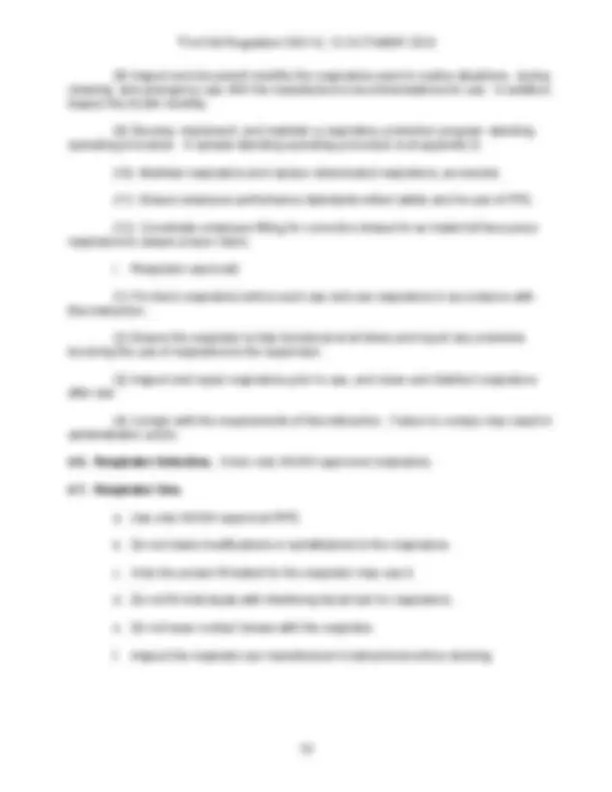
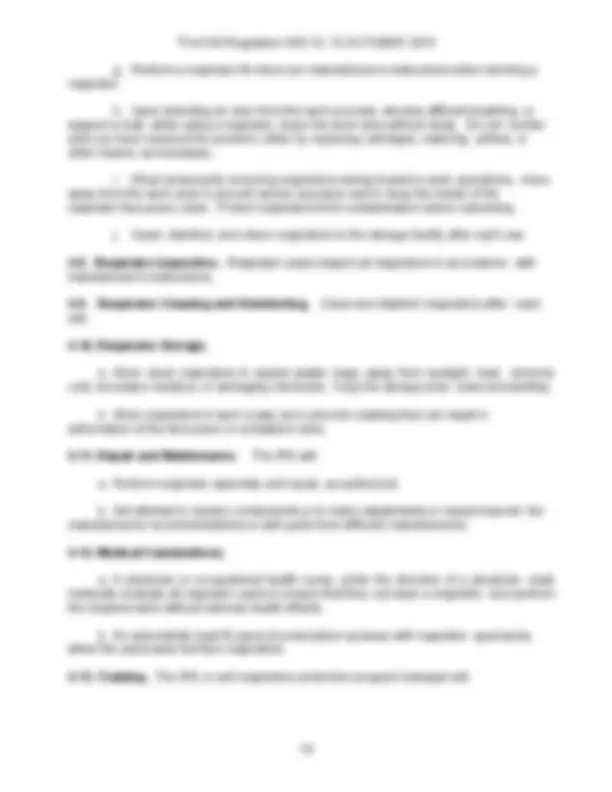
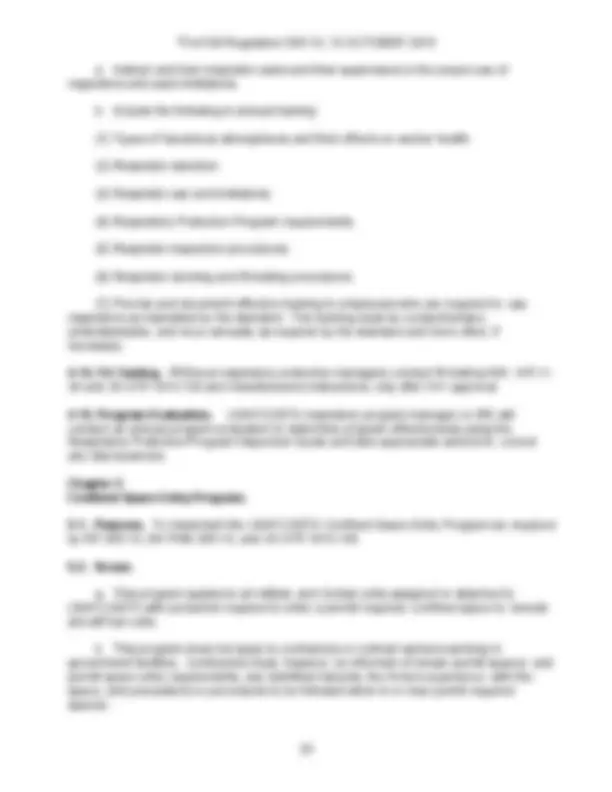

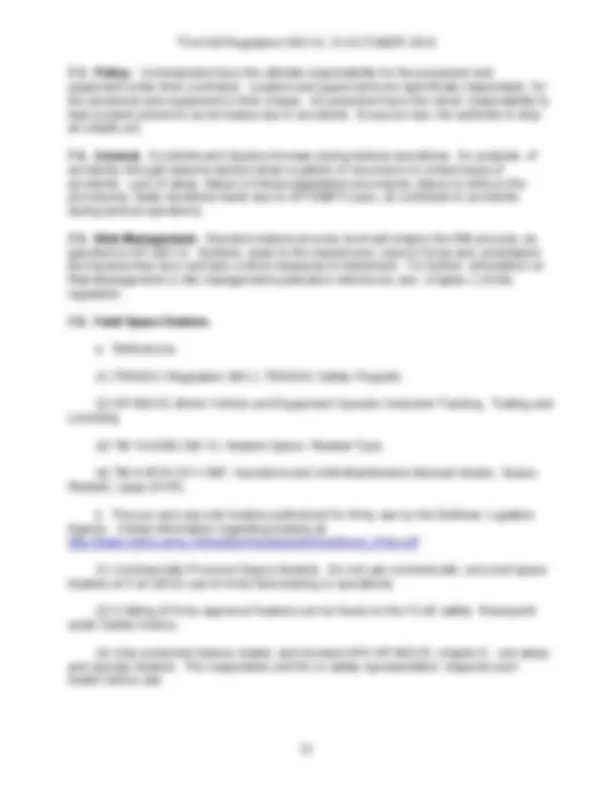
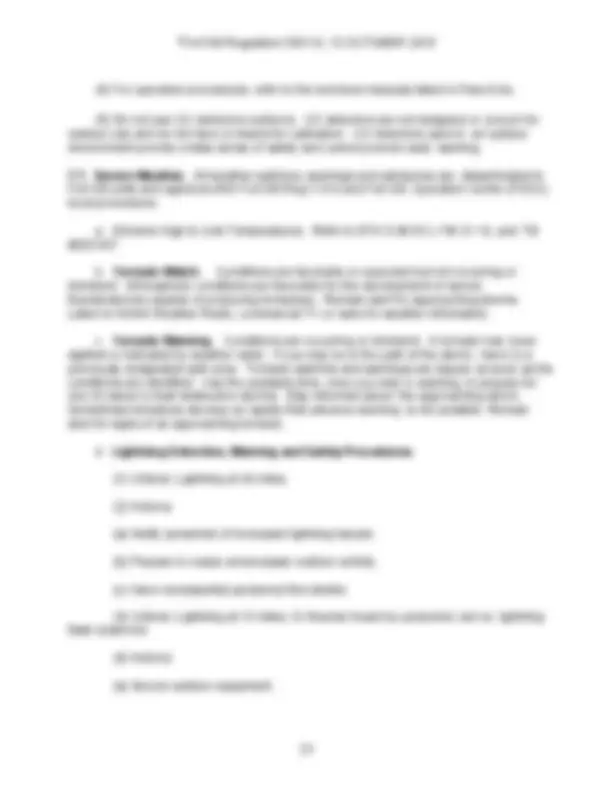
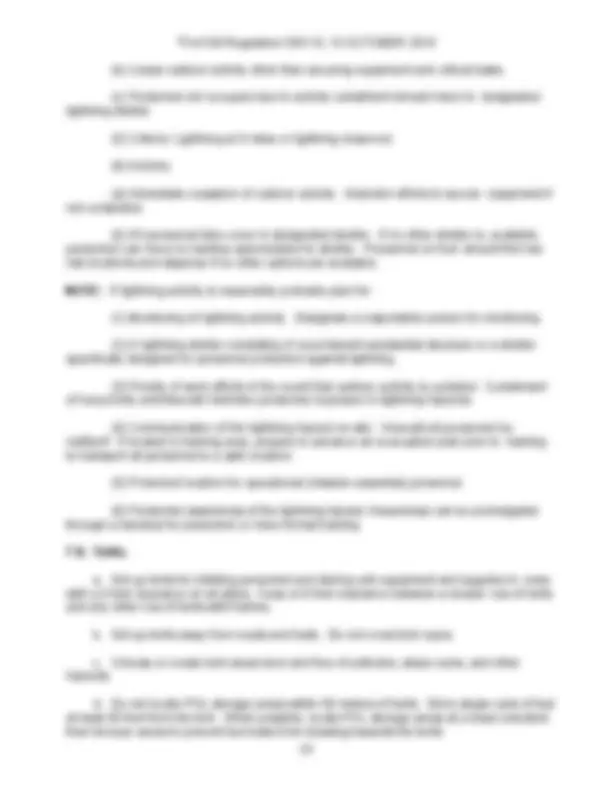
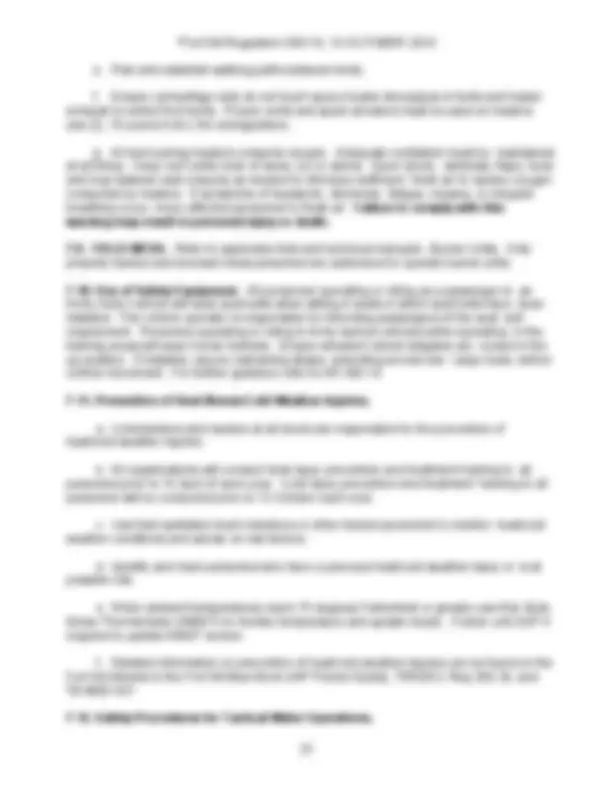
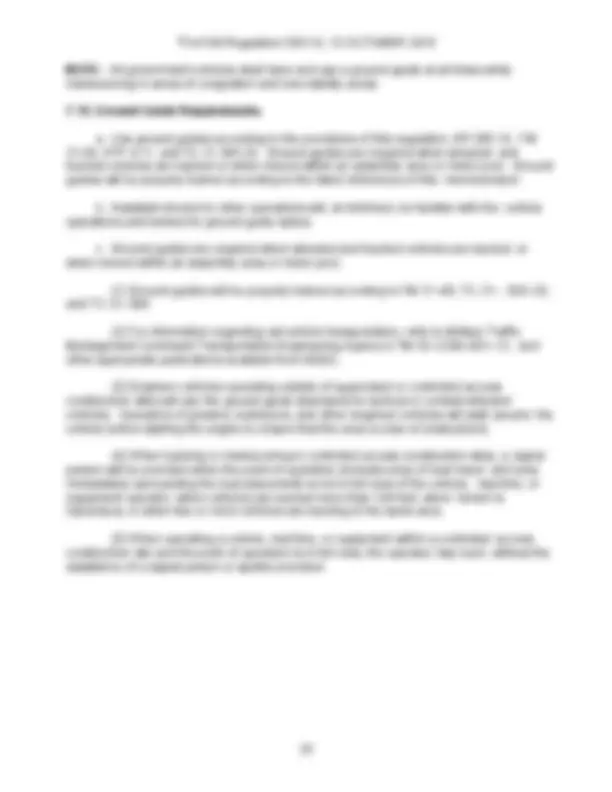
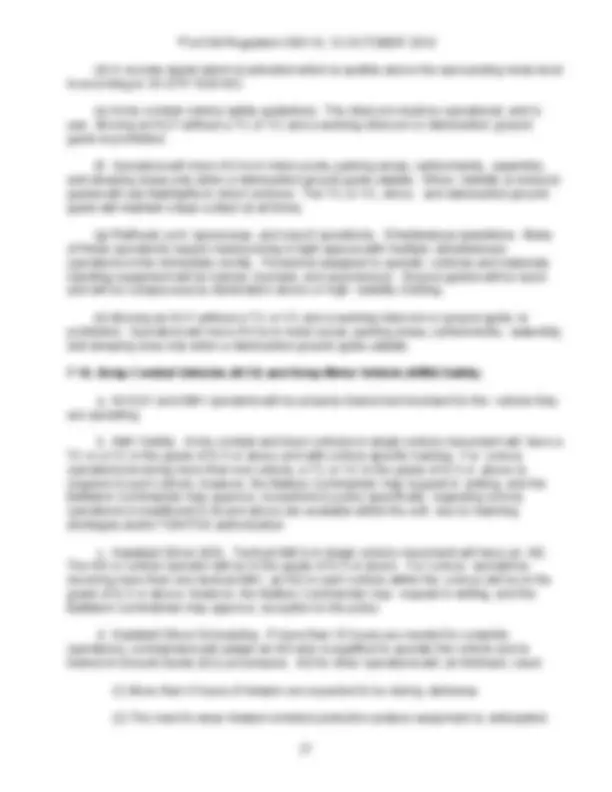
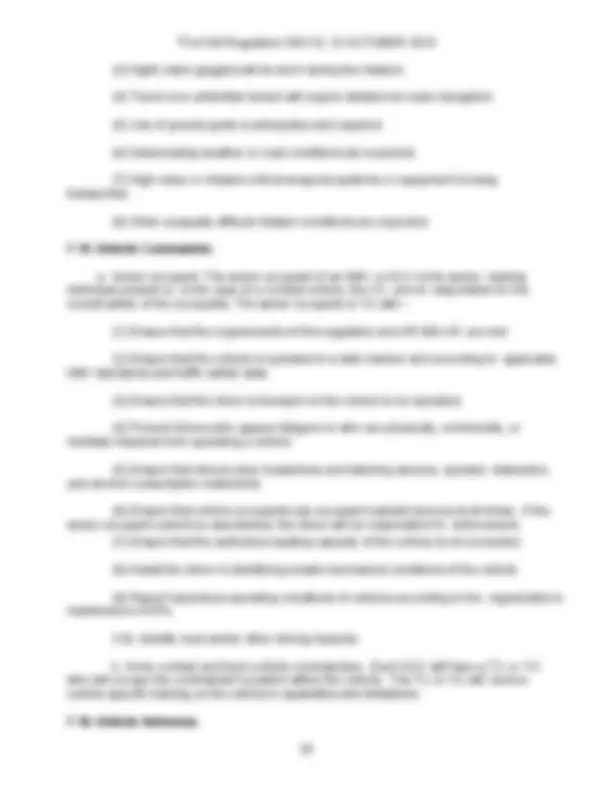
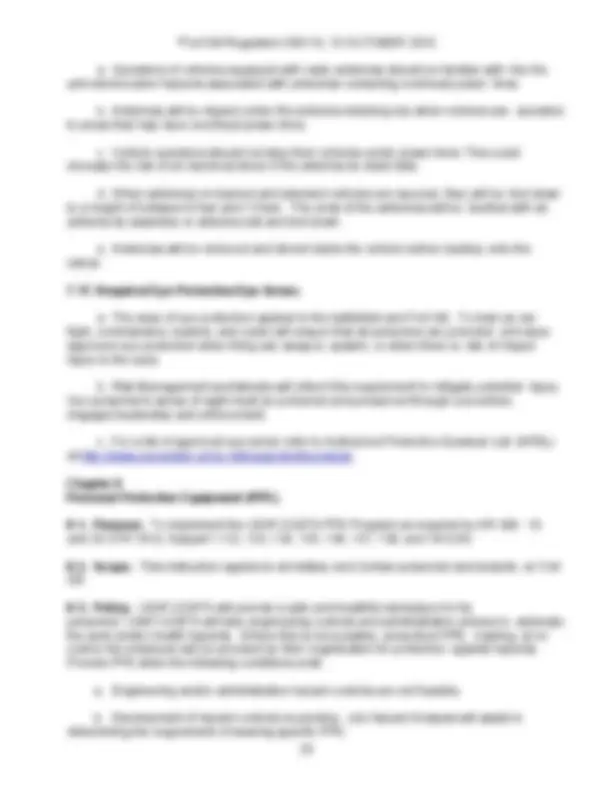
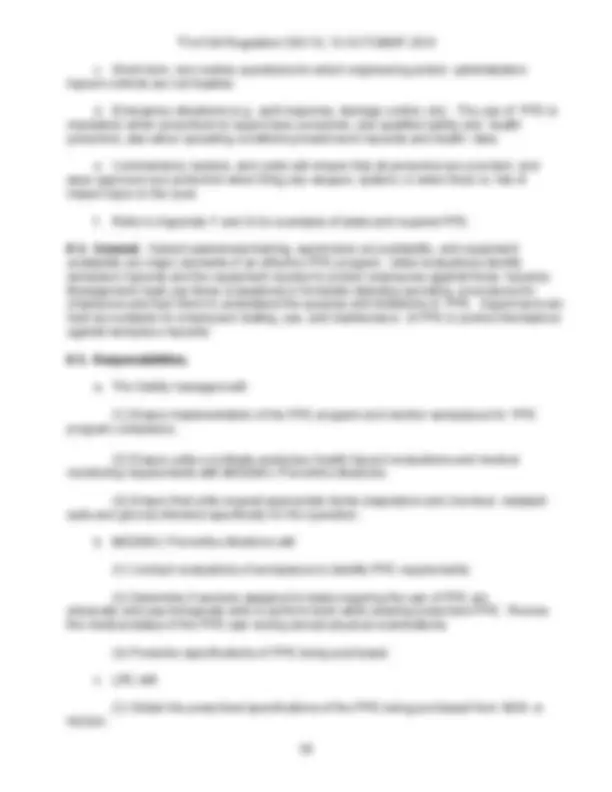
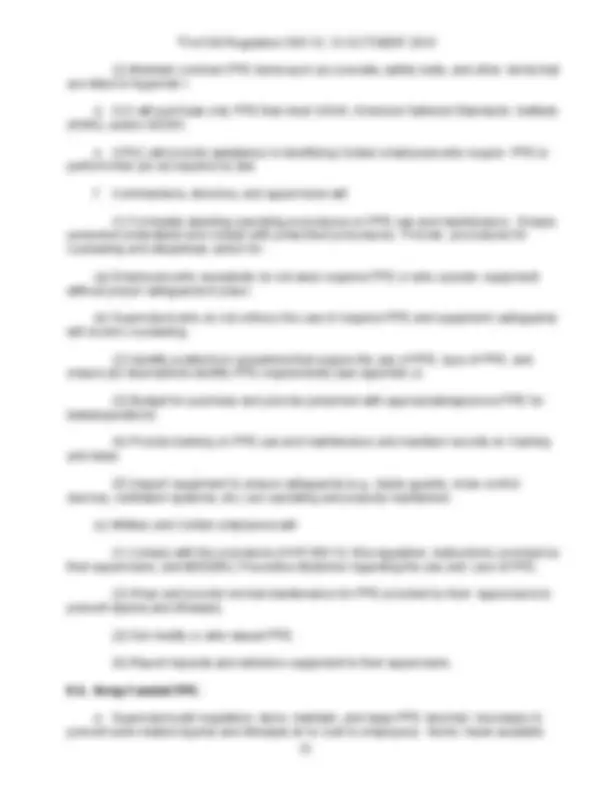
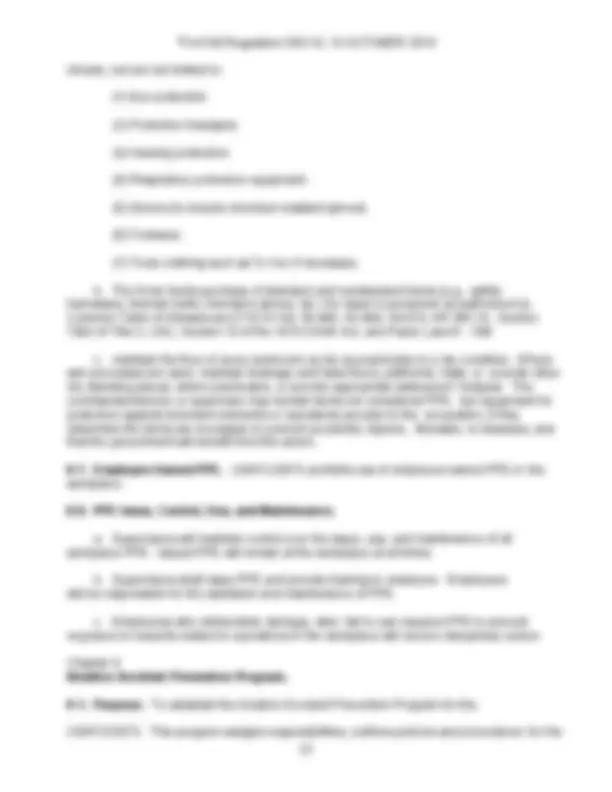
