
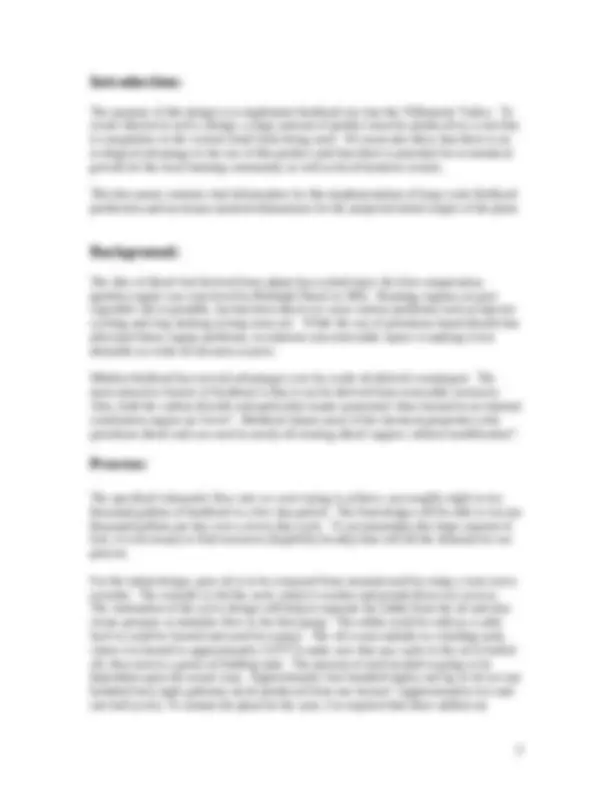
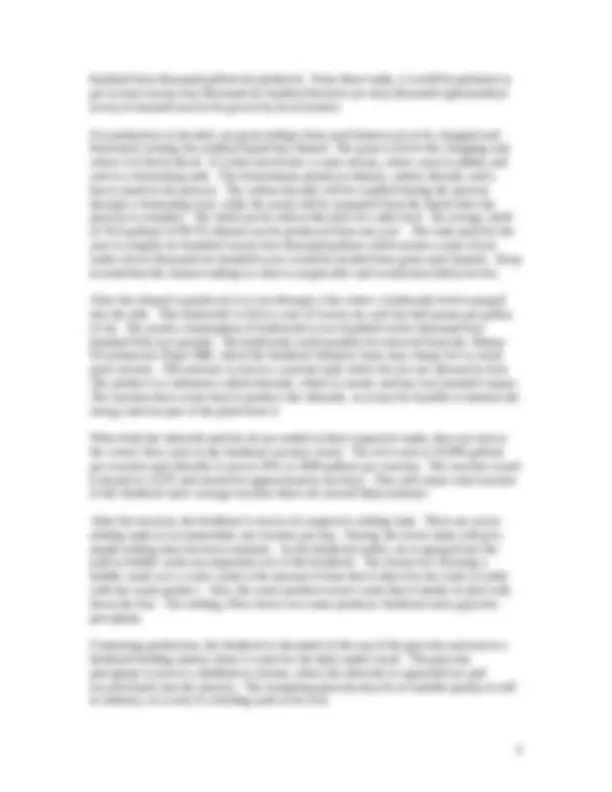
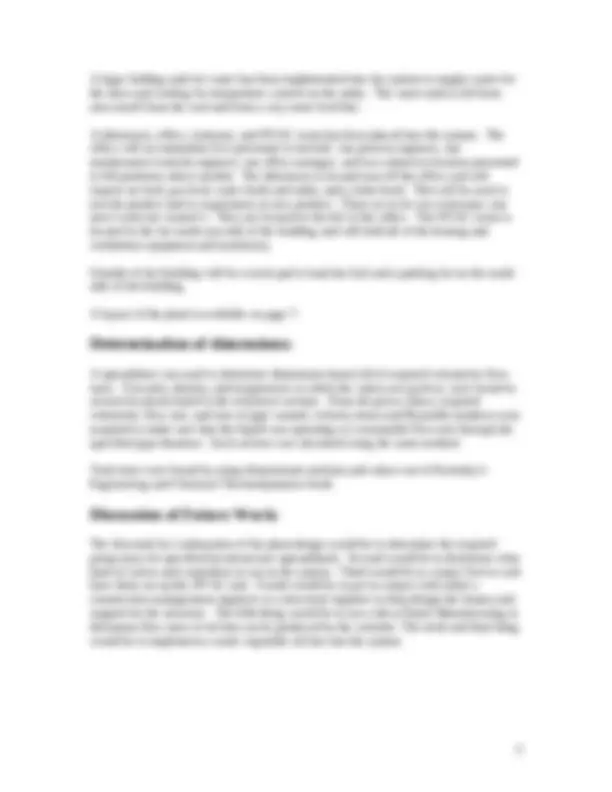
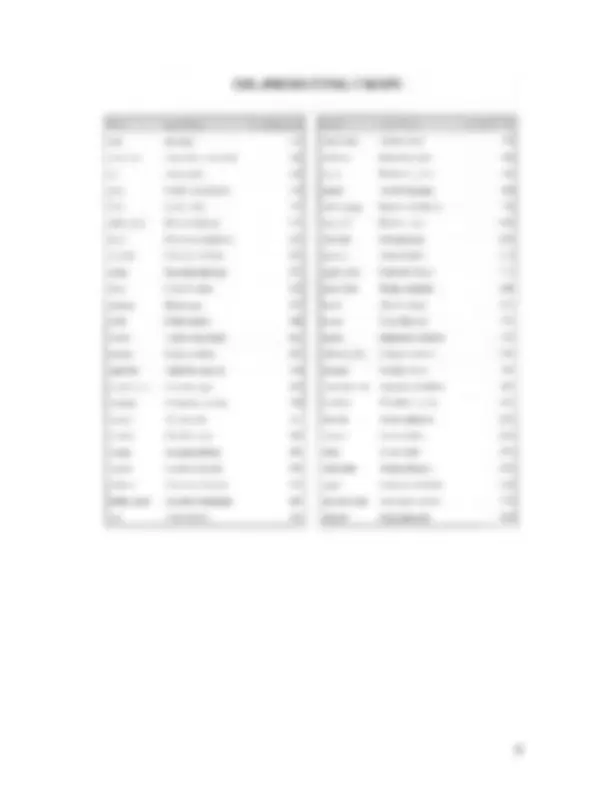

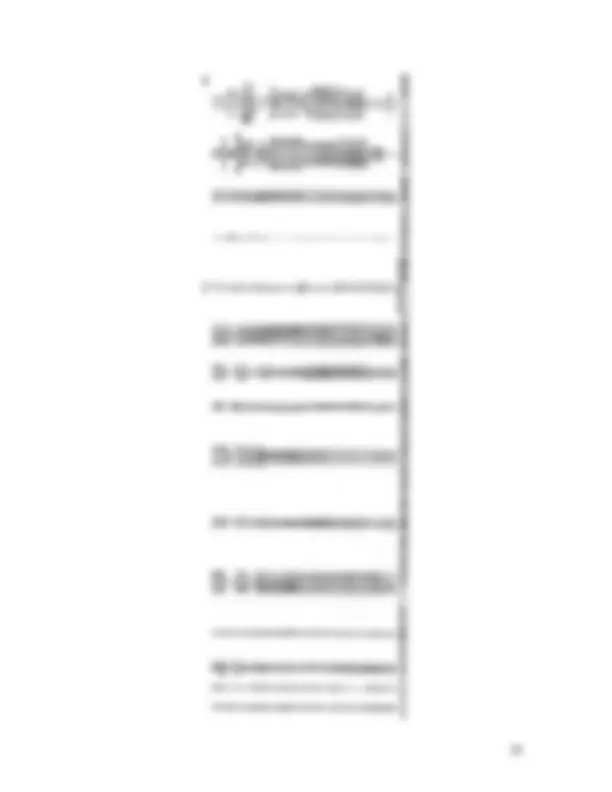
Study with the several resources on Docsity
Earn points by helping other students or get them with a premium plan
Prepare for your exams
Study with the several resources on Docsity
Earn points to download
Earn points by helping other students or get them with a premium plan
Community
Ask the community for help and clear up your study doubts
Discover the best universities in your country according to Docsity users
Free resources
Download our free guides on studying techniques, anxiety management strategies, and thesis advice from Docsity tutors
Material Type: Exam; Class: PROCESS ENGINEERING LABORATORY; Subject: Chemical Engineering; University: Oregon State University; Term: Winter 2005;
Typology: Exams
1 / 12
This page cannot be seen from the preview
Don't miss anything!
