
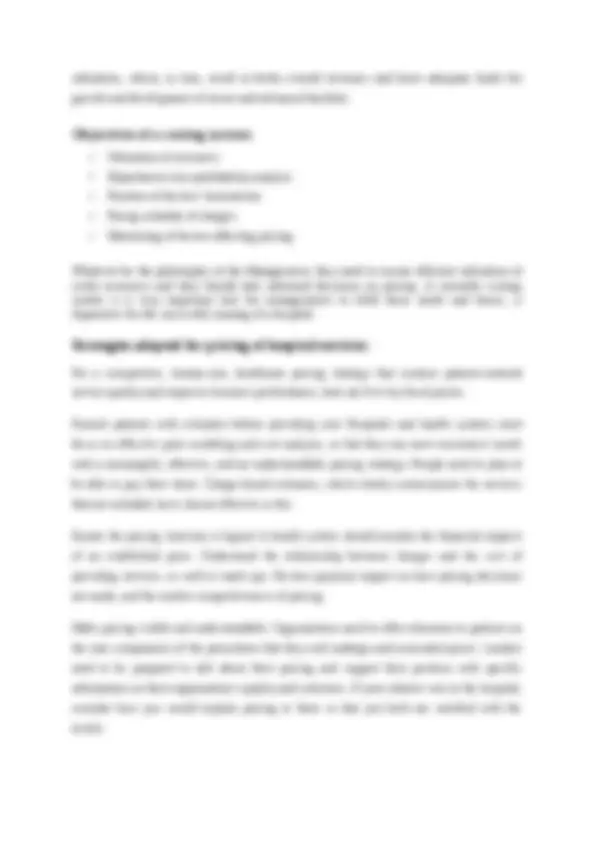
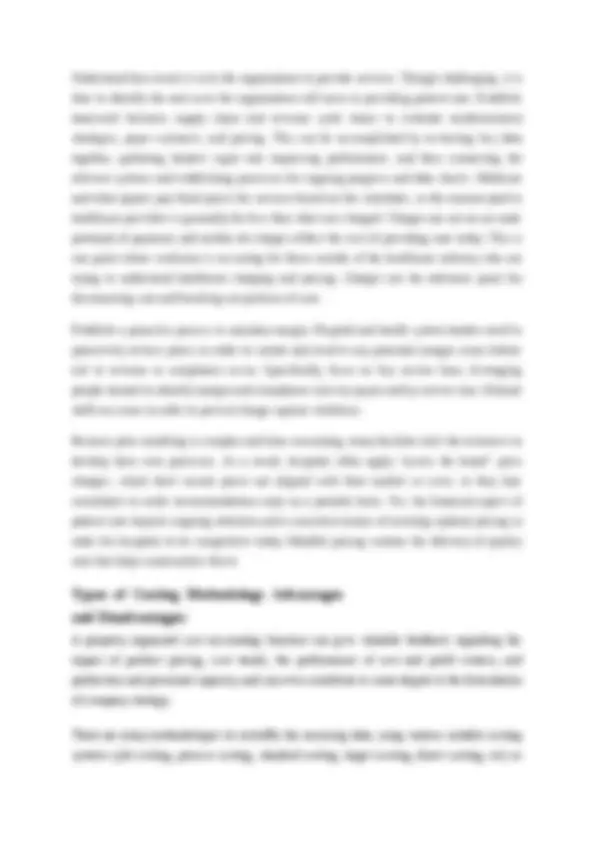
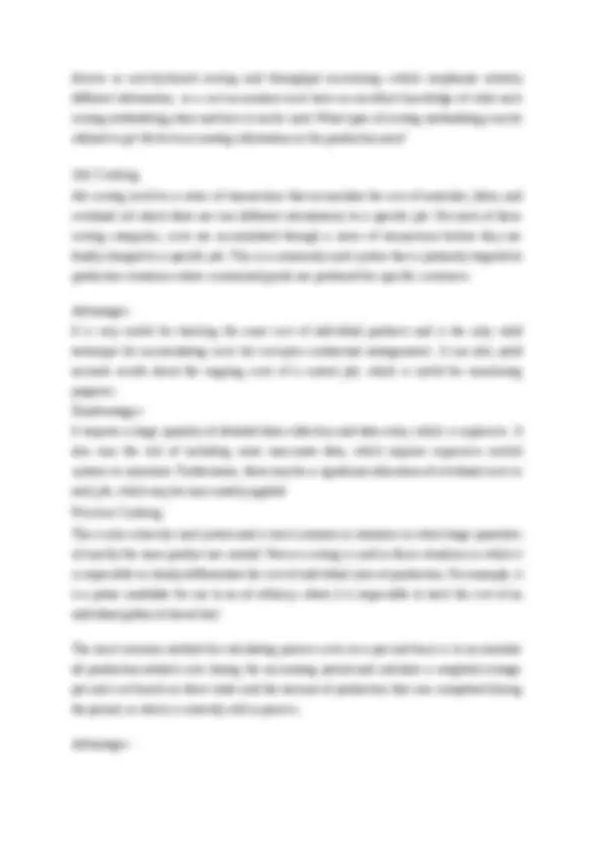
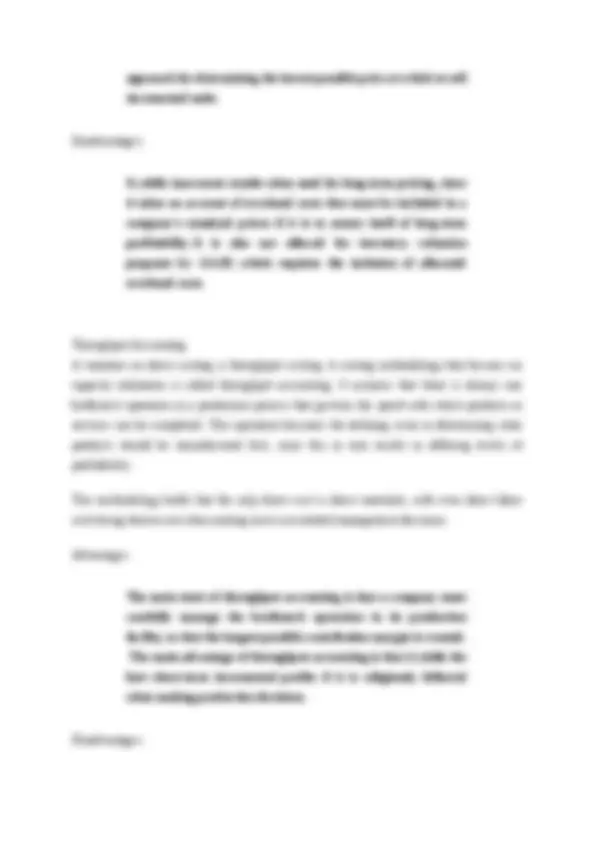
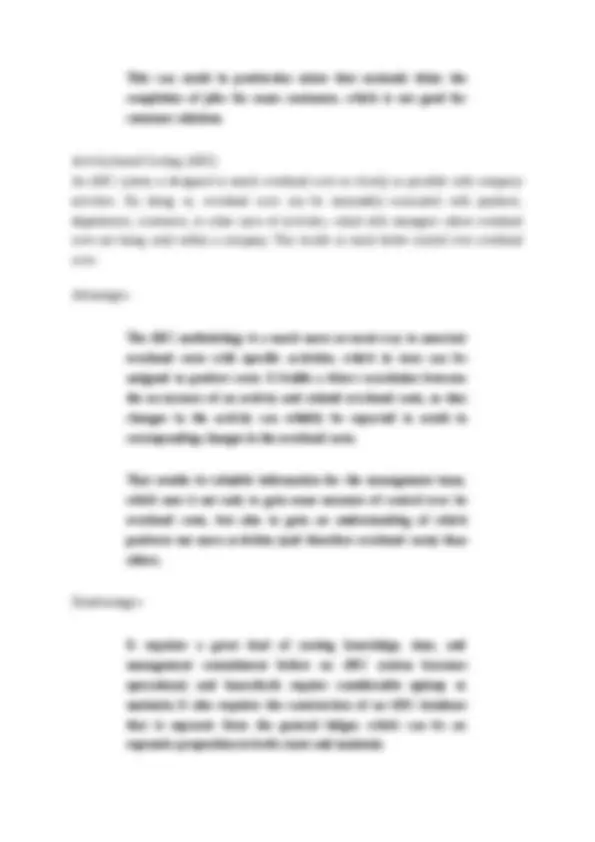
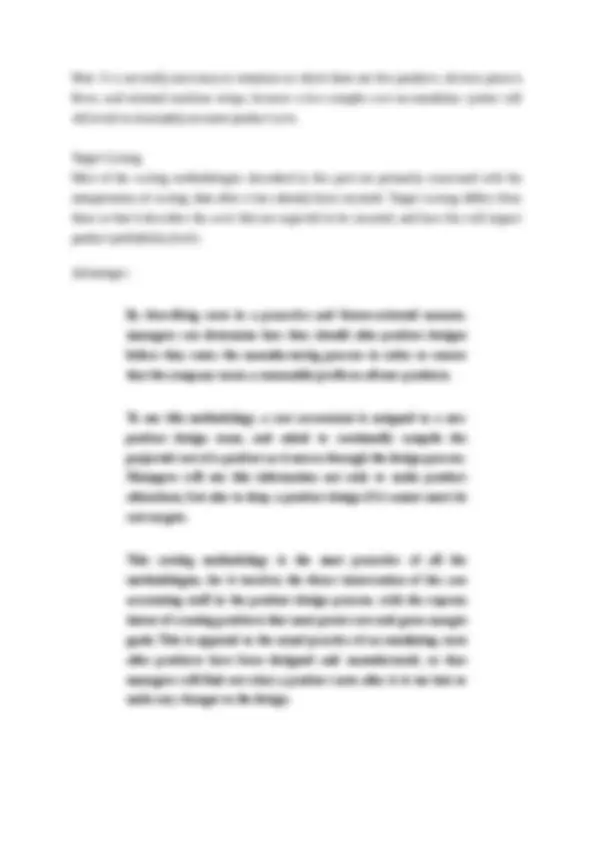
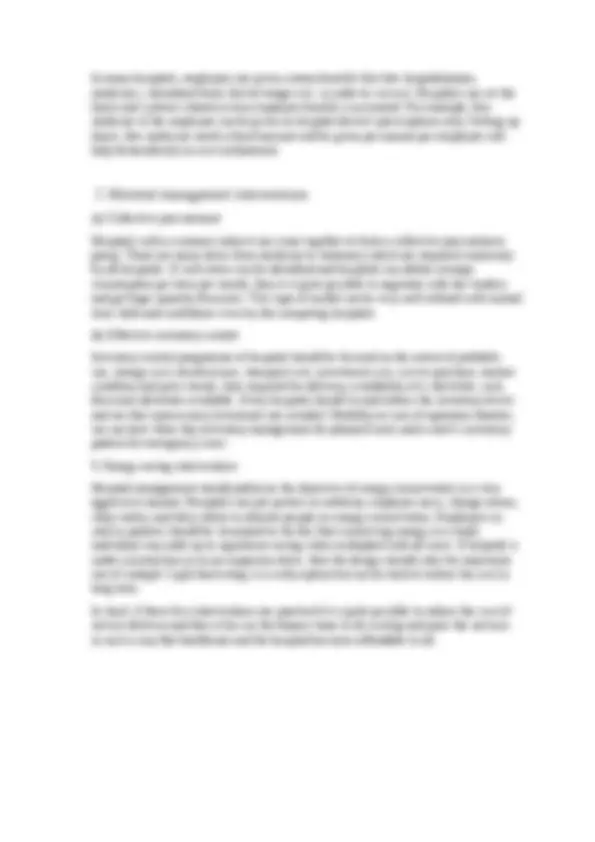
Study with the several resources on Docsity
Earn points by helping other students or get them with a premium plan
Prepare for your exams
Study with the several resources on Docsity
Earn points to download
Earn points by helping other students or get them with a premium plan
Community
Ask the community for help and clear up your study doubts
Discover the best universities in your country according to Docsity users
Free resources
Download our free guides on studying techniques, anxiety management strategies, and thesis advice from Docsity tutors
various costing techniques in hospital services with their merits and demerits
Typology: Exercises
1 / 13
This page cannot be seen from the preview
Don't miss anything!