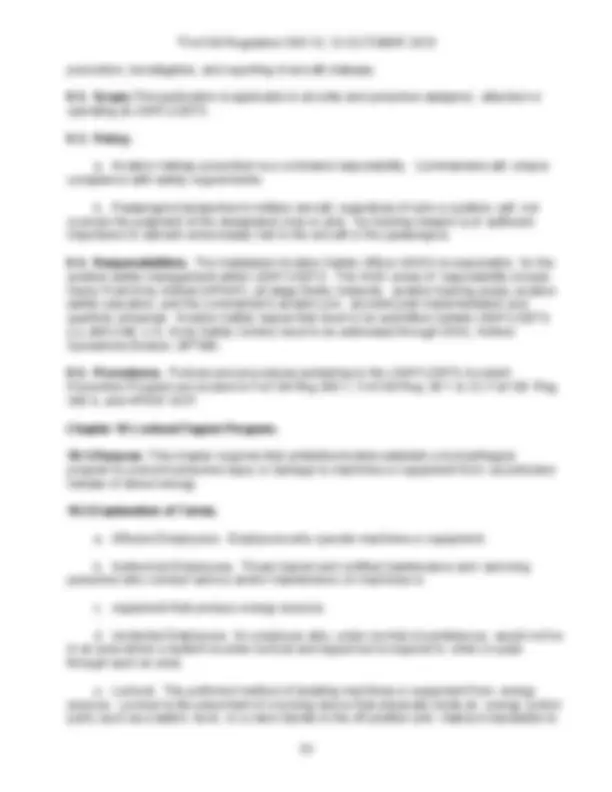
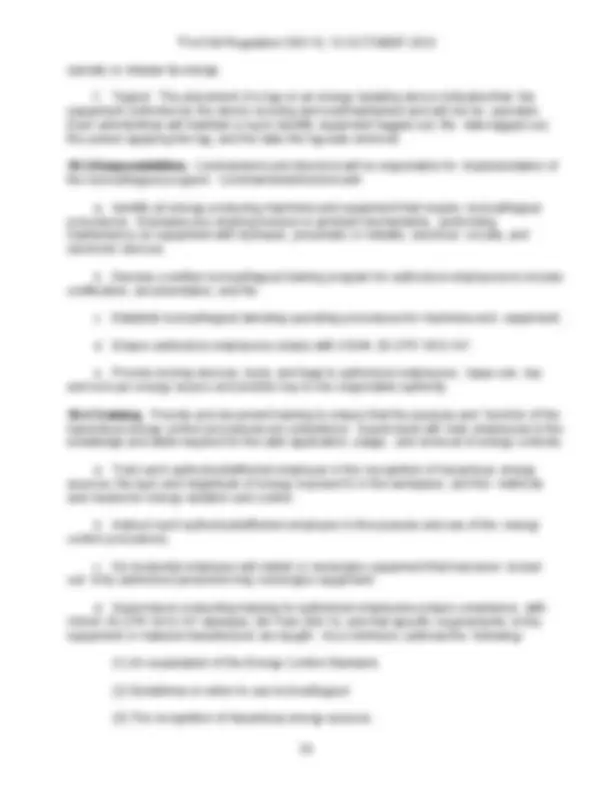
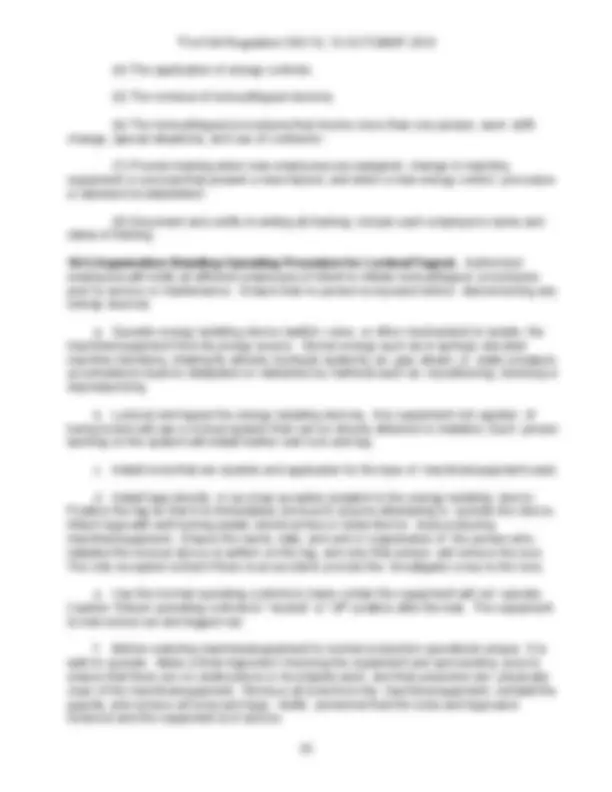
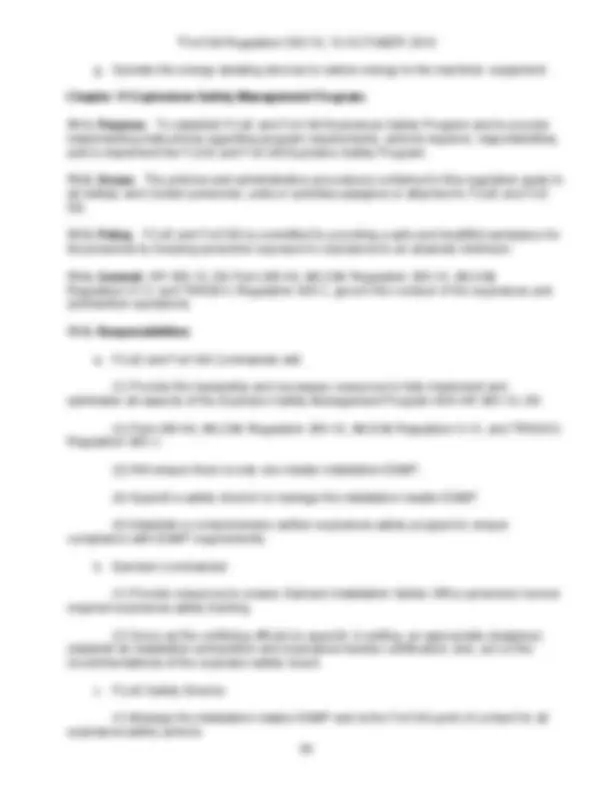
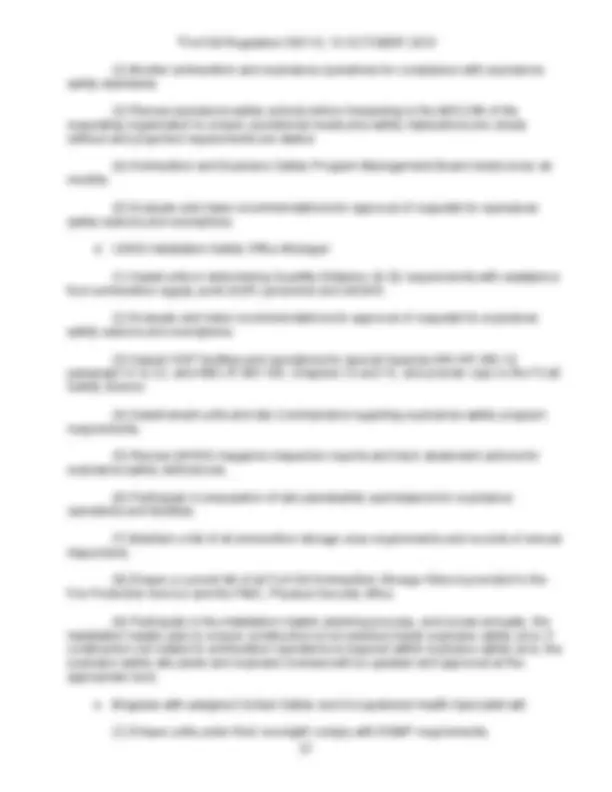
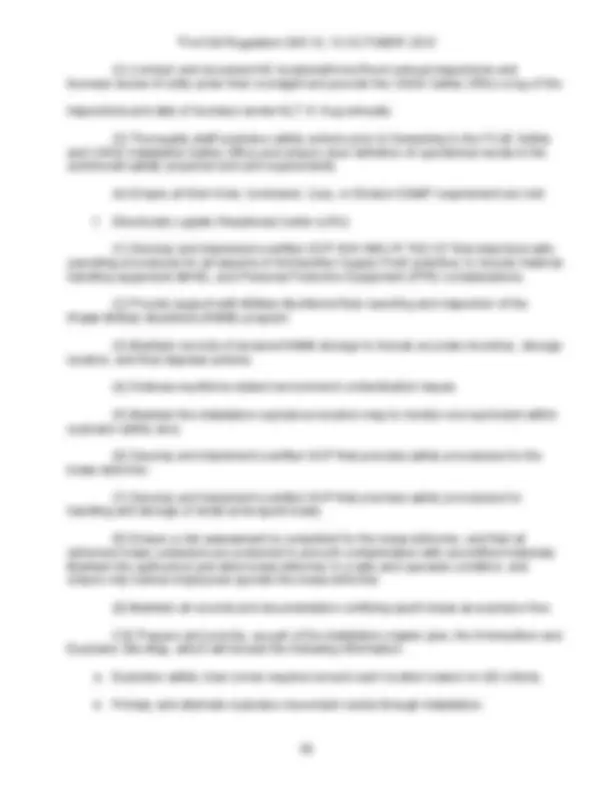
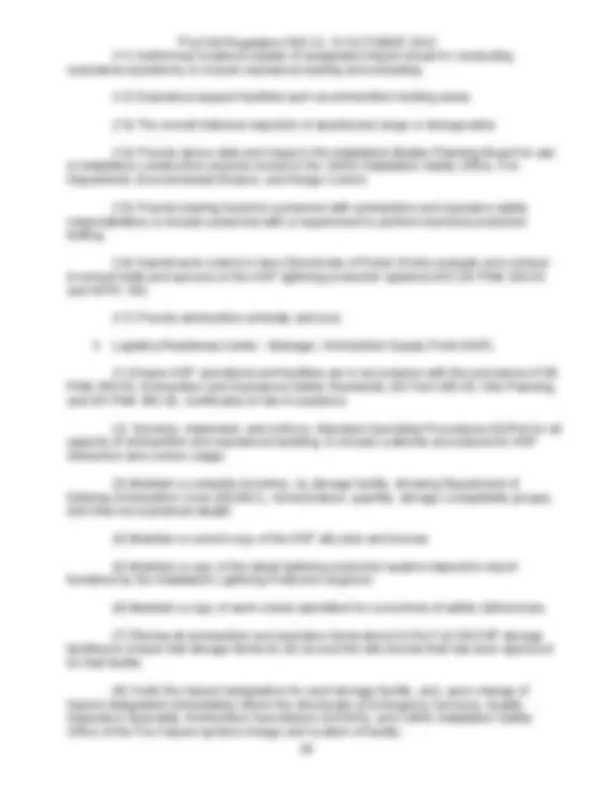
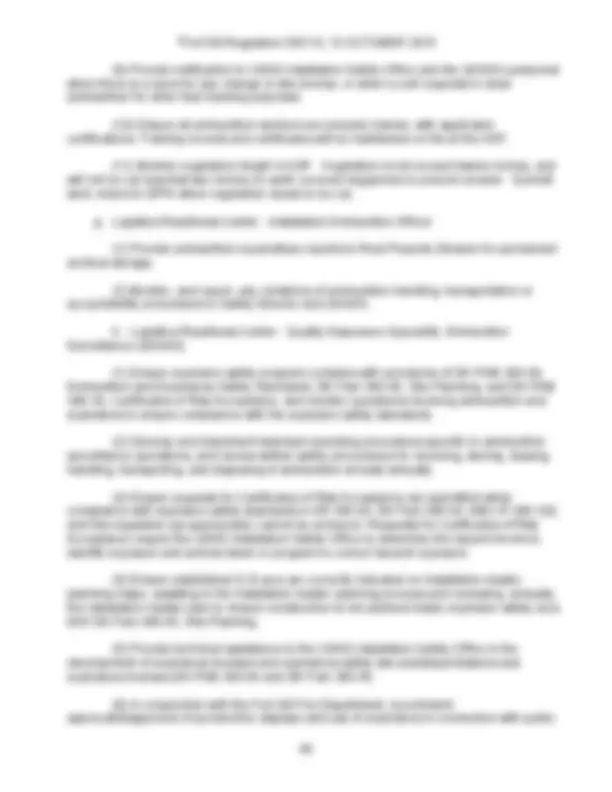
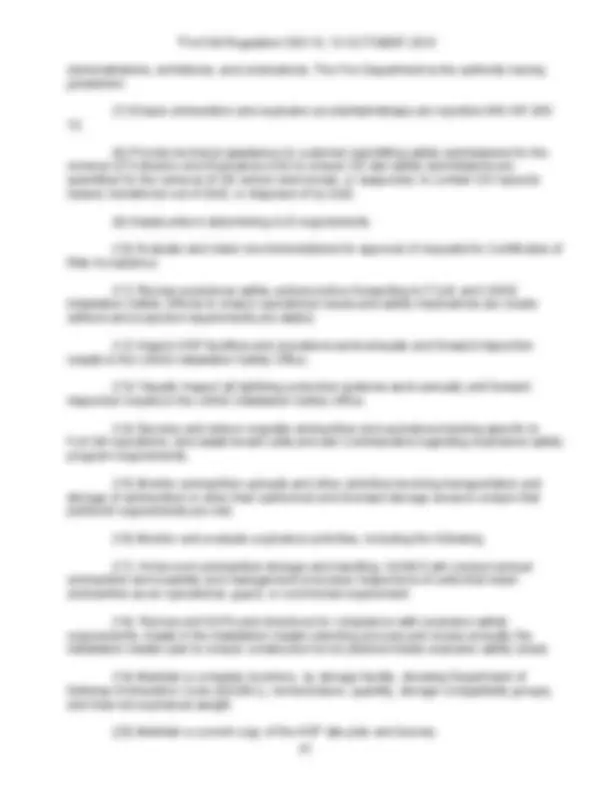
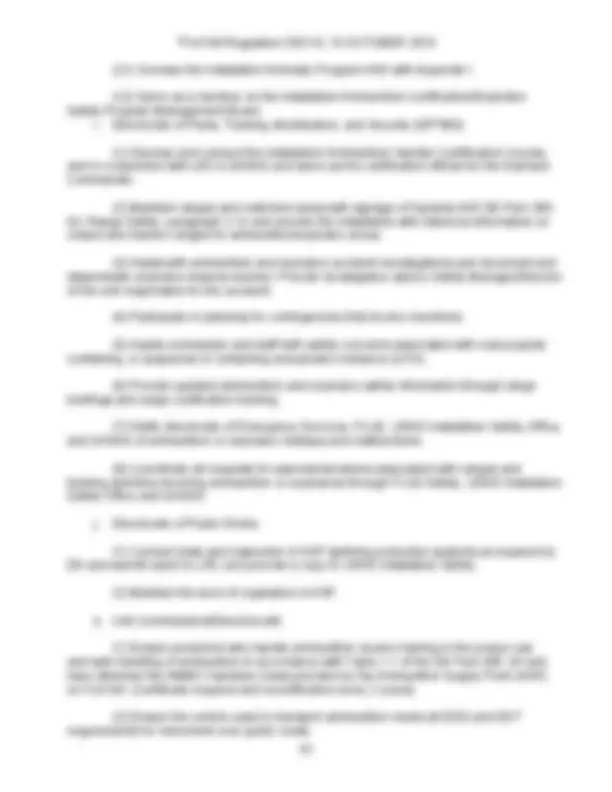
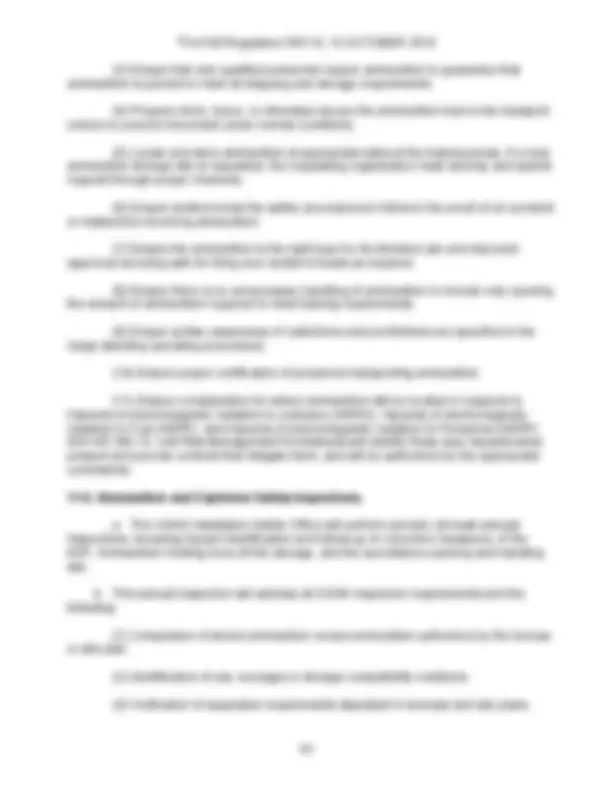
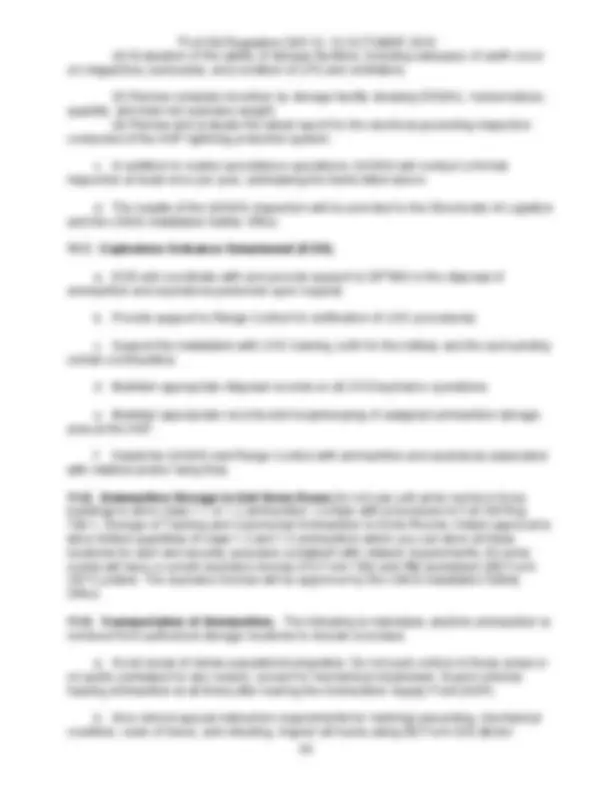
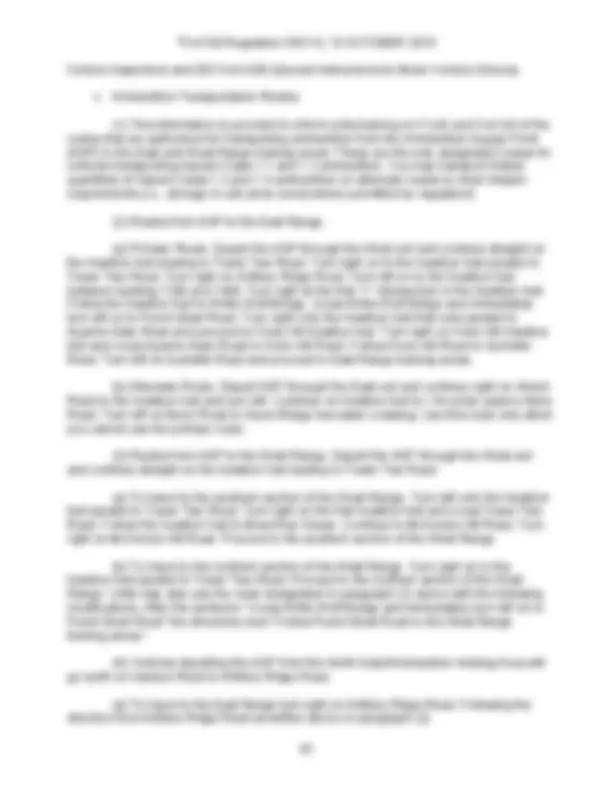
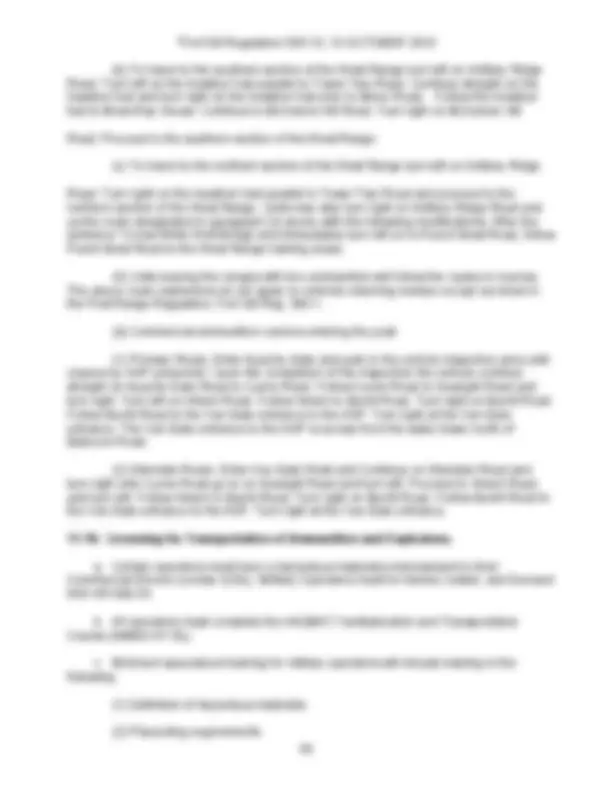
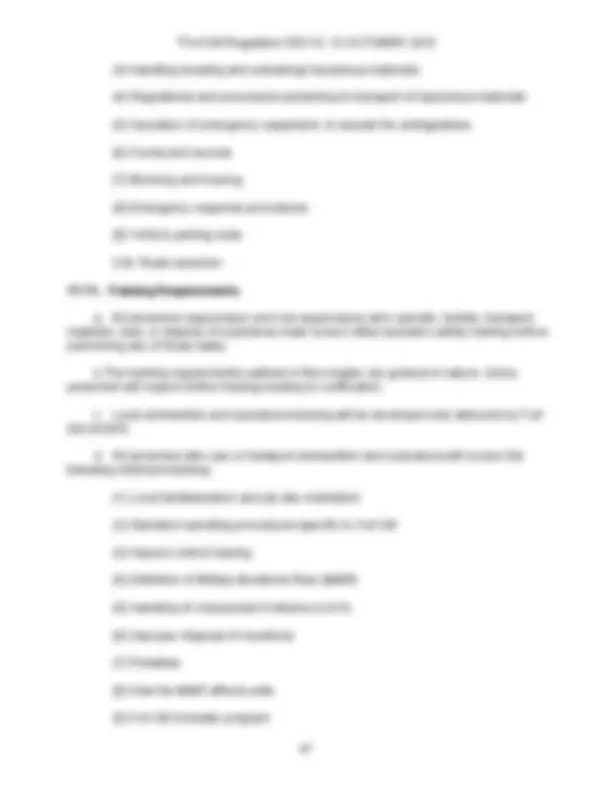
