
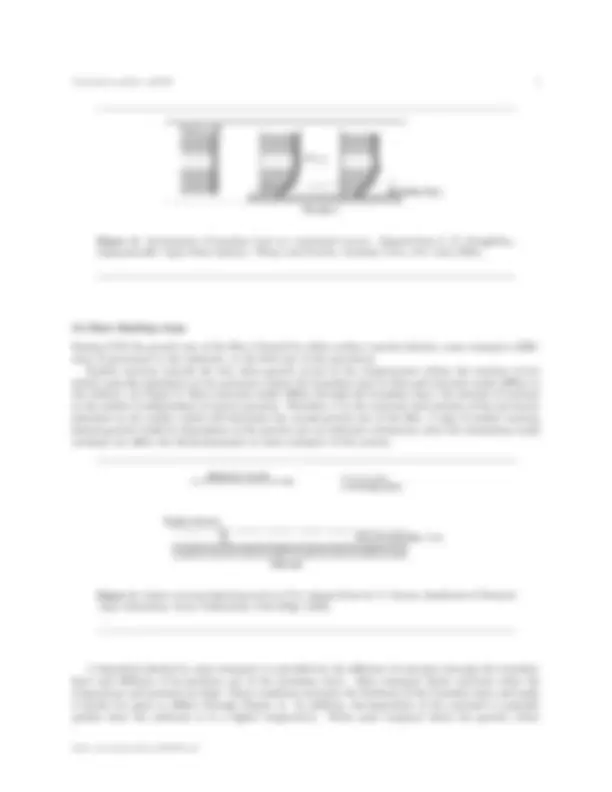
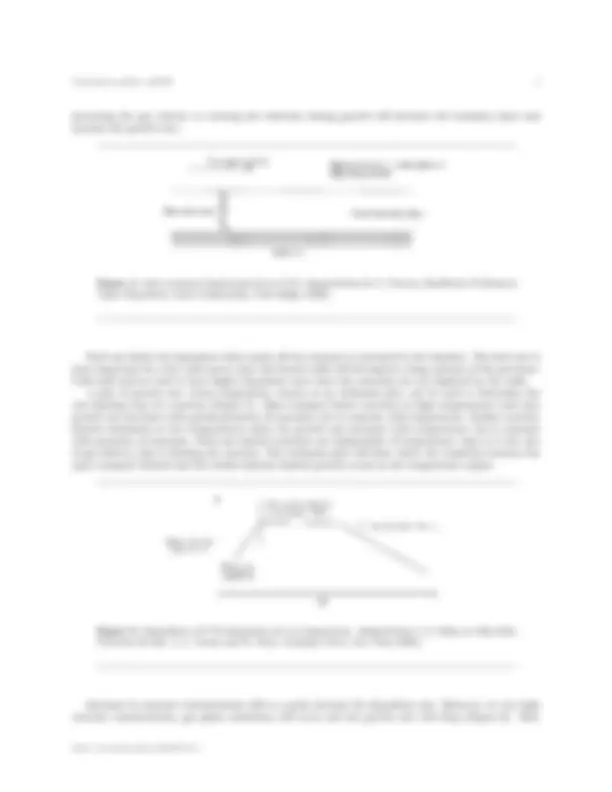
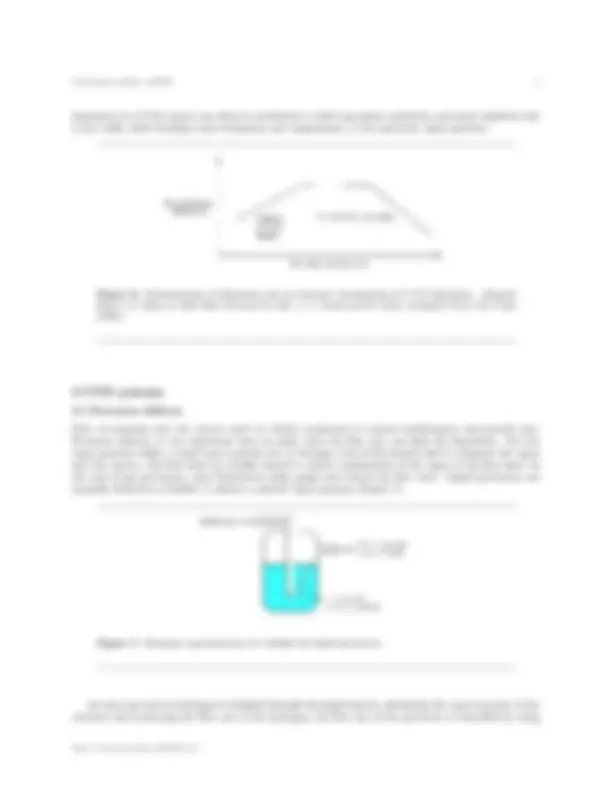
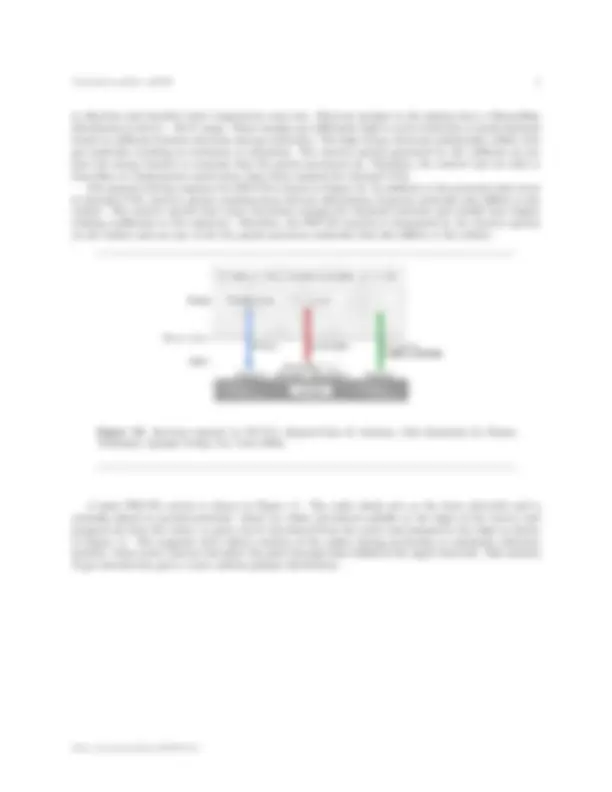
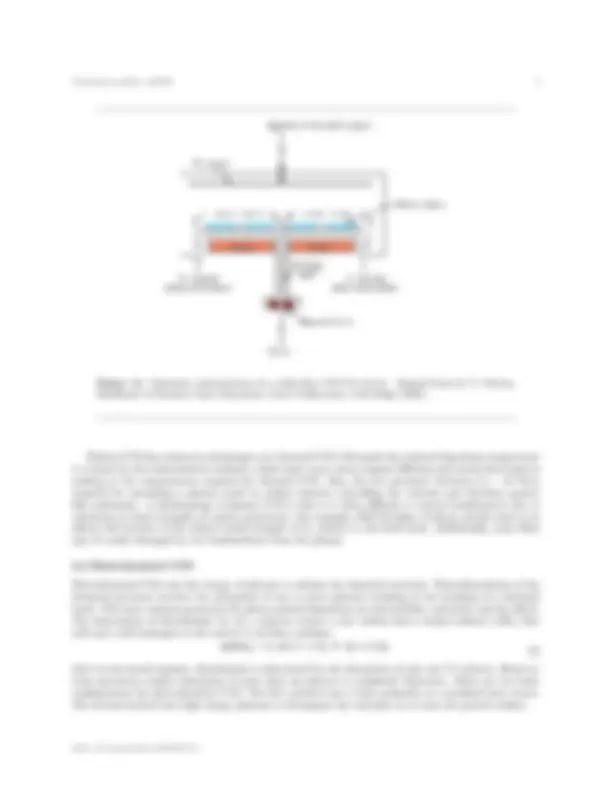
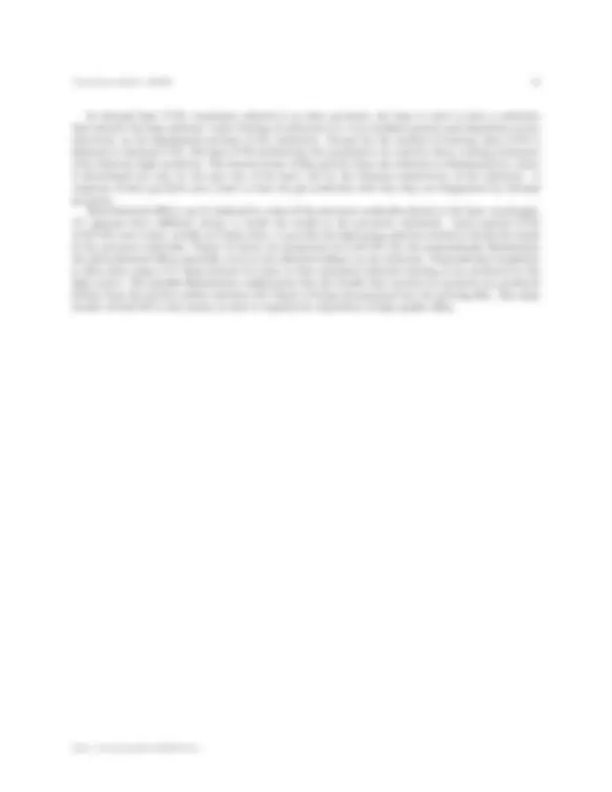
Study with the several resources on Docsity
Earn points by helping other students or get them with a premium plan
Prepare for your exams
Study with the several resources on Docsity
Earn points to download
Earn points by helping other students or get them with a premium plan
Community
Ask the community for help and clear up your study doubts
Discover the best universities in your country according to Docsity users
Free resources
Download our free guides on studying techniques, anxiety management strategies, and thesis advice from Docsity tutors
Study Material. Chemical vapor deposition (CVD) is a deposition process where chemical precursors are transported in the vapor phase to decompose on a heated substrate to form a lm. The lms may be epitaxial, polycrystalline or amorphous depending on the materials and reactor conditions. CVD has become the major method of lm deposition for the semiconductor industry due to its high throughput, high purity, and low cost of operation. CVD is also commonly used in optoelectronics applications, op
Typology: Study notes
1 / 12
This page cannot be seen from the preview
Don't miss anything!
This work is produced by The Connexions Project and licensed under the Creative Commons Attribution License †
