
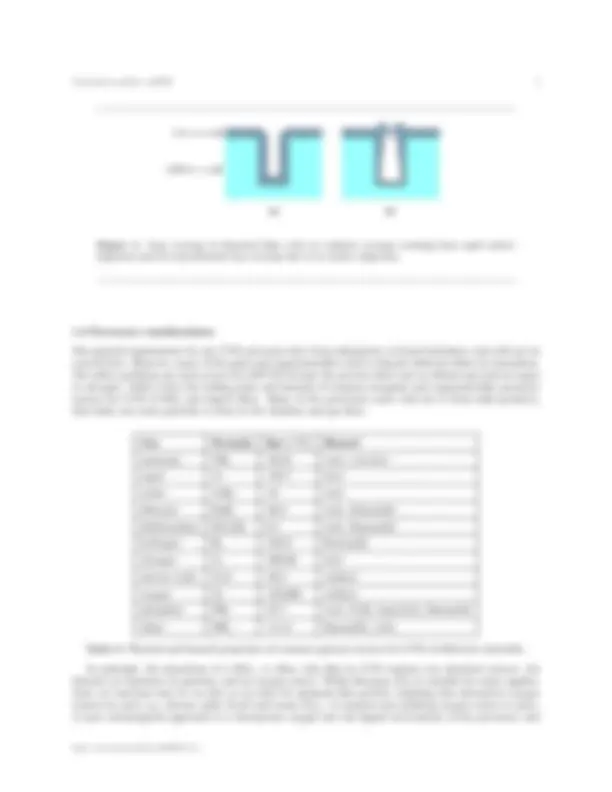
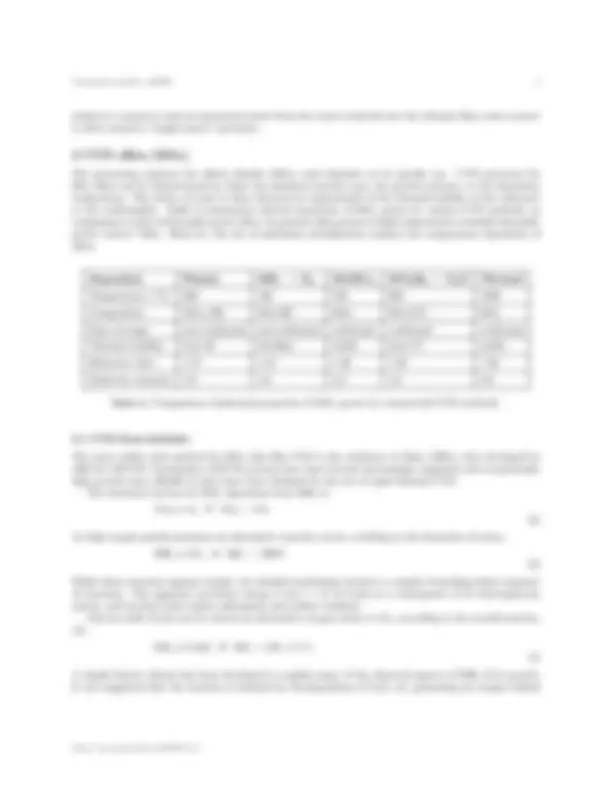
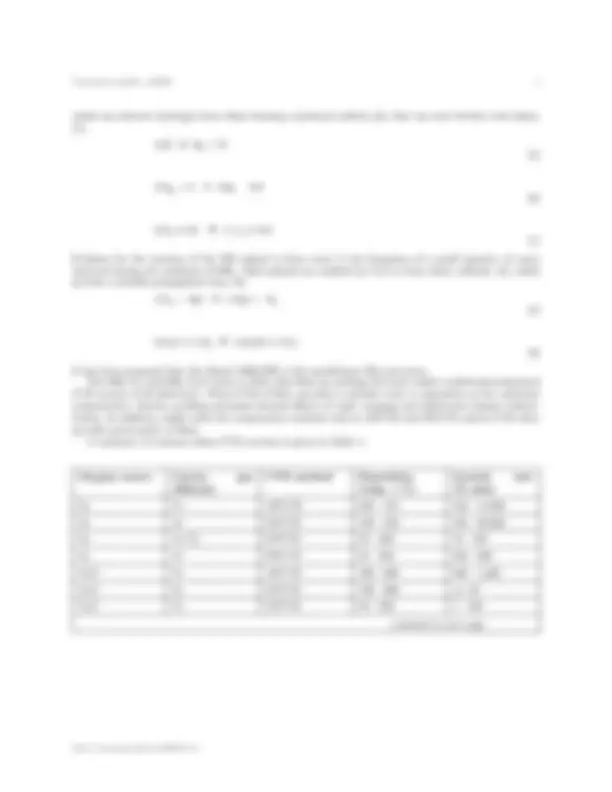
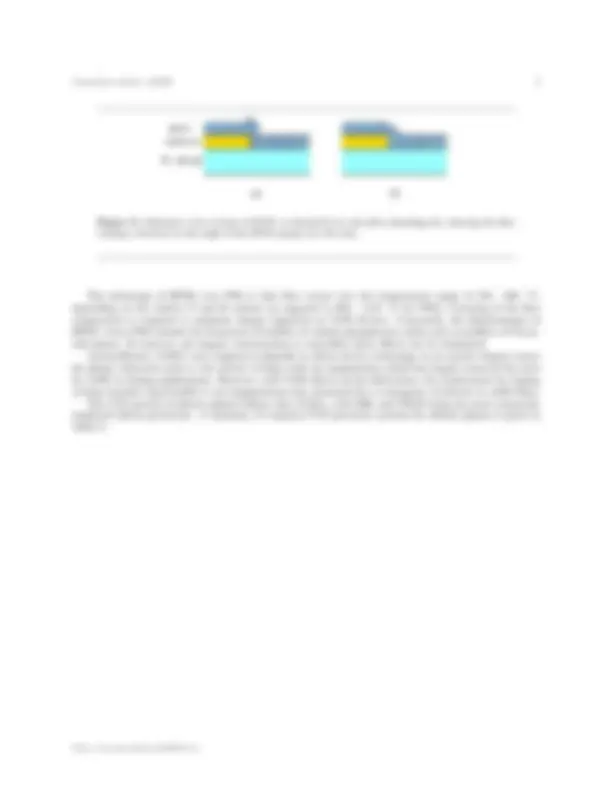
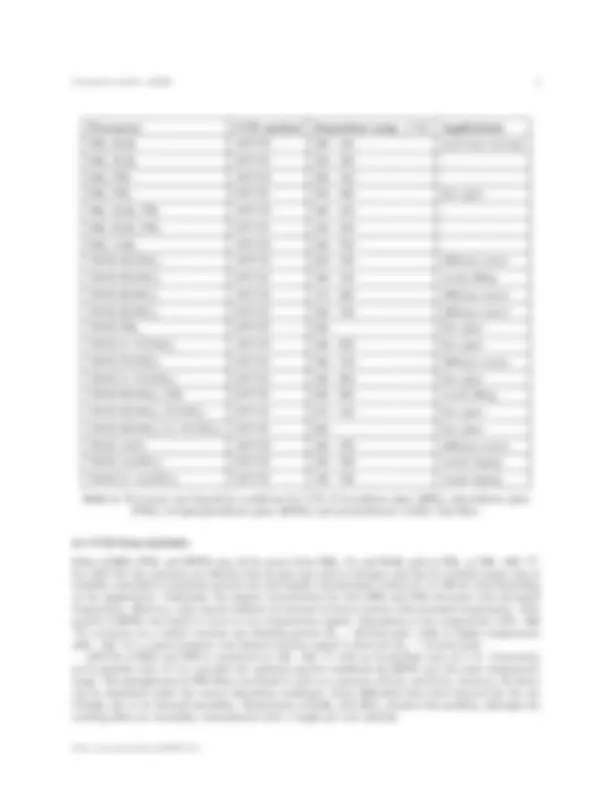
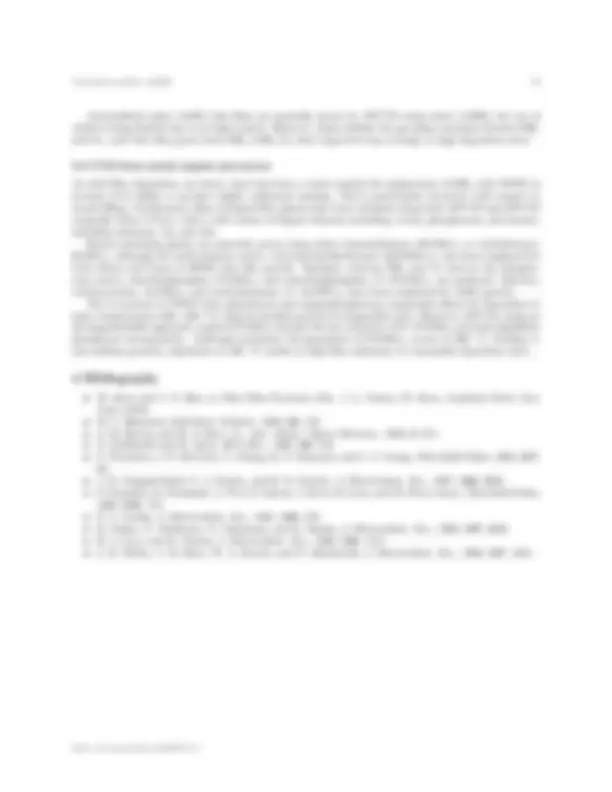
Study with the several resources on Docsity
Earn points by helping other students or get them with a premium plan
Prepare for your exams
Study with the several resources on Docsity
Earn points to download
Earn points by helping other students or get them with a premium plan
Community
Ask the community for help and clear up your study doubts
Discover the best universities in your country according to Docsity users
Free resources
Download our free guides on studying techniques, anxiety management strategies, and thesis advice from Docsity tutors
Study Material. Before describing individual chemical vapor deposition (CVD) systems for the deposition of silica thin lms, it is worth outlining general considerations to be taken into account with regard to the growth by CVD of any insulating lm: the type of CVD method, deposition variables, and limitations of the precursor. Chemical Vapor Deposition of Silica Thin Films, Connexions Web site. http://cnx.org/content/m24897/1.4/, Jan 22, 2010. Andrew R. Barron, Gener
Typology: Study notes
1 / 10
This page cannot be seen from the preview