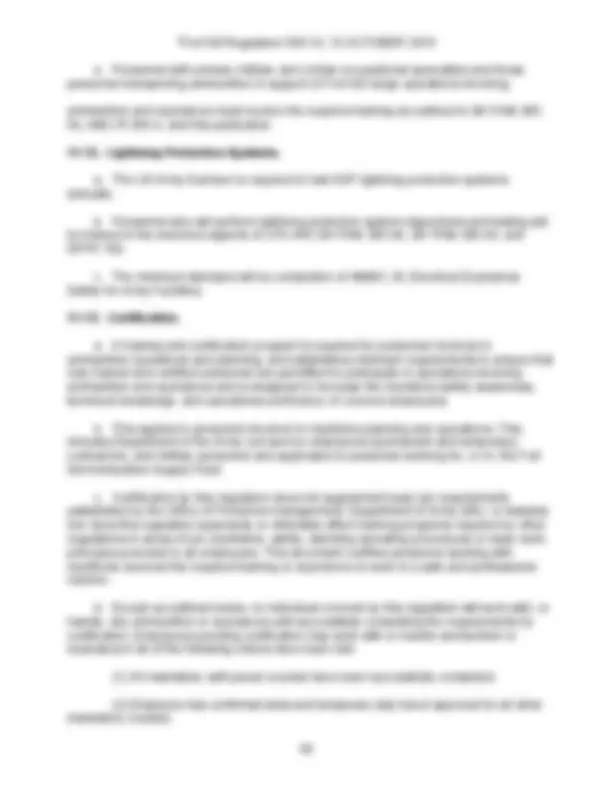
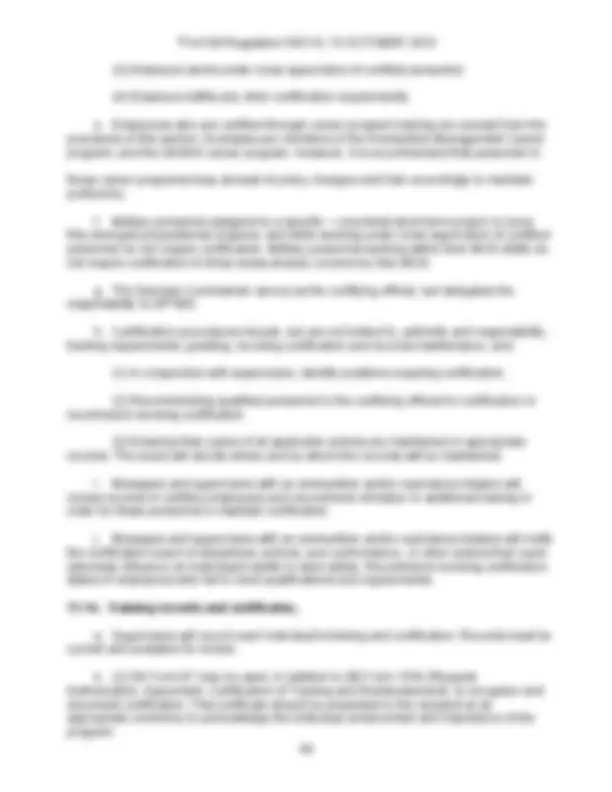
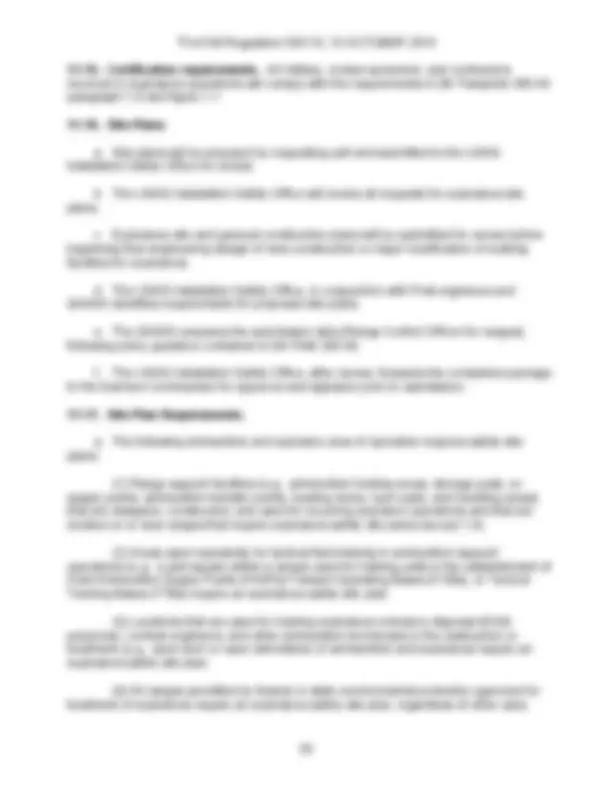
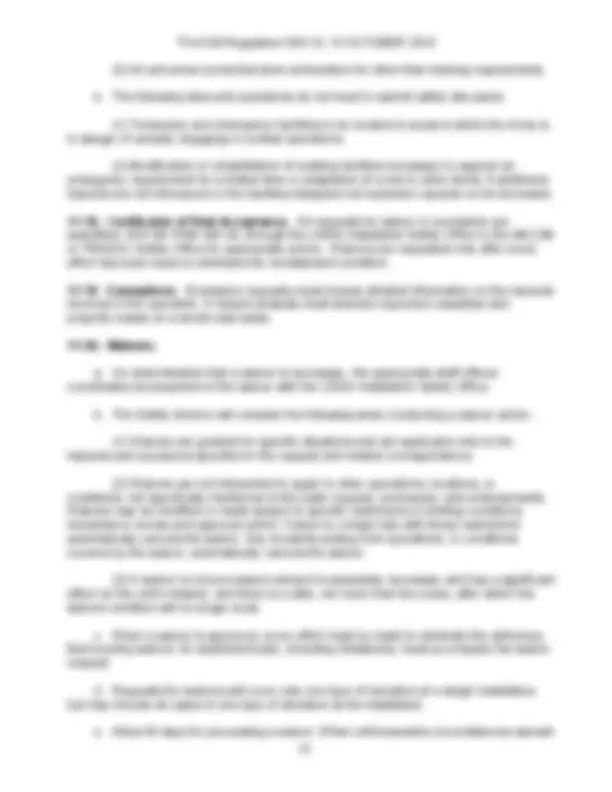
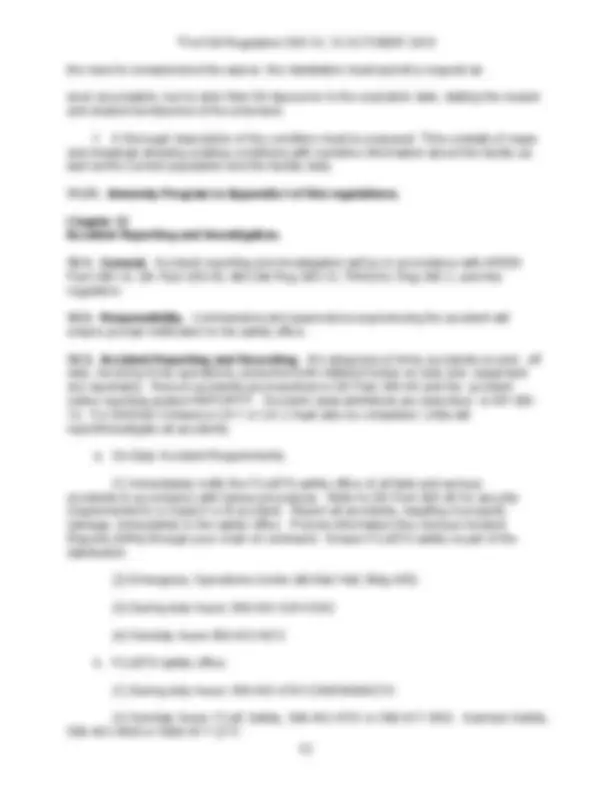
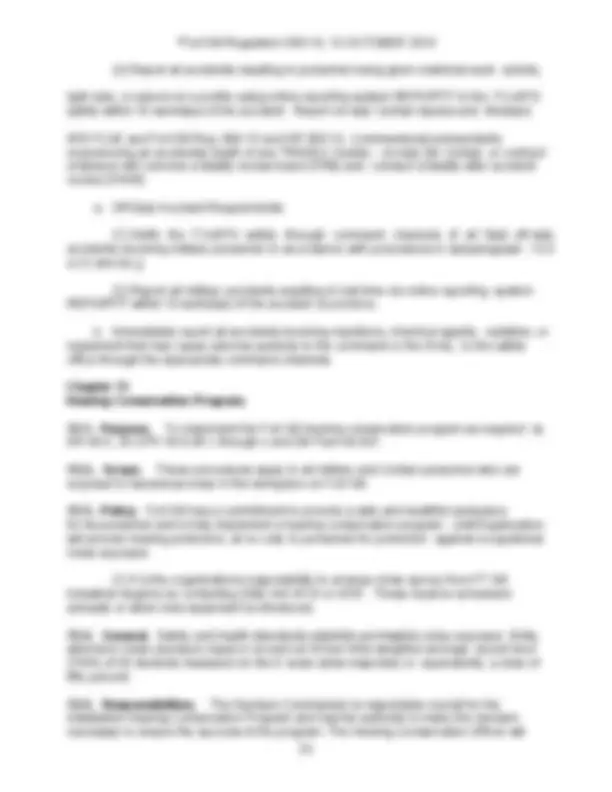
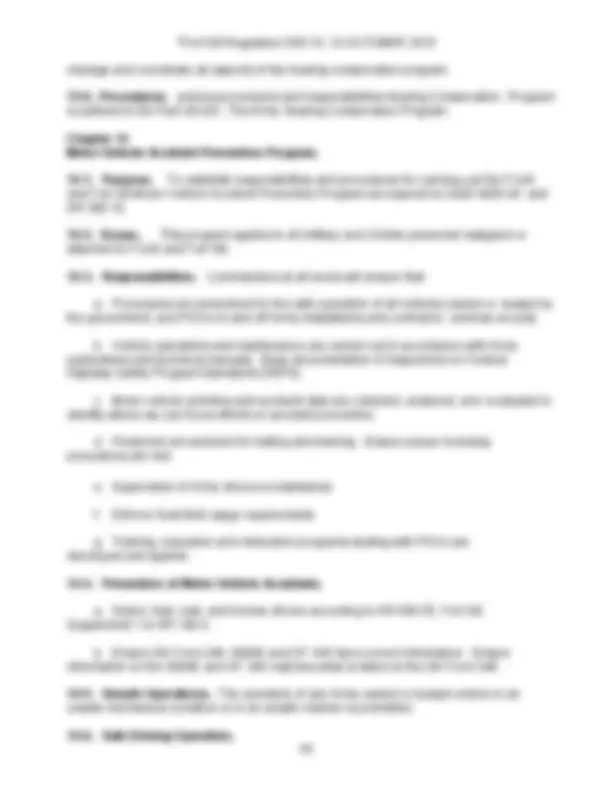
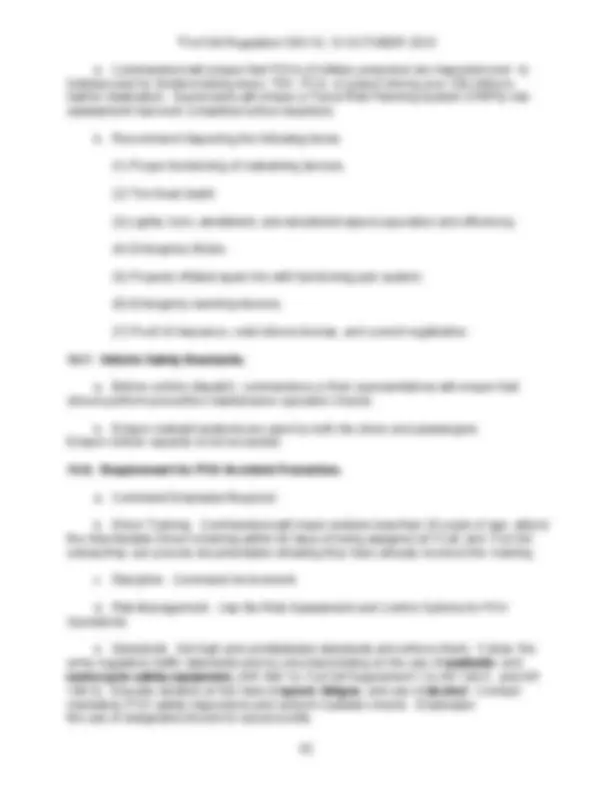
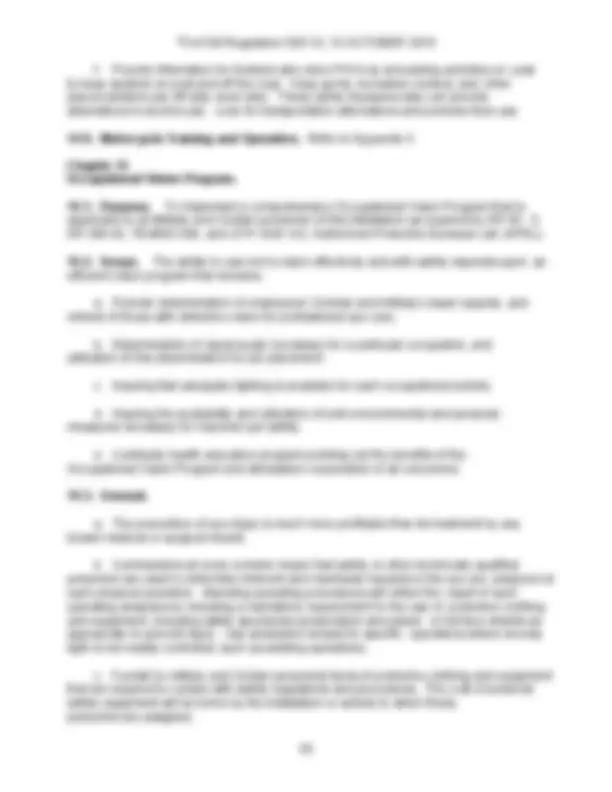
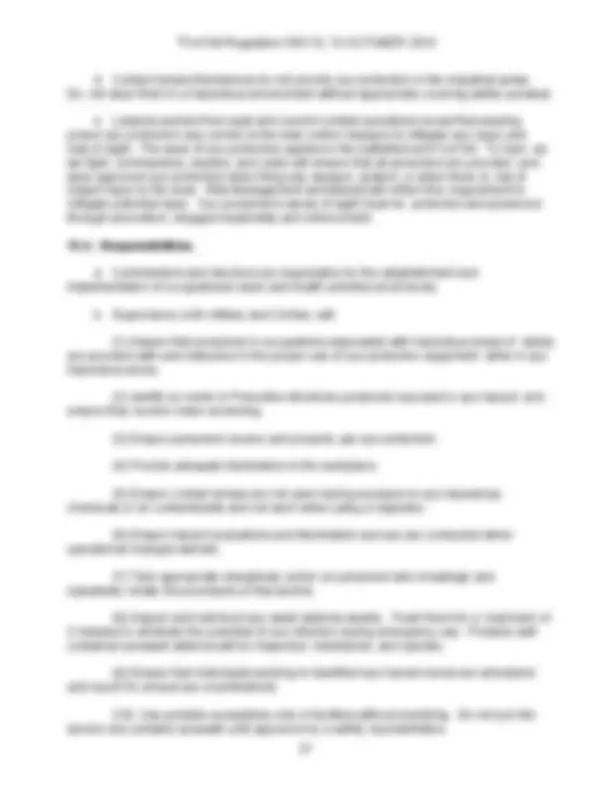
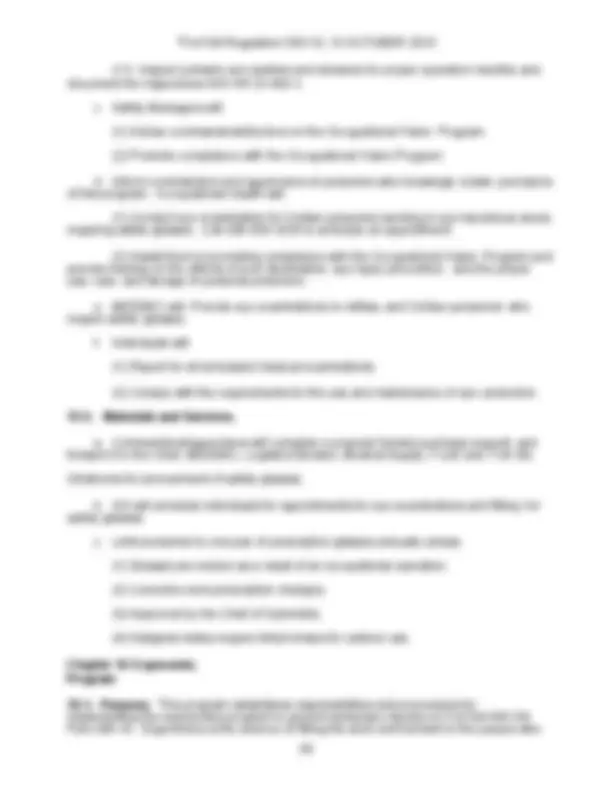
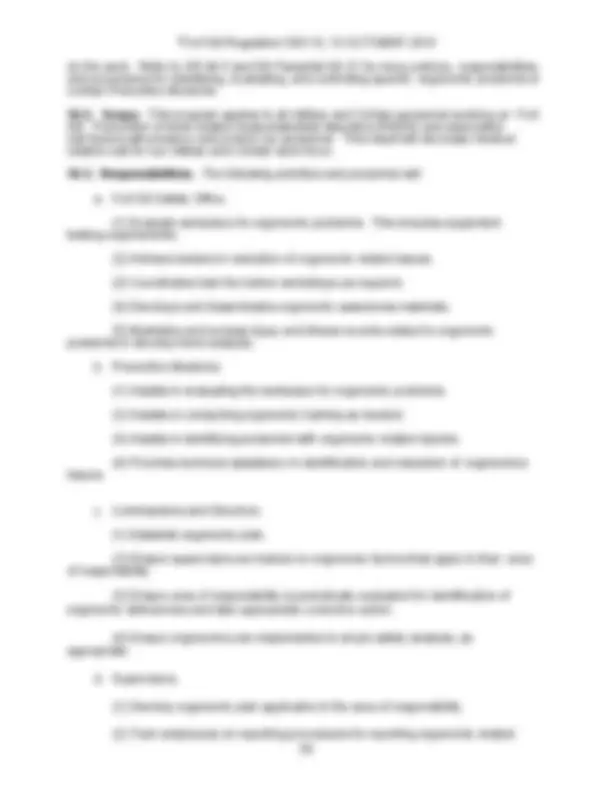
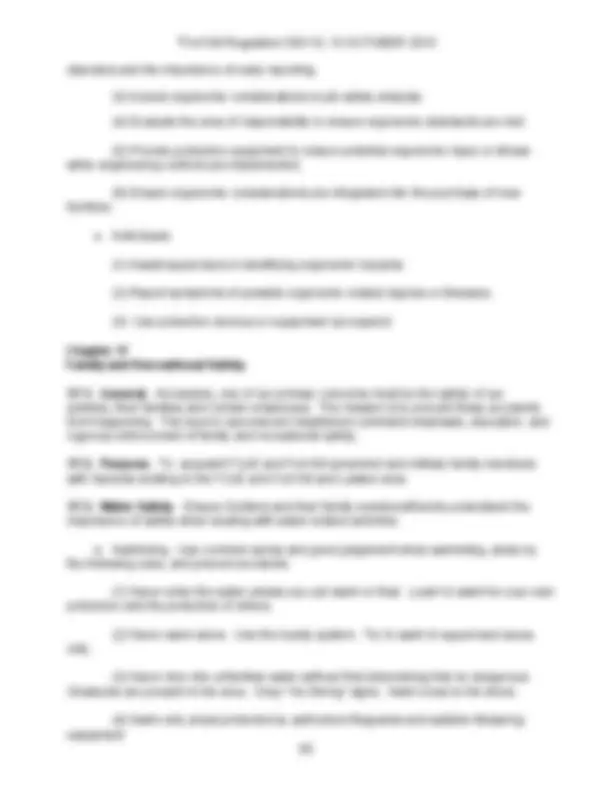
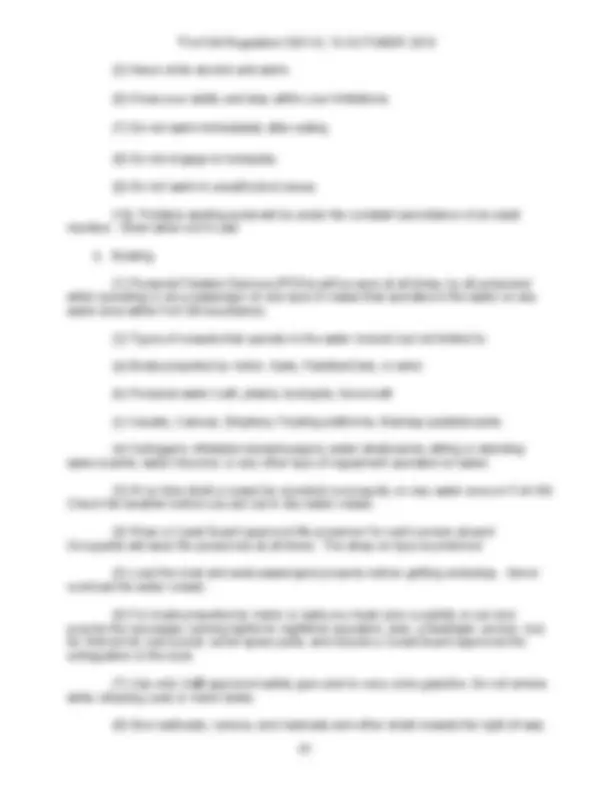