- i) Introduction…………………………………………………………………………… - ii) Background…………………………………………………………………………... - iii) Process……………………………………………………………………………. 3- - iv) Determination of dimensions…………………………………………………………
hundred forty thousand gallons be produced. From these totals, it would be pertinent to get at least twenty four thousand six hundred hectares (or sixty thousand eight hundred acres) of mustard seed to be grown by local farmers. For production of alcohol, rye grass tailings from seed farmers are to be chopped and fermented, turning the residual liquid into ethanol. The grass is fed to the chopping unit where it is finely diced. It is then mixed into a water stream, where yeast is added, and sent to a fermenting tank. The fermentation produces ethanol, carbon dioxide, and a heavy mash in the process. The carbon dioxide will be expelled during the process through a fermenting lock, while the mash will be separated from the liquid after the process is complete. The solid can be sold at this time for cattle feed. An average yield of 54.0 gallons of 99.5% ethanol can be produced from one acrev. The total need for the year is roughly six hundred twenty four thousand gallons which means a total of just under eleven thousand six hundred acres would be needed from grass seed farmers. Keep in mind that the farmers tailings is what is sought after and would most likely be free. After the ethanol is produced, it is run through a line where a hydroxide feed is purged into the side. This hydroxide is fed at a rate of twenty six and one half grams per gallon of oil. The yearly consumption of hydroxide is two hundred twelve thousand four hundred fifty two pounds. The hydroxide could possibly be removed from the Albany Weyerhaeuser Paper Mill, which the biodiesel initiative team may charge for to create more income. This mixture is sent to a reactant tank where the two are allowed to fuse. The product is a substance called ethoxide, which is caustic and has very harmful vapors. The reaction does create heat to produce the ethoxide, so it may be feasible to harness the energy and run part of the plant from it. When both the ethoxide and the oil are settled in their respective tanks, they are sent at the correct flow rates to the biodiesel reaction vessel. The oil is sent at 10,000 gallons per reaction and ethoxide is sent at 20% or 2000 gallons per reaction. The reaction vessel is heated to 125^0 F and stirred for approximately one hour. This will ensure total reaction of the biodiesel since average reaction times are around thirty minutes. After the reaction, the biodiesel is sent to its respective settling tank. There are seven settling tanks to accommodate one reaction per day. Having the seven tanks will give ample settling time between rotations. As the biodiesel settles, air is sparged into the tank to bubble wash any impurities out of the biodiesel. The reason for choosing a bubble wash over a water wash is the amount of time that it takes for the water to settle with the waste product. Also, the water produces more waste that is harder to deal with down the line. The settling effect leaves two main products: biodiesel and a glycerin precipitate. Continuing production, the biodiesel is decanted of the top of the glycerin and sent to a biodiesel holding station where it waits for the daily tanker truck. The glycerin precipitate is sent to a distillation column, where the ethoxide is vaporized out and recycled back into the process. The remaining glycerin may be of suitable quality to sell to industry, so is sent to a holding tank of its own.
A large holding tank for water has been implemented into the system to supply water for the lines and cooling for temperature control on the tanks. The water tank is fed from rain runoff from the roof and from a city water feed line. A laboratory, office, restroom, and HVAC room has been placed into the system. The office will accommodate five personnel to include: one process engineer, one maintenance/controls engineer, one office manager, and two unknown location personnel to fill positions where needed. The laboratory is located just off the office and will require air feed, gas feed, water feeds and sinks, and a fume hood. This will be used to test the product and to experiment on new product. There are to be two restrooms: one men’s and one women’s. They are located to the left of the office. The HVAC room is located to the far south east side of the building and will hold all of the heating and ventilation equipment and machinery. Outside of the building will be a truck pad to load the fuel and a parking lot on the south side of the building. A layout of the plant is available on page 7.
A spreadsheet was used to determine dimensions based off of required volumetric flow rates. Viscosity, density, and temperature at which the values are good at, were found in several locations listed in the references section. From the given values, required volumetric flow rate, and size of pipe wanted, velocity terms and Reynolds numbers were acquired to make sure that the liquid was operating at a reasonable flow rate through the specified pipe diameter. Each section was calculated using the same method. Tank sizes were found by using dimensional analysis and values out of Koretsky’s Engineering and Chemical Thermodynamics book.
The first task for continuation of the plant design would be to determine the required pump sizes for specified locations (see spreadsheet). Second would be to determine what kind of valves and controllers to use in the system. Third would be to contact Servco and have them set up the HVAC unit. Fourth would be to get in contact with either a construction management engineer or a structural engineer to help design the beams and support for the structure. The fifth thing would be to run a lab at Entek Manufacturing to determine flow rates of oil that can be produced by the extruder. The sixth and final thing would be to implement a waste vegetable oil line into the system.
1 Muniyappa, P.R., S.C. Brammer, H. Noureddini (1996). “Improved Conversion of Plant Oils and Animal Fats into Biodiesel and Co-Product.” Bioresource Technology. 56: 19-24. 2 Sheehan, J. et al. (1998) “An Overview of Biodiesel and Petroleum Diesel Life Cycles.” National Renewable Energy Laboratory. 3 Lewis, Alex., et al. Two Stage Biodiesel Production: Batch Production of Biodiesel from Used Vegetable Oils and Methanol. OSUBIT , 2004. 4 Pelly, Mike. Journey to Forever. <http//journeytoforever.org/> 5 Tickell, Joshua. From the Fryer to the Fuel Tank: The Complete Guide to Using Vegetable Oil as an Alternative Fuel. Tallahassee: TEC, 2000. 6 Koretsky, Milo D. Engineering and Chemical Thermodynamics. Hoboken: 2004. 7 Rorrer, Gregory. , et al. Fundamentals of Momentum, Heat, and Mass Transfer. 4 th^ ed. Corvallis, 2001.