Don't miss anything!
This work is produced by The Connexions Project and licensed under the Creative Commons Attribution License †
Before describing individual chemical vapor deposition (CVD) systems for the deposition of silica thin lms, it is worth outlining general considerations to be taken into account with regard to the growth by CVD of any insulating lm: the type of CVD method, deposition variables, and limitations of the precursor.
1.1 Deposition methods
In regard to the CVD of insulating lms in general, and silica lms in particular, three general reactors are presently used: atmospheric pressure CVD (APCVD), low and medium temperature low pressure CVD (LPCVD), and plasma-enhanced CVD (PECVD). LPCVD is often further divided into low and high tem- peratures. APCVD systems allow for high throughput and even continuous operation, while LPCVD provides for superior conformal step coverage and better lm homogeneity. PECVD has been traditionally used where low temperatures are required, however, lm quality is often poor. As compared to PECVD, photo-assisted CVD has the additional advantage of highly selective deposition, although it has been little used in commercial systems. Table 1 summarizes the advantages and disadvantages of each type of CVD system commercially used for SiO 2 lms.
Atmospheric pressure CVD
Low tempera- ture LPCVD
Medium temperature LPCVD
Plasma en- hanced CVD
Temperature ( ◦C) 300 - 500 300 - 500 500 - 900 100 - 350 Throughput high high high low Step coverage poor poor conformal poor continued on next page
∗Version 1.4: Jan 22, 2010 1:55 pm US/Central †http://creativecommons.org/licenses/by/3.0/
Film properties good good excellent poor Uses passivation, insu- lation
passivation, insu- lation
insulation passivation, insu- lation
Table 1: Comparison of dierent deposition methods for SiO 2 thin lms.
1.2 Deposition variables
The requirements of CVD lms for electronic device applications have become increasingly more stringent as device sizes are continually reduced. Film thickness must be uniform across an entire wafer, i.e., better than ±1%. The structure of the lm and its composition must be controlled and reproducible, both on a single wafer, as well as between wafer samples. It is also desirable that the process is safe, inexpensive, and easily automated. A number of variables determine the quality and rate of lm growth for any material. In general, the deposition rate increases with increased temperature and follows the Arrhenius equation, (1), where R is the deposition rate, Ea is the activation energy, T is the temperature (K), A is the frequency factor, and k is Boltzmann's constant (1.381 x 10-23^ J/K).
