
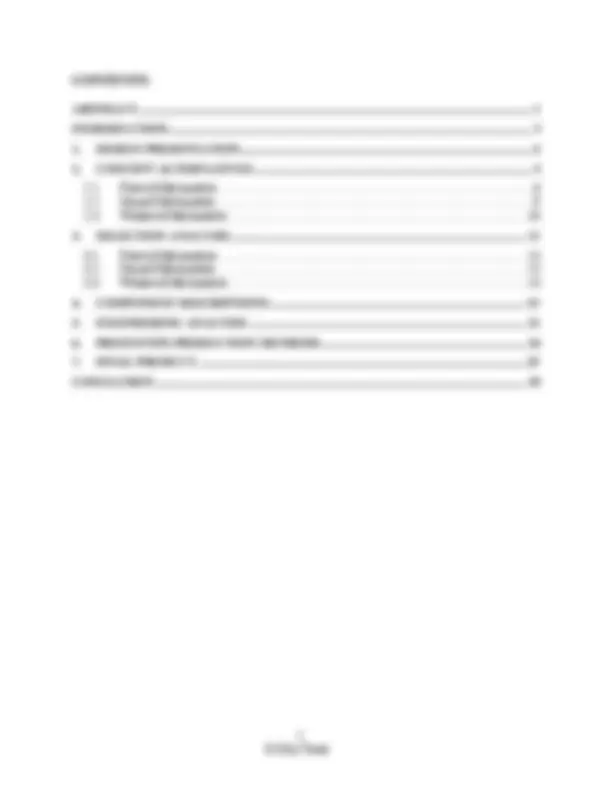
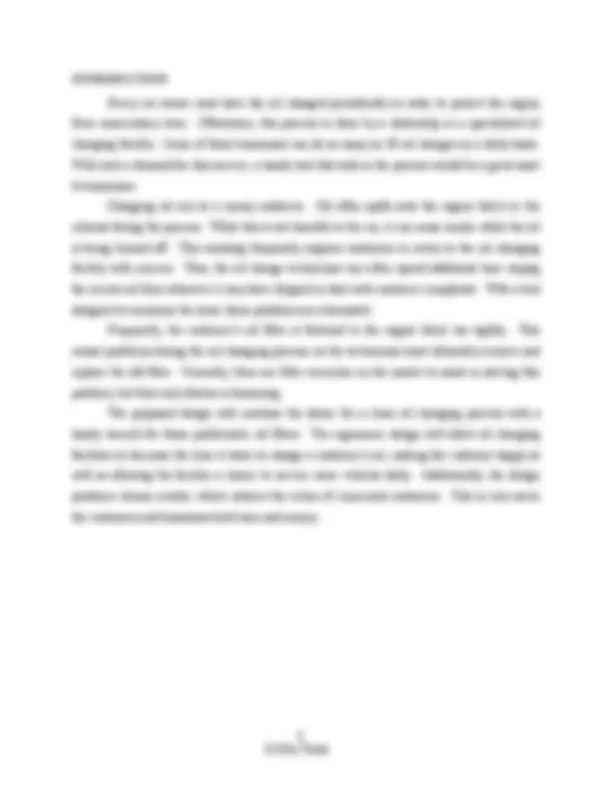
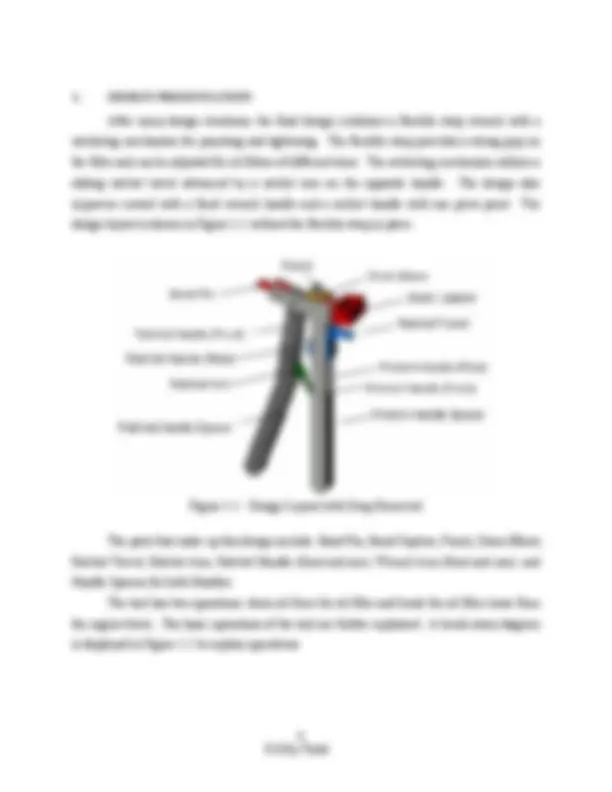
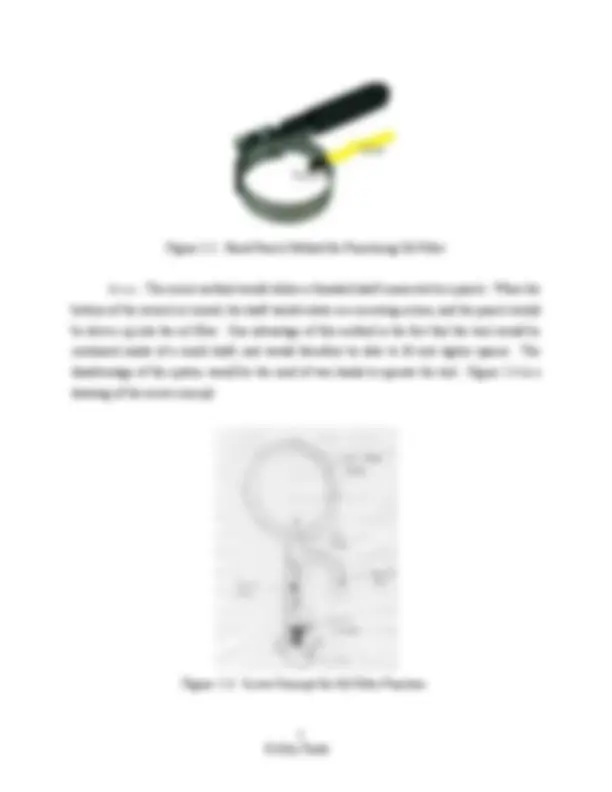
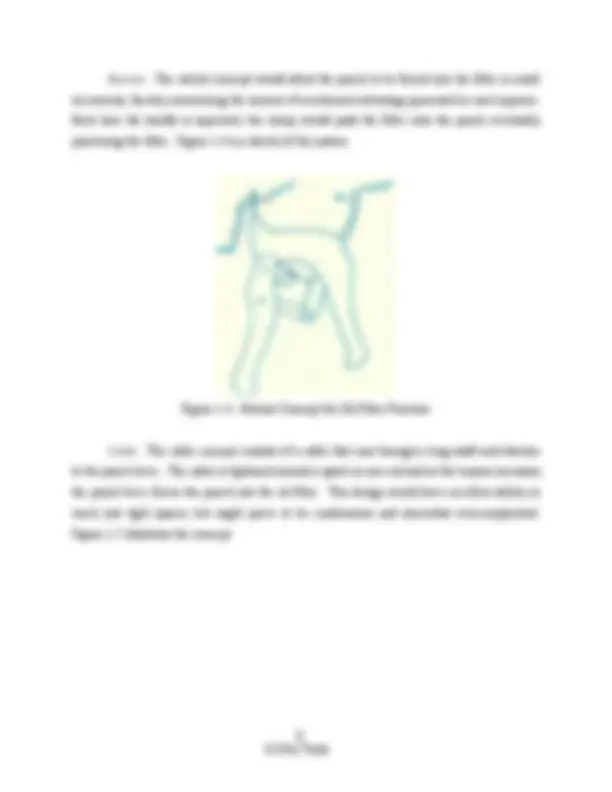
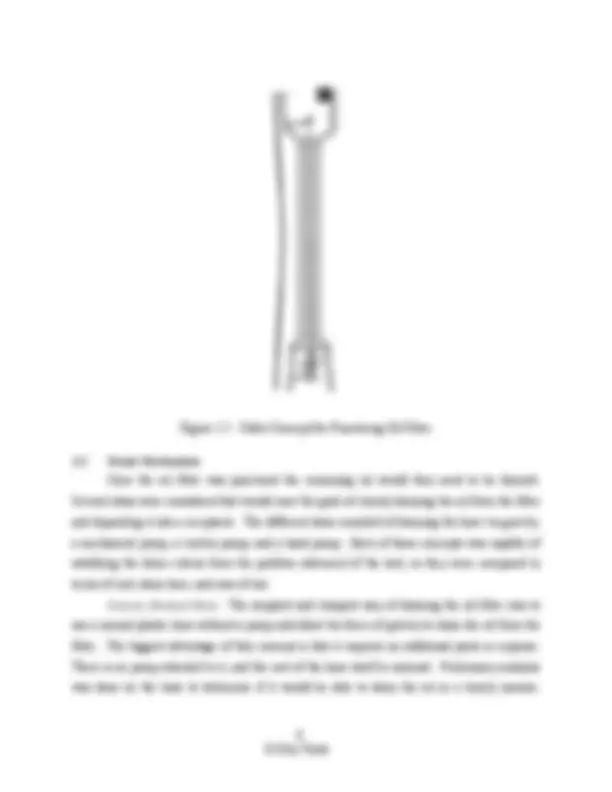
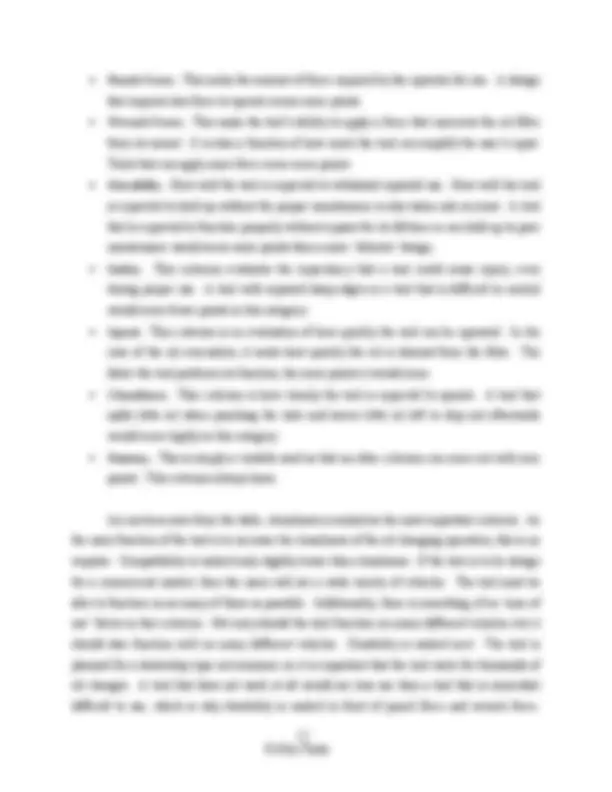
