
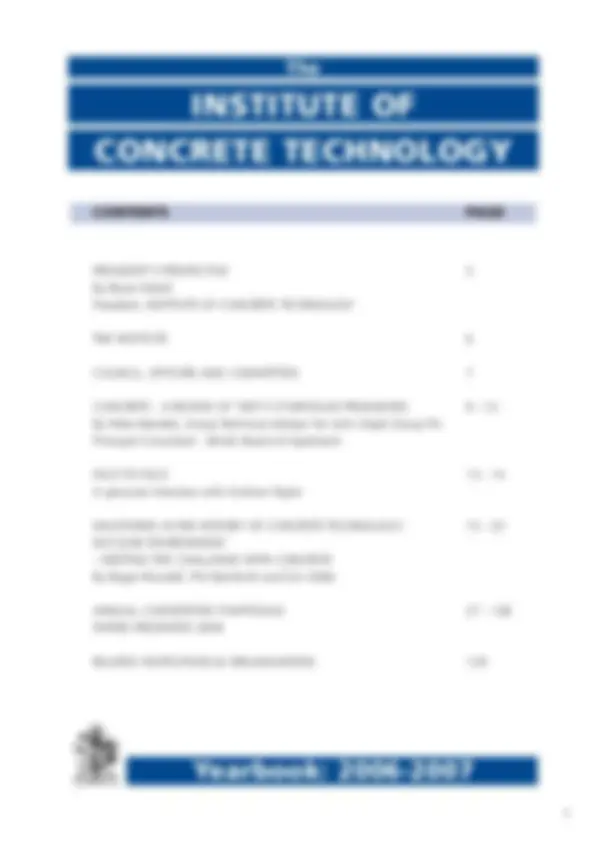
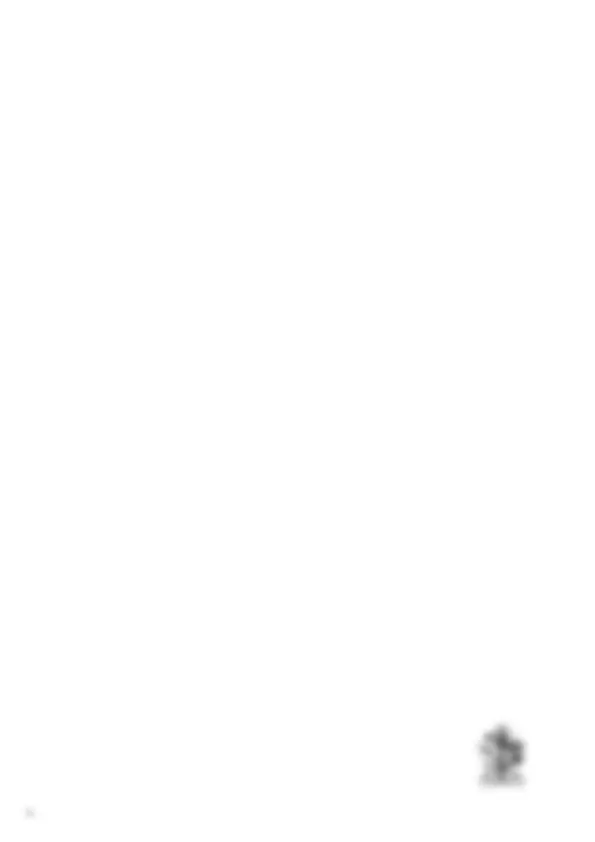
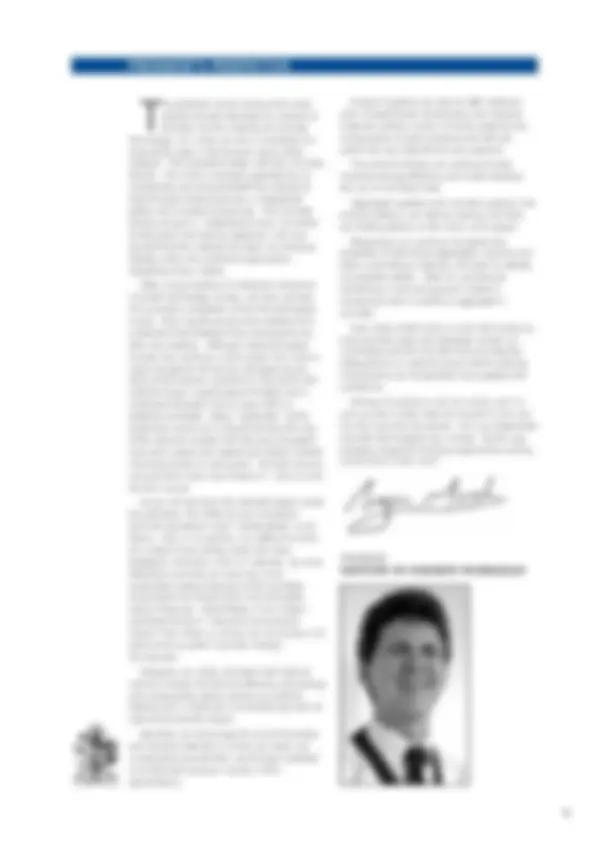
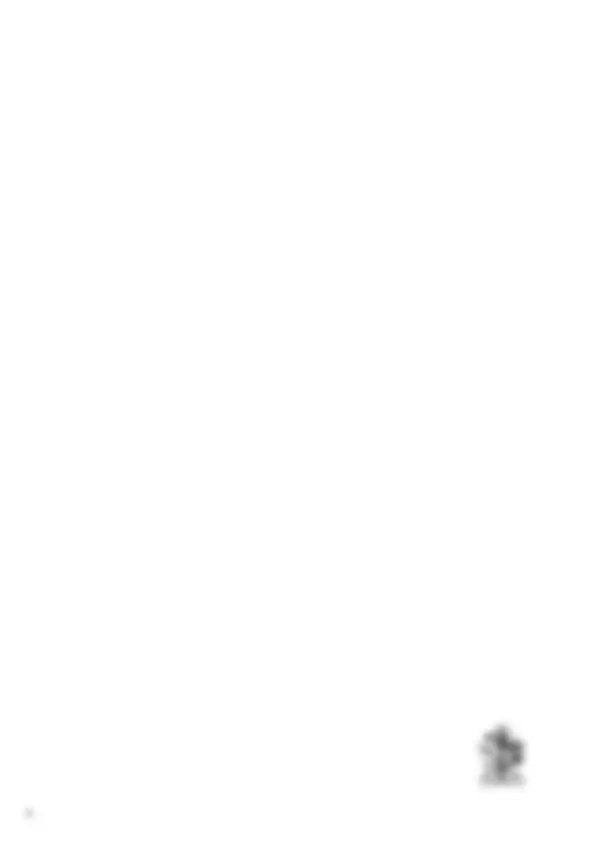
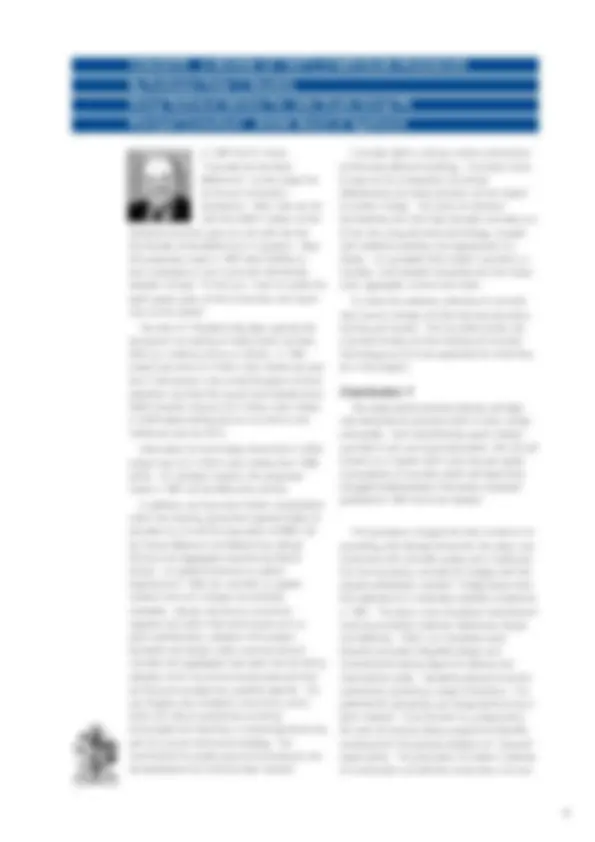
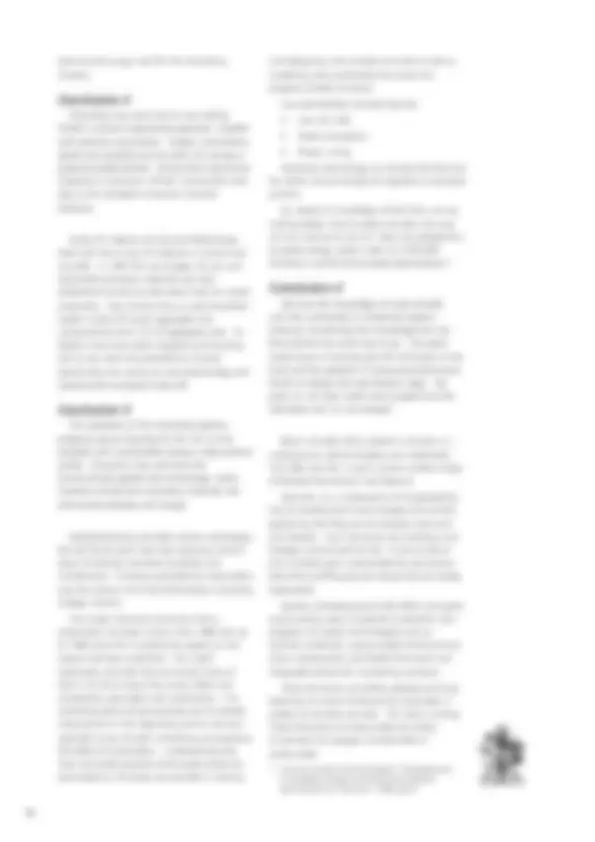
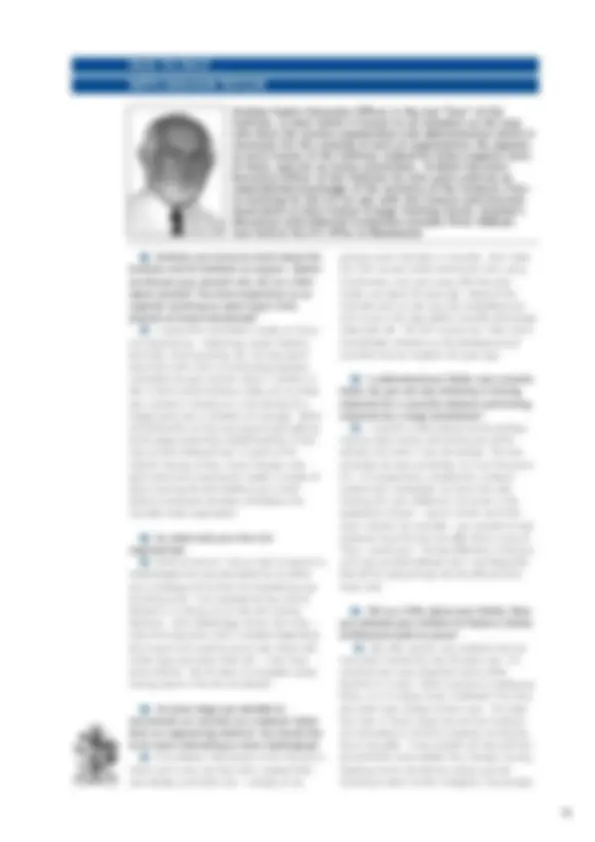
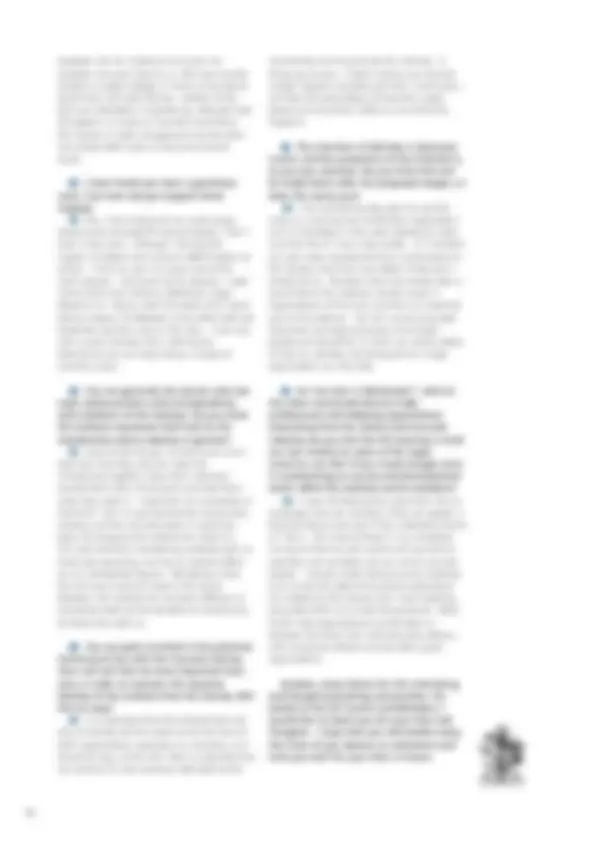
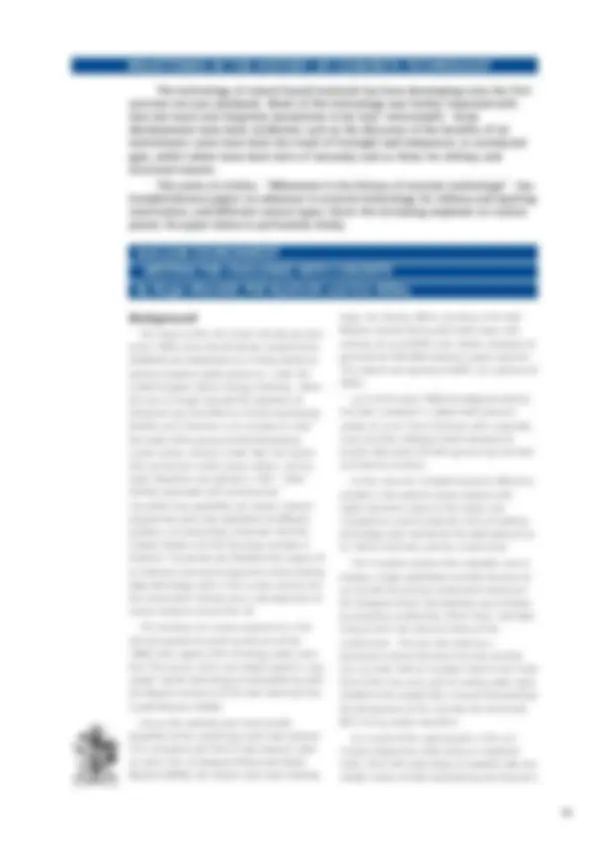
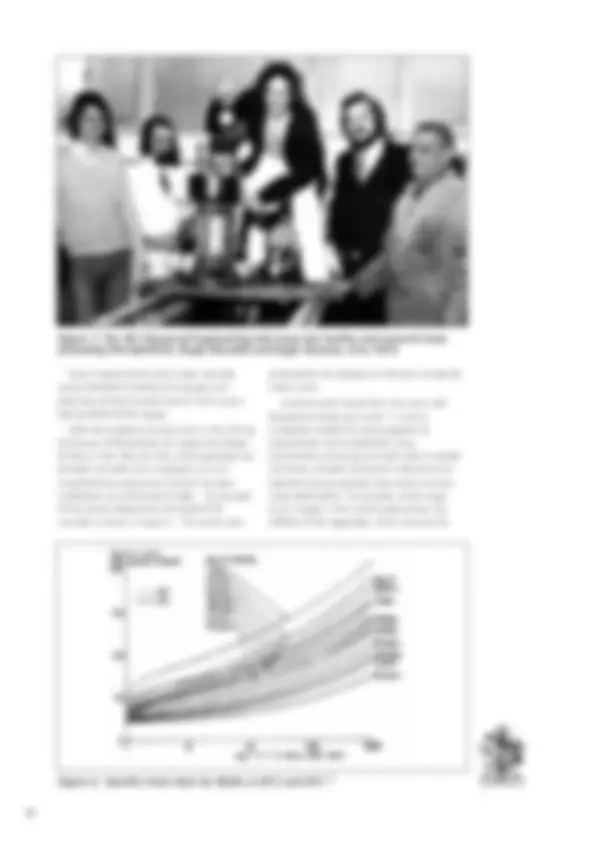
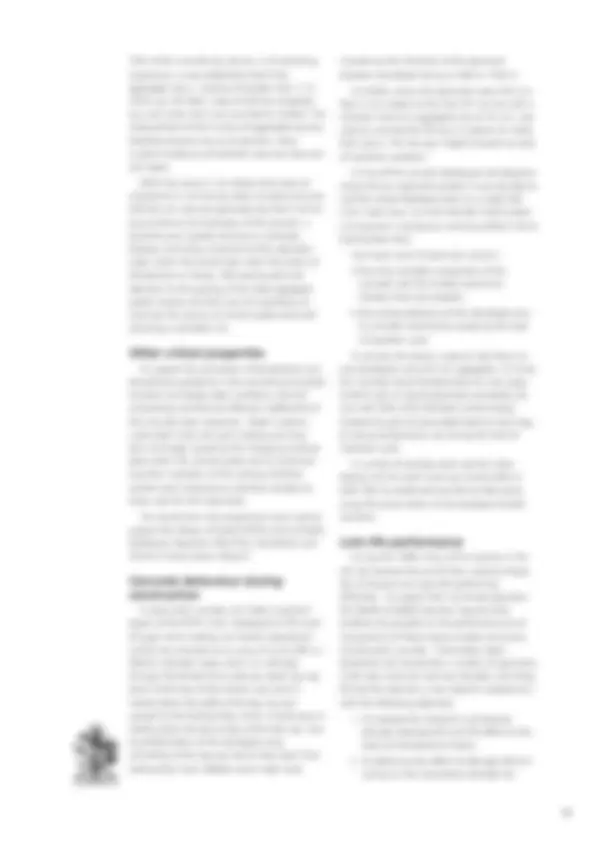
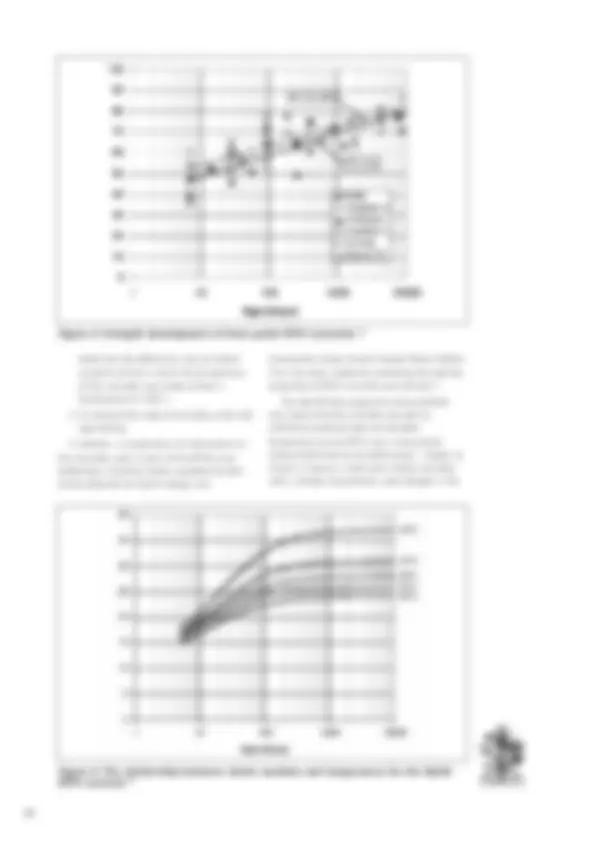
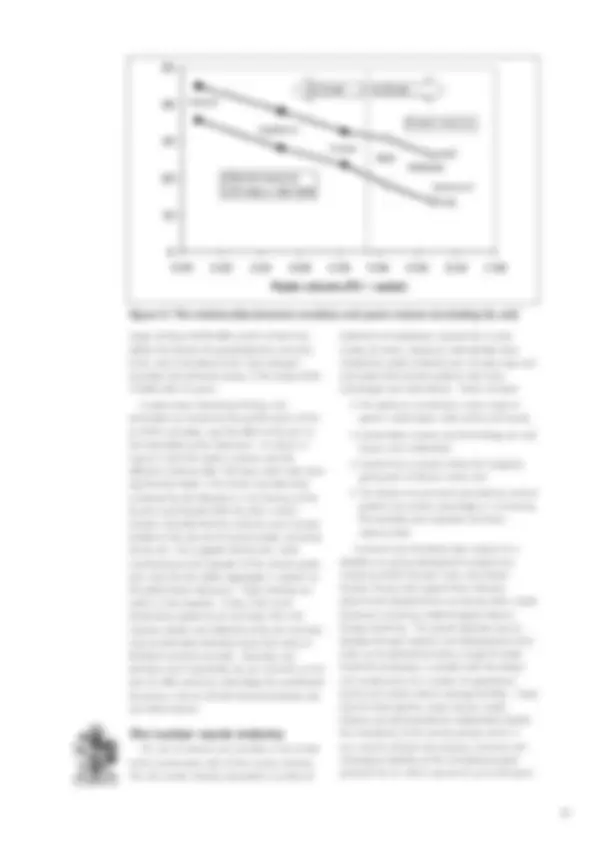
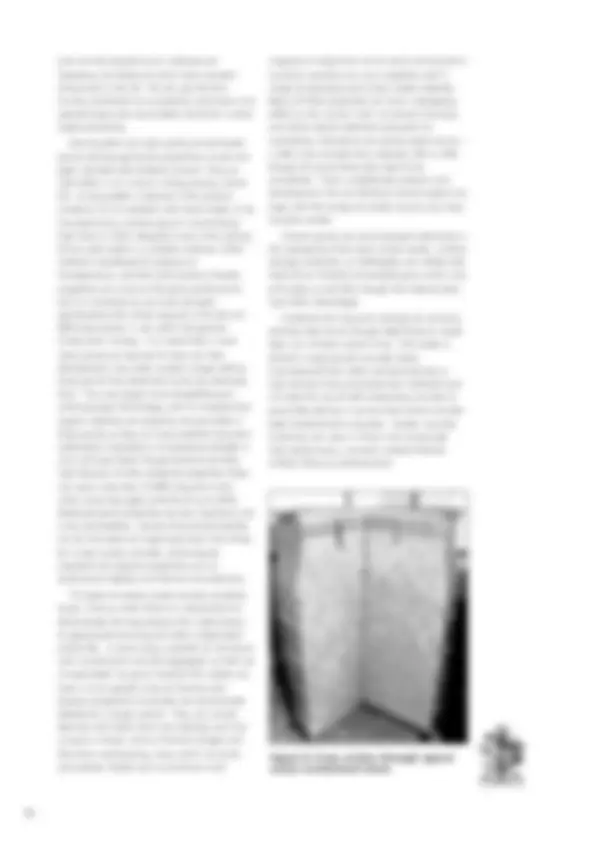
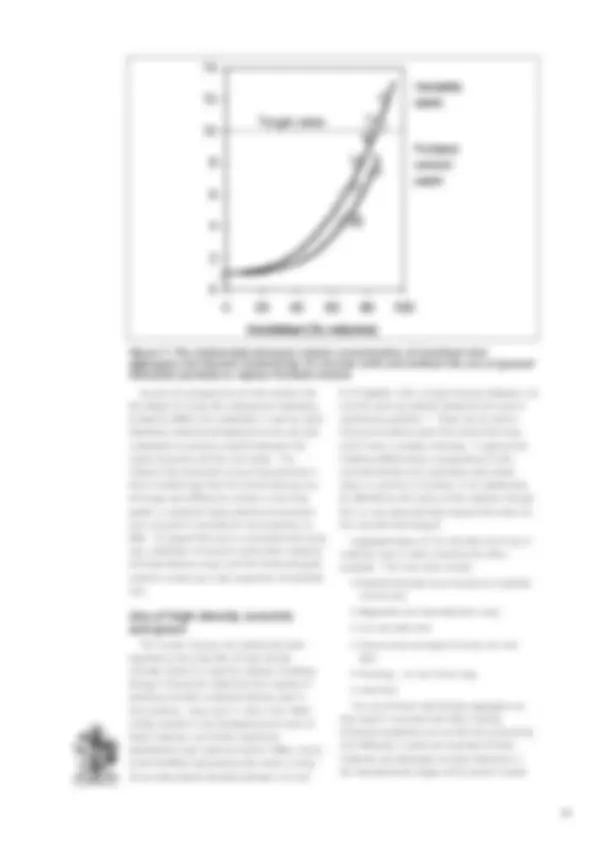
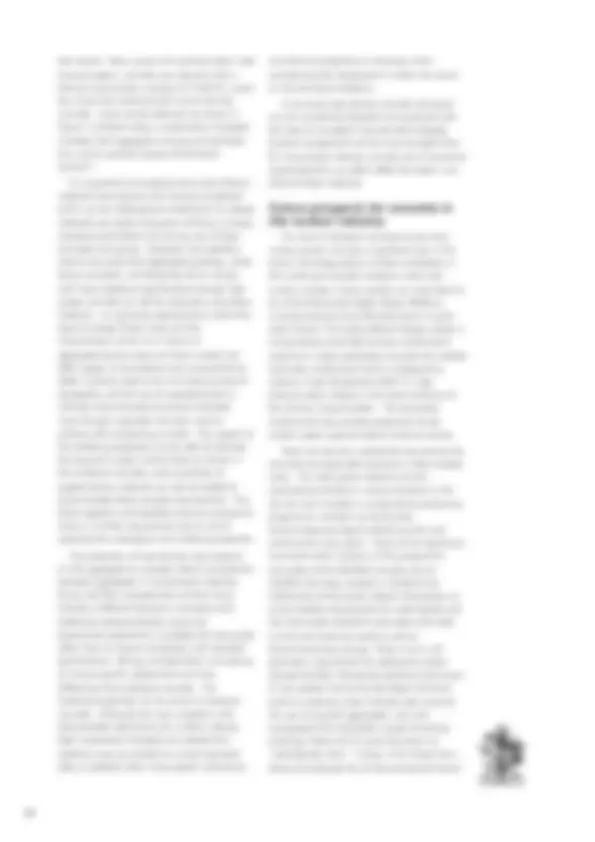
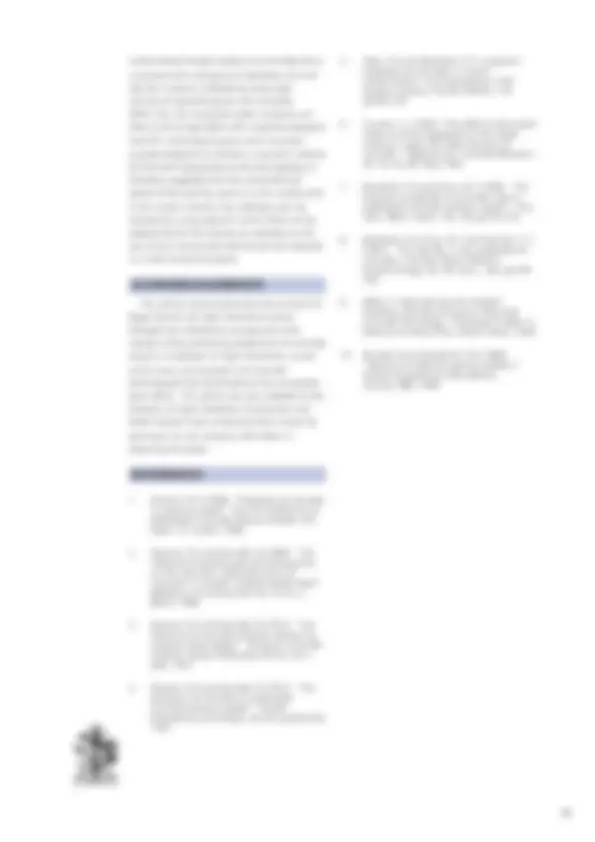
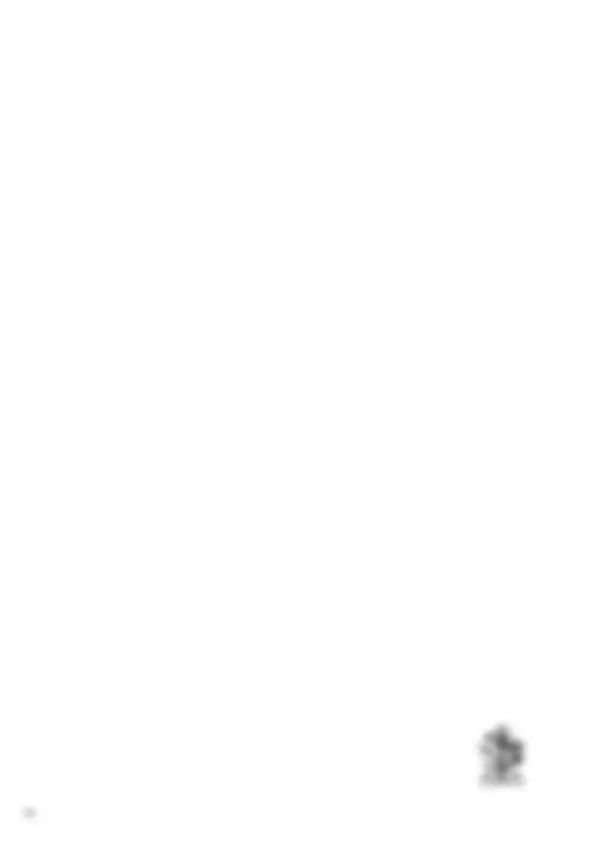
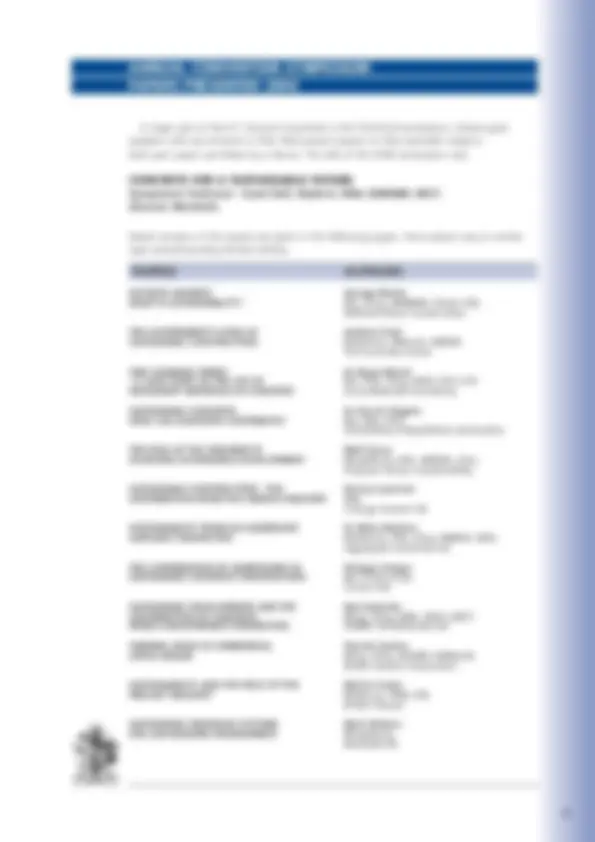
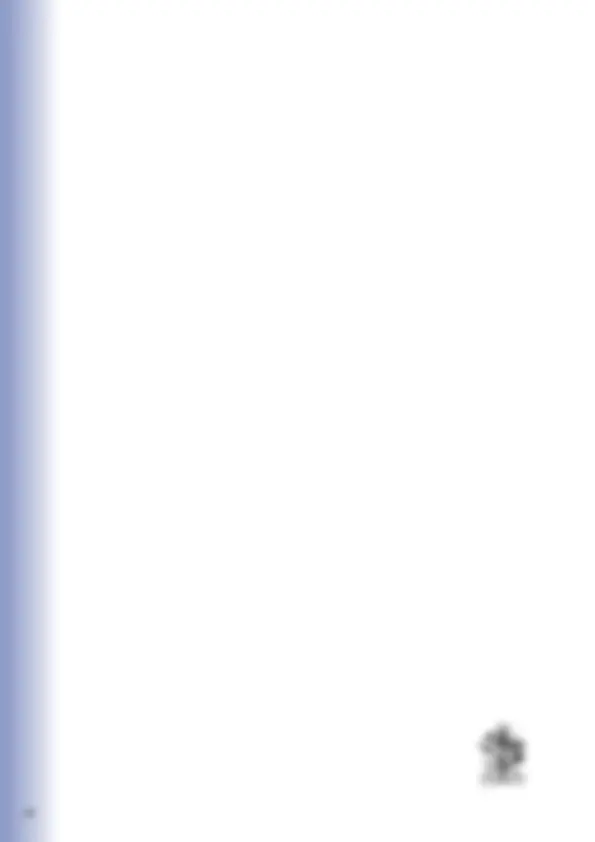
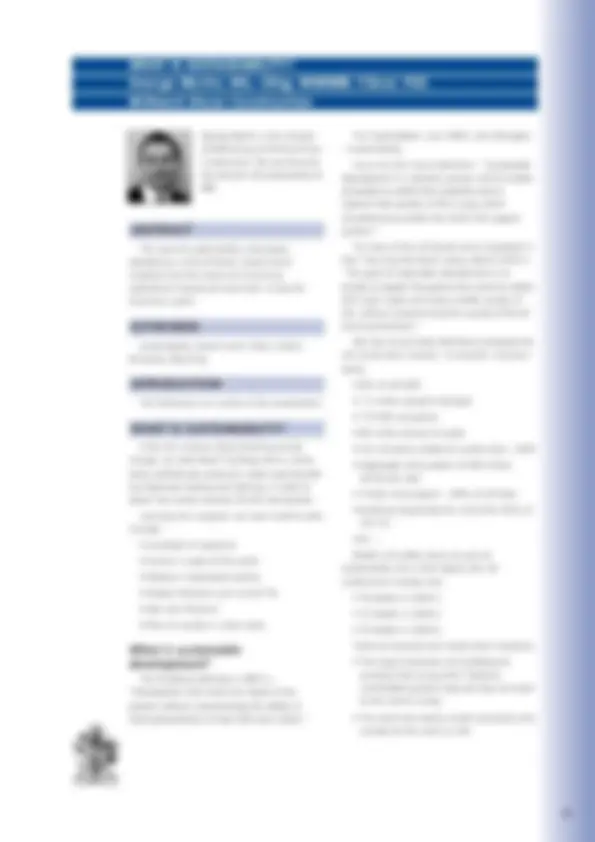
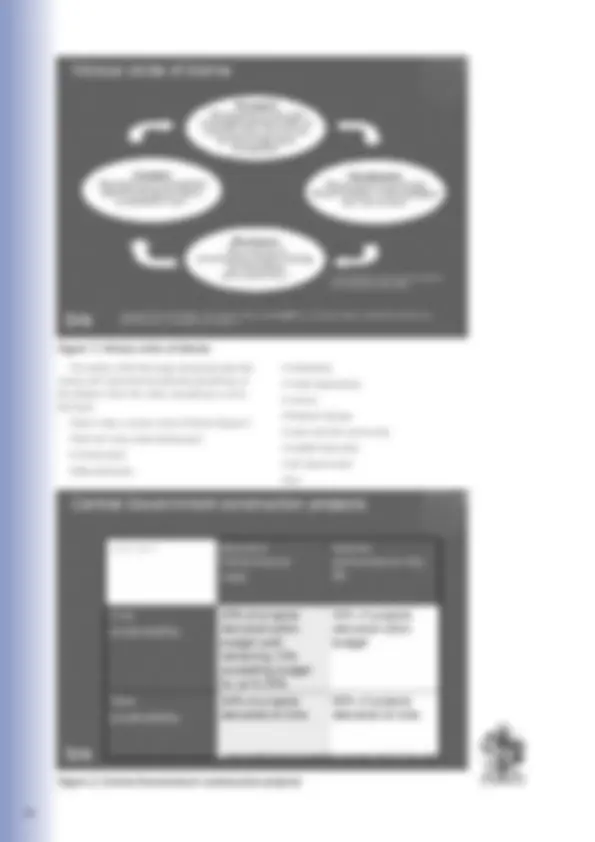
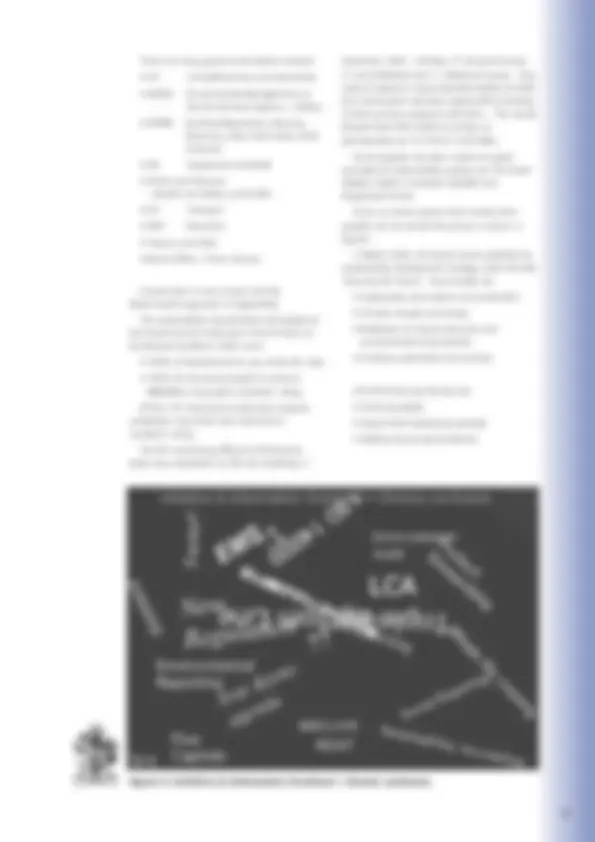
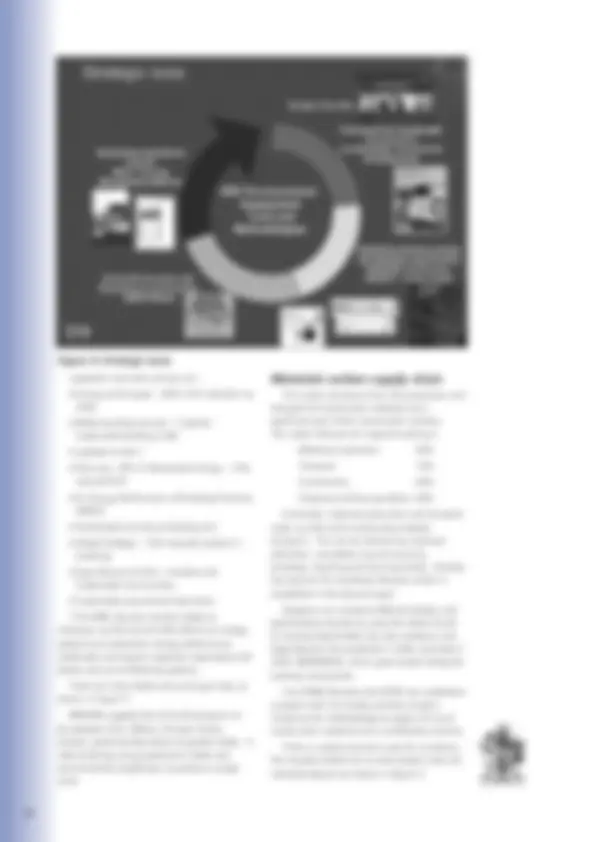
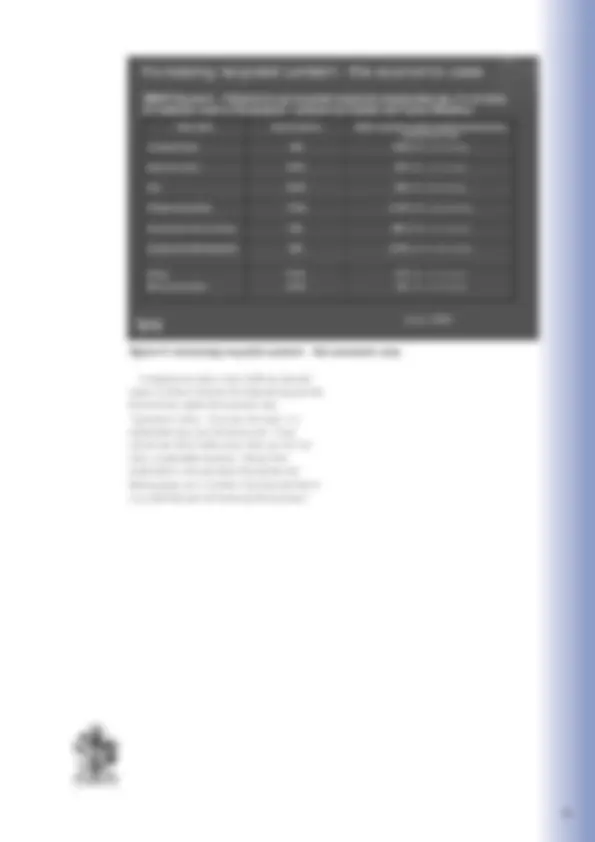
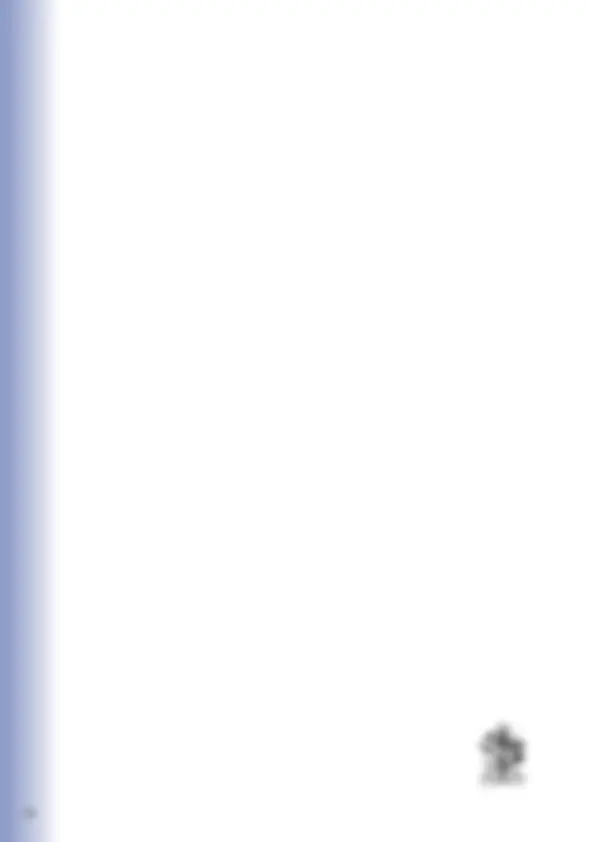
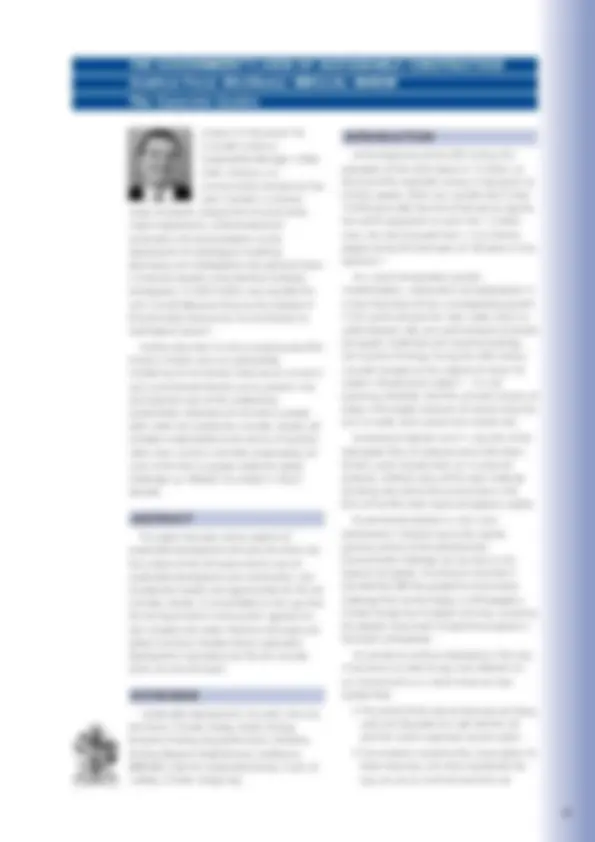