At the high temperatures the rate of deposition becomes mass transport limited. Meaning, the rate of surface reaction is faster than the rate at which precursors are transported to the surface. In multiple source systems, the lm growth rate is dependent on the vapor phase concentration (or partial pressure) of each of the reactants, but in certain cases the ratio of reactants is also important, e.g., the SiH 4 /O 2 growth of SiO 2. Surface catalyzed reactions can also alter the deposition rate. Such as the non-linear dependence of the deposition rate of SiO 2 on the partial pressure of Si(OEt) 4. Gas depletion may also be signicant requiring either a thermal ramp in the chamber and/or special reactor designs. The necessary incorporation of dopants usually lowers deposition rates, due to competitive surface binding. For the applications of insulating materials as isolation layers, an important consideration is step coverage: whether a coating is uniform with respect to the surface. Figure 1a shows a schematic of a completely uniform or conformal step coverage of a trench (such as occurs between isolated devices) where the lm thickness along the walls is the same as the lm thickness at the bottom of the step. Uniform step coverage results when reactants or reactive intermediates are able to migrate rapidly along the surface before reacting. When the reactants adsorb and react without signicant surface migration, deposition is dependent on the mean free path of the gas. Figure 1b shows an example of minimal surface migration and a short mean free path. For SiO 2 lm growth LPCVD has highly uniform coverage (Figure 1a) and PECVD poor step coverage (Figure 1b).
endeavor to preserve such an interaction intact from the source molecule into the ultimate lm; such a source is often termed a "single-source" precursor.
The processing sequence for silicon dioxide (SiO 2 ) used depends on its specic use. CVD processes for SiO 2 lms can be characterized by either the chemical reaction type, the growth pressure, or the deposition temperature. The choice of route is often dictated by requirements of the thermal stability of the substrate or the conformality. Table 3 summarizes selected properties of SiO 2 grown by various CVD methods, in comparison to that of thermally grown silica. In general, silica grown at high temperatures resemble thermally grown native SiO 2. However, the use of aluminum metallization requires low temperature deposition of silica.
Deposition Plasma SiH 4 + O 2 Si(OEt) 4 SiCl 2 H 2 + N 2 O Thermal Temperature ( ◦C) 200 450 700 900 1000 Composition SiO1.9(H) SiO 2 (H) SiO 2 SiO 2 (Cl) SiO 2 Step coverage non-conformal non-conformal conformal conformal conformal Thermal stability loses H densies stable loses Cl stable Refractive idex 1.47 1.44 1.46 1.46 1. Dielectric constant 4.9 4.3 4.0 4.0 3.
Table 3: Comparison of physical properties of SiO 2 grown by commercial CVD methods.
2.1 CVD from hydrides
The most widely used method for SiO 2 thin lm CVD is the oxidation of silane (SiH 4 ), rst developed in 1967 for APCVD. Nonetheless, LPCVD systems have since become increasingly employed, and exceptionally high growth rates (30,000 Å/min) have been obtained by the use of rapid thermal CVD. The chemical reaction for SiO 2 deposition from SiH 4 is:
At high oxygen partial pressures an alternative reaction occurs, resulting in the formation of water.
While these reactions appears simple, the detailed mechanism involves a complex branching-chain sequence of reactions. The apparent activation energy is low (< 41 kJ/mol) as a consequence of its heterogeneous nature, and involves both surface adsorption and surface catalysis. Nitrous oxide (N 2 O) can be used as an alternative oxygen source to O 2 , according to the overall reaction, (4).
A simple kinetic scheme has been developed to explain many of the observed aspects of SiH 4 -N 2 O growth. It was suggested that the reaction is initiated by decomposition of N 2 O, (5), generating an oxygen radical
which can abstract hydrogen from silane forming a hydroxyl radical, (6), that can react further with silane, (7).
Evidence for the reaction of the OH radical to form water is the formation of a small quantity of water observed during the oxidation of SiH 4. Silyl radicals are oxidized by N 2 O to form siloxy radicals, (8), which provide a suitable propagation step, (9).
It has been proposed that the silanol (SiH 3 OH) is the penultimate lm precursor. The SiH 4 -O 2 and SiH 4 -N 2 O routes to SiO 2 thin lms are perhaps the most widely studied photochemical CVD system of all dielectrics. Photo-CVD of SiO 2 provides a suitable route to deposition at low substrate temperatures, thereby avoiding potential thermal eects of wafer warpage and deleterious dopant redistri- bution. In addition, unlike other low temperature methods such as APCVD and PECVD, photo-CVD often provides good purity of lms. A summary of common silane CVD systems is given in Table 4.
Oxygen source Carrier gas (diluent)
CVD method Deposition temp. ( ◦C)
Growth rate (Å/min) O 2 N 2 APCVD 350 - 475 100 - 14, O 2 Ar LPCVD 100 - 550 100 - 30, O 2 Ar/N 2 LPCVD 25 - 500 10 - 450 O 2 Ar PECVD 25 - 200 200 - 900 N 2 O N 2 APCVD 490 - 690 200 - 1, N 2 O N 2 LPCVD 700 - 860 ca. 50 N 2 O N 2 LPCVD 25 - 350 7 - 180 continued on next page
Figure 2: Alternative organometallic silicon sources that have been investigated for the growth of silica thin lms.
