
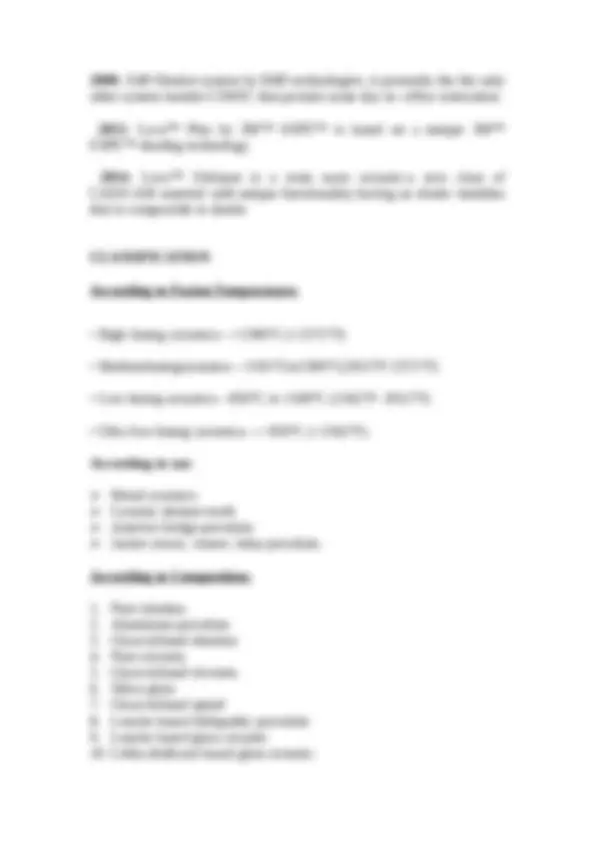
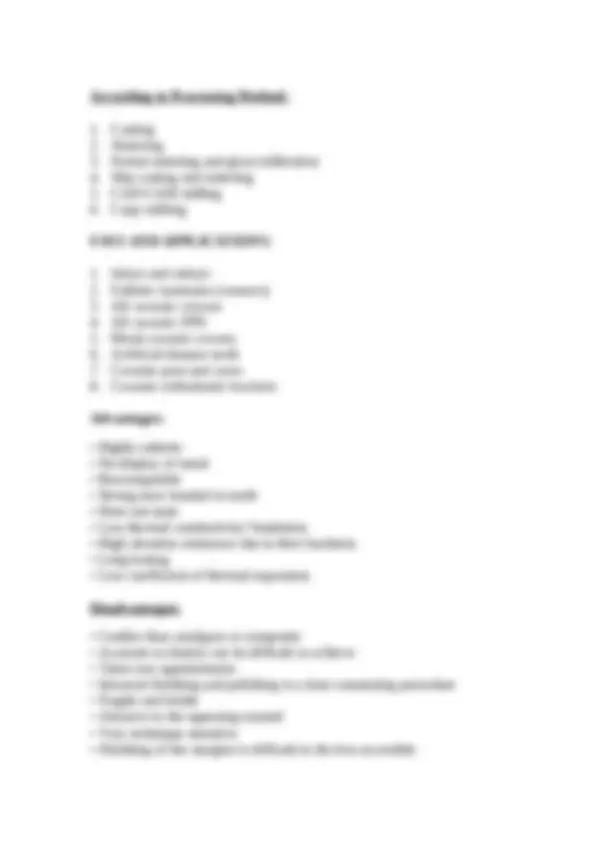
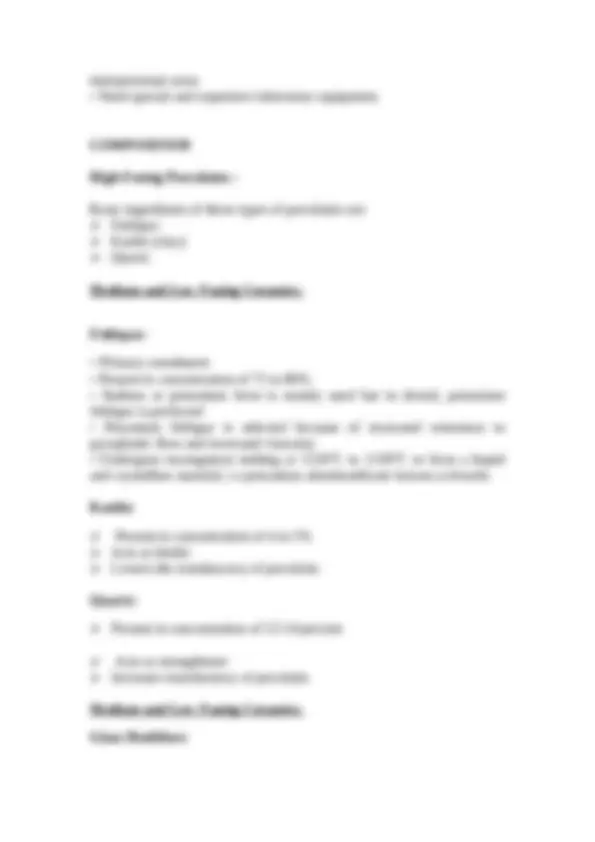
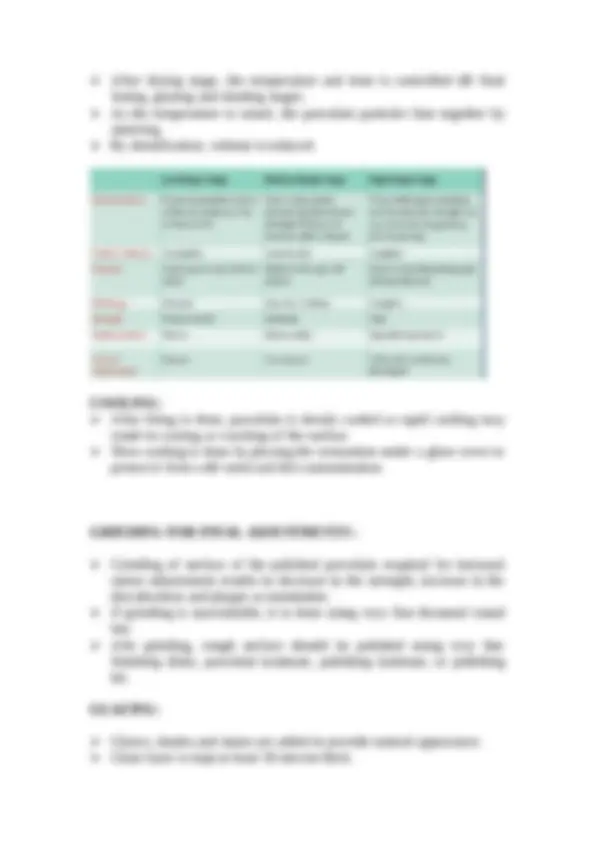
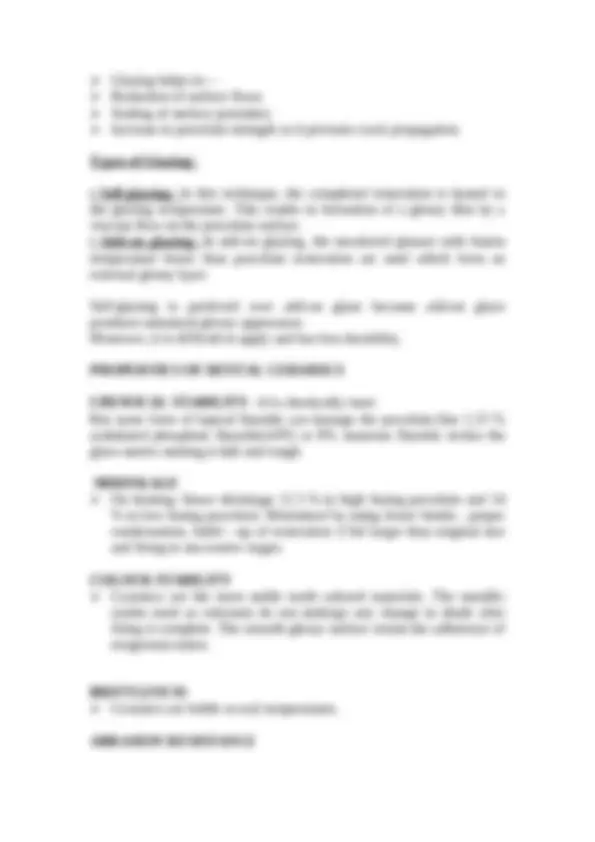
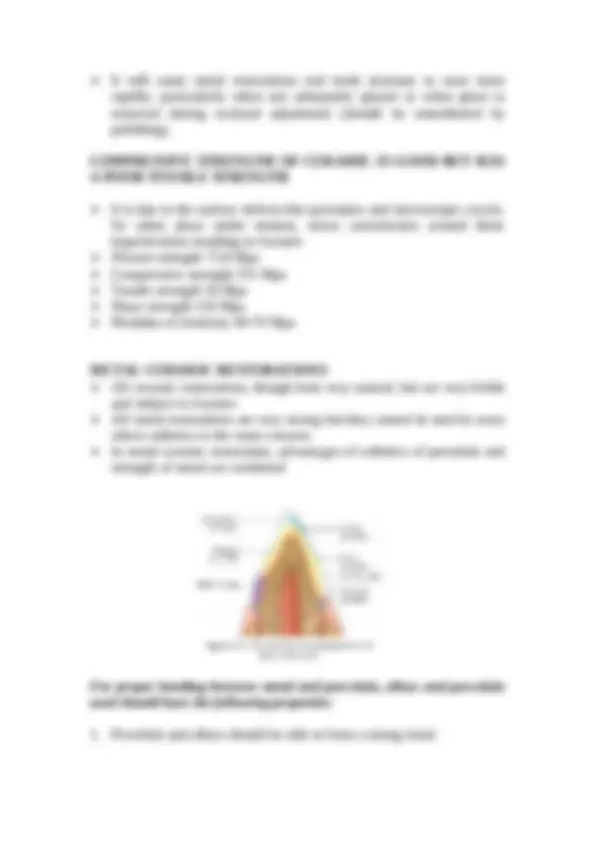
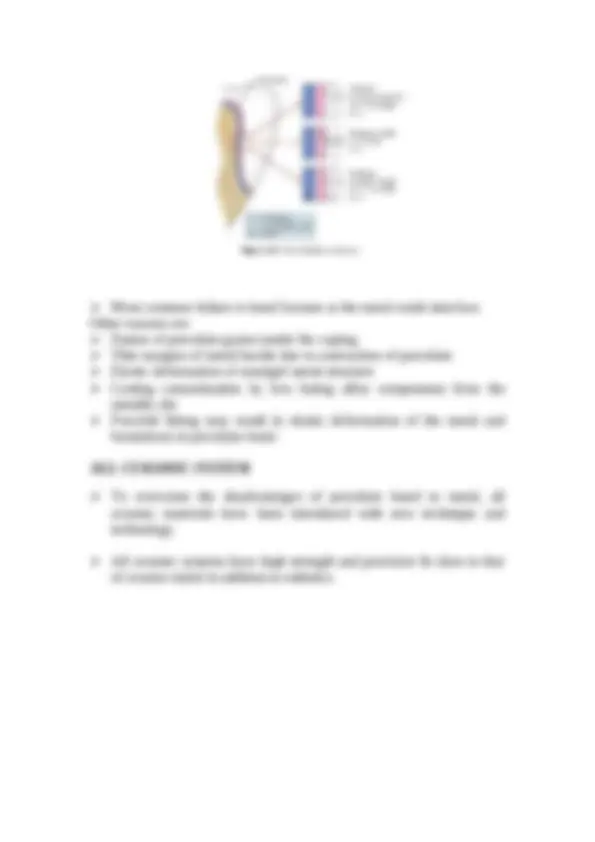
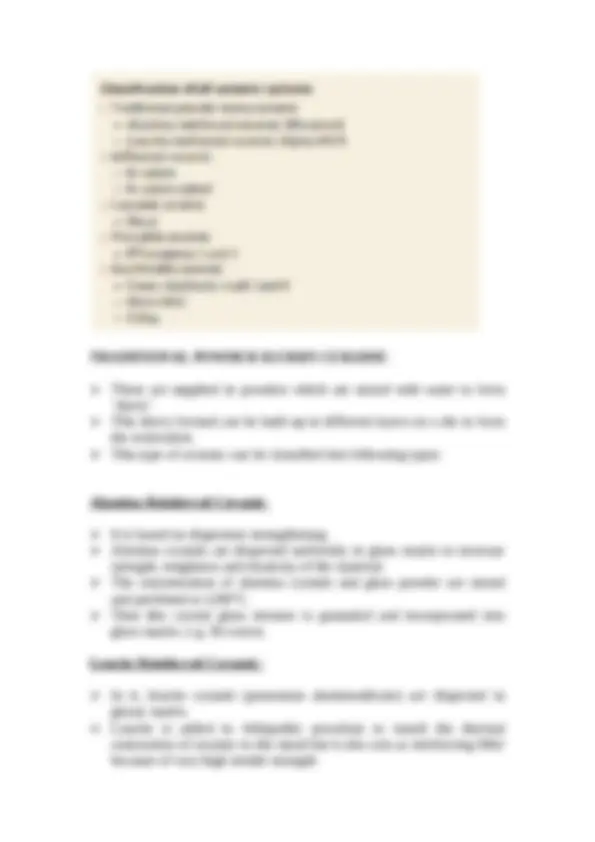
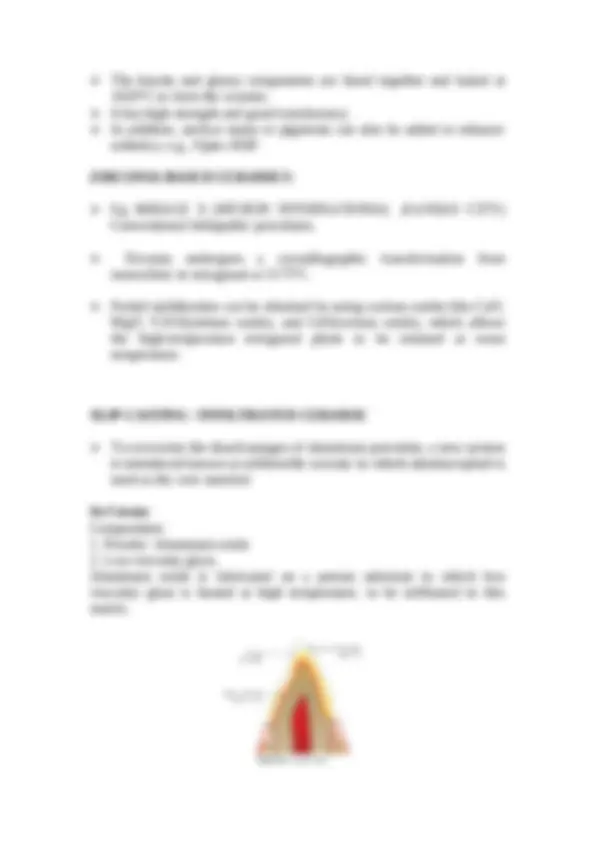
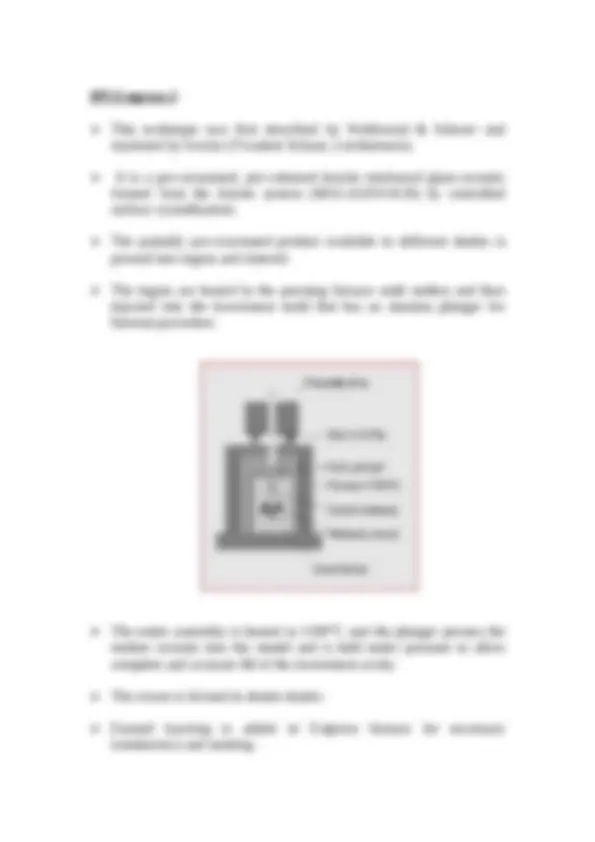
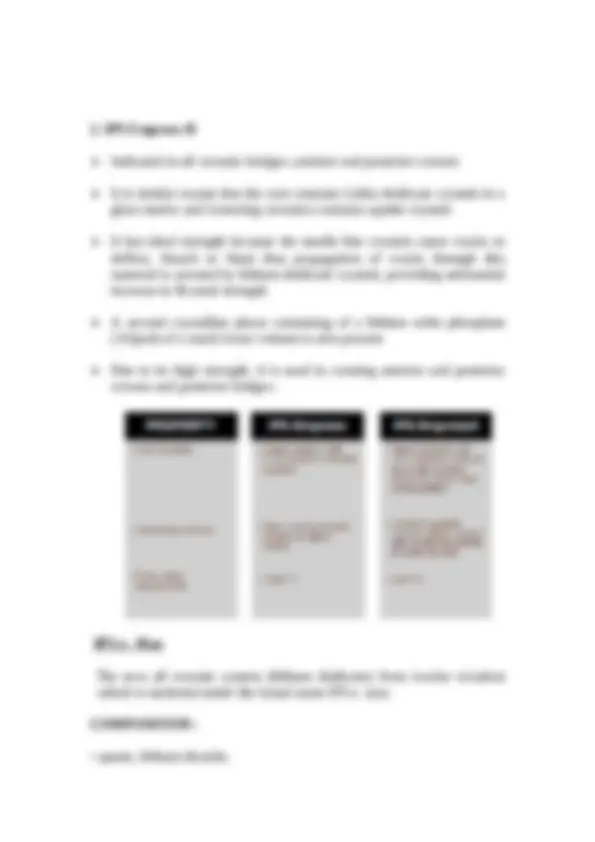
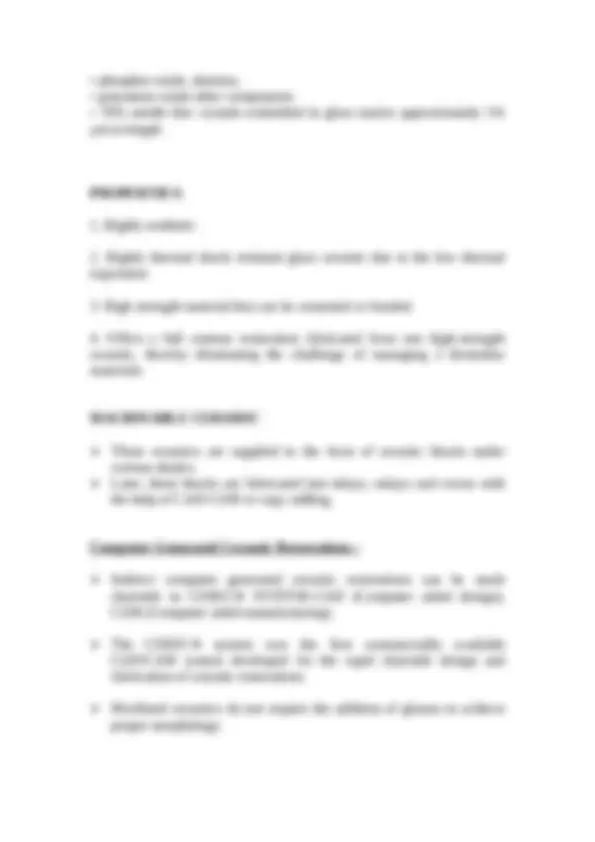
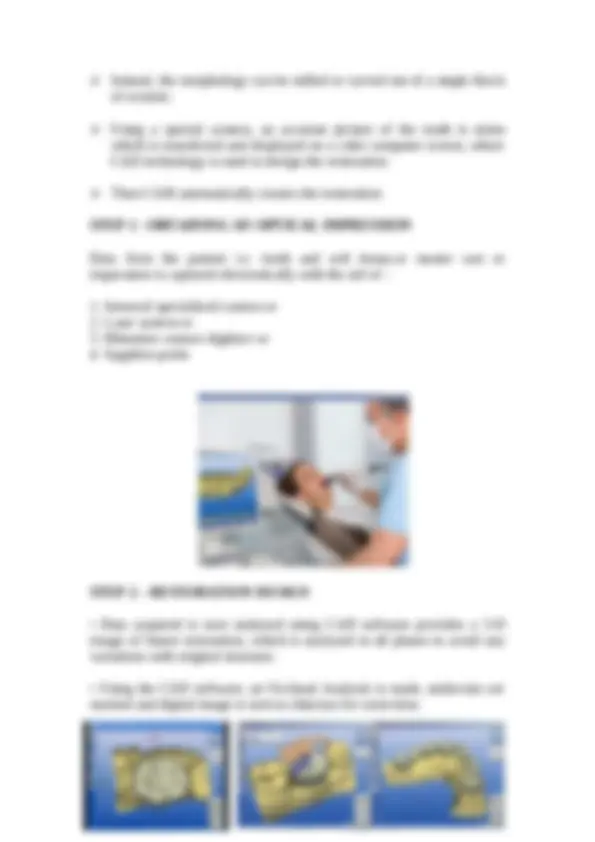
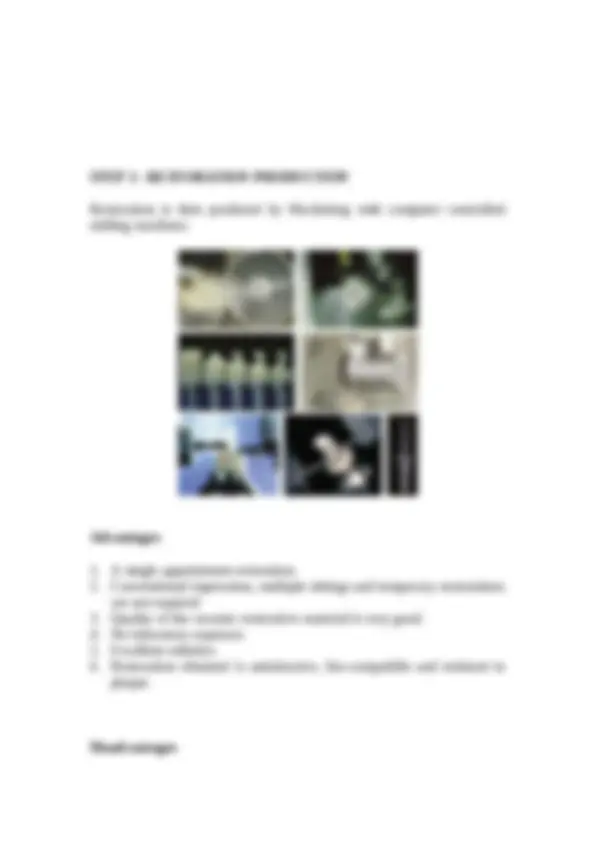
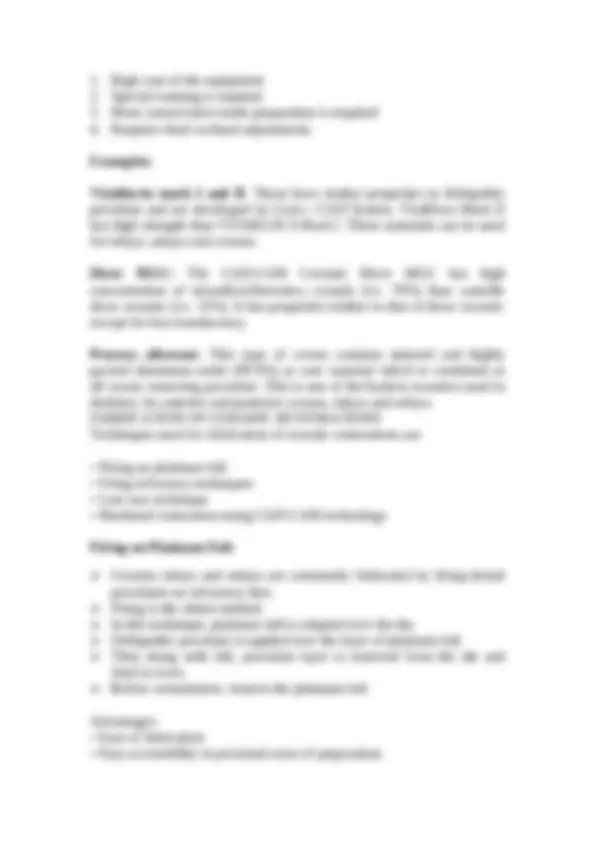