note: This module was developed as part of the Rice University course CHEM-496: Chemistry of Electronic Materials. This module was prepared with the assistance of Scott Stokes.
Chemical vapor deposition (CVD) is a deposition process where chemical precursors are transported in the vapor phase to decompose on a heated substrate to form a lm. The lms may be epitaxial, polycrystalline or amorphous depending on the materials and reactor conditions. CVD has become the major method of lm deposition for the semiconductor industry due to its high throughput, high purity, and low cost of operation. CVD is also commonly used in optoelectronics applications, optical coatings, and coatings of wear resistant parts. CVD has many advantages over physical vapor deposition (PVD) processes such as molecular beam evaporation and sputtering. Firstly, the pressures used in CVD allow coating of three dimensional structures with large aspect ratios. Since evaporation processes are very directional, PVD processes are typically line of sight depositions that may not give complete coverage due to shadowing from tall structures. Secondly, high precursor ow rates in CVD give deposition rates several times higher than PVD. Also, the CVD reactor is relatively simple and can be scaled to t several substrates. Ultra-high vacuum is not needed for CVD and changes or additions of precursors is an easy task. Furthermore, varying evaporation rates make stoichiometry hard to control in physical deposition. While for CVD stoichiometry is more easily controlled by monitoring ow rates of precursors. Other advantages of CVD include growth of high purity lms and the