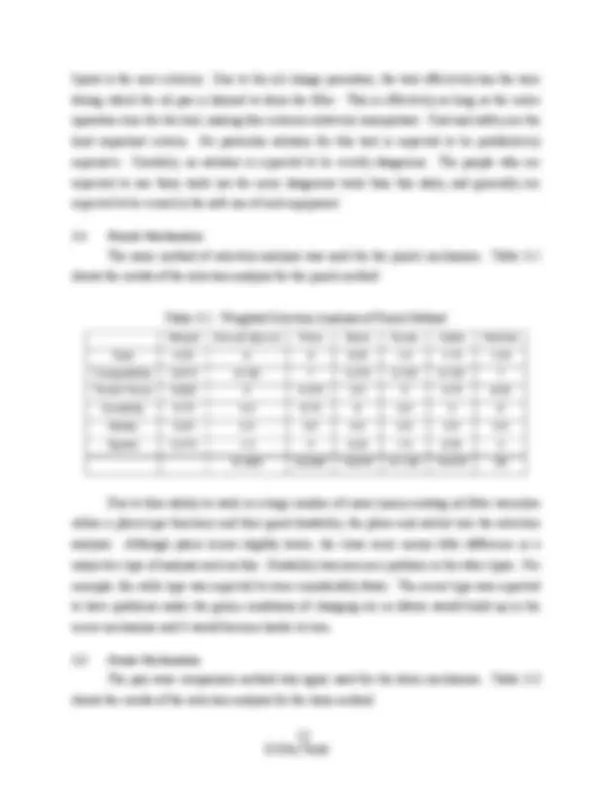
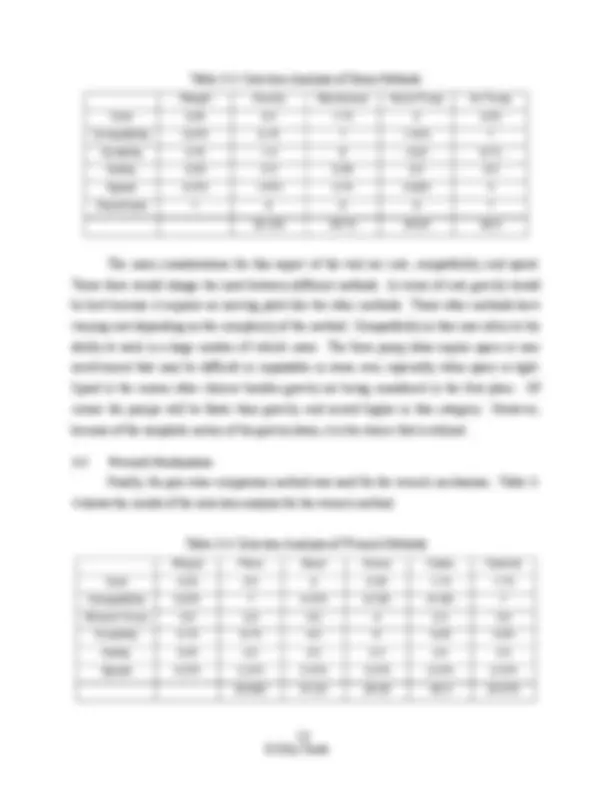
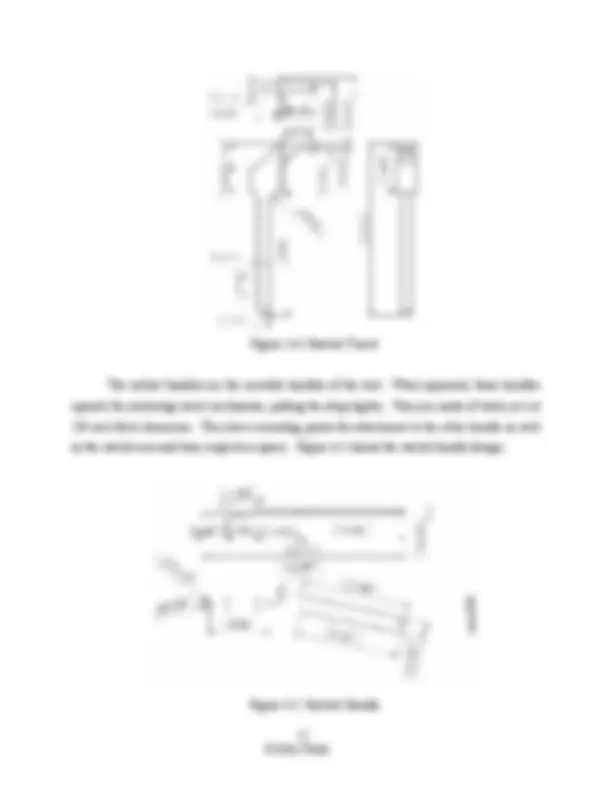
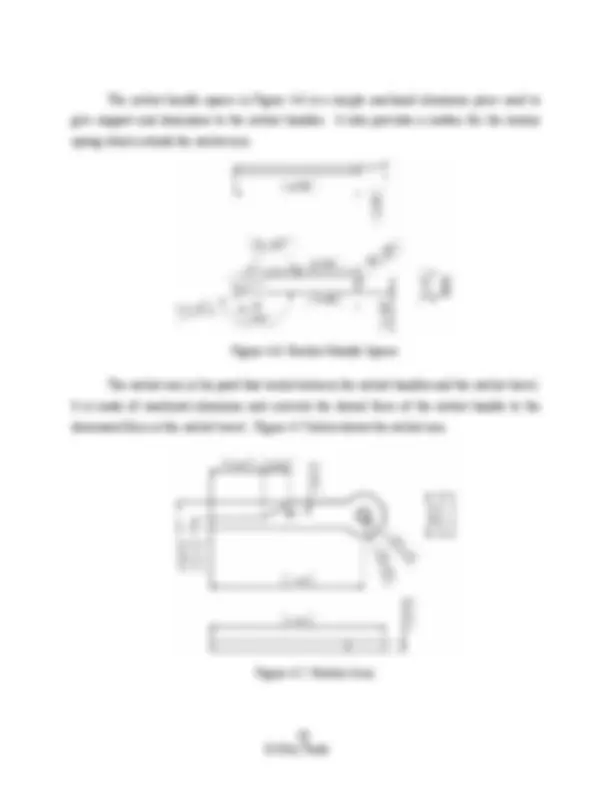
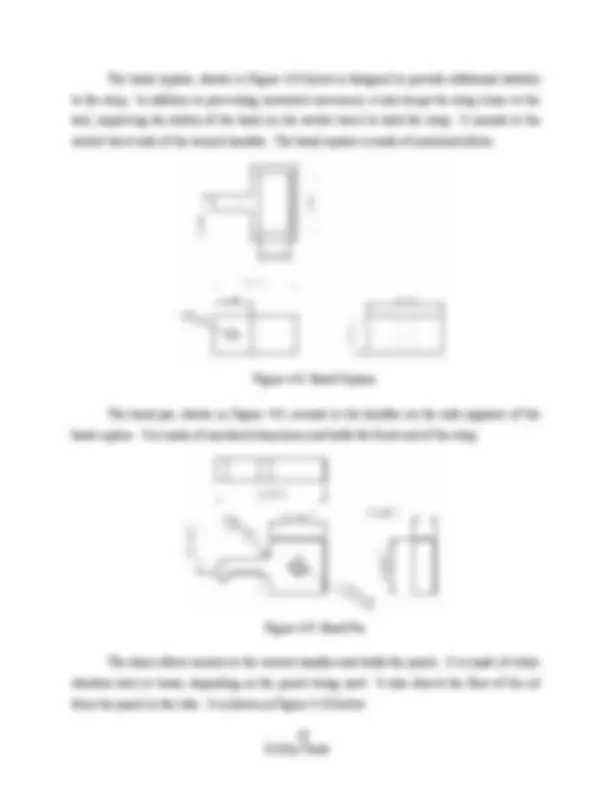
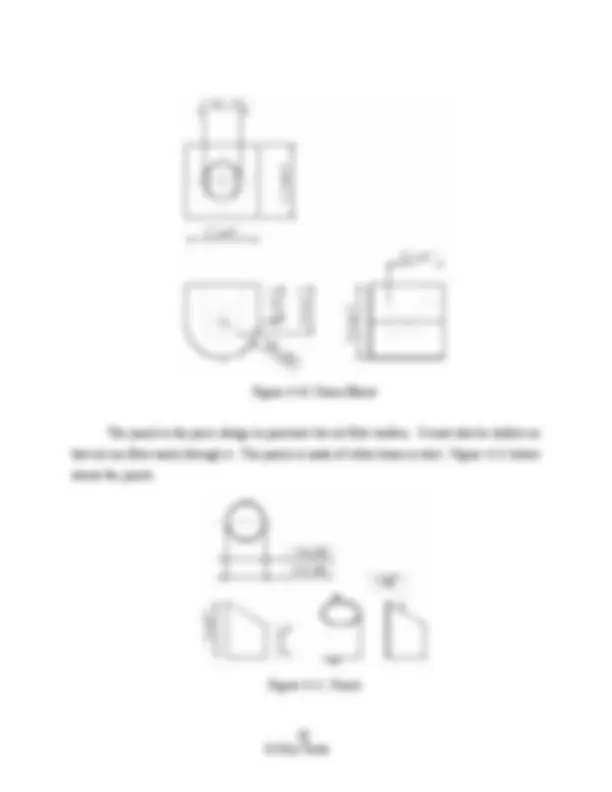
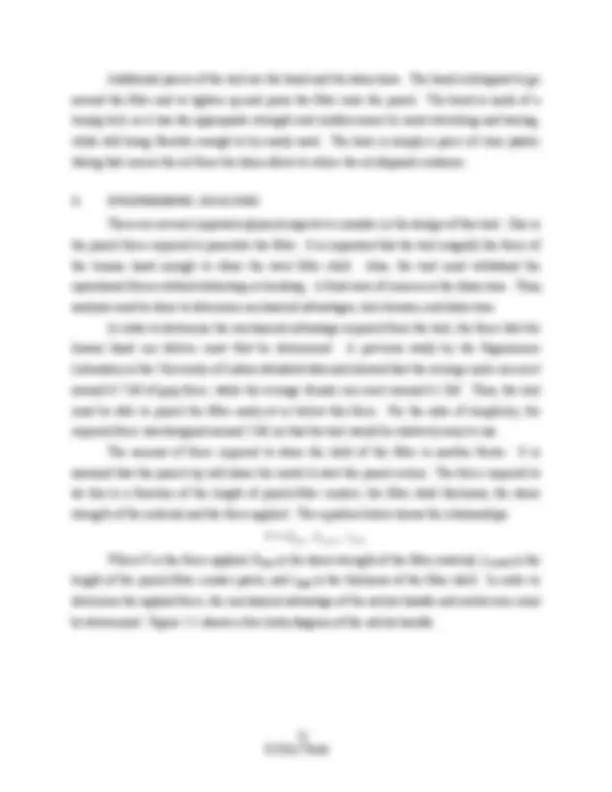
