
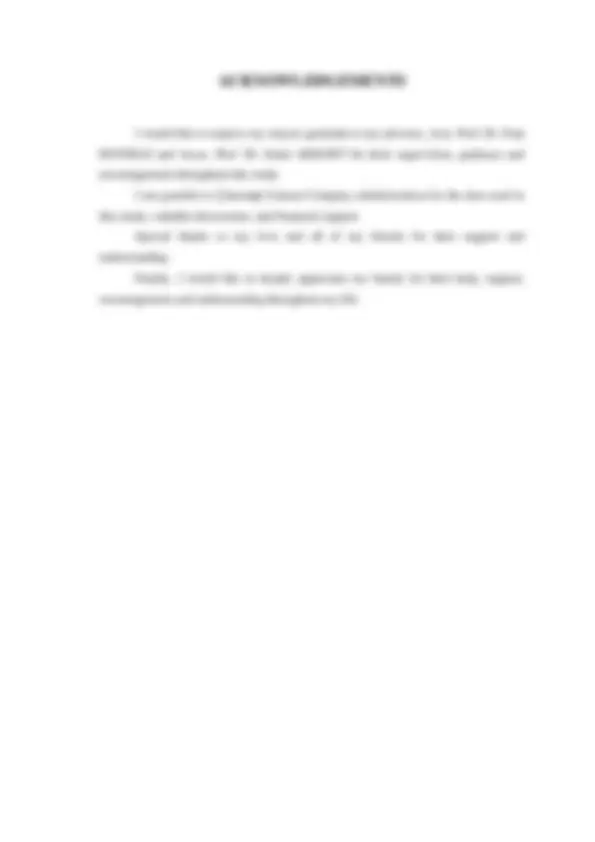
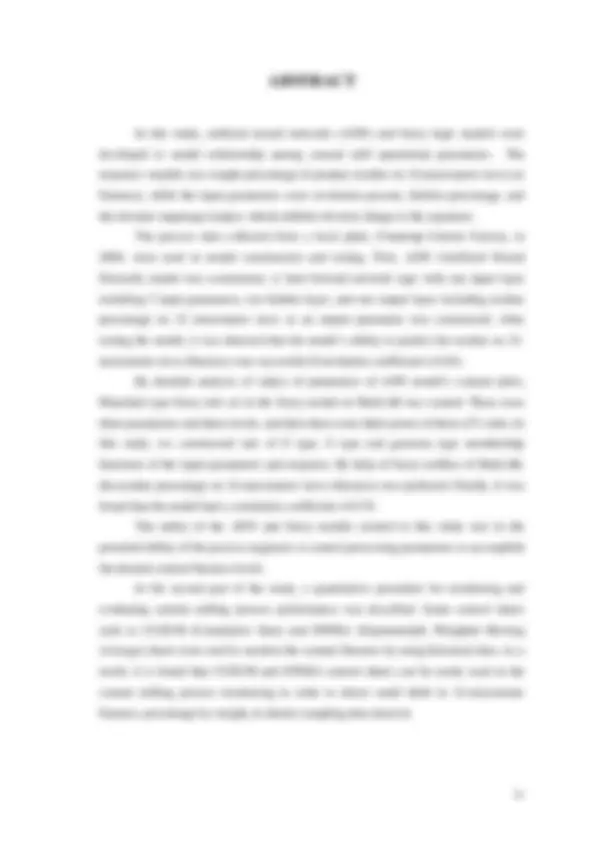
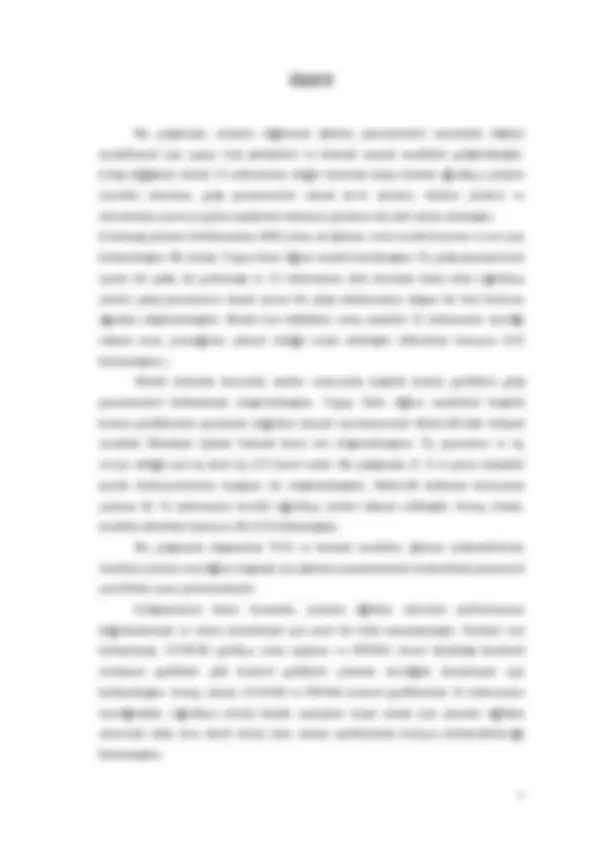
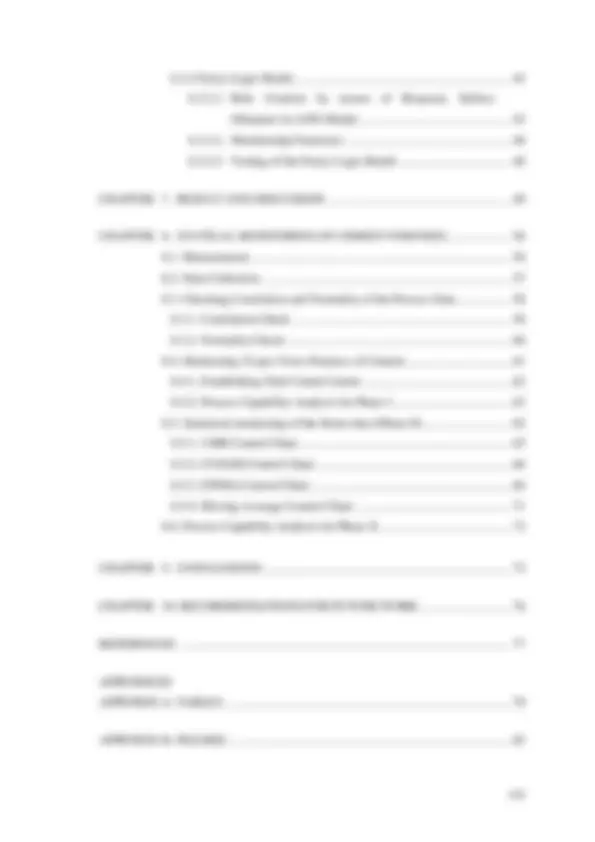
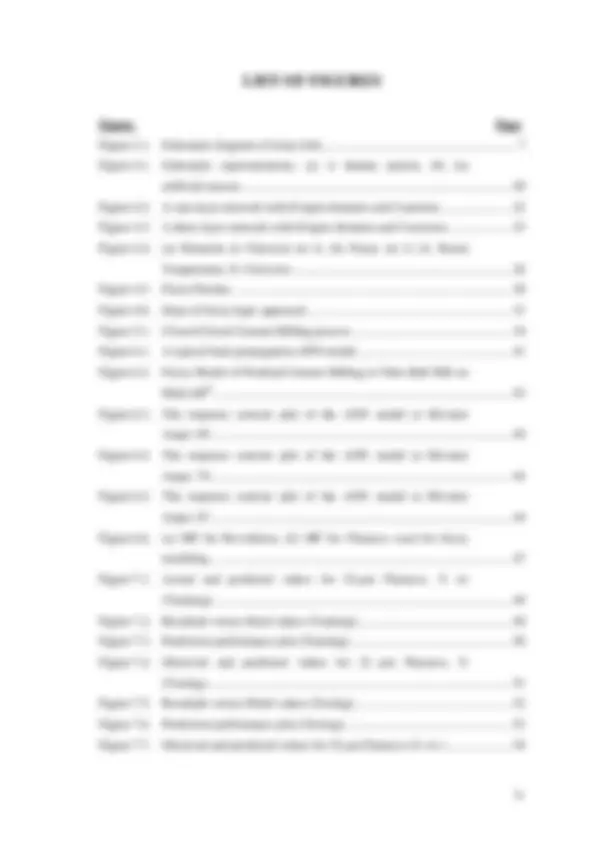
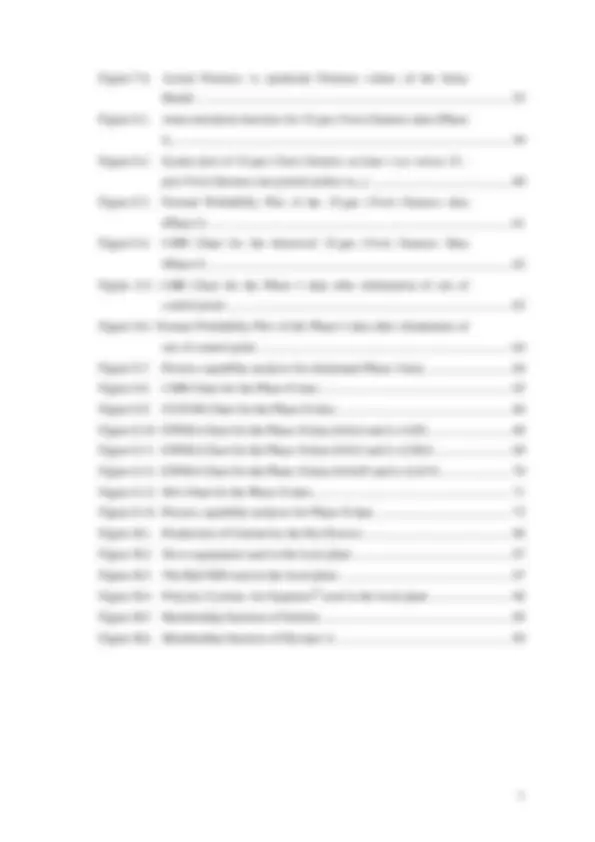
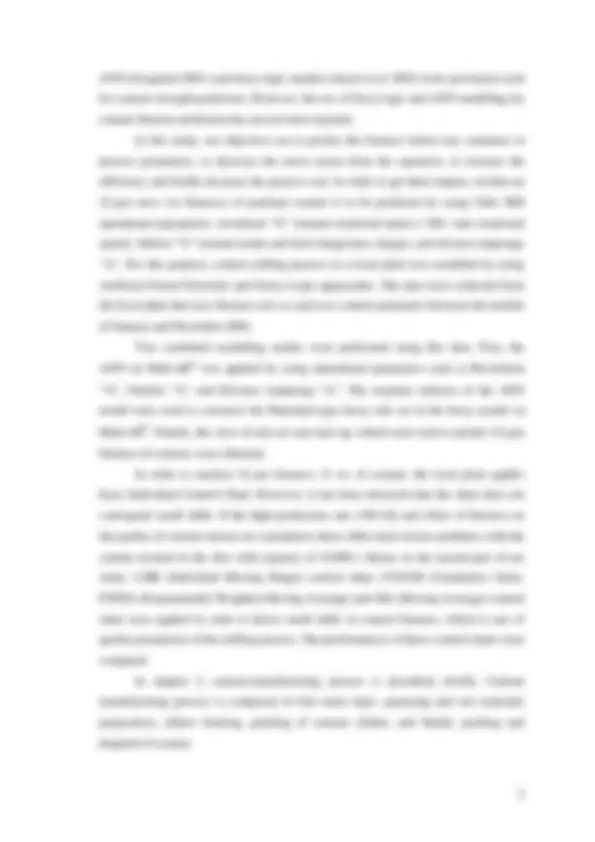
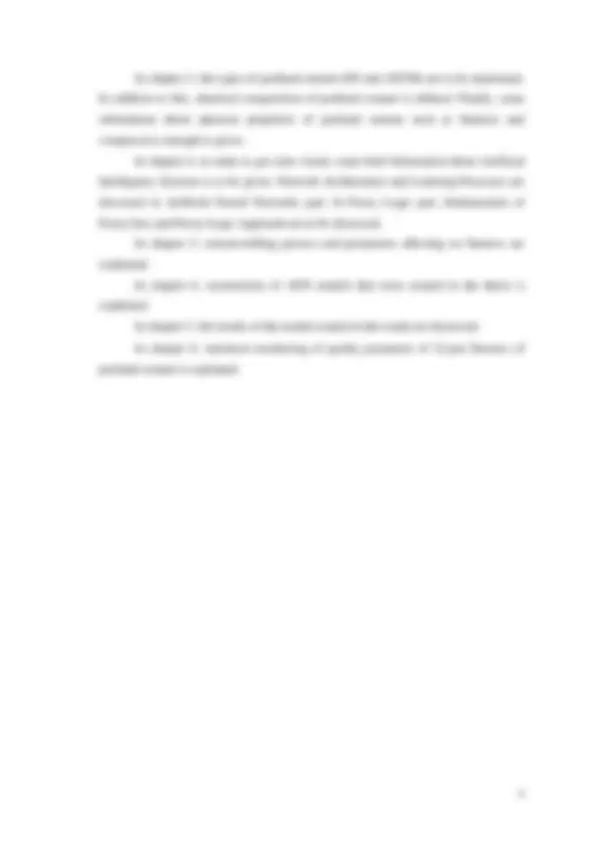
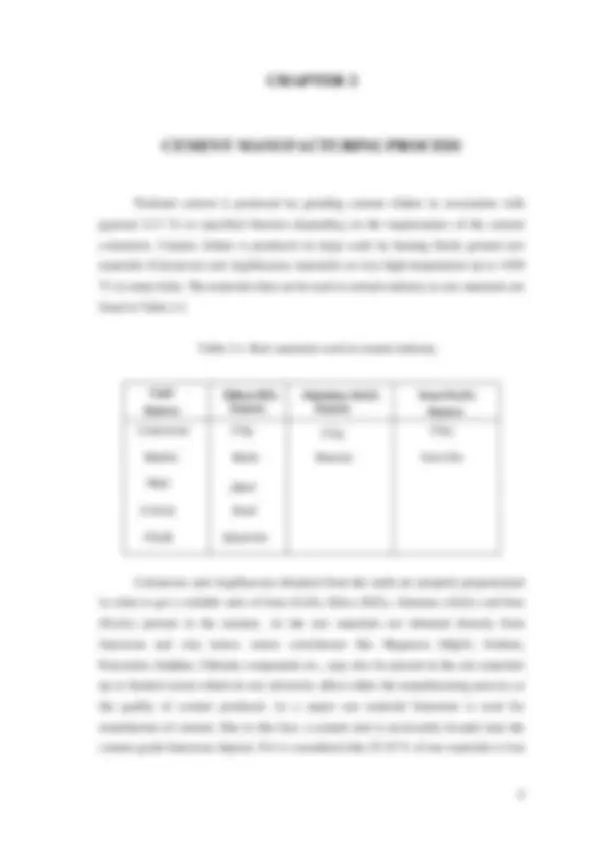
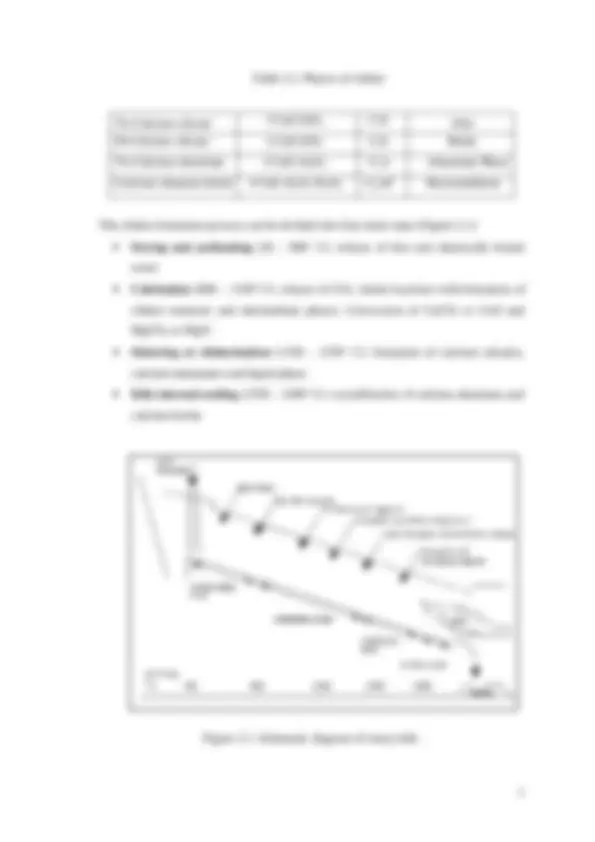
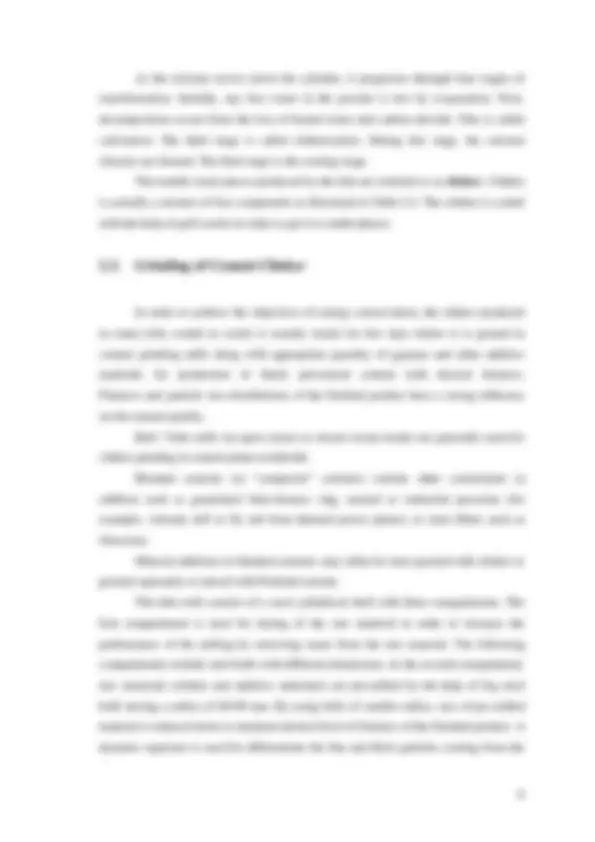
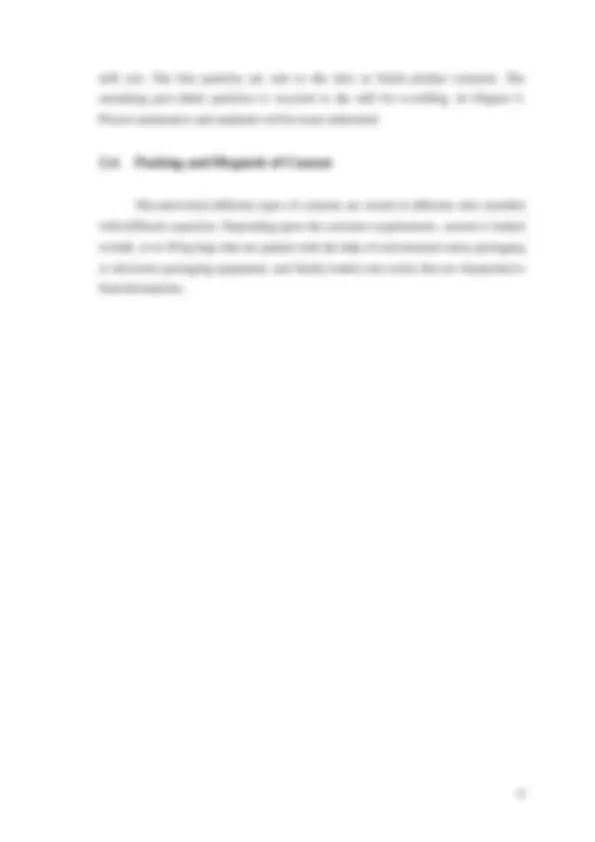
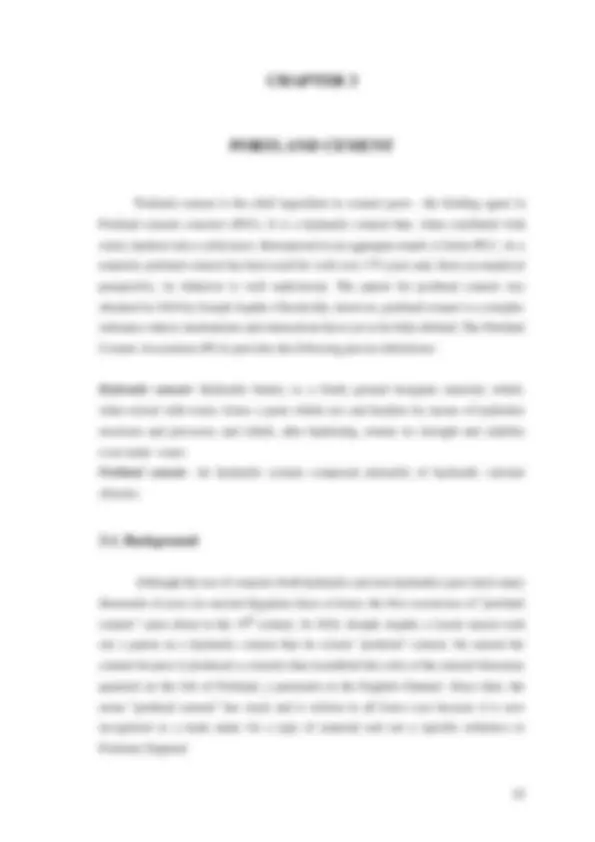

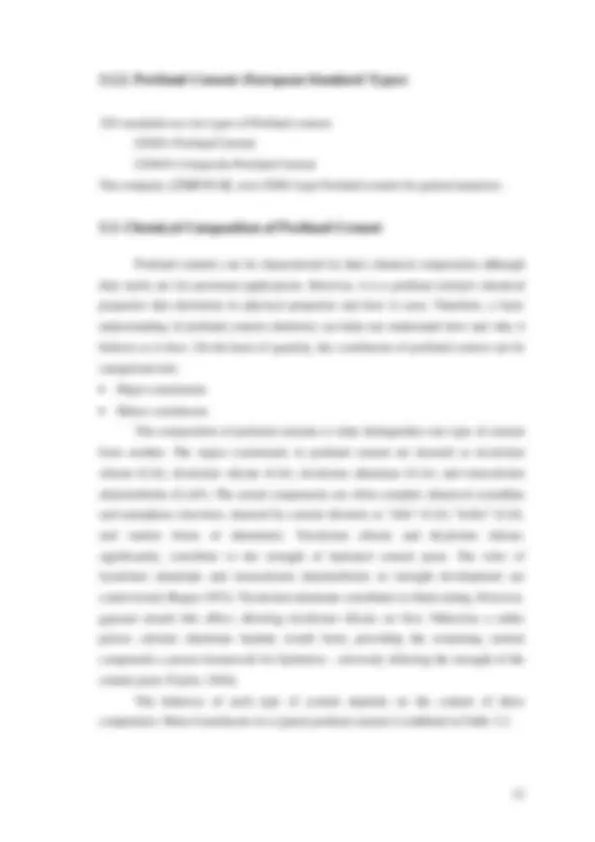
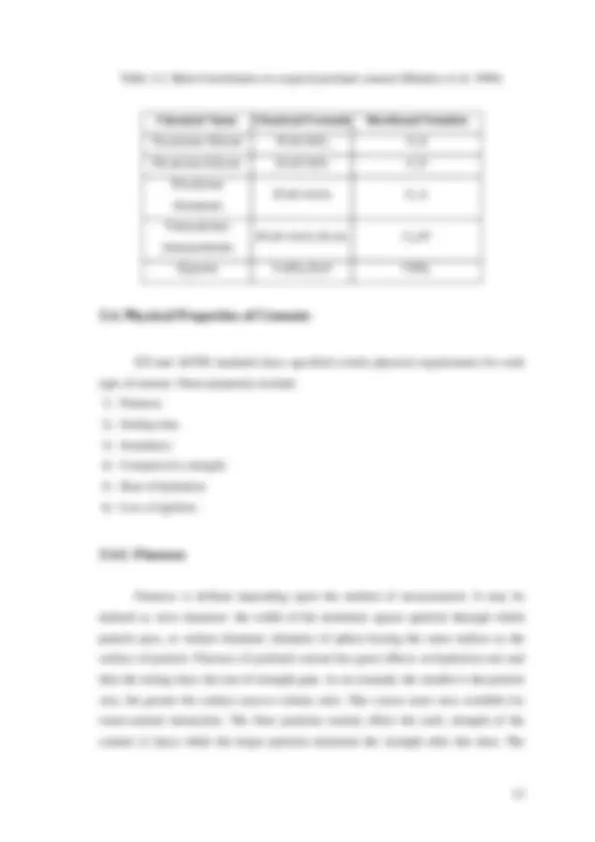