ability to fabricate abrupt junctions. There are, however, some disadvantages of CVD that make PVD more attractive for some applications. High deposition temperatures for some CVD processes (often greater than 600 ◦C) are often unsuitable for structures already fabricated on substrates. Although with some materials, use of plasma-enhanced CVD or metal-organic precursors may reduce deposition temperatures. Another disadvantage is that CVD precursors are often hazardous or toxic and the by-products of these precursors may also be toxic. Therefore extra steps have to be taken in the handling of the precursors and in the treatment of the reactor exhaust. Also, many precursors for CVD, especially the metal-organics, are relatively expensive. Finally, the CVD process contains a large number of parameters that must be accurately and reproducibly optimized to produce good lms.
A normal CVD process involves complex ow dynamics since gases are owing into the reactor, reacting, and then by-products are exhausted out of the reactor. The sequence of events during a CVD reaction are shown in Figure 1 and as follows: ∗Version 1.2: Jul 13, 2009 5:58 pm GMT- †http://creativecommons.org/licenses/by/3.0/
Figure 1: Sequence of events during CVD: (a) diusion of reactants through boundary layer, (b) adsorption of reactants on substrate, (c) chemical reaction takes place, (d) desorption of adsorbed species, and (e) diusion out of by-products through boundary layer. Adapted from H. O. Pierson, Handbook of Chemical Vapor Deposition, Noyes Publications, Park Ridge (1992).