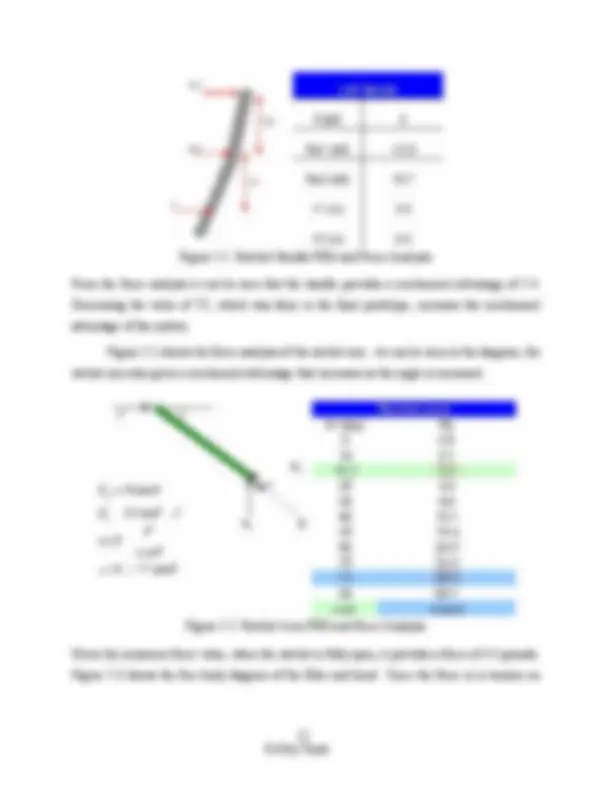
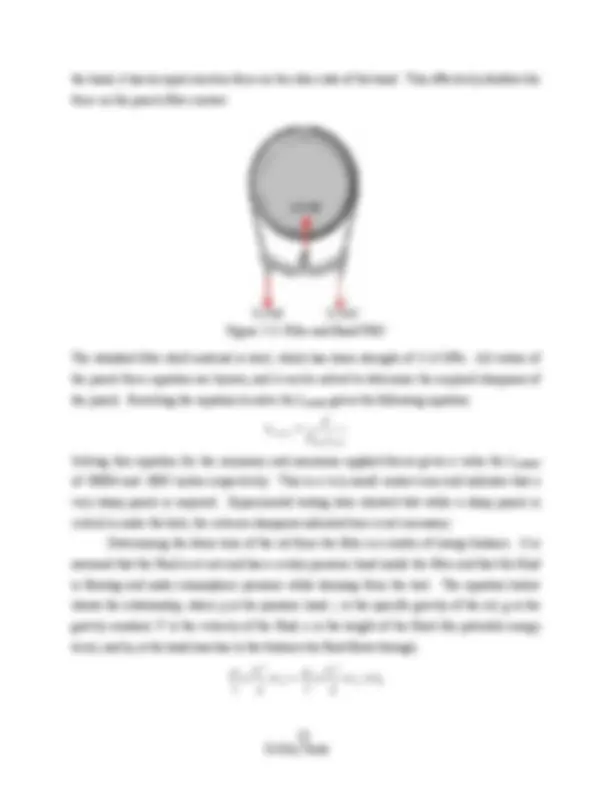
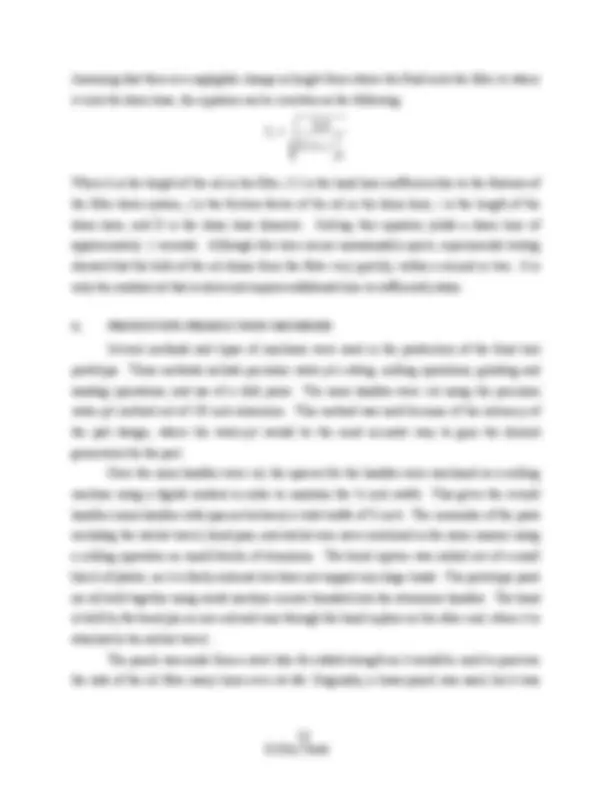
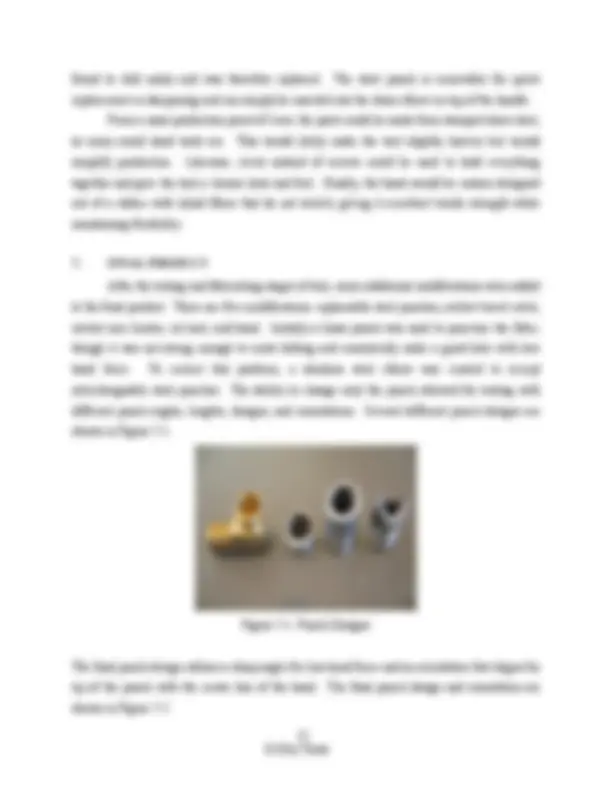
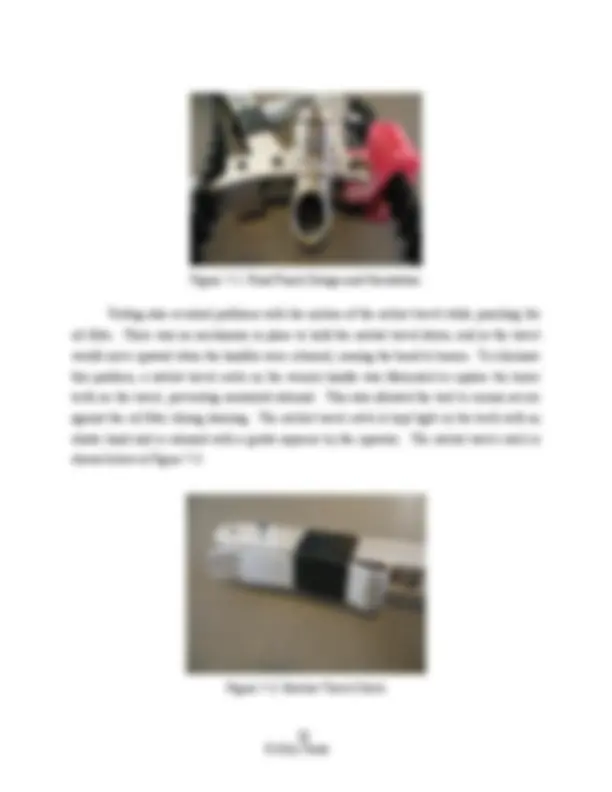
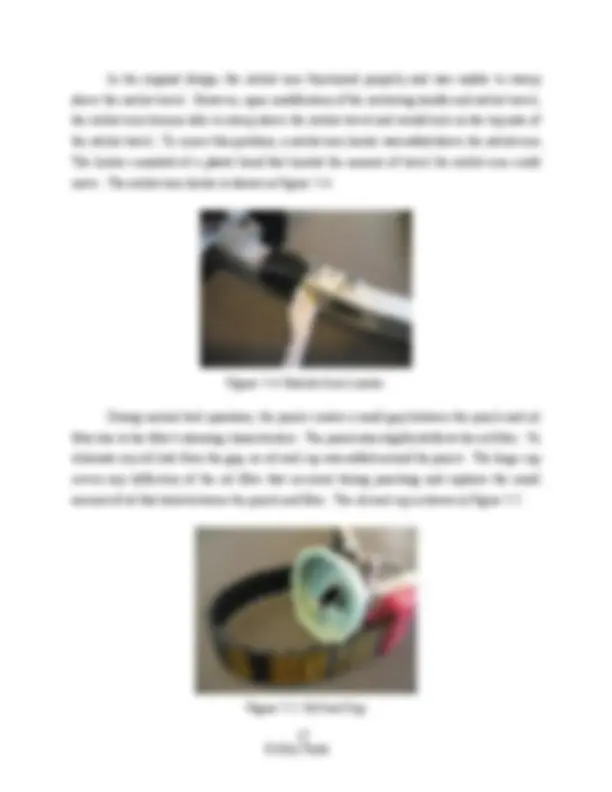
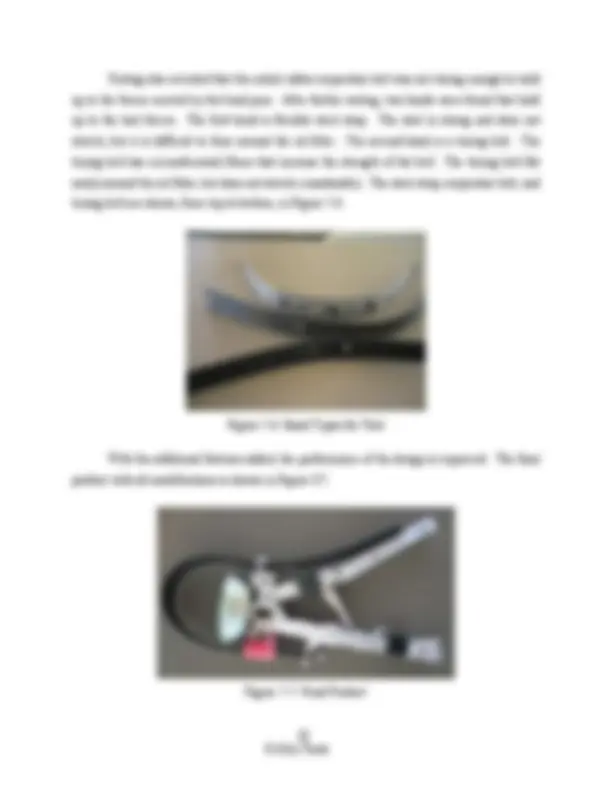