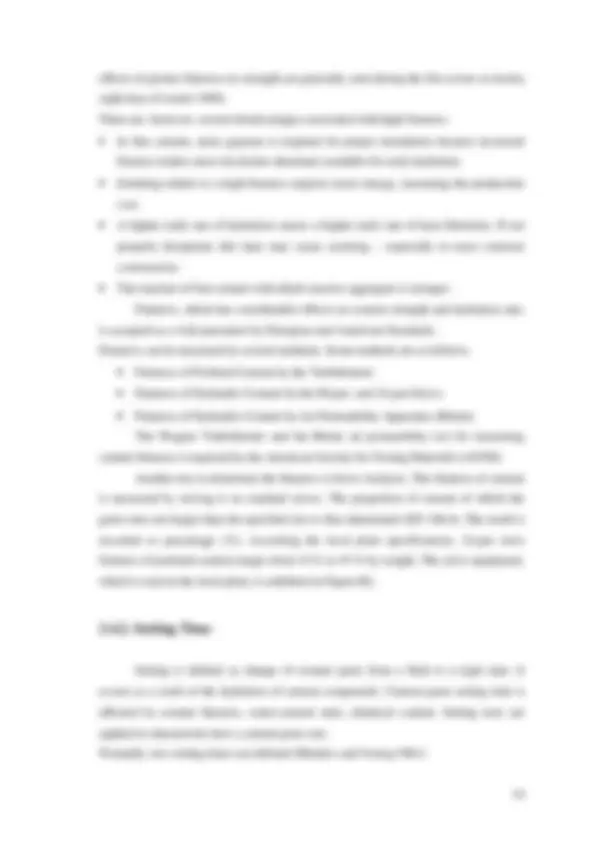
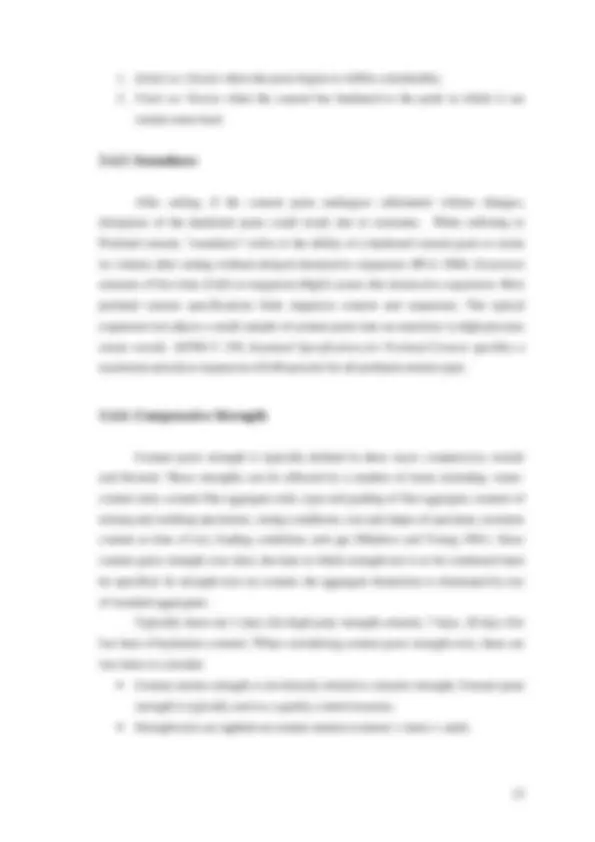
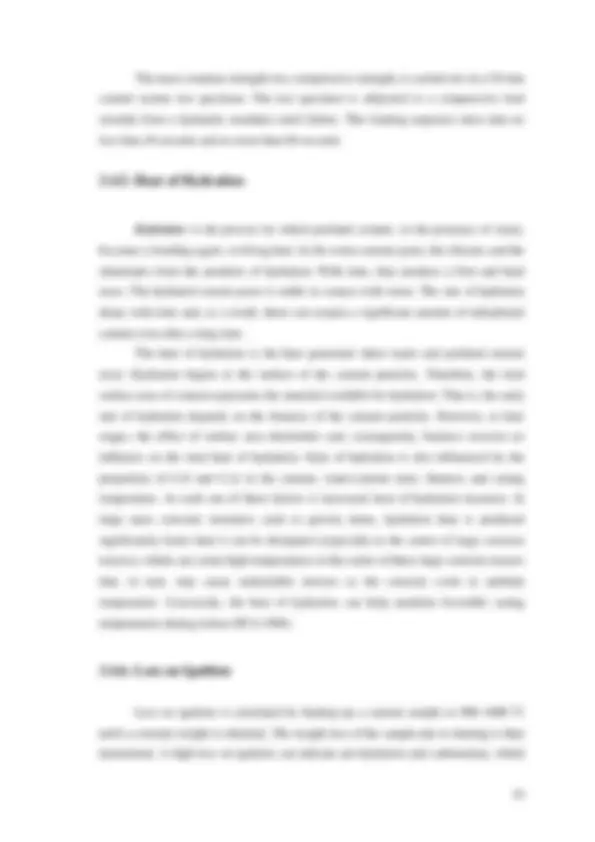
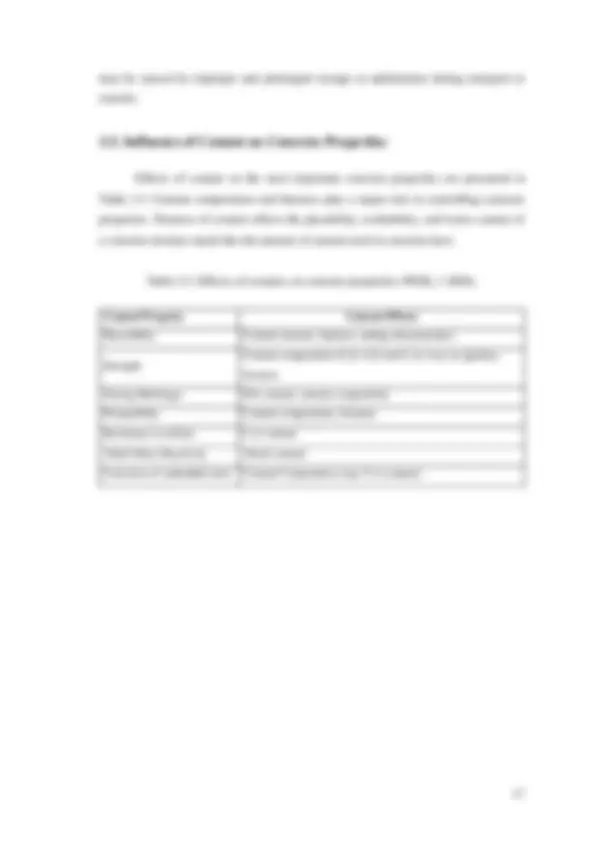
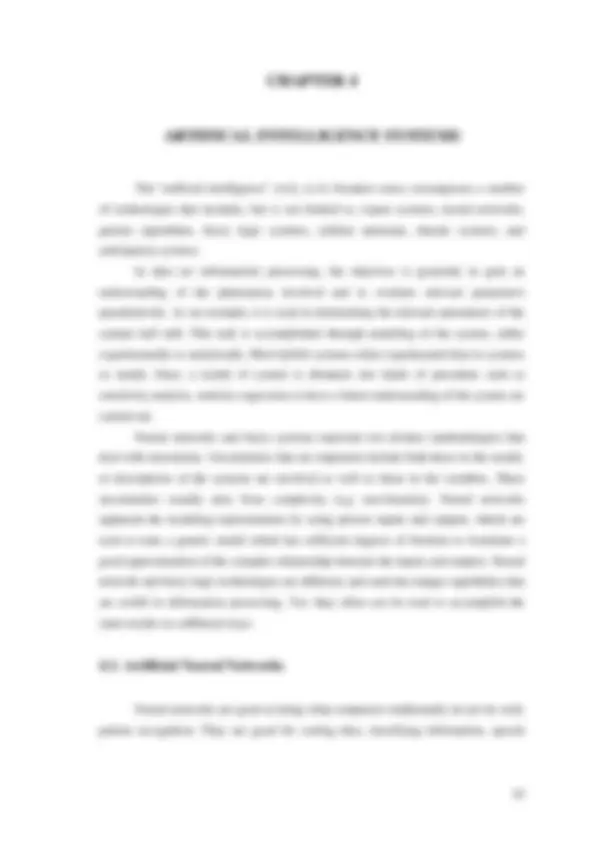
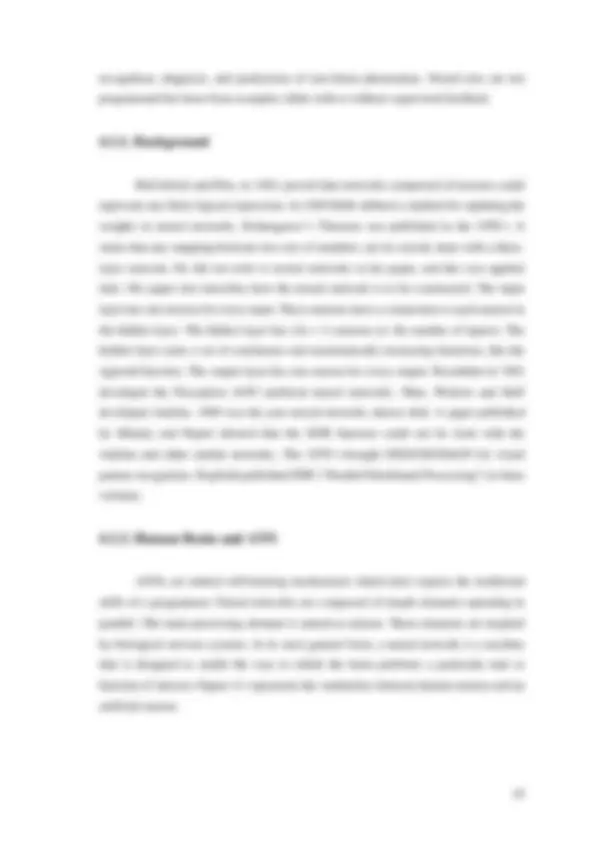
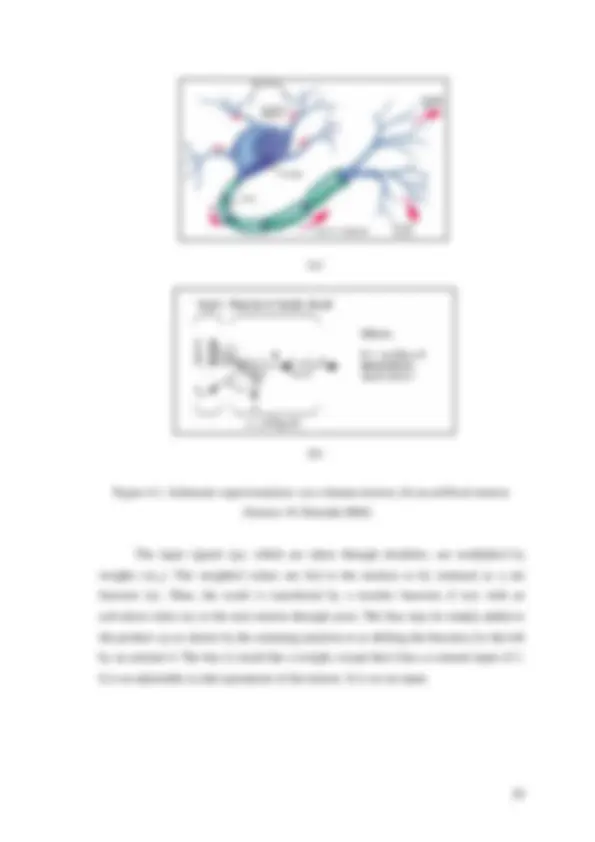
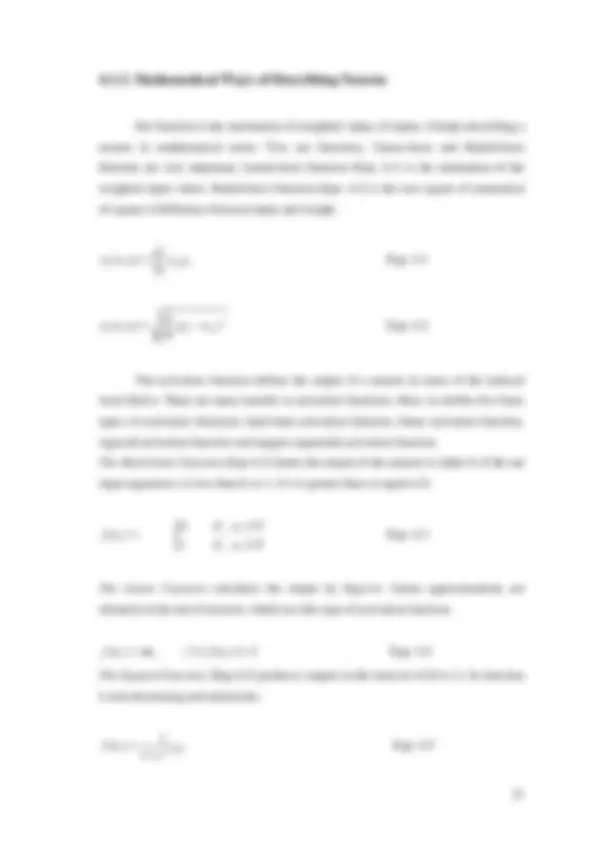
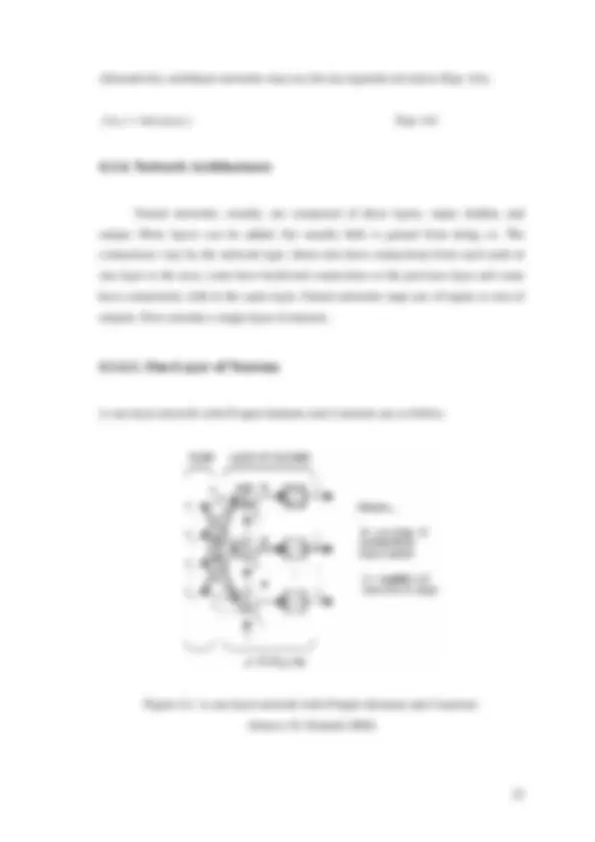
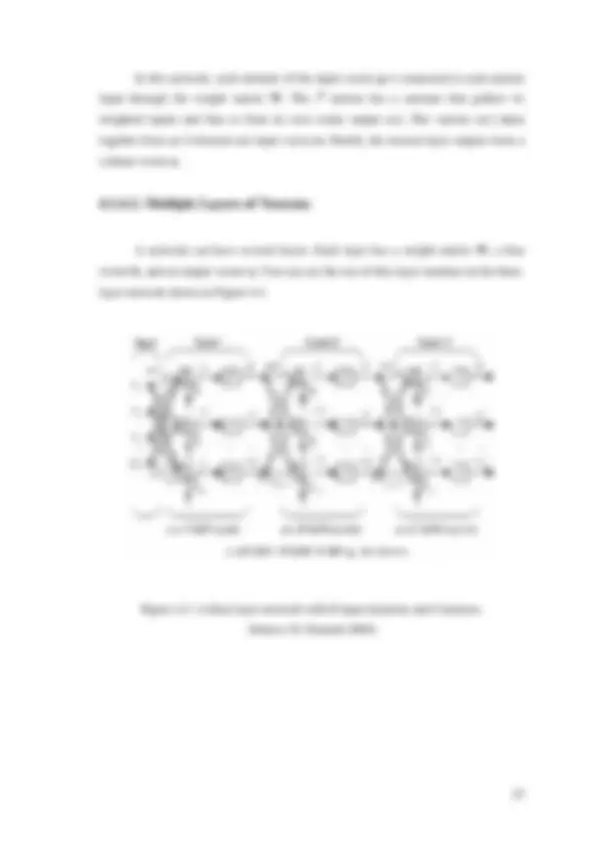
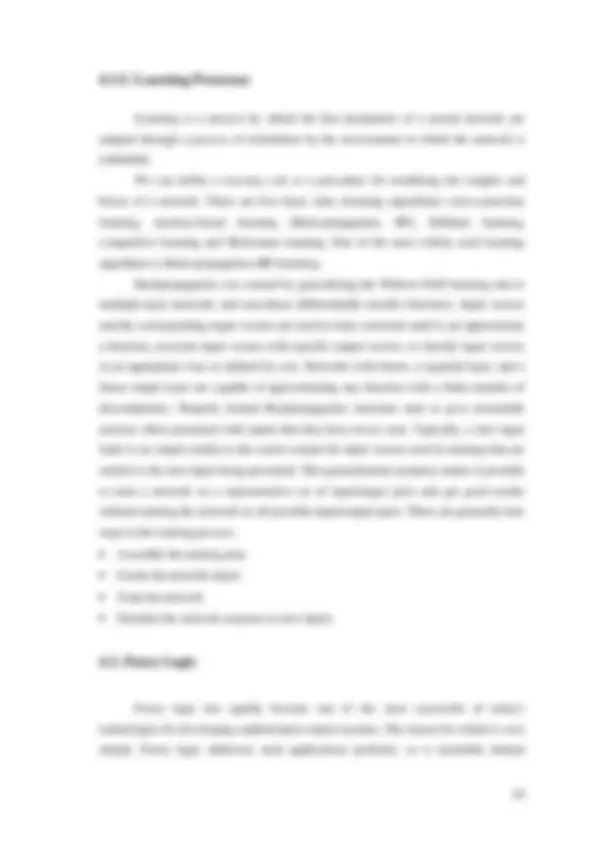
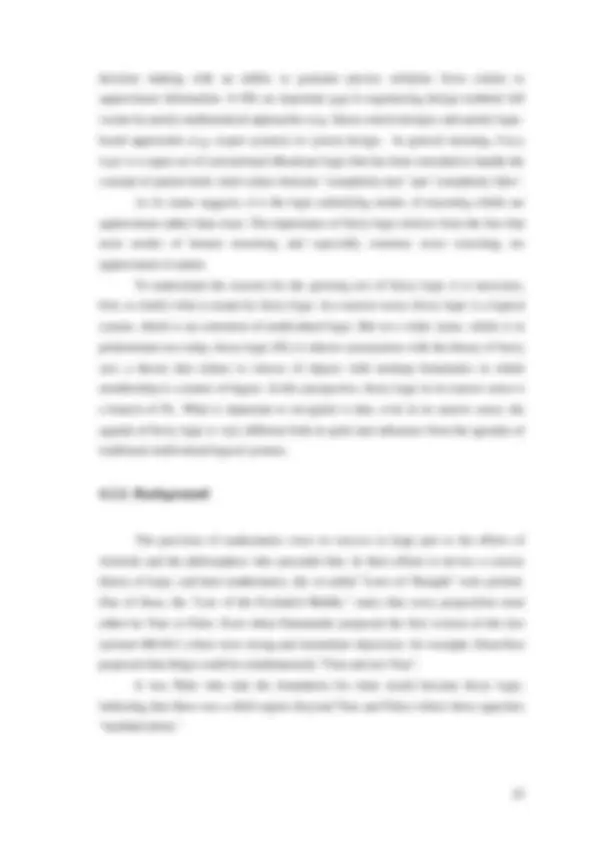
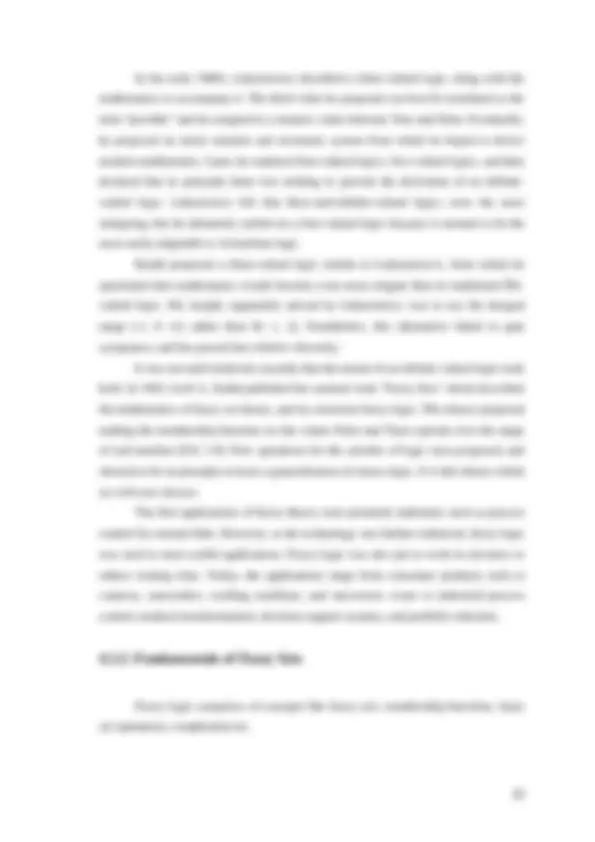
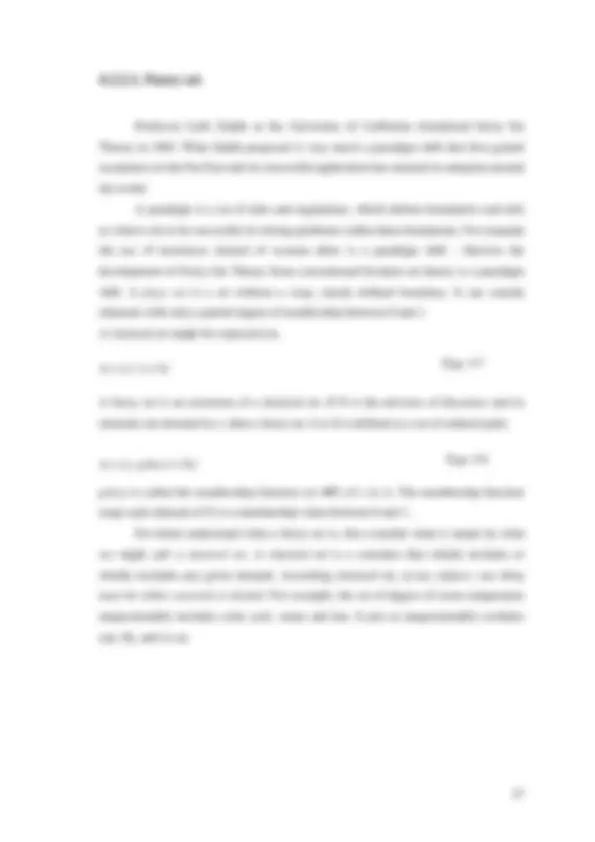
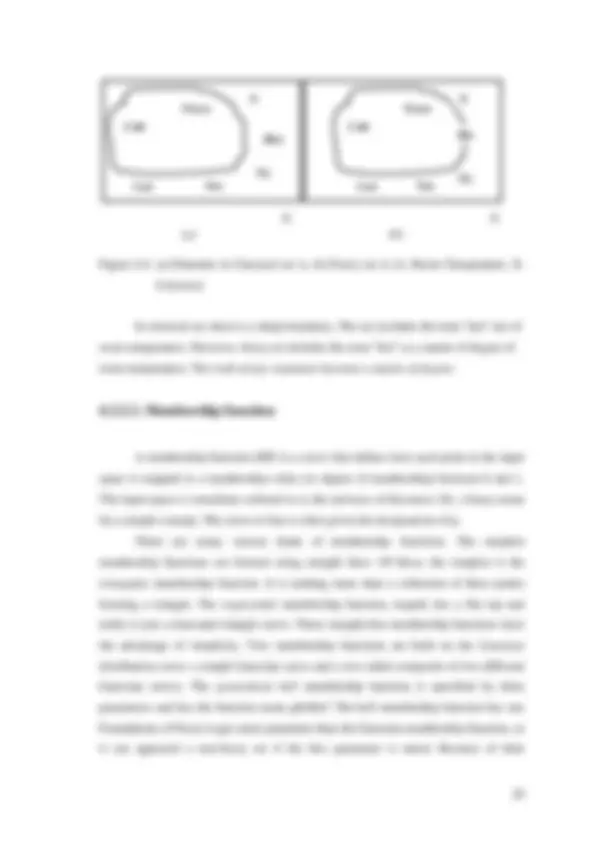
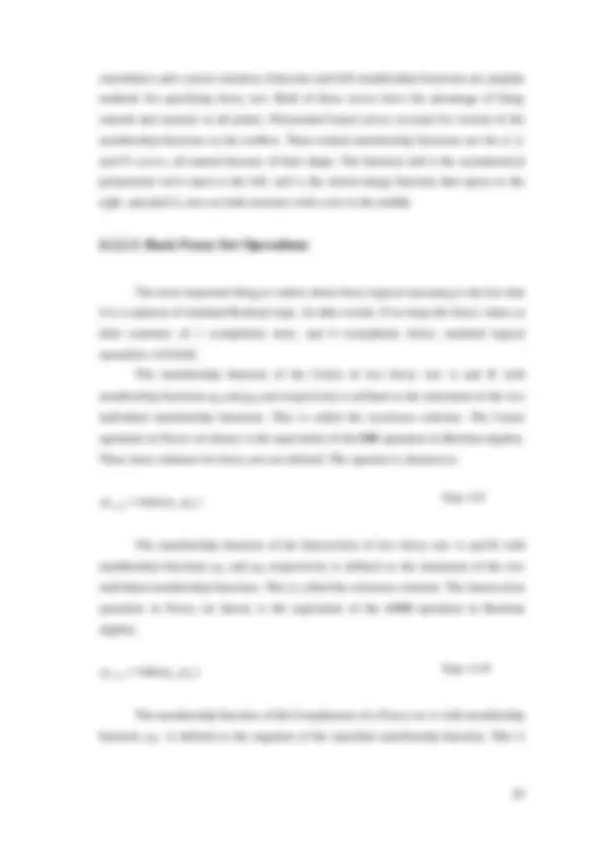
