
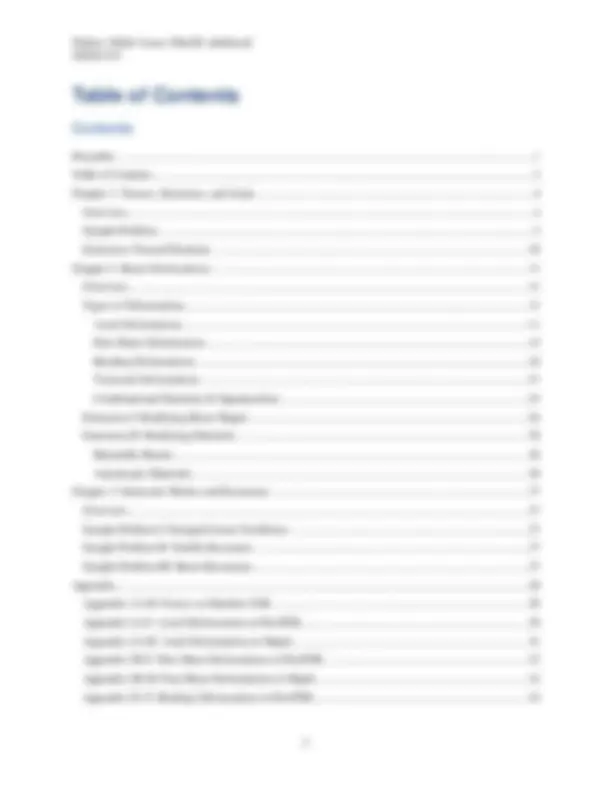
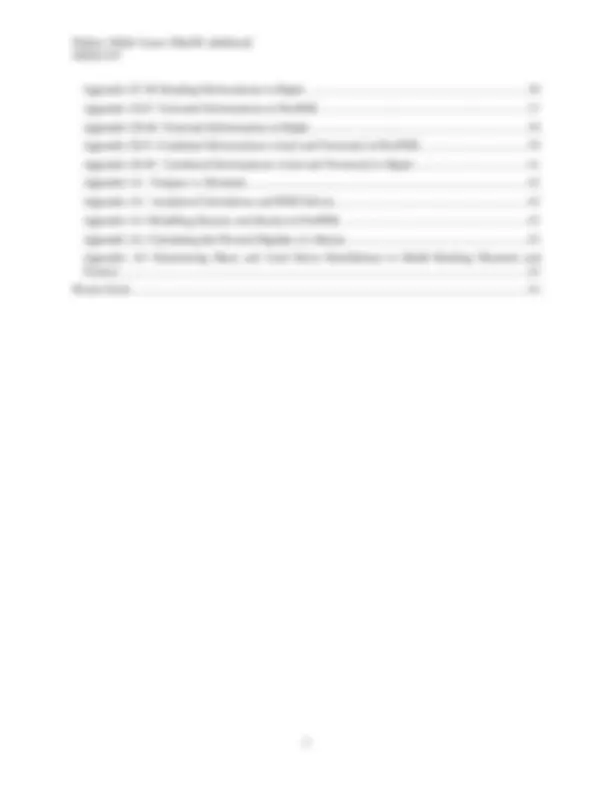
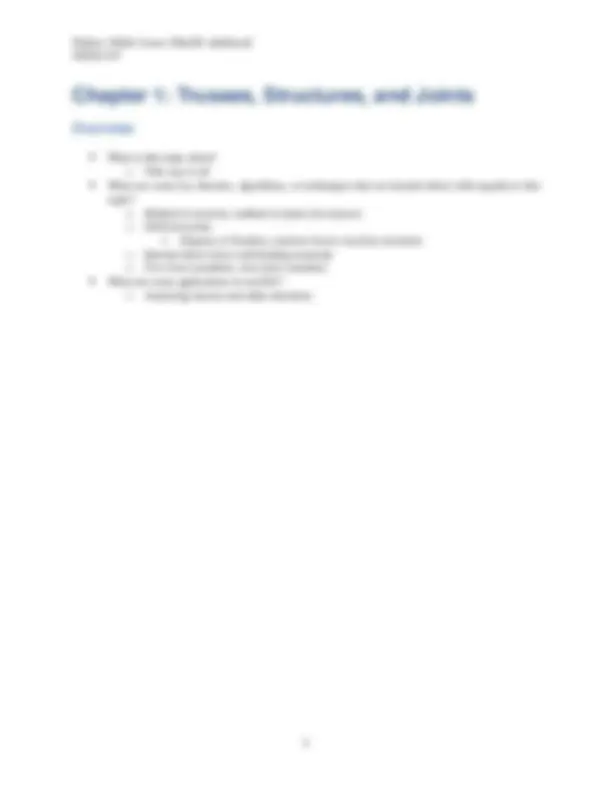
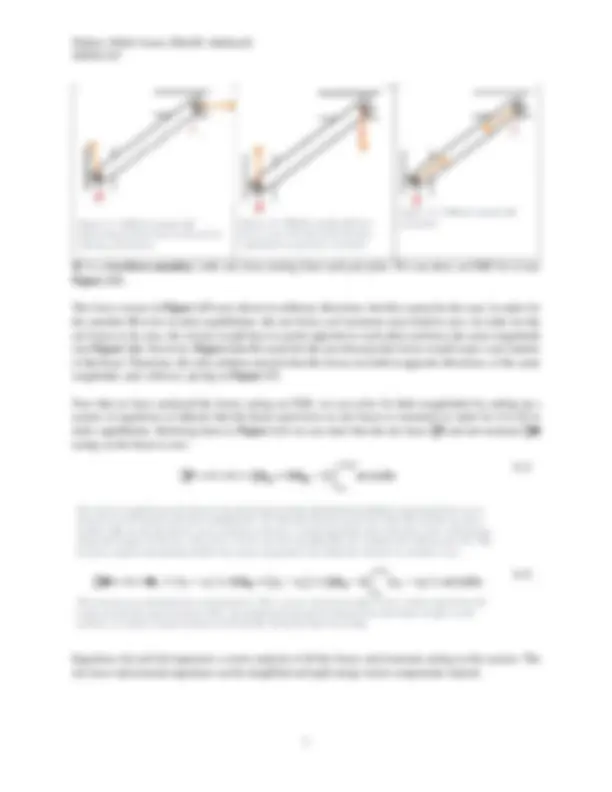
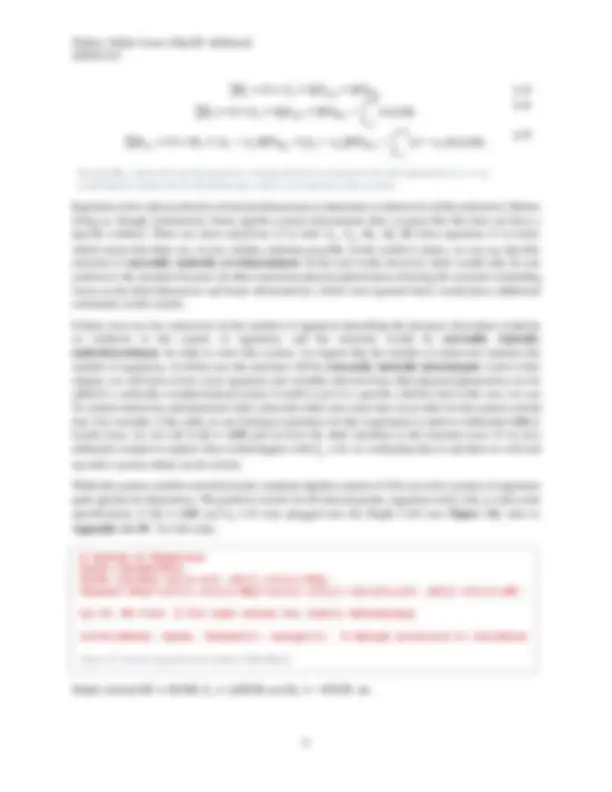
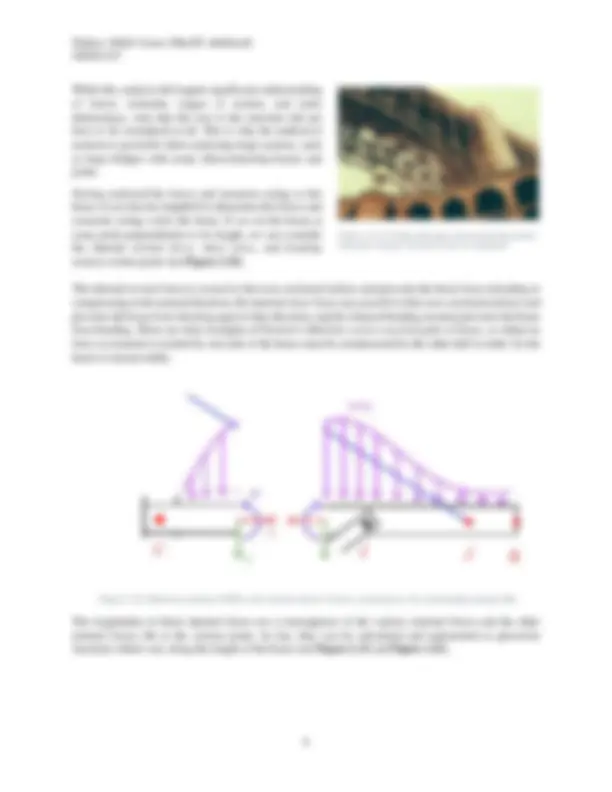
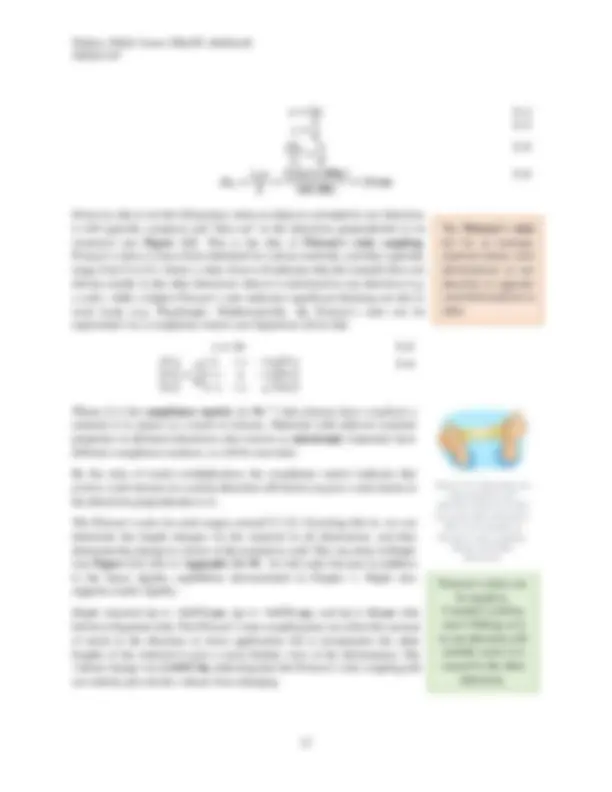
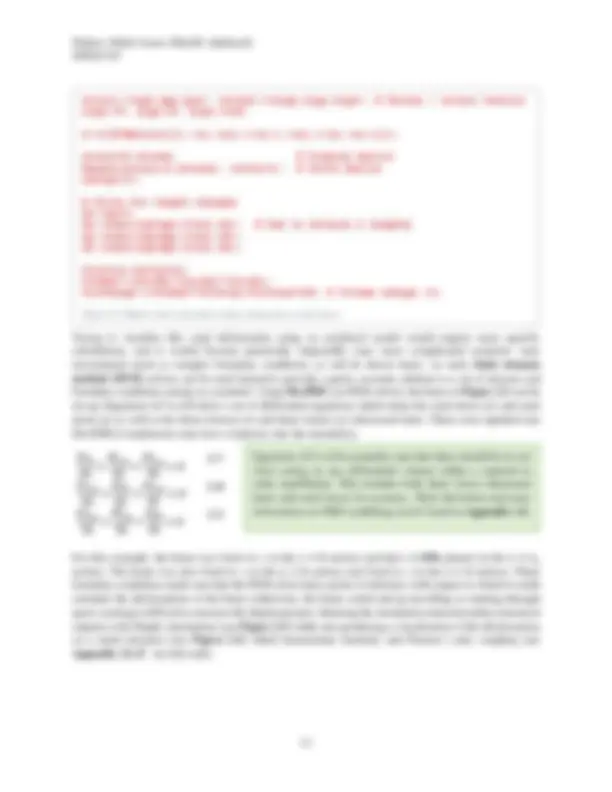
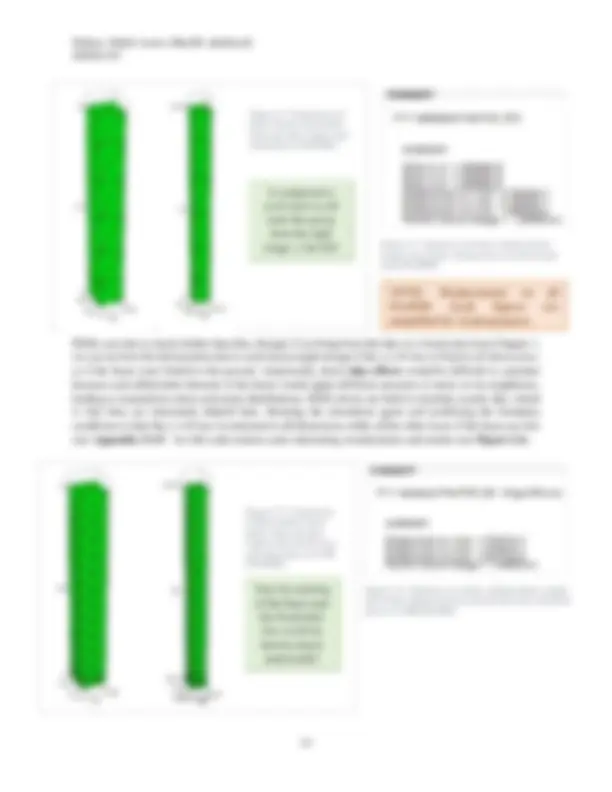
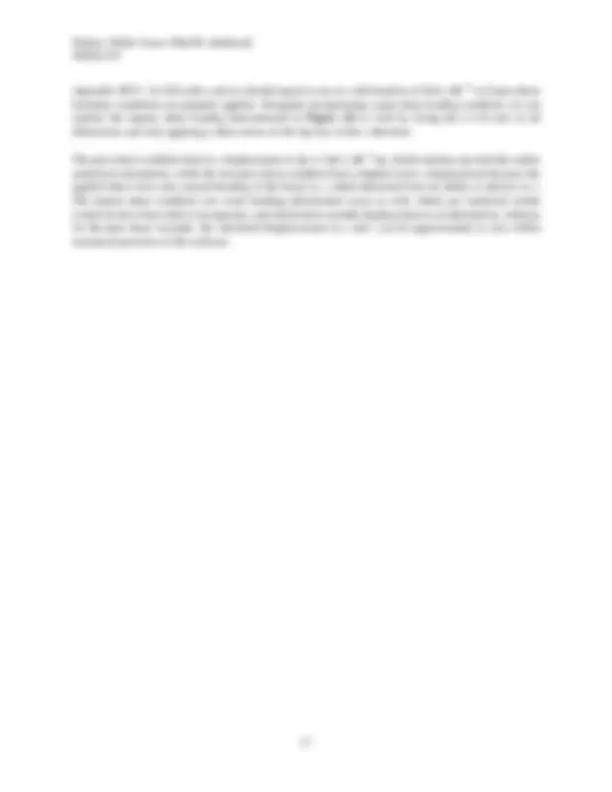
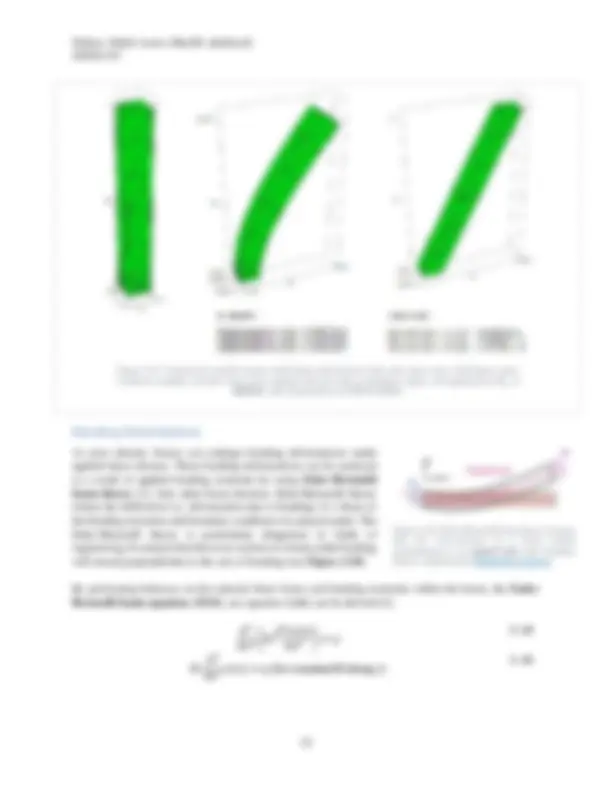
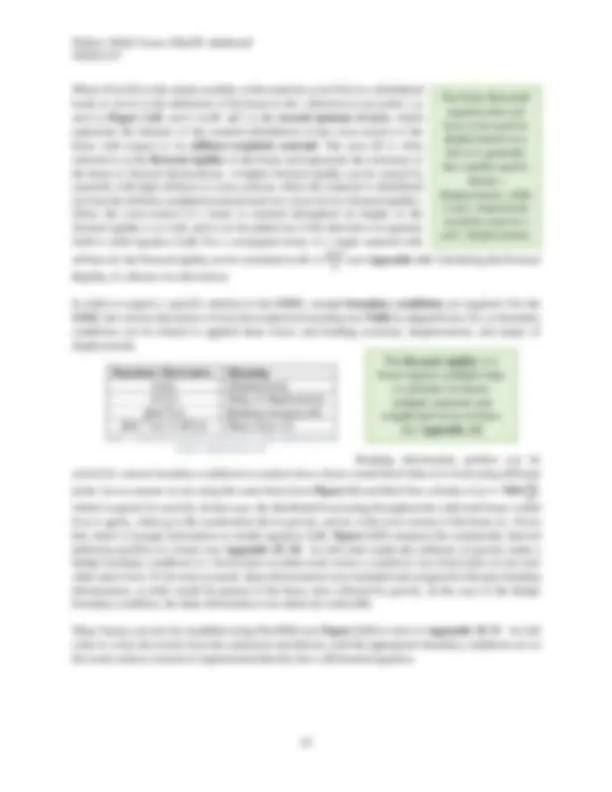
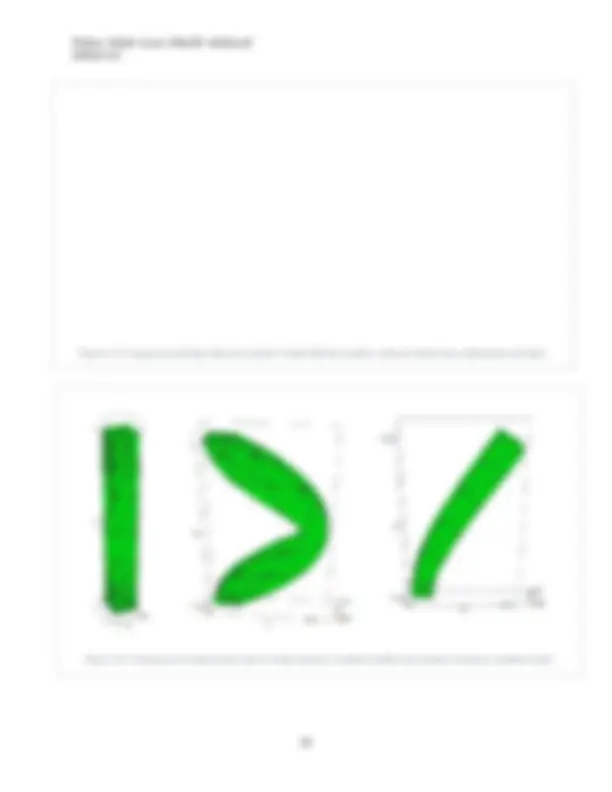
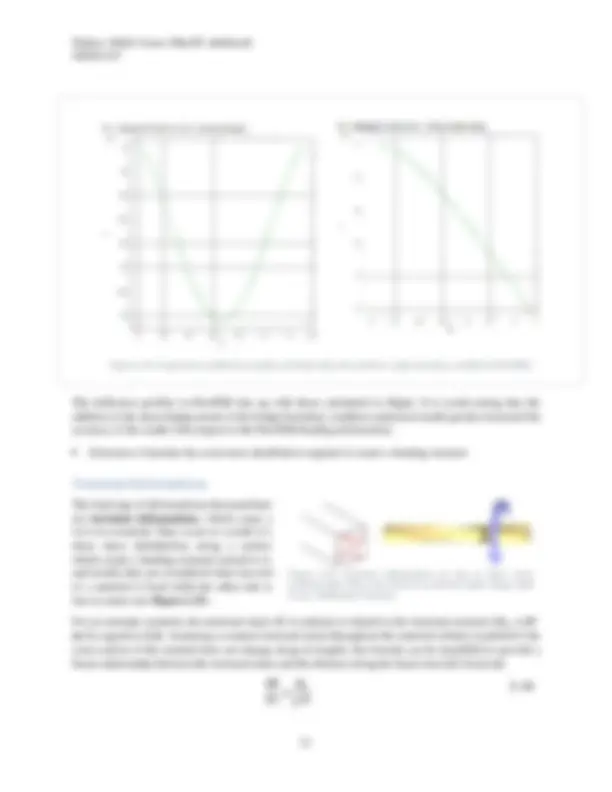