2.1 The boundary layer
Gas ow in a CVD reactor is generally laminar, although in some cases heating of the chamber walls will create convection currents. The complete problem of gas ow through the system is too complex to be described here; however, assuming we have laminar ow (often a safe assumption) the gas velocity at the chamber walls will be zero. Between the wall (zero velocity) and the bulk gas velocity there is a boundary layer. The boundary layer thickness increases with lowered gas velocity and the distance from the tube inlet (Figure 2). Reactant gases owing in the bulk must diuse through the boundary layer to reach the substrate surface. Often, the susceptor is tilted to partially compensate for the increasing boundary-layer thickness and concentration prole.
increasing the gas velocity or rotating the substrate during growth will decrease the boundary layer and increase the growth rate.
Figure 4: Mass transport limited growth in CVD. Adapted from H. O. Pierson, Handbook of Chemical Vapor Deposition, Noyes Publications, Park Ridge (1992).
Feed rate limits the deposition when nearly all the reactant is consumed in the chamber. The feed rate is more important for a hot wall reactor since the heated walls will decompose a large amount of the precursor. Cold wall reactors tend to have higher deposition rates since the reactants are not depleted by the walls. A plot of growth rate versus temperature, known as an Arrhenius plot, can be used to determine the rate limiting step of a reaction (Figure 5). Mass transport limits reactions at high temperatures such that growth rate increases with partial pressures of reactants, but is constant with temperature. Surface reaction kinetics dominates at low temperatures where the growth rate increases with temperature, but is constant with pressures of reactants. Feed rate limited reactions are independent of temperature, since it is the rate of gas delivery that is limiting the reaction. The Arrhenius plot will show where the transition between the mass transport limited and the surface kinetics limited growth occurs in the temperature regime.
Figure 5: Dependence of CVD deposition rate on temperature. Adapted from J. G. Eden, in Thin Film Processes II, Eds. J. L. Vossen and W. Kern, Academic Press, New York (1991).
Increases in reactant concentrations will to a point increase the deposition rate. However, at very high reactant concentrations, gas phase nucleation will occur and the growth rate will drop (Figure 6). Slow
deposition in a CVD reactor can often be attributed to either gas phase nucleation, precursor depletion due to hot walls, thick boundary layer formation, low temperature, or low precursor vapor pressure.
Figure 6: Demonstration of deposition rate on reactant concentration for CVD deposition. Adapted from J. G. Eden, in Thin Film Processes II, Eds. J. L. Vossen and W. Kern, Academic Press, New York (1991).
3.1 Precursor delivery
Flow of reactants into the reactor must be closely monitored to control stoichiometry and growth rate. Precursor delivery is very important since in many cases the ow rate can limit the deposition. For low vapor pressure solids, a carrier gas is passed over or through a bed of the heated solid to transport the vapor into the reactor. Gas ow lines are usually heated to reduce condensation of the vapor in the ow lines. In the case of gas precursors, mass owmeters easily gauge and control the ow rates. Liquid precursors are normally heated in a bubbler to achieve a desired vapor pressure (Figure 7).
Figure 7: Schematic representation of a bubbler for liquid precursors.
An inert gas such as hydrogen is bubbled through the liquid and by calculating the vapor pressure of the reactant and monitoring the ow rate of the hydrogen, the ow rate of the precursor is controlled by using
Figure 9: Schematic of a typical low pressure hot wall CVD reactor used in coating silicon substrates. Adapted from H. O. Pierson, Handbook of Chemical Vapor Deposition, Noyes Publications, Park Ridge (1992).
In a cold wall reactor only the substrate is heated, usually by induction or radiant heating. Since most CVD reactions are endothermic, deposition is preferentially on the area of highest temperature. As a result, deposition is only on the substrate and the cooler reactor walls stay clean. Cold wall CVD has two main advantages over the hot wall conguration. First, particulate contamination is reduced since there are no deposits formed on the walls of the reactor. Second, since decomposition only occurs on the substrate there is no depletion of source gases due to reaction on the walls. However, hot wall reactors tend to have higher throughput since the designs more easily accommodate multiple wafer congurations. The nal issue in design of a thermal CVD reactor is the operating pressure. The pressure of the reactor has a large eect on the rate limiting step of the deposition. Atmospheric pressure reactors have a large boundary layer (Figure 4) and non-uniform diusion of reactants through the boundary layer often results in non-uniform lm compositions across the wafer. Conversely, low pressure reactors have a nearly non-existent boundary later and reactants easily diuse to the substrate (Figure 3). However, the diculty in maintaining a uniform temperature prole across the wafer can result in thickness non-uniformities since the deposition rate in low pressure reactors is strongly temperature dependent. Careful studies of the ow dynamics and temperature proles of CVD reactors are always carried out in order to achieve uniform material depositions.
