
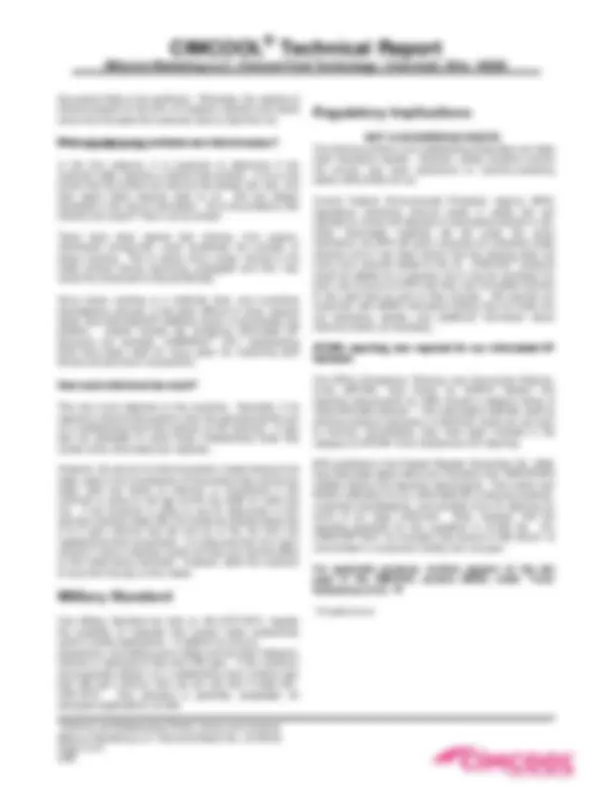
Study with the several resources on Docsity
Earn points by helping other students or get them with a premium plan
Prepare for your exams
Study with the several resources on Docsity
Earn points to download
Earn points by helping other students or get them with a premium plan
Community
Ask the community for help and clear up your study doubts
Discover the best universities in your country according to Docsity users
Free resources
Download our free guides on studying techniques, anxiety management strategies, and thesis advice from Docsity tutors
The sources of chlorine in metalworking fluids, its implications, especially in the aerospace industry, and regulatory compliance. Chlorine can occur in metalworking fluids as chlorinated olefins, a component of raw materials, or as chlorides from water. The potential problems caused by chlorine, including stress cracking, and regulatory implications such as military standard mil-std-767c and epcra reporting.
Typology: Schemes and Mind Maps
1 / 2
This page cannot be seen from the preview
Don't miss anything!
Where chlorine comes from, what form it can take and its implications, especially in the aerospace industry:
Chlorine is an element belonging to the same group as fluorine, bromine and iodine. This group is called the halogens. Chlorine is the only member of this group currently of concern.
Chlorine can occur in a metalworking fluid mix in one of three ways:
“Chlorine and Metalworking Fluids: Issues and Answers”
are natural impurities the water picks up while filtering through rocks on its way to the reservoir. Typically, city water will contain about 50 ppm chloride.
Since city water is used to manufacture semi-synthetic and synthetic metalworking fluids concentrates these products will contain some chloride ions from this source. However, since the customer will generally use city water containing at least 50 ppm chloride ions to make the mix the chloride content of the product becomes insignificant.
(It makes no difference if the customer uses softened water, chloride ions are not removed by the softening process, only calcium and magnesium ions are taken out. All ions, however, are removed if the customer is using deionized or RO (reverse osmosis) water.
How much chlorine?
A product containing a chlorinated EP lubricant will contain comparatively large amounts of chlorine, in the form of organic chloro- compounds. A typical figure (for a 5% mix) would be 0.25% chlorine (2500 ppm chlorine).
If the product contains a chlorine containing raw material (other than a chlorinated EP lubricant) then this might contribute 0.001% to 0.01% chlorine (10 to 100 ppm chlorine) to a 5% mix. A comparatively low level. If the chlorine is present as the chloride ion, simply as part of the water used in the manufacture of the metalworking fluid concentrate and as the water used to make the mix, then typical figures for chlorine content would be 0.002% to 0.005% (20 - 50 ppm chlorine).