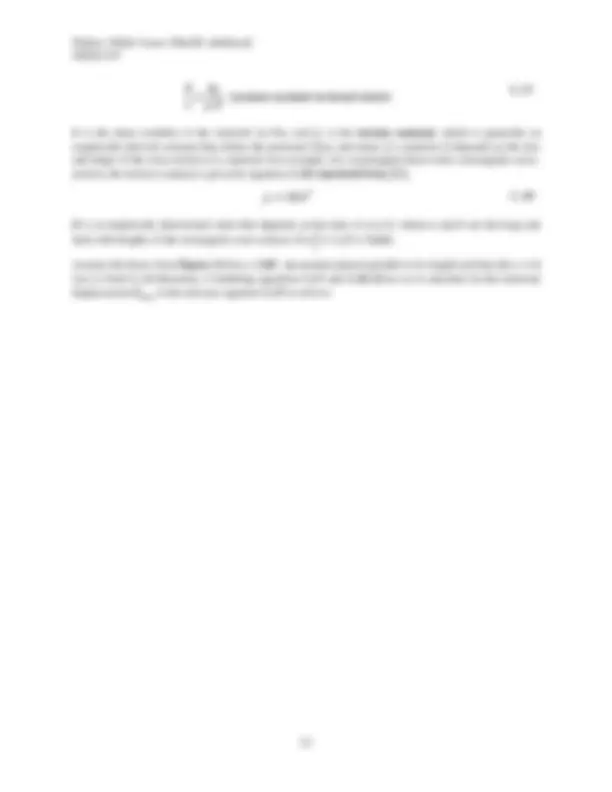
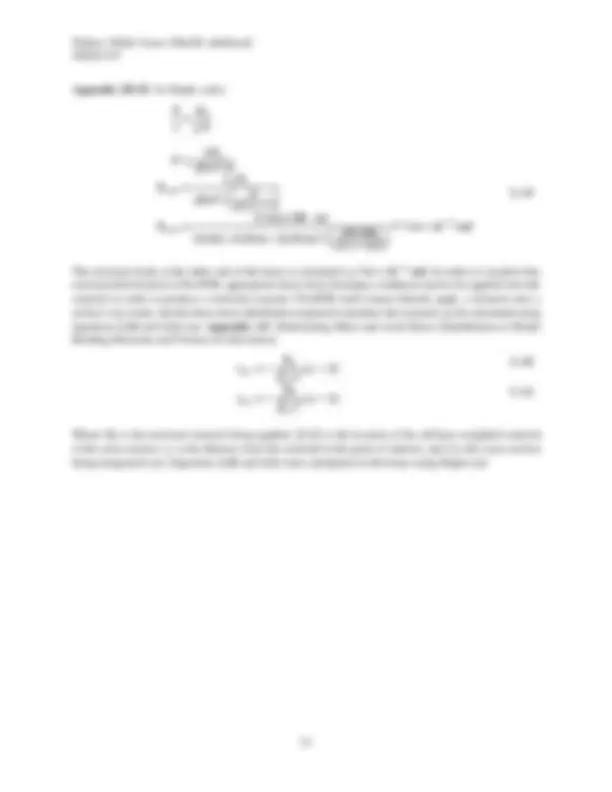
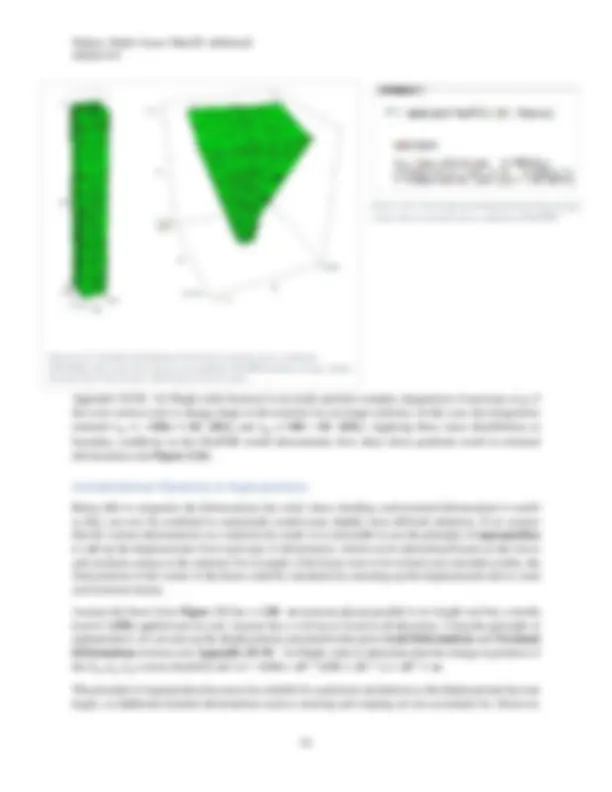
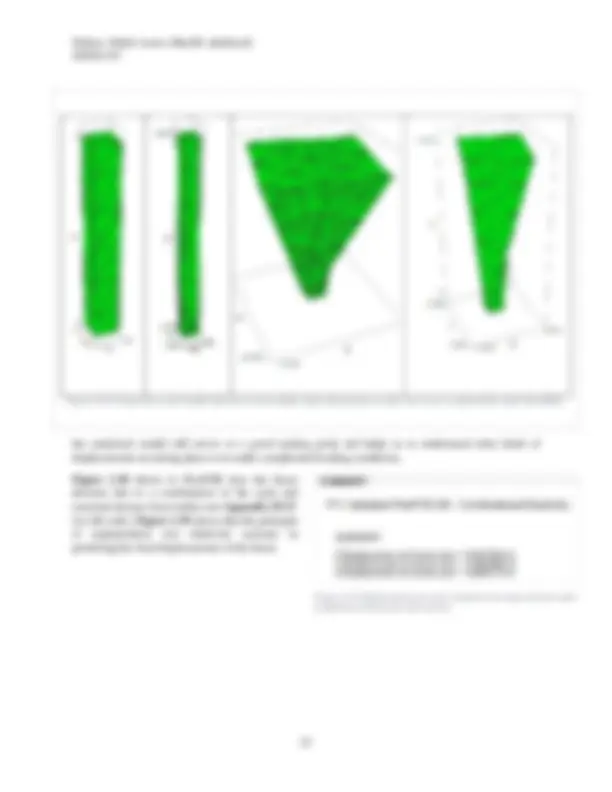
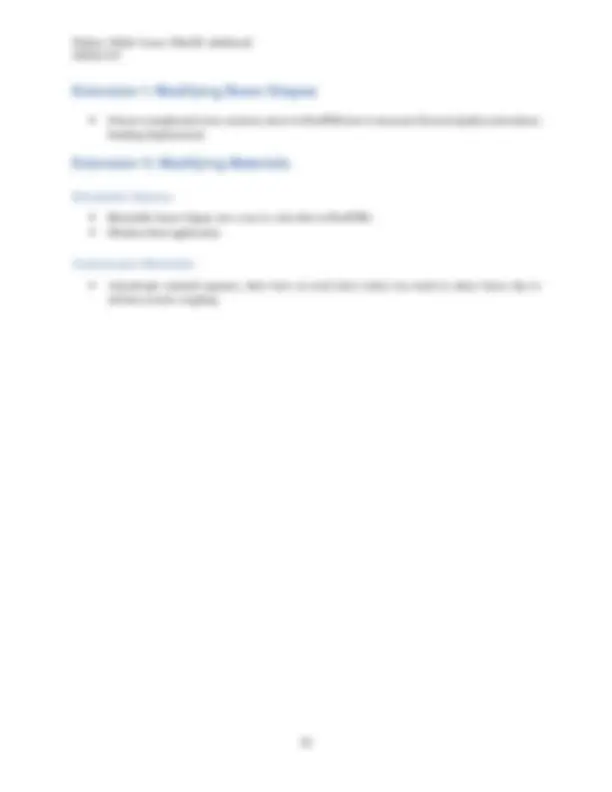

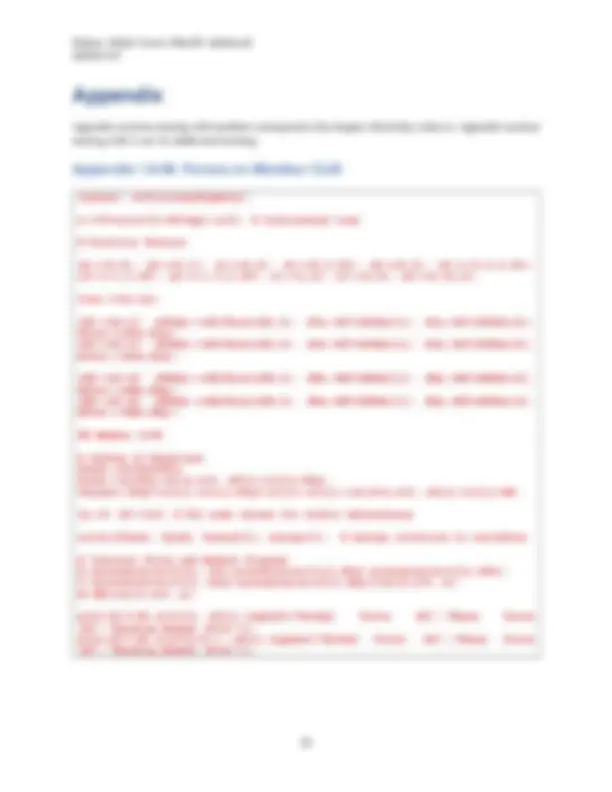
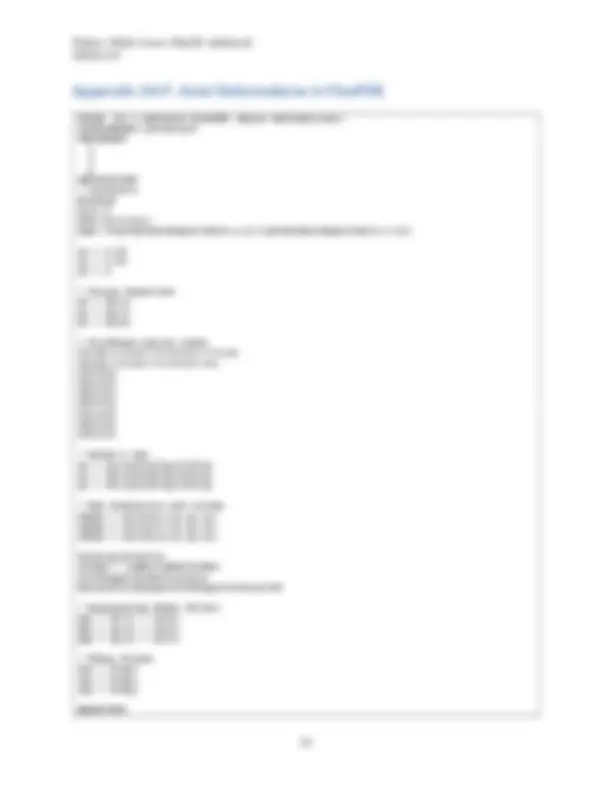
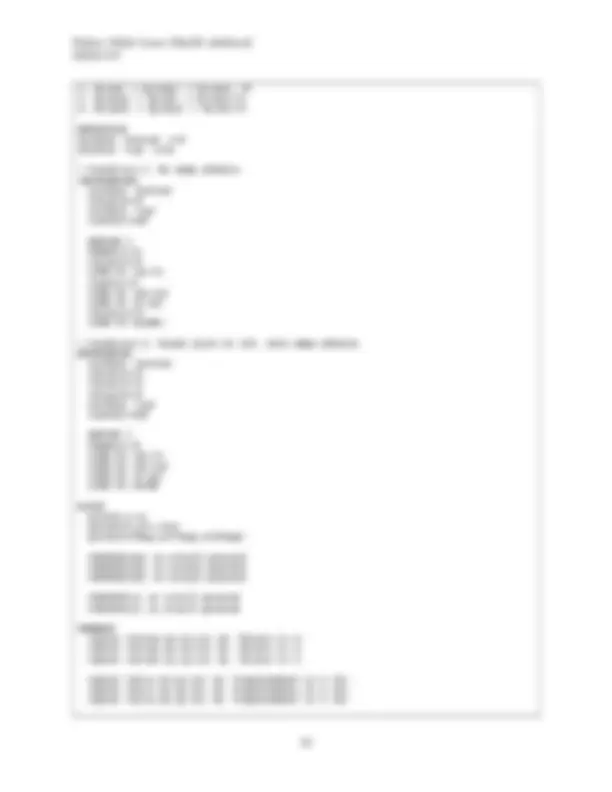
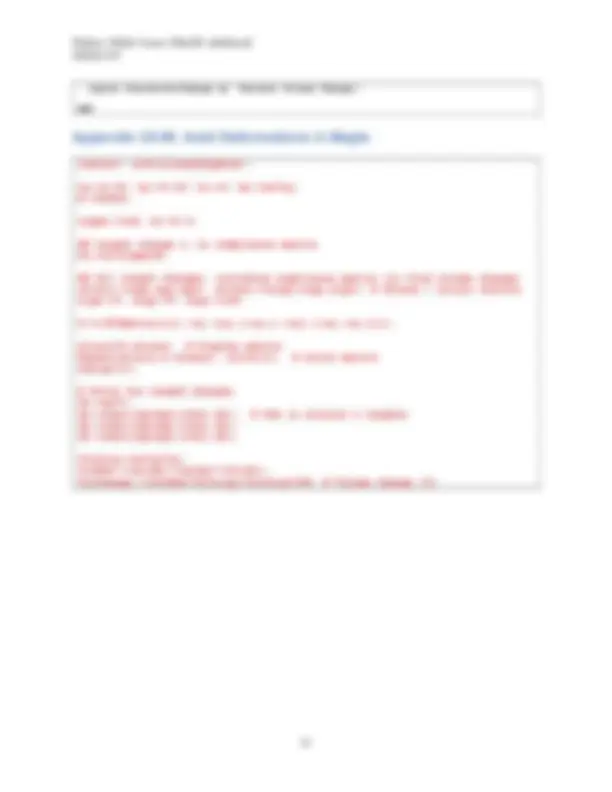
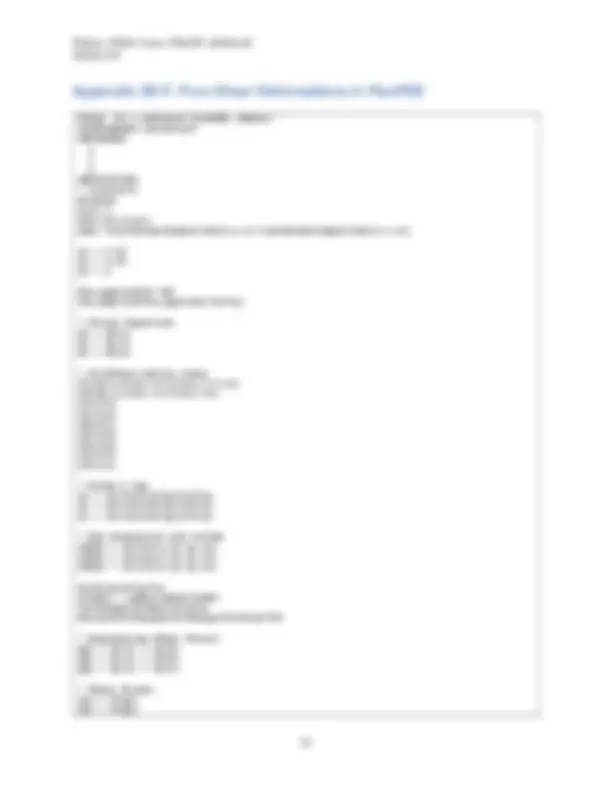
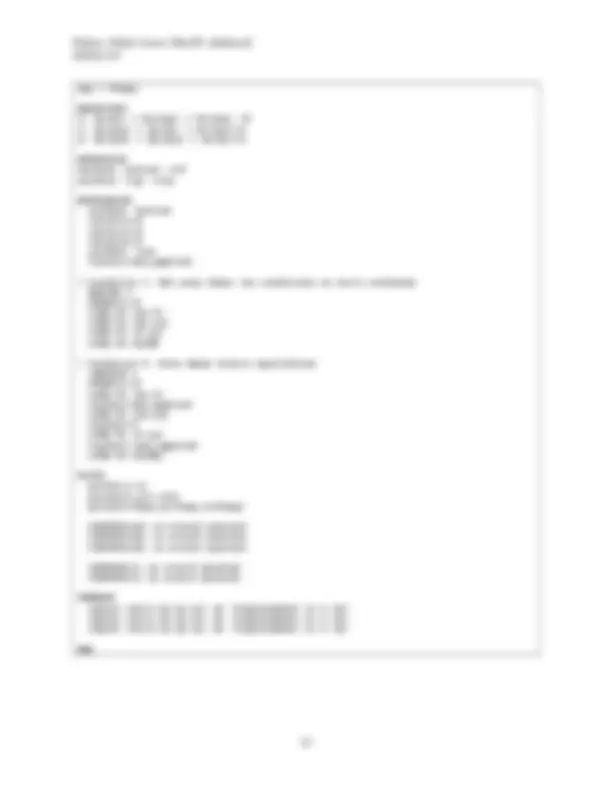
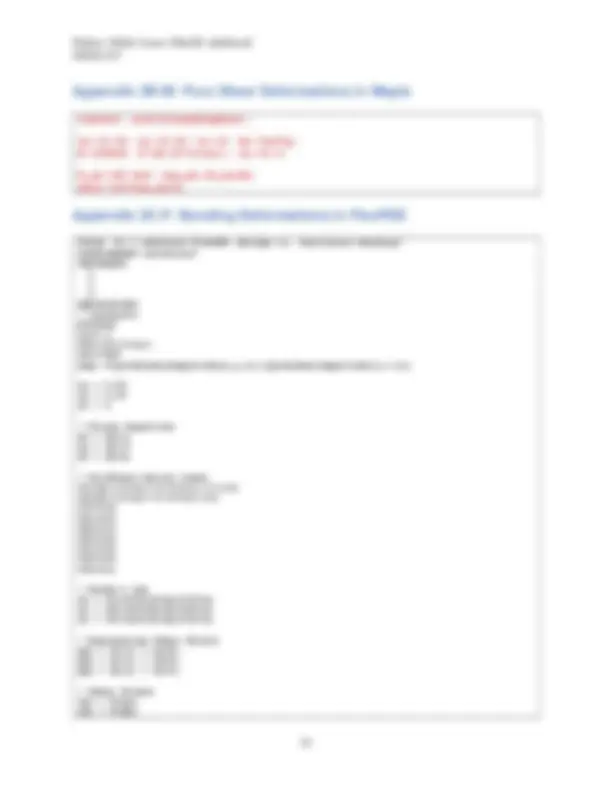
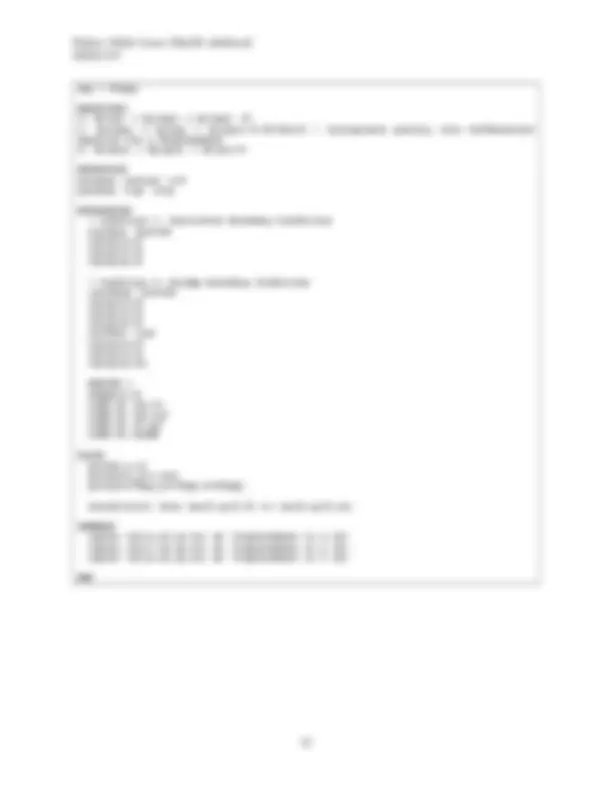
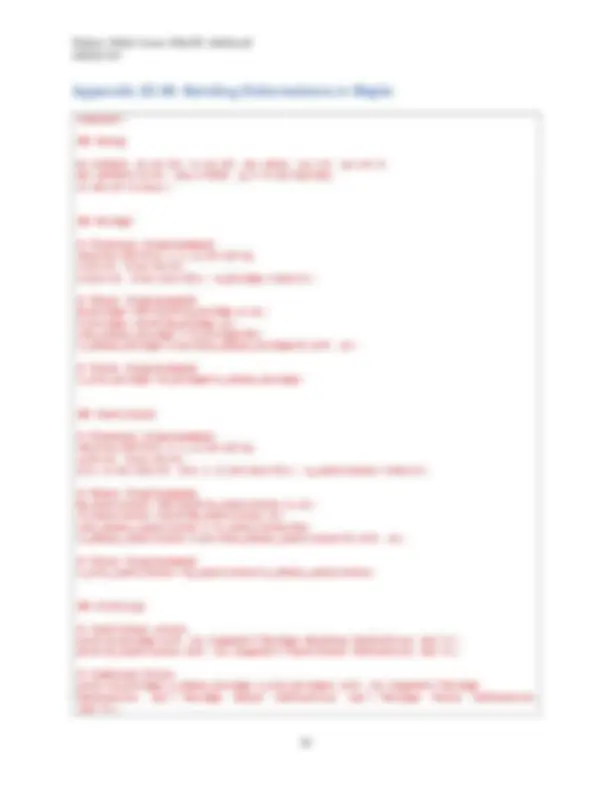
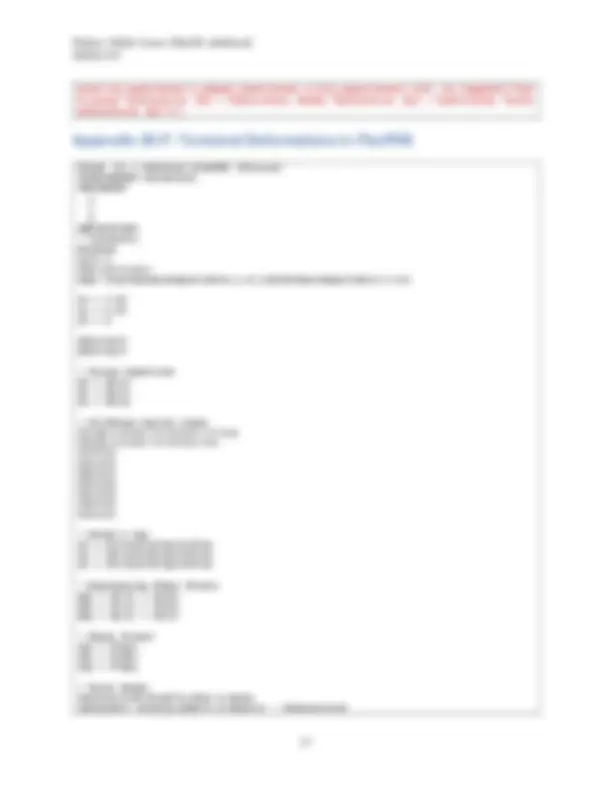