3.3 Plasma-enhanced CVD
Plasmas are generated for a variety of thin lm processes including sputtering, etching, ashing, and plasma- enhanced CVD. Plasma-enhanced CVD (PECVD), sometimes called plasma-assisted (PACVD), has the advantage that plasma activated reactions occur at much lower temperatures compared to those in thermal CVD. For example, the thermal CVD of silicon nitride occurs between 700 - 900 ◦C, the equivalent PECVD process is accomplished between 250 - 350 ◦C. A plasma is a partially ionized gas consisting of electrons and ions. Typical ionization fractions of 10-5^ to 10 -1^ are encountered in process reactors. Plasmas are electrically conductive with the primary charge carriers being the electrons. The light mass of the electron allows it to respond much more quickly to changes in the eld than the heavier ions. Most plasmas used for PECVD are generated using a rf electric eld. In the high frequency electric eld, the light electrons are quickly accelerated by the eld but do not increase the temperature of the plasma because of their low mass. The heavy ions cannot respond to the quick changes
in direction and therefore their temperature stays low. Electron energies in the plasma have a Maxwellian distribution in the 0.1 20 eV range. These energies are suciently high to excite molecules or break chemical bonds in collisions between electrons and gas molecules. The high energy electrons inelastically collide with gas molecules resulting in excitation or ionization. The reactive species generated by the collisions do not have the energy barriers to reactions that the parent precursors do. Therefore, the reactive ions are able to form lms at temperatures much lower than those required for thermal CVD. The general reaction sequence for PECVD is shown in Figure 10. In addition to the processes that occur in thermal CVD, reactive species resulting from electron dissociation of parent molecules also diuse to the surface. The reactive species have lower activation energies for chemical reactions and usually have higher sticking coecients to the substrate. Therefore, the PECVD reaction is dominated by the reactive species on the surface and not any of the the parent precursor molecules that also diuse to the surface.
Figure 10: Reaction sequence in PECVD. Adapted from M. Konuma, Film Deposition by Plasma Techniques, Springer-Verlag, New York (1992).
A basic PECVD reactor is shown in Figure 11. The wafer chuck acts as the lower electrode and is normally placed at ground potential. Gases are either introduced radially at the edges of the reactor and pumped out from the center, or gases can be introduced from the center and pumped at the edges as shown in Figure 11. The magnetic drive allows rotation of the wafers during processing to randomize substrate position. Some newer reactors introduce the gases through holes drilled in the upper electrode. This method of gas introduction gives a more uniform plasma distribution.
In thermal laser CVD, sometimes referred to as laser pyrolysis, the laser is used to heat a substrate that absorbs the laser photons. Laser heating of substrates is a very localized process and deposition occurs selectively on the illuminated portions of the substrates. Except for the method of heating, laser CVD is identical to thermal CVD. The laser CVD method has the potential to be used for direct writing of features with relatively high resolution. The lateral extent of lm growth when the substrate is illuminated by a laser is determined not only by the spot size of the laser, but by the thermal conductivity of the substrate. A variation of laser pyrolysis uses a laser to heat the gas molecules such that they are fragmented by thermal processes. Photochemical eects can be induced by a laser if the precursor molecules absorb at the laser wavelength. UV photons have sucient energy to break the bonds in the precursor chemicals. Laser-assisted CVD (LACVD) uses a laser, usually an eximer laser, to provide the high energy photons needed to break the bonds in the precursor molecules. Figure 12 shows two geometries for LACVD. For the perpendicular illumination the photochemical eects generally occur in the adsorbed adlayer on the substrate. Perpendicular irradiation is often done using a UV lamp instead of a laser so that unwanted substrate heating is not produced by the light source. The parallel illumination conguration has the benet that reaction by-products are produced further from the growth surface and have less chance of being incorporated into the growing lm. The main benet of LACVD is that nearly no heat is required for deposition of high quality lms.
Figure 12: Parallel (a) and perpendicular (b) irradiation in laser CVD. Adapted from J. G. Eden, in Thin Film Processes II, Eds. J. L. Vossen and W. Kern, Academic Press, New York (1991).
An application of laser photolysis is photonucleation. Photonucleation is the process by which a chemisorbed adlayer of metal precursors is photolyzed by the laser to create a nucleation site for further growth. Photonu- cleation is useful in promoting growth on substrates that have small sticking coecients for gas phase metal atoms. By beginning the nucleation process with photonucleation the natural barrier to surface nucleation on the substrate is overcome.