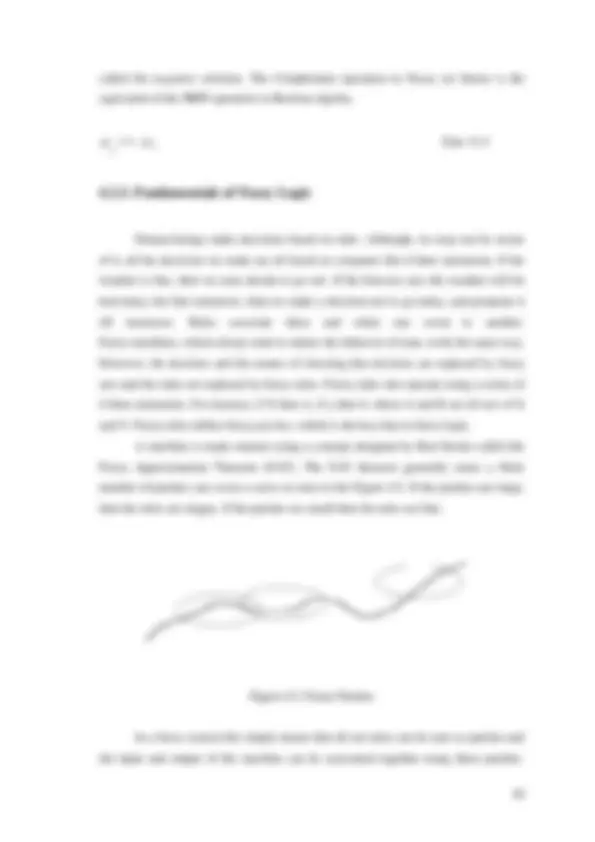
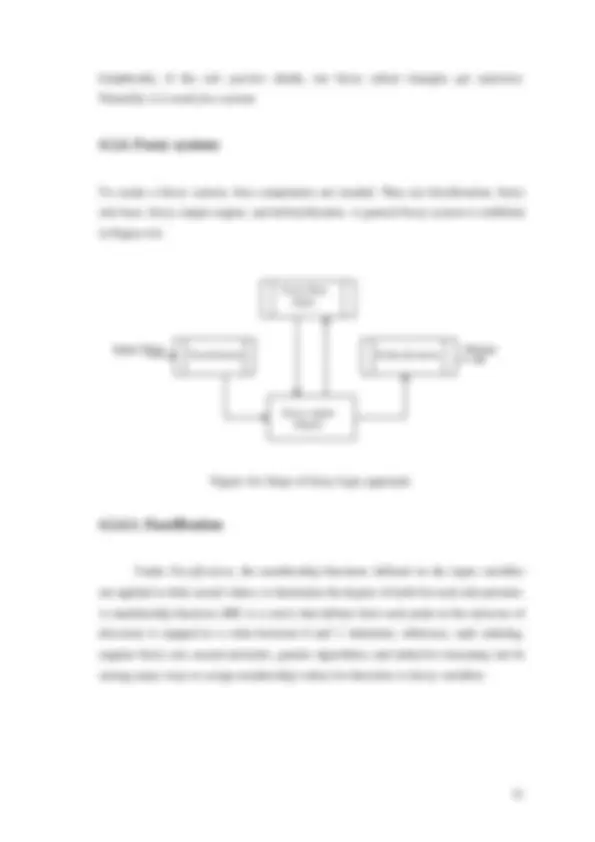
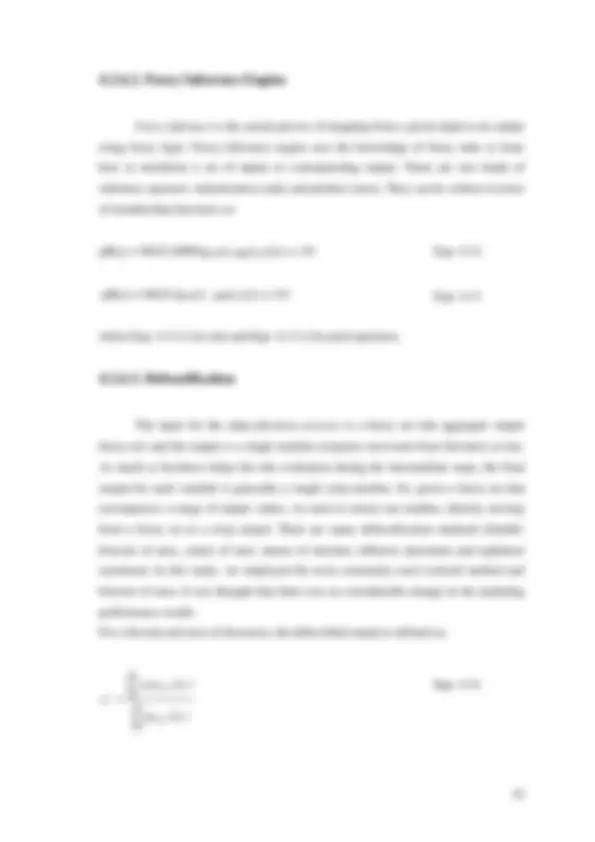
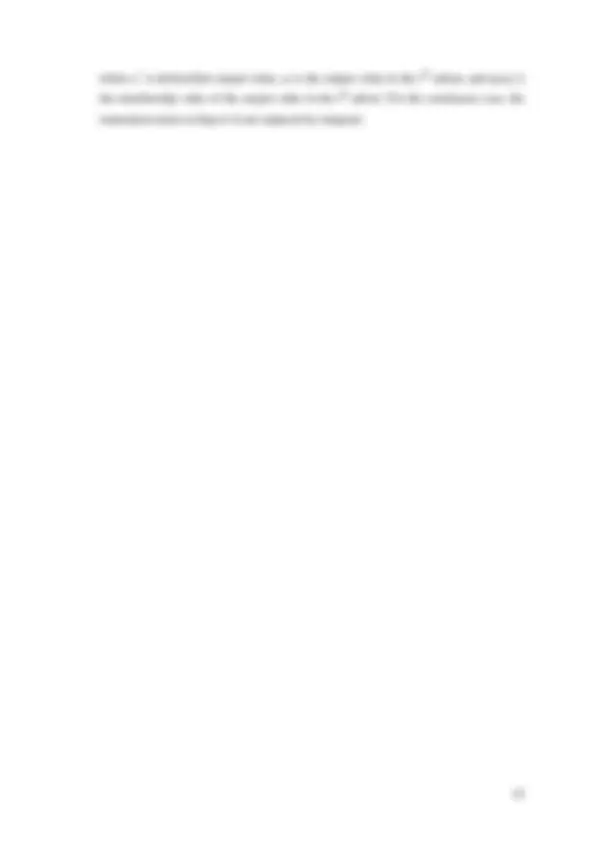
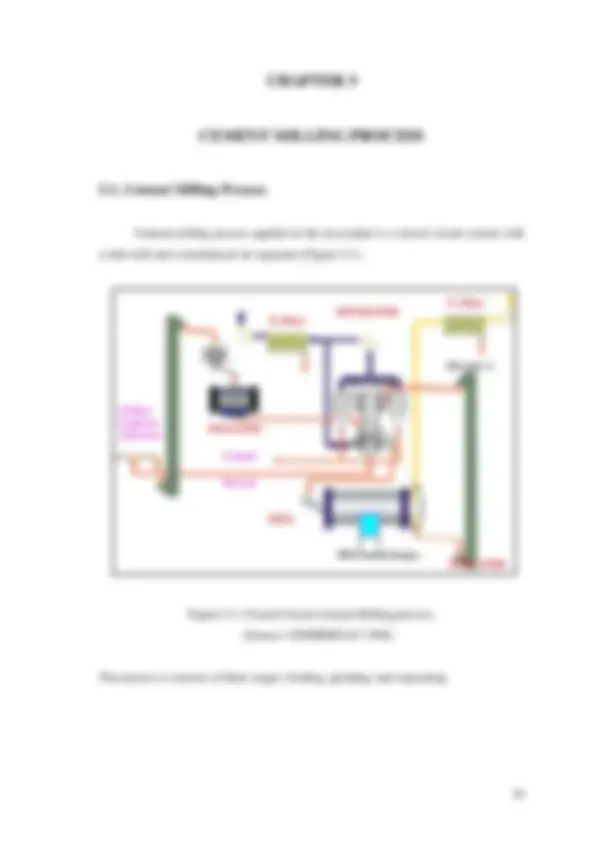
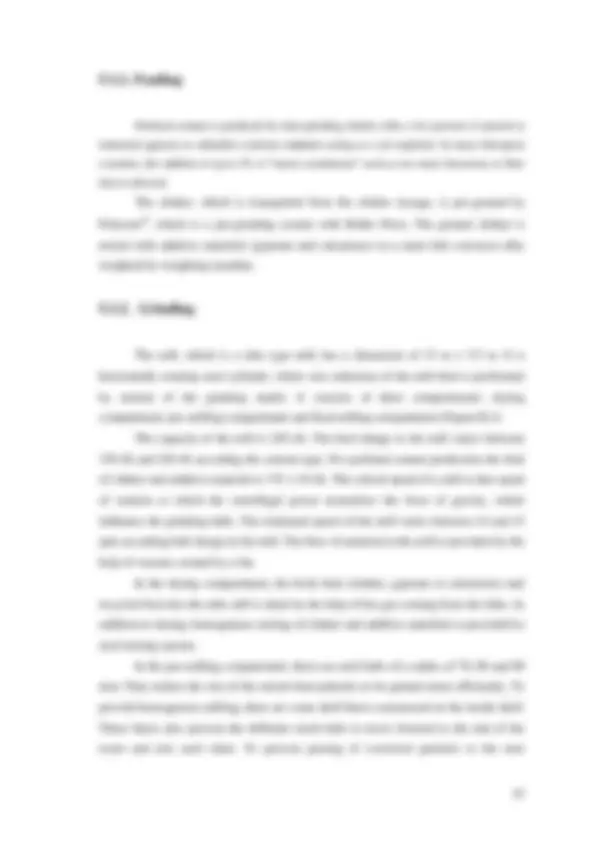
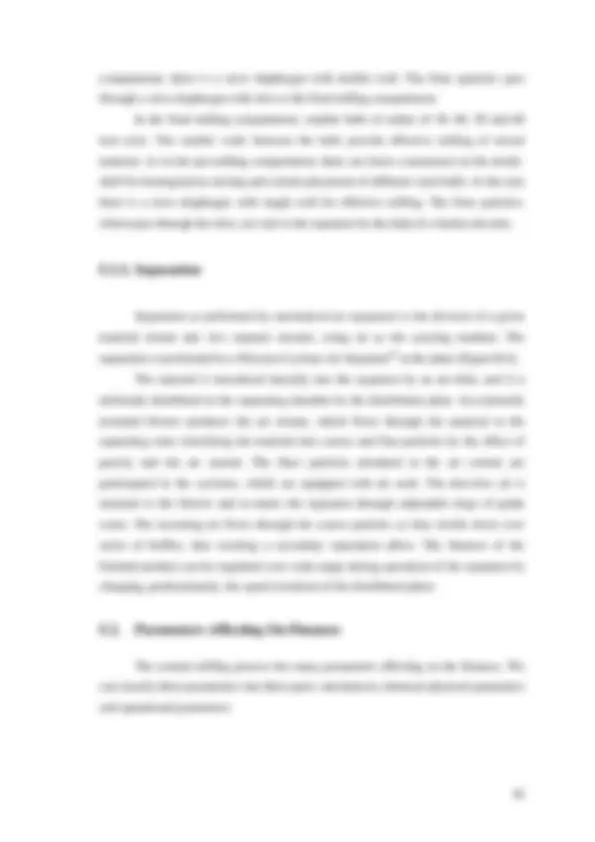
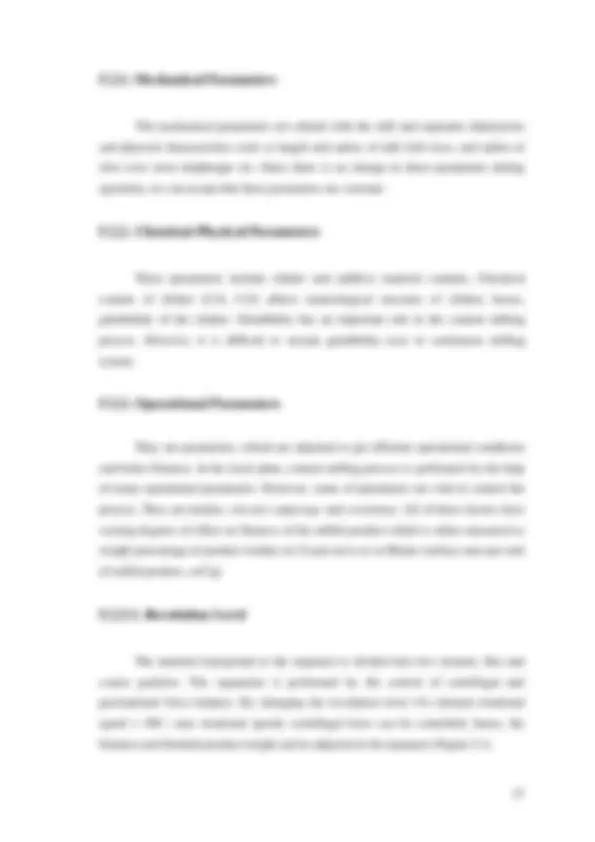
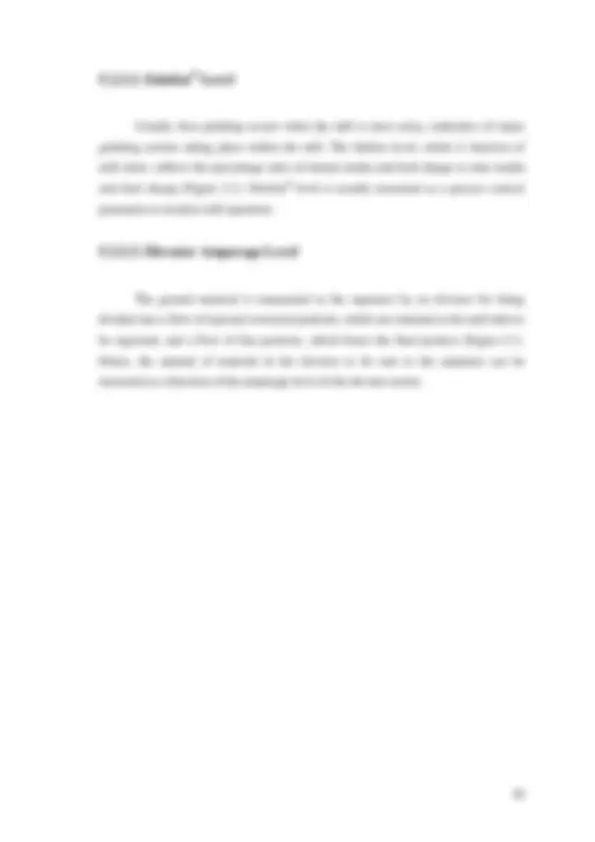
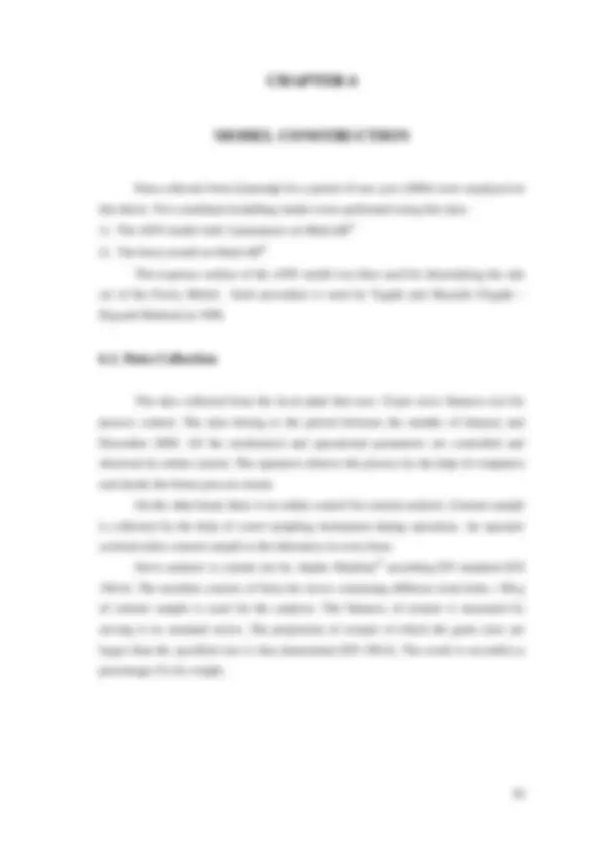
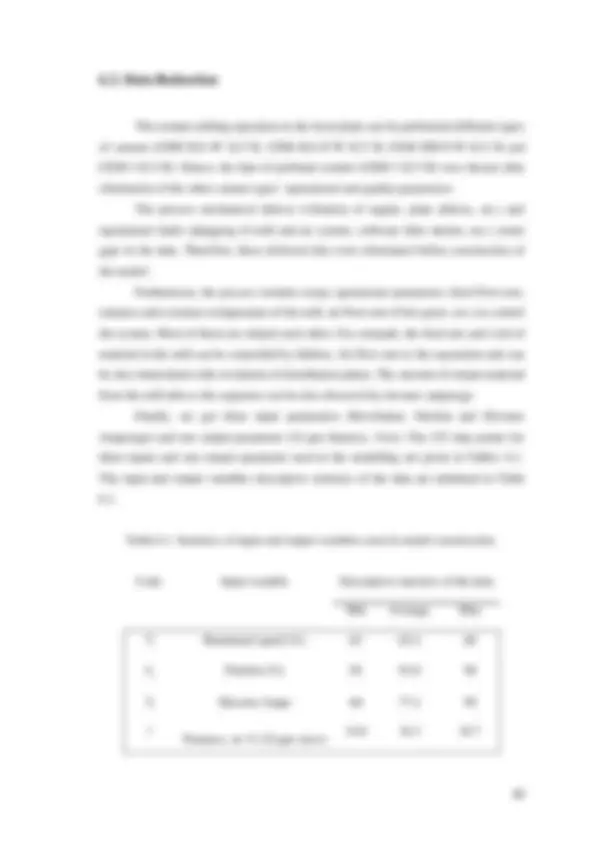
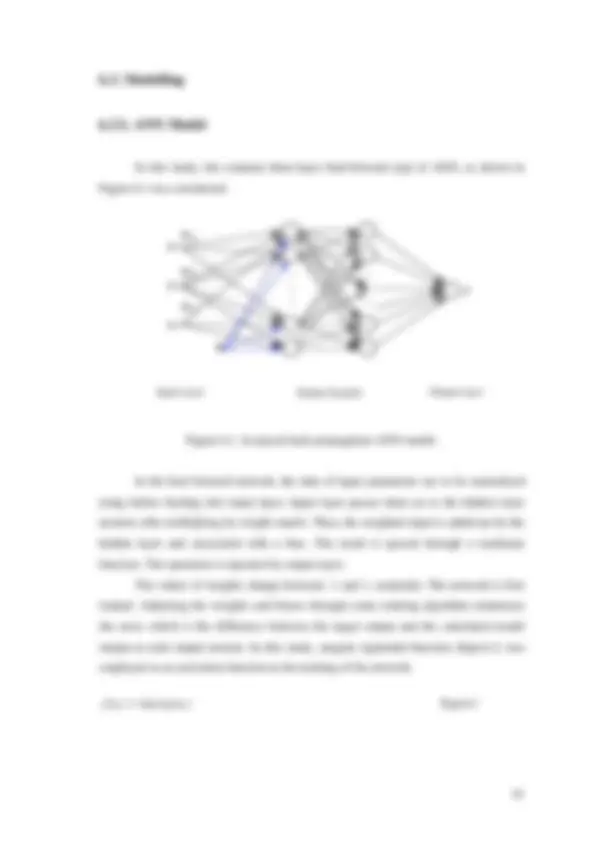
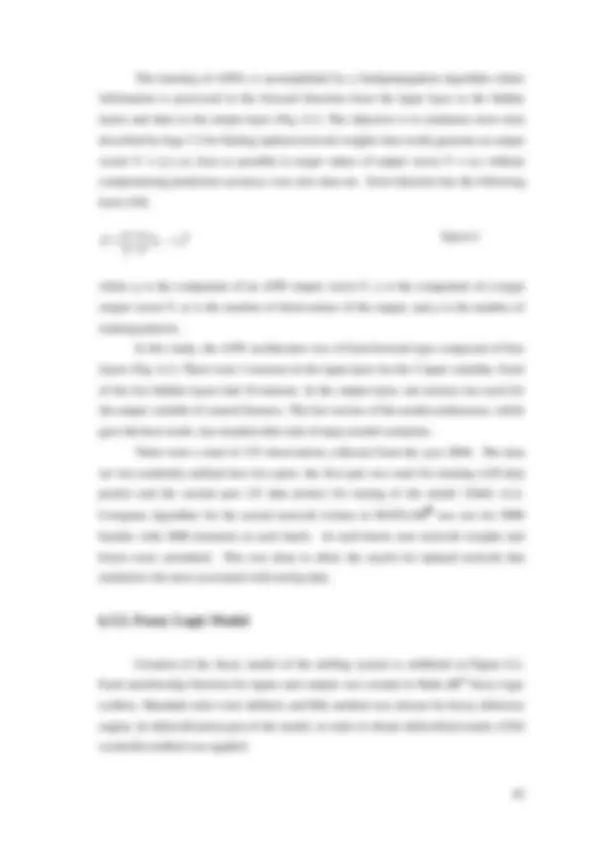
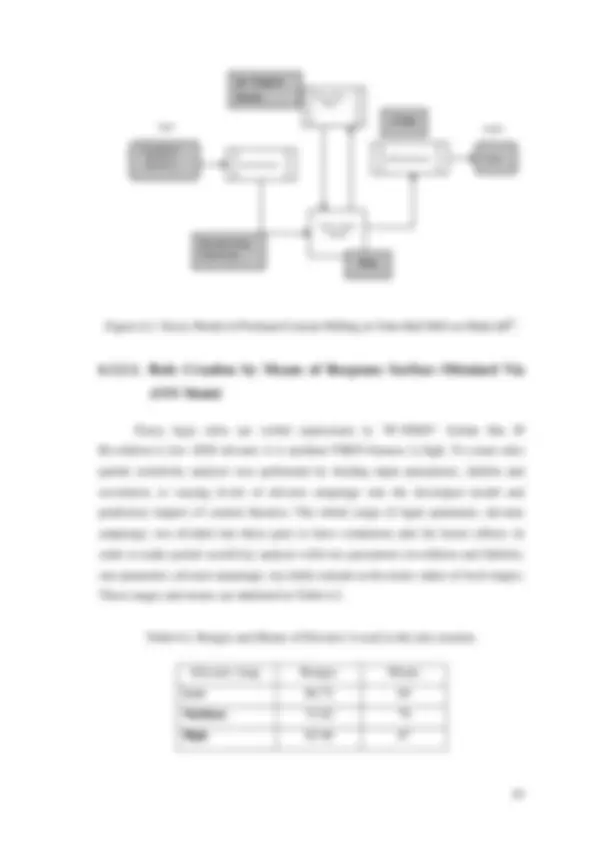
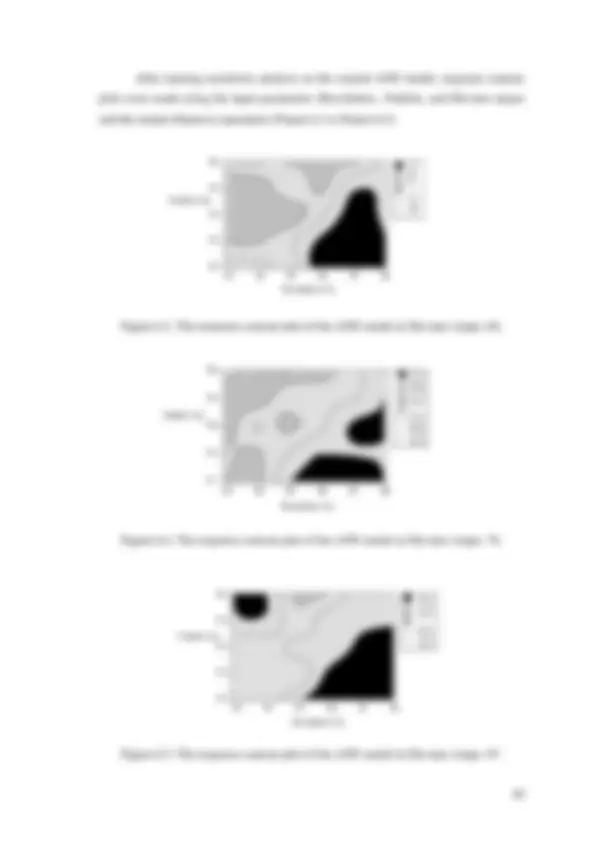