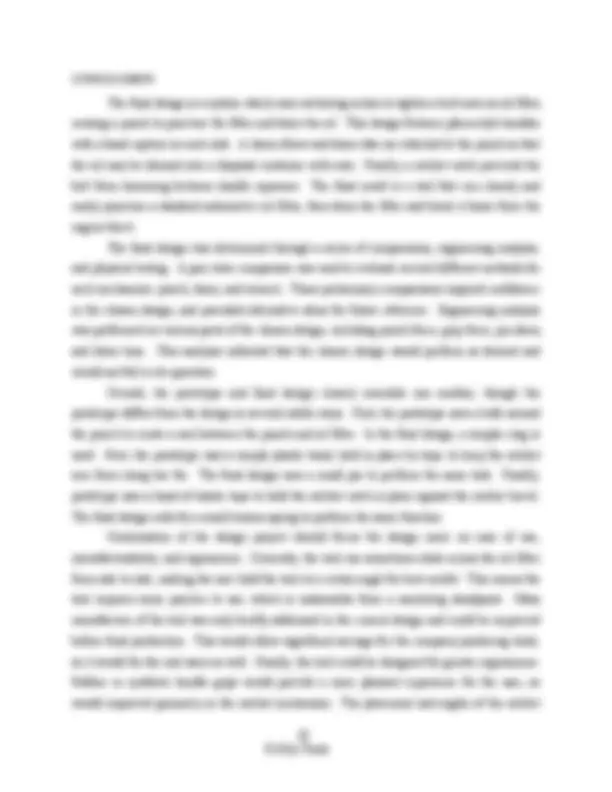
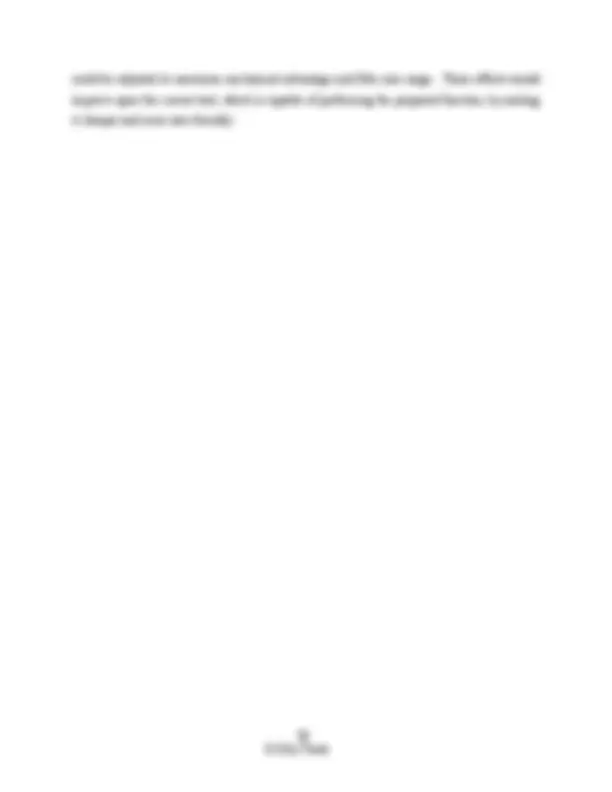
Study with the several resources on Docsity
Earn points by helping other students or get them with a premium plan
Prepare for your exams
Study with the several resources on Docsity
Earn points to download
Earn points by helping other students or get them with a premium plan
Community
Ask the community for help and clear up your study doubts
Discover the best universities in your country according to Docsity users
Free resources
Download our free guides on studying techniques, anxiety management strategies, and thesis advice from Docsity tutors
Material Type: Paper; Professor: Lipkin; Class: Capstone Design; Subject: Mechanical Engineering; University: Georgia Institute of Technology-Main Campus; Term: Spring 2006;
Typology: Papers
1 / 31
This page cannot be seen from the preview
Don't miss anything!