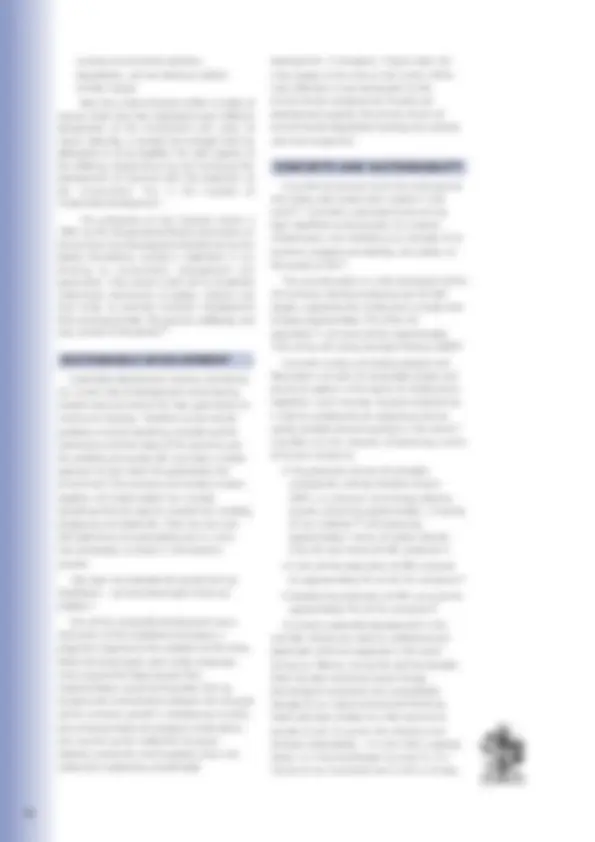
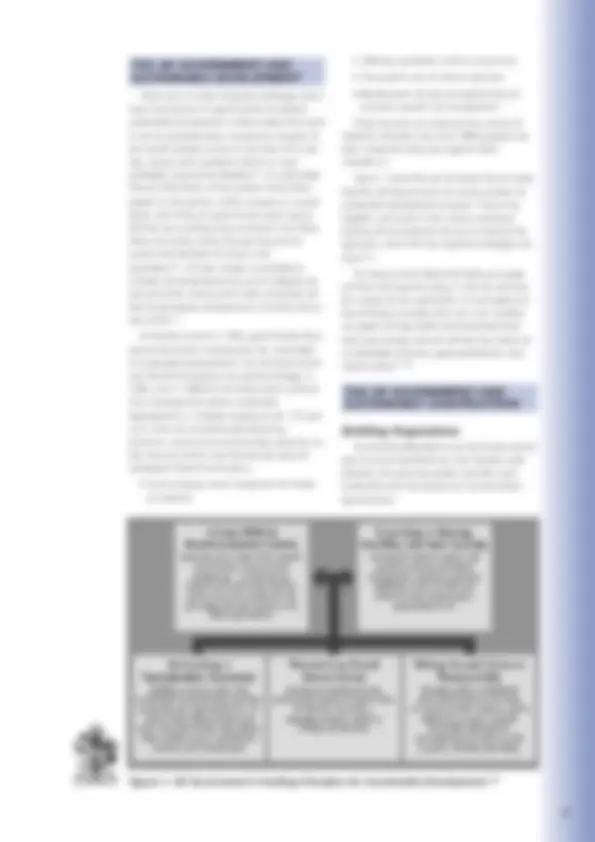
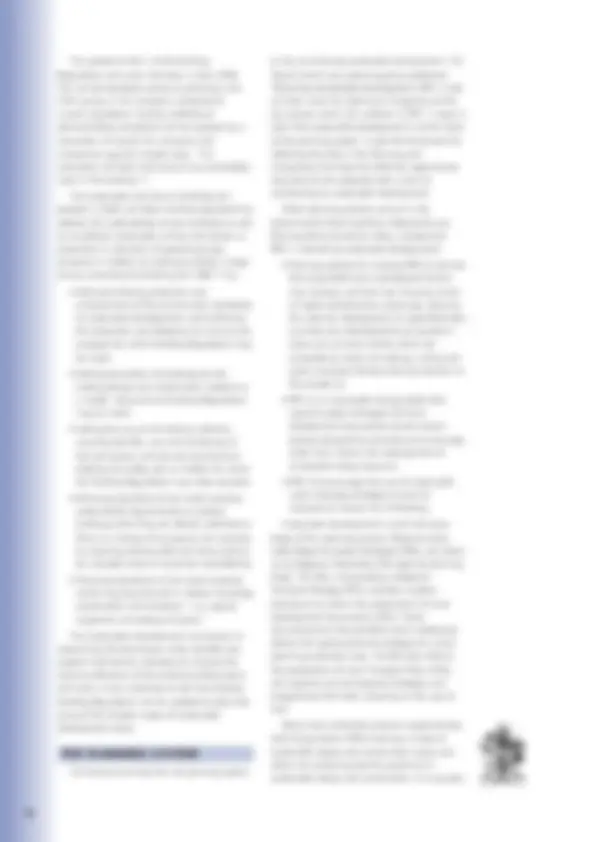
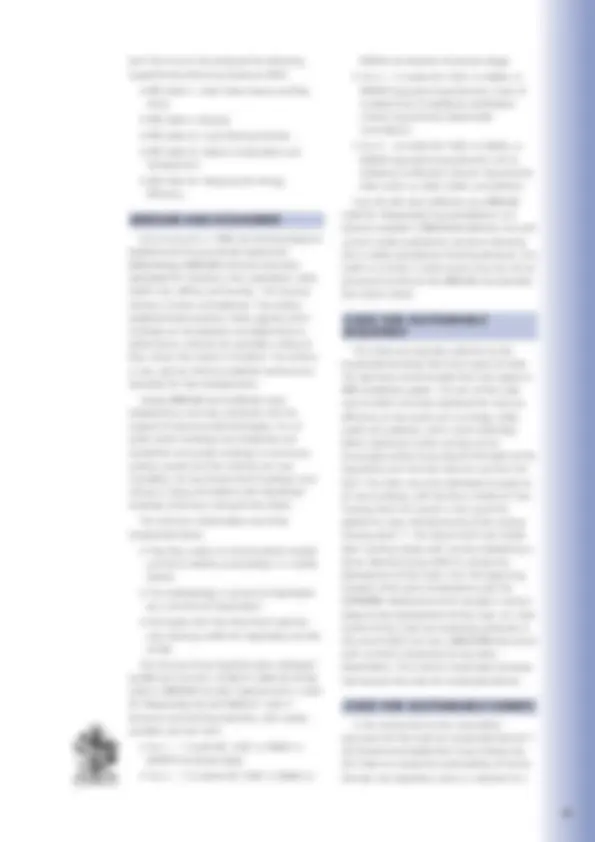
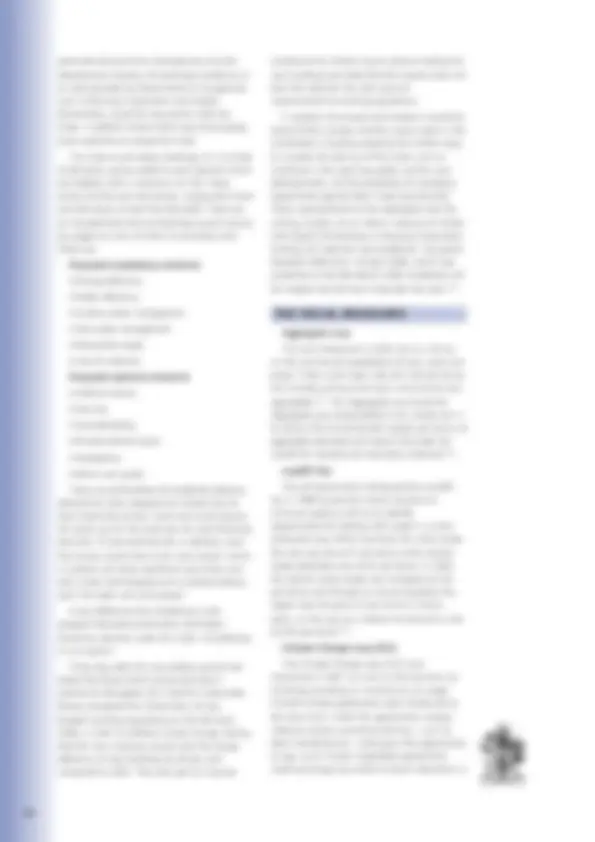
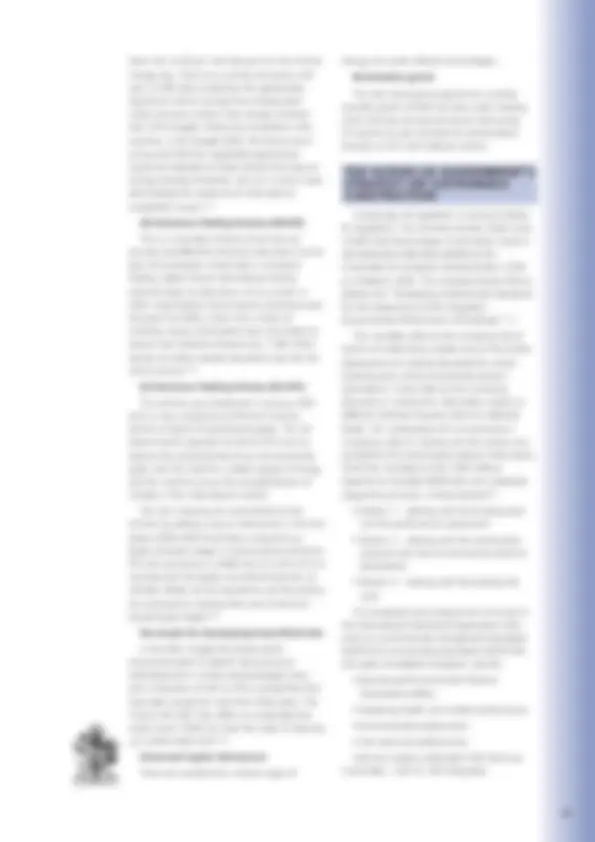
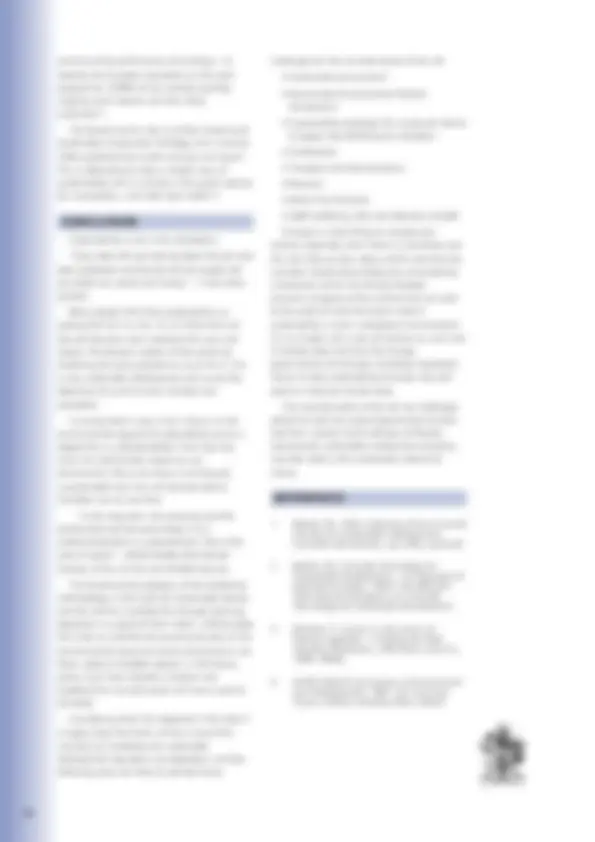
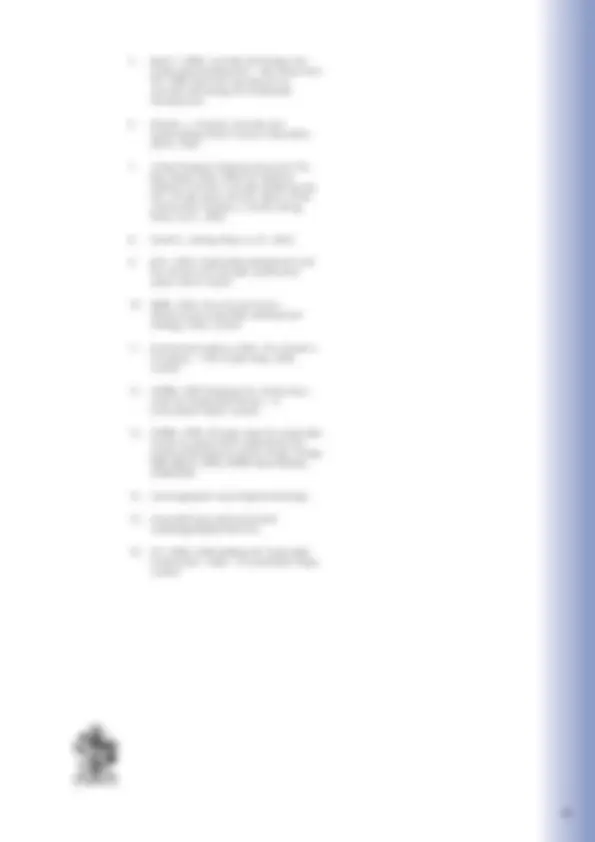
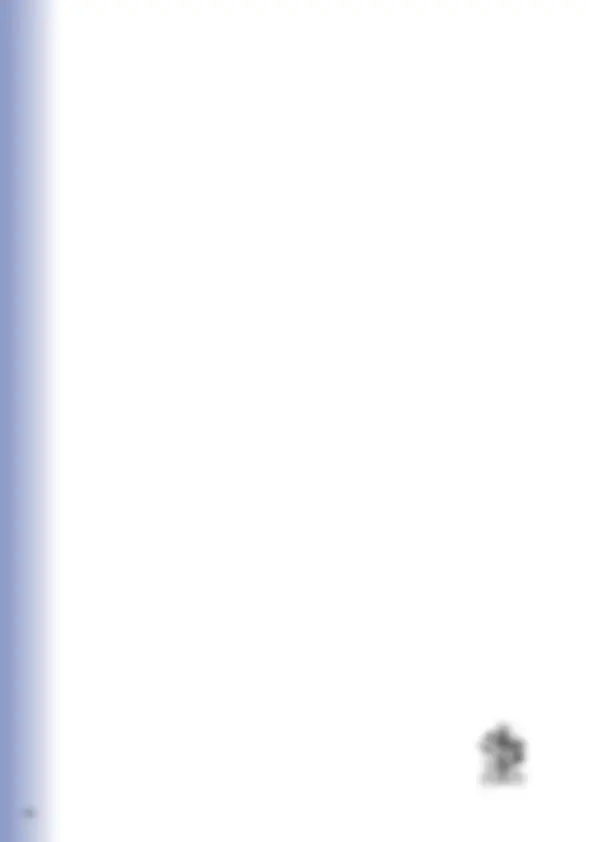
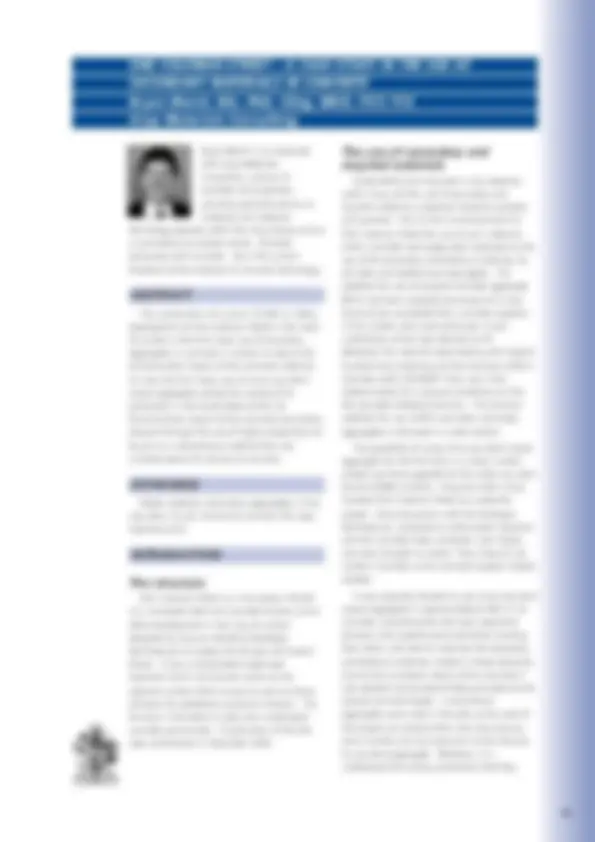
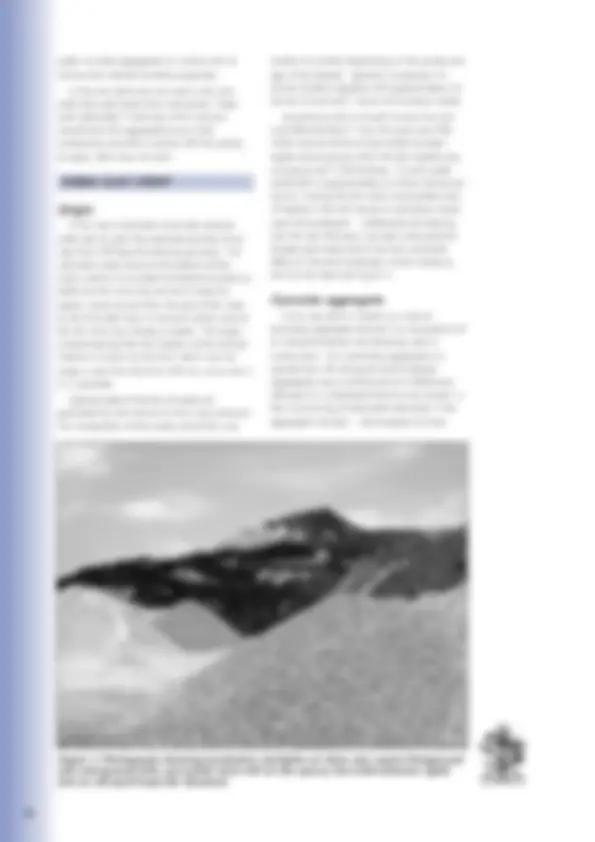
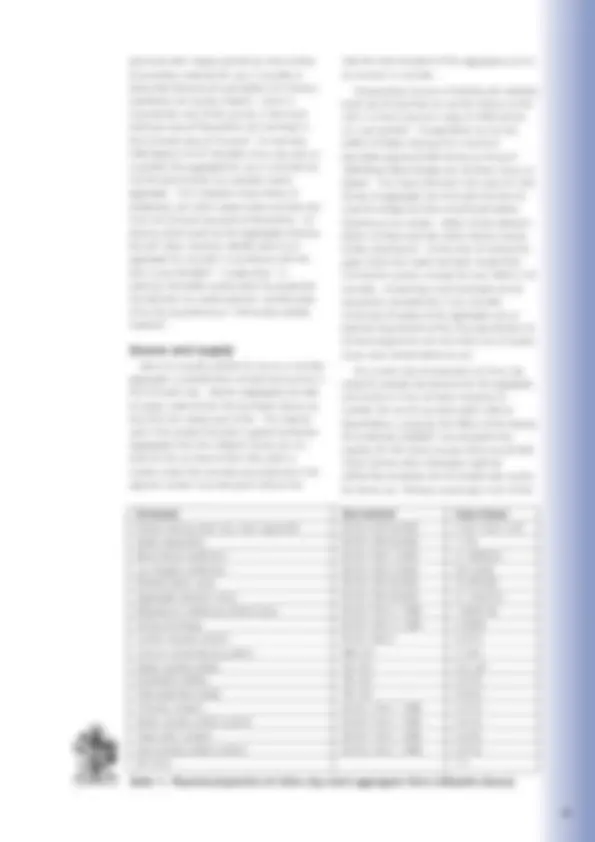
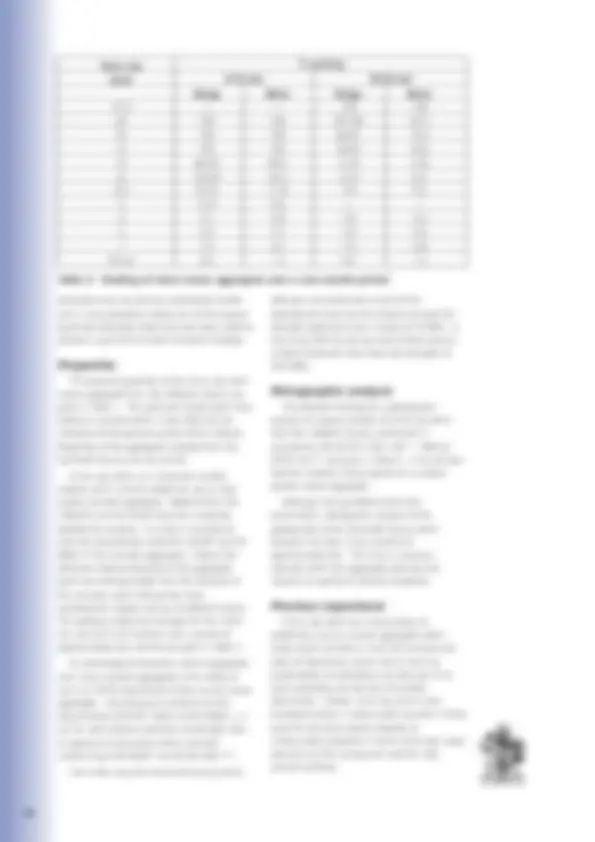
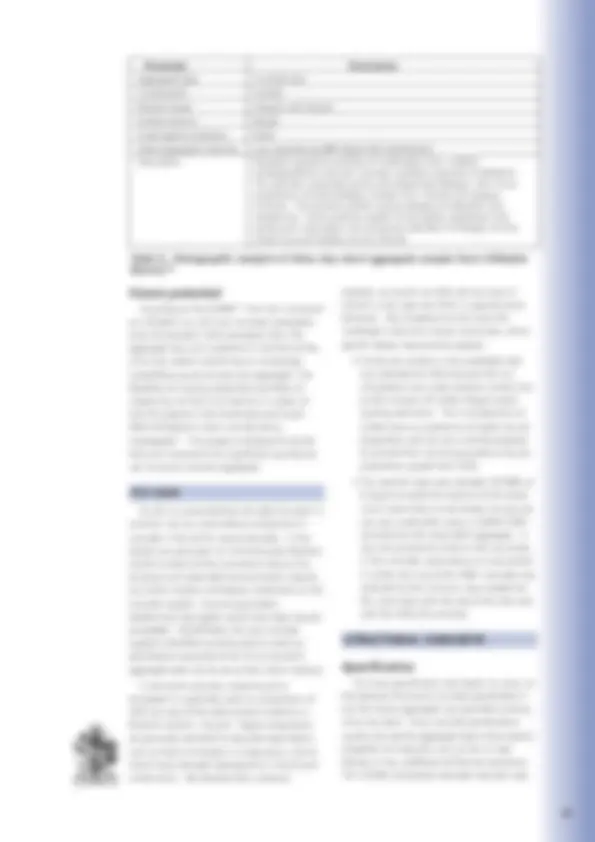
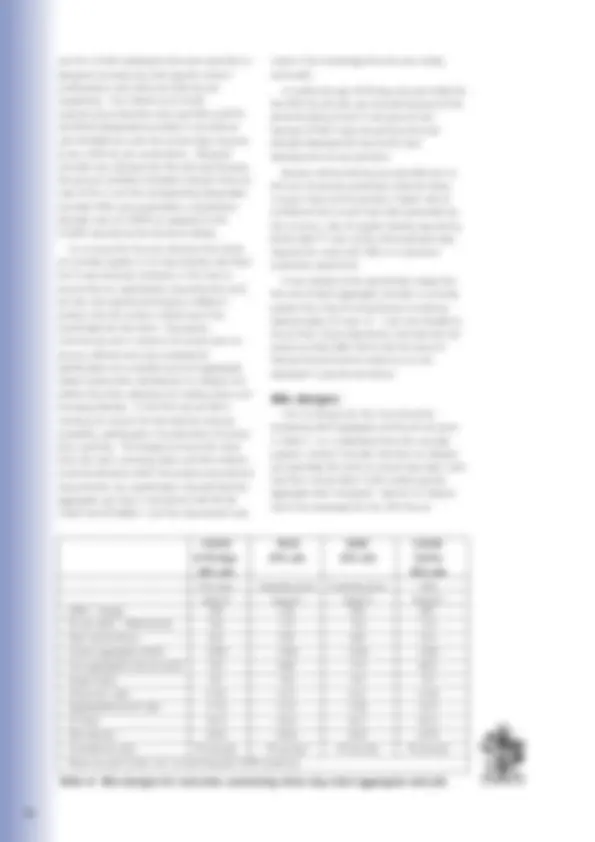
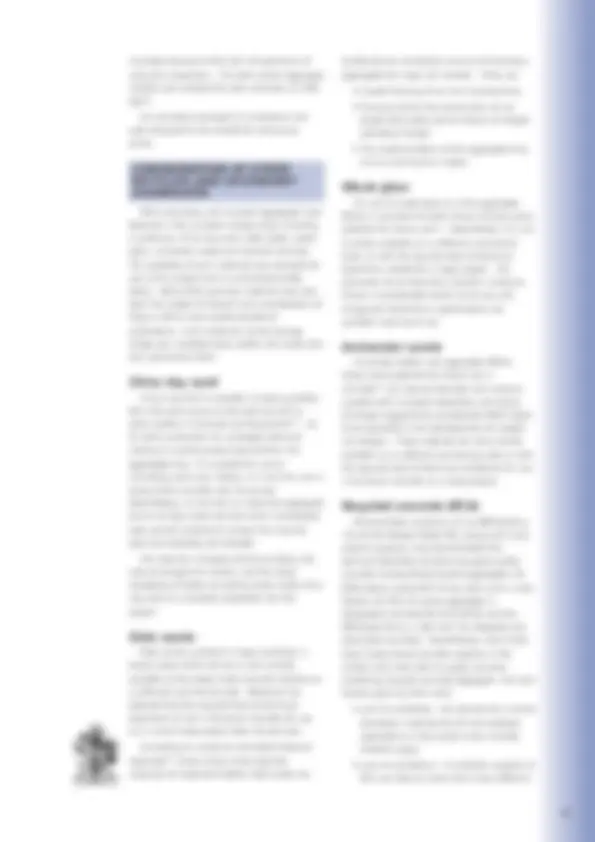
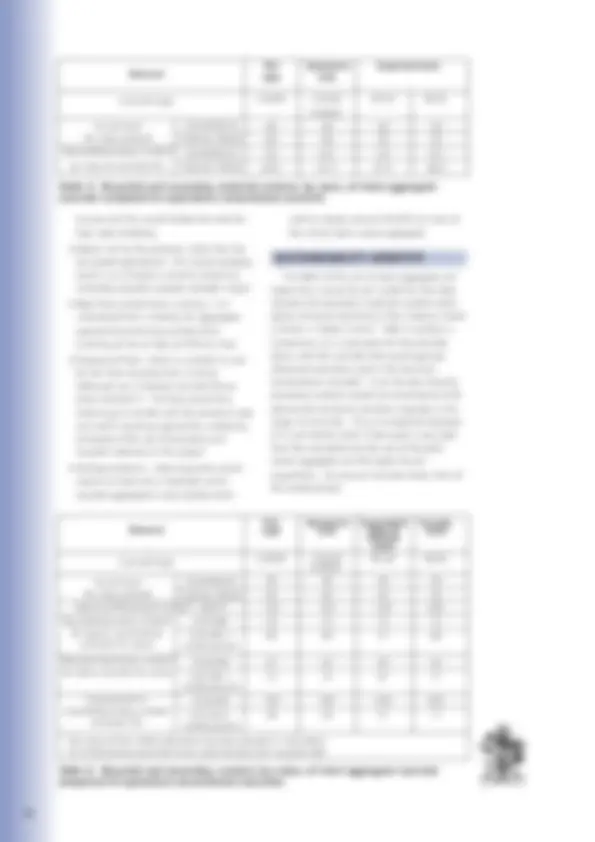
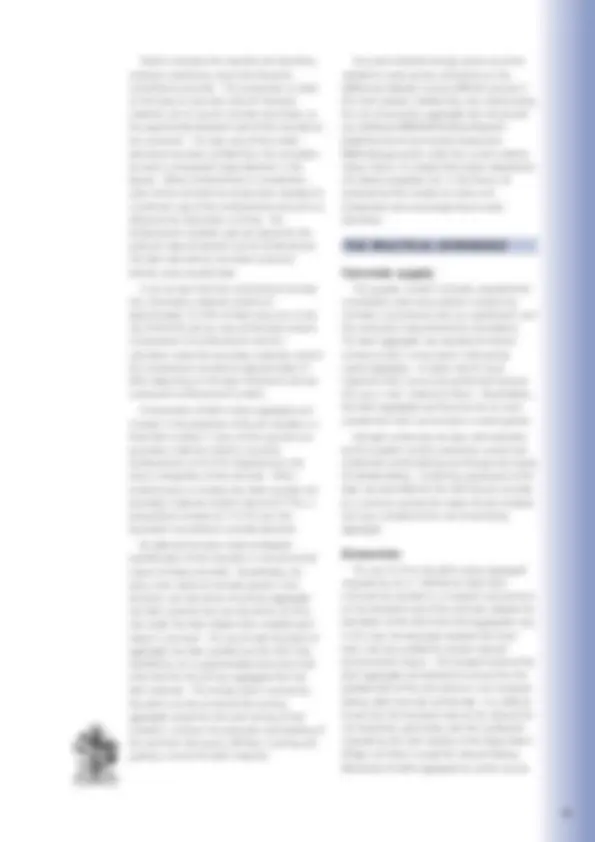
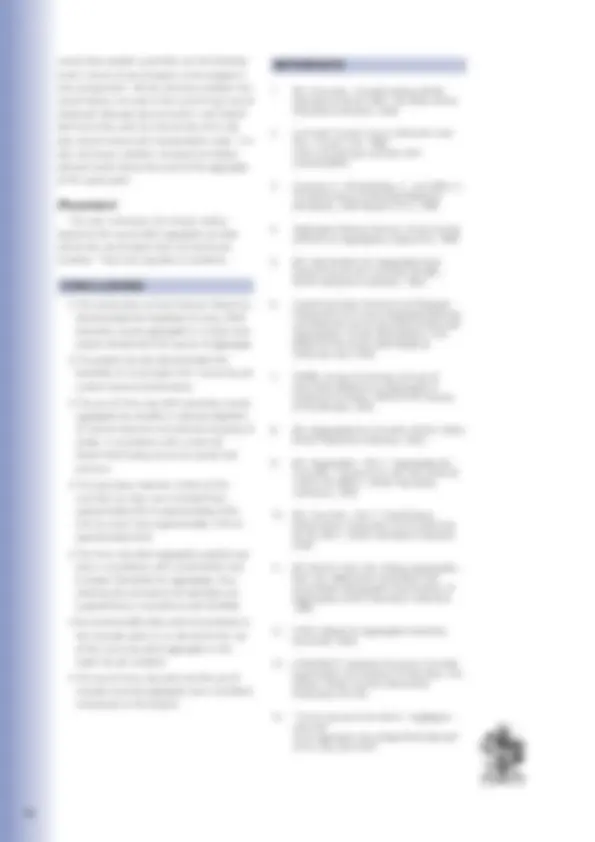
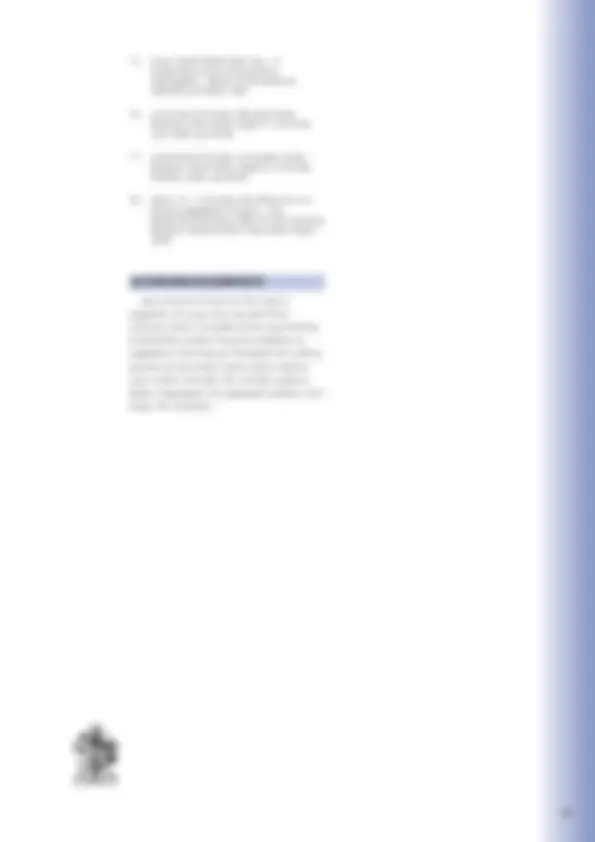
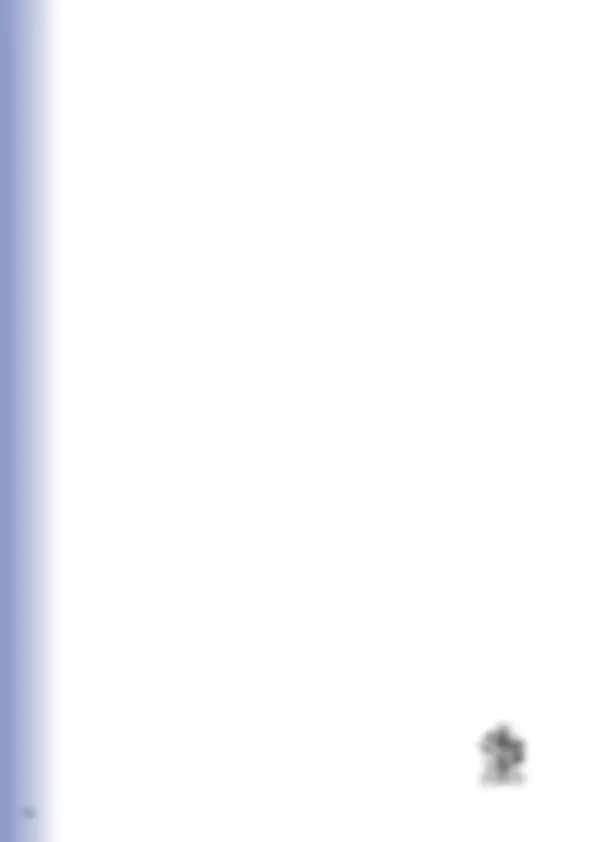
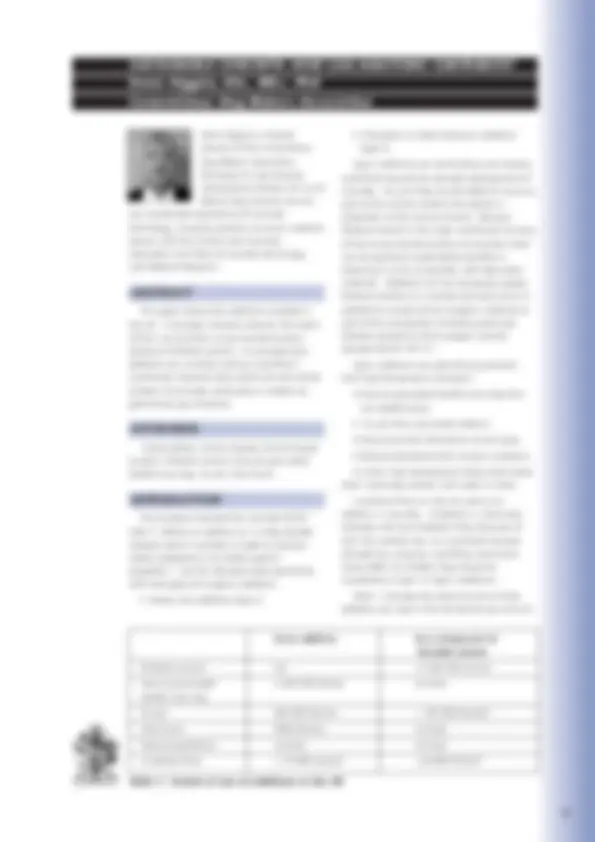
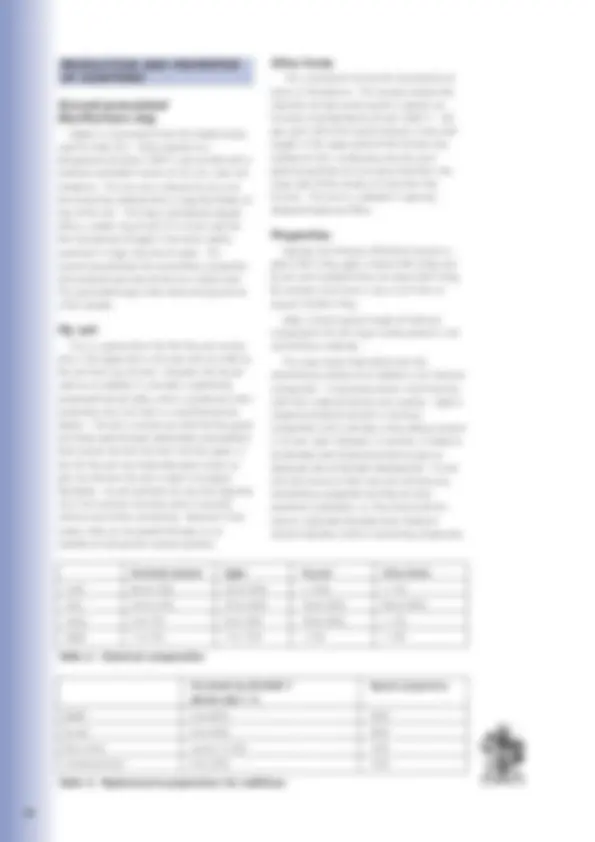
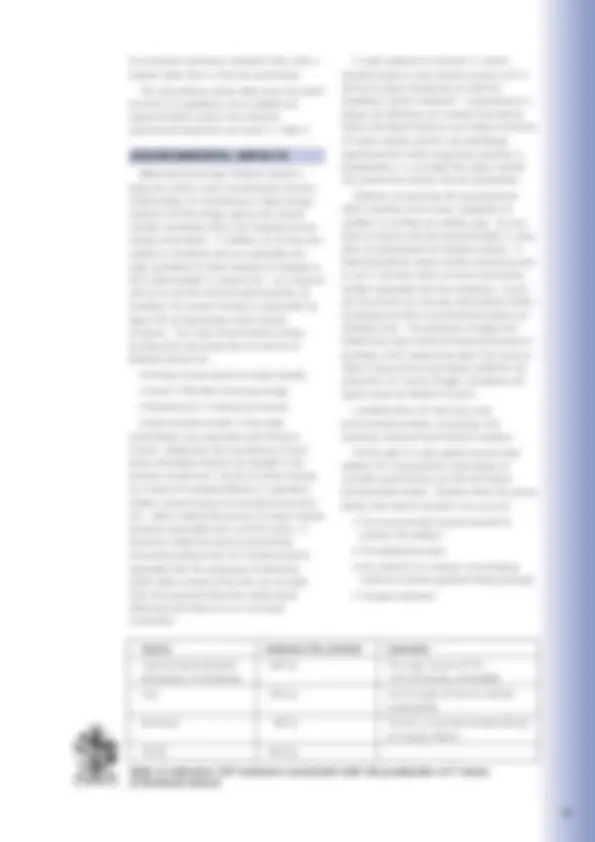
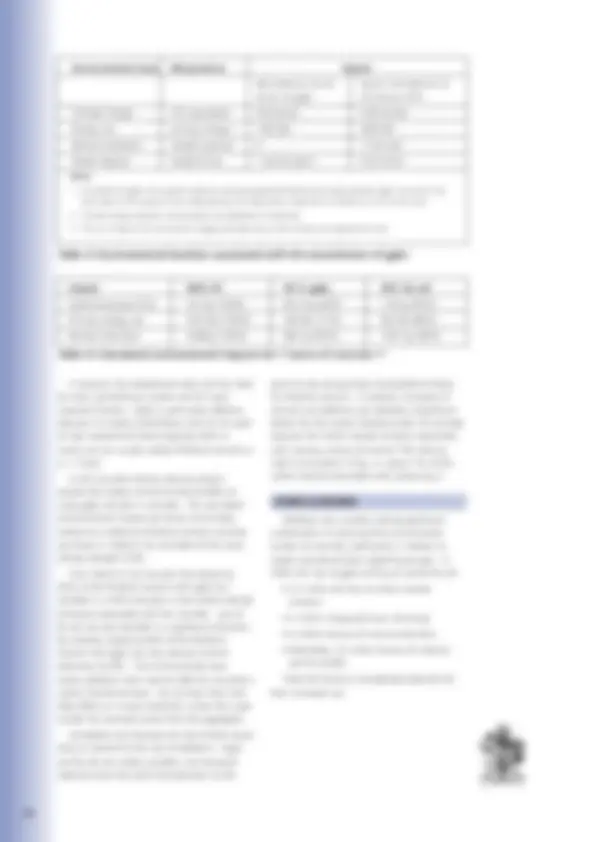
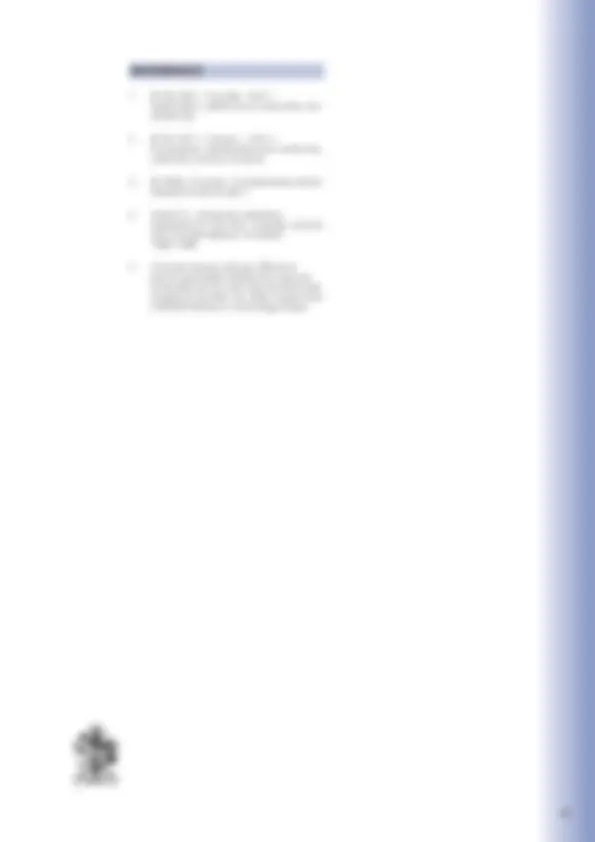
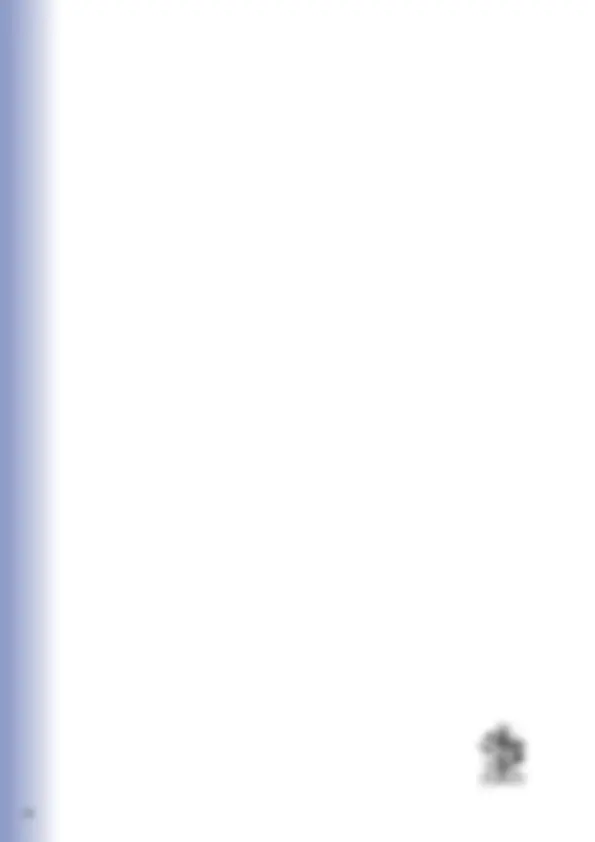