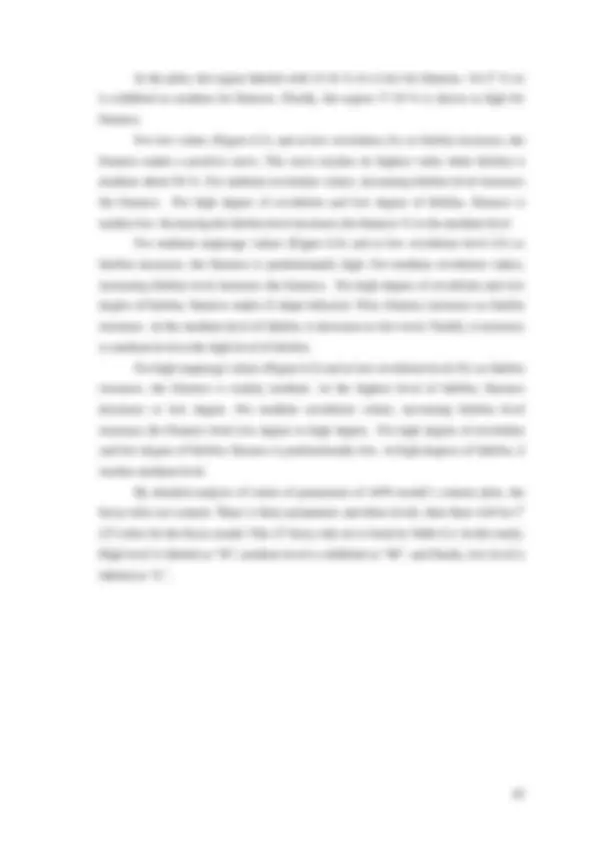
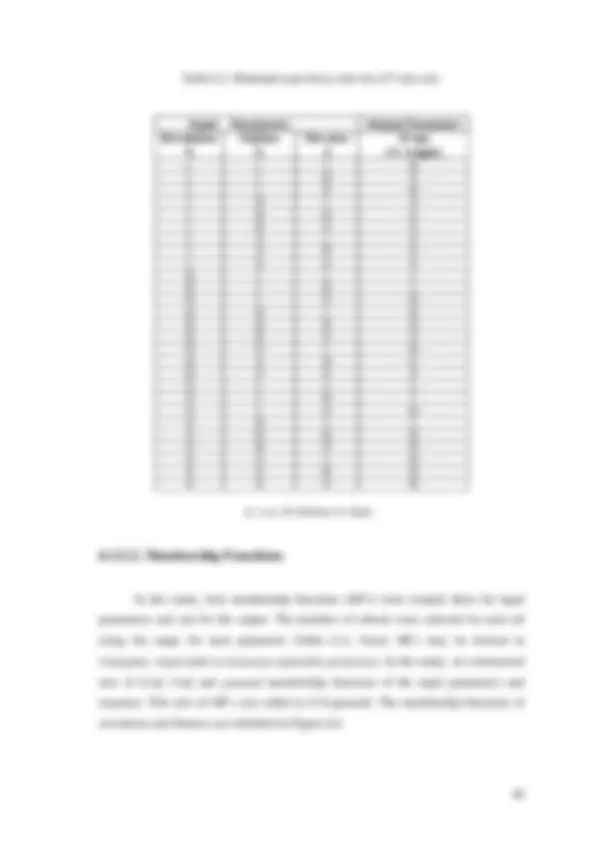
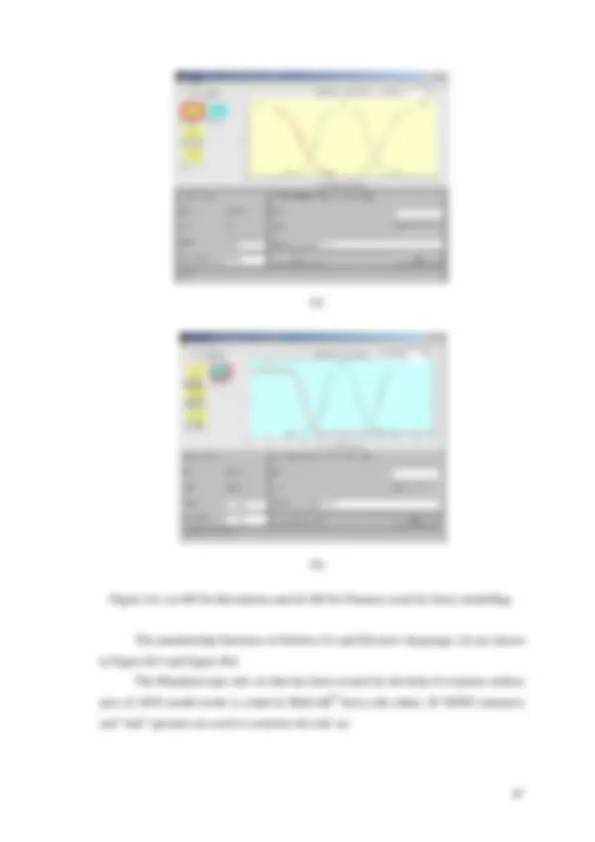
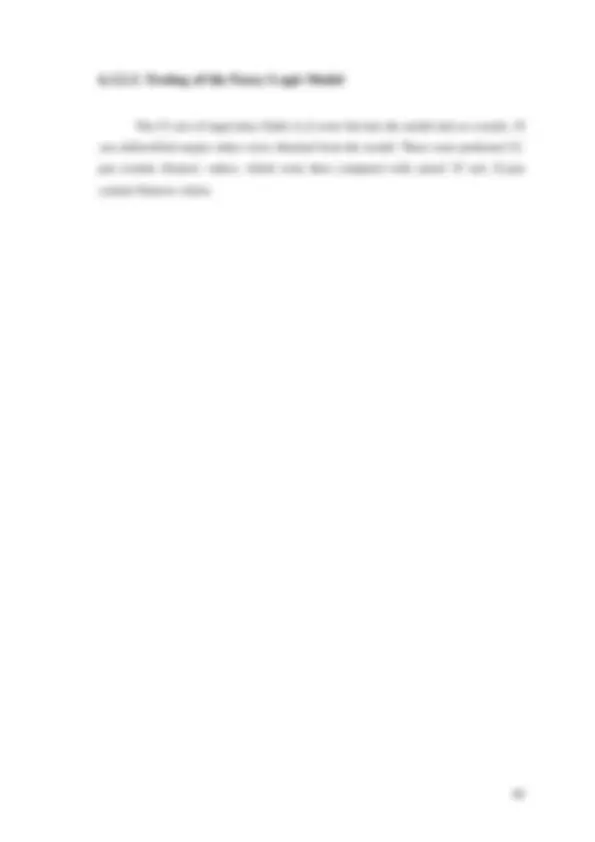
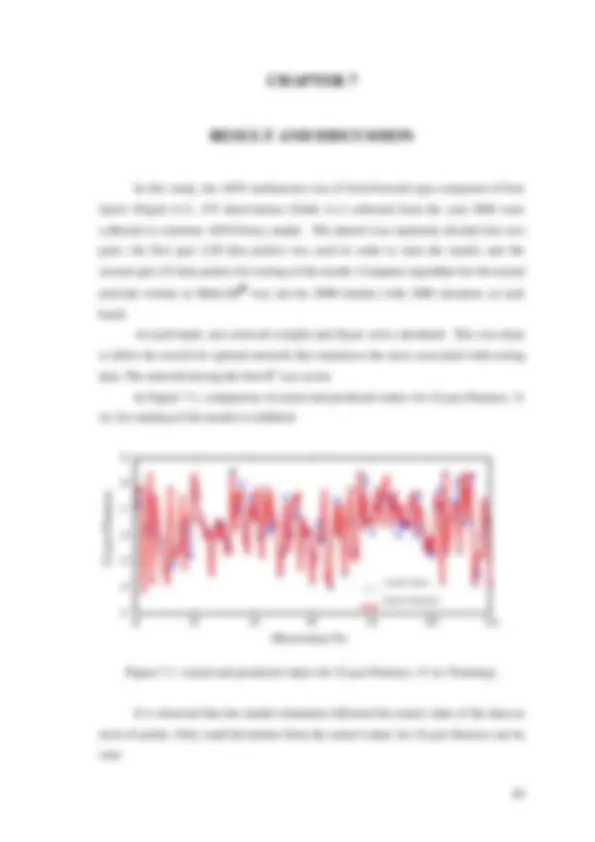
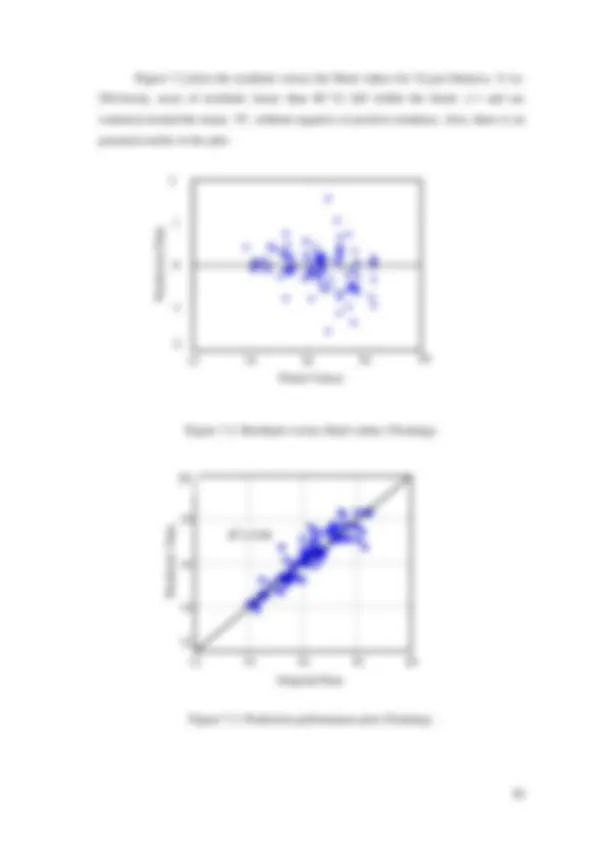
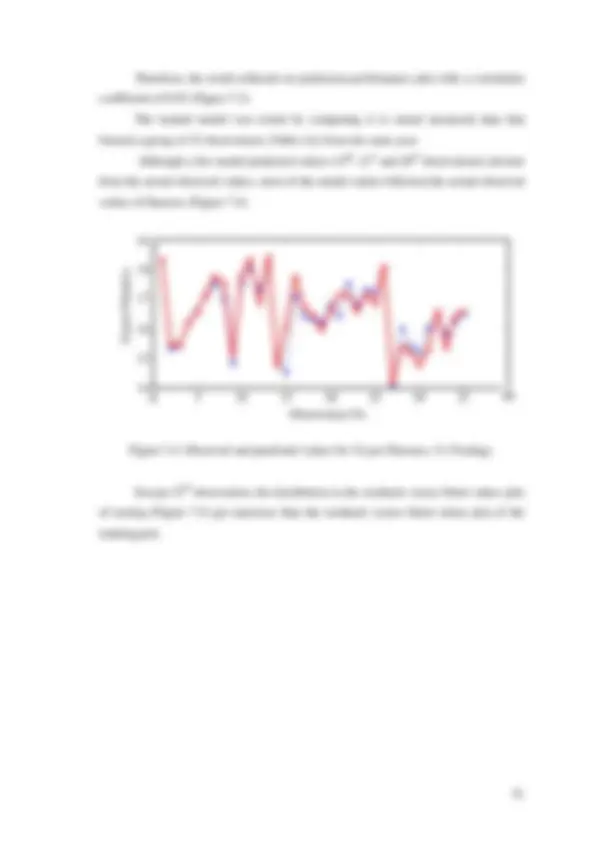
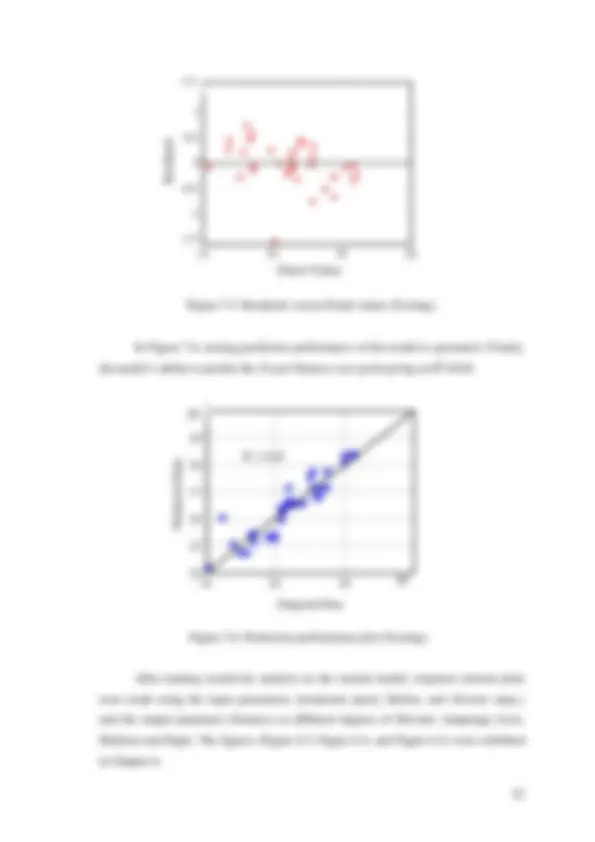
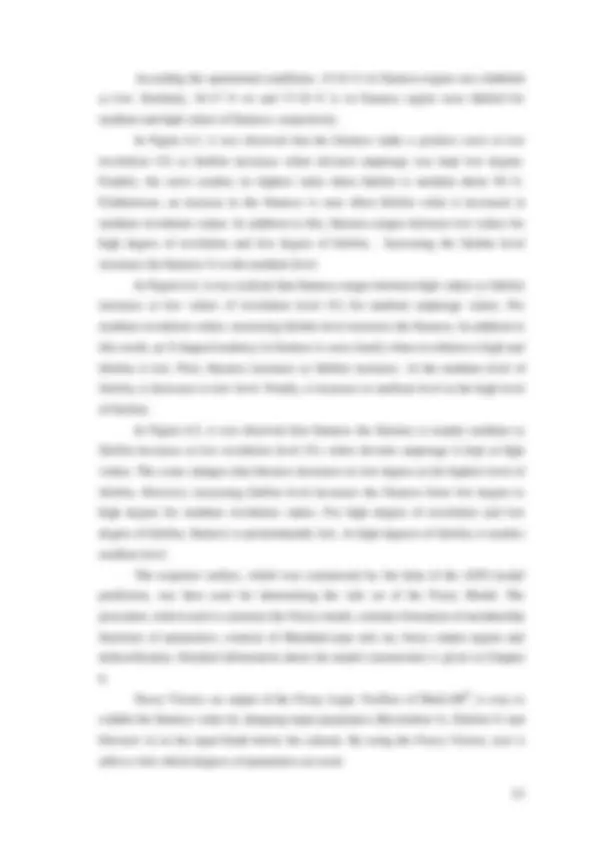
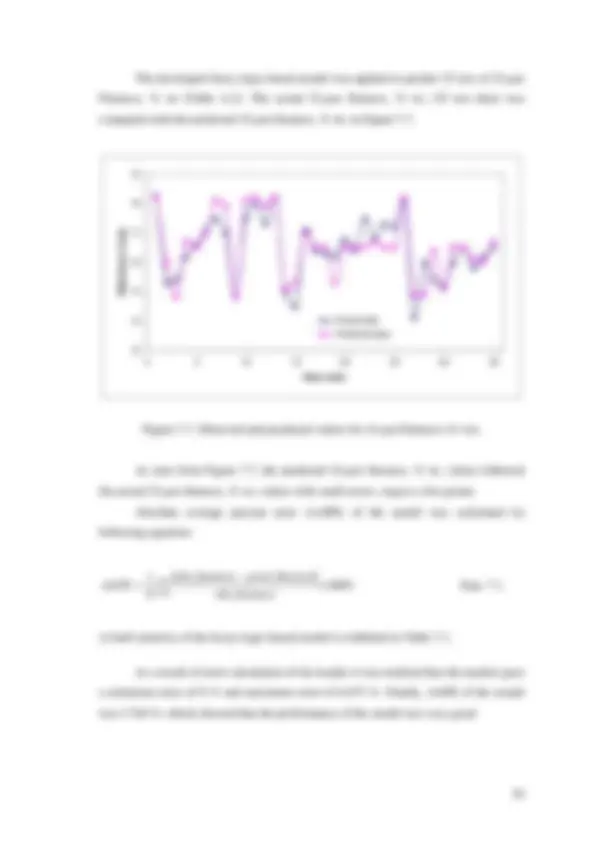
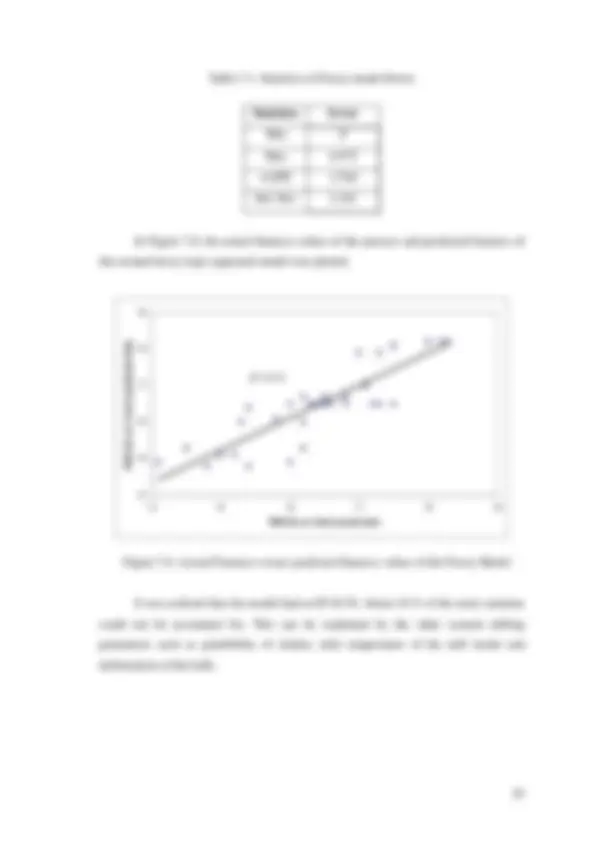
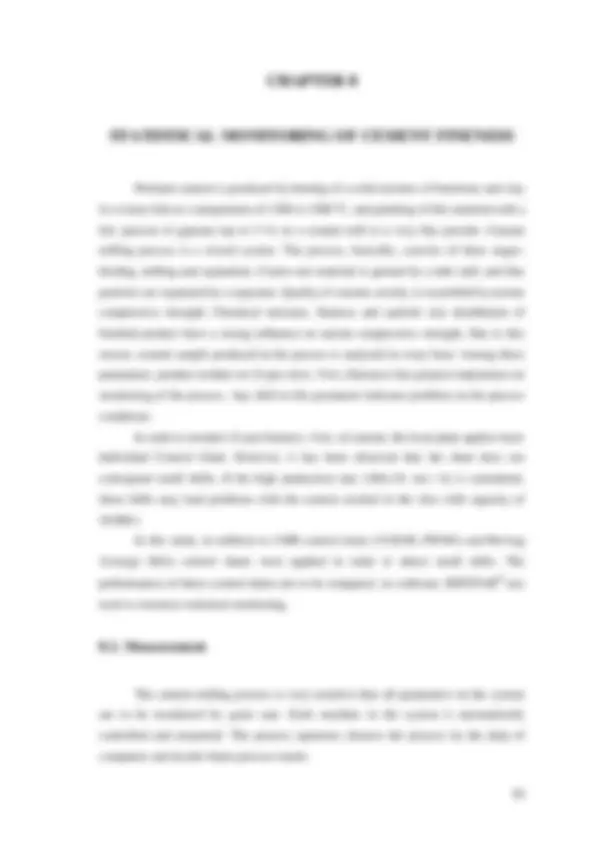
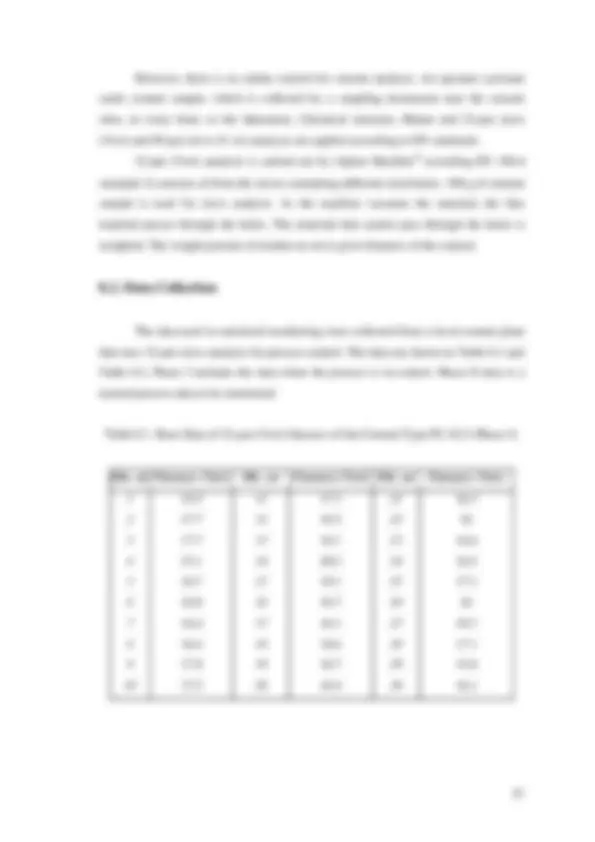
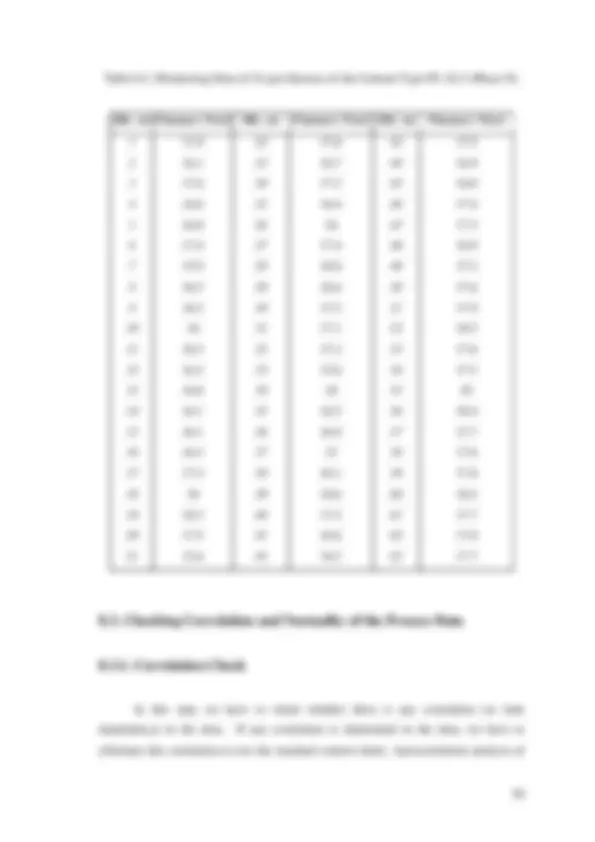
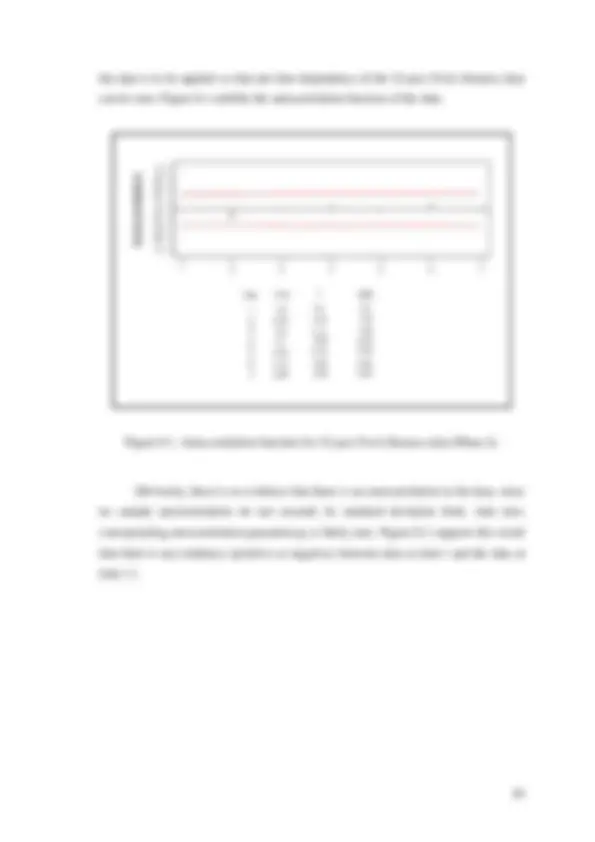
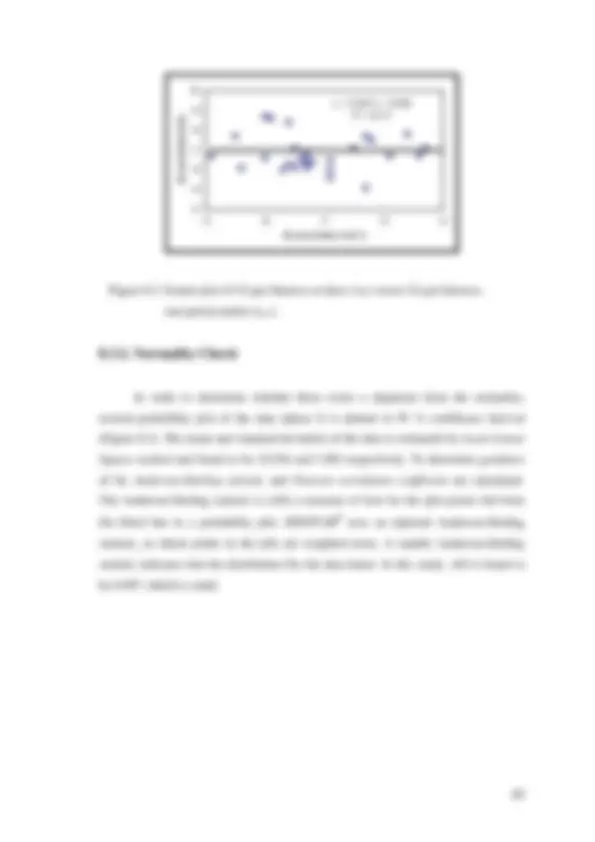