If the customer is using deionized or RO water to make the mix then a concentrate that contained 50 ppm chlorine, would yield a mix containing only about 2 or 3 ppm chlorine (assuming a 5% mix was made). Thus, only if the product contains a chlorinated EP additive (chlorinated olefin), or other organic chloro-compound is the level of chlorine in
Milacron Marketing LLC Technical Report No. J/N 96/ Page 1 of 2 3/
CIMCOOL
® Technical Report
the product likely to be significant. Otherwise, the majority of chlorine present (in the form of inorganic chloride ions) would come from the water the customer uses to make the mix.
What manufacturing problems can chlorine cause?
In the first instance, it is important to determine if the customer really requires a chlorine free product. If he or she insists that the product be chlorine free please ask why, and then report these reasons back to us. We are always interested in this sort of information. As to the problems that chlorine can cause? That is not so simple:
There have been reports that chlorine, from organo- chlorinated compounds, could accelerate the process of stress cracking. This is where micro cracks, formed in the metal surface during machining, propagate and thus may cause the component to fail prematurely.
Since stress cracking is a relatively slow, and somewhat serendipitous process, it has been difficult to show, beyond doubt, that chlorinated EP additives cause, or accentuate, the problem. Indeed, soluble oils containing chlorinated EP lubricants (for example, CIMPERIAL ® 1011 metalworking fluid) have been used for many years for machining both ferrous and aluminum components.
How much chlorine is too much?
This very much depends on the customer. Generally, if he requires a chlorine free product, then this will preclude the use of a metalworking fluid that contains an EP lubricant. It may also be advisable to avoid those metalworking fluids that contain other chlorinated raw materials.
However, the amount of chlorine present, simply because the water used in the manufacture of the product was normal city water (with low levels of chlorine), is insignificant if the customer is going to use his normal city water to make the mix. If the customer is going to use DI (deionized) or RO (reverse osmosis) water then he should be advised about the 2 to 3 ppm chlorine that will end up in the mix from the metalworking fluid concentrate. It is assumed that 2 to 3 ppm chlorine in such a situation would not have any harmful effect on the metal being machined. However, allow the customer to have the final say on this matter.
Military Standard
One Military Standard we refer to, MIL-STD-767C, regards the suitability of materials that contact metal components used in nuclear applications. In addition to mercury, phosphorus, low-melting-point metals and the other halogens, chlorine is restricted to less than 250 ppm. If the maximum recommended dilution of a metalworking fluid contains less than 250 ppm chlorine, then we can say that it meets MIL- STD-767C. This standard is generally acceptable for aerospace applications, as well.
Regulatory Implications
The chlorine content in our metalworking fluids does not make them hazardous wastes. However, certain locations around the country may have restrictions on chlorine-containing waste, while others do not.
Current Federal Environmental Protection Agency (EPA) regulations restricting chlorine levels in waste oils are intended to control the disposal of chlorinated solvents in oils. Other chlorinated materials will fall under the same restrictions, but EPA will grant variances for individual waste streams once it has been shown that the chlorine does not come from solvents added to the oil. CIMCOOL®^ products would be eligible for a variance, but it may be necessary for each user to prove to EPA that they had not added solvents to the used fluid as part of their process. We provide our customers with MSDS information stating that our fluids are not hazardous wastes, and additional information about chlorine content, as necessary.
EPCRA reporting now required for our chlorinated EP lubricant.
The EPA's Emergency Planning and Community Right-to- Know (EPCRA-- also known as "SARA") Section 313 reporting requirements for 1995 include a category listing of "polychlorinated alkanes." The chlorinated materials used as extreme pressure lubricants in CIMCOOL fluids are non-toxic to humans, nevertheless, they have been included in the category for EPCRA Toxic Substances 313 reporting:
EPA published in the Federal Register (November 30, 1994) that chlorinated alpha olefins are included in the 1995 EPCRA (SARA) Section 313 reporting requirements. This means new MSDS notification for our chlorinated EP-containing products, unwanted recordkeeping, and possible Form R reporting for some of our large customers. Note, however, that the reporting threshold for this ingredient is 10,000 lbs. For CIMSTAR®^ 60LF, for example, that amount is 362 drums* of concentrate in a customer's facility over one year.
For applicable products, notation appears on the last page of the CIMCOOL product MSDS, under "Toxic Substances (313)."
“Chlorine and Metalworking Fluids: Issues and Answers” Milacron Marketing LLC Technical Report No. J/N 96/ Page 2 of 2 3/