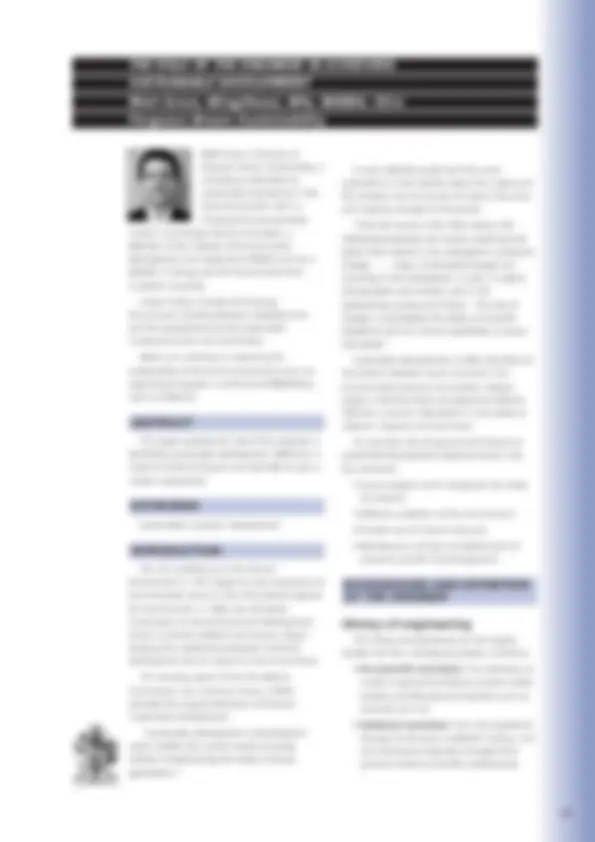
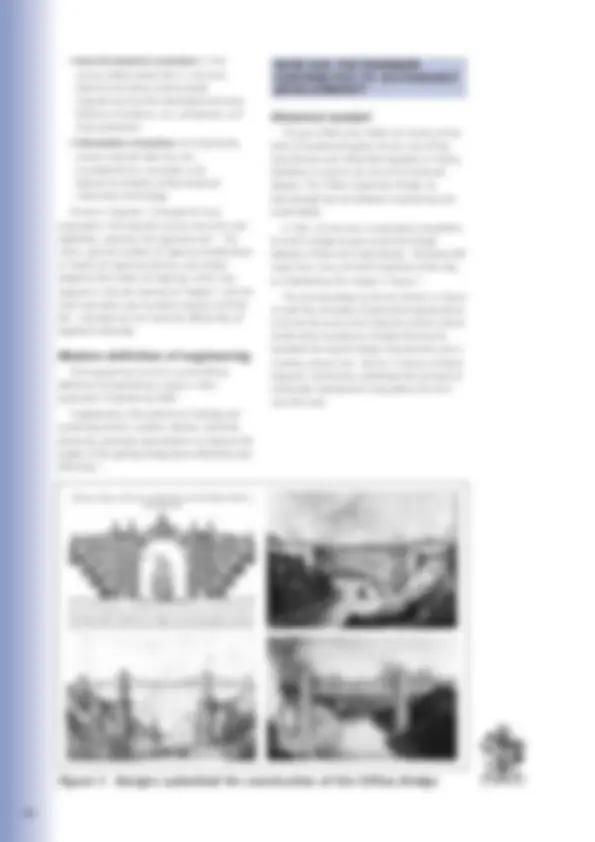

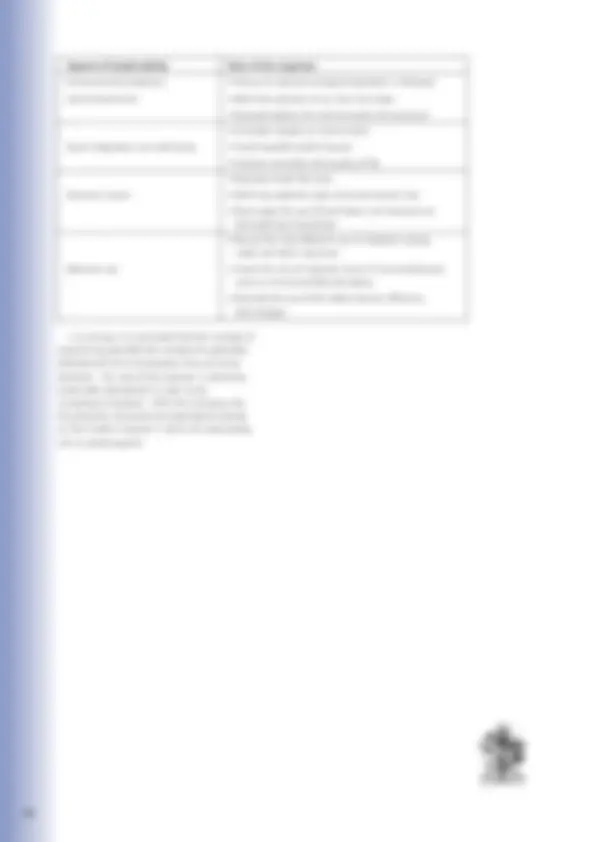
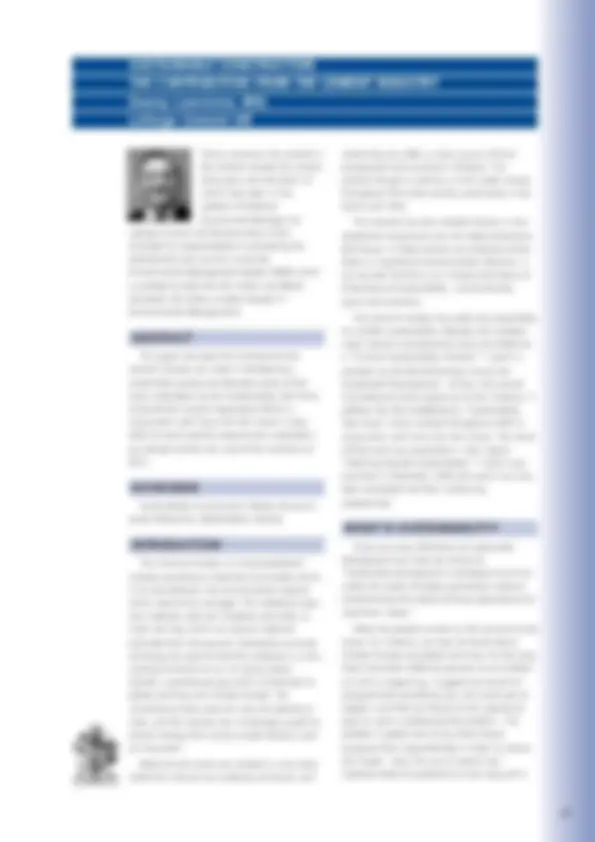
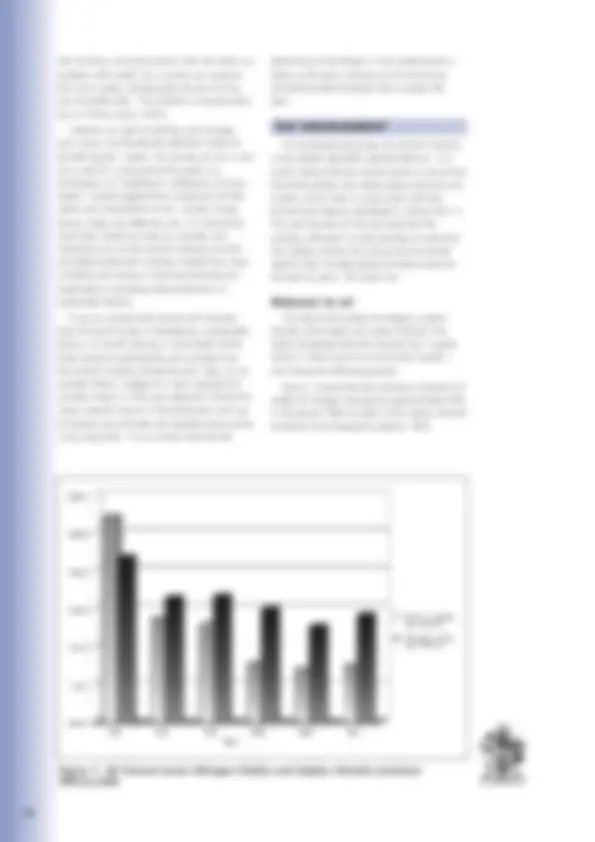
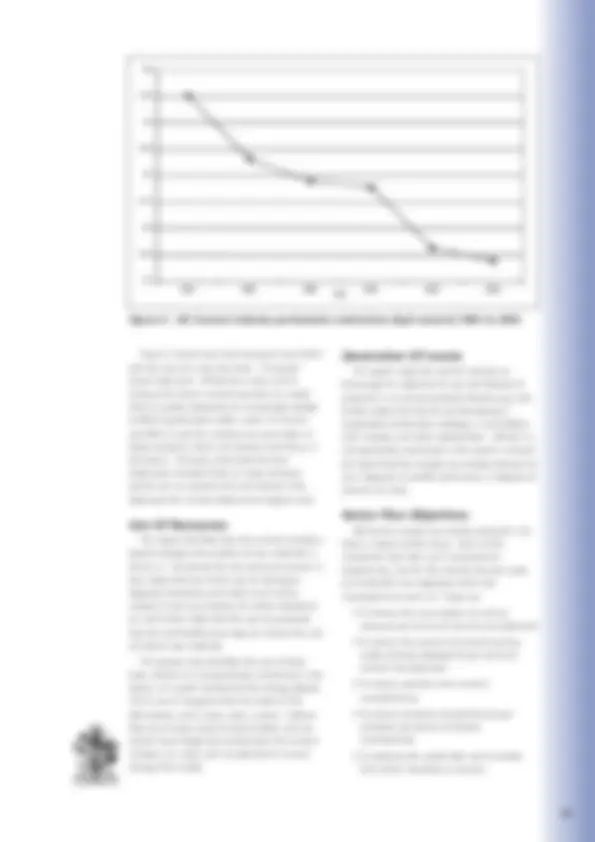
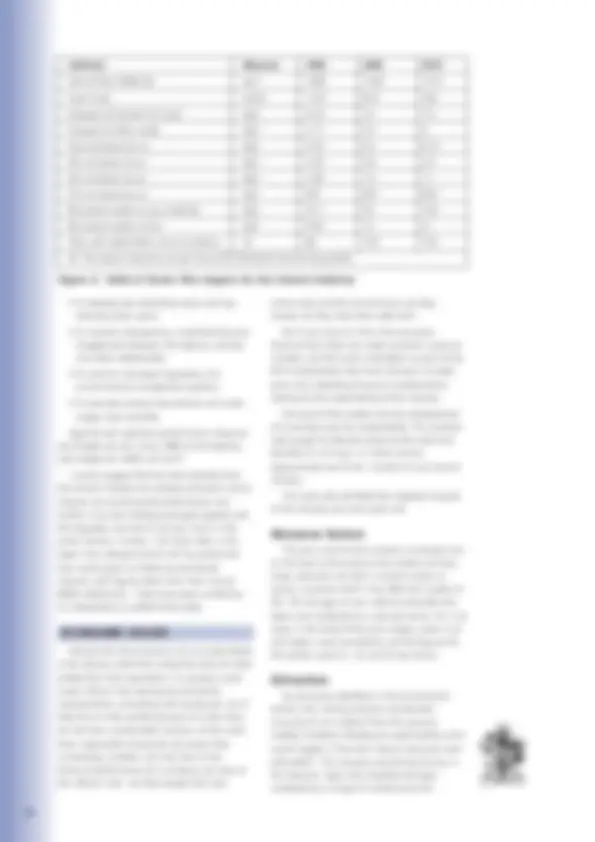
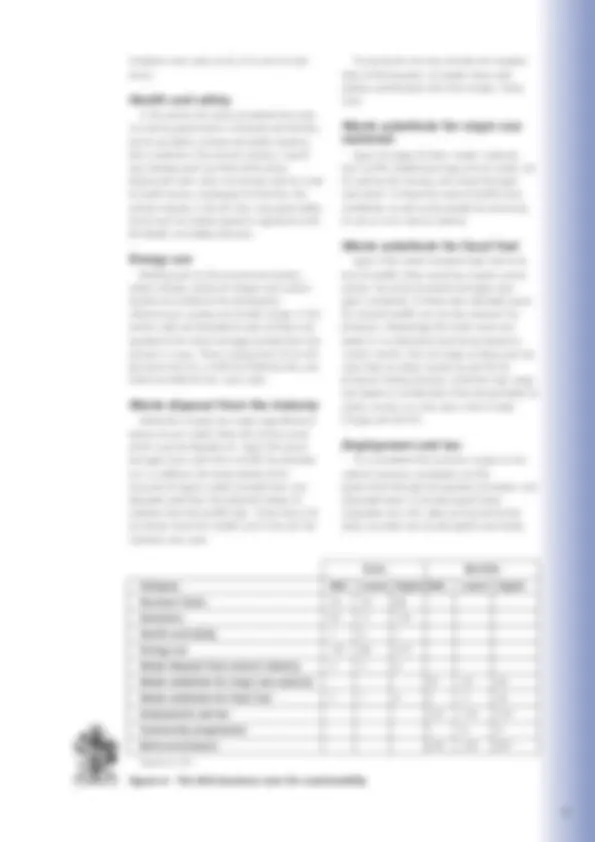
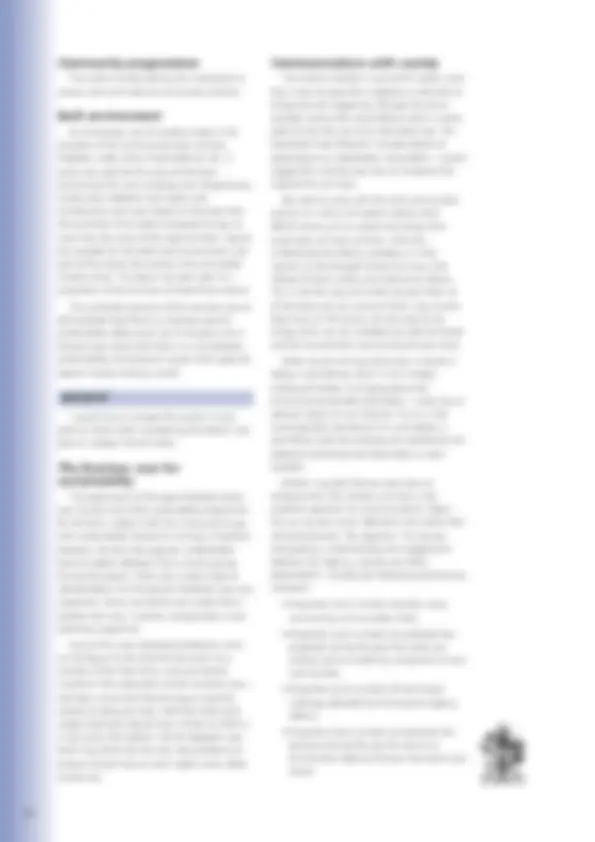
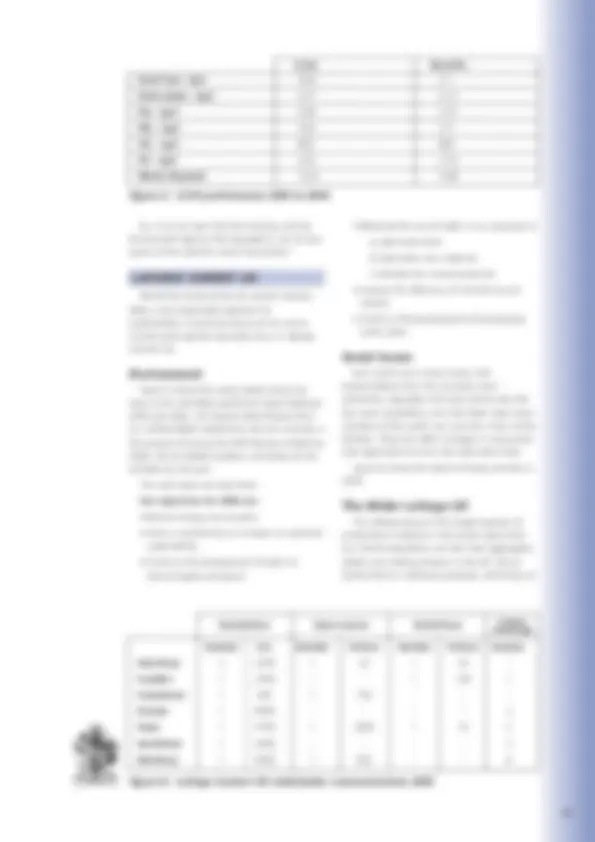
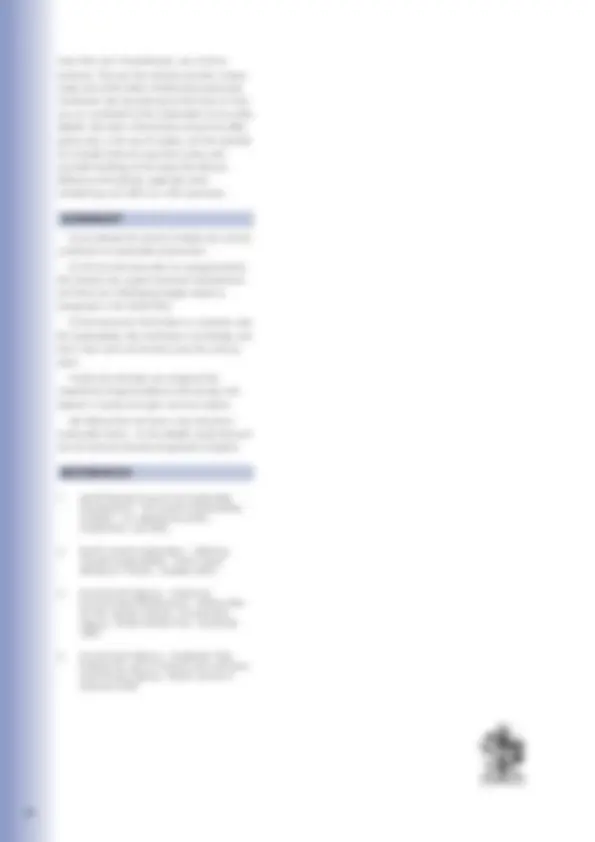
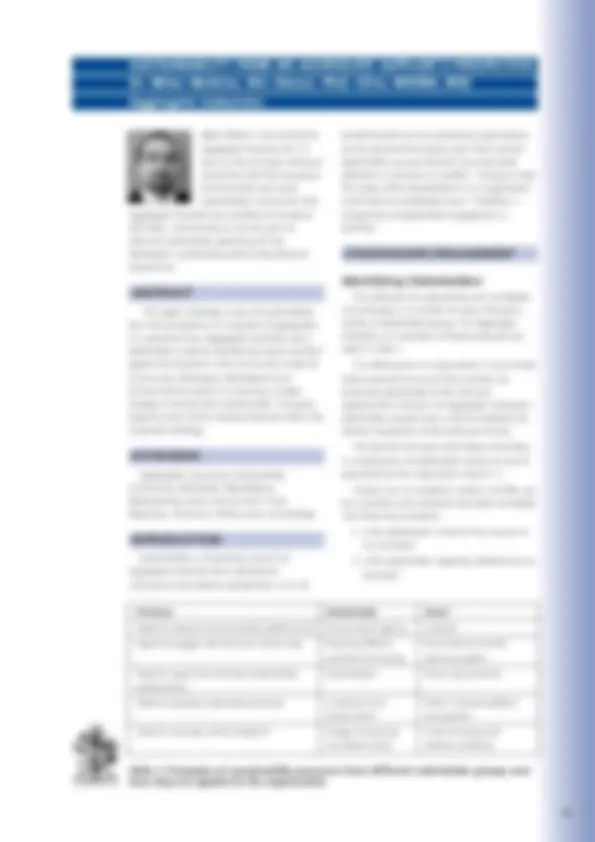
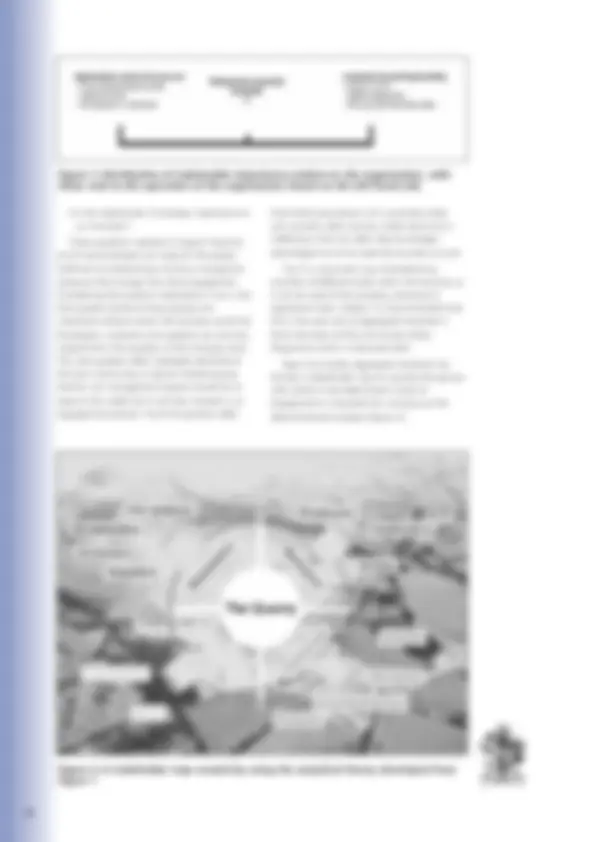
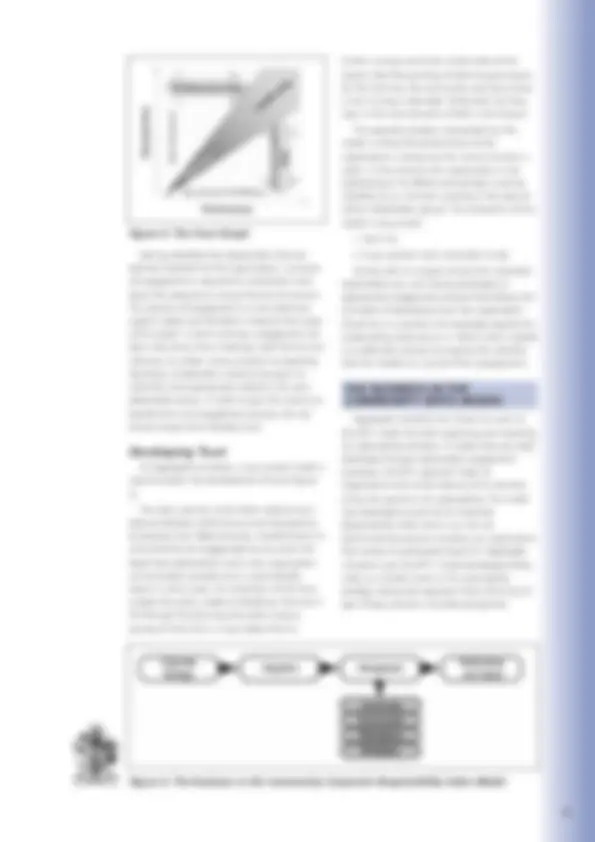
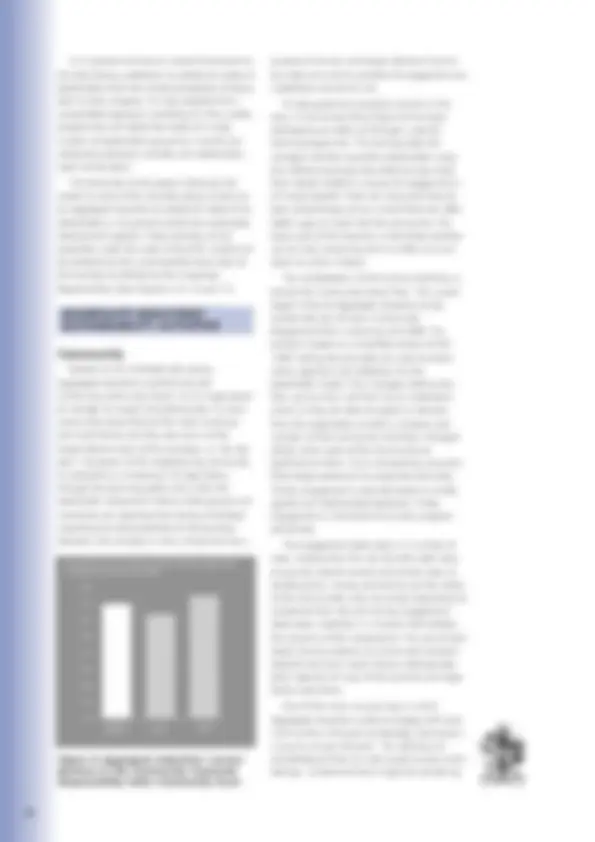
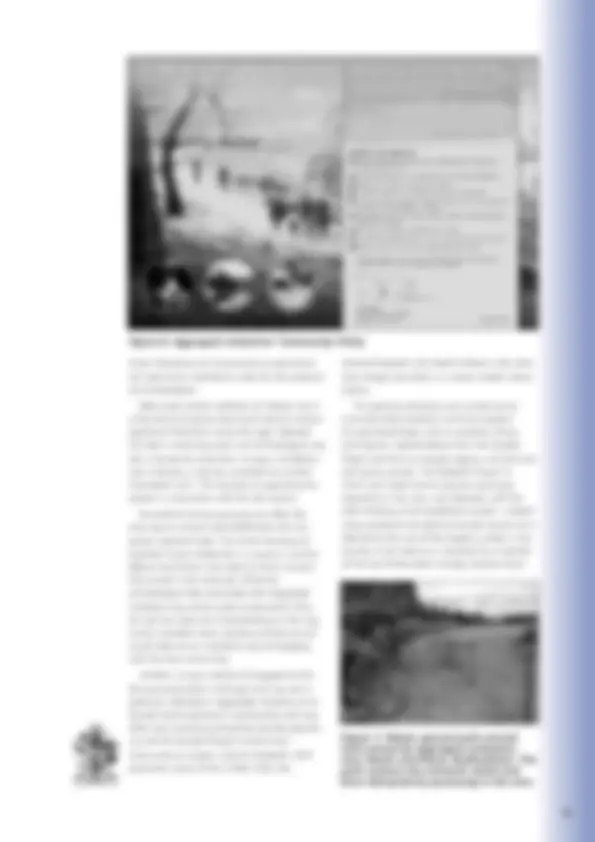
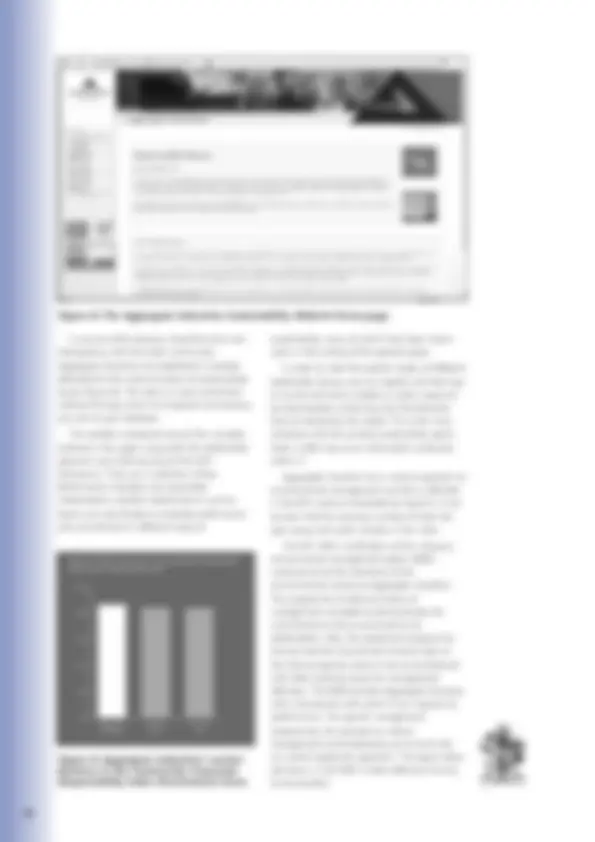
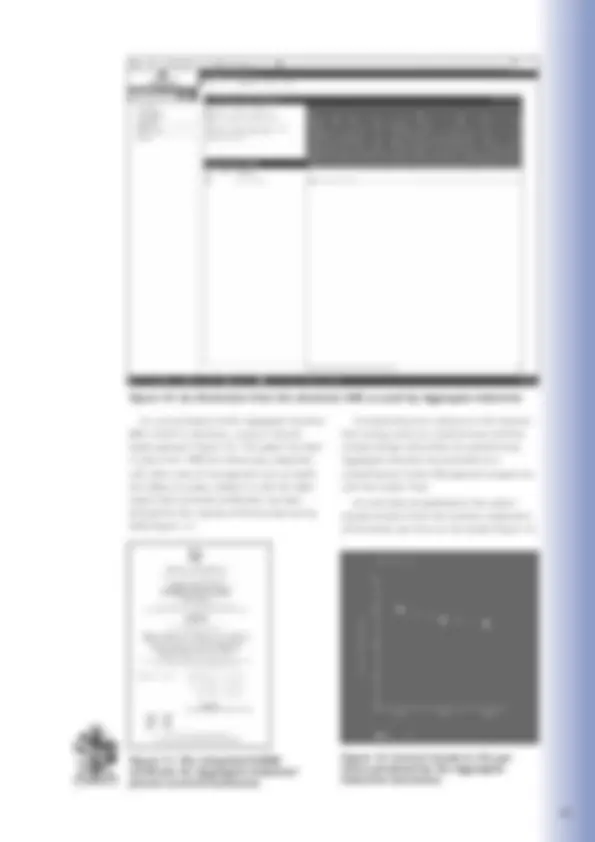
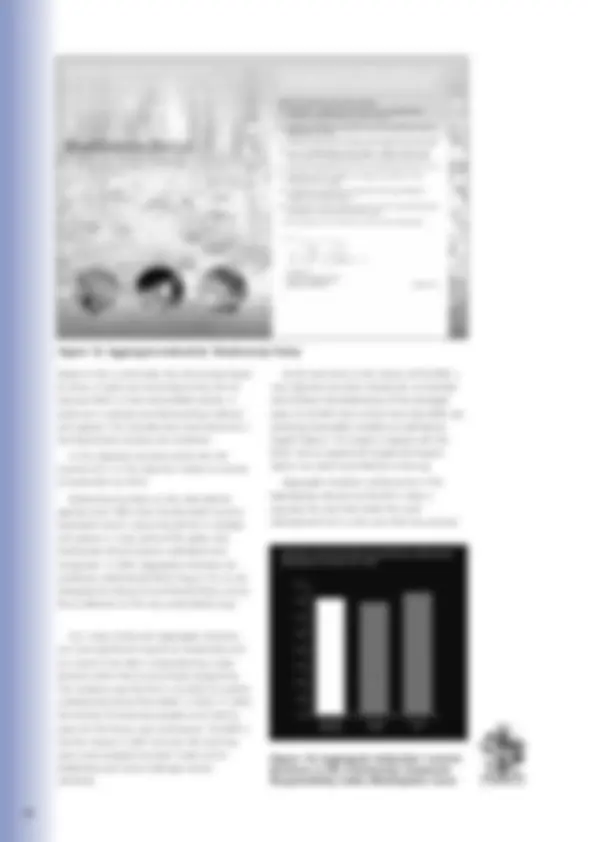
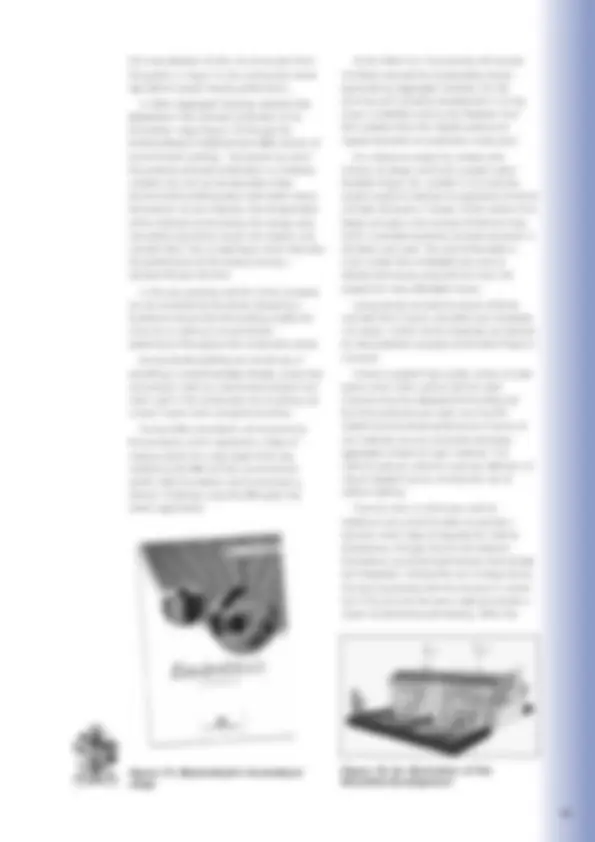
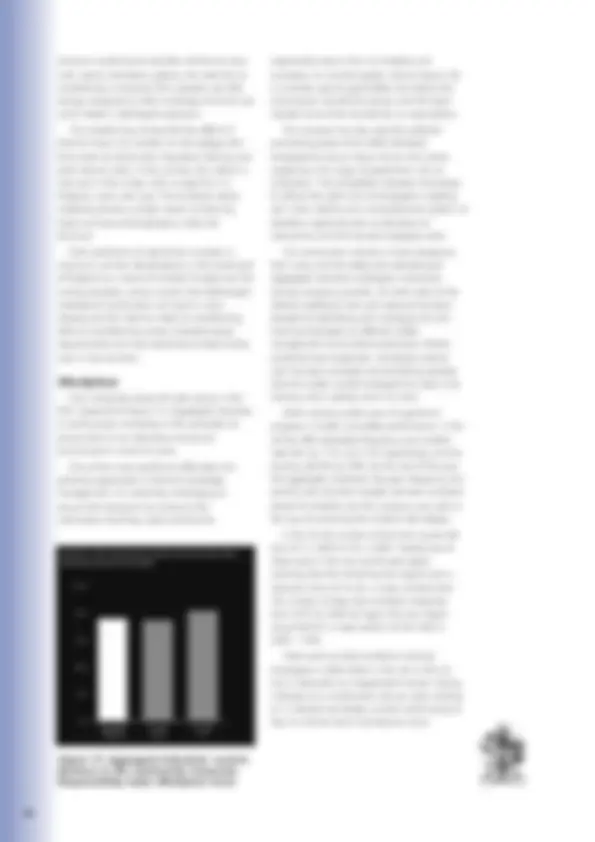
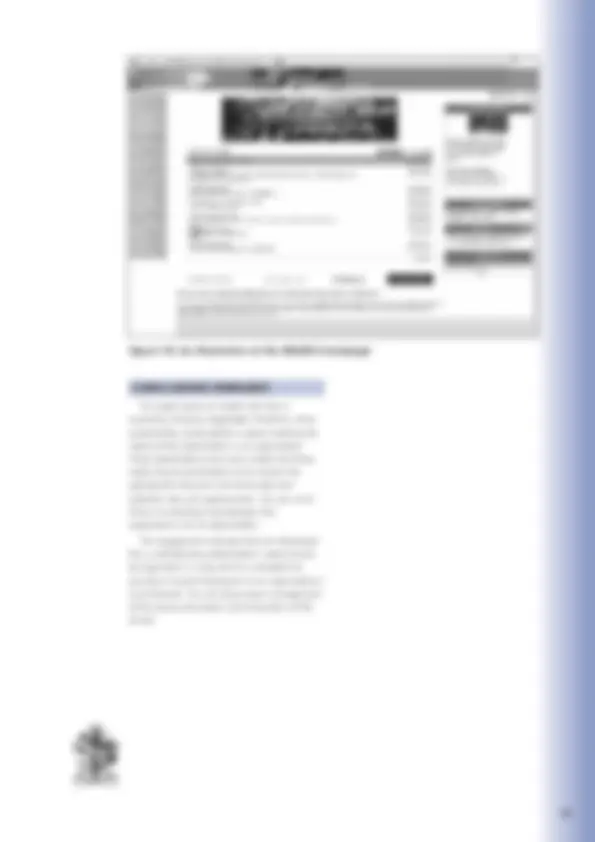
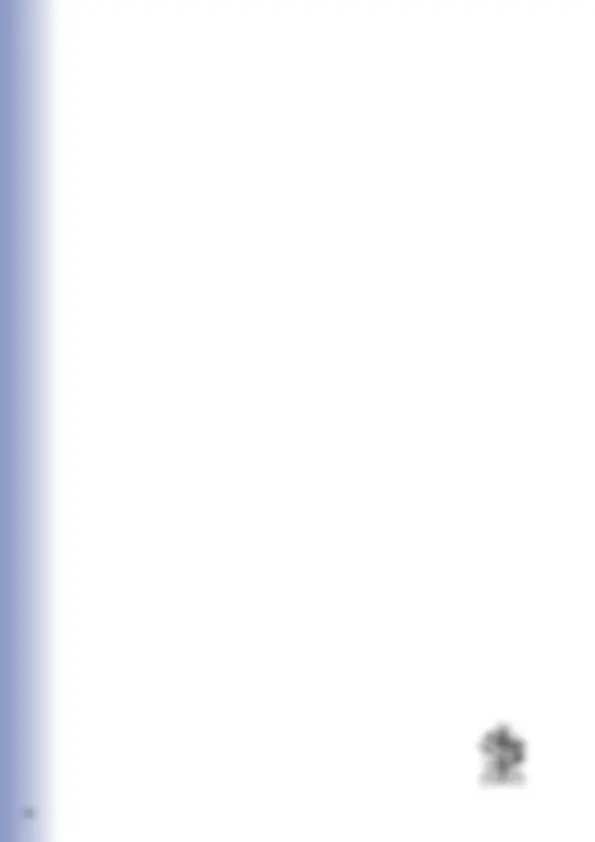
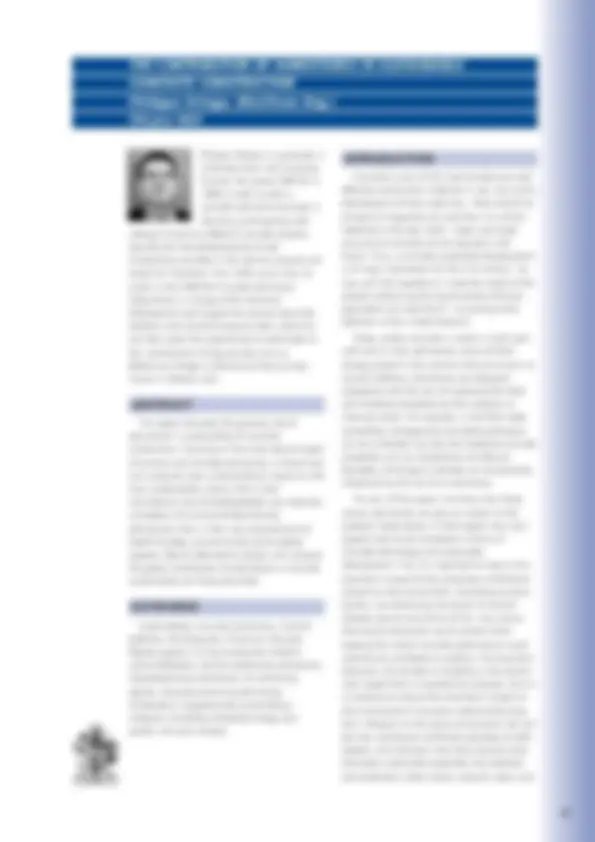
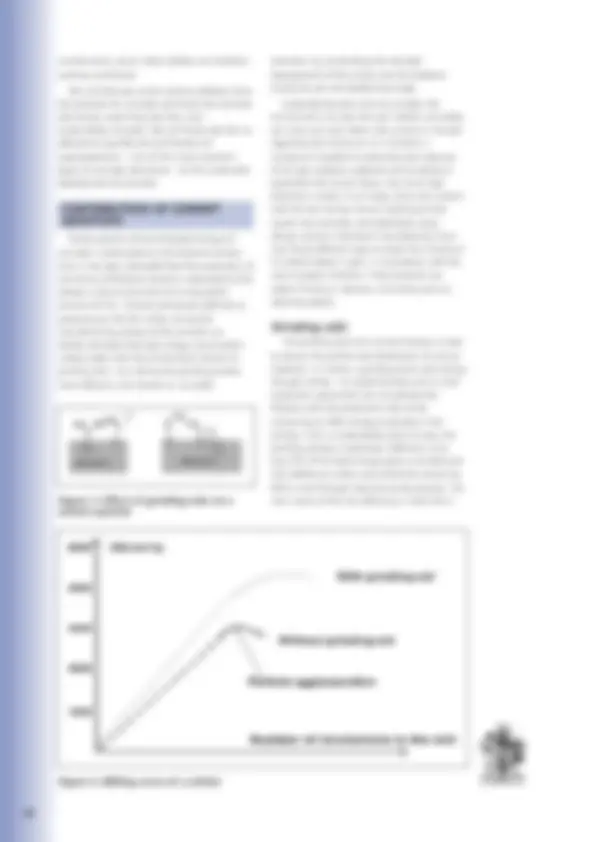
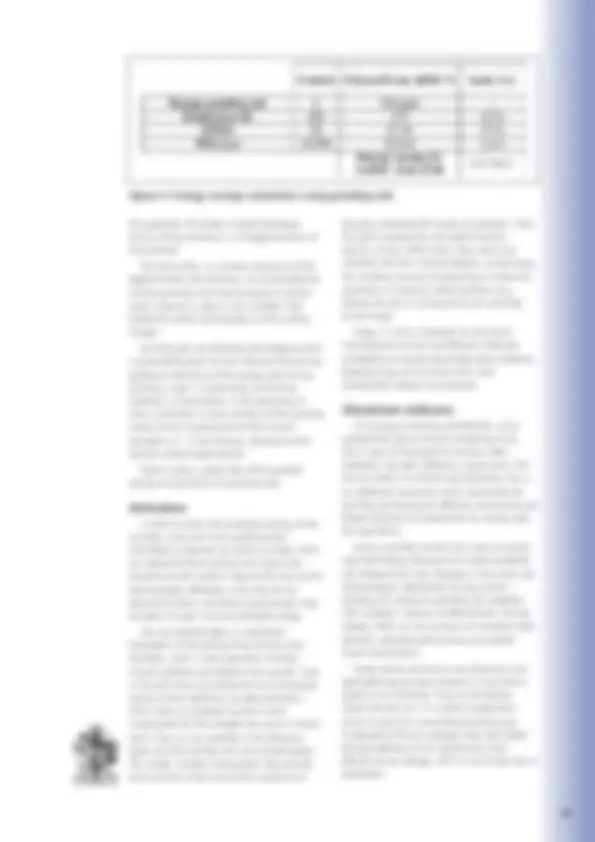
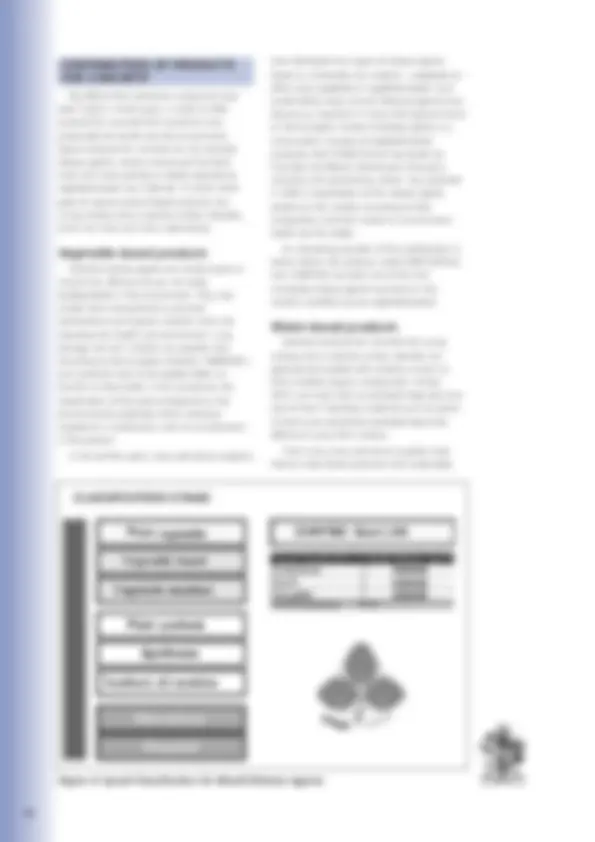
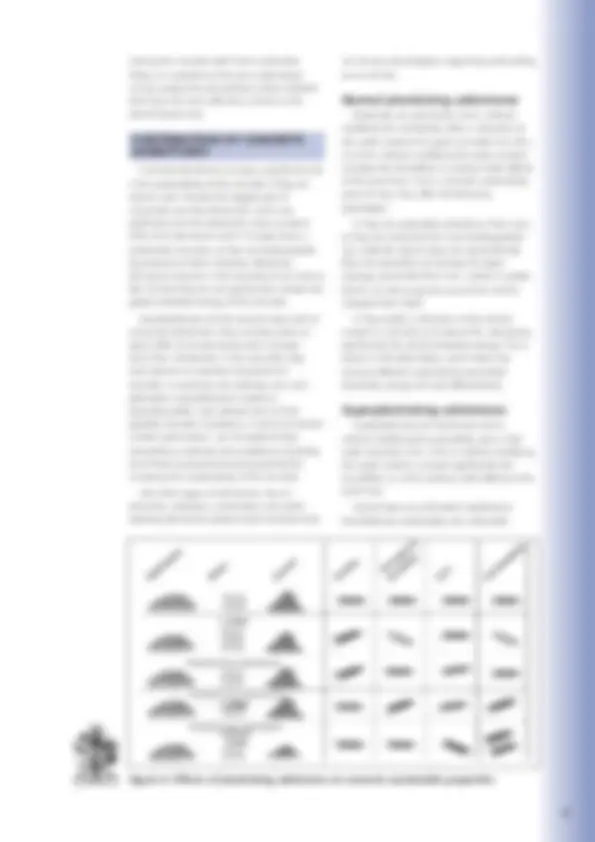