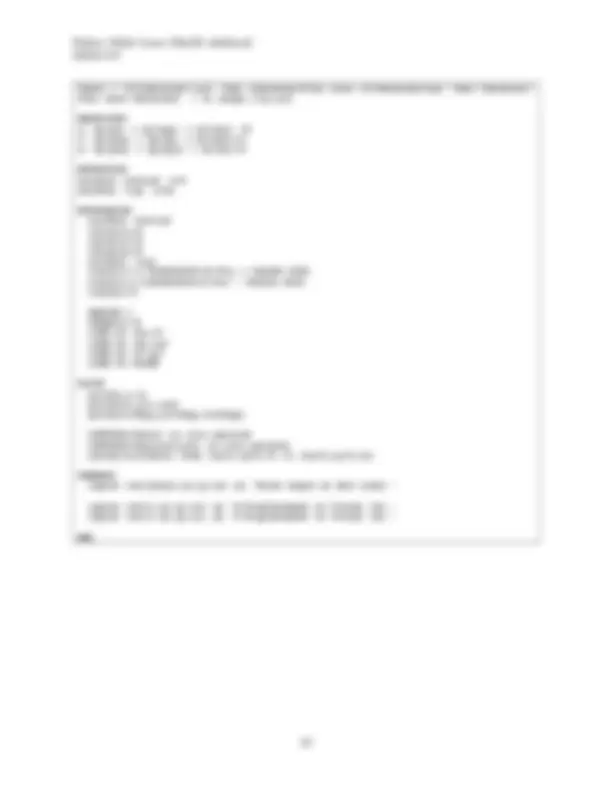
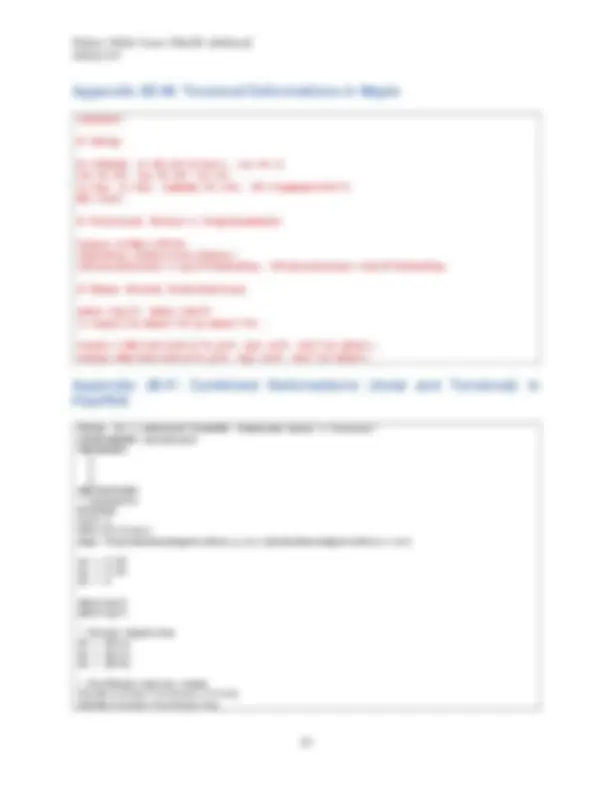
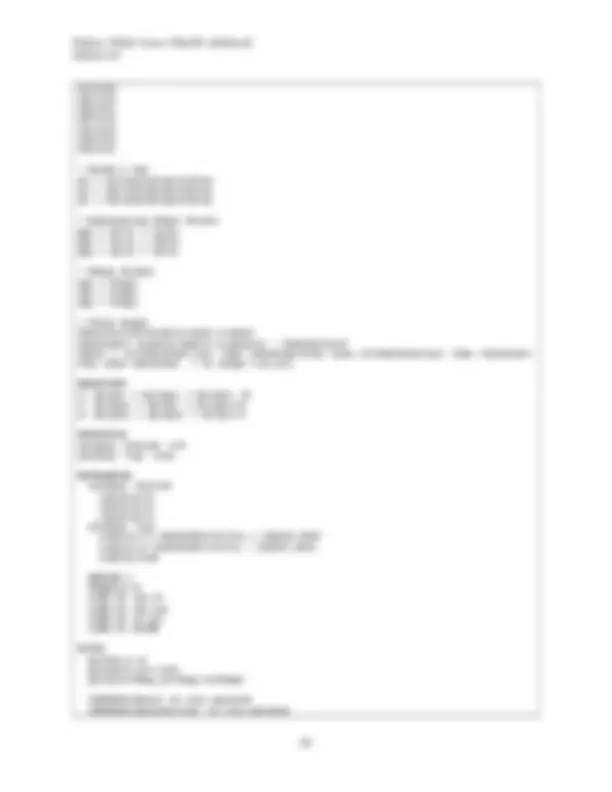
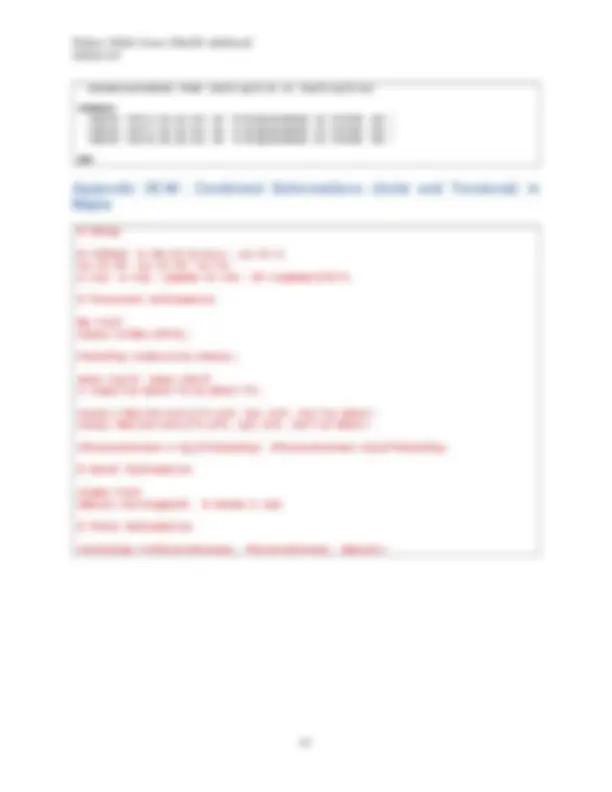
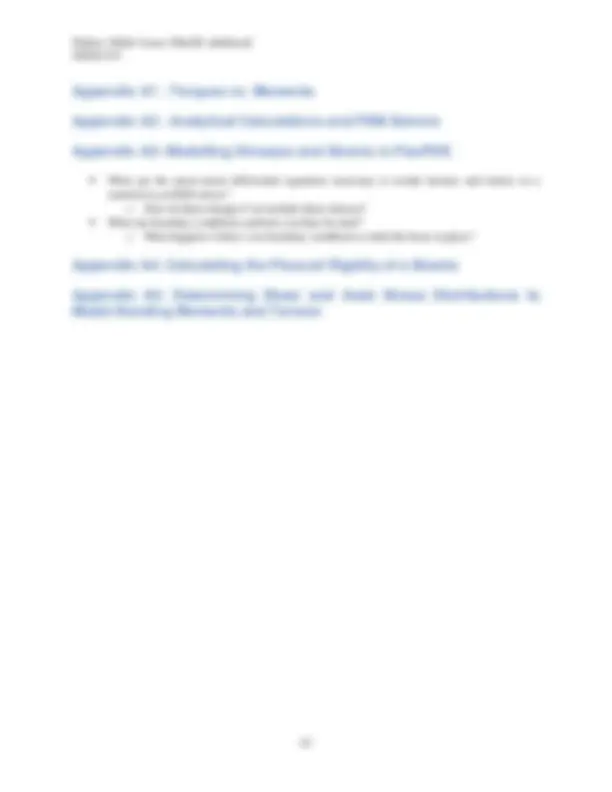
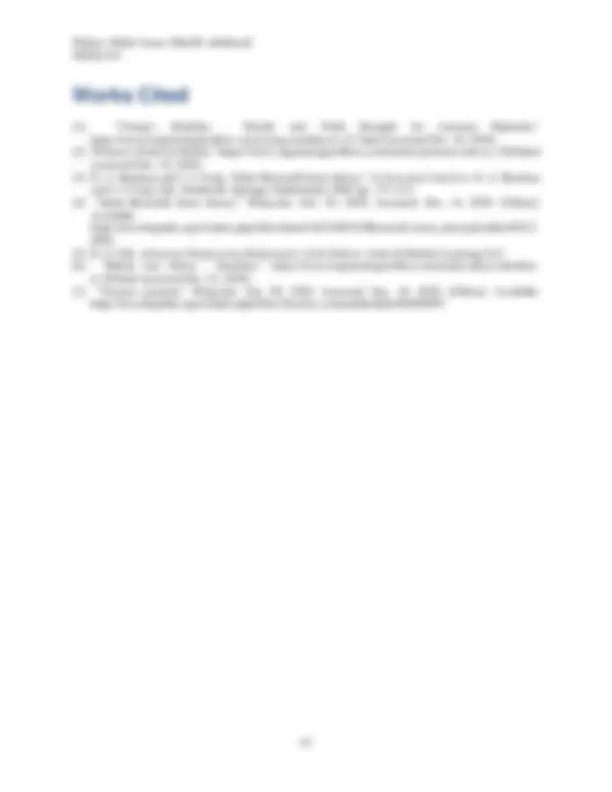
Study with the several resources on Docsity
Earn points by helping other students or get them with a premium plan
Prepare for your exams
Study with the several resources on Docsity
Earn points to download
Earn points by helping other students or get them with a premium plan
Community
Ask the community for help and clear up your study doubts