An interesting concept has been to preform the -Si-O-Si- framework in the precursor. In this regard, the novel precursor T 8 -hydridospherosiloxane (H 8 Si 8 O 12 , Figure 2d) gives smooth amorphous stoichiometric SiO 2 at 450 - 525 ◦C by LPCVD. The decomposition mechanism in the presence of added oxygen involves the loss of water, (11). IR studies indicate that the Si-O-Si bonds are preserved during deposition. While lms are of high quality, the present synthesis of H 8 Si 8 O 12 is of low yield (ca. 21%), making it currently impractical for large scale processing.
Borosilicate glasses (BSG), phosphosilicate glasses (PSG) and borophosphosilicate glasses (BPSG) are fre- quently used as insulating layers separating conducting layers. These glasses have lower intrinsic stress, lower melting temperatures and better dielectric properties than SiO 2 itself. PSG and BPSG have the added prop- erty of gettering and immobilizing dopants. Particularly important is the gettering of sodium ions, which are a source of interface traps. The low temperature molten properties of BSG, PSG, and BPSG glasses allow for the smoothing of the device topography by viscous thermal fusion to convert abrupt steps to more gradually tapered steps (Figure 3a) as well as planarization of complex topologies (Figure 3b), enabling deposition of continuous metal layers. This process is commonly called P-glass ow. The boron and phosphorous contents of the silicate glasses vary, depending on the application, typically being from 2 to 8 weight per cent.
Figure 3: Schematic cross section of BPSG as deposited (a) and after annealing (b), showing the ow causing a decrease in the angle of the BPSG going over the step.
The advantage of BPSG over PSG is that ow occurs over the temperature range of 750 - 950 ◦C, depending on the relative P and B content (as opposed to 950 - 1110 ◦C for PSG). Lowering of the ow temperature is required to minimize dopant migration in VLSI devices. Conversely, the disadvantages of BPSG versus PSG include the formation of bubbles of volatile phosphorous oxides and crystallites of boron- rich phases. If, however, the dopant concentration is controlled, these eects can be minimized. Arsenosilicates (AsSG) were employed originally in silicon device technology as an arsenic dopant source for planar substrates prior to the advent of large scale ion implantation which has largely removed the need for AsSG in doping applications. However, with ULSI silicon circuit fabrication, the requirement for doping of deep trenches (inaccessible to ion implantation) has witnessed the re-emergence of interest in AsSG lms. The CVD growth of silicate glasses follows that of SiO 2 , with SiH 4 and TEOS being the most commonly employed silicon precursors. A summary of common CVD precursor systems for silicate glasses is given in Table 5.
Arsenosilicate glass (AsSG) thin lms are generally grown by APCVD using arsine (AsH3); the use of which is being limited due to its high toxicity. However, arsine inhibits the gas phase reactions between SiH 4 and O 2 , such that lm grown from SiH 4 /AsH 3 /O 2 show improved step coverage at high deposition rates.
3.2 CVD from metal organic precursors
As with SiO 2 deposition, see above, there has been a trend towards the replacement of SiH 4 with TEOS on account of its ability to produce highly conformal coatings. This is particularly attractive with respect to trench lling. Furthermore, lms of doped SiO 2 glasses have been obtained using both APCVD and LPCVD (typically below 3 Torr), with a wide variety of dopant elements including: boron, phosphorous, and arsenic, including antimony, tin, and zinc. Boron-containing glasses are generally grown using either trimethylborate, B(OMe) 3 , or triethylborate, B(OEt) 3 , although the multi-element source, tris(trimethylsilyl)borate, B(OSiMe 3 ) 3 , has been employed for both silicon and boron in BPSG thin lm growth. Similarly, whereas PH 3 may be used as the phospho- rous source, trimethylphosphite, P(OMe) 3 , and trimethylphosphate, O=P(OMe) 3 , are preferred. Likewise, triethoxyarsine, As(OEt) 3 , and triethylarsenate, O=As(OEt) 3 , have been employed for AsSG growth. The co-reaction of TEOS with organoboron and organophosphorous compounds allows for deposition at lower temperatures (500 - 650 ◦C) than for hydride growth of comparable rates. However, LPCVD, using an all organometallic approach, requires P(OMe) 3 because the low reactivity of O=P(OMe) 3 prevents signicant phosphorus incorporation. Although premature decomposition of P(OMe) 3 occurs at 600 ◦C (leading to non-uniform growth), deposition at 550 ◦C results in high lm uniformity at reasonable deposition rates.