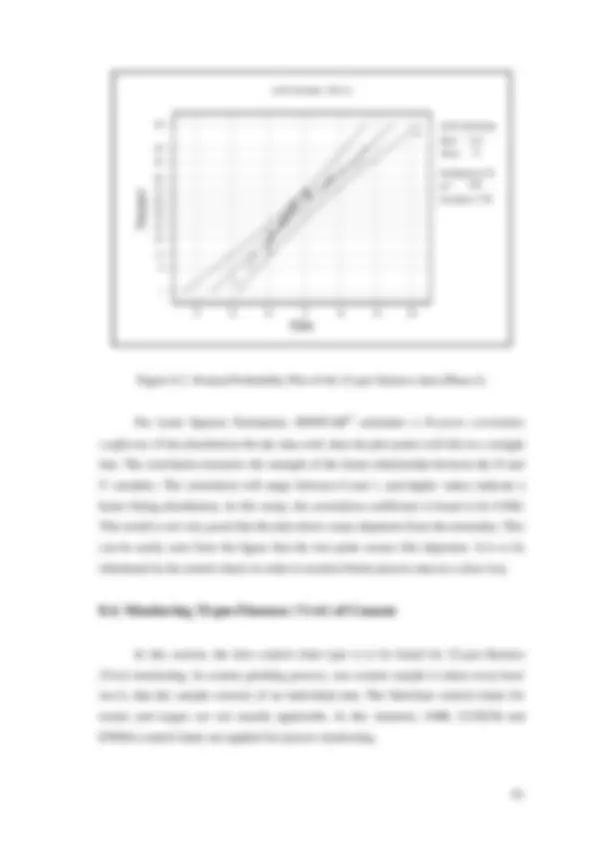
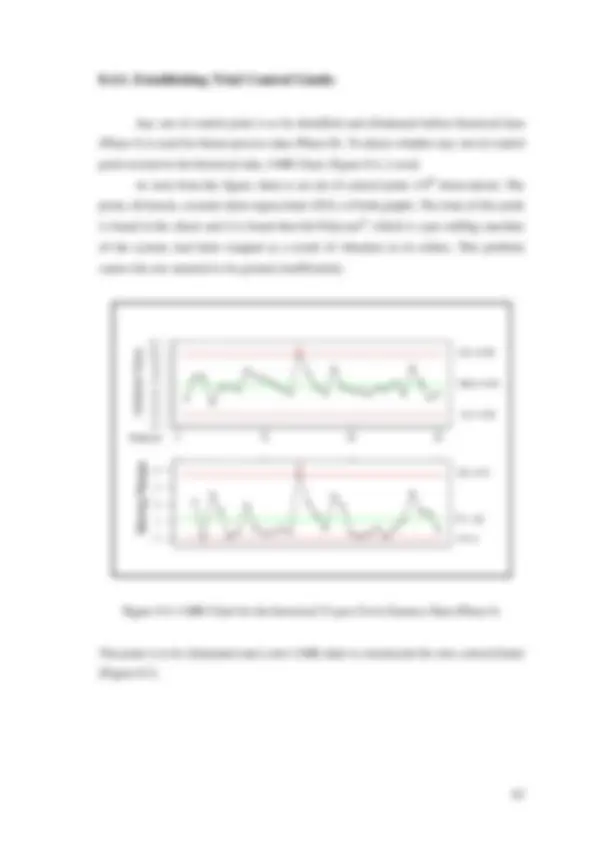
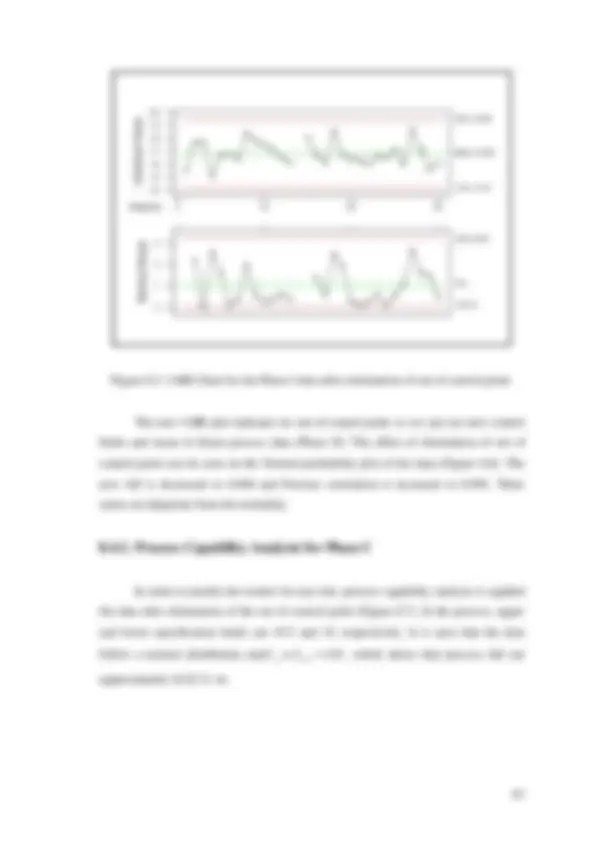
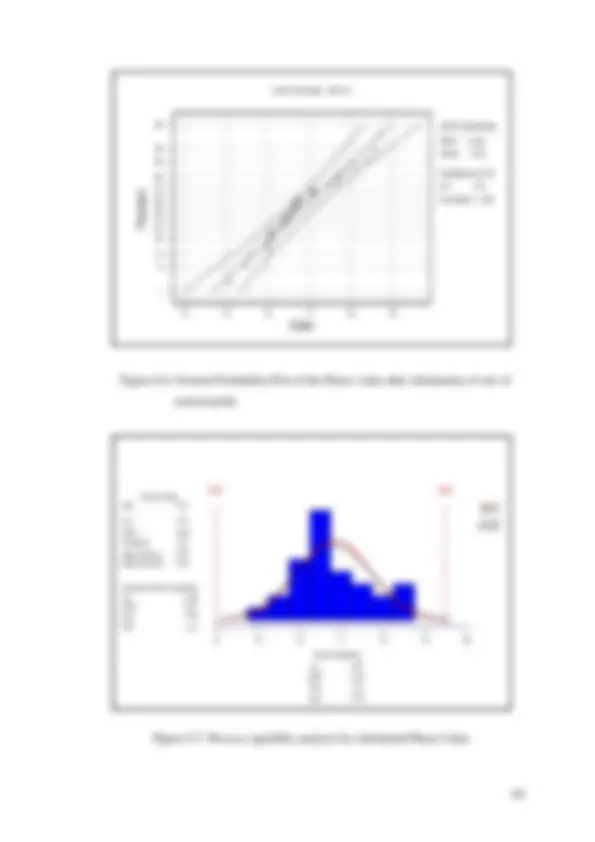
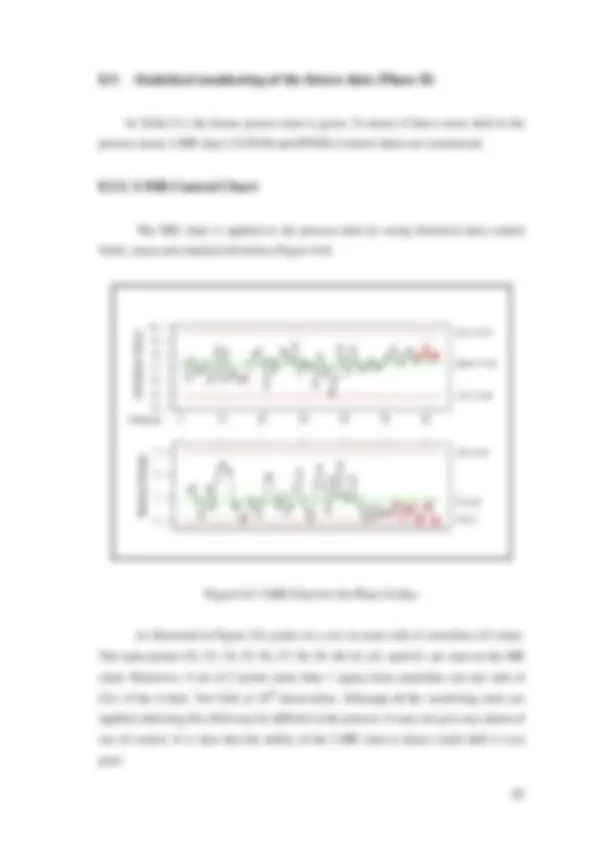
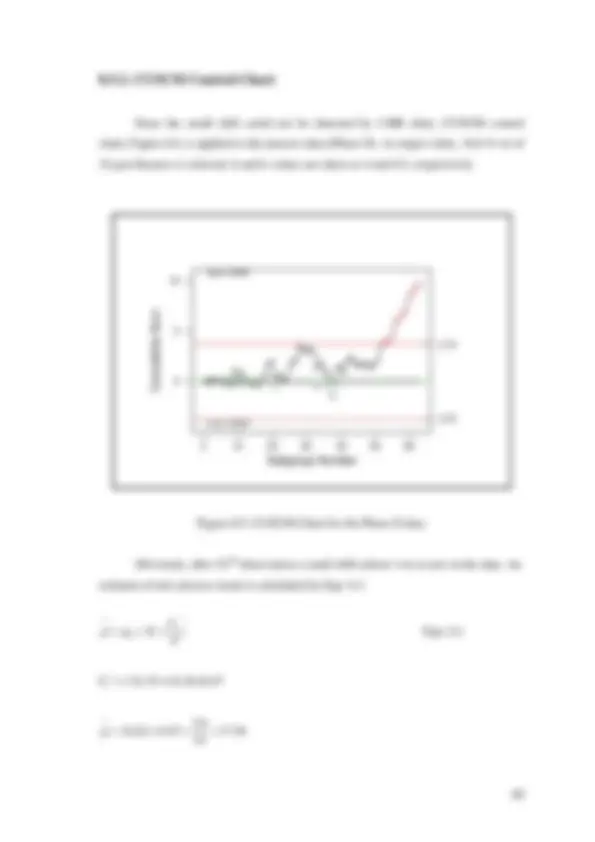
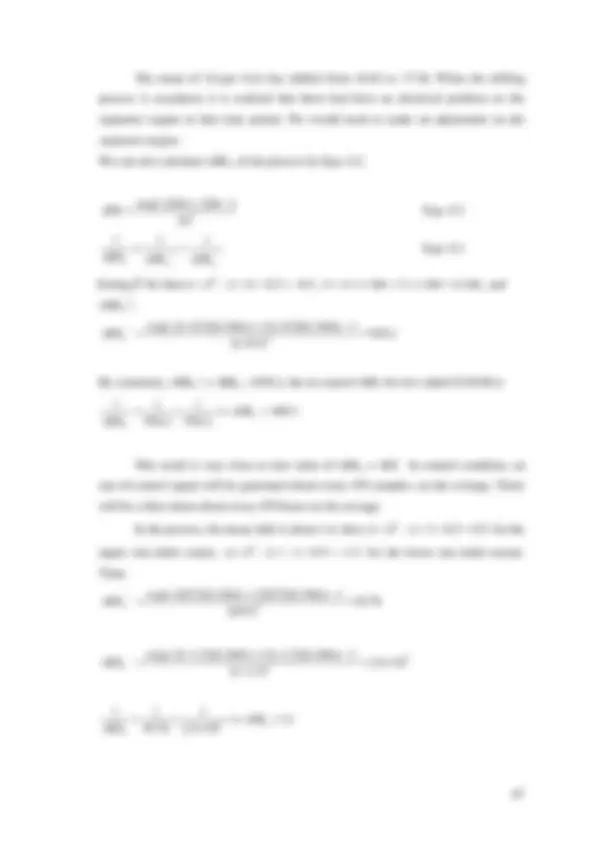
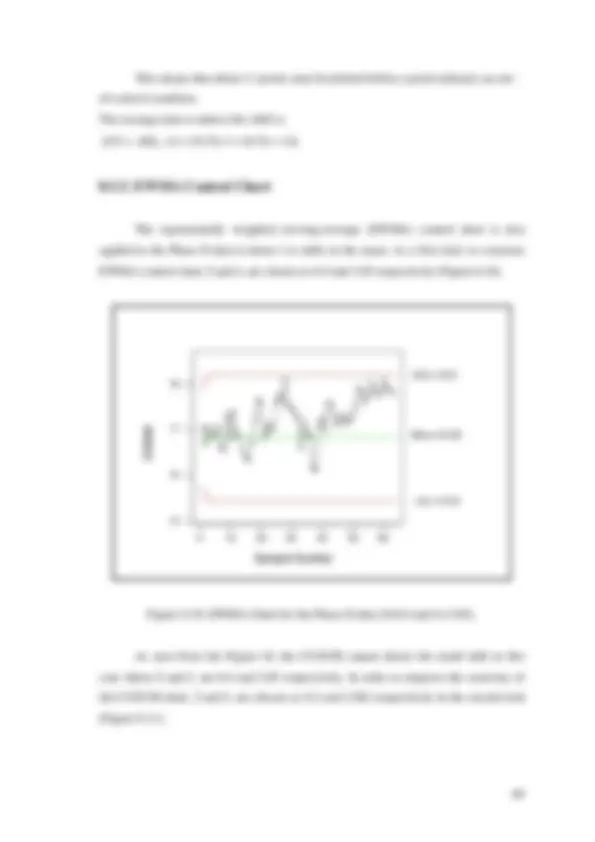
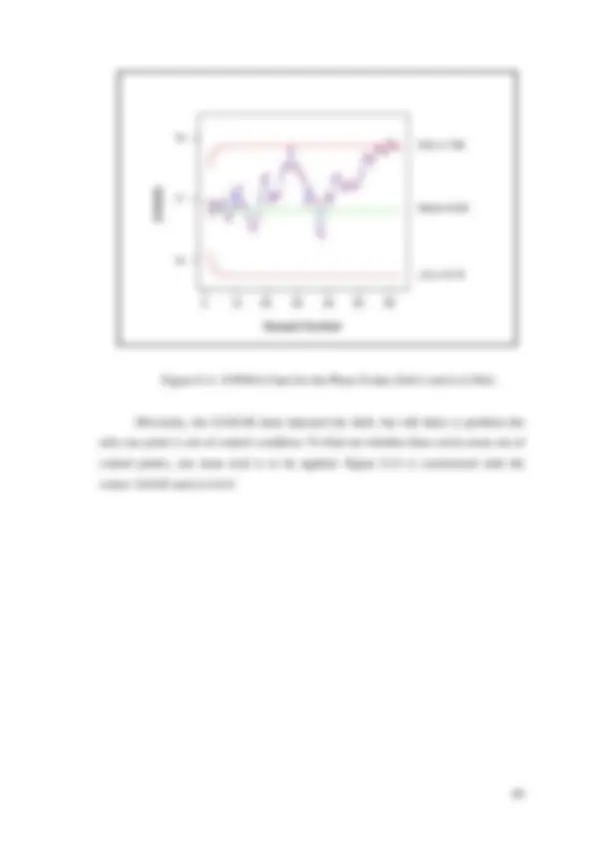
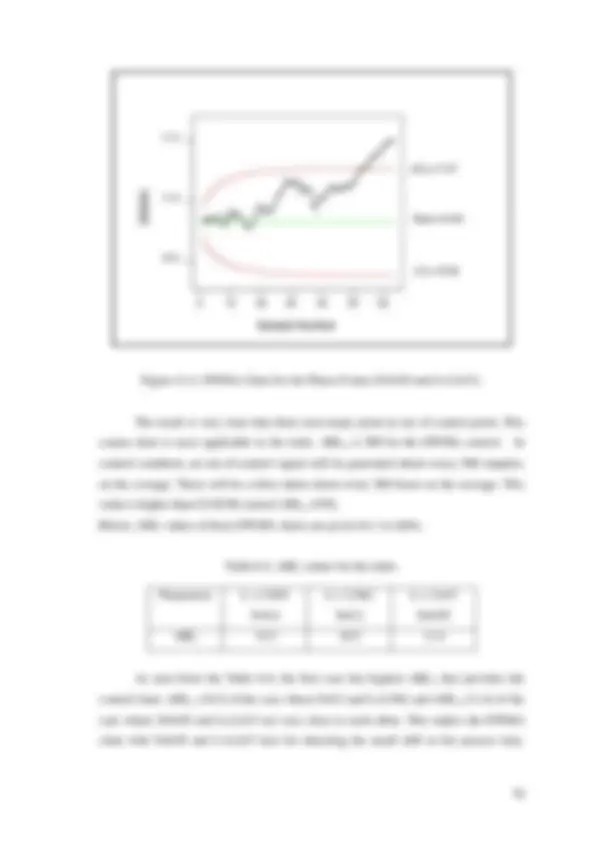
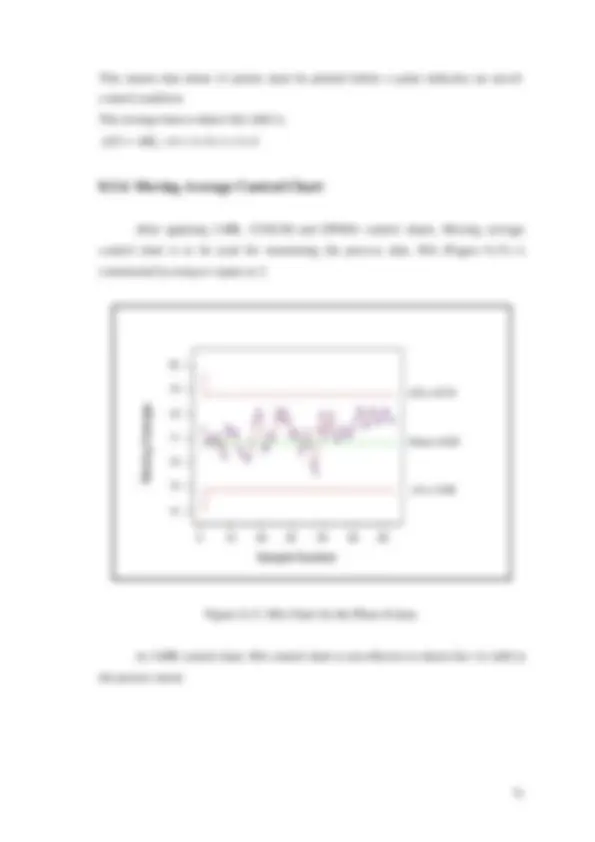
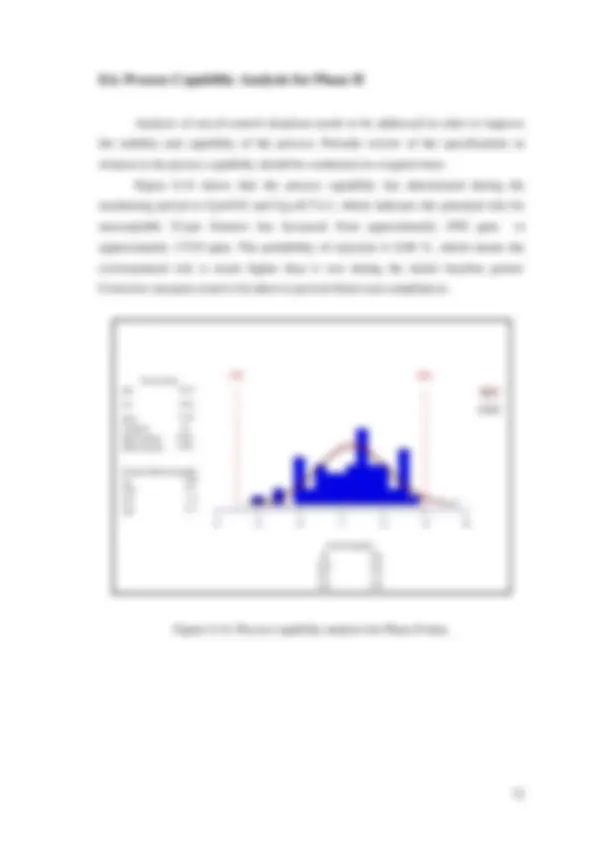
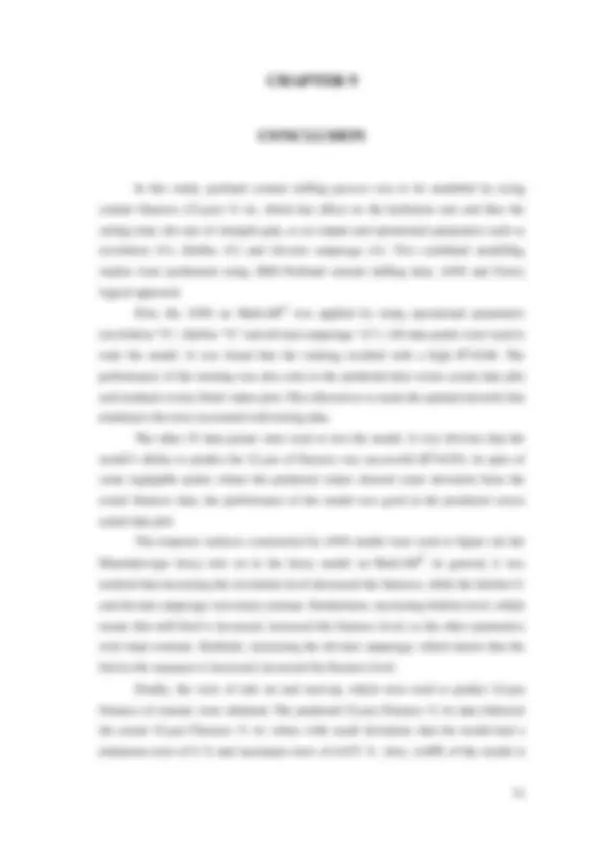
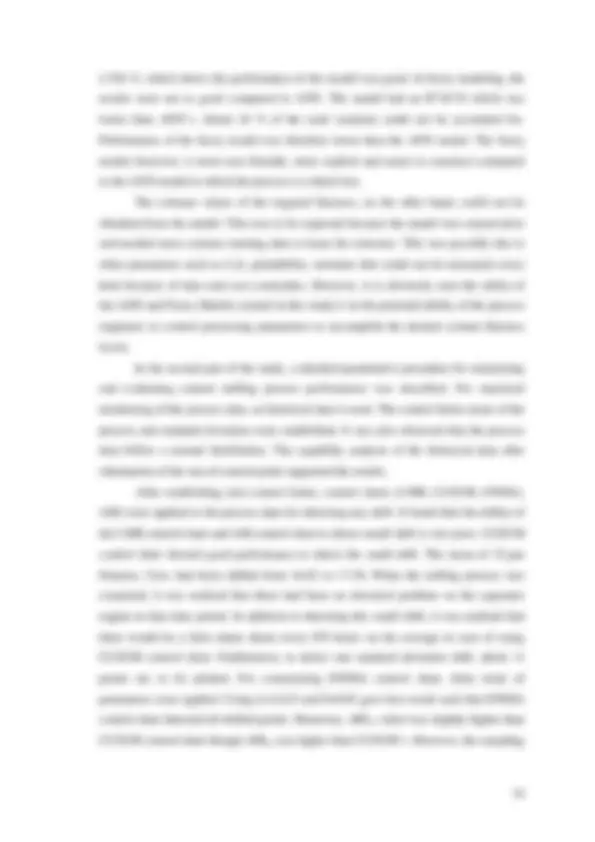
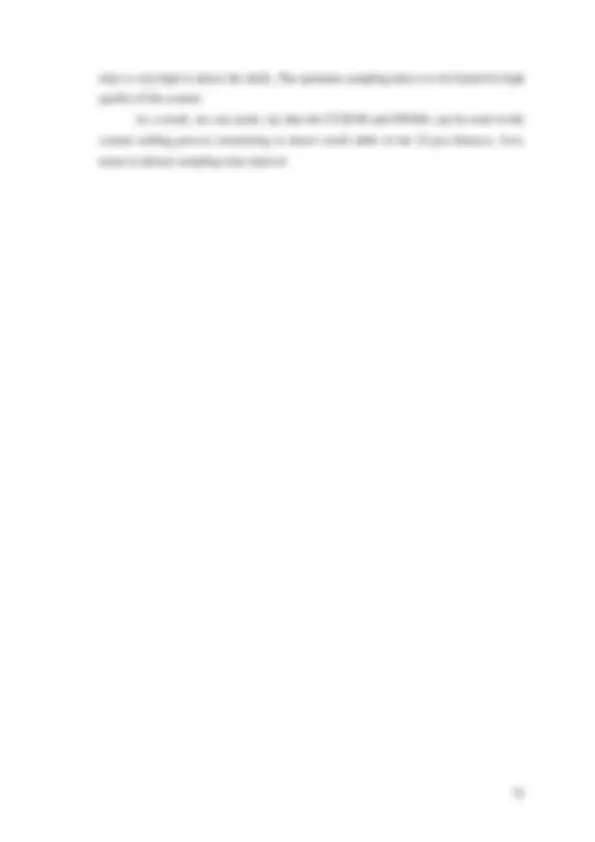