Discover the best universities in your country according to Docsity users
Free resources
Download our free guides on studying techniques, anxiety management strategies, and thesis advice from Docsity tutors
Introduction to computational mechanics
Typology: Study Guides, Projects, Research
1 / 44
This page cannot be seen from the preview
Don't miss anything!
by Dabeer Abdul-Azeez (MacID: abdulazd)
To whom this may concern,
My plan is to work on this portfolio over the break, but Dr. Minnick has allowed for me to submit parts of it that are done well for the final submission. If you see jot notes, feel free to look at them, but they are only rough ideas for the extensions that I plan to do for this document. For this submission, I have fully gone through parts of Chapter 1 and Chapter 2, which analyze forces within structures as well as various beam deformations.
Regards,
Dabeer Abdul-Azeez
Static equilibrium implies that an object has no net force or torques acting on it and that it has no velocity. In other words, it is completely still and is not accelerating. For member CIJK, the external distributed load 𝑤𝑤(𝑥𝑥) is already specified, but we also need to determine what forces and torques internal to the structure are acting on it. We can note that these will arise from joint C , the support member BI , and cable EJ. Including these forces onto Figure 1.2 will give us a free body diagram (FBD) for member CIJK (see Figure 1.3 ).
How was it determined what forces arose from where and what directions they would be in? That is a question that depends on the types of joints being analyzed. Looking at member CIJK specifically, we can analyze the rationale for the types of forces from points C , I , and J respectively.