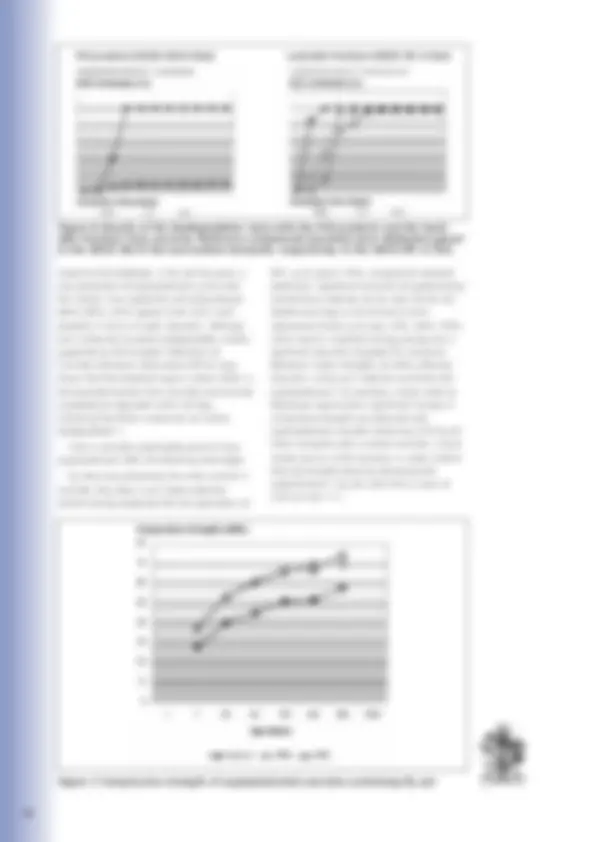
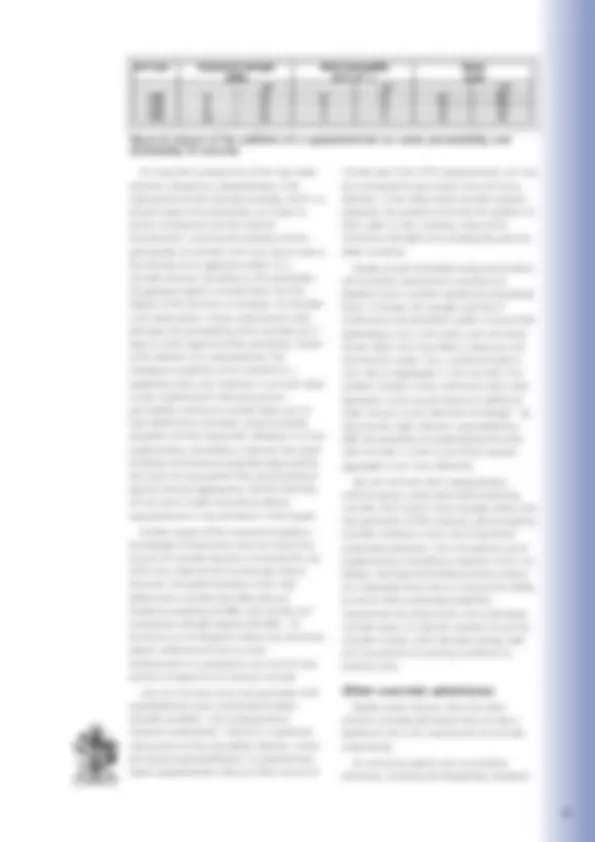
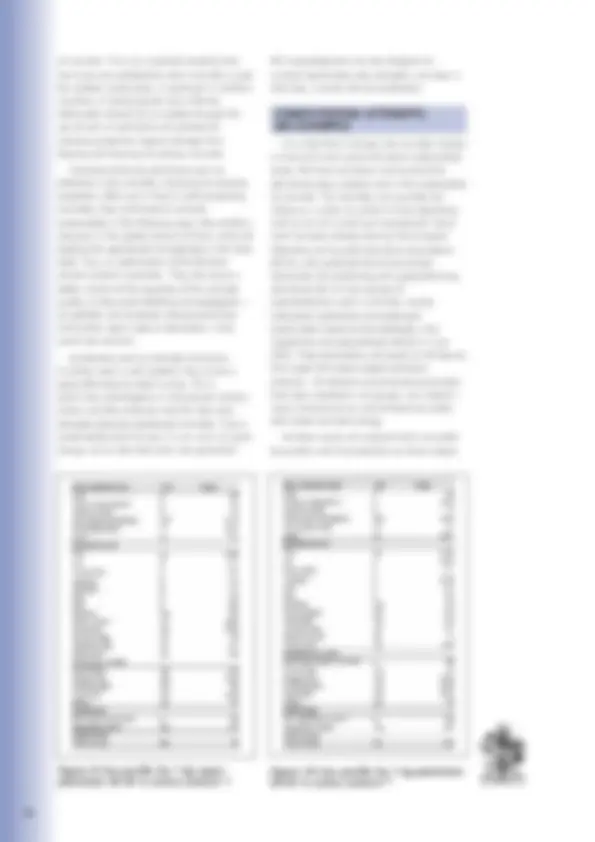
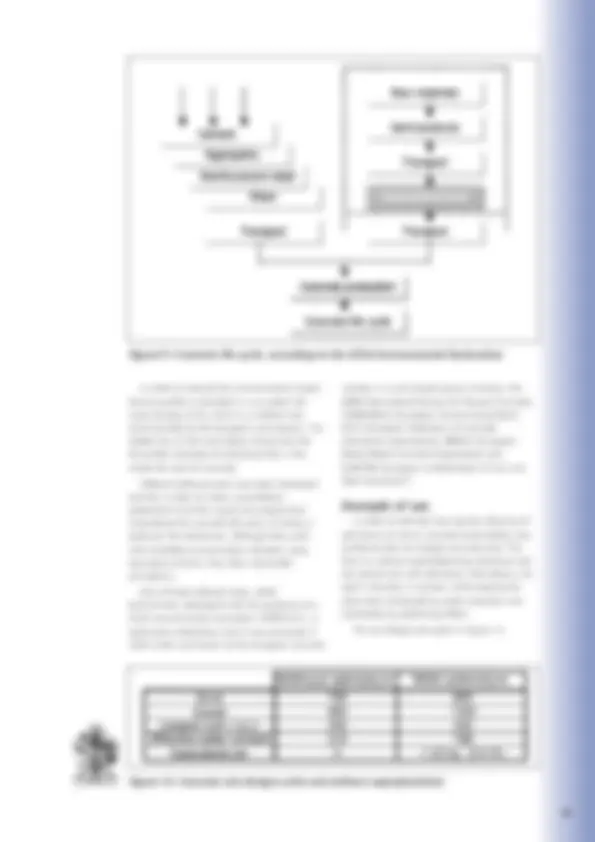
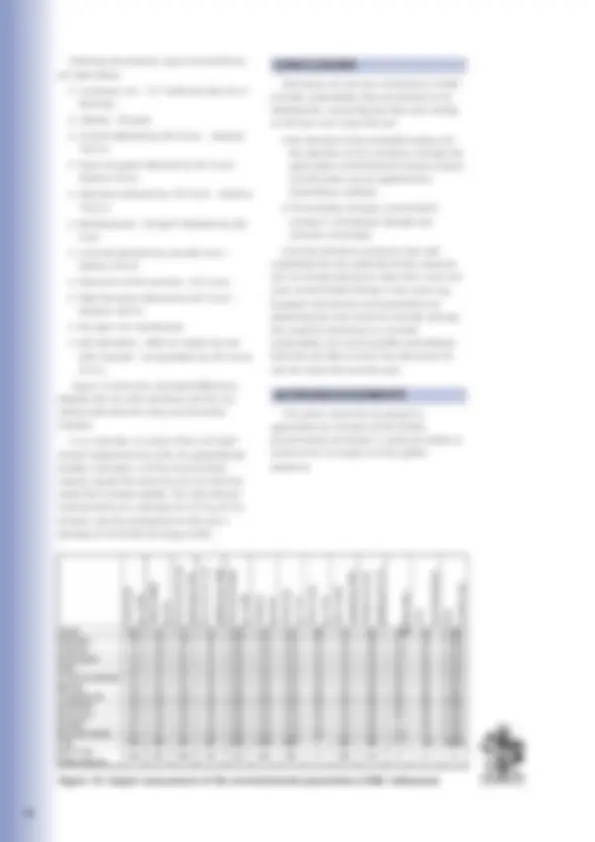
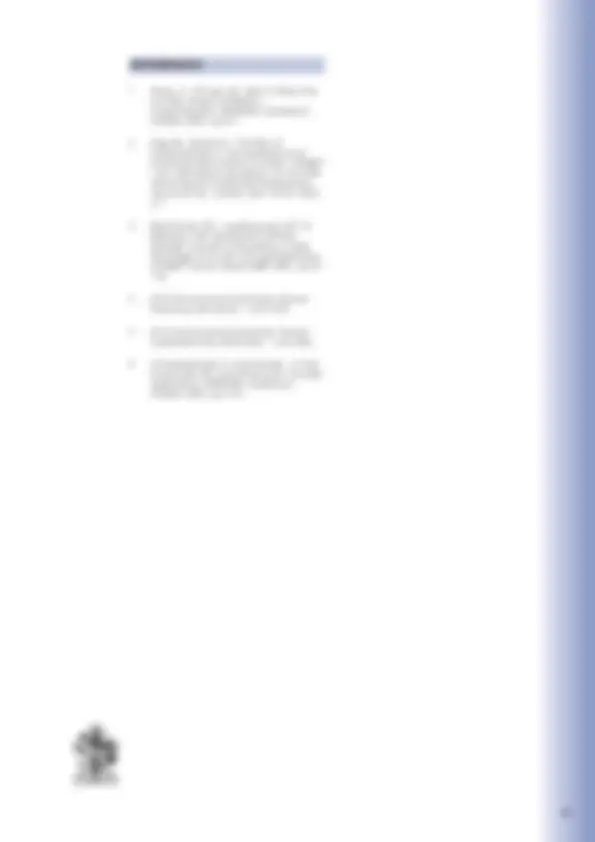
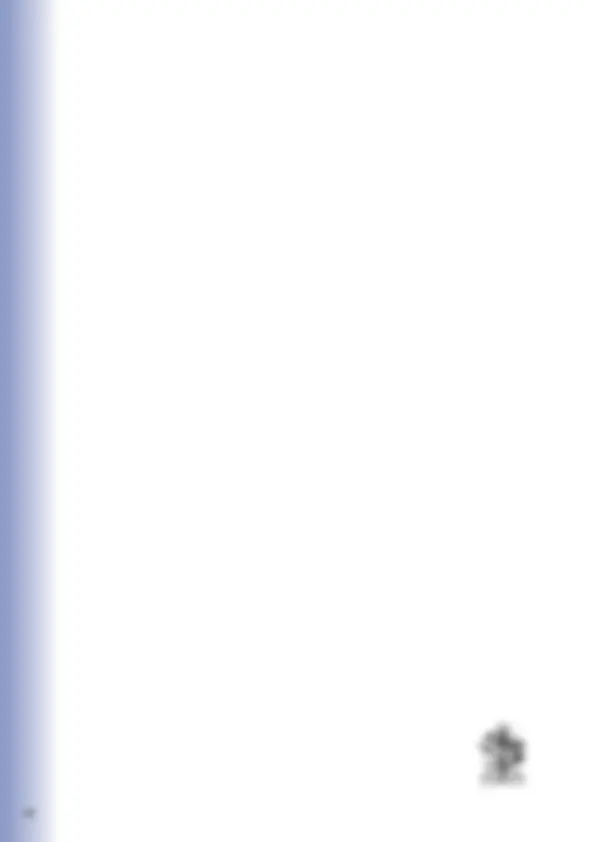
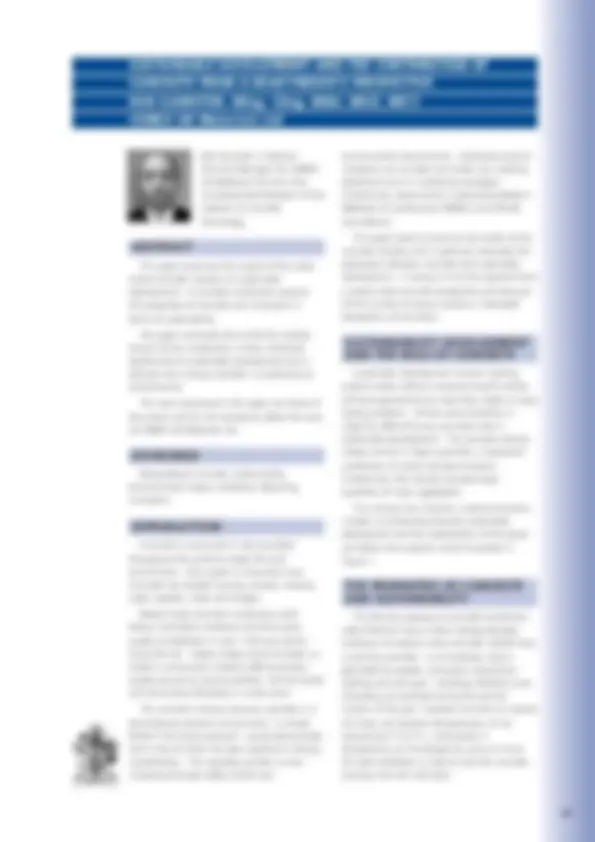
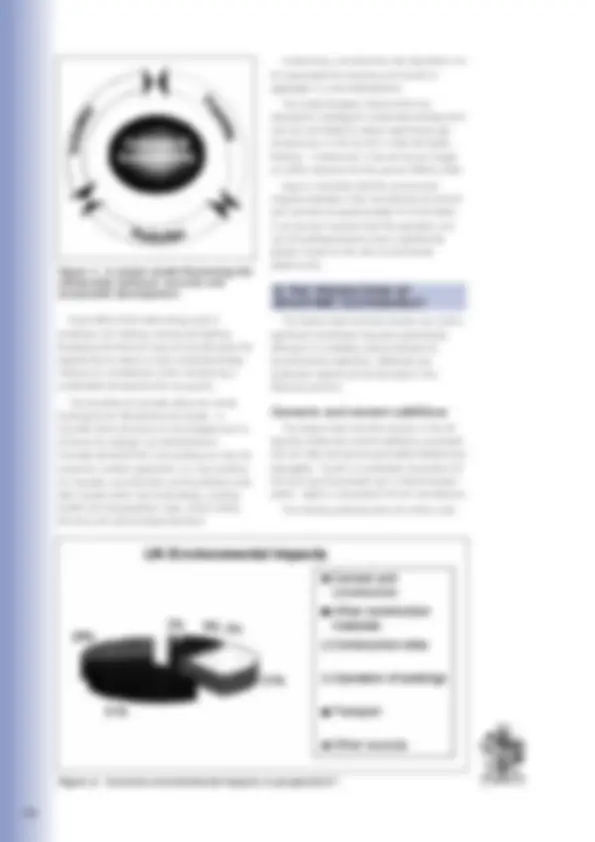
Study with the several resources on Docsity
Earn points by helping other students or get them with a premium plan
Prepare for your exams
Study with the several resources on Docsity
Earn points to download
Earn points by helping other students or get them with a premium plan
Community
Ask the community for help and clear up your study doubts
Discover the best universities in your country according to Docsity users
Free resources
Download our free guides on studying techniques, anxiety management strategies, and thesis advice from Docsity tutors
Related to cement, concrete for engineering students
Typology: Study notes
1 / 138
This page cannot be seen from the preview
Don't miss anything!
CONCRETE TECHNOLOGY
INSTITUTE OF