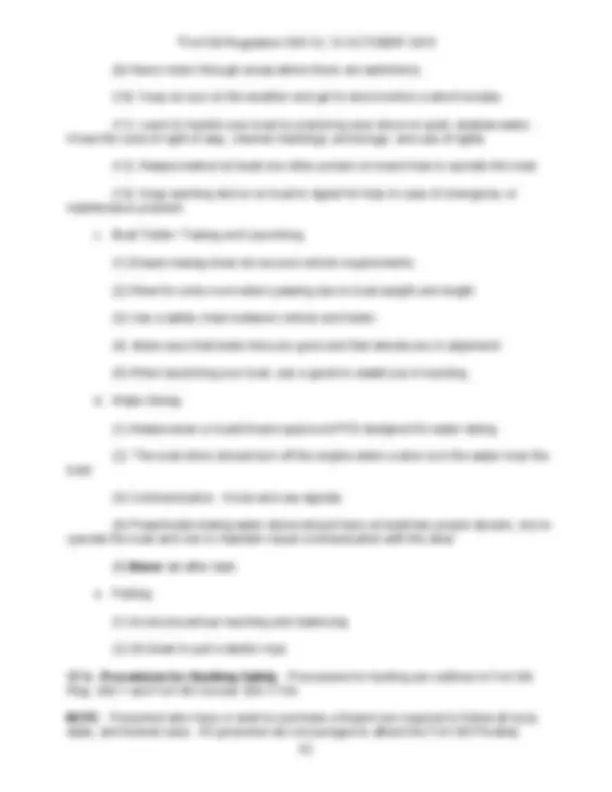
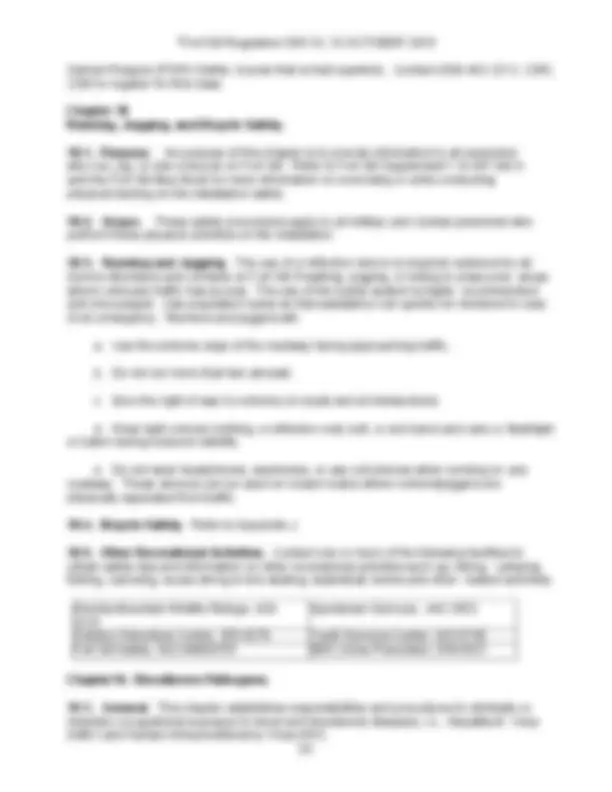
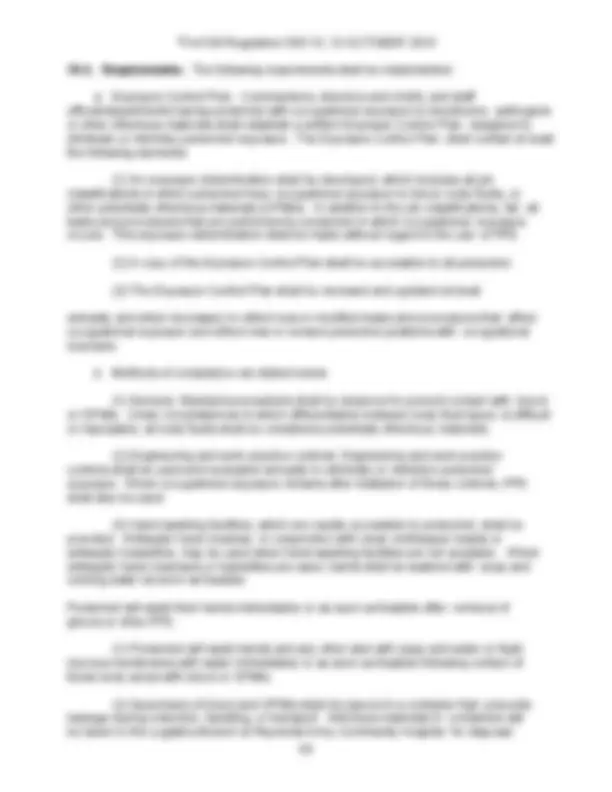
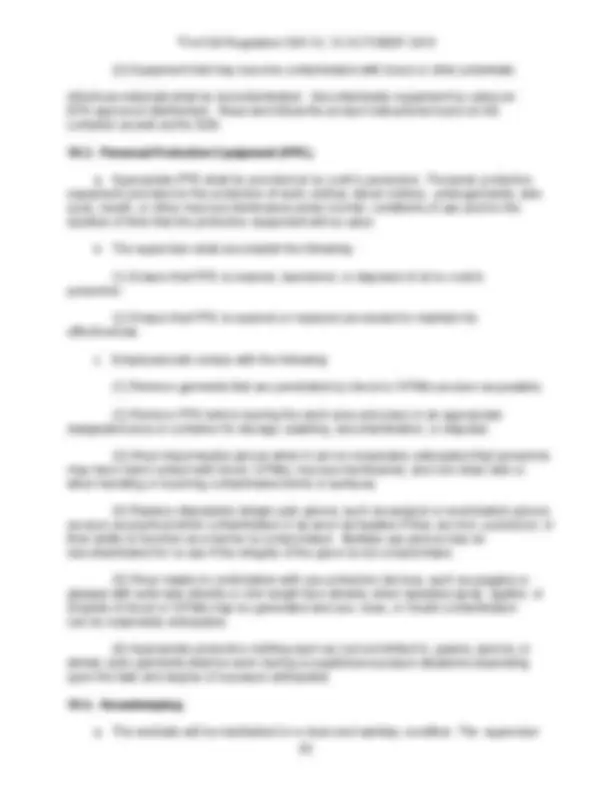
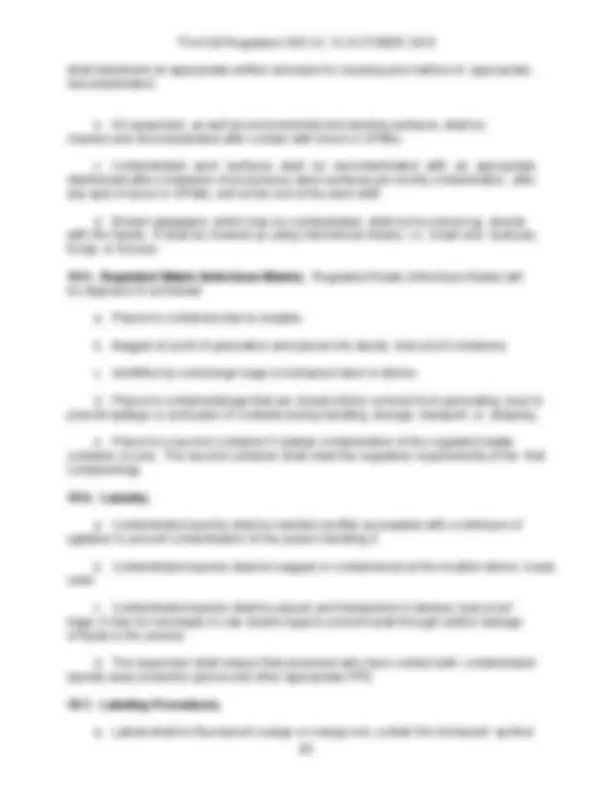
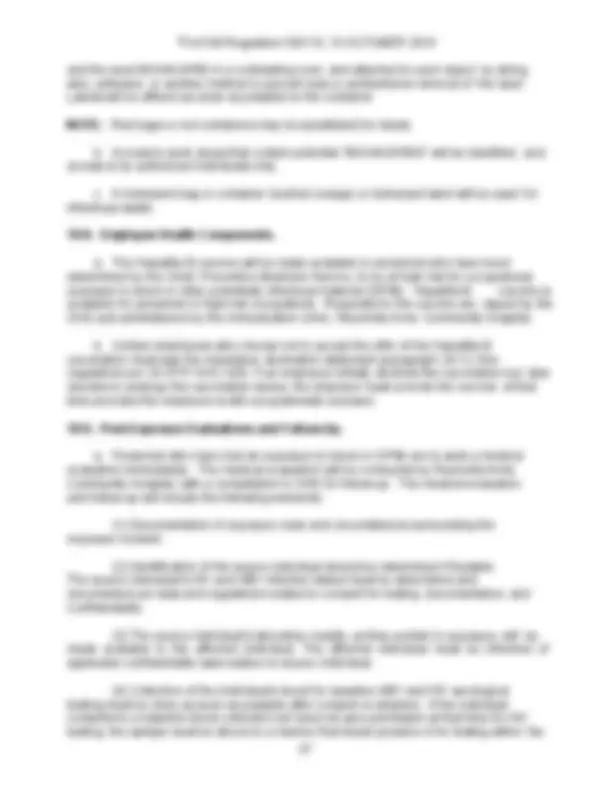
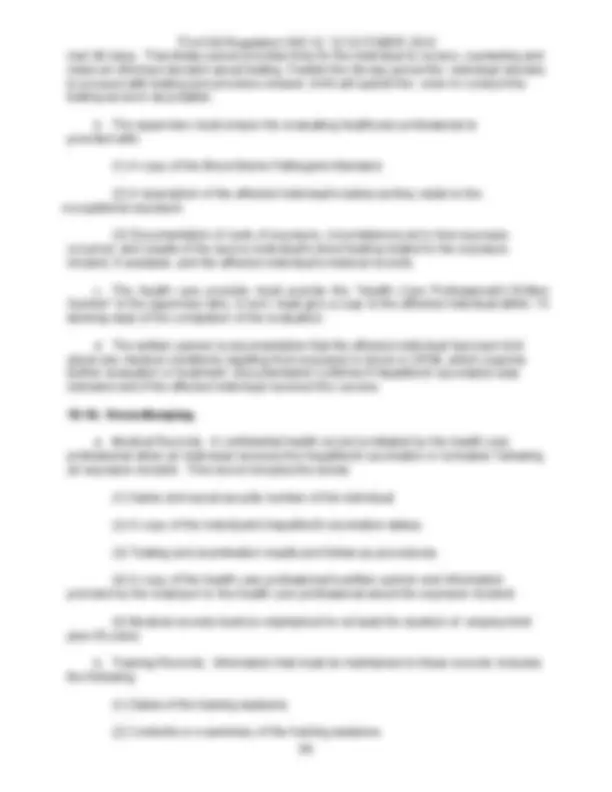
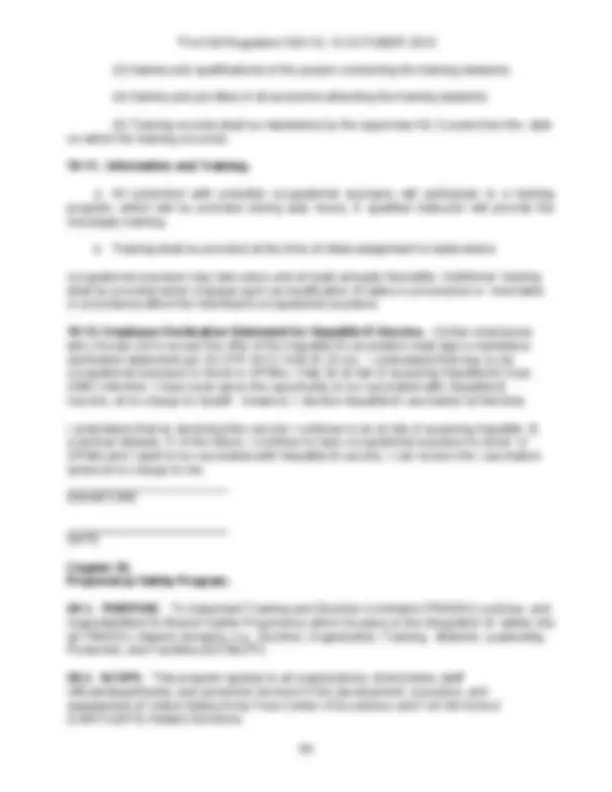
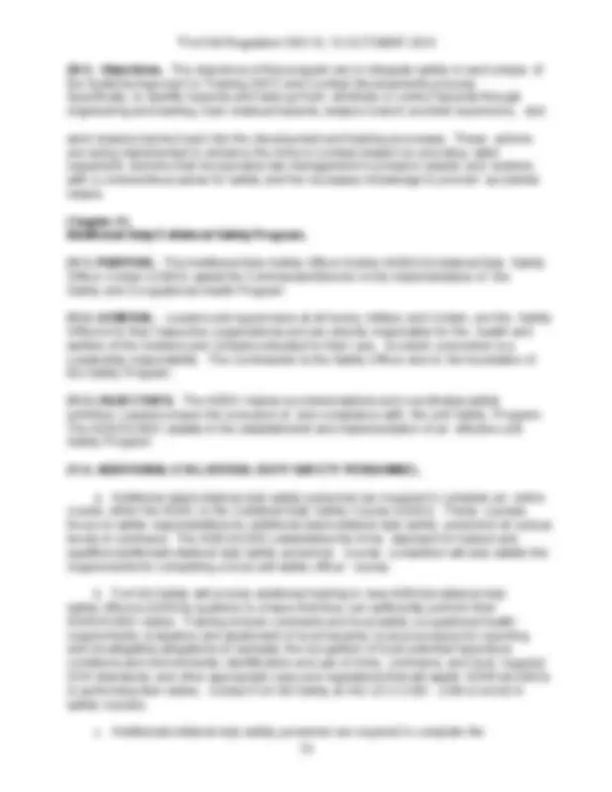
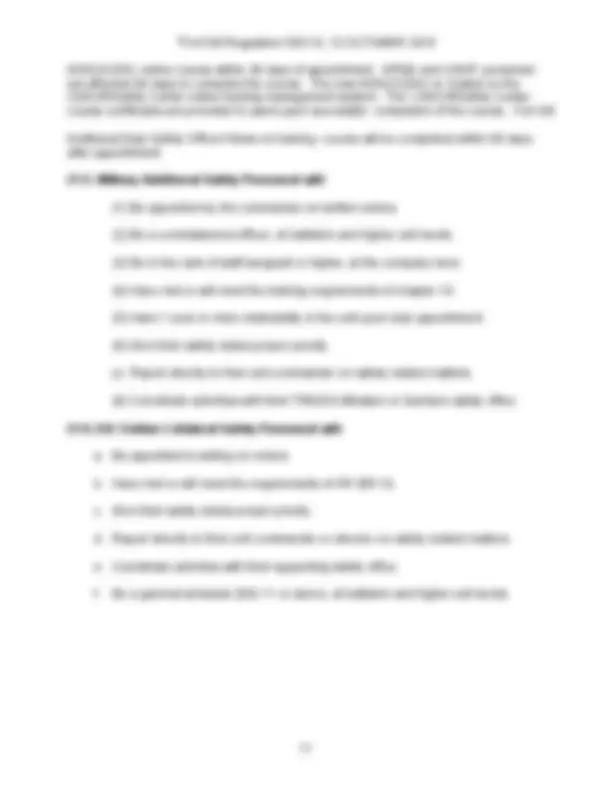
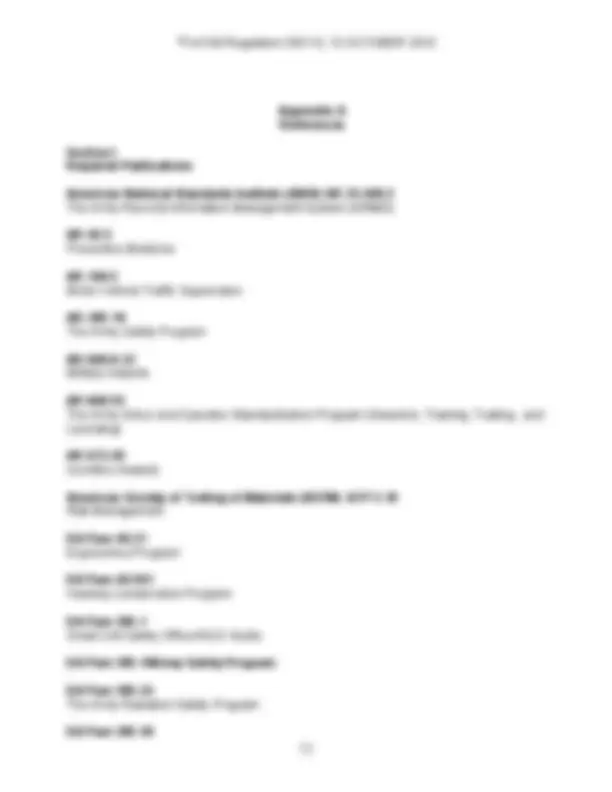
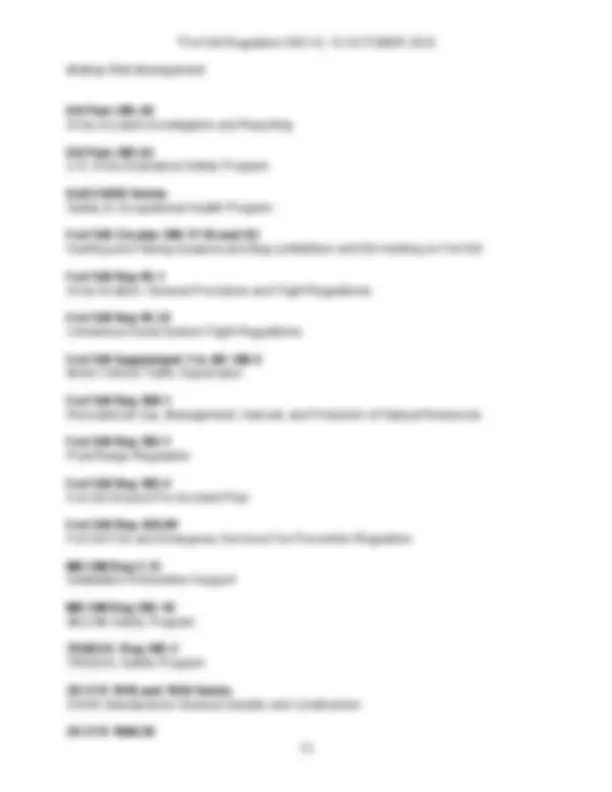
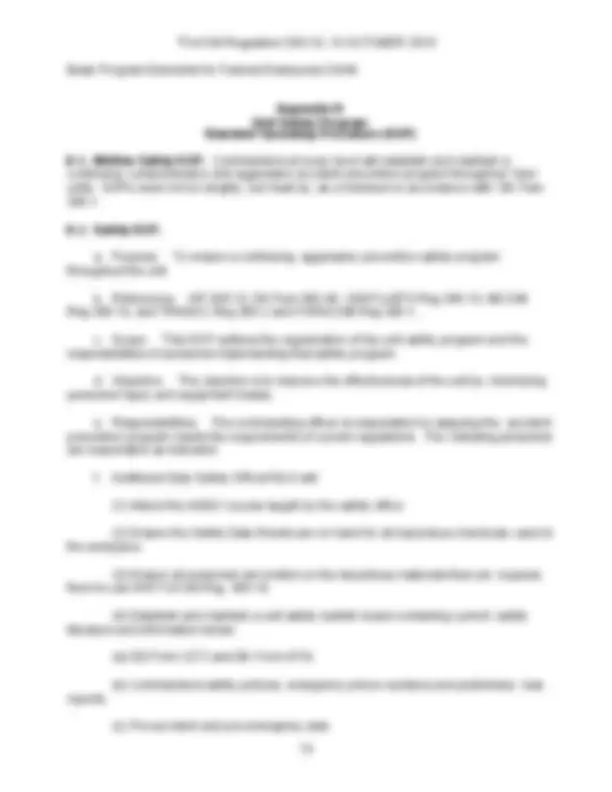
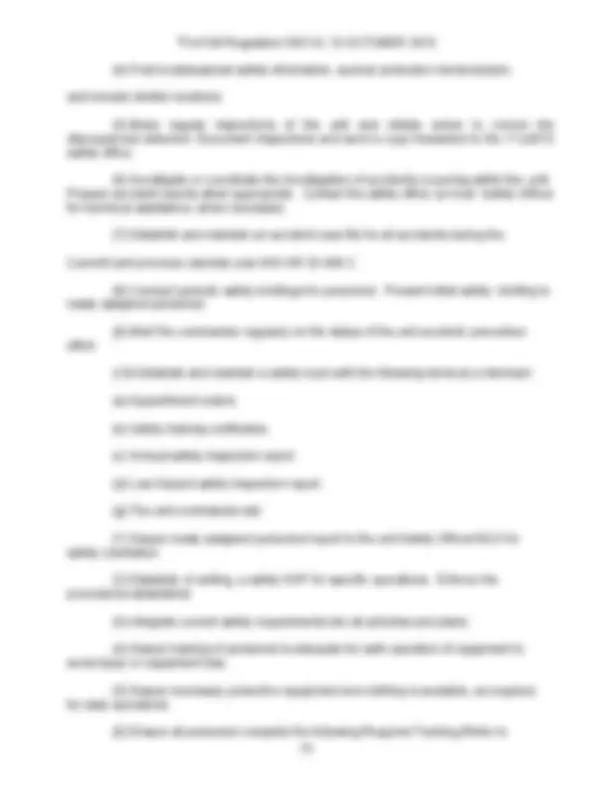