Point C represents a fixed joint, which in real life might indicate that member CIJK was bolted onto member ABCDE. A fixed joint does not allow translational or rotational movement about that joint in any direction, so it will provide resistive forces and torques that will help to counteract whatever forces and torques the beam itself is experiencing (i.e. if you were to stand on the end of a beam that was fixed into a wall, the beam would provide appropriate resistive forces and torques to maintain itself in static equilibrium). The notation 𝑀𝑀𝐶𝐶 represents a moment about point C, and according to the right hand rule indicates a moment pointing in the + z direction. While joint C is a fixed joint, there are many other types of joints which have different ranges of motion , or directions in which they can move translationally or rotationally (e.g. hinge joints like the one in your elbow or a ball and socket joint like the one found in your hip allow for different kinds of motion). The cable joint at J can only resist translational motion in the direction which extends the cable (hence why force EJ was drawn the way it was). The cable cannot prevent translational or rotational motion in any other direction.
There is also member BI which is connected to CIJK by a pin joint. Something to note, though, is that the force generated by member BI on member CIJK through joint I must point in the direction of BI , similar to how the cable’s force can only point in the direction of the cable. In this way, the member BI is like the cable, except that it can also provide resistance in compression as opposed to only tension. Where did the assumption come from that the force must be in line with the member itself? If we take a look back at Figure 1.1 , we can note that member BI is connected to the structure by two pin joints. Each of these pin joints can only provide a resistive force in the xy plane (they cannot resist rotation in this plane), so member
A moment is a form of torque (i.e. a “rotational force”) See Appendix A for more.
Figure 1.3: Free body diagram (FBD) of member CIJK
Figure 1.4: A beam bolted into the ground represents a fixed joint. Image: English StackExchange
BI is a two-force member, with one force arising from each pin joint. We can draw an FBD for it (see Figure 1.5 ).
The force vectors in Figure 1.5 were drawn in arbitrary directions, but this cannot be the case; in order for the member BI to be in static equilibrium, the net forces and moments must both be zero. In order for the net forces to be zero, the vectors would have to point opposite to each other and have the same magnitude (see Figure 1.6 ). However, Figure 1.6 still cannot be the case because the forces would cause a net rotation of the beam. Therefore, the only solution must be that the forces are both in opposite directions, of the same magnitude, and collinear , giving us Figure 1..
Now that we have analyzed the forces acting on CIJK, we can solve for their magnitudes by setting up a system of equations to indicate that the beam must have no net forces or moments in order for it to be in static equilibrium. Referring back to Figure 1.3 , we can state that the net force ∑𝐅𝐅 and net moment ∑𝐌𝐌 acting on the beam is zero.
(𝒙𝒙𝑲𝑲)
𝒙𝒙 (^) 𝑪𝑪
The net force applied onto the beam by the downwards-pointing distributed load 𝑤𝑤(𝑥𝑥) is represented here as an integral over the length of the beam multiplied by −𝑦𝑦�. Note that the forces from the cable (EJ) and the two-force member (BI) can be specified in vector notation as having a certain magnitude and a direction vector which points along their length. In this way, these force vectors are more specified than, for example, the arbitrary force 𝐶𝐶. This becomes useful in determining whether the system of equations describing the structure is solvable or not.
𝒙𝒙𝑲𝑲
𝒙𝒙 (^) 𝑪𝑪 The moment was calculated here around point C. The 𝑟𝑟 vectors represent position vectors, which extend from the origin towards the point of interest. Here, the distributed load must be integrated to determine its effect on the moment, as it gains a longer moment arm the further along the beam it is acting.
Equations 1.1 and 1.2 represent a vector analysis of all the forces and moments acting on the system. The net force and moment equations can be simplified and split using vector components instead.
Figure 1.5: FBD for member BI (inaccurate because forces at B and I in arbitrary directions).
Figure 1.6: FBD for member BI (net force is zero, but inaccurate because coupled forces generate a moment)
Figure 1.7: FBD for member BI (accurate)
While this analysis did require significant understanding of forces, moments, ranges of motion, and static determinacy, note that the rest of the structure did not have to be considered at all. This is why the method of sections is powerful when analyzing large systems, such as large bridges with many interconnecting beams and joints.
Having analyzed the forces and moments acting on the beam, it can also be insightful to determine the forces and moments acting within the beam. If we cut the beam at some point perpendicular to its length, we can consider the internal normal force , shear force , and bending moment at that point (see Figure 1.10 ).
The internal normal force is normal to the cross-sectional surface and prevents the beam from extending or compressing in the normal direction; the internal shear force acts parallel to the cross-sectional surface and prevents the beam from shearing apart in that direction; and the internal bending moment prevents the beam from bending. These are clear examples of Newton’s third-law action-reaction pairs of forces, as whatever force or moment is exerted by one side of the beam must be counteracted by the other half in order for the beam to remain stable.
The magnitudes of these internal forces are a consequence of the various external forces and the other internal forces felt at the various joints. In fact, they can be calculated and represented as piecewise functions which vary along the length of the beam (see Figure 1.11 and Figure 1.12 ).
Figure 1.9: A bridge with many interconnecting beams and joints. Image: Charlie Foster on Unsplash
Figure 1.10: Dissection of beam CIJK to show internal shear (V) force, normal force (N), and bending moment (M)
Figure 1. 11 : Internal normal force, shear force, and bending moment diagram for member CIJK (Maple). Note the curviness in the graphs comes from the distributed load.
Figure 1.12: Internal normal force, shear force, and bending moment diagram for member CIJK, no distributed load (Maple)
Figure 1.11 shows how the last section of the beam for 𝑥𝑥 > 𝑥𝑥𝐸𝐸 experiences barely any internal forces or moments, which makes sense since that length of the beam is not being supported at all (i.e. it is freely hanging), so it cannot contribute much towards maintaining the beam in static equilibrium. The only force which that section of the beam is helping to support is the distributed load. If we remove the distribute load, the corresponding internal force and moment diagram has only straight curves (see Figure 1.12 ), and all internal forces and moments become zero for 𝑥𝑥 > 𝑥𝑥𝐸𝐸.
By being able to analyze structures as a whole and in parts, engineers are able to better design structures to more effectively be able to distribute loads…
( 4 m)( 1 MPa) 200 GPa
= 20 μm
However, this is not the full picture; when an object is extended in one direction, it will typically compress and “thin out” in the directions perpendicular to its extension (see Figure 2.2 ). This is the idea of Poisson’s ratio coupling. Poisson’s ratios (𝜈𝜈) have been tabulated for various materials, and they typically range from 0 to 0.5, where a value close to 0 indicates that the material does not deform axially in the other directions when it is deformed in one direction (e.g. a cork), while a higher Poisson’s ratio indicates significant thinning out due to axial loads (e.g. Playdough). Mathematically, the Poisson’s ratio can be represented via a compliance matrix (see Equations 2.5 & 2.6)
𝐸𝐸 = 𝑆𝑆𝜎𝜎 2. 5
�
Where 𝑆𝑆 is the compliance matrix (in Pa−1) that denotes how compliant a material is to strains as a result of stresses. Materials with different material properties in different directions (also known as anisotropic materials) have different compliance matrices, as will be seen later.
By the rules of matrix multiplication, the compliance matrix indicates that positive axial stresses in a certain direction will lead to negative axial strains in the directions perpendicular to it.
The Poisson’s ratio for steel ranges around 0.3 [2]. Factoring this in, we can determine the length changes for the material in all dimensions, and thus determine the change in volume of the material as well. This was done in Maple (see Figure 2.3 , refer to Appendix 2A-M : for full code) because in addition to the linear algebra capabilities demonstrated in Chapter 1, Maple also supports matrix algebra.
Maple returned Δ𝑥𝑥 = −0.375 μm, Δ𝑦𝑦 = −0.375 μm, and Δ𝑧𝑧 = 20 μm (like before in Equation 2.4). The Poisson’s ratio coupling does not affect the amount of strain in the direction of stress application, but it incorporates the other lengths of the material to give a more holistic view of the deformation. The volume change was 0.0002 %, indicating that the Poisson’s ratio coupling did not entirely prevent the volume from changing.
The Poisson’s ratio ( 𝝂𝝂 ) for an isotropic material relates axial deformations in one direction to opposite axial deformations in other
Poisson’s ratios can be negative. Consider a folding chair! Pulling on it in one direction will actually cause it to expand in the other directions.
Figure 2.2: Stretching out play-dough in one direction causes it to thin out in the other directions. This is an example of Poisson's ratio coupling. Image: Scientific American.
Trying to visualize this axial deformation using an analytical model would require some specific calculations, and it would become practically impossible once more complicated scenarios were encountered (such as complex boundary conditions, as will be shown later). As such, finite element method (FEM) solvers can be used instead to provide a quick, accurate solution to a set of stresses and boundary conditions acting on a material. Using FlexPDE (an FEM solver), the beam in Figure 2.1 can be set up. Equations 2.7 to 2.9 show a set of differential equations which relate the axial stress (𝜎𝜎) and axial strain (𝐸𝐸) as well as the shear stresses (𝜏𝜏) and shear strains (𝛾𝛾) (discussed later). These were inputted into FlexPDE to implement some laws of physics into the simulation.
For this example, the beam was fixed in z on the 𝑧𝑧 = 0 surface and had a 1 MPa placed on the 𝑧𝑧 = 𝐿𝐿 (^) 𝑧𝑧 surface. The beam was also fixed in y on the 𝑦𝑦 = 0 surface and fixed in x on the 𝑥𝑥 = 0 surface. These boundary conditions made sure that the FEM solver had a point of reference with respect to which it could calculate the deformations of the beam (otherwise, the beam could end up travelling or rotating through space, making it difficult to measure the displacements). Running the simulation returned similar numerical outputs to the Maple calculations (see Figure 2.5 ) while also producing a visualization of the deformations on a mesh structure (see Figure 2.4 ) which demonstrate elasticity and Poisson’s ratio coupling (see Appendix 2A-F : for full code).