Published by:
THE INSTITUTE OF
Blackwater, Camberley,4 Meadows Business Park,CONCRETE TECHNOLOGY Surrey GU17 9AB
Email: ict@ictech.orgTel/Fax: 01276 37831
Website: www.ictech.org
Professor Peter C. Hewlett (Chairman) GROUP TECHNICAL ADVISOR FOR PRINCIPAL CONSULTANT -JOHN DOYLE GROUP PLC
BRITISH BOARD OF AGRÉMENT LTD
CHRISTEYNS UK LTD Peter C. Oldham Dr. Bill Price
LAFARGE CEMENT UK Graham Taylor
INSTITUTE OF CONCRETE TECHNOLOGY
INITIAL CONTACTS^ Laurence E. Perkis
Rights reserved. No part of this publication may publication are those of the Author and notpublisher. The comments expressed in thiswithout the prior written consent of thebe reproduced or transmitted in any form
necessarily those of the ICT. ISSN 1366 - 4824 £50.
Professional Affiliate Engineering Council
PRESIDENT’S PERSPECTIVE
his yearbook comes during what could possibly be best described as a period of transition for the Institute of Concrete Technology. As I write, we are in mid-stride of a momentous step in the forward march of the Institute – the proposed merger with the Concrete Society. This move is strongly supported by our