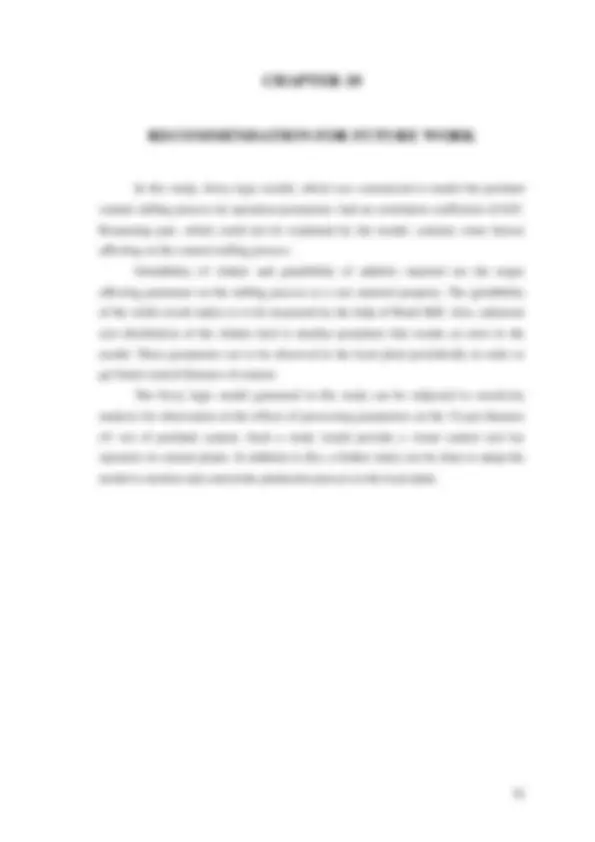
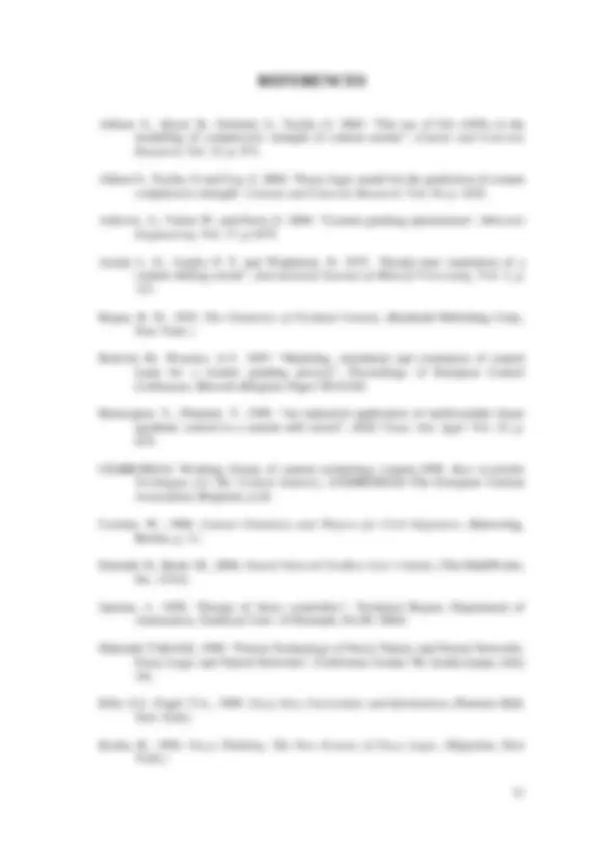
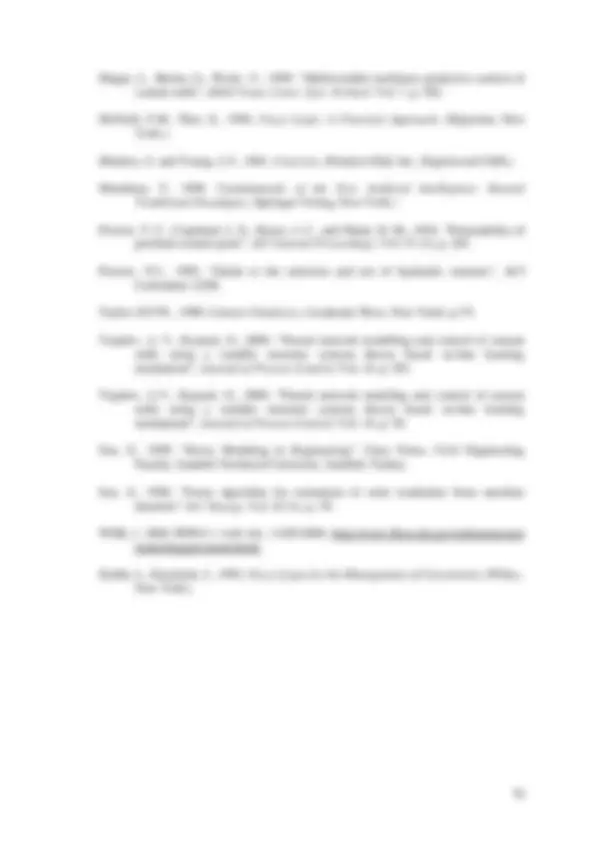

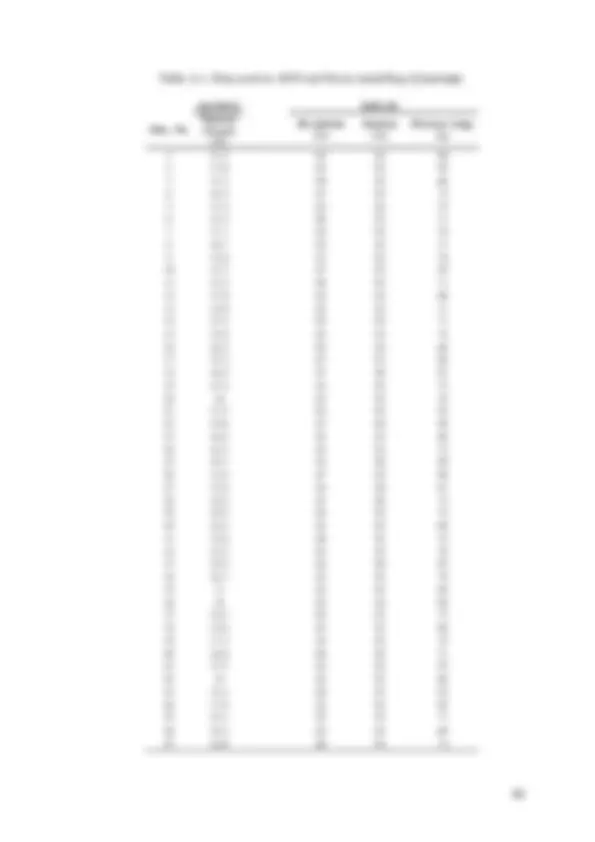
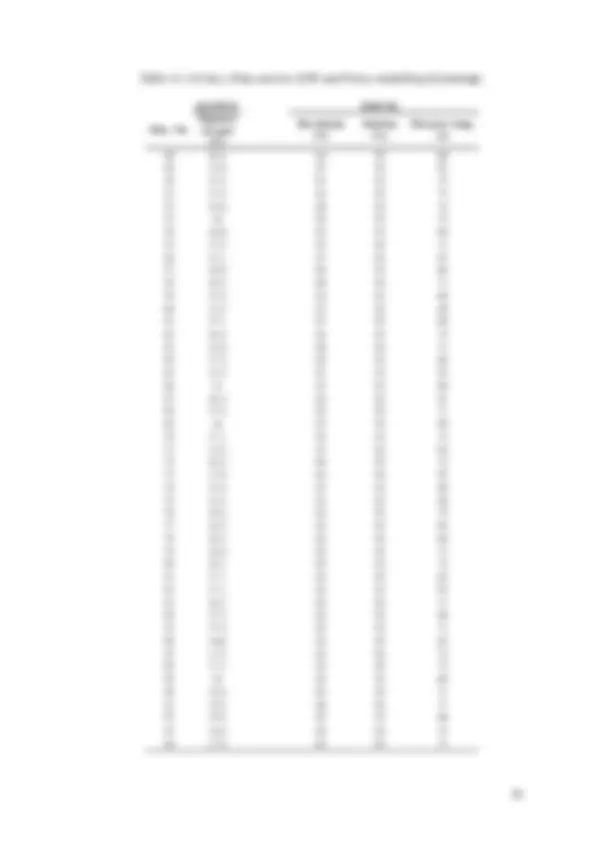
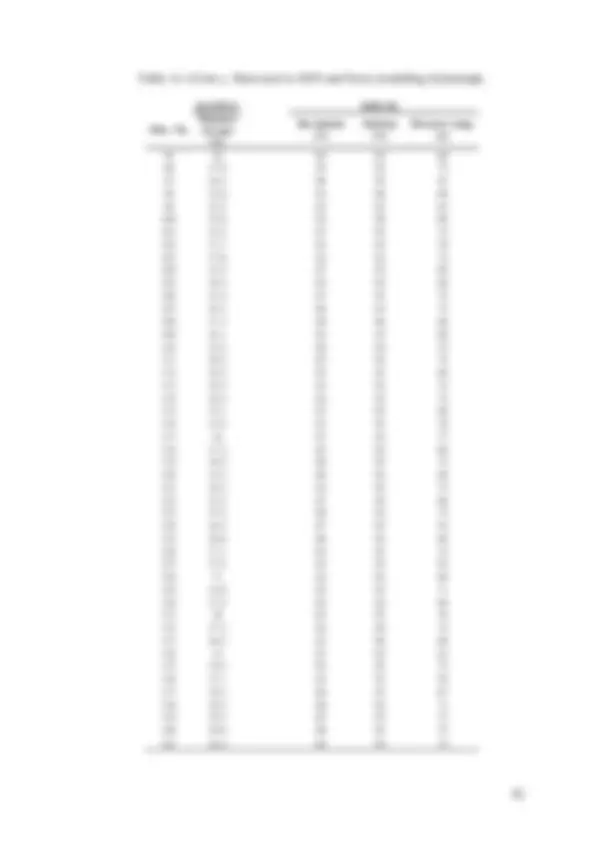
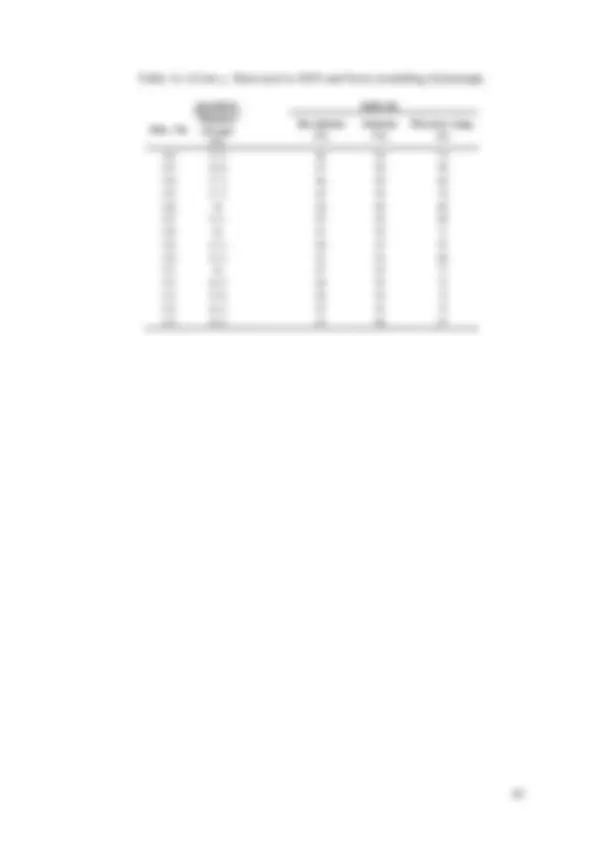
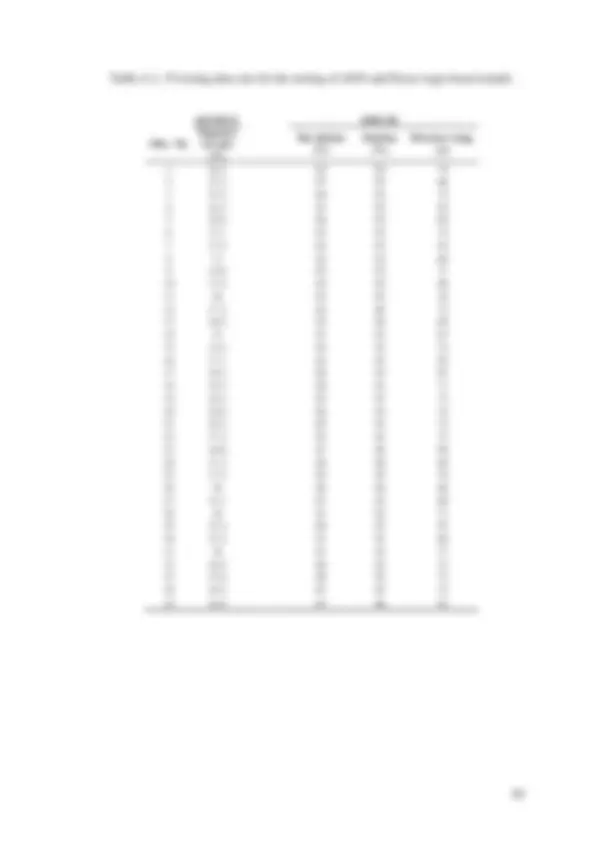
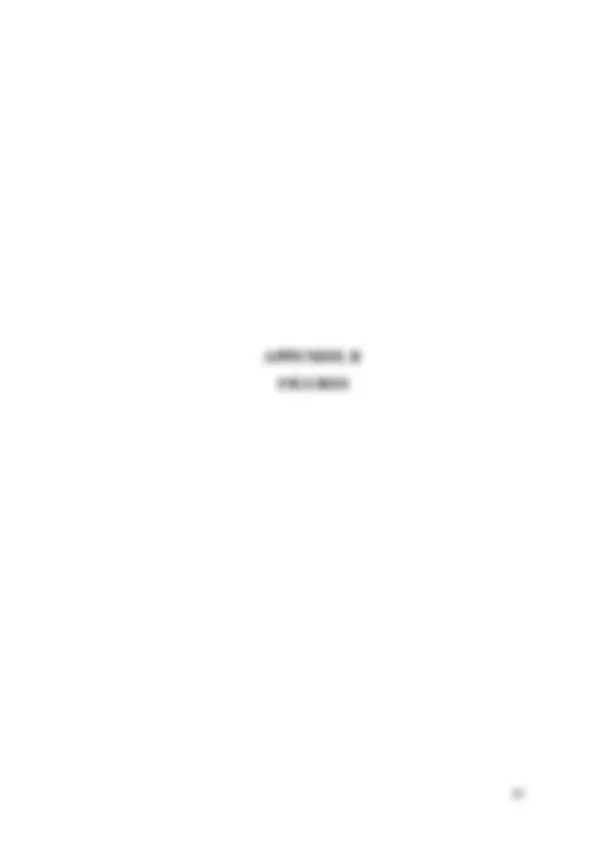
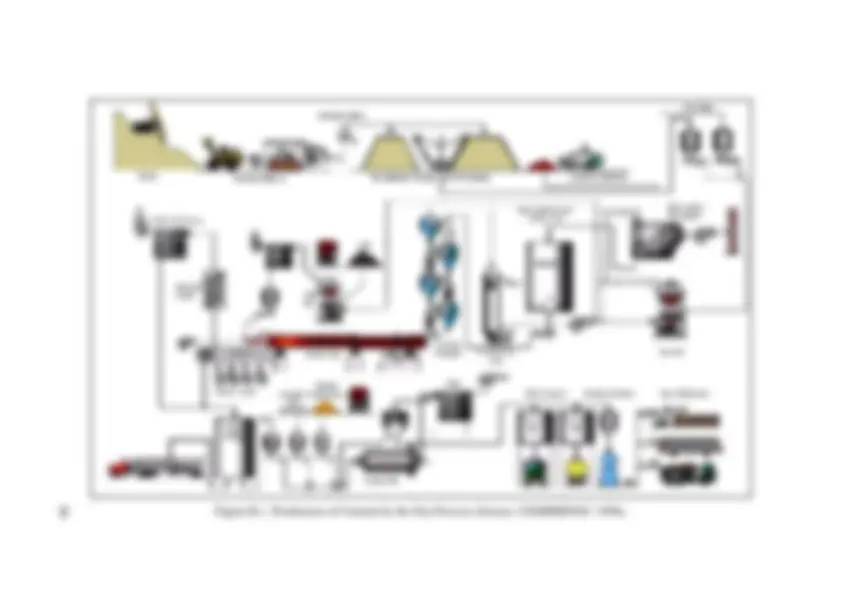
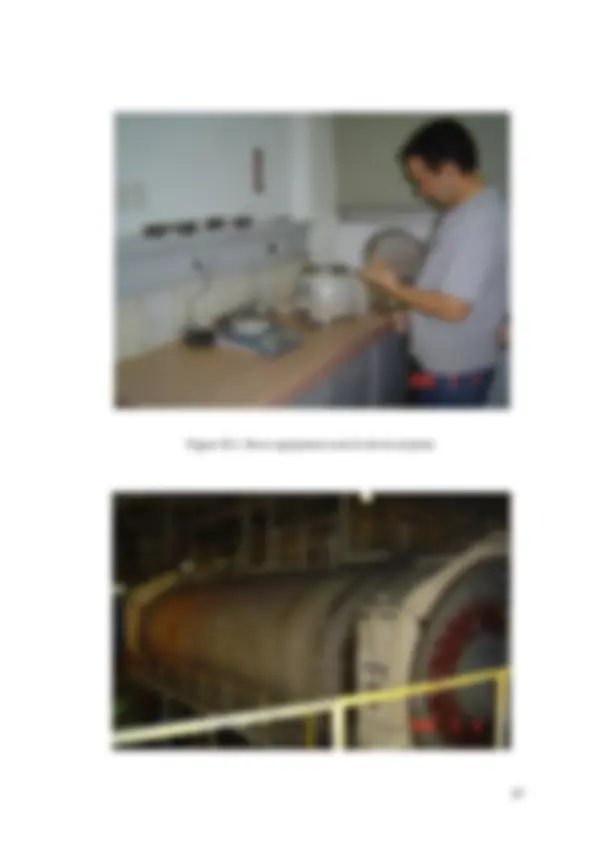
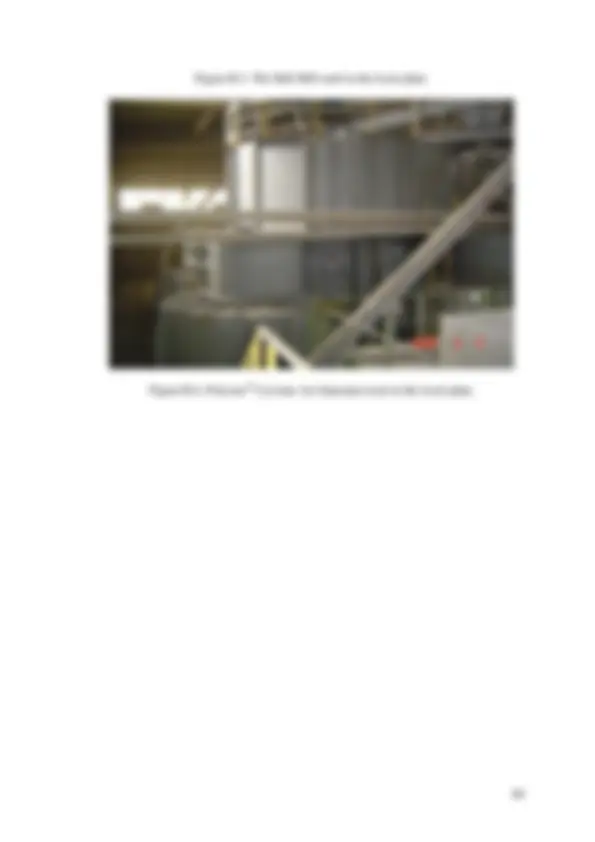
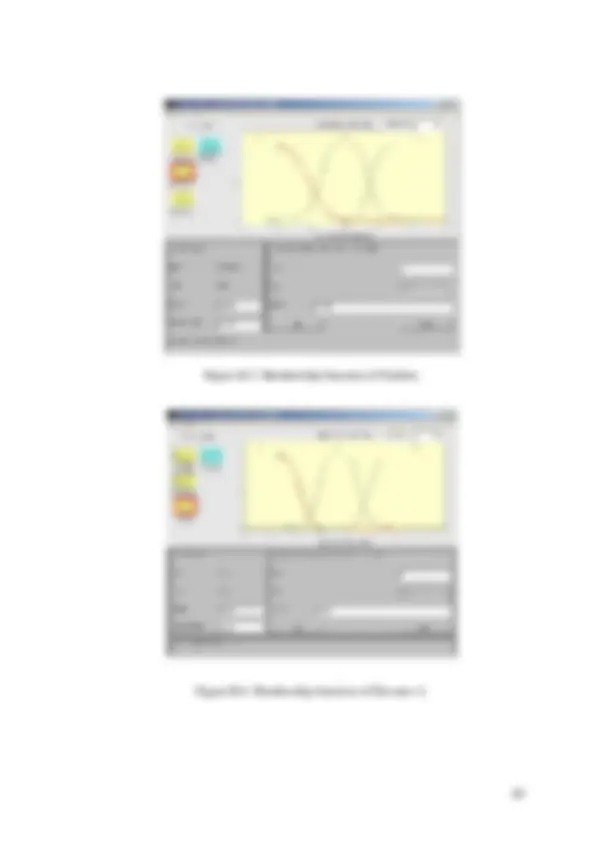
Study with the several resources on Docsity
Earn points by helping other students or get them with a premium plan
Prepare for your exams
Study with the several resources on Docsity
Earn points to download
Earn points by helping other students or get them with a premium plan
Community
Ask the community for help and clear up your study doubts
Discover the best universities in your country according to Docsity users
Free resources
Download our free guides on studying techniques, anxiety management strategies, and thesis advice from Docsity tutors
control optimization and monitoring of portland cement
Typology: Thesis
Uploaded on 11/29/2019
1 document
1 / 100
This page cannot be seen from the preview
Don't miss anything!