Equations 2. 7 to 2. 9 essentially state that there should be no net force acting on any differential volume within a material in static equilibrium. This includes both shear forces (discussed later) and axial forces for accuracy. Their derivation and more information on FEM modelling can be found in Appendix A3.
strain:=<epx,epy,epz>: stress:=<sigx,sigy,sigz>: # Stress / strain vectors sigx:=0: sigy:=0: sigz:=1e6:
S:=1/EMatrix([[1,-nu,-nu],[-nu,1,-nu],[-nu,-nu,1]]):*
strain=S.stress; # Display matrix Equate(strain,S.stress): solve(%); # Solve matrix assign(%);
# Solve for length changes dL:=epL: dx:=subs([ep=epx,L=Lx],dL); # Sub in strains & lengths dy:=subs([ep=epy,L=Ly],dL); dz:=subs([ep=epz,L=Lz],dL);*
VolOrig:=LxLyLz: VolNew:=(Lx+dx)(Ly+dy)(Lz+dz): VolChange:=(VolNew-VolOrig)/VolOrig100; # Volume change (%)*
Figure 2.3: Maple code to determine volume change due to axial stress.
Though the effect of the new boundary condition on the displacements of the beam is miniscule because the applied load was relatively small compared to the stiffness of the material, Figure 2.6 shows that there is a decrease in the net displacement in all dimensions. This is a consequence of the more restrictive “fixed joint” boundary condition applied against the axial tensile load. Additionally, Figure 2.6 shows some necking of the material visible near the 𝑧𝑧 = 0 surface which contributed towards the lower x and y displacements (allowing them to move further inwards). The simulation’s grid density (i.e. its precision) had to be increased in order to return meaningful results, indicating how complicated a different set of boundary conditions can be and how FEM solvers can help to resolve the issue.
Shear deformations occur when two equal, antiparallel forces are applied tangentially to opposite faces of an object (see Figure 2.8 ). They represent planes of atoms sliding over each other.
For isotropic materials, shear stress (𝜏𝜏, in Pa) and strain (𝛾𝛾) are related by a similar Hooke’s law as axial stress and strain: 𝜏𝜏 = 𝐺𝐺𝛾𝛾, where 𝐺𝐺 (in Pa) is the shear modulus of a material. For an isotropic material, it
turns out that 𝐺𝐺 = (^2) (1+2𝜈𝜈𝐸𝐸 ).
Shear stress is applied on a surface in a particular direction and is usually represented with two subscripts denoting such. For example, 𝜏𝜏𝑥𝑥𝑧𝑧 represents a shear force on the x surface in the z direction. Shear strain (𝛾𝛾) is defined as the ratio of the deformation in the direction of the applied shear force to the length of the material in the direction transverse to the force’s application (i.e. the first subscript of the shear stress). This is outlined in Figure 2..
Figure 2.8: Shear deformations are caused by antiparallel forces of equal magnitude applied tangentially to opposite surfaces of a material. Pure shear deformations have a consistent shear strain, 𝛾𝛾. Impure shear deformations can cause some bending in the material.
In reality, shear forces are usually accompanied by bending as well, such as when gravity deforms a cantilever beam (see Figure 2.9 ). In these cases, analytical calculations including only shear forces will be less accurate, as there will be non-uniform stress and strain distributions through the material. However, if we have a specific loading of shear stresses, we can achieve pure shear (refer back to Figure 2.8 ), in which there are no bending deformations and there is no deformation in the plane transverse to the applied shear forces. This simplifies analytical calculations as 𝛾𝛾 is now constant throughout the object. This is also important to consider when we are modelling our material in an FEM solver, as without the proper boundary conditions, the material will not be in pure shear, and some bending will arise. Using the shear stress elasticity equation, we can determine the amount of shear strain (𝛾𝛾𝑧𝑧𝑥𝑥) produced on the beam from earlier due to a 𝐹𝐹𝑧𝑧𝑥𝑥 = 62.5 kN force (acting in the x direction) distributed evenly on the 𝑧𝑧 = 𝐿𝐿𝑧𝑧 face (see equations 2.10 to 2.13 or refer to Appendix 2B-M : for Maple code).
𝜏𝜏𝑧𝑧𝑥𝑥 = 𝐺𝐺𝛾𝛾𝑧𝑧𝑥𝑥 2. 10 𝐹𝐹𝑧𝑧𝑥𝑥 𝐴𝐴𝑧𝑧
2 � 1 + ( 0. 3 )�( 62. 5 kN)( 2 m) ( 200 GPa)( 0. 25 m)^2 = 2. 6 × 10 −^5 m
We can model this in FlexPDE as well (see Figure 2.11, refer to
Figure 2.9: A cantilever beam (a beam that is fixed on one end) bends under shear stress). Source: University of Cambridge
As seen already, beams can undergo bending deformations under applied shear stresses. These bending deformations can be analyzed as a result of applied bending moments by using Euler-Bernoulli beam theory [3]. Like other beam theories, Euler-Bernoulli theory relates the deflection (i.e. deformation due to bending) of a beam to the bending moments and boundary conditions it is placed under. The Euler-Bernoulli theory is particularly ubiquitous in fields of engineering. It assumes that the cross-section of a beam under bending will remain perpendicular to the axis of bending (see Figure 2.10).
By performing balances on the internal shear forces and bending moments within the beam, the Euler- Bernoulli beam equation (EBBE, see equation 2.14) can be derived [4].
𝑑𝑑^2 𝑑𝑑𝑥𝑥^2
𝑤𝑤(𝑥𝑥) = 𝑞𝑞 (for constant EI along 𝑥𝑥)
Figure 2.10: Euler-Bernoulli beam theory assumes that the cross-sections of a beam remain perpendicular to its neutral axis when bending. Source: adapted from Wikimedia Commons.
Figure 2. 11 : Comparison of finite element mesh before deformations (left), after shear stress with impure shear conditions (middle), and after shear stress applied with pure shear csonditions (right), with applied force 𝐹𝐹𝑧𝑧𝑥𝑥 =
Where 𝐸𝐸 (in Pa) is the elastic modulus of the material, 𝑞𝑞 (in N/m) is a distributed load), 𝑤𝑤 (in m) is the deflection of the beam in the z direction at any point x as seen in Figure 2.10 , and 𝐵𝐵 (in N ⋅ m^2 ) is the second moment of area , which represents the distance of the material distribution of the cross-section of the beam with respect to its stiffness-weighted centroid. The term 𝐸𝐸𝐵𝐵 is often referred to as the flexural rigidity of the beam and represents the resistance of the beam to flexural deformations. A higher flexural rigidity can be caused by materials with high stiffness or cross-sections where the material is distributed far from the stiffness-weighted centroid (and vice versa for low flexural rigidity). Often, the cross-section of a beam is constant throughout its length, so the flexural rigidity is as well, and it can be pulled out of the derivative in equation 2.14 to yield equation 2.15. For a rectangular beam of a single material with
stiffness 𝐸𝐸, the flexural rigidity can be calculated as 𝐸𝐸𝐵𝐵 = 𝐸𝐸𝐵𝐵ℎ^
3 12 (see^ Appendix A4 : Calculating the Flexural Rigidity of a Beams for derivation).
In order to acquire a specific solution to the EBBE, enough boundary conditions are required. For the EBBE, the various derivatives of 𝑤𝑤(𝑥𝑥) have physical meaning (see Table 1, adapted from [5]), so boundary conditions can be related to applied shear forces and bending moments, displacements, and slopes of displacements.
Bending deformation profiles can be solved for various boundary conditions to analyze how a beam would bend when it is fixed using different
joints. Let us assume we are using the same beam from Figure 2.1 and that it has a density of 𝜌𝜌 = 7850 (^) mkg 3 ,
which is typical for steel [6]. In that case, the distributed load acting throughout the solid steel beam would be 𝑞𝑞 = 𝑔𝑔𝜌𝜌𝐴𝐴𝑧𝑧, where 𝑔𝑔 is the acceleration due to gravity, and 𝐴𝐴𝑧𝑧 is the cross-section of the beam in z. From this, there is enough information to model equation 2.15. Figure 2.13 compares the analytically derived deflection profiles of a beam (see Appendix 2C-M : for full code) under the influence of gravity under a bridge boundary condition (i.e. fixed joints on either end) versus a cantilever one (fixed joint on one end, other end is free). To be more accurate, shear deformations were included and compared to the pure bending deformations, as both would be present if the beam were affected by gravity. In the case of the bridge boundary condition, the shear deformation was relatively noticeable.
These beams can also be modelled using FlexPDE (see Figure 2.12 or refer to Appendix 2C-F : for full code) to verify the results from the analytical calculations, with the appropriate boundary conditions set on the mesh surfaces instead of implemented directly into a differential equation.
The Euler-Bernoulli equation does not have to be used for displacements in 𝑧𝑧, but 𝑤𝑤 is generally the variable used to denote z displacements, while u and v respectively would be used for x and y displacements.
The flexural rigidity of a beam requires multiple steps to calculate for beams multiple materials and complicated cross-sections. See Appendix A
Function / Derivative Meaning 𝑤𝑤(𝑥𝑥) Displacement 𝑤𝑤′(𝑥𝑥) Slope of displacement 𝐸𝐸𝐵𝐵𝑤𝑤′′(𝑥𝑥) Bending moment ( M ) 𝐸𝐸𝐵𝐵𝑤𝑤′′′(𝑥𝑥) = 𝑀𝑀′(𝑥𝑥) Shear force ( V ) Table 1: Physical meanings of derivatives of the deflection of the beams. Adapted from [5]