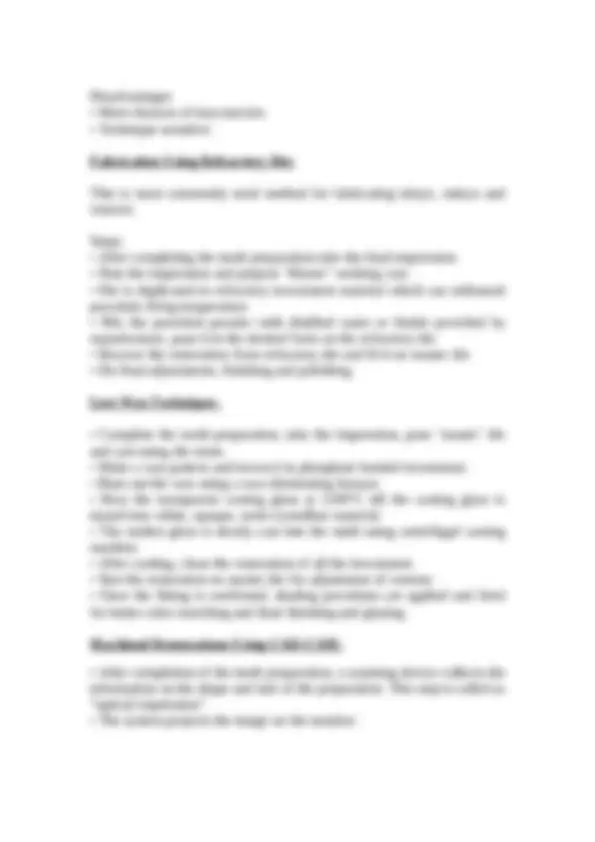
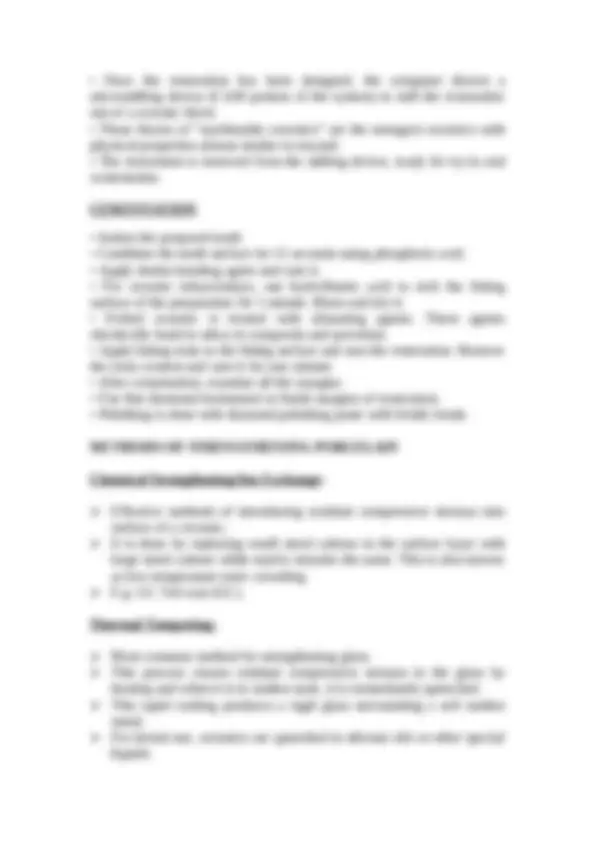
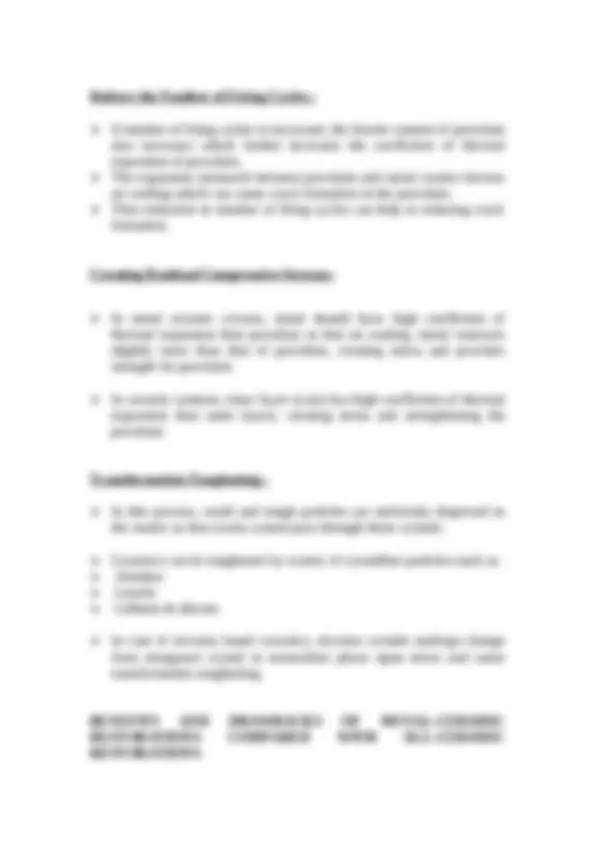
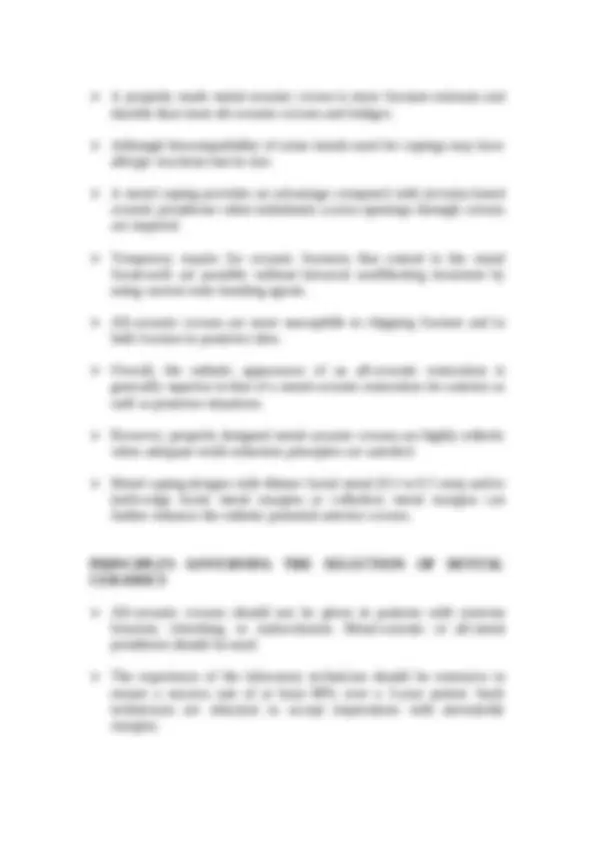
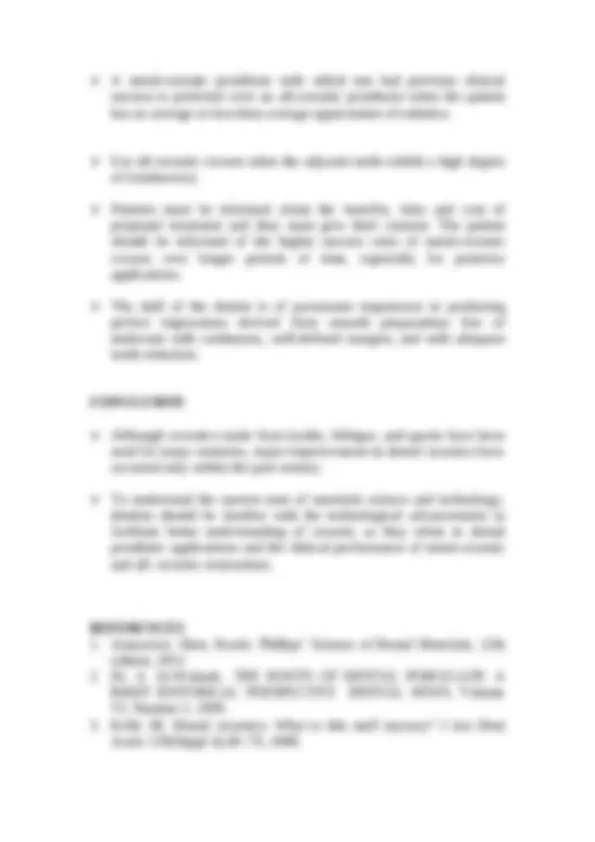
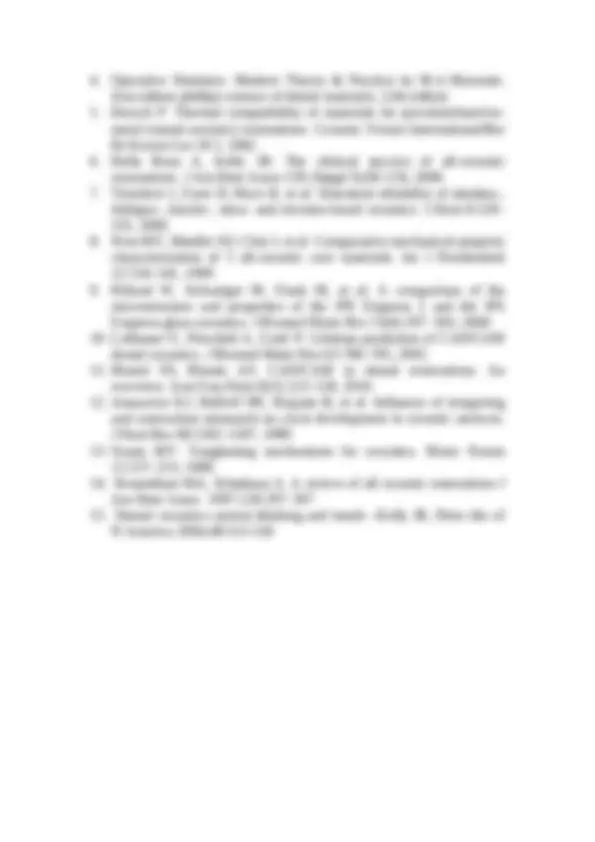
Study with the several resources on Docsity
Earn points by helping other students or get them with a premium plan
Prepare for your exams
Study with the several resources on Docsity
Earn points to download
Earn points by helping other students or get them with a premium plan
Community
Ask the community for help and clear up your study doubts
Discover the best universities in your country according to Docsity users