ii
We approve the thesis of Hakan AV AR
Date of Signature
…………………………………. 16 January 2006 Asst. Prof. Dr. Fuat DOYMAZ Supervisor Department of Chemical Engineering zmir Institute of Technology
…………………………… 16 January 2006 Assoc. Prof. Dr. Sedat AKKURT Co-Supervisor Department of Mechanical Engineering zmir Institute of Technology
…………………………….. 16 January 2006 Asst. Prof. Dr. Fikret NAL Department of Chemical Engineering zmir Institute of Technology
………………………………….. 16 January 2006 Asst. Prof. Dr. Serhan ÖZDEM R Department of Mechanical Engineering zmir Institute of Technology
……………………………….. 16 January 2006 Prof. Dr. Devrim BALKÖSE Head of Department zmir Institute of Technology
Assoc. Prof. Dr. Semahat ÖZDEM R Head of the Graduate School
iv
In this study, artificial neural networks (ANN) and fuzzy logic models were developed to model relationship among cement mill operational parameters. The response variable was weight percentage of product residue on 32-micrometer sieve (or fineness), while the input parameters were revolution percent, falofon percentage, and the elevator amperage (amps), which exhibits elevator charge to the separator. The process data collected from a local plant, Cimenta Cement Factory, in 2004, were used in model construction and testing. First, ANN (Artificial Neural Network) model was constructed. A feed forward network type with one input layer including 3 input parameters, two hidden layer, and one output layer including residue percentage on 32 micrometer sieve as an output parameter was constructed. After testing the model, it was detected that the model’s ability to predict the residue on 32- micrometer sieve (fineness) was successful (Correlation coefficient is 0.92). By detailed analysis of values of parameters of ANN model’s contour plots, Mamdani type fuzzy rule set in the fuzzy model on MatLAB was created. There were three parameters and three levels, and then there were third power of three (27) rules. In this study, we constructed mix of Z type, S type and gaussian type membership functions of the input parameters and response. By help of fuzzy toolbox of MatLAB, the residue percentage on 32-micrometer sieve (fineness) was predicted. Finally, It was found that the model had a correlation coefficient of 0.76. The utility of the ANN and fuzzy models created in this study was in the potential ability of the process engineers to control processing parameters to accomplish the desired cement fineness levels. In the second part of the study, a quantitative procedure for monitoring and evaluating cement milling process performance was described. Some control charts such as CUSUM (Cumulative Sum) and EWMA (Exponentially Weighted Moving Average) charts were used to monitor the cement fineness by using historical data. As a result, it is found that CUSUM and EWMA control charts can be easily used in the cement milling process monitoring in order to detect small shifts in 32-micrometer fineness, percentage by weight, in shorter sampling time interval.
v
Bu çalımada, çimento deirmeni iletme parametreleri arasındaki ilikiyi modellemek için yapay sinir ebekeleri ve bulanık mantık modelleri gelitirilmitir. Çıkı deikeni olarak 32 mikrometre elein üzerinde kalan ürünün aırlıkça yüzdesi (incelik) alınırken, giri parametreleri olarak devir yüzdesi, falofon yüzdesi ve elevatörden ayırıcıya giden maddenin miktarını gösteren elevatör akımı alınmıtır. Çimenta çimento fabrikasından 2004 yılına ait iletme verisi model kurumu ve test için kullanılmıtır. lk olarak, Yapay Sinir Aları modeli kurulmutur. Üç giri parametresini içeren bir giri, iki gizlenmi ve 32 mikrometre elek üzerinde kalan ürün (aırlıkça yüzde) çıkı parametresi olarak içeren bir çıkı tabakasından oluan bir ileri besleme aından oluturulmutur. Model test edildikten sonra modelin 32 mikrometre incelii tahmin etme yeteneinin yüksek olduu tespit edilmitir (Düzeltme katsayısı 0, bulunmutur.). Model üzerinde hassaslık analizi sonucunda karılık kontur grafikleri giri parametreleri kullanılarak oluturulmutur. Yapay Sinir Aları modelinin karılık kontur grafiklerinin parametre deerleri detaylı incelenmesiyle MatLAB’daki bulanık modelde Mamdani tipinde bulanık kural seti oluturulmutur. Üç parametre ve üç seviye olduu için üç üzeri üç (27) kural vardır. Bu çalımada, Z, S ve gauss tipindeki üyelik fonksiyonlarının karıımı ile oluturulmutur. MatLAB kullanım kutusunun yardımı ile 32 mikrometre incelik (aırlıkça yüzde) tahmin edilmitir. Sonuç olarak, modelin düzeltme katsayısı (R) 0,76 bulunmutur. Bu çalımada oluturulan YSA ve bulanık modeller, iletme mühendislerine istenilen çimento inceliine ulamak için iletme parametrelerini kontrolünde potansiyel yeterlilikte yarar göstermektedir. Çalımamızın ikinci kısmında, çimento öütüm sürecinin performansını deerlendirmek ve süreci denetlemek için nicel bir izlek tanımlanmıtır. Tarihsel veri kullanılarak, CUSUM (gittikçe artan toplam) ve EWMA (üssel ölçülmü hareketli ortalama) grafikleri gibi kontrol grafikleri çimento inceliini denetlemek için kullanılmıtır. Sonuç olarak, CUSUM ve EWMA kontrol grafiklerinin 32 mikrometre inceliindeki, (aırlıkça yüzde) küçük sapmaları tespit etmek için çimento öütüm sürecinde daha kısa süreli örnek alım zaman aralıklarında kolayca kullanılabilecei bulunmutur.
x
Figure 7.8. Actual Fineness vs predicted Fineness values of the fuzzy Model ......................................................................................................... 55 Figure 8.1. Autocorrelation function for 32-m (%wt) fineness data (Phase I)................................................................................................................. 59 Figure 8.2. Scatter plot of 32-m (%wt) fineness at time t (xt) versus 32 - m (%wt) fineness one period earlier (xt-1) ............................................... 60 Figure 8.3. Normal Probability Plot of the 32-m (%wt) fineness data (Phase I) ..................................................................................................... 61 Figure 8.4. I-MR Chart for the historical 32-m (%wt) fineness Data (Phase I) ..................................................................................................... 62 Figure 8.5. I-MR Chart for the Phase I data after elimination of out of control point............................................................................................... 63 Figure 8.6. Normal Probability Plot of the Phase I data after elimination of out of control point .................................................................................... 64 Figure 8.7. Process capability analysis for eliminated Phase I data............................. 64 Figure 8.8. I-MR Chart for the Phase II data ............................................................... 65 Figure 8.9. CUSUM Chart for the Phase II data .......................................................... 66 Figure 8.10. EWMA Chart for the Phase II data (=0,4 and L=3,05) ........................... 68 Figure 8.11. EWMA Chart for the Phase II data (=0,2 and L=2,962) ......................... 69 Figure 8.12. EWMA Chart for the Phase II data (=0,05 and L=2,615) ....................... 70 Figure 8.13. MA Chart for the Phase II data.................................................................. 71 Figure 8.14. Process capability analysis for Phase II data ............................................. 72 Figure B.1. Production of Cement by the Dry Process................................................. 86 Figure B.2. Sieve equipment used in the local plant..................................................... 87 Figure B.3. The Ball Mill used in the local plant.......................................................... 87 Figure B.4. Polysius Cyclone Air Separator^ used in the local plant ........................... 88 Figure B.5. Membership function of Falofon ............................................................... 89 Figure B.6. Membership function of Elevator A .......................................................... 89
xi
Table Page Table 2.1. Raw materials used in cement industry .......................................................... 4 Table 2.2. Phases of clinker ............................................................................................. 7 Table 3.1. Portland cement types and their uses............................................................ 11 Table 3.2. Main Constituents in a Typical Portland Cement ........................................ 13 Table 3.3. Effects of cements on concrete properties .................................................... 17 Table 6.1. Statistics of input and output variables used in model construction................................................................................................... 40 Table 6.2. Ranges and Means of Elevator A used in the rule creation .......................... 43 Table 6.3. Mamdani-type fuzzy rule sets (27 rule-set) .................................................. 46 Table 7.1. Statistics of Fuzzy model Errors................................................................... 55 Table 8.1. Base Data of 32-m (%wt) fineness of the Cement Type CEM I 42.5 (Phase I) ................................................................................................ 57 Table 8.2. Monitoring Data of 32-m (%wt) fineness of the Cement Type CEM I 42.5 (Phase II)................................................................................... 58 Table 8.4. ARL values for the trials............................................................................... 70 Table A.1. Data used in the modeling (Çimenta).......................................................... 80 Table A.2. 35 testing data sets used in the testing of fuzzy logic-based model ............. 84
ANN (Grognard 2001) and fuzzy logic models (Akyol et al. 2003) were previously used for cement strength prediction. However, the use of fuzzy logic and ANN modelling for cement fineness prediction has not yet been reported. In this study, our objectives are to predict the fineness before any variations in process parameters, to decrease the errors arisen from the operators, to increase the efficiency and finally decrease the process cost. In order to get these targets, residue on 32-m sieve (or fineness) of portland cement is to be predicted by using Tube Mill operational parameters: revolution “%” (instant rotational speed x 100 / max rotational speed), falofon “%” (instant media and feed charge/max charge), and elevator amperage “A”. For this purpose, cement milling process in a local plant was modelled by using Artificial Neural Networks and Fuzzy Logic approaches. The data were collected from the local plant that uses fineness test as a process control parameter between the months of January and December 2004. Two combined modelling studies were performed using this data. First, the ANN on MatLAB^ was applied by using operational parameters such as Revolution “%”, Falofon “%” and Elevator Amperage “A”. The response surfaces of the ANN model were used to construct the Mamdani-type fuzzy rule set in the fuzzy model on MatLAB. Finally, the view of rule set and start-up, which were used to predict 32-μm fineness of cement, were obtained. In order to monitor 32-m fineness, % wt, of cement, the local plant applies basic Individual Control Chart. However, it has been observed that the chart does not correspond small shifts. If the high production rate (180 t/h) and effect of fineness on the quality of cement mortar are considered, these shifts lead serious problems with the cement stocked in the silos with capacity of 10.000 t. Hence, in the second part of our study, I-MR (Individual Moving Range) control chart, CUSUM (Cumulative Sum), EWMA (Exponentially Weighted Moving Average) and MA (Moving Average) control chart were applied in order to detect small shifts in cement fineness, which is one of quality parameters of the milling process. The performances of these control charts were compared. In chapter 2, cement-manufacturing process is described, briefly. Cement manufacturing process is composed of four main steps: quarrying and raw materials preparation, clinker burning, grinding of cement clinker, and finally, packing and dispatch of cement.
In chapter 3, the types of portland cement (EN and ASTM) are to be mentioned. In addition to this, chemical composition of portland cement is defined. Finally, some information about physical properties of portland cement such as fineness and compressive strength is given. In chapter 4, in order to get clear visual, some brief information about Artificial Intelligence Systems is to be given. Network Architectures and Learning Processes are discussed in Artificial Neural Networks part. In Fuzzy Logic part, fundamentals of Fuzzy Sets and Fuzzy Logic Approach are to be discussed. In chapter 5, cement-milling process and parameters affecting on fineness are explained. In chapter 6, construction of ANN models that were created in the thesis is explained. In chapter 7, the results of the model created in this study are discussed. In chapter 8, statistical monitoring of quality parameter of 32-μm fineness of portland cement is explained.
in the atmosphere in the form of gaseous compounds such as carbon dioxide and nitrogen oxides, the location of a cement unit near the deposits is seen as a vital aspect in cement manufacturing process. Figure B1 represents a typical dry process of cement production flow chart. Major unit operations involved in cement manufacturing process include:
Major quantity of limestone is obtained from the captive limestone mines of the plant. However, depending upon the proportions of different cement clinker phase forming components, additive materials including high grade / low grade limestone can be purchased from outside parties in required quantities in order to obtain the desired quality of cement grade raw meal. Big boulders, which are produced during drilling and blasting methods of limestone mining, are crushed in suitable type of crushers. The crushing is carried out either in single or double stages by using Primary crusher and Secondary crusher, or in a single stage crushing machine depending upon the size of the boulder produced from mining. This also depends on the type of grinding mills used for grinding raw materials for preparation of finally pulverized raw meal. A jaw hammer crusher is used in Çimenta Cement Company for size reduction of limestone boulders to a suitable feed size. Such crusher was installed at the plant site. Limestone produced in the mine is transported to crusher site with the help of dumpers. Crushed limestone is then transported to plant stockpile with the help of Belt conveyor. Crushed limestone is then transported to stacker reclaimer site with the help of belt conveyor / rope ways installed at different sites of the plant. Finally, crushed limestone is pre-blended with the help of stacker and reclaimer systems. Crushed limestone traveling on the belt conveyors is stacked in layers with the help of stacker machine. Stacked materials is then cut in slices with the help of a reclaiming machine
which mixes layers of stacked limestone to reduce the variation in quality of limestone relative to large variations seen in the limestone ore. The pre-blended limestone from stack pile is then transported to raw mill hoppers. More than one hoppers are used for proportioning of raw mix incase the limestone is obtained from several sources or additive materials required to be mixed with captive mines of limestone. Presently, raw mill hoppers are provided with continuous weighing machines known as weigh feeders in order to produce a suitable raw meal proportioned appropriately for production of desired good quality of cement clinker. Vertical Roller Mill and Tube Mill Grinding machines are used for production of pulverized raw meal at the company.
Portland cement clinker is produced from a mixture of raw materials containing calcium, silicon, aluminum, and iron as the main elements. The mixture is heated in kilns that are long rotating steel cylinders on an incline. The kilns may be up to 6 meters in diameter and 180 meters in length. Mixture of raw materials enters at the high end of the cylinder and slowly moves along the length of the kilns due to the constant rotation and inclination. At the low end of the kilns, fuel is injected and burned, thus providing the heat necessary to make the materials react. It can take up to 2 hours for the mixture to pass through the kiln, depending upon the length of the cylinder. When mixed in correct proportions, new minerals with hydraulic properties – the so-called clinker phases – are formed upon heating up to the sintering (or clinkerization) temperature as high as 1450° C. The main mineral components in clinker are silicates, aluminates and ferrites of the element calcium. The main clinker phases are listed in Table 2..
As the mixture moves down the cylinder, it progresses through four stages of transformation. Initially, any free water in the powder is lost by evaporation. Next, decomposition occurs from the loss of bound water and carbon dioxide. This is called calcination. The third stage is called clinkerisation. During this stage, the calcium silicates are formed. The final stage is the cooling stage. The marble-sized pieces produced by the kiln are referred to as clinker. Clinker is actually a mixture of four compounds as illustrated in Table 2.2. The clinker is cooled with the help of grill cooler in order to get it to stable phases.
In order to achieve the objectives of energy conservation, the clinker produced in rotary kiln cooled in cooler is usually stored for few days before it is ground in cement grinding mills along with appropriate quantity of gypsum and other additive materials for production of finely pulverized cement with desired fineness. Fineness and particle size distributions of the finished product have a strong influence on the cement quality. Ball / Tube mills (in open circuit or closed circuit mode) are generally used for clinker grinding in cement plant worldwide. Blended cements (or “composite” cements) contain other constituents in addition such as granulated blast-furnace slag, natural or industrial puzzolan (for example, volcanic tuff or fly ash from thermal power plants), or inert fillers such as limestone. Mineral additions in blended cements may either be inter-ground with clinker or ground separately or mixed with Portland cement. The tube mill consists of a steel cylindrical shell with three compartments. The first compartment is used for drying of the raw material in order to increase the performance of the milling by removing water from the raw material. The following compartments include steel balls with different dimensions. In the second compartment, raw materials (clinker and additive materials) are pre-milled by the help of big steel balls having a radius of 60-90 mm. By using balls of smaller radius, size of pre-milled material is reduced down to maintain desired level of fineness of the finished product. A dynamic separator is used for differentiate the fine and thick particles coming from the
mill exit. The fine particles are sent to the silos as finish product (cement). The remaining part (thick particles) is recycled to the mill for re-milling. In Chapter 5, Process parameters and standards will be more elaborated.
The pulverized different types of cements are stored in different silos installed with different capacities. Depending upon the customer requirements, cement is loaded in bulk, or in 50 kg bags that are packed with the help of conventional rotary packaging or electronic packaging equipment, and finally loaded onto trucks that are dispatched to final destinations.