The growing need of hospitals to have an efficient system to control costs and at the same time maintain quality_._ Modern day hospitals provide a variety of services to patients under one roof. It is akin to a large service organisation considering the number of personnel involved and the capital-intensive nature of the business be it the civil structures, operation theatres and equipment, diagnostic and therapeutic equipment, resuscitation equipment, gas lines, surgical instruments, consumables, and so on. Moreover, it is a 24×7 operations with people playing a vital role in the wellbeing of the patients in the hospital.
Traditionally, hospitals used bed occupancy as the yardstick of measurement of performance. With the advancements in medical technology, the average length of stay (ALOS) is reducing and hence, bed occupancy is not the main performance measure any longer.
The increased utilisation of costly resources, e.g. equipment in operating theatres, ICUs, Cath-Lab, Pathology Lab etc. in addition to doctors’ times are the key to success in hospitals.
The advent of health insurance companies has also queered the pitch. With the costs of treatment going up and the privatisation of the insurance industry, the hospitals are forced to give quality service at highly competitive prices as the insurance companies will pay only for the services that are desired and will also monitor the services that are rendered closely. This leads to deductibles, co-payments and all claims by hospitals do not get settled hundred percent. There is also a time element involved as costs are incurred upfront and outstanding amount is received only after a couple of months. It is therefore imperative for hospitals to have a system to control the costs, while at the same time providing high quality service to the patients.
Patients undergoing treatment receive services of varied nature from different departments. The hospital has to recover the expenses of the direct departments as also of the support departments from the patients availing these services. Nowadays, any composite hospital with latest facilities for advanced medical/surgical procedures in the various areas of treatment will have nearly 50 or more revenue centres and about 10 to 15 supporting service centres. Furthermore, most of the revenue centres, particularly, in-patient wards, will have classification depending on the level of services for different class of patients according to their monetary or other needs. Again, each department, other than wards, undertakes several types of procedures/operations etc.
All these make the list of procedures and classification of services quite large. It is for this reason that ascertaining true costs of various services and fixing of the Schedule of Charges becomes extremely complex. Costing needs to be done after careful analysis of past data, comparative data from other hospitals, study of utilisation of capacities. Costing techniques shall be applied to provide acceptable costs and charges, enabling optimization of capacity
Understand how much it costs the organization to provide services. Though challenging, it is time to identify the real costs the organization will incur in providing patient care. Establish teamwork between supply chain and revenue cycle teams to evaluate reimbursement strategies, payer contracts, and pricing. This can be accomplished by reviewing key data together, gathering leaders' input into improving performance, and then connecting the relevant systems and establishing processes for ongoing progress and data checks. Medicare and other payers pay fixed prices for services based on fee schedules; so the amount paid to healthcare providers is generally far less than what was charged. Charges are not an accurate portrayal of payment, and neither do charges reflect the cost of providing care today. This is one point where confusion is occurring for those outside of the healthcare industry who are trying to understand healthcare charging and pricing. Charges are the reference point for documenting care and breaking out portions of care.
Establish a proactive process to maintain margin. Hospital and health system leaders need to proactively review prices in order to isolate and resolve any potential margin issues before risk to revenue or compliance occur. Specifically, focus on key service lines, leveraging people trained to identify margin and compliance risks by payer and by service line. Educate staffs on issues in order to prevent charge capture violations.
Because price modeling is complex and time consuming, many facilities lack the resources to develop their own processes. As a result, hospitals often apply "across the board" price changes, which don't ensure prices are aligned with their market or costs; or they hire consultants to make recommendations only on a periodic basis. Yet, the financial aspect of patient care requires ongoing attention and a consistent means of ensuring optimal pricing in order for hospitals to be competitive today. Mindful pricing sustains the delivery of quality care that helps communities thrive.