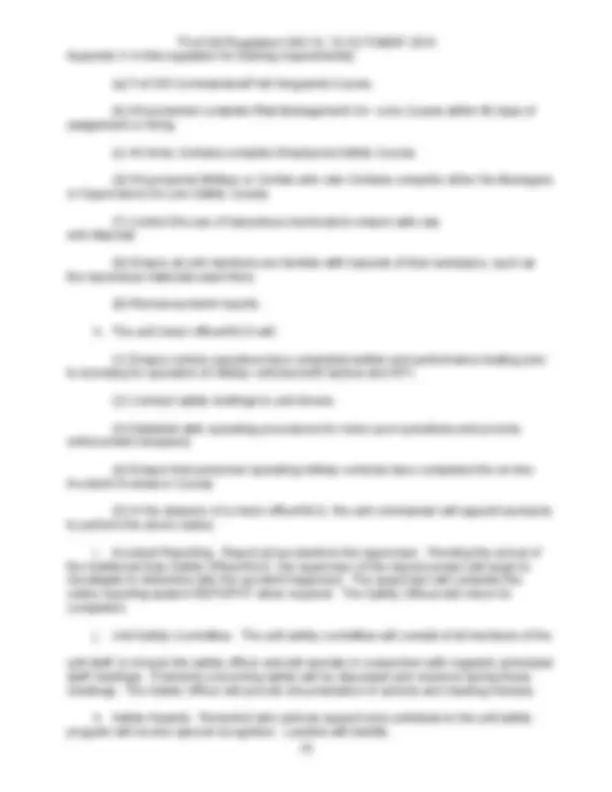
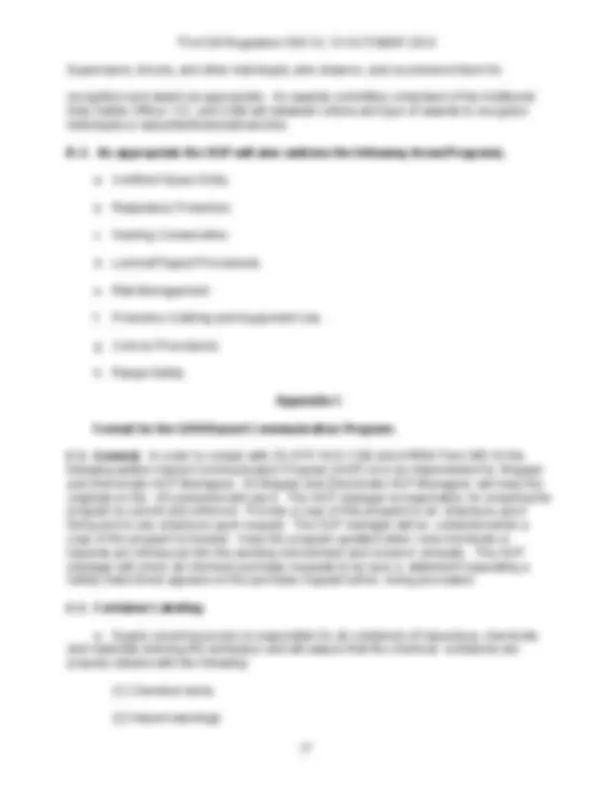
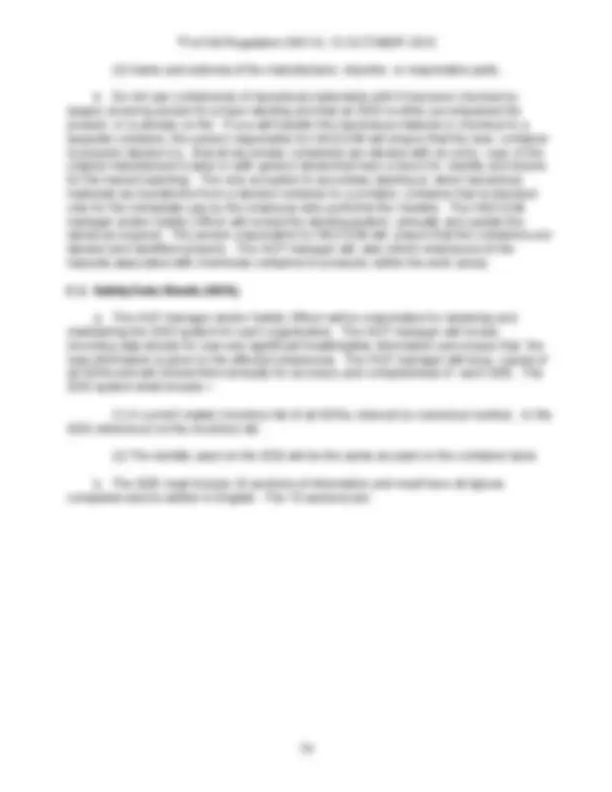
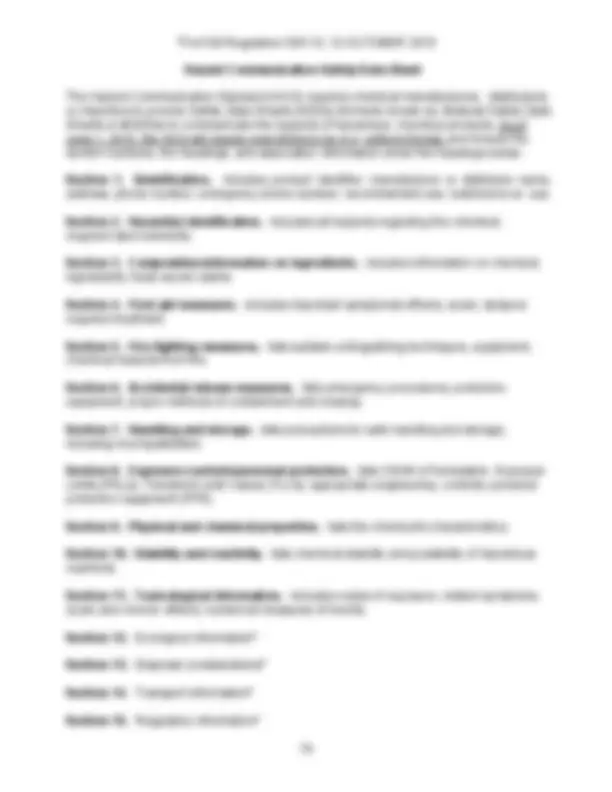
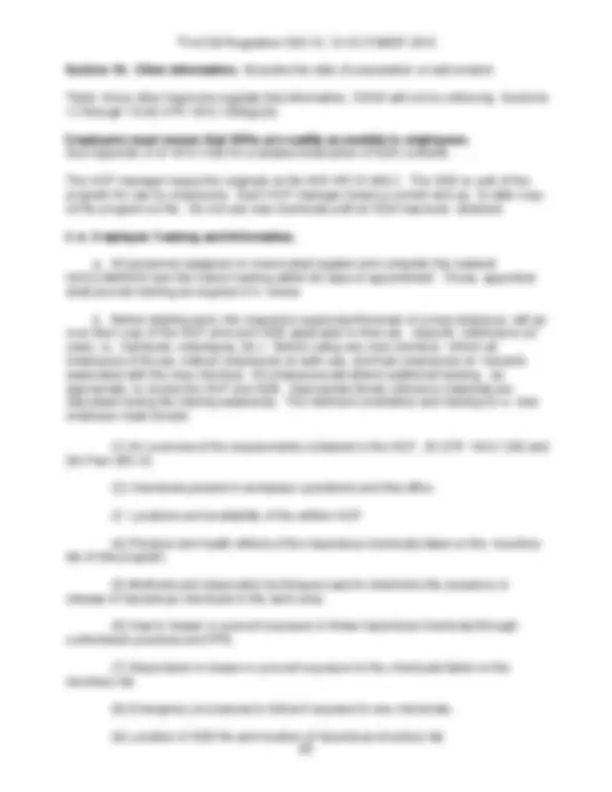
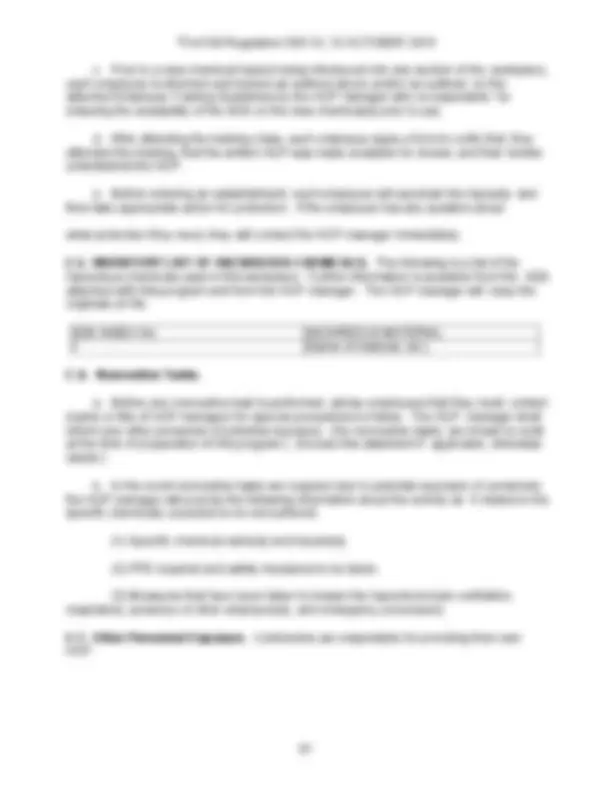
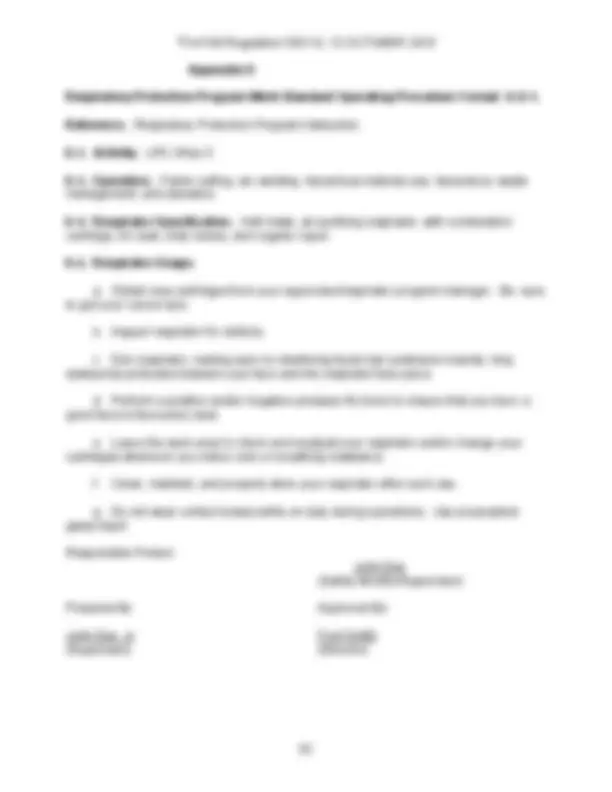
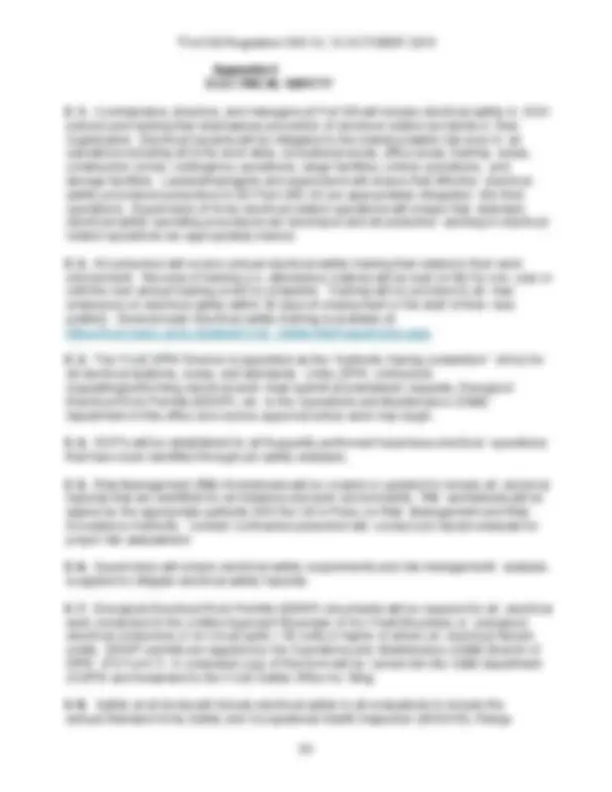
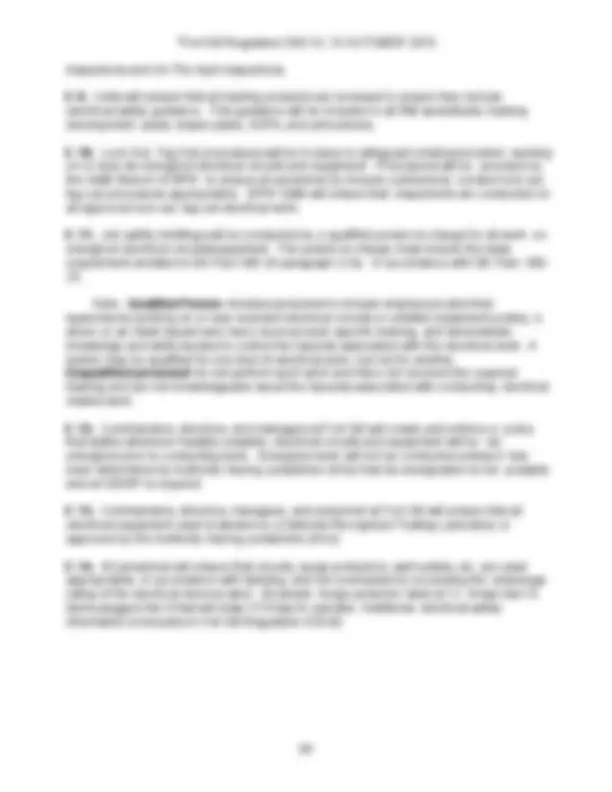
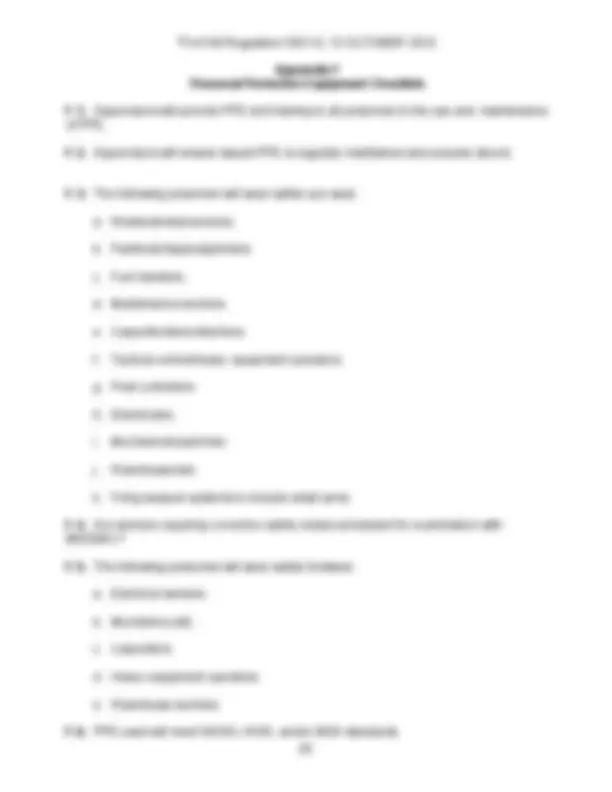
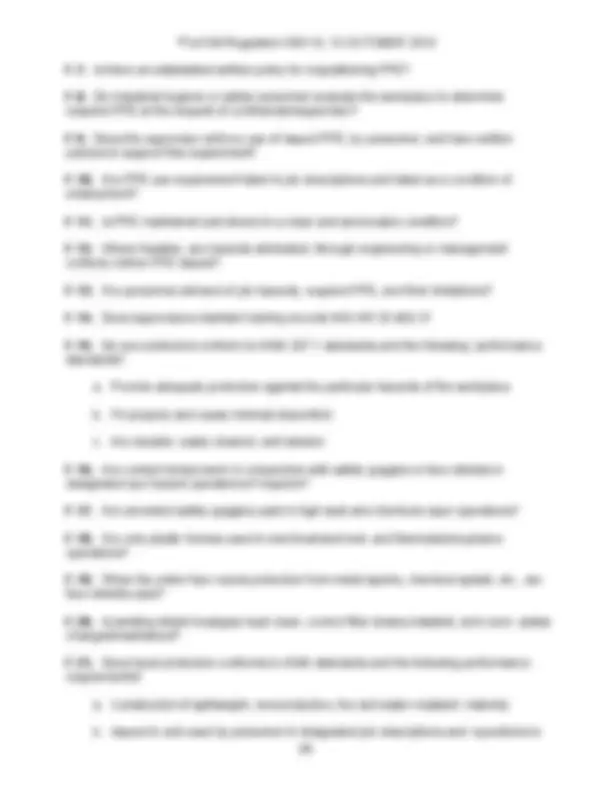

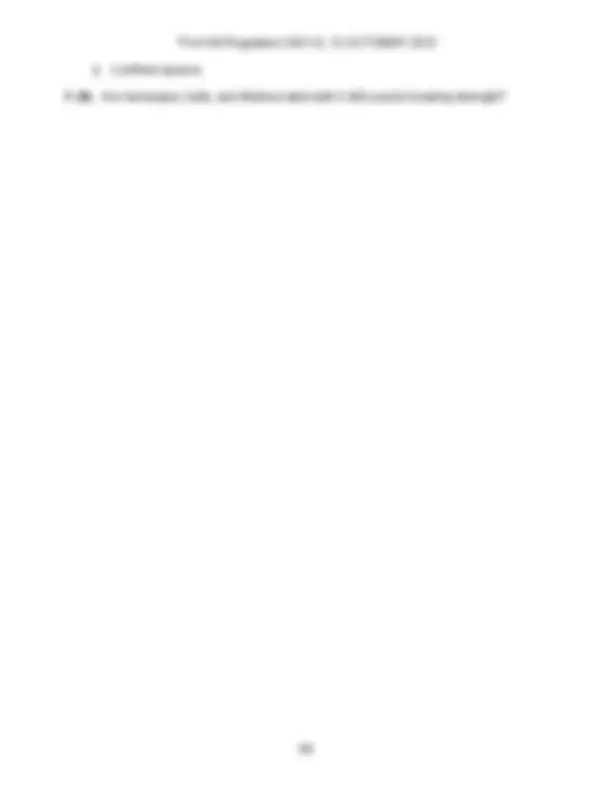
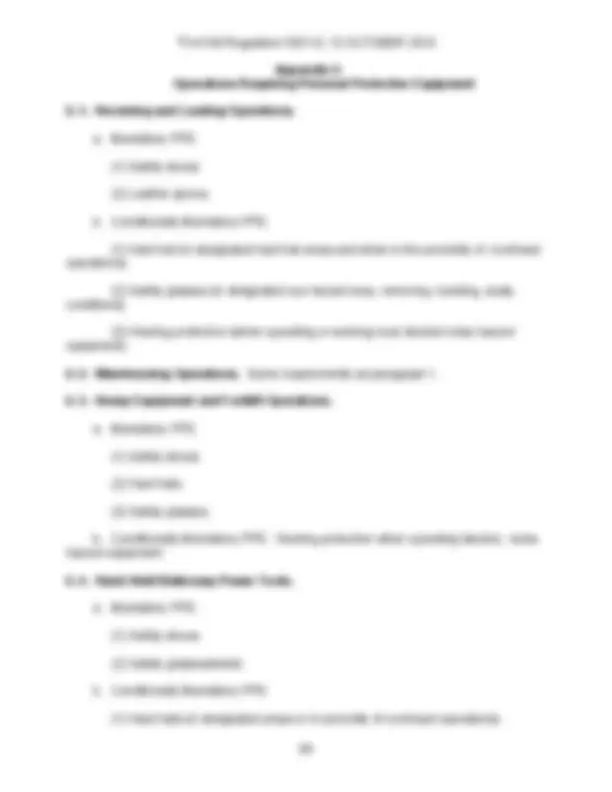
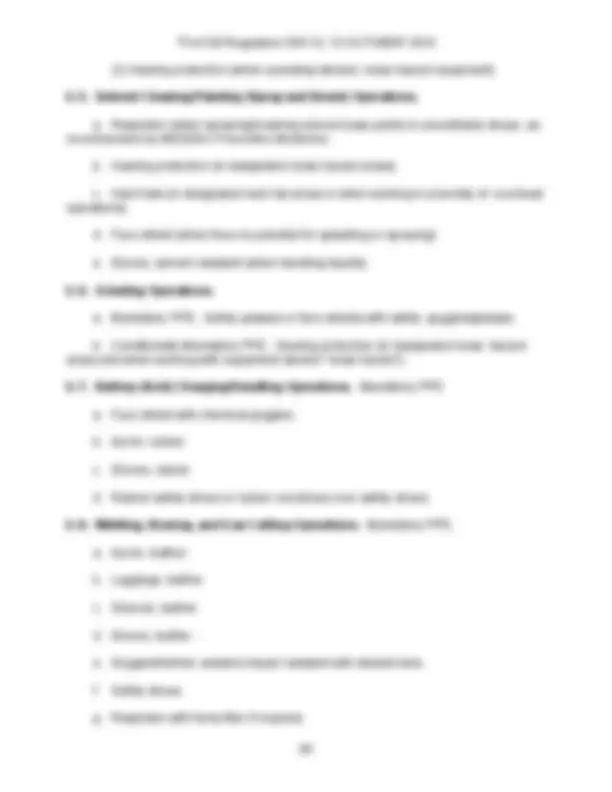
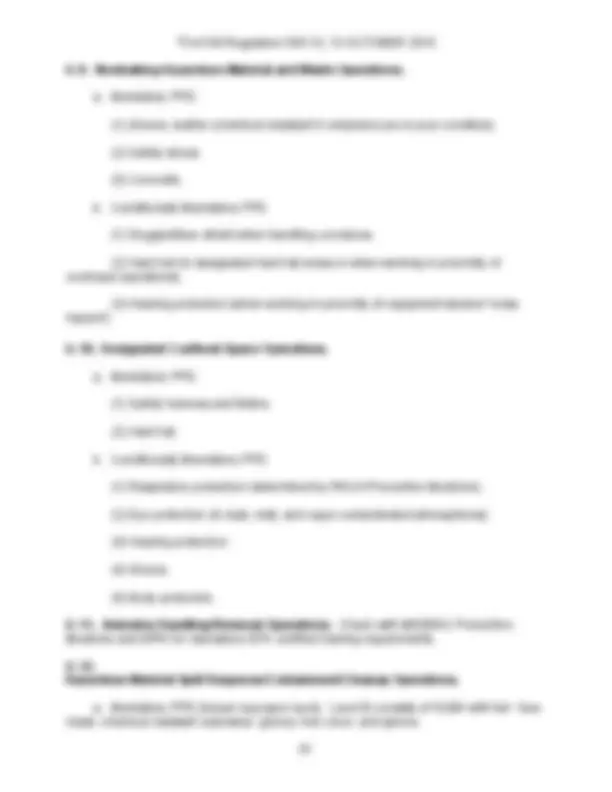