membership and should benefit the Institute at least through shared resources, a heightened profile and increased conspicuity. The Concrete Society will gain a “professional wing” to further its education and training objectives. But rest assured that the Institute will retain its individual identity within the combined organisation. Interesting times, indeed. After a long tradition of residential Advanced Concrete Technology courses, we have just seen the successful completion of the first web-based course. Exam results are yet to be released but I understand that feedback from participants has been very positive. Although classroom-based courses may continue in some areas, this marks a major change for the former UK-based course. Now almost anyone, anywhere in the world with internet access, a good grasp of English and a bubbling enthusiasm for our grey stuff is a potential candidate. Many “graduates” of the residential course will no doubt bemoan the loss of the personal contact with the array of experts who were coaxed and cajoled (but seldom bribed) into lecturing for so many years. But look around, many of them have now moved on – and so must the ACT course. As you will see from the collected papers inside this yearbook, the 2006 Annual Convention Technical Symposium took “Sustainability” as its theme. And, in my opinion, it is difficult to think of a subject more worthy of this the most prestigious of events in the ICT calendar. By some definitions concrete can never be a truly sustainable material because of the inevitable consumption of at least some non-renewable natural resources. Nevertheless, if we instead substitute the term “reduced environmental impact” then there is a lot we can do to help in all parts of the so-called ’concrete industry’. For example: Designers can utilise concrete’s high thermal mass to increase the thermal efficiency of buildings and consequently reduce reliance on artificial heating and, in particular, air-conditioning with its high environmental impact. Specifiers can encourage the use of secondary and recycled materials or, at the very least, not unnecessarily exclude their use through outdated or ill-informed exclusion clauses in their specifications.