A properly organized cost accounting function can give valuable feedback regarding the impact of product pricing, cost trends, the performance of cost and profit centers, and production and personnel capacity, and can even contribute to some degree to the formulation of company strategy.
There are many methodologies to reshuffle the incoming data, using various suitable costing systems (job costing, process costing, standard costing, target costing, direct costing, etc) as
diverse as activity-based costing and throughput accounting—which emphasize entirely different information, so a cost accountant must have an excellent knowledge of what each costing methodology does and how it can be used. What types of costing methodology can be utilized to get the best accounting information in the production area?
Job costing involves a series of transactions that accumulate the cost of materials, labor, and overhead (of which there are two different calculations) to a specific job. For each of these costing categories, costs are accumulated through a series of transactions before they are finally charged to a specific job. This is a commonly used system that is primarily targeted at production situations where customized goods are produced for specific customers.
Advantages: It is very useful for tracking the exact cost of individual products and is the only valid technique for accumulating costs for cost-plus contractual arrangements. It can also yield accurate results about the ongoing costs of a current job, which is useful for monitoring purposes. Disadvantages: It requires a large quantity of detailed data collection and data entry, which is expensive. It also runs the risk of including some inaccurate data, which requires expensive control systems to minimize. Furthermore, there may be a significant allocation of overhead costs to each job, which may be inaccurately applied.
This is also a heavily used system and is most common in situations in which large quantities of exactly the same product are created. Process costing is used in those situations in which it is impossible to clearly differentiate the cost of individual units of production. For example, it is a prime candidate for use in an oil refinery, where it is impossible to track the cost of an individual gallon of diesel fuel.
The most common method for calculating process costs on a per-unit basis is to accumulate all production-related costs during the accounting period and calculate a weighted average per-unit cost based on these totals and the amount of production that was completed during the period, or which is currently still in process.
Advantages:
Disadvantages: It is time-consuming to set and maintain standards; in environments where this maintenance function is not performed, standards can be so far away from actual results that variance analysis is no longer useful for management purposes. Also, a company that has adopted continuous process improvement principles will find that any standards adopted will almost immediately become obsolete, requiring constant correction. Furthermore, most standards are set at the product level, rather than at the batch level, so there is no basis of comparison when using this method for cost control over production batches.Another problem is that comparisons to actual costs tend to focus management attention on labor variances, which have historically been a large part of the cost accounting report package, even though these costs comprise only a small proportion of total production costs in most manufacturing environments. Finally, it tends to perpetuate inefficiencies if personnel use the current standard cost as a baseline for behavior; they will have no incentive to improve costs to a point that is substantially better than the pre-set standard, resulting in languishing efficiency levels. For these reasons, standard costing is now used in a more limited role that in previous years.
Direct Costing A direct cost is a cost that is directly associated with changes in production volume. This usually restricts the definition of direct costs to direct materials and direct labor (and a strong case can be made for not using direct labor, since this cost tends to be present even when production volumes vary).
For example, the materials used to create a product are a direct cost, whereas the machine used to convert the materials into a finished product is not a direct cost, because it is still going to be sitting on the factory floor, irrespective of any changes in production volume.
Advantages:
This is a favorite methodology for those managers who are constantly confronted with incremental costing and pricing decisions where the inclusion of overhead costs in a product’s total cost will yield inaccurate information. Direct costing is an ideal
approach for determining the lowest possible price at which to sell incremental units.
Disadvantages:
It yields inaccurate results when used for long-term pricing, since it takes no account of overhead costs that must be included in a company’s standard prices if it is to assure itself of long-term profitability. It is also not allowed for inventory valuation purposes by GAAP, which requires the inclusion of allocated overhead costs.
Throughput Accounting A variation on direct costing is throughput costing. A costing methodology that focuses on capacity utilization is called throughput accounting. It assumes that there is always one bottleneck operation in a production process that governs the speed with which products or services can be completed. This operation becomes the defining issue in determining what products should be manufactured first, since this in turn results in differing levels of profitability.
This methodology holds that the only direct cost is direct materials, with even direct labor costs being thrown out when making most cost-related management decisions.