Free resources
Download our free guides on studying techniques, anxiety management strategies, and thesis advice from Docsity tutors
DENTAL CERAMICS MATERIAL USED IN RESTORATIVE DENTISRTY AS INDIRECT RESTORATION OF CARIOUS TOOTH WITH ESXTENSIVE LOSS OF TOOTH STRUCTURE
Typology: Study notes
1 / 29
This page cannot be seen from the preview
Don't miss anything!
Dental ceramics are known for their natural appearance and their durable chemical, mechanical and optical properties. The word “ceramic” is derived from the Greek word “Keramos” which means “potter’s clay”. Dental ceramics are non-metallic, inorganic structures, primarily containing compounds of oxygen with one or more metallic or semi- metallic elements (aluminium, boron, calcium, lithium, magnesium, zirconium, potassium etc.) These materials are a part of systems designed with the purpose of producing dental prostheses that in turn are used to replace missing or damaged dental structures. DEFINITIONS CERAMIC: Inorganic, nonmetallic material composed of metallic or semi-metallic oxides, phosphates, sulphates or other inorganic compounds. DENTAL CERAMIC : A specially formulated ceramic material that exhibits adequate strength, durability and color that is used intraorally to restore anatomic form and function and esthetics. DENTAL PORCELAIN : A ceramic produced by sintering a mixture of feldspar, silica, alumina and other metal oxides, pigments and opacifying agents. FELDSPATHIC PORCELAIN : A specially formulated dental porcelain that contains leucite crystals (KAlSi2O6) in a glass matrix that is used for veneering the metal framework of metal-ceramic prostheses. ZIRCONIA: A partially stabilized zirconium oxide, usually in a tetragonal phase that is used primarily as a core for dental prostheses.
1728 Pierre Fauchard- Suggested the use of porcelain in dentistry 1789 Duchateau and DeChemant- Introduced porcelain tooth material for bridge work and denture 1808 Fonzi- Terra-metallic porcelain (held in place by platinum foil) 1903 Dr Charles Land- Introduction of first ceramic crown using platinum foil matrix and high fusing porcelain 1962 Weinstein- Introduction of porcelain fused to metal restorations 1965 Mclean and Hughes- Improved the fracture resistance by introducing aluminous porcelain 1984 Adair and Grossman- Introduction of castable glass ceramic (Dicor) 1985 – First CAD/CAM crown was publically milled and installed in the mouth. Late 1990’s – IPS Empress 2, a second generation pressable ceramic made from lithium-disilicate frame work with an apatite layered ceramic was introduced. 1999 – IPS SIGN (Ivoclar AG), a feldspar-free fluorapatite glass ceramic system for use in metal-ceramics was presented. 2001 - CERCON from Dentsply International introduced dental restorations from sintered yttrium stabilized zirconia based ceramic core material 2006 -Lithium disilicate re-emerged in 2006 as a pressable ingot and partially crystalized milling block 2007 - ITERO by Cadent as the first digital impression system for conventionally manufactured crown and bridges.