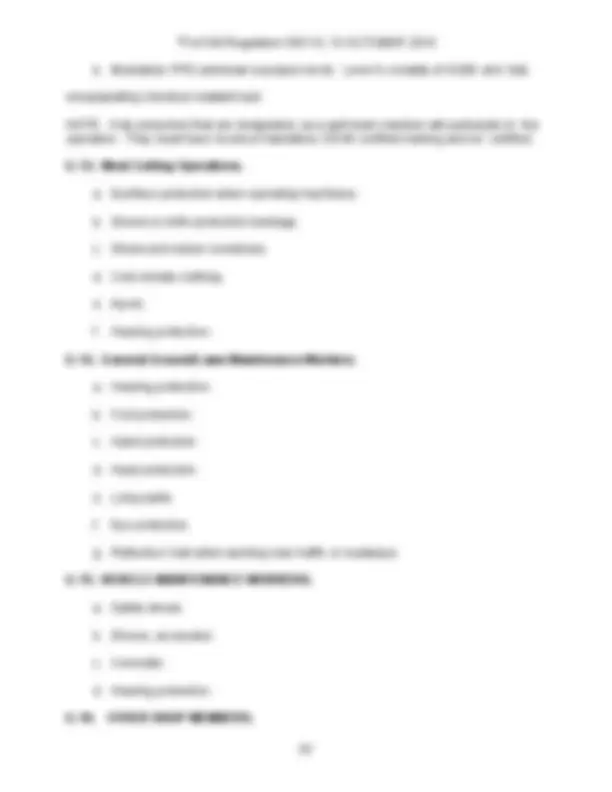
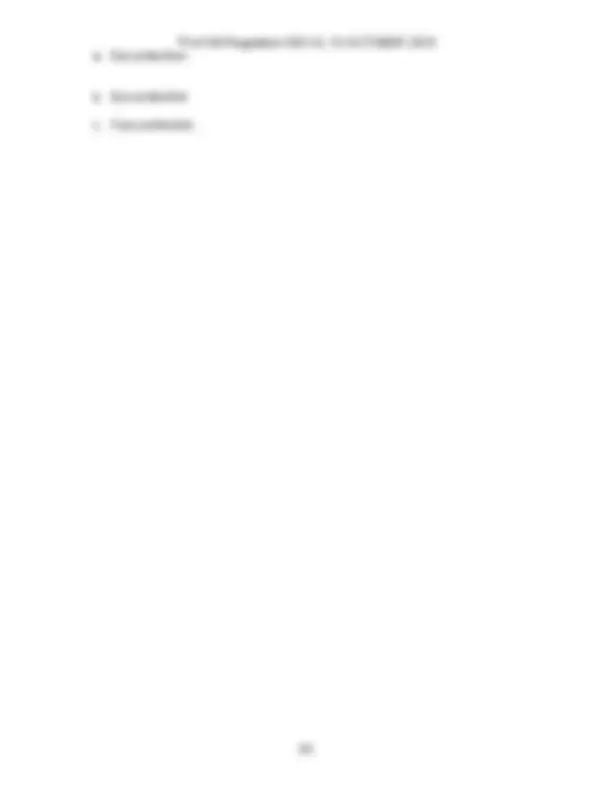
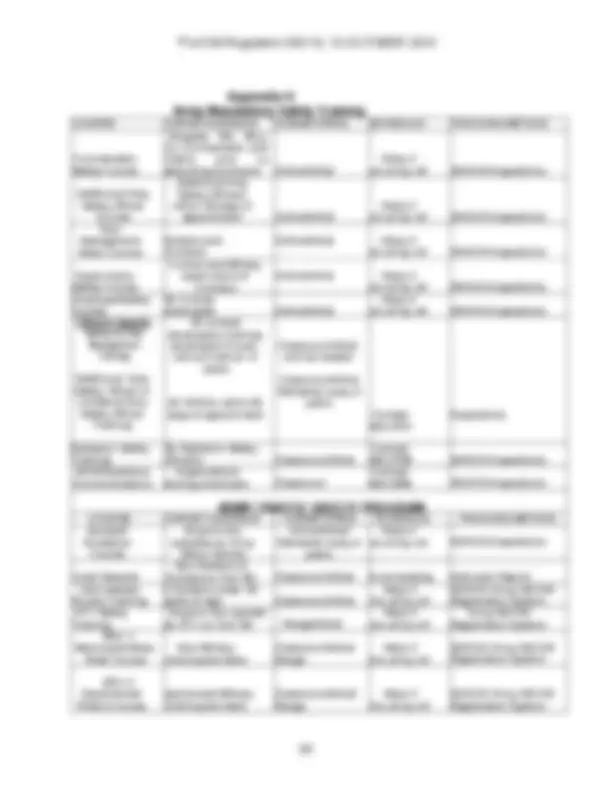
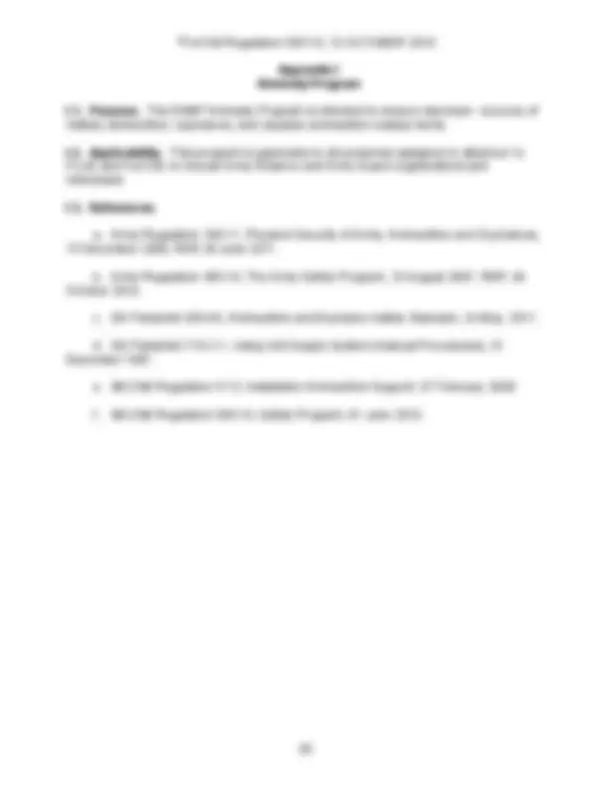
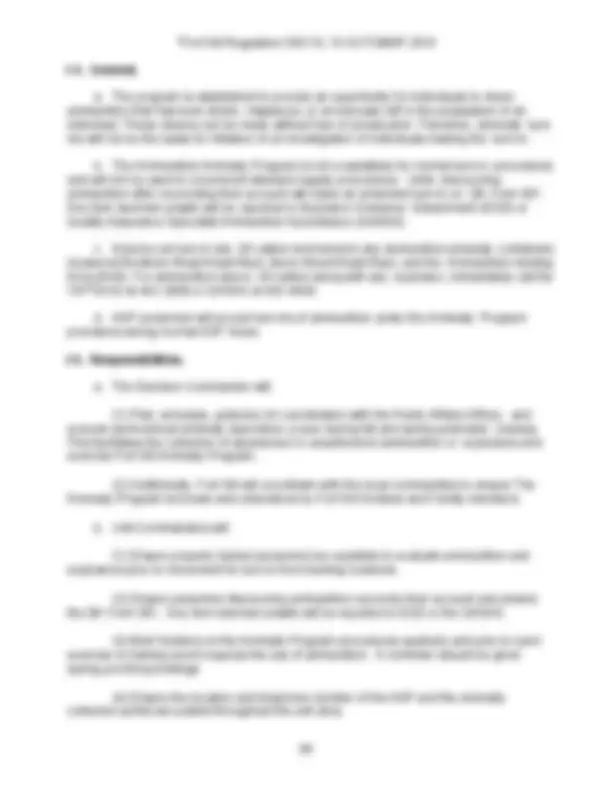
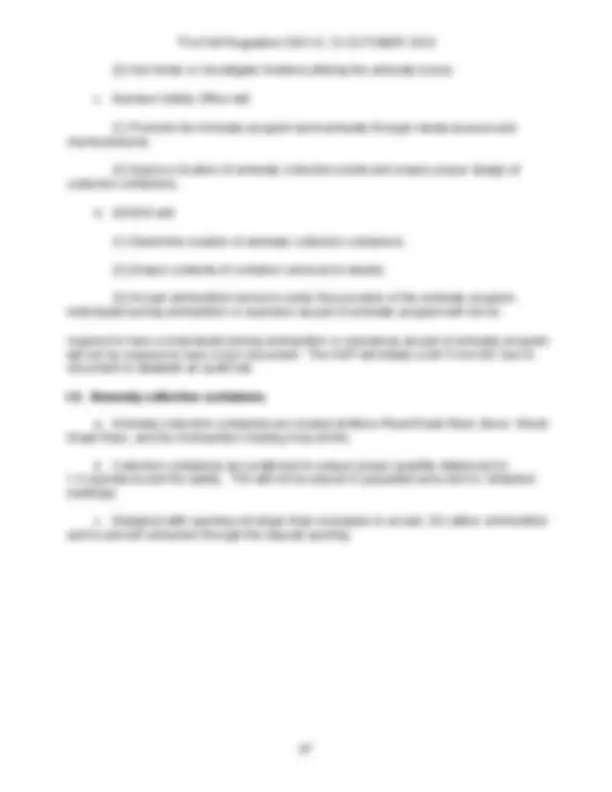
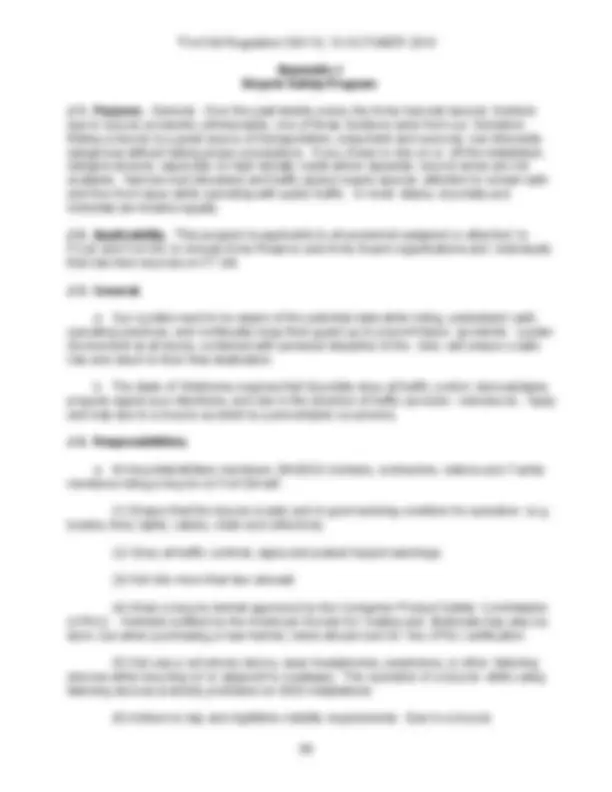
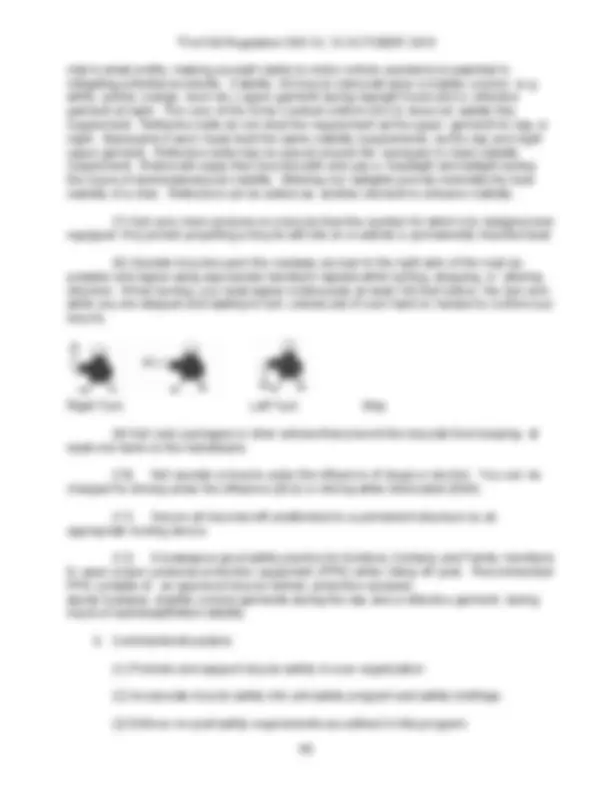
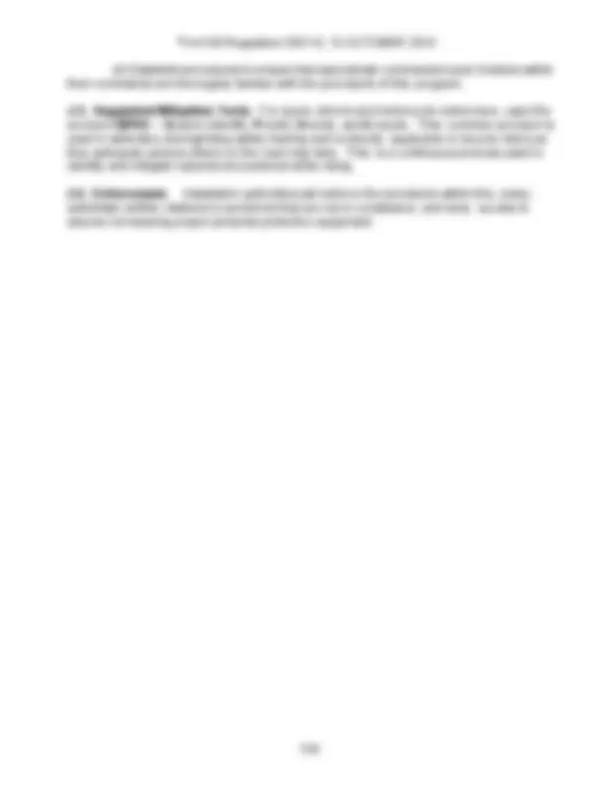
Study with the several resources on Docsity
Earn points by helping other students or get them with a premium plan
Prepare for your exams
Study with the several resources on Docsity
Earn points to download
Earn points by helping other students or get them with a premium plan
Community
Ask the community for help and clear up your study doubts
Discover the best universities in your country according to Docsity users
Free resources
Download our free guides on studying techniques, anxiety management strategies, and thesis advice from Docsity tutors
Summary. This regulation prescribes policy, procedures, and responsibilities for the United. States Army Fires Center of Excellence and Fort ...
Typology: Lecture notes
1 / 143
This page cannot be seen from the preview
Don't miss anything!