Product suppliers can seek to offer products with increased levels of secondary and recycled materials content, and to minimise waste by the incorporation of reject products and off-cuts within the raw materials for new products. The cement industry can continue to seek improved energy efficiency and further develop the use of non-fossil fuels. Aggregate suppliers and concrete suppliers, like school canteens, can help by making sure there are healthy options on the menu, so to speak. Researchers can continue to explore the properties of alternative aggregates, cements and other cementitious materials, and seek to identify any possible pitfalls. After all, just because something is hard and granular it doesn’t necessarily make it suitable as aggregate in concrete. Even code-writers have a crucial role to play by ensuring that codes and standards contain no unnecessary barriers but also that any essential safeguards are in place to ensure these materials and products can be specified and supplied with confidence. Perhaps it’s become a bit of a cliché, and I’m sure you don’t really need me to point it out, but we only have the one planet – let us as responsible concrete technologists use it wisely. By the way, whatever happened to those experiments making cement from moon rock?
COUNCIL, OFFICERS AND COMMITTEES - SUMMER 2006
Chairman
Secretary
(corresponding)
Chairman
Chairman
(corresponding)
Chairman
Secretary
Chairman
Secretary
(corresponding)
Chairman
Secretary
Treasurer
Chairman
Secretary
(corresponding)
planning also augur well for the precasting industry.
Precasting may come into its own taking further a process engineering approach, coupled with precision automation. Quality, convenience, speed and versatility are key with cost savings a potential added benefit. Government sponsored initiatives to maximise ‘off-site’ construction also play to the strengths of precast concrete solutions.
Doctor R F Bakker of Cemij BV Netherlands dealt with the re-use of materials in cement and concrete. In 1997 the use of ggbs, fly ash and associated secondary materials was well- established but less so alternative fuels for clinker production. Also at that time re-used demolition waste in place of coarse aggregate only comprised less than 1% of aggregate used. Dr Bakker’s view was rather negative and recycling and re-use were not predicted to increase significantly due mainly to cost disadvantage and questionable ecological trade-off.
The realisation of this somewhat gloomy prognosis about recycling for the UK is to be doubted with sustainability having a high political profile. Economics may well drive the environmental agenda and increasingly, waste materials will become secondary materials and entrenched attitudes will change.
Notwithstanding concrete’s proven advantages, the last 30-40 years have seen growing concern about reinforced concrete’s durability and maintenance. Corrosion preceded by carbonation was the concern of Dr M G Richardson (University College, Dublin).
The simple chemical conversion that is carbonation has been known since 1880 and up to 1990 some five hundred plus papers on the subject had been published. You might reasonably conclude that we should know all there is to know about the cause, effect and remediation associated with carbonation. The controlling factor of permeability and its reliable measurement in the laboratory and on site was regarded as key to both controlling and assessing the effect of carbonation. Understanding the inter-connected porosity of the paste phase has dominated our thinking and resulted in making
and designing more durable concrete as well as modelling more predictably the onset and progress of steel corrosion. Low permeability concrete requires:
We have the knowledge to make durable concrete, particularly in temperate regions. However, transferring this knowledge into site best practice has some way to go. This again raised issues of training and the skill status at site level and the adoption of measured performance factors at design and specification stage. Ten years on, we have made some progress but the indications are it is not enough.
Much concrete that is placed is not seen i.e. underground, behind facades and underwater. The latter was the, in part, concern of Ms U Kjaer of Ramboll Hannemann and Hojlund. Denmark, as a consequence of its geography, has of necessity built many bridges and tunnels, typified by the Öresund link between Denmark and Sweden. Such structures are ambitious and strategic and are built to last. A service life of one hundred years is demanded for permanent elements and fifty years for those that are readily replaceable. Quality control/assurance (ISO 9001) and good workmanship were considered as essential, plus adoption of modern technologies such as cathodic protection, epoxy-coated reinforcement, silane impregnation, permeable formwork and integrated sensors for monitoring corrosion. These structures and others globally are living testimony to what can/should be achievable in relation to durable concrete. The clock is ticking. These structures will presumably be closely scrutinised and progress corroborated or confounded. * Concrete Society Technical Report “Developments in Durability, Design and Performance-Based Specifications of Concrete” 1996, pp72.
At say, five or ten year intervals, the actual performance of the structures should be quantified, declared and compared to what was expected. Such prudent auditing will help to identify which measures actually contribute to extended service life and consolidate the practice of achieving durable concrete even under adverse conditions so engendering increased confidence in the long term performance of concrete structure.
We hear a great deal about concrete quality. No matter how well the process of making and placing concrete is specified and controlled, to achieve the expected quality the materials have to be up to the task. In this respect, the quality of cement is crucial and no more so than when using blended cements. The South African experience is relevant and was described in the paper by Dr G R H Grieve of the South African Cement and Concrete Institute - “Blended Cements: Control of Quality”.
Cement quality variation would seem to be a major problem in South Africa, notwithstanding the existence of standards and a history of use of cement additives. One of the drivers behind this trend is cost, resulting in sub-quality extenders sometimes being used. The situation was exacerbated by high proportions also sometimes being used. Taken together, this raises concern over the long-term durability of the resulting concretes.
These examples highlighted the need to have confidence in the underlying testing and conformity certification procedures. In some ways, protecting the users from themselves. This is difficult if compliance to a standard is not mandatory.
At the time of writing this article, it is not known if the proven implementation of SABS has occurred. What is clear, if the checking of conformance is not carried out, entrepreneurial opportunity can create a legacy of problems. Discipline and market sampling/auditing are essential.
In the 1990s and currently construction activity in South East Asia and the Far East has been substantial. C C Stanley of Test Consult CEBTP Ltd gave an overview. In some ways, this part of
the world readily adopts innovation and beneficial technical opportunity unhampered by excessive regulation, high taxation and political interference (part quote!). The problems familiar to concrete that have arisen are the same as in other parts of the world and in this regard history is repeating itself. Interestingly, the situation has kindled a commitment to high-performance concretes having exceptional durability, albeit at a price. Concretes having strengths in excess of 135 MPa and slumps of 100 mm are in regular use. Such concretes give design opportunities, for instance, the Tsing Ma bridge. Major constructions such as this using tertiary blends and w/c ratios of 0.39. The Chek Lap Kok Airport, Petronas Towers in Kuala Lumpa and the Central Plaza in Hong Kong are testimony to the confident, if not aggressive, use of high- performance concretes. Stanley predicted the trend to continue and that major activity would occur in Indonesia and South Vietnam.
There is opportunity for the best in concrete to excel in this region of the world. However, coupled with the opportunity is a real need to transfer the newer technologies to such advanced construction. There is an opportunity for skill and educational services to be offered. Is that happening, ICT and Concrete Society? I have reason to believe it is.
We can make every effort to provide excellent design, good materials and disciplined site practices that result in iconic structures. Nature then destroys all this effort in a matter of minutes by way of earthquakes. The result is social and material havoc. The insatiable demand for land use increases the likelihood of being subject to such conditions in the future and they need to be addressed. That was the concern of J E Roberts of The Engineering Service Centre of the California Department of Transportation. The North Ridge Earthquake in 1994 was a severe test case for damage remediation. The task was Herculean. It is difficult to envisage how such forces could ever be resisted. Main arterial road slabs tossed about like confetti, supporting columns compressed like sponges. Reclamation was rapid – a matter of months! Co-operation between all involved was exceptional and very effective. The disaster was also an opportunity from a design point of view.
Q: Graham, you know as much about the Institute and its members as anyone. Before we discuss your present role, tell us a little about yourself. You have experience as an engineer working on some major Civils projects at home and abroad? A: I worked for contractors mostly, on heavy civil engineering – motorways, power stations, terminals, chemical plants, etc. but also spent some time with a firm of consulting engineers. Just before we got married I spent 7 months on site in Sierra Leone building a jetty and my three- year contract in Zambia on a new facility for a copper plant was a condition of marriage. When we left Zambia our two young girls were getting to the stage where they needed stability in their lives so there followed over 13 years at the C&CA’s Training Centre, Fulmer Grange I also spent some time working for myself, a couple of years manning the BCA Hotline and a short period as Executive Secretary of Britpave, the concrete roads organisation.
Q: So what took you into civil engineering? A: When at school, I had an idea to become a meteorologist but was persuaded by my father and a colleague of his that civil engineering was the thing to do. Civil engineering has a lot of freedom in it, being out on site and making decisions. And meteorology comes into it too – most of construction work is weather-dependant. But it wasn’t all sunshine out on site, those cold winter days have taken their toll – I now have some arthritis. But it’s been an enjoyable career, moving about in the UK and abroad.
Q: At some stage you decided to concentrate on concrete as a material rather than an engineering element. You found this to be more interesting or more challenging? A: Dick Watson interviewed me for the job at C&CA and it was only then that I realised that I was already a concrete man – virtually all my
previous work had been in concrete. And I took the CGLI courses whilst working for John Laing Construction and came away with the silver medal, just about 40 years ago. Most of the concrete work on site was very straightforward and it was in the days before concrete technology really took off. The ACT course has, I feel, had a considerable influence on the development of concrete since its inception 30 years ago.
Q: I understand your father was a master baker. Do you see any similarity in mixing materials for a concrete element and mixing materials for a large wholemeal? A: I worked in dad’s bakery during holidays, making cakes mainly, and driving one of the delivery vans when I was old enough. The two processes do have similarities; it’s much the same art – mix proportions, constituents, moisture content and ‘workability’ all come into cake making; the main difference, of course, is the application of heat. I squirm at the use of the word ‘cement’ for concrete – you wouldn’t invite someone round for tea and offer them a slice of ‘flour’, would you? The big difference is that you can’t eat concrete leftovers and I was frequently told off for eating things like the off-cuts from Swiss rolls!
Q: Tell us a little about your family. Have you advised your children to follow a similar professional path to yours? A: My wife, Sandra, was a teacher and we have been married for over 40 years now. It’s amazing how many engineers marry either teachers or nurses – there must be an inadequacy there, or is it a desire to be ‘mothered’? Our two girls both have children of their own. The older one lives in France where she and her husband are renovating an old farm property, turning the barns into gîtes. It has amazed me how well the grandchildren have settled into a foreign country, speaking French almost like natives and not wanting to return to life in England. The younger
daughter and her husband and 4-year old daughter live quite close to us. We have recently bought a modest cottage in France to be able to spend time with both families. Neither of the girls was interested in engineering, although Kate did appear in a book on concrete mushrooms. She trained in hotel management and the other one advises NHS trusts on fuel procurement issues.
Q: I have heard you have a good bass voice. You have always enjoyed choral singing? A: Yes, I love singing but am quite happy being buried amongst the second basses; I don’t have a solo voice – although I did play the Captain of Gilbert and Sullivan’s HMS Pinafore at school. I think by now I’ve sung most of the more popular – and some not so popular - major choral works from Brahms, Beethoven, Elgar, Mozart et al. Being under the baton of Sir David Willcox singing The Messiah at the Albert Hall last November was the icing on the cake. I now sing with a small, friendly choir; nothing too adventurous but we enjoy doing a couple of concerts a year.
Q: You are generally the person who has most communication and correspondence with members of the Institute. Do you think the Institute represents itself well to the membership and to industry in general? A: Some of the things I’ve tried to do since I took over from Roy Jolly are: keep the membership together; keep them informed; provide them with a focal point and help them when they need it. I hope that I’ve succeeded on that front. But I’m worried that the construction industry, and the concrete sector in particular, does not recognise the Institute for what it is. The push towards multi-tasking, probably seen as financially rewarding, has had an adverse effect on our membership figures. My feeling is that this will come home to roost in the future. However, the Institute has not been effective at promoting itself and the benefits of membership to those who need us.
Q: You are quite involved in the potential closening of ties with the Concrete Society. Your role will then be more important than ever, in order to maintain the separate identity of the Institute from the Society. Will this be easy? A: It is important that the Institute does not lose its identity and this seems to be the view of both organisations, especially our members, so it should be easy. To this end I feel it is essential that we continue to have someone dedicated to the
membership and to promote the Institute. If things go to plan, I intend making sure that the merger happens smoothly and then I shall retire; I will take the presentation of beautiful crystal glasses at Convention 2006 as a hint that this happens!
Q: The retention of identity is obviously crucial, and the promotion of the Institute is, as you say, essential. Do you think this will be made easier after the proposed merger, or does this worry you? A: The Concrete Society seem to want to make us a training and certification organisation and it is therefore in their best interests to make sure that the ICT has a high profile. ICT members can also make valuable technical contributions to the Society's technical committees if they don't already do so. However, there has always been a social side to the Institute, almost unique in organisations of this kind, and this is an essential part of its existence. The ACT course promoted interaction amongst previously arms-length people and disciplines. In short, we cannot afford to lose our identity, and being part of a larger organisation can only help.
Q: As "our man in Blackwater", with all the other varied and diverse trade, professional and lobbying organisations emanating from the cement and concrete industry, do you feel the ICT, bearing in mind our size relative to some of the larger concerns, can feel it has a loud enough voice in commenting on events and developments which affect the Institute and its members? A: I have the feeling that, apart from the six employees who are members, there are people in Riverside House who don't fully understand where ICT fits in. But most of those in my immediate vicinity are there to sell cement and concrete to specifiers and architects and are not all concrete people. I do get invited along to some meetings, such as the one determining what publications are needed by the industry and I have hopefully persuaded them to include site personnel. Most of the inter-organisational co-ordination is between the three main chief executive officers, with occasional reference to the other guest organisations.
Graham, many thanks for this interesting and thought-provoking conversation. On behalf of the ICT Council and Members, I would like to thank you for your time and thoughts. I hope that you and Sandra enjoy the fruits of you labours on retirement and wish you well for your time in France.
storage of the various levels of waste generated both during operation and subsequent decommissioning. To support this need, starting from the mid-late 1970s, a 20-year expansion programme commenced at Sellafield to cope with the demand for reprocessing, both within the UK and commercially from overseas. These included large storage ponds, new reprocessing facilities, notably THORP (Thermal Oxide Reprocessing Plant), and a number of waste treatment plants and associated product stores. During this period, Sellafield was probably one of the largest construction sites in the world, and in the order of 1.5 million cubic metres of concrete, mainly of high quality structural grades, were produced.
The advent of the Prestressed Concrete Pressure Vessel (PCPVs as they became known) created a unique and unprecedented challenge for the designers, the concrete technologist and the constructors. It was likened to the space race in civil engineering.
The design life of these structures was 30 years
Such operating conditions for concrete, let alone in such a demanding environment, were totally unprecedented and required an understanding of both the short and long term behaviour of concrete that went way beyond the civil engineer’s normal characterisation of the material in terms of ‘slump’ as a measure of its properties in the fresh state and 28 day compressive strength, as measured on an artificially cured 150mm cube, as providing a measure of its properties in the hardened state.
Furthermore these were mass concrete structures with walls of up to 12 metres thickness which when combined with the generally high cement contents used (approx 420 kg/m 3 ), would result in a high temperature rise during early age hydration of the cement and the risk of either cracking during cooling or distortion of the numerous penetrations that passed through the concrete.
Essentially a detailed understanding of the material was needed at a fundamental physical and chemical level such that its properties could be adequately described at all stages through both construction and over the full range of conditions throughout its operating design life.
The unique nature of the PCPVs required that relative movements were minimised and predictable. For example, fuel rods were generally loaded through the top cap of the vessel, while the reactor sat on the bottom cap. Excessive relative movement between the two would, therefore, severely jeopardise the operation of the reactors Movements occur in concrete for a variety of reasons, but principally as a result of changes in temperature, moisture or loading. Drying shrinkage was not considered to be significant due to the massive section sizes. Thermal movements occurred at various stages in the life of the vessels, beginning with construction. Concreting involved massive sections and was, in many respects similar to dam construction. Commonly, 2 m thick sections were cast using what was, at the time, considered to be high strength concrete (6000 psi, about 40 MPa). Early thermal movements were thus significant. Longer term thermal movements also occurred as the vessels were commissioned and operated and the design had to accommodate local temperature excursions. A principal concern of the designers, however, was its long term deformation under sustained load, or creep, which was known to be significantly affected by temperature and moisture movement, as this would have significant impact on the performance of PCPVs At ambient temperatures, for structures such as prestressed concrete bridges and offshore oil and gas rigs, the effects of this property in terms of long term deflections and prestress relaxation can generally be adequately accommodated by applying a factor to elastic deformations. However, the critical importance of creep in calculating long term movements of the structure with respect both to tolerances on penetrations and plant and to prestress relaxation, meant that this simple approach was totally inadequate to determine the measures needed to either accommodate or mitigate it’s effects. Furthermore, at the time, the effects of both age
Station Wylfa Hartlepool Heysham Heysham Torness Sizewell B A 2 [1] Source of materials Cement Padeswood Weardale Ribble Ribble Dunbar Masons PFA Fiddlers Ferry Longannet Ironbridge Sand Igneous Glacial Glacial Sea dredged Pit Sea dredged Aggregate 40mm 40mm 40mm 40mm 20mm 20mm Limestone Dolerite Hornfels Dolerite Dolerite Sea dredged Admixture Lignosulphonate plasticizer used in all mixes Quantities and proportions (kg/m^2 ) Cement 410 420 435 270 340 215 PFA - - - 90 115 140 Water 175 205 190 165 175 140 Sand 600 630 620 705 720 660 Aggregate 1215 1280 1190 1315 1090 1230 Density 2400 2535 2435 2545 2440 2385 w/c 0.42 0.49 0.44 0.46 0.39 0. a/c 4.40 4.52 4.15 5.56 3.98 5. %PFA - - - 25 25 40 Strength 50 60 55 52.5 60.5 61 (MPa) [1] Secondary containment structure for Pressurized Water Reactor
at loading and elevated temperature on this property had not been fully investigated.
As a result a pioneering research programme was commenced in the early 1960s to measure the magnitude of creep deformation at maximum design levels of sustained uniaxial load. The programme was designed to obtain data that would reflect the in-situ performance of the concrete [1,2,3,4]^. The following factors were therefore taken into account:
14, 28, 60, 180, 400 days, 3 years, 10 years and in some limited cases as late as 24 years, as part of the development of the safety case for continued operation beyond the notional design life of 30 years ,sustained load being maintained over such a period of time as to enable confident extrapolation of the data over 30 years. In the event, over a period of approximately 25 years, six number concretes, the details of which are given in Table 1 [5]^ , were comprehensively tested in a moisture stable ‘mass concrete’ state with representative samples being maintained under sustained load and deformation measurements made over a period in excess of 20 years. In total approximately 400 samples were loaded together with a further 150 samples that were maintained under identical conditions as unloaded control samples. Test samples took the form of 150mm diameter by 450mm long cylinders, which were sealed in butyl rubber jackets to simulate the mass concrete conditions (Figure 1). The 3: aspect ratio of the test cylinders was chosen to ensure that over the central 1/3rd height, where strain measurements were made, a uniaxial stress state existed, this being unaffected by the lateral restraint induced by the bearing plates of the loading frames.
70% of the concrete by volume, is of overriding importance. It was established that if the aggregate had a modulus of greater than 11. million psi (76 GPa), creep would be acceptably low and similar from one concrete to another. The measurement of the E value of aggregate sources therefore became key to its selection. Hard, crushed limestone and dolerite were the favoured rock types.
Other key issues in mix design that were of importance in minimising creep included ensuring that the w/c ratio was generally less than 0.45 to ensure that on full hydration of the cement, a discontinuous capillary structure is achieved, thereby minimising movement of the absorbed water within the cement gel under the action of temperature or drying. Also paying particular attention to the packing of the total aggregate system (coarse and fine) was of importance to minimise the volume of cement paste whilst still achieving a workable mix.
To support the calculation of temperature and temperature gradients in the concrete during both transient and steady state conditions, thermal conductivity and thermal diffusion coefficients of the concrete were measured. Elastic modulus under both initial and cyclic loading and long term shrinkage caused by the changing moisture state within the cement paste due to continued long term hydration of the ordinary Portland cement were measured on identical samples to those used for the creep tests.
The results from this programme were used to support the design of twelve PCPVs built at Wylfa, Hartlepool, Heysham (4No PVs), Hunterston and Torness nuclear power stations.
A particularly complex and vitally important region of the PCPV is the ‘standpipe (or SP) zone’ through which fuelling and reactor operational control are achieved via an array of up to 300 no. 300mm diameter tubes which run vertically through the 6metre thick pressure vessel top cap down to the top of the reactor core some 5 metres below the soffit of the top cap and upward to the fuelling floor which is itself some 4 metres above the top surface of the top cap. Due to prefabrication of the standpipe array, concreting of the top cap had to take place from fuelling floor level. Matters were made more
complex by the thickness of the ligaments between standpipes being as little as 150mm. For Wylfa, where the ligaments were 250 mm thick a mix, based on the main PV mix but with a reduced maximum aggregate size of 20 mm, was used to concrete the SP zone in twelve 0.5 metre thick pours. The low pour height ensured no heat of hydration problems For the PCPVs at both Hartlepool and Heysham where thinner ligaments existed, it was decided to cast the whole Standpipe Zone as a single 300 cubic metre pour via small diameter tremie pipes running from a temporary working platform set at fuelling floor level. Two issues were of particular concern:
During the 1990s many of the reactors in the UK had reached the end of their notional design life of 30 years but were still performing efficiently. To support their continued operation the Health & Safety Executive required that evidence be provided on the performance of all components of these highly complex structures, including the concrete. Fortunately, Taylor Woodrow had maintained a number of specimens under test, some for over two decades, and these formed the basis for a new research programme [7] with the following objectives
determine the effects of a loss of coolant accident (LOCA) in which the temperature of the concrete may locally achieve a temperature of 150˚C )
construction phase of each Nuclear Power Station. From this data, models for predicting the late-life, properties of PCPV concrete were derived [8]^. The late-life test programme demonstrated very clearly that the concrete was able to withstand sustained load and elevated temperature (up to 95˚C) over a long period without detriment to its performance. Indeed, as shown in Figure 3, what were initially concretes with a 28-day characteristic cube strength in the