Most cars need to have their oil changed about every 3000 miles. This routine service is provided by car dealerships and is also offered by service stations such as Jiffy-Lube, which specialize in quick oil changes. These types of establishments perform dozens of oil changes each day, and even though the process of changing oil is straightforward, there are several routine problems. During an oil change, most of the oil is first drained out of the oil pan, which is typically at the lowest part of the car and is easily accessible. The oil filter, however, is not always in the most convenient place. When the oil filter is removed, the oil that is trapped inside may leak out onto the underpinnings of the car. This creates two main problems for dealerships and oil change facilities. First, the oil can get on the engine block and then burn or smoke when the engine is running, causing a bad odor in the car. Second, the oil can also drip off of the engine block onto the shop floor, creating a slippery mess. Even worse, the oil can drip on the customerâs garage floor. This is undesirable for oil change providers because it leads to customer dissatisfaction and unnecessary work. The objective of this design project is to create a tool which will reduce or eliminate the oil that leaks out of the filter during oil changes, thus eliminating the businessesâ extra hassle and customer complaints.
Every car owner must have the oil changed periodically in order to protect the engine from unnecessary wear. Oftentimes, this process is done by a dealership or a specialized oil changing facility. Some of these businesses can do as many as 30 oil changes on a daily basis. With such a demand for this service, a handy tool that aids in the process would be a great asset to businesses. Changing oil can be a messy endeavor. Oil often spills onto the engine block or the exhaust during the process. While this is not harmful to the car, it can cause smoke while the oil is being burned off. This smoking frequently inspires customers to return to the oil changing facility with concern. Thus, the oil change technicians can either spend additional time wiping the excess oil from wherever it may have dripped or deal with customer complaints. With a tool designed to minimize the mess, these problems are eliminated. Frequently, the customerâs oil filter is fastened to the engine block too tightly. This causes problems during the oil changing process, as the technicians must ultimately remove and replace the old filter. Currently, there are filter wrenches on the market to assist in solving this problem, but their only feature is loosening. The proposed design will combine the desire for a clean oil changing process with a handy wrench for those problematic oil filters. The ergonomic design will allow oil changing facilities to decrease the time it takes to change a customerâs oil, making the customer happy as well as allowing the facility a chance to service more vehicles daily. Additionally, the design produces cleaner results, which reduces the return of concerned customers. This in turn saves the customers and businesses both time and money.
After many design iterations, the final design combines a flexible strap wrench with a ratcheting mechanism for punching and tightening. The flexible strap provides a strong grip on the filter and can be adjusted for oil filters of different sizes. The ratcheting mechanism utilizes a sliding ratchet travel advanced by a ratchet arm on the opposite handle. The design also improves control with a fixed wrench handle and a ratchet handle with one pivot point. The design layout is shown in Figure 1-1 without the flexible strap in place.
Figure 1-1. Design Layout with Strap Removed
The parts that make up this design include: Band Pin, Band Capture, Punch, Drain Elbow, Ratchet Travel, Ratchet Arm, Ratchet Handle (front and rear), Wrench Arm (front and rear), and Handle Spacers for both Handles. The tool has two operations: drain oil from the oil filter and break the oil filter loose from the engine block. The basic operations of the tool are further explained. A break-away diagram is displayed in Figure 1-2 to explain operations.
component then removes the oil inside the punctured filter. The wrench mechanism serves as a way to break the filter loose from the engine block. Several different concepts were evaluated for each mechanism.
2.1 Punch Mechanism The main objective of the punch mechanism is to puncture the side of the oil filter in a clean and reliable way. The punched hole allows any oil trapped inside the filter to drain before removal. Some of the different concepts are as follows: Pliers, Band, Screw, Ratchet and Cable. Pliers. This method consists of a simple pair of pliers with a punch attached to one or both arms of the pliers. A picture of the concept is shown in Figure 2-1.
Figure 2-1. Method for Puncturing Oil Filter with Pliers
One of the advantages of the pliers is the amount of mechanical advantage produced. Additionally, it is a very simple tool, would be easy to manufacture, and has few parts. Band. The band method consists of using an existing band type filter wrench and attaching a punch to it. The punch would have to be attached in a location where it would be able to penetrate the oil filter when the maximum clamp force is reached. Thus, this design has the disadvantage of possible filter size limitations. Figure 2-2 shows what the band idea would look like.
Figure 2-2. Band Punch Method for Puncturing Oil Filter
Screw. The screw method would utilize a threaded shaft connected to a punch. When the bottom of the wrench is turned, the shaft would rotate in a screwing action, and the punch would be driven up into the oil filter. One advantage of this method is the fact that the tool would be contained inside of a small shaft, and would therefore be able to fit into tighter spaces. The disadvantage of the system would be the need of two hands to operate the tool. Figure 2-3 is a drawing of the screw concept.
Figure 2-3. Screw Concept for Oil Filter Puncture.
Figure 2-5. Cable Concept for Puncturing Oil Filter
2.2 Drain Mechanism Once the oil filter was punctured the remaining oil would then need to be drained. Several ideas were considered that would meet the goal of cleanly draining the oil from the filter and depositing it into a receptacle. The different ideas consisted of draining the hose via gravity, a mechanical pump, a venturi pump, and a hand pump. Each of these concepts was capable of satisfying the drain criteria from the problem statement of the tool, so they were compared in terms of cost, drain time, and ease of use. Gravity Drained Hose. The simplest and cheapest way of draining the oil filter was to use a normal plastic hose without a pump and allow the force of gravity to drain the oil from the filter. The biggest advantage of this concept is that it requires no additional parts or expense. There is no pump attached to it, and the cost of the hose itself is minimal. Preliminary analysis was done on the hose to determine if it would be able to drain the oil in a timely manner.
Assuming that the oil was warm and draining through a hose with a minimum diameter of 0. inch, the drain time was found to be less than a minute, which is suitable for this application. Mechanical Pump. Attaching a mechanical pump to the hose decreased the time required to drain the residual oil out of the filter. The mechanical pump could be driven by a common drill that most shops would likely have on hand. The disadvantage of adding the pump is the increased cost and the need to hook up additional tools to drain the oil. If drain time is a big issue to the customer, however, the added cost and complexity might be insignificant in comparison to the increased drain speed. Venturi Pump. Creating a venturi pump for the drain hose would also increase the drain speed of the tool. This could be achieved by attaching an air compressor to the drain hose in a âTâ fitting. The air flow from the compressor would create a pressure drop in the fitting and draw the oil out of the filter. This method is less expensive than the mechanical pump method, but it still requires the use of additional tools - namely, an air compression system. Furthermore, it could prove somewhat difficult to keep the air and oil from mixing too much or causing a mess. Hand Pump. Adding a hand pump to the hose is also cheaper than a mechanical pump and would increase the drain speed over the gravity-fed hose. The suction achieved with this type of pump is less than the previous two pumps, but has an advantage over them when considering that no additional tools are required in its use. However, this method does require the use of both hands during operation, and would add to the employeesâ physical demands.