*Department of the Army Fort Sill Regulation 385- Headquarters, U.S. Army Garrison 462 Hamilton Road, Suite 120 Fort Sill, Oklahoma 73503 10 OCTOBER 2018
Safety SAFETY REGULATION
Summary. This regulation prescribes policy, procedures, and responsibilities for the United States Army Fires Center of Excellence and Fort Sill (USAFCOEFS) Accident Prevention Program. It implements requirements of the Occupational Safety and Health Act of 1970 as implemented in Executive Order 12196; 29 Code of Federal Regulations 1960; Department of Defense Instructions 6055 Series; Army Regulation (AR) and Department of the Army (DA) Pamphlet (PAM) 385-10.
Applicability. This regulation applies to all military, Civilian, and contracting personnel working on USAFCOEFS. Tenant commands and activities may establish host tenant agreements to cover specific issues necessary to implement their accident prevention programs in accordance with requirements unique to their Major Army Commands (MACOMs).
Supplementation. Supplementation of this regulation is prohibited without prior approval from the Safety Office, USAFCOEFS, 4700 Mow-Way Road, Suite 465, Fort Sill, OK 73503.
Suggested Improvements. The proponent of this regulation is the Safety Office, USAFCOEFS. Users are invited to send comments and suggested improvements on DA Form 2028 (Recommended Changes to Publications and Blank Forms) directly to the Fires Center/Fort Sill Safety Office.
Distribution. This regulation is distributed solely through the Director of Human Resources, Administrative Services Division Homepage at http://sill-www.army.mil/USAG/publications2012.html.
*This regulation supersedes FS regulation 385-10, 13 July 2018.
Table of Contents Paragraph Page CHAPTER 1. Introduction 5 Purpose 1-1 5 References 1-2 6 Explanation of Abbreviations and Terms 1-3 6 Records Management 1-4 6 Policy 1-5 6 Responsibilities 1-6 6-
Introduction 1-1. Purpose. This regulation prescribes policies, responsibilities, and provides procedures for implementing, managing, and conducting the USAFCOEFS Safety and Occupational Health (SOH) Program in accordance with federal law and Army
(6) Administer expeditious investigation and reporting of all accidents in accordance with DA Pam 385-40.
(7) Ensure all personnel are assigned to a medical surveillance and training program and attend all appointments and scheduled classes.
(8) Promptly abate all safety and health deficiencies.
(9) Include safety standards in supervisors’ performance appraisals.
(10) Budget and fund for safety supplies, equipment, and training.
(11) Establish and maintain a safety board to display safety and occupational health policies and materials. Strategically place safety posters throughout the area. Some posters are available from the safety office. Use posters designed by members of the unit and oriented toward unit needs whenever possible. These are normally more effective than stock posters. Replace posters frequently. They lose their effectiveness rapidly.
(12) Maintain a reading file of available safety literature. Include items such as safety standard operating procedures, bulletins, newsletters, memorandums, pamphlets, and other safety correspondence that applies to the organization.
(13) Post contact information, office location, and photo of ADSO/CDSO on all safety bulletin boards. Include locations where personnel notices are usually placed. The following items below are mandatory to be posted:
(a) Safety and Occupational Health Protection Program (DD Form 2272).
(b) Employee Report of Alleged Unsafe/Unhealthful Working Conditions (DA Form 4755).
(c ) Commanders Safety Policies.
(14) Establish written awards program to include unit, battalion (BN), brigade (BDE) and higher for awards program signed by Commander (see appendix B).
(15) Develop a Unit Safety Standard Operating Procedure (see appendix C). Units/organizations that adopt a higher headquarters safety program must have a memorandum signed by the commander/director.
(16) Conduct quarterly safety meetings down to battery/company level with a representative from each section and record minutes of the meeting. Maintain meeting minutes for record.
(17) Brigade, battalion, and company commanders, Command Sergeant Majors (CSMs) and First Sergeants (1SGs) will complete the Commander's Safety Course prior to assuming Initial Entry Training (IET) duties IAW TRADOC 350-6, Par 5-
(18) Ensure that all Soldiers and Army Civilians complete the On-Line Risk Management Course (AR 350-1, Par G-15) within 60 days of assignment or hiring.
(19) Ensure all Army Civilians complete the Employee Safety Course (DA PAM 385-10, Par 10-4) within 30 days of assignment or hiring.
(20) Ensure all personnel Military or Civilian that rate Civilians complete the Managers or Supervisors Safety Course (AR 385-10, Par 10-5) within 60 days of assignment.
(21) Appoint personnel at all levels of command for the following additional duties that fall within safety oversight, and ensure training is complete within 30 days of appointment:
(a) Hazardous Communications/Globally Harmonized System (HAZCOM) On- line registration: https://fcoe.tradoc.army.mil/sites/FCoE_Safety/SitePages/Home.aspx
(b) Fire Prevention, FS 420-90 (Call 442-5911 to schedule training)
(c) Master Driver, AR 600-55, Par 4-2 (Register through Schools NCO
(d) Motor Mentor, FS 385-10, App K (Current on MSF, Experienced, a Motorcycle Mentorleader)
(e) Radiation Safety, DA Pam 385-24, Par 1-4 (Only if organizations have Radiation Comodities)
(f) Safety Directors and Managers will:
(1) Develop mishap prevention and loss control measures and programs.
(2) Prepare specific activity safety rules and regulations for approval and issue by the Commander.
(3) Organize, coordinate, and conduct safety inspections, surveys, and workplace monitoring programs to identify violations, hazards, and deficiencies in the operations of facilities and equipment.
(4) Conduct safety mishap investigations, studies, and analyze reports of injuries or illnesses and property damage to identify causal factors. Determine trends, and initiate program improvement action.
(5) Maintain complete and accurate records on the mishap, injury, and
REPORTIT Army Accident Reporting System.
(5) Arrange immediate medical care and attention for employees injured on the job.
(6) Implement all Federal and DA rules and regulations.
(7) Conduct daily safety inspections within your departments, correct deficiencies, and maintain property and equipment in a safe operating condition.
(8) Document safety inspections on a monthly basis and maintain inspection records for one year.
(9) Ensure compliance with all safety training and medical surveillance programs and require strict adherence to all schedules and appointments.
(10) Document all safety, fire, and occupational health training provided to employees.
h. ADSO/CDSO’s shall:
(1) Complete the On-Line ADSO/CDSO course within 30 days of appointment.
(2) Complete required resident training within 90 days of appointment call (580) 442-2212/2265/2266 to schedule seat.
(3) Post contact information and photo on safety boards in their footprint.
(4) Conduct quarterly low hazard inspections that must be documented and maintained for a minimum of one year.
(5) Schedule Annual Standard Army Safety and Occupational Health inspections with the Fort Sill Safety Office.
i. Soldiers and Civilian employees will:
(1) Immediately report all occupational injuries or illnesses to their safety representative no matter how minor.
(2) Abide by all verbal or written safety rules given by a supervisor and/or safety professional.
(3) Accomplish work in a manner that will assure your own and other employees' safety and health.
(4) Report all unsafe or unhealthful working conditions to your supervisor.
(5) Use and maintain all personal protective clothing and equipment specified for the safe performance of your duties.
Chapter 2 Risk Management.
2-1. Purpose. This chapter establishes requirements for training safety measures for USAFCOEFS. All USAFCOEFS units must assess and control the risks associated with all potentially hazardous operations. The risk management process will be used IAW AR 350- 1, AR 385-10, ATP 5-19, FM 3-0, DA Pam 385-1, IMCOM Regulation 385- 10 and TRADOC Reg. 385-2.
2-2. General. Leaders at every level must be aware of correct safety procedures during training. All personnel shall complete the On-Line Risk Management training within 60 days of assignment or hiring, and further complete ongoing annual risk management training and document training. Subordinates follow and learn from the actions of leaders in the performance of their duties. Safety is no exception. Soldiers develop a "sixth safety sense" after being exposed to repetitive words and deeds that reflect leader's safety awareness and concern. Moreover, Soldiers be aware that you are accountable for accidents when you fail to exercise prudent caution or fail to accomplish a task in which you are trained or instructed. There is no choice between safety and realism. Safety always prevails.
2-3. Risk Management. Leaders at all levels utilize risk management procedures to integrate safety into planning and implementation phases of all operations to effectively accomplish the mission and provide protection against accidental losses of personnel and equipment.
2-4. Risk Acceptance Authorities. All personnel assigned to USAFCOEFS will follow current Commanding General‘s Policy on Risk Management and Risk Acceptance Authority.
Chapter 3 Hazard Communication Program.
3-1. Purpose. To provide guidelines and assign responsibilities for the implementation of 29 CFR 1910.1200, Occupational Safety and Health Administration (OSHA) Hazard Communication Standard (HCS)/Globally Harmonized Standard (GHS), and Appendix D, at USAFCOEFS subordinate commands and tenant activities.
3-2. Scope.
(6) Ensure Inventory check lists are completed and maintained at each location where chemicals are located.
c. Medical Department Activity (MEDDAC), Preventive Medicine will-
(1) Assist by providing technical guidance upon request and participating in formal training programs.
(2) Evaluate SDSs of "new" material to minimize the addition of HMs to the command's supply system.
(3) Conduct hazard evaluation and identify HMs in the workplace and the employees covered by the program. An industrial hygienist will conduct and document the evaluation, which must include-
(a) Identification of HMs that are physical or health hazards. Exclude from the assessment items such as hazardous waste (HW), drugs, food, tobacco, and common consumer products (household detergents, typing correction fluid, etc.), if other regulations cover them or they are used in the same manner as in typical consumer applications.
(b) Identification of employees potentially exposed to the HM. Potential exposure situations could occur during normal work activities, nonroutine tasks, and accidental spills.
d. Mission & Installation Contracting Command (MICC) will incorporate clauses in contracts that require contractors to comply with DOD & OSHA standards as well as provide SDSs of HMs they intend to use on projects.
e. Logistics Readiness Center (LRC) will forward a copy of each SDS, provided by vendors, to MEDDAC Preventive Medicine for review and approval.
f. Directorate of Public Works (DPW) will ensure proper identification and marking of piping systems, equipment, and storage tanks containing HM.
g. Civilian Personnel Advisory Center, (CPAC) will assist in identifying Civilian employees requiring training as required by law or for the success of the command’s HCP.
h. Fort Sill Safety Office has oversight and monitors the HCP.
i. Commanders, directors, and supervisors will appoint a HM/HW manager who develops, implements, and maintains a written HCP for their workplace in accordance with 29 CFR 1910.1200. A written program is in appendix D.
j. Army military and Civilian employees will-
(1) Use and handle HMs safely and in accordance with manufacturer's specifications.
(2) Use engineering controls, protective equipment, and safe procedures to prevent HM mishap.
(3) Obtain supervisor’s approval prior to introducing new HMs into the workplace or changing operations or procedures using HMs.
(4) All personnel that have a potential to come in contact with chemicals shall be trained. All training shall be documented and maintained on file for a period no less than one year.
Chapter 4 Respiratory Protection Program.
4-1. Purpose. To implement the command's Installation Respiratory Protection Program (IRPP) as required by AR 11-34, DA Pam 385-10, and 29 CFR 1910.134(c).
4-2. Scope. This applies to all units assigned or attached to USAFCOEFS elements.
4-3. Policy. USAFCOEFS has a commitment to provide a safe and healthy workplace for its personnel and to fully implement a respiratory protection program. Unit/Organization provides respiratory protection equipment, at no cost, to personnel for protection against chemical and other respiratory hazards when the following conditions exist.
a. Engineering and/or administrative hazard controls are not feasible.
Development of hazard controls is pending.
b. Short-term, nonroutine operations for which engineering and/or administrative hazard controls are not feasible.
c. Emergency situations (e.g., spill response, damage control, etc).
d. At the request of an employee.
4-4. General. Safety and health standards establish permissible exposure limits (PELs) for airborne concentrations of potentially hazardous dusts, fumes, mists, and vapors. When engineering controls are not feasible, or as an interim step, implement a respiratory protection program governing respirator selection, use, maintenance, and release of appropriate respirators to employees.
4-5. Responsibilities.
(1) Install and maintain breathing air systems capable of providing Grade D breathing air where required.
(2) Maintain compressed air breathing system alarms in an operable manner.
(3) Implement a schedule of routine maintenance for servicing and inspecting airline purification panels and changing filters and cartridges as necessary.
e. The Fire Department will:
(1) Provide training for firefighters using Respiratory Protection Equipment (RPE) and respirator specialists in coordination with the Installation Respirator Specialist FCFSSO and Preventive Medicine Service as outlined in AR 11-34. Training includes the following:
(a) Handling, use, and maintenance of respirators.
(b) Respirator selection based on the contaminant in the atmosphere and the appropriate protection factor to include the approval of Industrial Hygienist of a selected respirator and cartridge.
(c) Records management.
(d) Medical and safety aspects of the program.
(e) Fitting and testing of respirators.
(f) Coordinating with respirator specialists to inspect monthly the emergency use respirators and SCBAs.
(g) Being available for emergency situations where a SCBA would be required to enter a contaminated atmosphere.
f. Garrison Safety Office Manager will:
(1) Evaluate, annually, the RPP IAW CFR 1910.134 and review SOPs during the annual Standard Army Safety and Occupational Health Inspections (SASOHI).
(2) Perform work site inspections to determine the type of RPE best suited for the task involved. Safety Manager requests the Industrial Hygienist perform surveys where personnel suspect there is hazards to health.
(3) Conduct random inspections to ensure respirator specialists maintain records of monthly inspection conducted on emergency use respirators and SCBA.
g. MEDDAC, Preventive Medicine will:
(1) Conduct a medical examination/evaluation on personnel who are identified to wear a respirator. Contact the Occupational Health (OH) clinic for an appointment.
(2) Notify the IRPPM and CPAC when an employee is unable to pass a medical examination.
(3) Provide technical guidance and actively assist the IRPPM in meeting program- training requirements.
(4) Assist the safety manager in reviewing the RPP and conducting on site evaluations.
(5) Provide training to the IRS.
h. CPAC will:
(1) Refer personnel considered for employment, requiring the use of RPE, to the OH Clinic for a pre-employment physical examination.
(2) Assist installation managers in reassigning employees required to wear RPE, who are unable to do so properly, as determined by the OH Clinic.
i. Commanders, directors, and supervisors appoint a unit respiratory protection manager who will:
(1) Ensure a Health Hazard Assessment is conducted and posted, of existing, new, or modified operations, regarding respiratory protection.
(2) Fund and issue RPE to personnel who have successfully completed medical and fit testing requirements.
(3) Ensure workers use respirators IAW this regulation and local SOPs
(4) Ensure all respirator users and their supervisors receive annual respirator training.
(5) Ensure scheduling of medical examination for all respirator users as required for that specific hazard(s). Ensure scheduling of fit-tests by the IRS.
(6) Coordinate with the IRS, who shall ensure that employees using a tight-fitting face piece respirator pass an appropriate qualitative fit test (QLFT) or quantitative fit test (QNFT) prior to initial use of the respirator or whenever a different respirator face piece (size, style, model, or make) is used and at least annually thereafter.
(7) Maintain all records pertaining to respirator training, fit-testing, employee exposure to respiratory hazards such as welding fumes and HM/HW spills IAW AR 25-400-
g. Perform a respirator fit-check per manufacturer’s instructions when donning a respirator.
h. Upon detecting an odor from the work process, develop difficult breathing, or suspect a leak, while using a respirator, leave the work area without delay. Do not reenter until you have resolved the problem, either by replacing cartridges, restoring airflow, or other means, as necessary.
i. When temporarily removing respirators during breaks in work operations, move away from the work area to prevent worker exposure and to keep the inside of the respirator face-piece clean. Protect respirators from contamination before redonning.
j. Clean, disinfect, and return respirators to the storage facility after each use.
4-8. Respirator Inspection. Respirator users inspect all respirators in accordance with manufacturer’s instructions.
4-9. Respirator Cleaning and Disinfecting. Clean and disinfect respirators after each use.
4-10. Respirator Storage.
a. Store clean respirators in sealed plastic bags, away from sunlight, heat, extreme cold, excessive moisture, or damaging chemicals. Keep the storage area clean and sanitary.
b. Store respirators in such a way as to prevent crushing that can result in deformation of the face-piece or exhalation valve.
4-11. Repair and Maintenance. The IRS will:
a. Perform respirator assembly and repair, as authorized.
b. Not attempt to replace components or to make adjustments or repairs beyond the manufacturers' recommendations or with parts from different manufacturers.
4-12. Medical Examinations.
a. A physician or occupational health nurse, under the direction of a physician must medically evaluate all respirator users to ensure that they can wear a respirator and perform the required work without adverse health effects.
b. An optometrist must fit users of prescription eyewear with respirator spectacles when the users wear full-face respirators.
4-13. Training. The IRS or unit respiratory protection program manager will.
a. Instruct and train respirator users and their supervisors in the proper use of respirators and users limitations.
b. Include the following in annual training:
(1) Types of hazardous atmospheres and their effects on worker health.
(2) Respirator selection.
(3) Respirator use and limitations.
(4) Respiratory Protection Program requirements.
(5) Respirator inspection procedures.
(6) Respirator donning and fit-testing procedures.
(7) Provide and document effective training to employees who are required to use respirators as mandated by the standard. The training must be comprehensive, understandable, and recur annually as required by the standard and more often, if necessary.
4-14. Fit-Testing. IRS/local respiratory protection managers conduct fit testing IAW AR 11- 34 and 29 CFR 1910.139 and manufacturers instructions, only after OH approval.
4-15. Program Evaluation. USAFCOEFS respiratory program manager or IRS will conduct an annual program evaluation to determine program effectiveness using the Respiratory Protection Program Inspection Guide and take appropriate actions to correct any discrepancies.
Chapter 5 Confined Space Entry Program.
5-1. Purpose. To implement the USAFCOEFS Confined Space Entry Program as required by AR 385-10, DA PAM 385-10, and 29 CFR 1910.146.
5-2. Scope.
a. This program applies to all military and Civilian units assigned or attached to USAFCOEFS with personnel required to enter a permit required, confined space to include aircraft fuel cells.
b. This program does not apply to contractors or contract workers working in government facilities. Contractors must, however, be informed of known permit spaces and permit space entry requirements, any identified hazards, the Army's experience with the space, and precautions or procedures to be followed when in or near permit required spaces.-