Advantages:
The main tenet of throughput accounting is that a company must carefully manage the bottleneck operation in its production facility, so that the largest possible contribution margin is created. The main advantage of throughput accounting is that it yields the best short-term incremental profits if it is religiously followed when making production decisions.
Disadvantages:
Note: It is not really necessary in situations in which there are few products, obvious process flows, and minimal machine setups, because a less complex cost accumulation system will still result in reasonably accurate product costs.
Target Costing Most of the costing methodologies described in this post are primarily concerned with the interpretation of costing data after it has already been incurred. Target costing differs from them in that it describes the costs that are expected to be incurred, and how this will impact product profitability levels.
Advantages:
By describing costs in a proactive and future-oriented manner, managers can determine how they should alter product designs before they enter the manufacturing process in order to ensure that the company earns a reasonable profit on all new products.
To use this methodology, a cost accountant is assigned to a new product design team, and asked to continually compile the projected cost of a product as it moves through the design process. Managers will use this information not only to make product alterations, but also to drop a product design if it cannot meet its cost targets.
This costing methodology is the most proactive of all the methodologies, for it involves the direct intervention of the cost accounting staff in the product design process, with the express intent of creating products that meet preset cost and gross margin goals. This is opposed to the usual practice of accumulating costs after products have been designed and manufactured, so that managers will find out what a product costs after it is too late to make any changes to the design.
This costing system is highly recommended to any company that designs its own products, since it can result in significant reductions in product costs before they are “locked in” when the design is completed.
Disadvantages:
This technique usually requires a great deal of cost accounting staff time, and can lengthen the product development process, but is well worth the effort.
By-product and Joint Product Costing There are a few situations in which multiple salable products are created as part of a production process, and for which there are no demonstrably clear-cut costs beyond those incurred for the main production process. When this happens, the cost accountant must determine a reasonable method for allocating these costs.
Advantages:
This type of costing involves using some rational means for allocating costs to products for which there is no clearly attributable cost. The various methods for conducting these allocations are primarily used for valuing inventory for external reporting purposes.
Disadvantages:
It is generally unwise to use this information for any management purpose, since decisions based on allocated costs, with the intention of changing those costs, will usually fail. Consequently, by-product and joint product costing is not recommended for anything other than inventory valuation.
In many hospitals, employees are given certain benefits like free hospitalization, medicines, subsidized food, free beverages etc. in order to cut cost. Hospitals can set the limits and systems wherein every employee benefit is accounted. For example, free medicine to the employee can be given on hospital doctor's prescriptions only. Setting up limits, like medicine worth a fixed amount will be given per annum per employee will help tremendously in cost containment.
(a) Collective procurement
Hospitals with a common interest can come together to form a collective procurement group. There are many items from medicine to stationary which are required commonly by all hospitals. If such items can be identified and hospitals can define average consumption per item per month, then it is quite possible to negotiate with the vendors and get huge quantity discounts. This type of model can be very well utilized with mutual trust, faith and confidence even by the competing hospitals.
(b) Effective inventory control
Inventory control programme of hospital should be focused on the extent of probable use, storage cost, obsolescence, transport cost, investment cost, cost to purchase, market condition and price trends, time required for delivery, availability of a substitute, cash flow and substitutes available. Every hospital should try and reduce the inventory levels and see that unnecessary inventories are avoided. Probably in case of operation theatres, we can have three day inventory management for planned cases and a week's inventory pattern for emergency cases.
Hospital management should publicise the objective of energy conservation in a very aggressive manner. Hospitals can put posters in cafeteria, employee mess, change rooms, clean utility, and dirty utility to educate people on energy conservation. Employees as well as patients should be sensitized to the fact that conserving energy in a small, individual way adds up to significant saving when multiplied with all users. If hospital is under construction or on an expansion drive, then the design should cater for maximum use of sunlight. Light harvesting is a costly option but can be tried to reduce the cost in long term.
In short, if these few interventions are practiced it is quite possible to reduce the cost of service delivery and then it lies on the finance team to do costing and price the services in such a way that healthcare and the hospital becomes affordable to all.