2.3 Wrench Mechanism The purpose of the wrench is to break the oil filter loose from the engine block to facilitate disassembly. The installation specifications on most oil filters state that the filter should be âhand tightenedâ to the engine block. That is to say that the filter should be removable by hand during an oil change. However, this is often not the case. Sometimes during operation, the filter may seize to the block and can be very difficult to break loose by hand. Overzealous mechanics can also over tighten the filter during installation, making removal especially difficult. With this in mind, the tool must be able to generate sufficient torque to remove the filter. Each of the punch methods explained above would also have the capability of functioning as a wrench. Once the punch is inserted into the oil filter, the tool needs only then to be rotated slightly to break the filter loose. Once the filter is loose, it can be removed the rest of the way by hand.
As can been seen from the table, cleanliness is ranked as the most important criterion. As the main function of the tool is to increase the cleanliness of the oil changing operation, this is no surprise. Compatibility is ranked only slightly lower than cleanliness. If the tool is to be design for a commercial market, then the users will see a wide variety of vehicles. The tool must be able to function on as many of these as possible. Additionally, there is something of an âease of useâ factor in this criterion. Not only should the tool function on many different vehicles, but it should also function well on many different vehicles. Durability is ranked next. The tool is planned for a dealership type environment, so it is important that the tool work for thousands of oil changes. A tool that does not work at all would see less use than a tool that is somewhat difficult to use, which is why durability is ranked in front of punch force and wrench force.
12
Speed is the next criterion. Due to the oil change procedure, the tool effectively has the time during which the oil pan is drained to drain the filter. This is effectively as long as the entire operation time for the tool, making this criterion relatively unimportant. Cost and safety are the least important criteria. No particular solution for this tool is expected to be prohibitively expensive. Similarly, no solution is expected to be overtly dangerous. The people who are expected to use these tools use far more dangerous tools than this daily, and generally are expected to be versed in the safe use of such equipment.
3.1 Punch Mechanism The same method of selection analysis was used for the punch mechanism. Table 3- shows the results of the selection analysis for the punch method.
Table 3-2. Weighted Selection Analysis of Punch Method Weight Aircraft Spruce Pliers Band Screw Cable Ratchet Cost 0.25 2 2 2.25 1.5 1.75 1. Compatibility 0.875 6.125 7 4.375 6.125 6.125 7 Punch Force 0.625 5 4.375 2.5 5 3.75 6. Durability 0.75 4.5 6.75 6 4.5 3 6 Safety 0.25 2.5 2.5 2.5 2.5 2.5 2. Speed 0.375 1.5 3 2.25 1.5 2.25 3 21.625 25.625 19.875 21.125 19.375 26
Due to their ability to work in a large number of cases (many existing oil filter wrenches utilize a pliers-type function) and their good durability, the pliers and ratchet win the selection analysis. Although pliers scores slightly lower, the close score means little difference in a subjective type of analysis such as this. Durability was seen as a problem in the other types. For example, the cable type was expected to wear considerably faster. The screw type was expected to have problems under the grimy conditions of changing oil, as debris would build up in the screw mechanism and it would become harder to turn.
3.2 Drain Mechanism The pair-wise comparison method was again used for the drain mechanism. Table 3- shows the results of the selection analysis for the drain method.
13
The tool needs to be practical in loosening the oil filter once it has finished its job of draining the filter. Compatibility is how well a certain type would fit different makes and models of vehicles. The pliers scored high because they can fit into many vehicles. Indeed, they are the most common type of filter wrench in use in the industry today. The ratchet also scored high, as it is a derivative of the pliers. Screw and cable both scored relatively high as well, due to their thin design. Band scored lowest because it often requires a large range of motion to properly grip the filter. Wrench Force is based on how much leverage the tool is expected to give. A long tool like the screw or pliers type can give more leverage, while the band type scored low because the range of motion required to grip the filter often dictates a short handle.
4. COMPONENT DESCRIPTIONS
Figures 4-1 and 4-2 show the wrench handle design, with dimensions in inches. The handles are made of aluminum and were cut in a water-jet. The wrench handle sides have mounts for the other wrench handle, ratchet handles, punch and elbow, as well as the guide and mounting point for the strap.
Figure 4-1. Wrench Handle âRearâ Side
Figure 4-2. Wrench Handle âFrontâ Side
The spacer is located between the two halves of the wrench handle shown above. It is also made of aluminum. It holds the handle halves apart so the ratchet can slide between, as well as providing backing support of the load into the ratchet. The spacer is shown in Figure 4- below.
Figure 4-3. Handle Spacer
The ratchet travel is the piece that the pawl acts against to pull the strap down onto the filter. It is made of machined aluminum and fits between the halves of the handle. It has a series of ratchet teeth for movement as well as a hook onto which the strap attaches. Figure 4-4 below shows the ratchet travel.
16
The ratchet handle spacer in Figure 4-6 is a simple machined aluminum piece used to give support and dimension to the ratchet handles. It also provides a surface for the torsion spring which extends the ratchet arm.
Figure 4-6. Ratchet Handle Spacer
The ratchet arm is the pawl that works between the ratchet handles and the ratchet travel. It is made of machined aluminum and converts the lateral force of the ratchet handle to the downward force at the ratchet travel. Figure 4-7 below shows the ratchet arm.
Figure 4-7. Ratchet Arm
The band capture, shown in Figure 4-8 below is designed to provide additional stability to the strap. In addition to preventing unwanted movement, it also keeps the strap closer to the tool, improving the ability of the hook on the ratchet travel to hold the strap. It mounts to the ratchet travel side of the wrench handles. The band capture is made of machined delrin.
Figure 4-8. Band Capture
The band pin, shown in Figure 4-9, mounts to the handles on the side opposite of the band capture. It is made of machined aluminum and holds the fixed end of the strap.
Figure 4-9. Band Pin
The drain elbow mounts to the wrench handles and holds the punch. It is made of either stainless steel or brass, depending on the punch being used. It also directs the flow of the oil from the punch to the tube. It is shown in Figure 4-10 below.
19