According to Processing Method:
interproximal areas
This helps in maximum incorporation of porcelain powder and proper condensation of porcelain powder particles. Wet porcelain powder condensation can be done by the following methods: Vibration method: Mild vibrations help in packing the wet powder densely. This is most useful method in removing excess water from the mix. Spatulation method: In this method, a small spatula is used to smoothen the wet powder and the wet particles condense together by which the excess water comes to the surface from where it can be removed. Brush technique: In this method, dry porcelain powder is added to the surface with the help of a brush which absorbs the extra water, making the condensation of wet particles. FIRING OF PORCELAIN: Stages of Firing Porcelain undergoes different stages during firing known as bisque stages:
After drying stage, the temperature and time is controlled till final fusing, glazing and shading stages. As the temperature is raised, the porcelain particles fuse together by sintering. By densification, volume is reduced. COOLING: After firing is done, porcelain is slowly cooled as rapid cooling may result in crazing or cracking of the surface. Slow cooling is done by placing the restoration under a glass cover to protect it from cold wind and dirt contamination. GRINDING FOR FINAL ADJUSTMENTS : Grinding of surface of the polished porcelain required for intraoral minor adjustments results in decrease in the strength, increase in the discoloration and plaque accumulation. If grinding is unavoidable, it is done using very fine diamond round bur. Afte grinding, rough surface should be polished using very fine finishing disks, porcelain laminate, polishing laminate, or polishing kit. GLAZING: Glazes, shades and stains are added to provide natural appearance. Glaze layer is kept at least 50 micron thick.
It will cause metal restorations and tooth structure to wear more rapidly; particularly when not adequately glazed or when glaze is removed during occlusal adjustment (should be smoothened by polishing). COMPRESSIVE STRENGTH OF CERAMIC IS GOOD BUT HAS A POOR TENSILE STRENGTH It is due to the surface defects like porosities and microscopic cracks. So when place under tension, stress concentrates around these imperfections resulting in fracture. Flexure strength 75.8 Mpa Compressive strength 331 Mpa Tensile strength 34 Mpa Shear strength 110 Mpa Modulus of elasticity 60-70 Mpa METAL CERAMIC RESTORATIONS All ceramic restorations, though look very natural, but are very brittle and subject to fracture. All metal restorations are very strong but they cannot be used in areas where esthetics is the main concern. In metal ceramic restoration, advantages of esthetics of porcelain and strength of metal are combined. For proper bonding between metal and porcelain, alloys and porcelain used should have the following properties:
Most common failure is bond fracture at the metal oxide interface. Other reasons are: Fusion of porcelain grains inside the coping Thin margins of metal buckle due to contraction of porcelain Elastic deformation of nonrigid metal structure Casting contamination by low fusing alloy components from the metallic die Forceful fitting may result in elastic deformation of the metal and breakdown in porcelain bond. ALL CERAMIC SYSTEM To overcome the disadvantages of porcelain fused to metal, all ceramic materials have been introduced with new technique and technology. All ceramic systems have high strength and precision fit close to that of ceramo-metal in addition to esthetics.
These are supplied in powders which are mixed with water to form ‘slurry’. This slurry formed can be built up in different layers on a die to form the restoration. This type of ceramic can be classified into following types: Alumina Reinforced Ceramic It is based on dispersion strengthening. Alumina crystals are dispersed uniformly in glass matrix to increase strength, toughness and elasticity of the material. The concentration of alumina crystals and glass powder are mixed and prefritted at 1200°C. Then this crystal glass mixture is grounded and incorporated into glass matrix, e.g. Hi-ceram. Leucite Reinforced Ceramic: In it, leucite crystals (potassium aluminosilicate) are dispersed in glassy matrix. Leucite is added in feldspathic porcelain to match the thermal contraction of ceramic to the metal but it also acts as reinforcing filler because of very high tensile strength.
Procedure : Alumina powder is mixed with water to form slurry known as ‘Slip’ which is painted on die. It leaves a layer of solid alumina on the surface. Sintering is done at 1120°C for 10 hours to form porous core. Glass is selected and applied on the porous core and firing is done at 1100°C for 3 to 5 hours. The molten glass infiltrates by capillary action into core. This results in high strength composite structure, i.e. In ceram. In Ceram Spinel: In this spinel (aluminum and magnesium oxide) is used as the core material. It has better translucency than In ceram. It can be used for both anterior and posterior crowns. CASTABLE CERAMIC Castable ceramic was first introduced in 1984. In this, glass ceramic is modified into the desired shape and size as a glass and heat treatment is given to induce crystallization. The process of crystallization is known as ceramming. In 1984, castable ceramic was marketed under the trade name DICOR. Composition: After ceramming, the material contains:
Advantages :
2. IPS Empress II Indicated in all ceramic bridges ,anterior and posterior crowns It is similar except that the core contains Lithia disilicate crystals in a glass matrix and veneering ceramics contains apatite crystals It has ideal strength because the needle like crystals cause cracks to deflect, blanch or blunt thus propagation of cracks through this material is arrested by lithium disilicate crystals, providing substantial increase in flexural strength. A second crystalline phase containing of a lithium ortho phosphate ( li3po4) of a much lower volume is also present Due to its high strength, it is used in creating anterior and posterior crowns and posterior bridges. IPS e. Max The new all ceramic system (lithium disilicate) from ivoclar vivadent which is marketed under the brand name IPS e .max. COMPOSITION: