
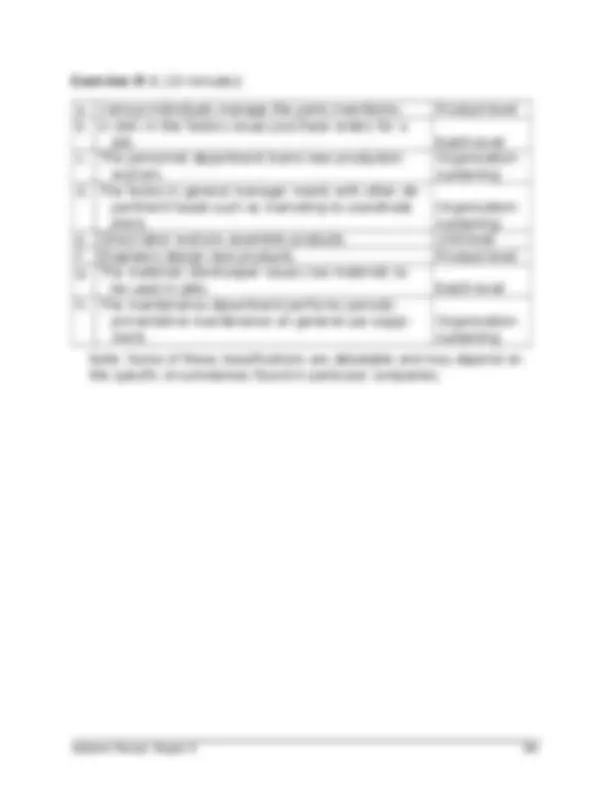

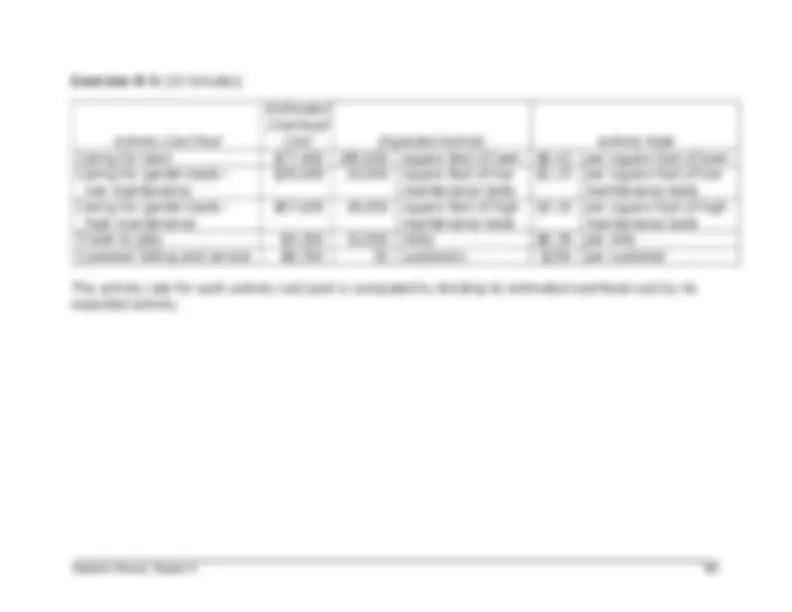
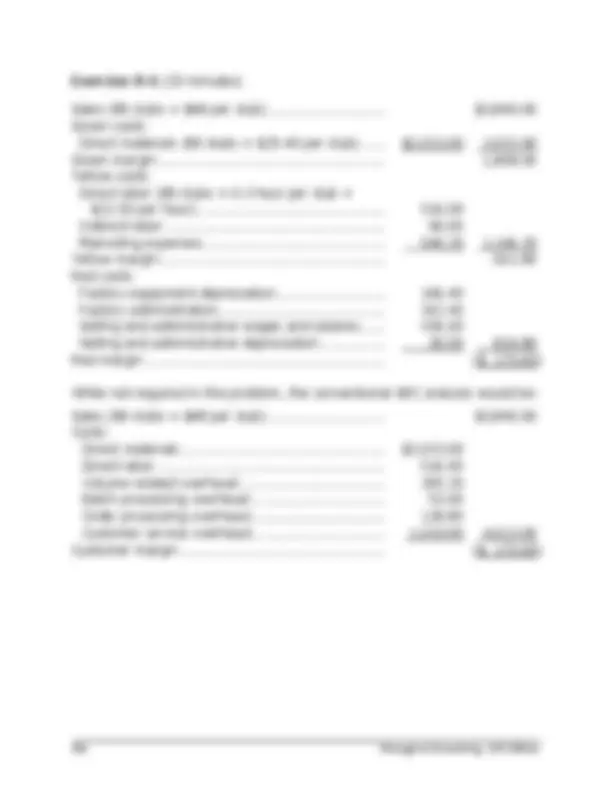
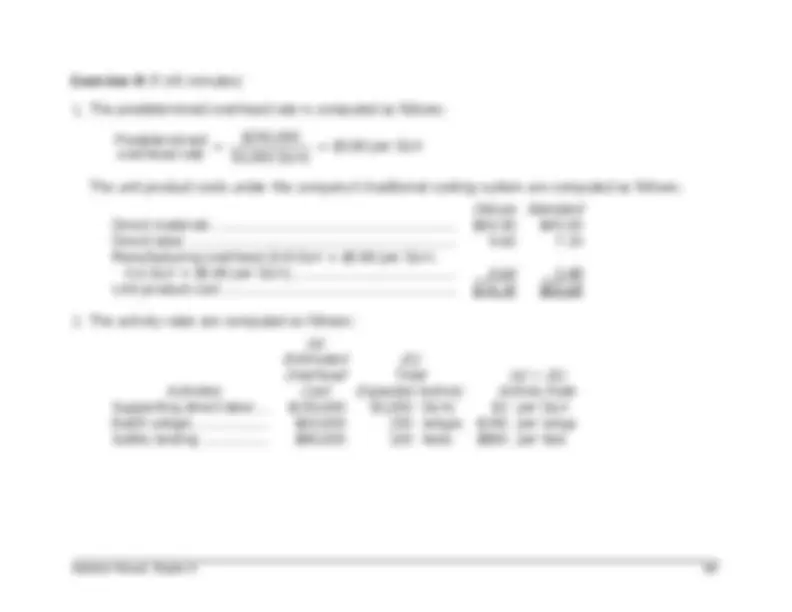
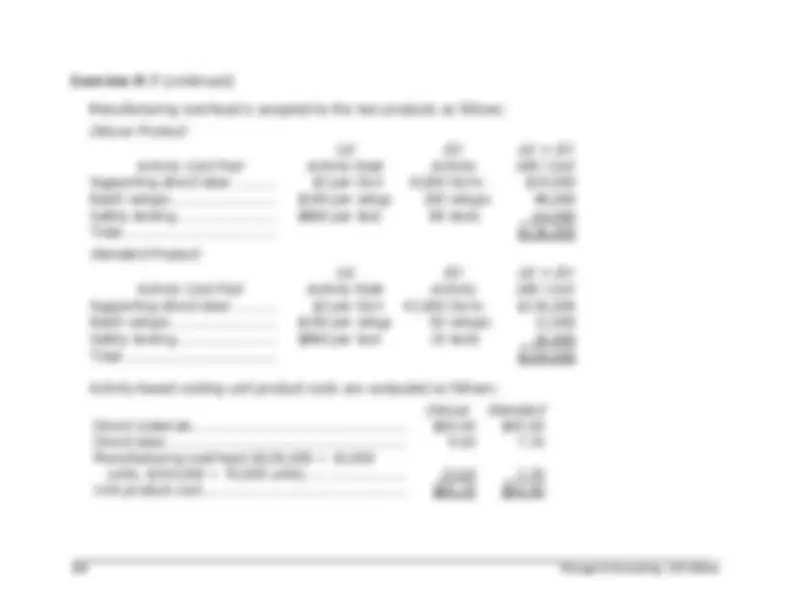
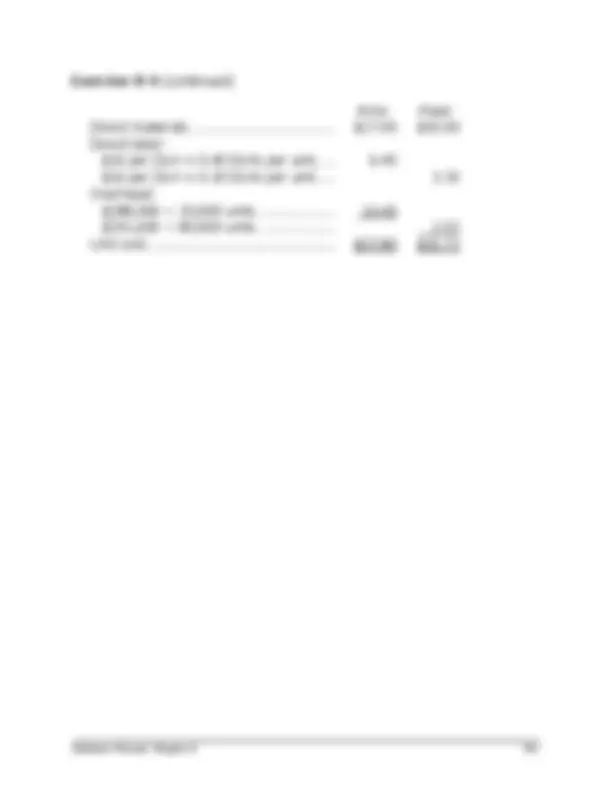
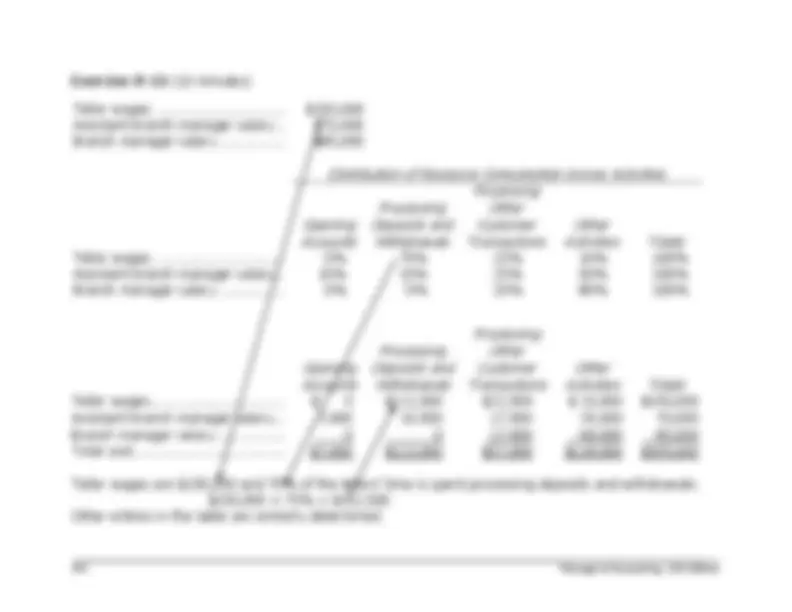
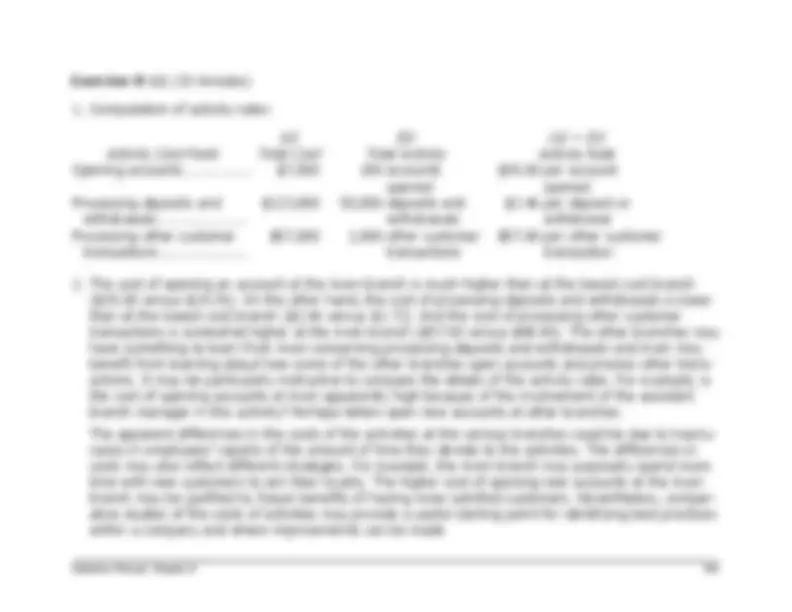
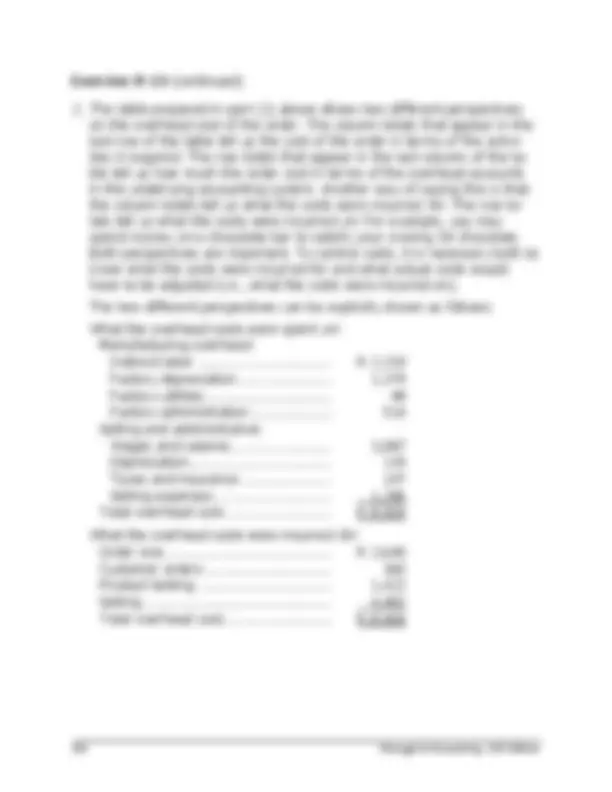
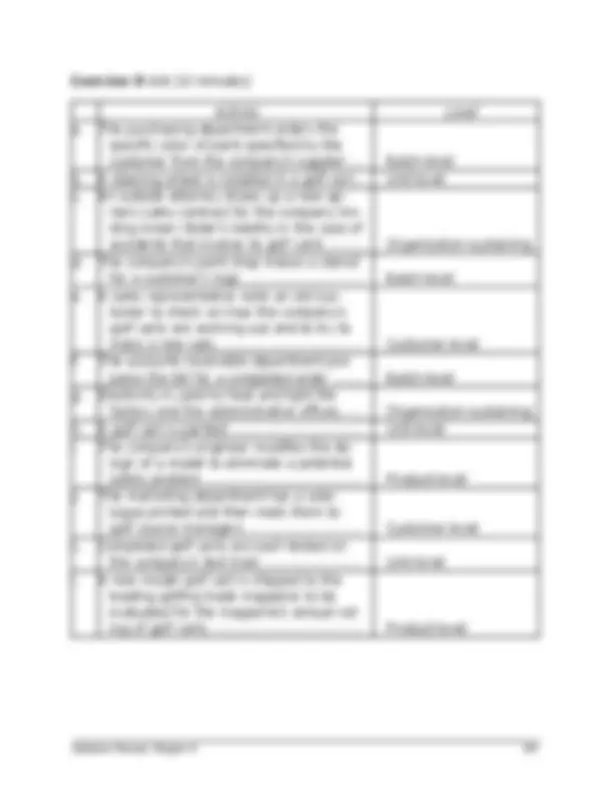
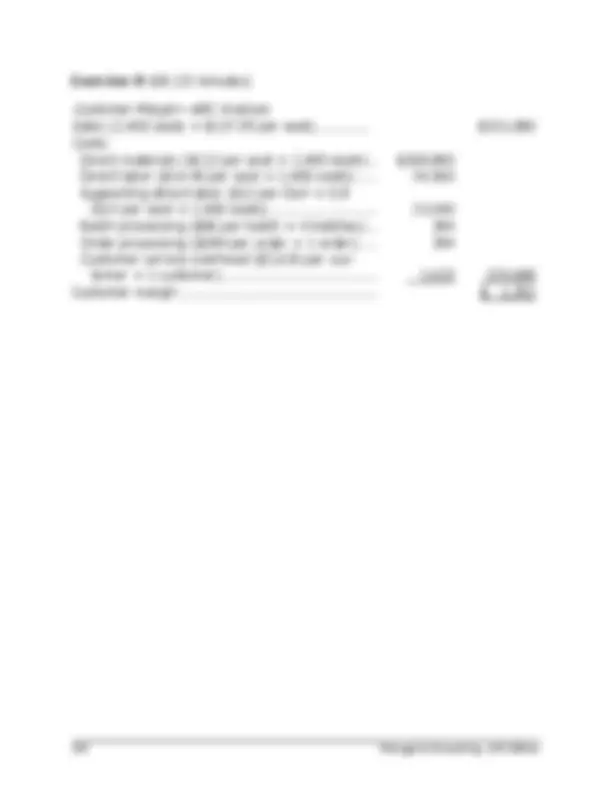
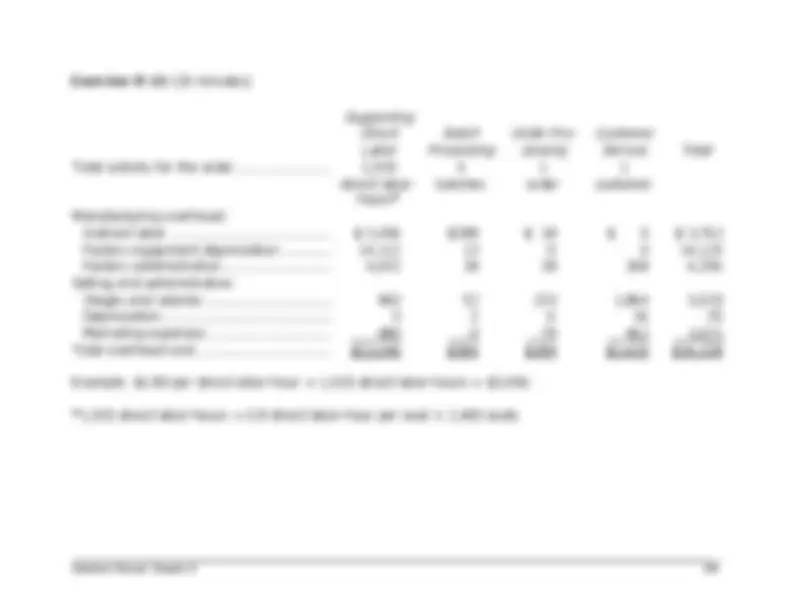
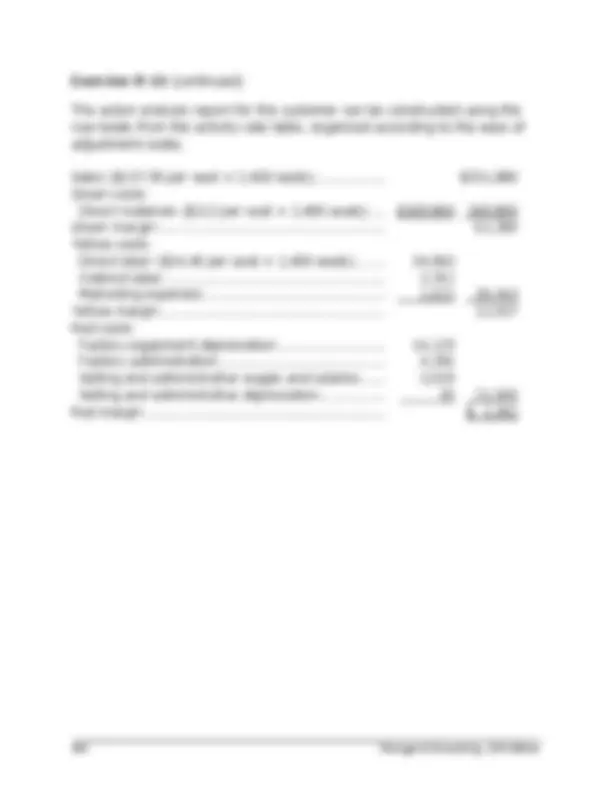
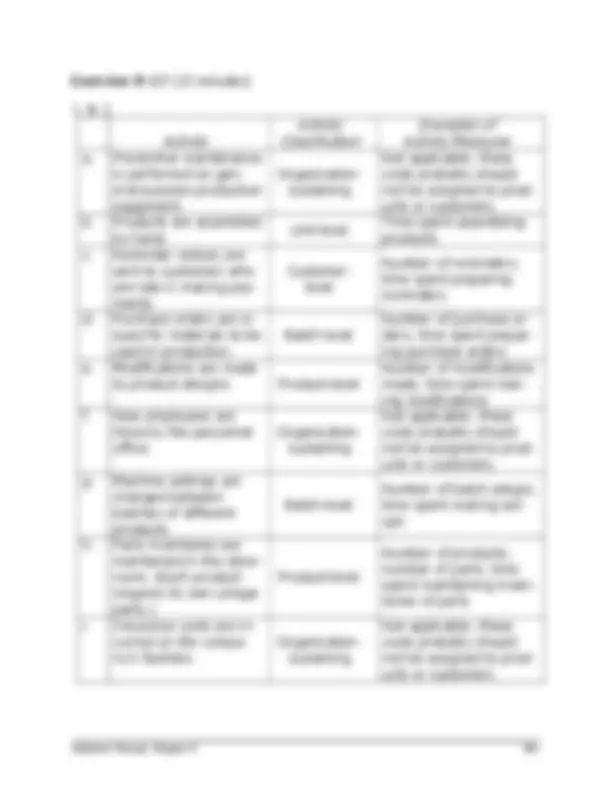
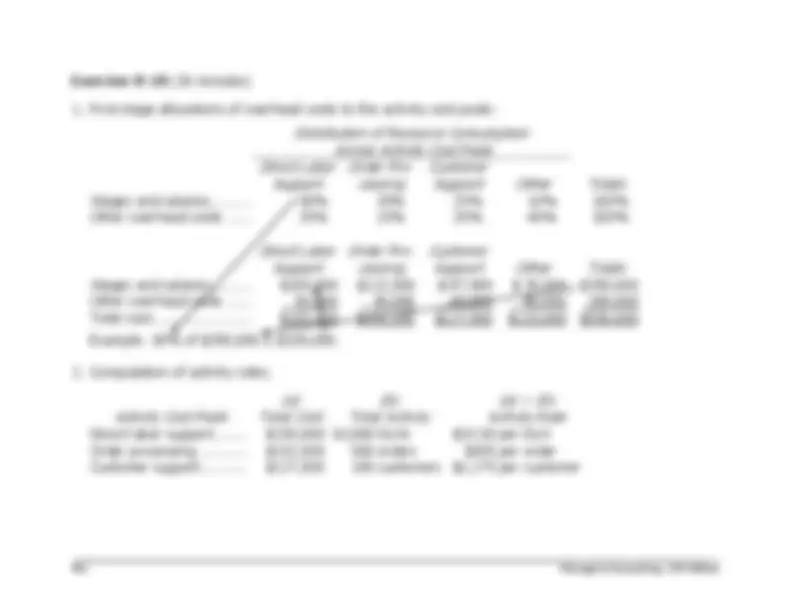
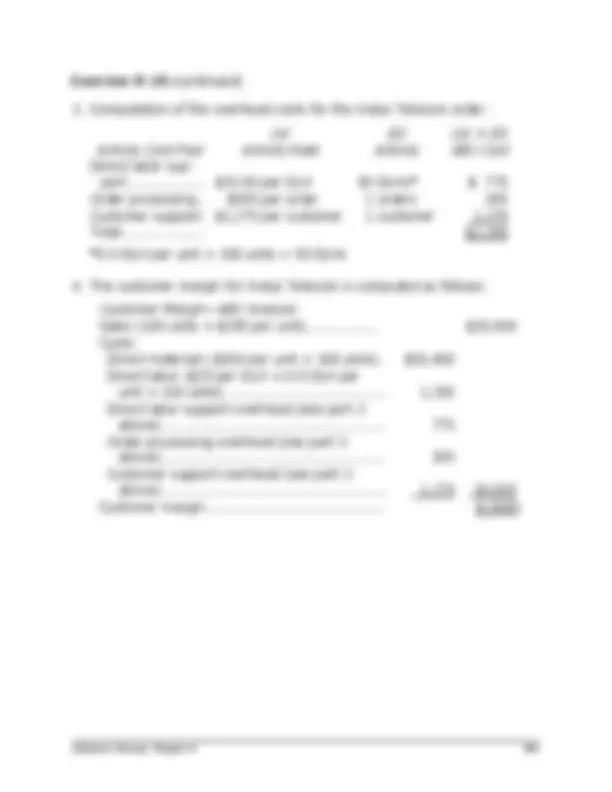
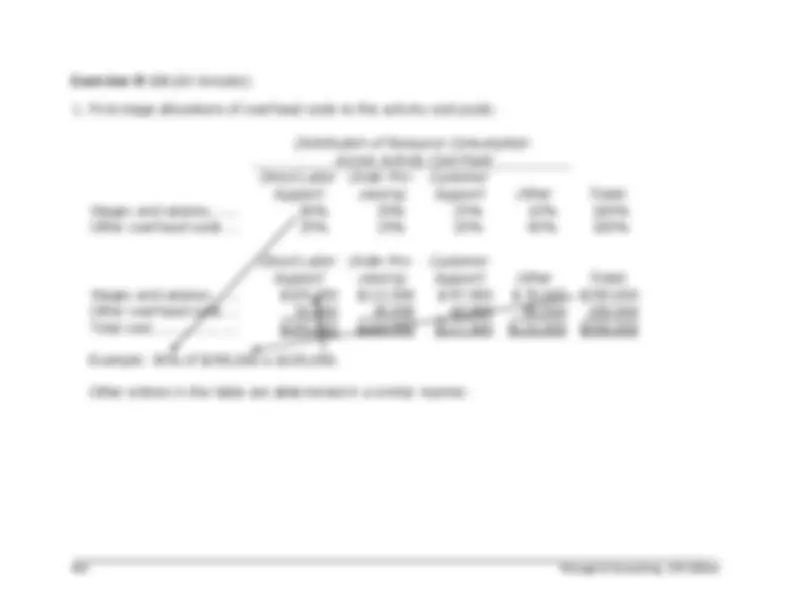
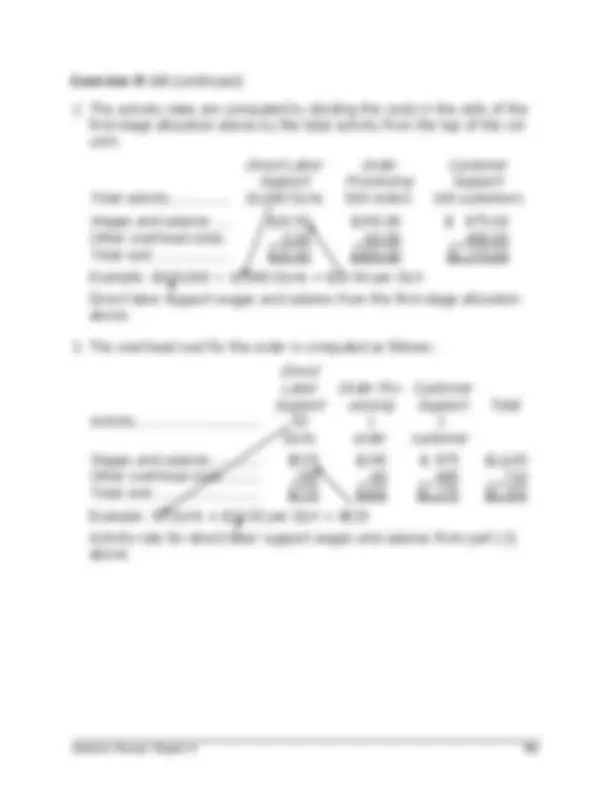
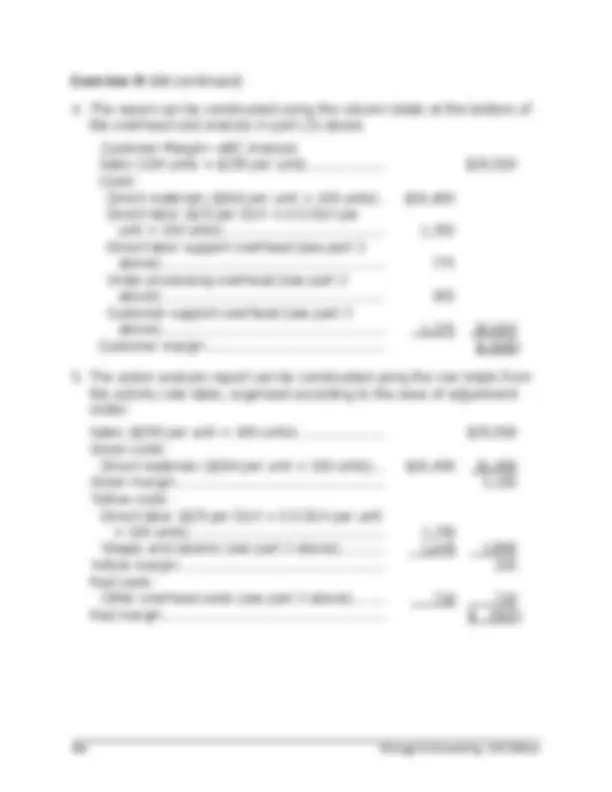
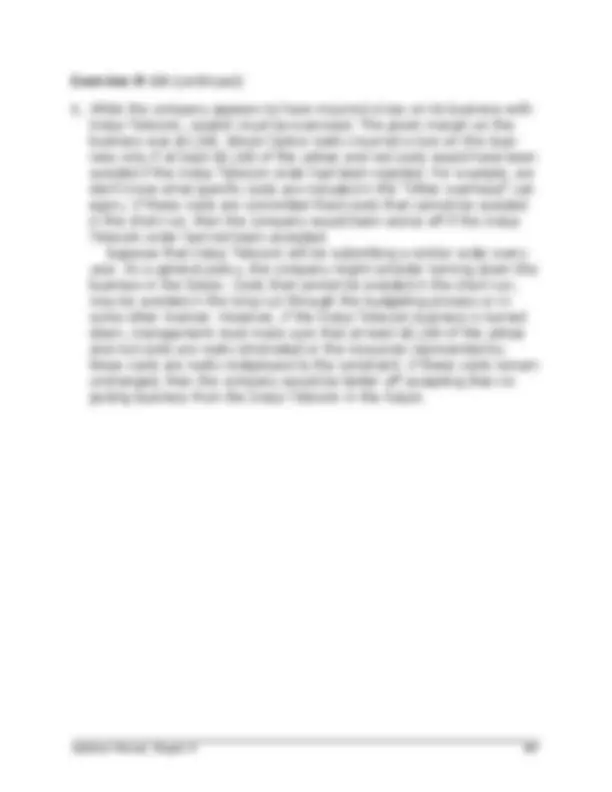
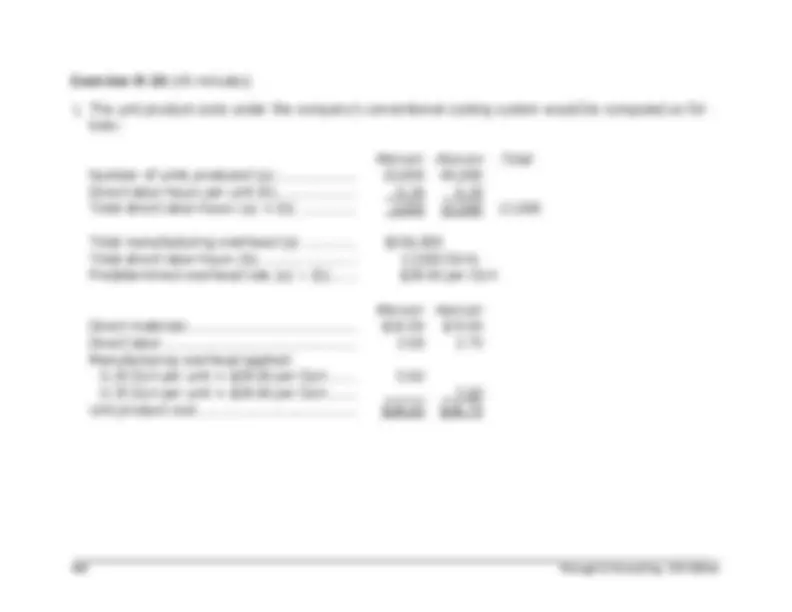
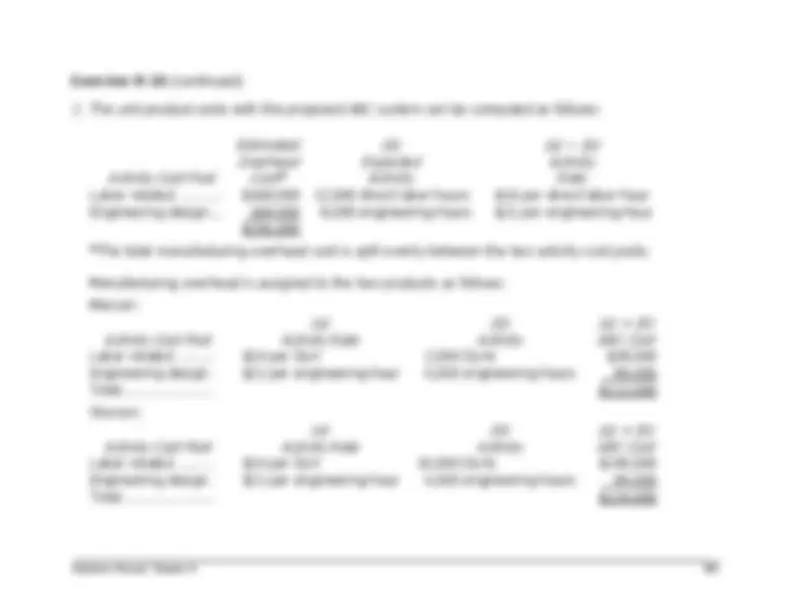

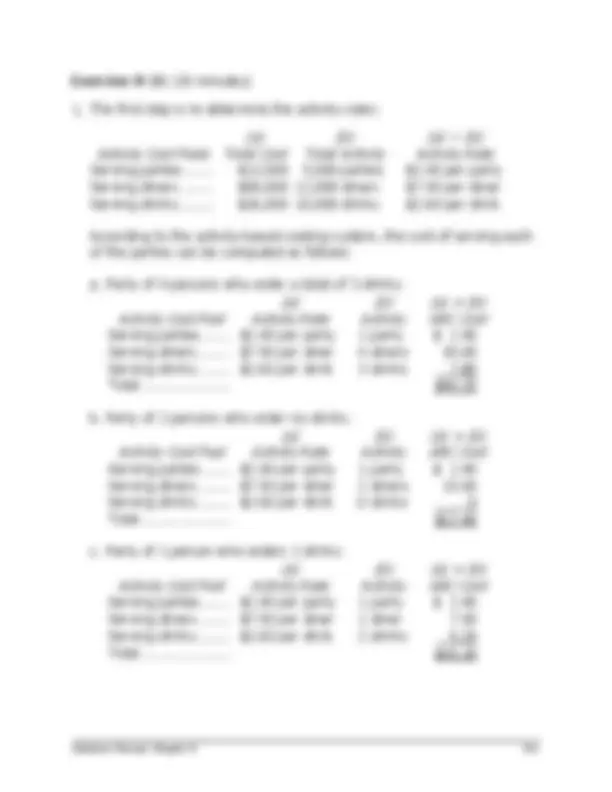
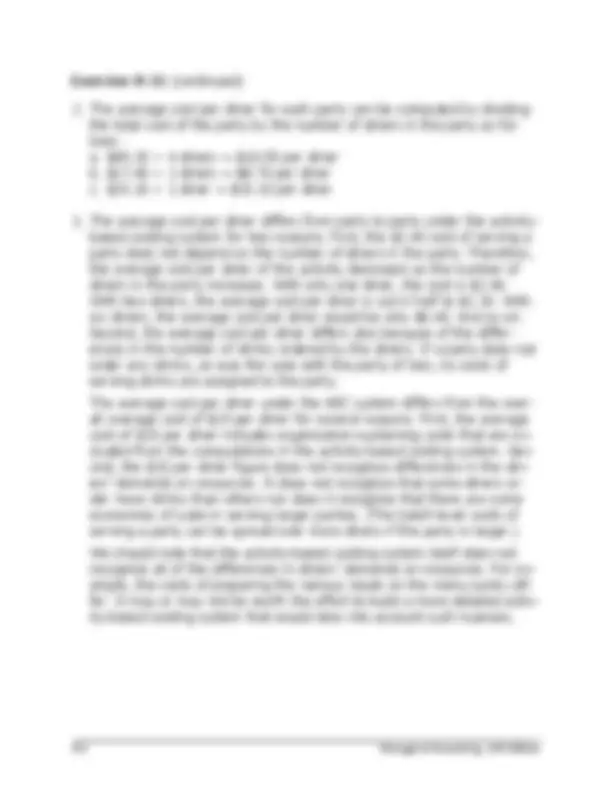
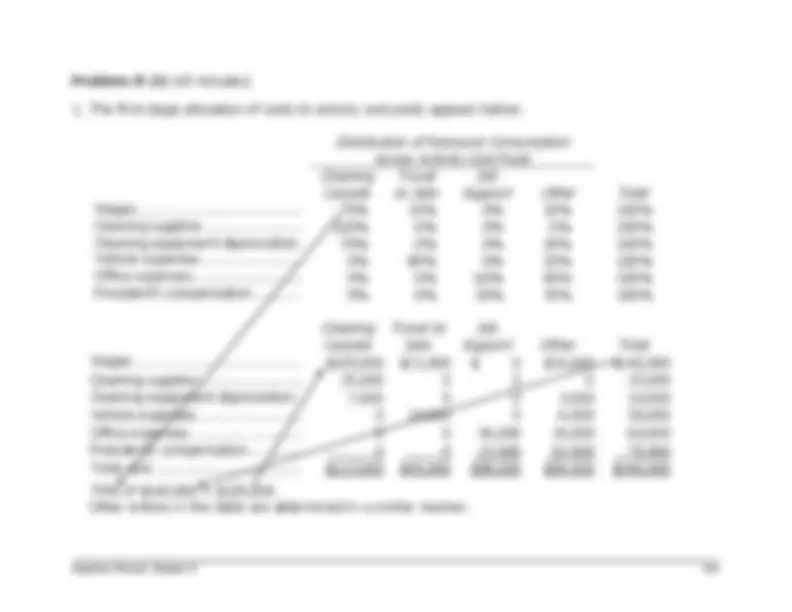
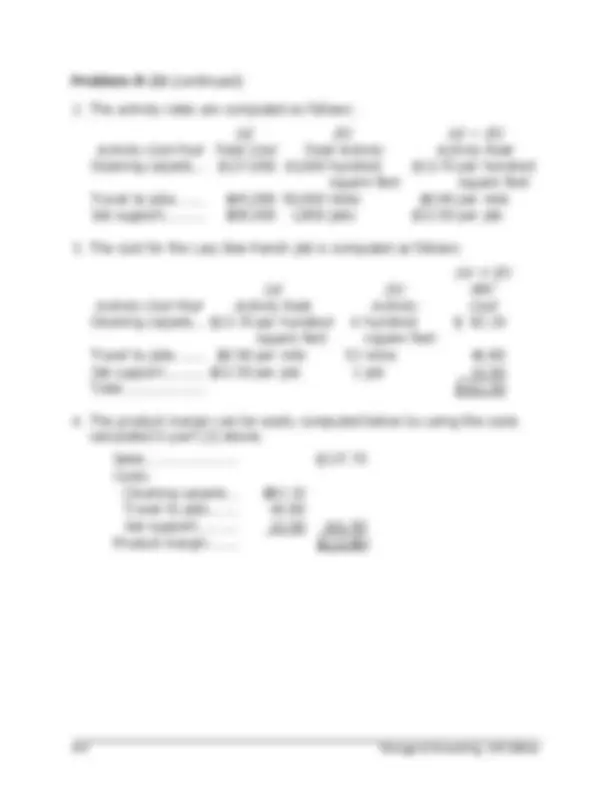
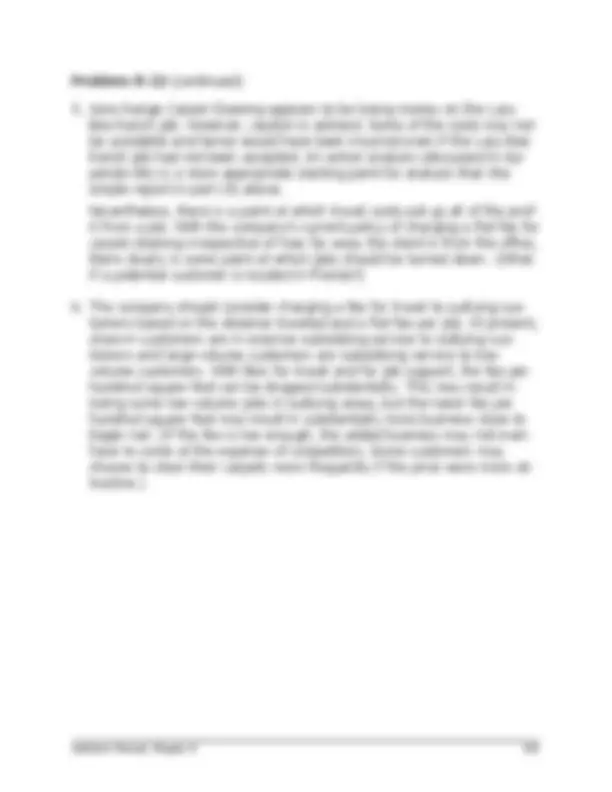
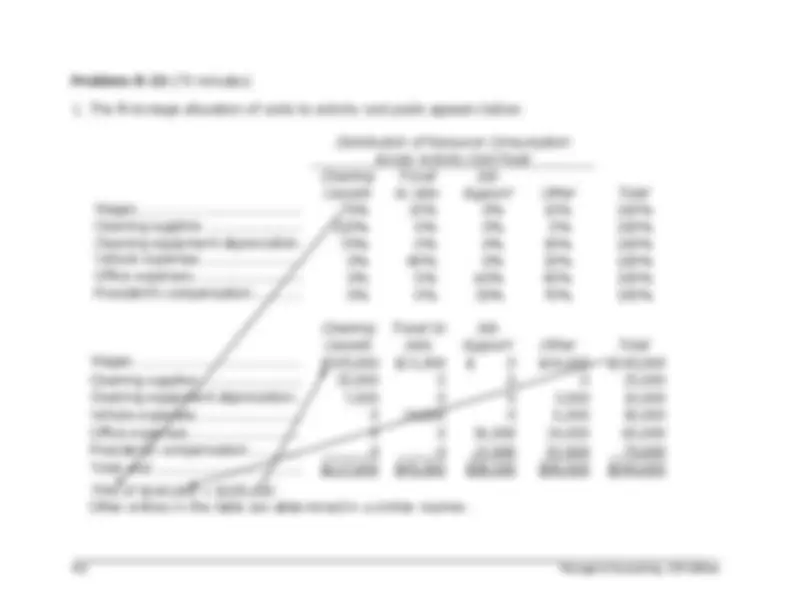
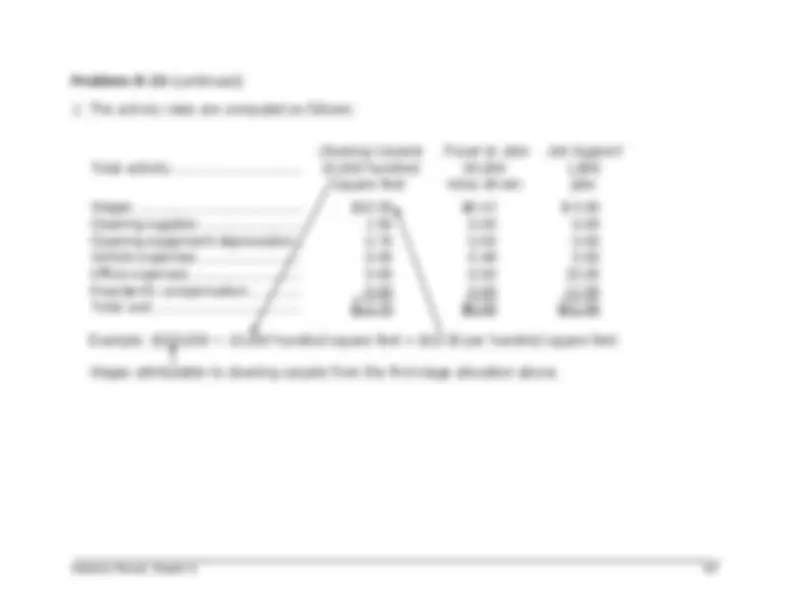
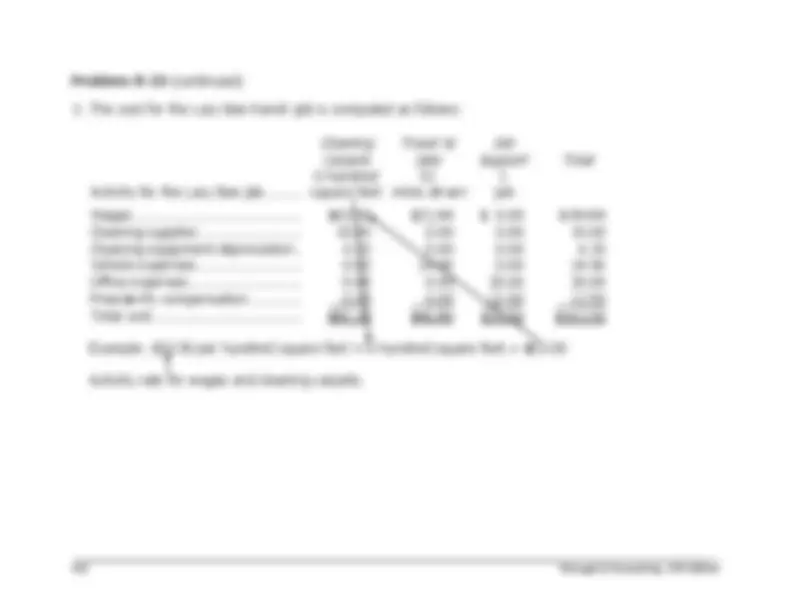
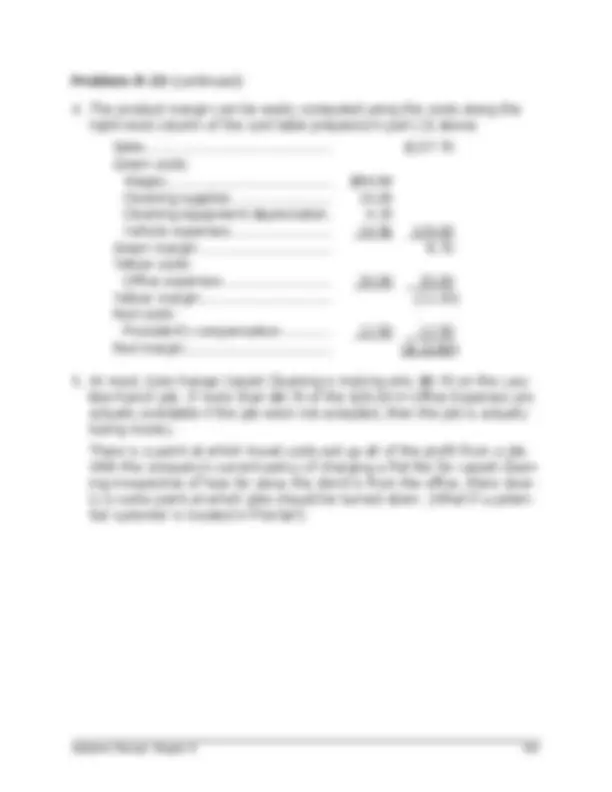
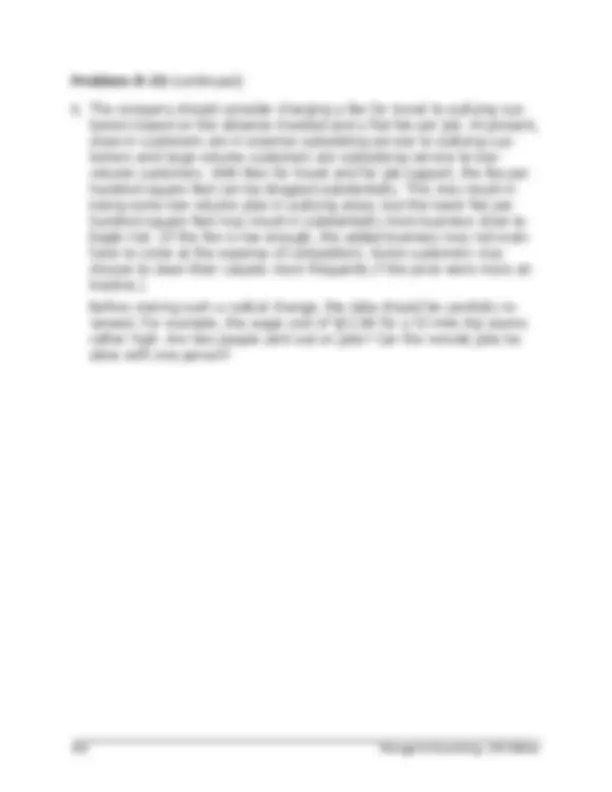
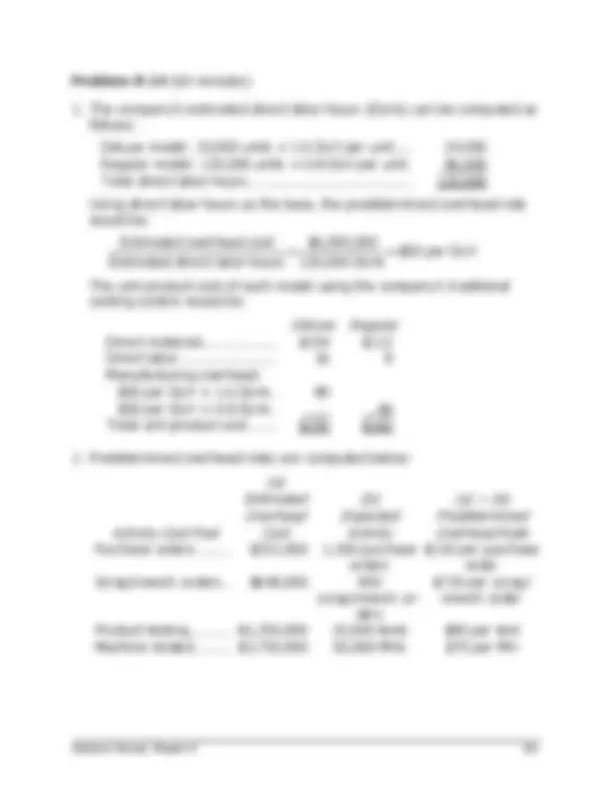
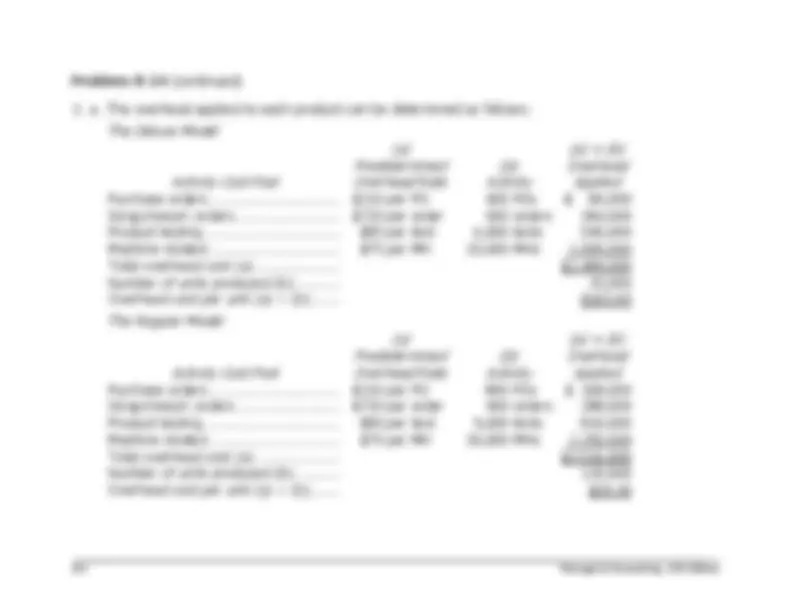
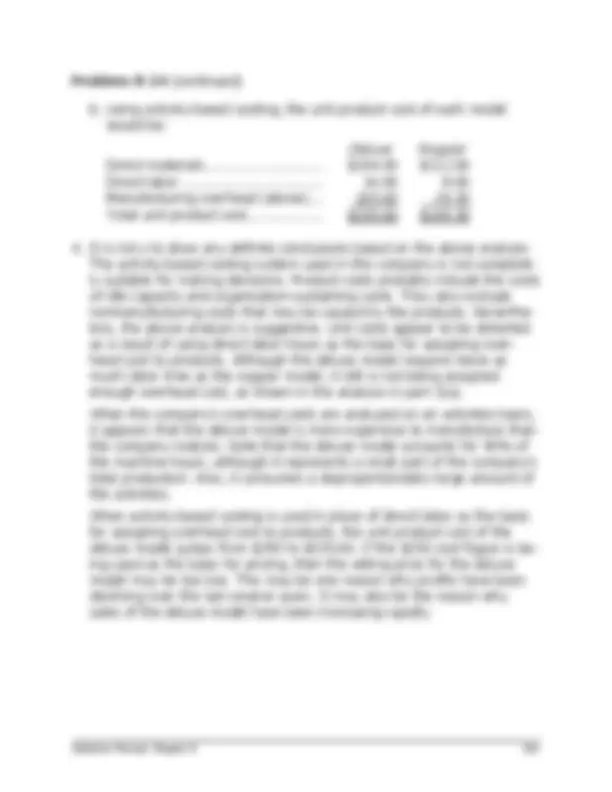
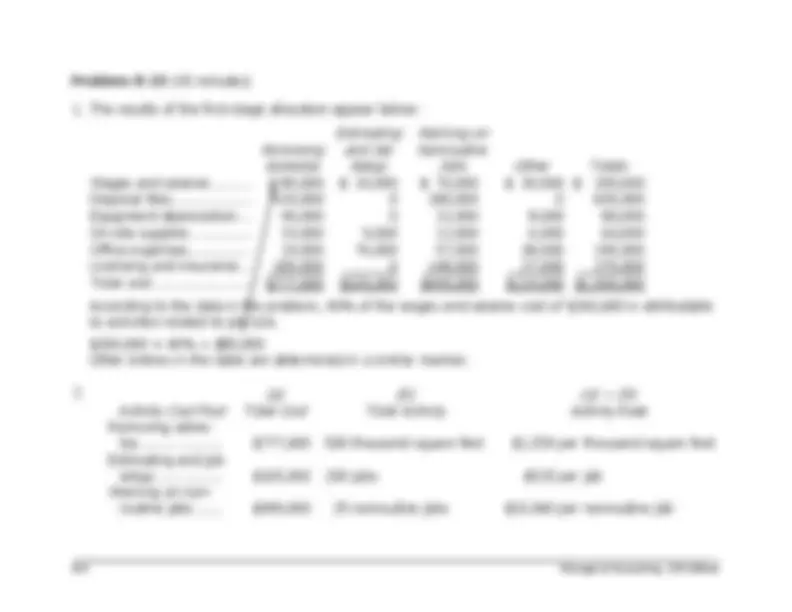

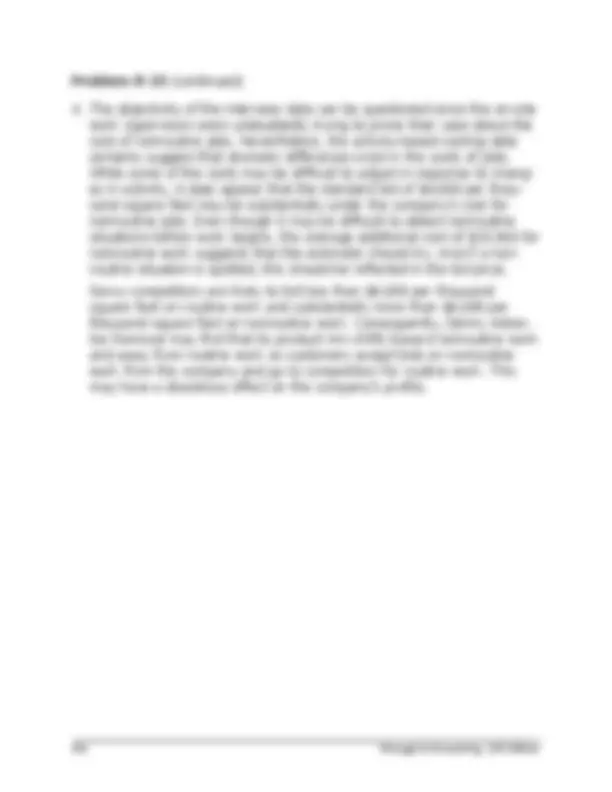
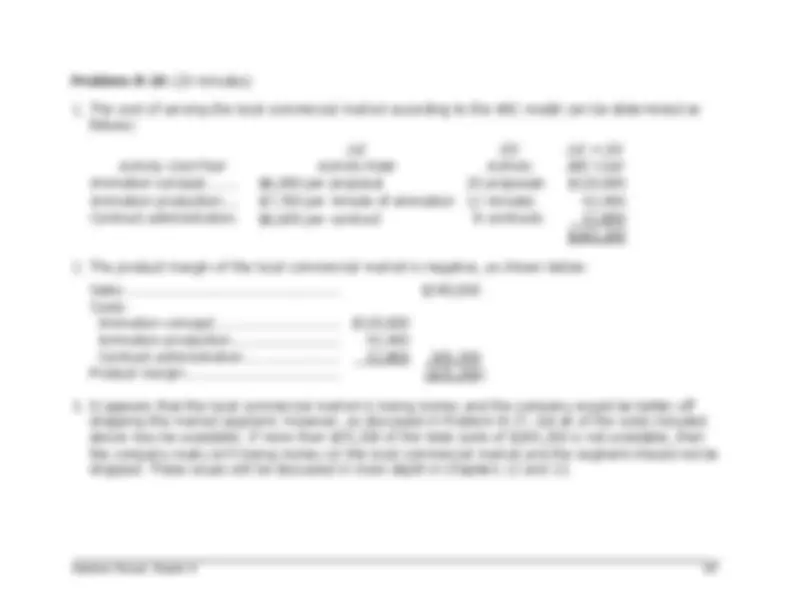
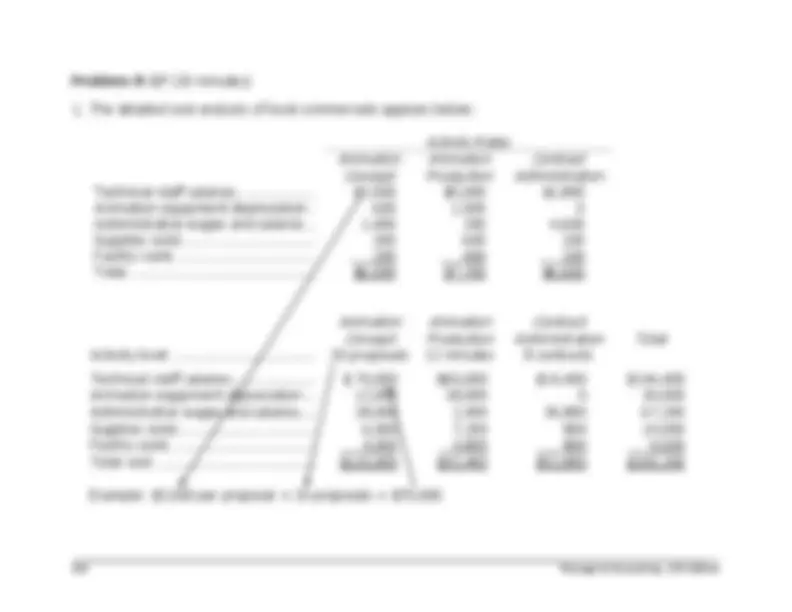
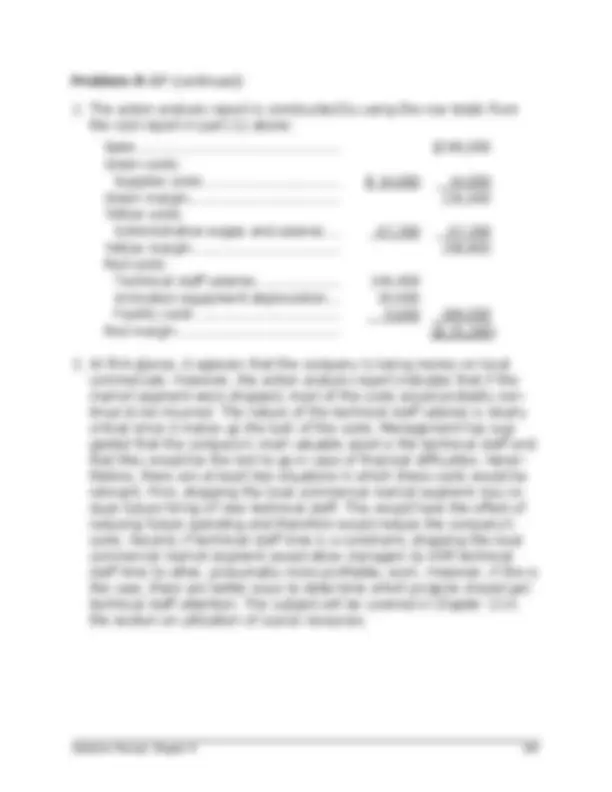
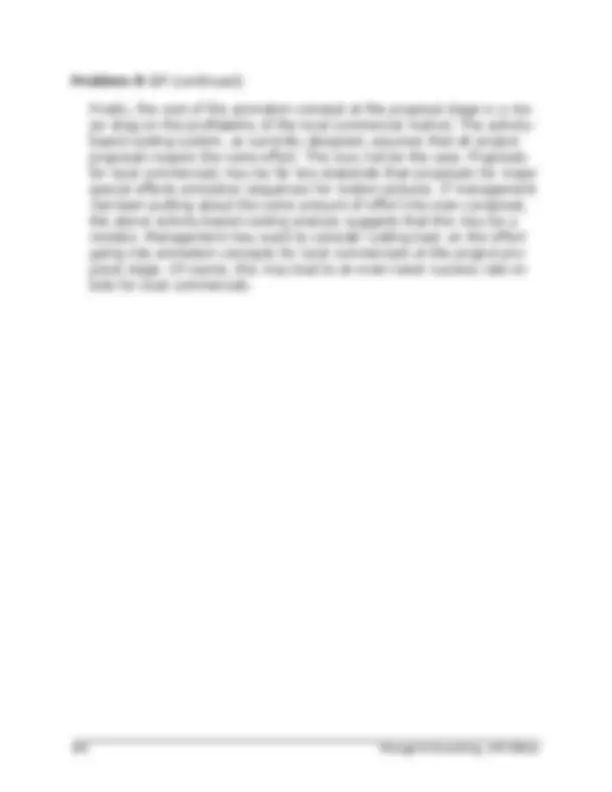
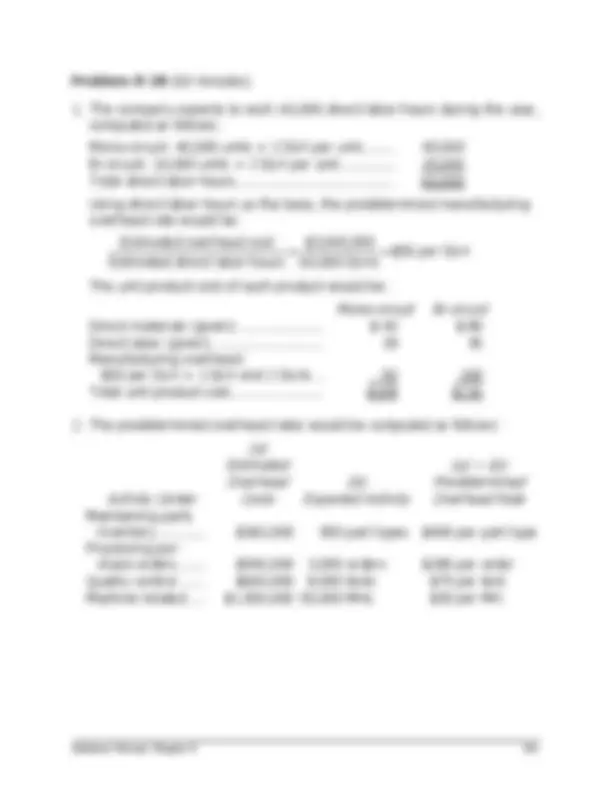
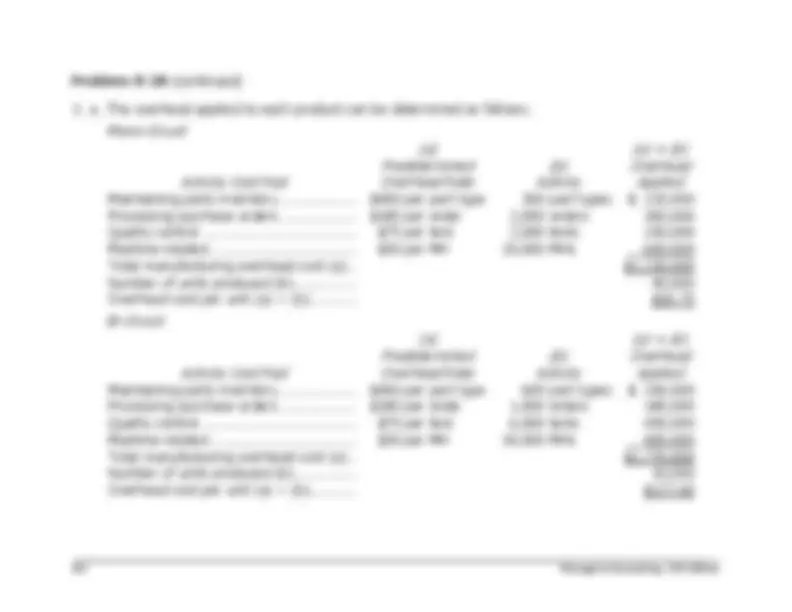
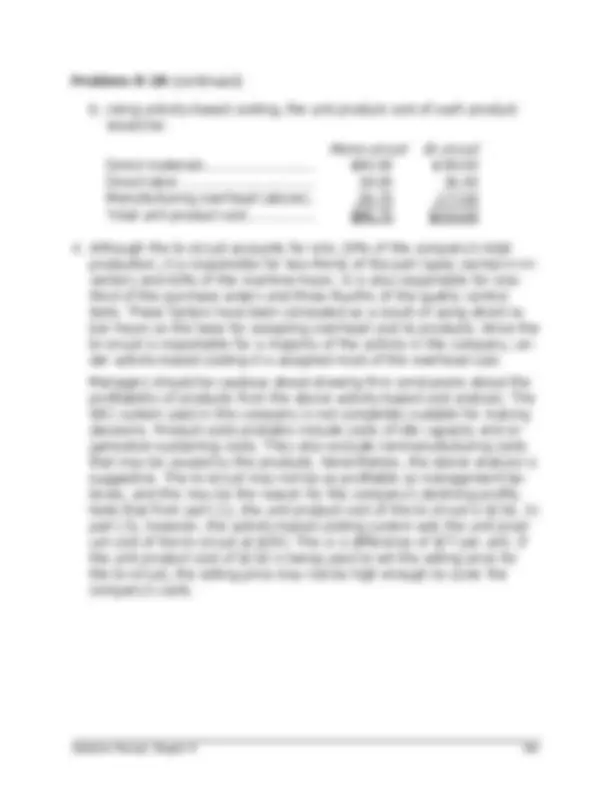
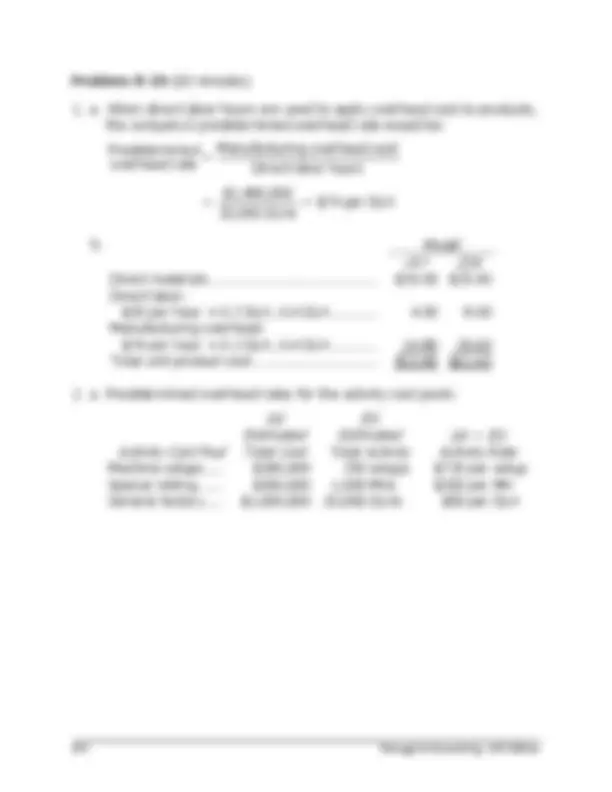
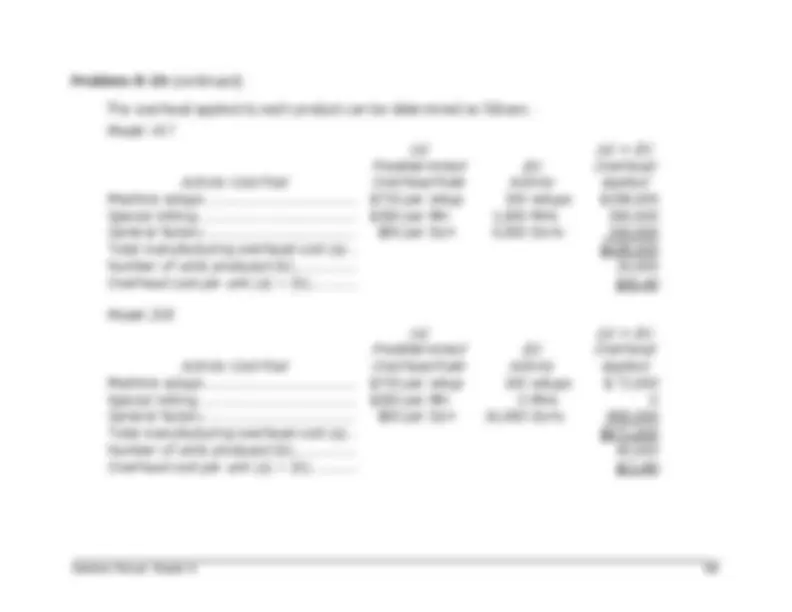
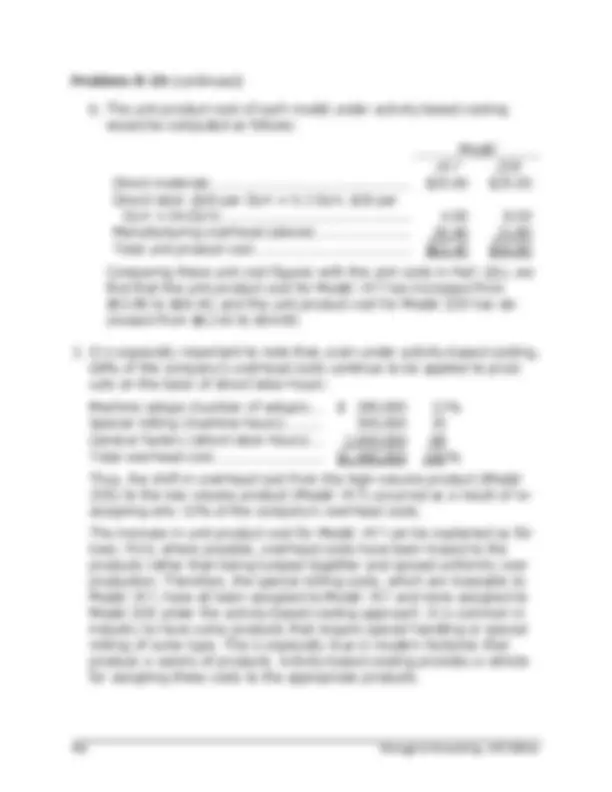
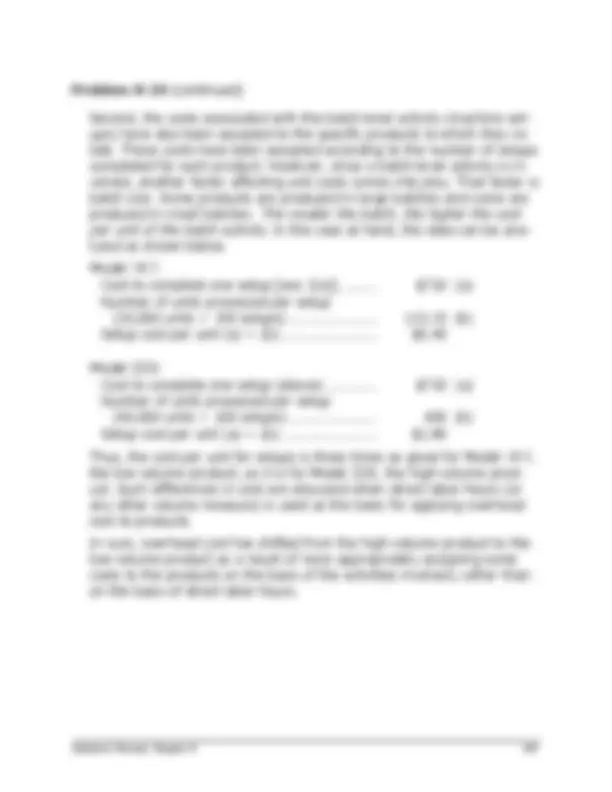
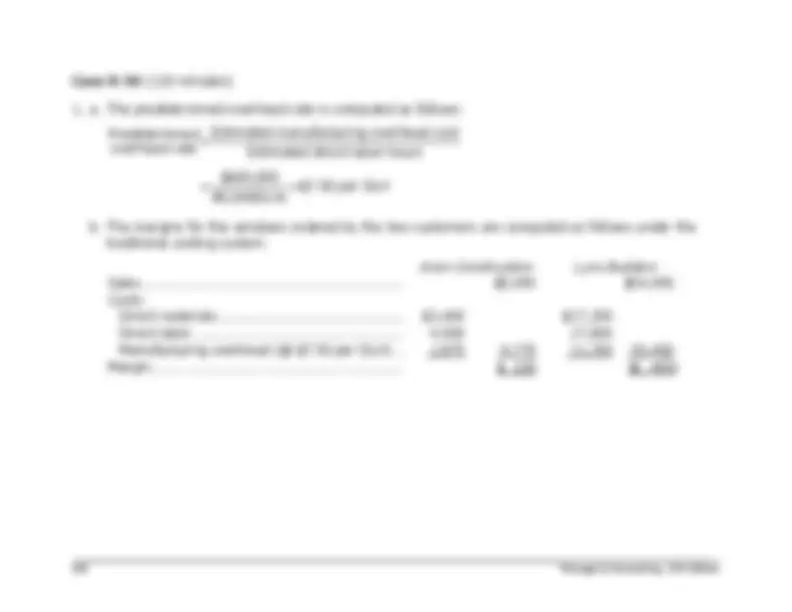
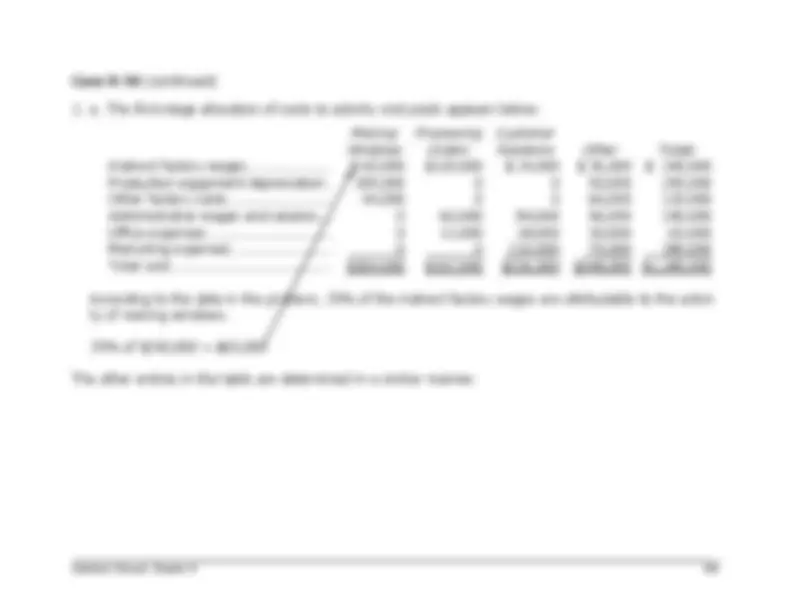
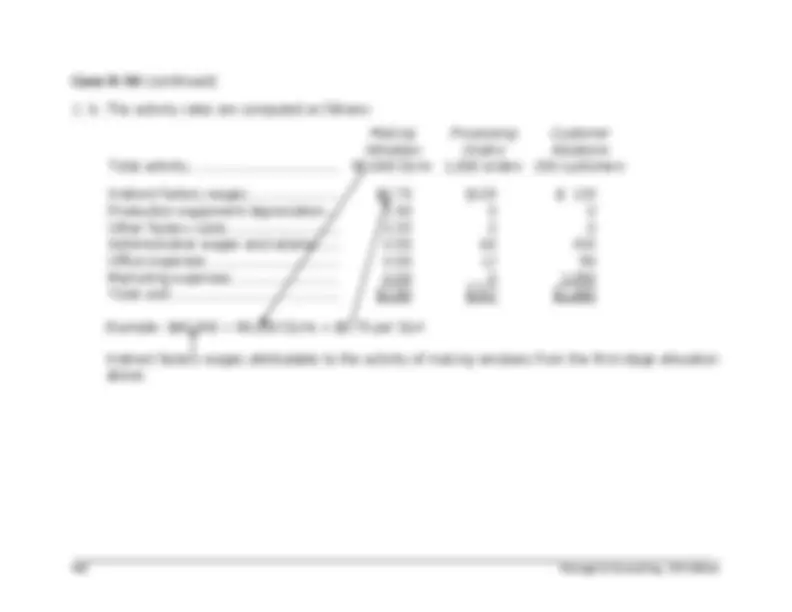
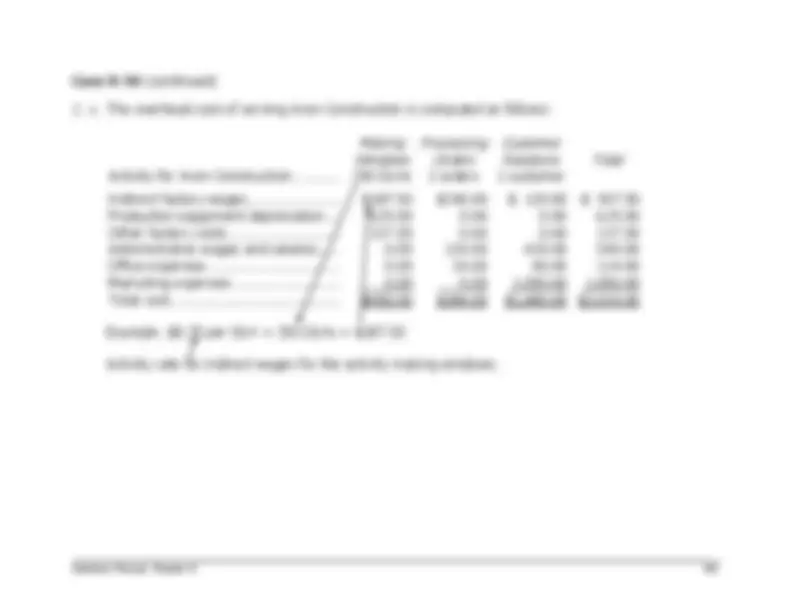
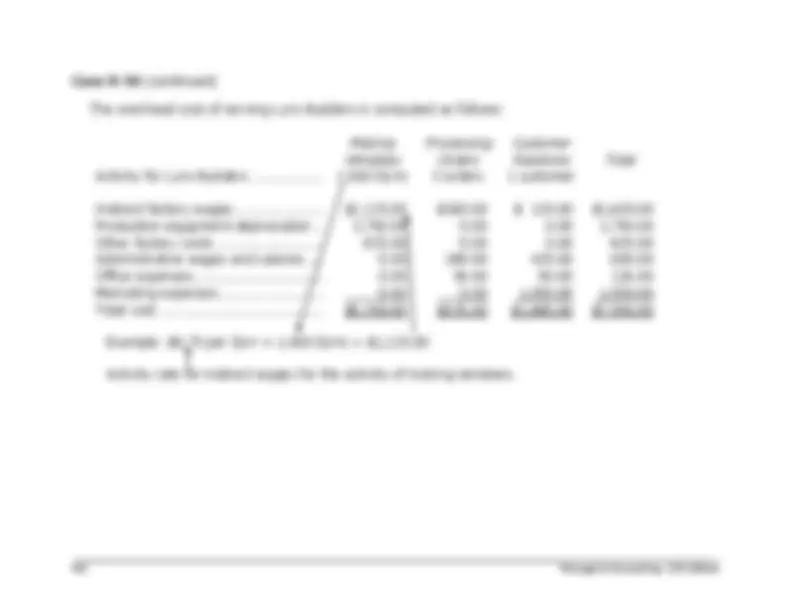
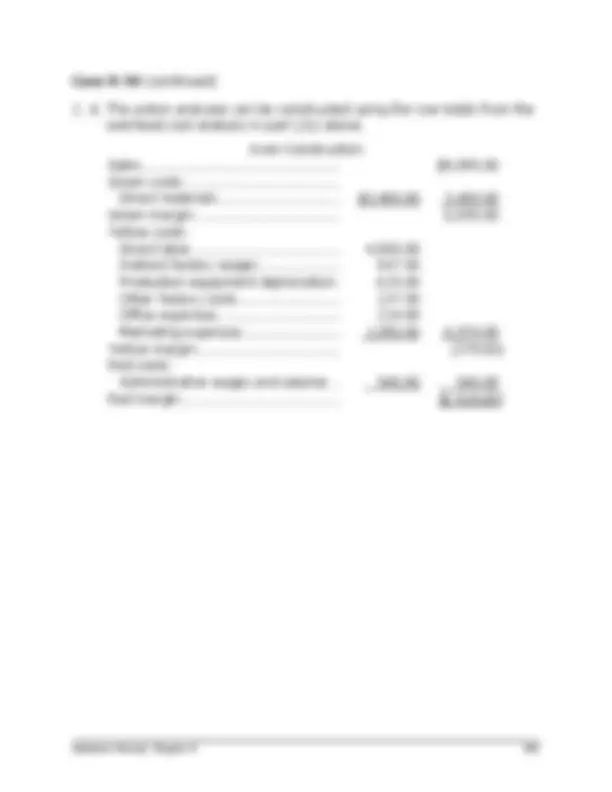
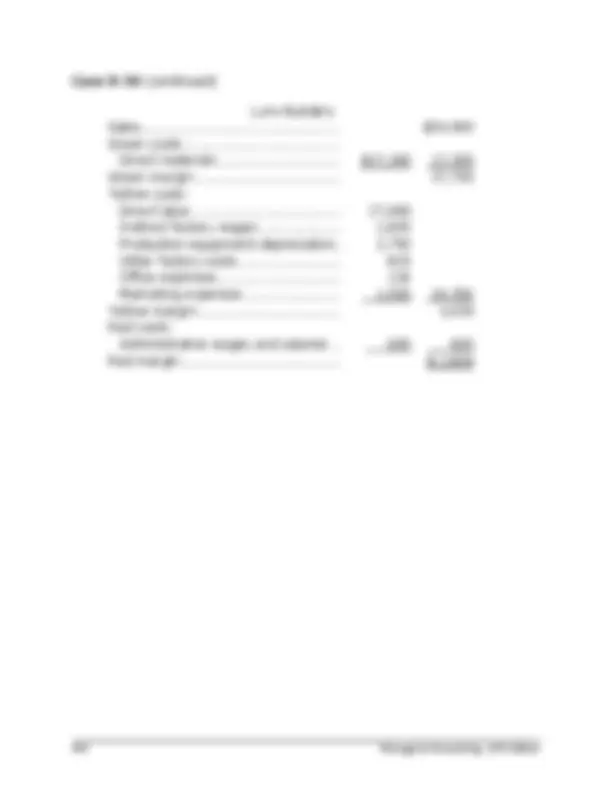
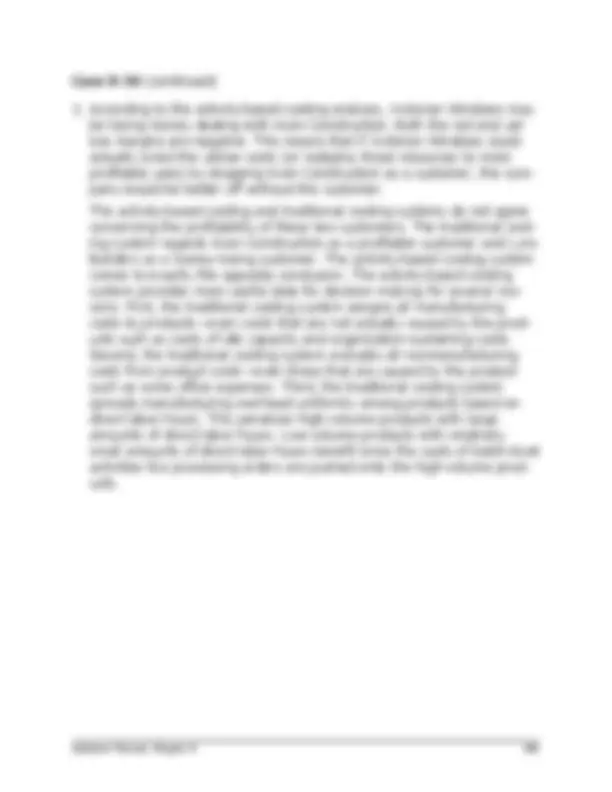

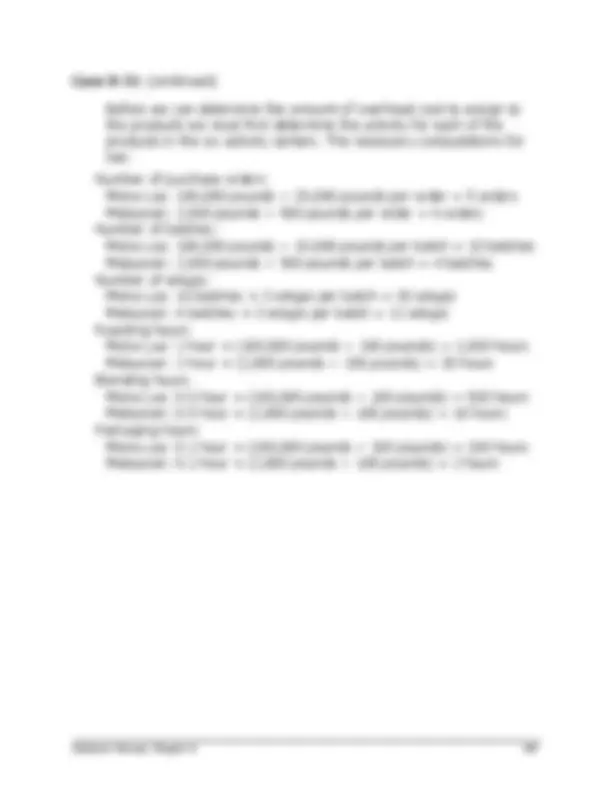
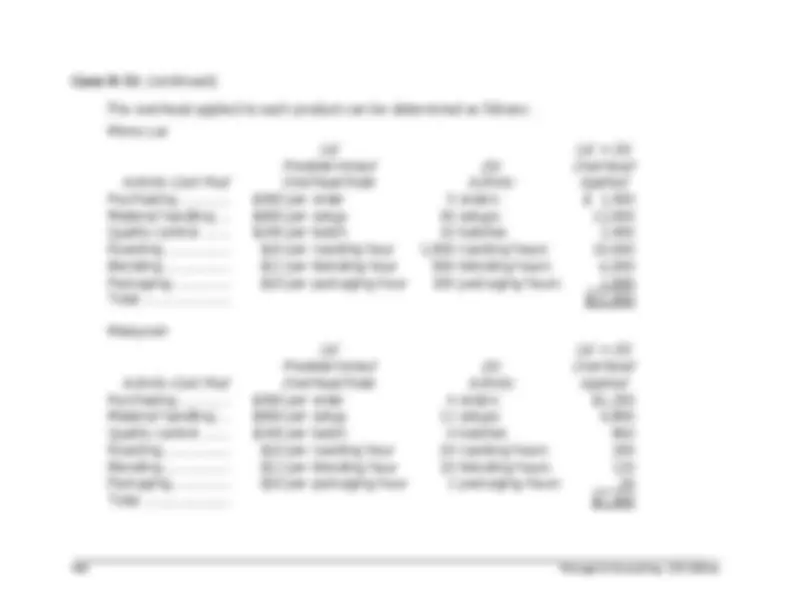
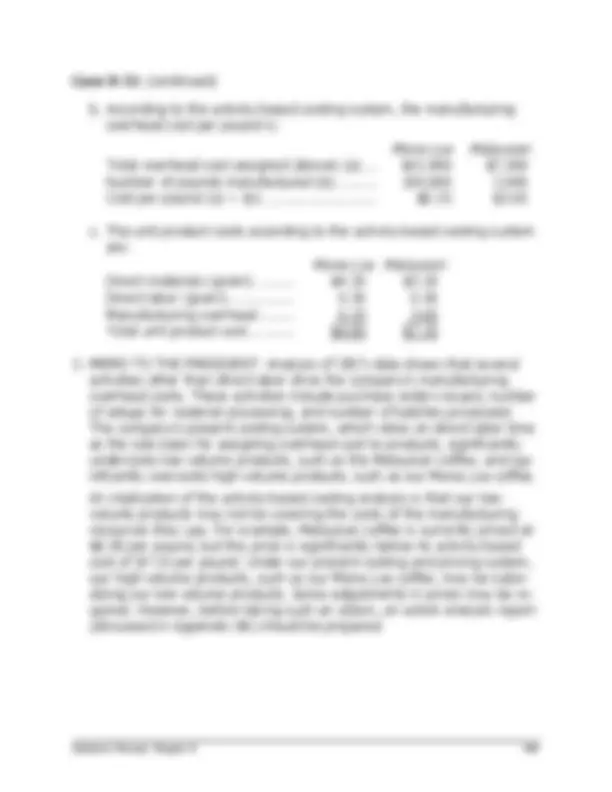
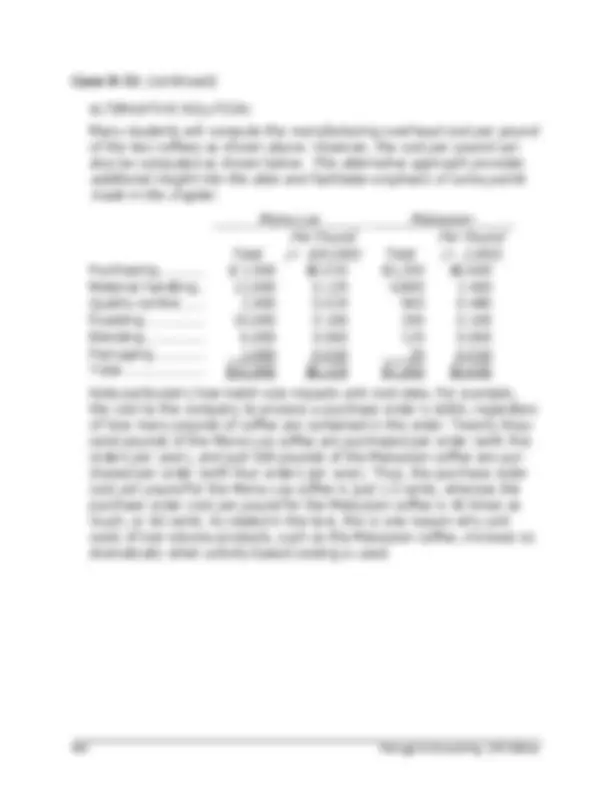
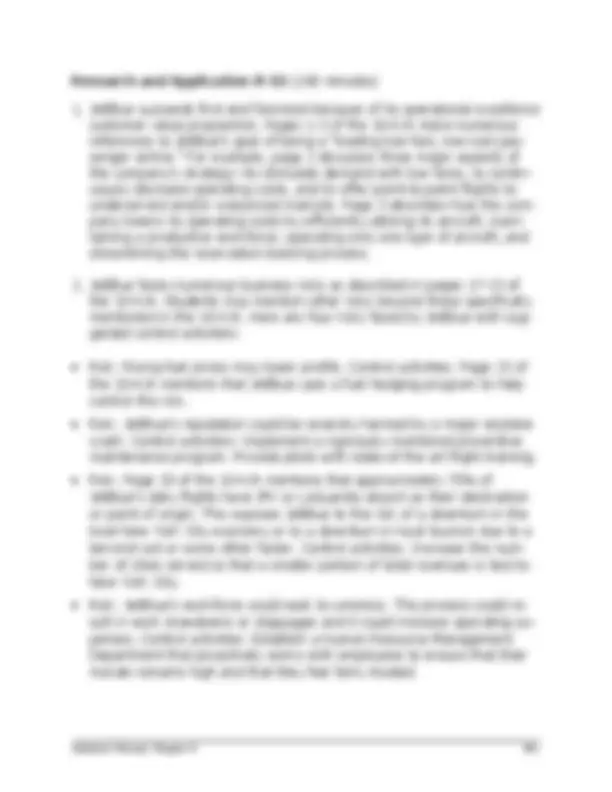
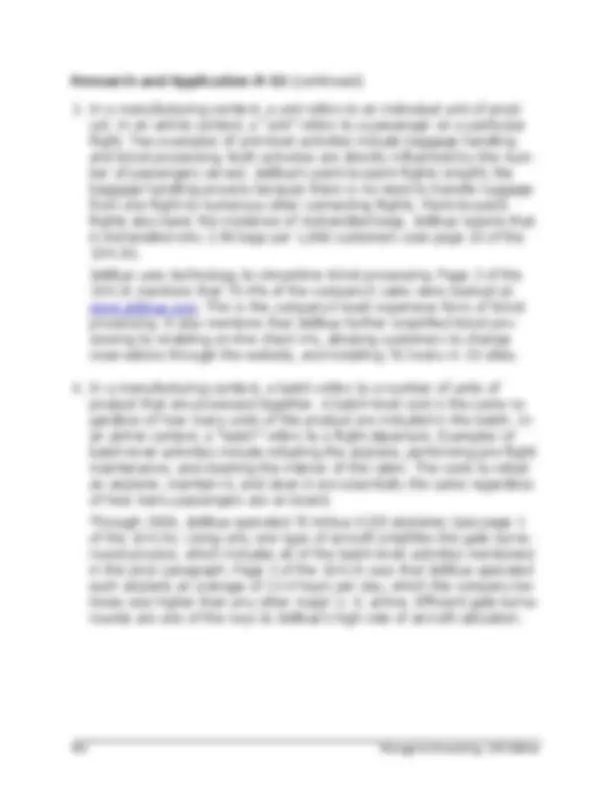
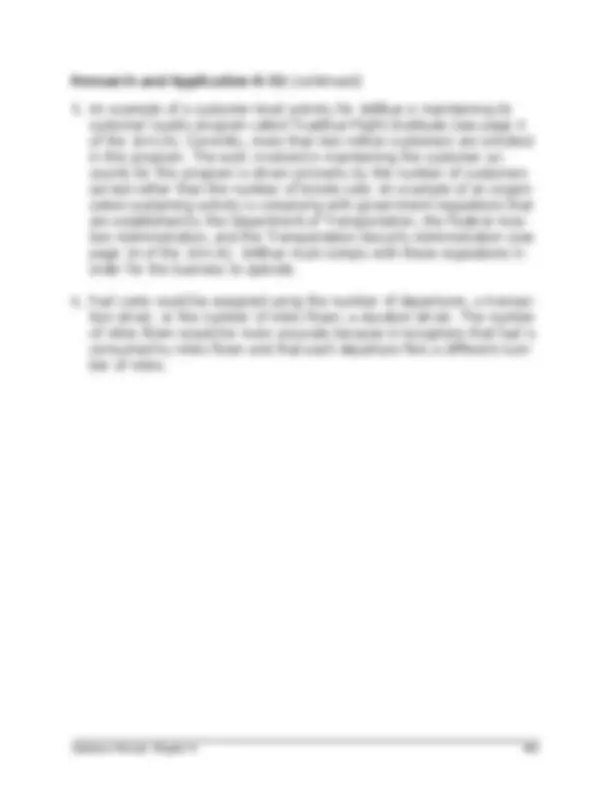
Study with the several resources on Docsity
Earn points by helping other students or get them with a premium plan
Prepare for your exams
Study with the several resources on Docsity
Earn points to download
Earn points by helping other students or get them with a premium plan
Community
Ask the community for help and clear up your study doubts
Discover the best universities in your country according to Docsity users
Free resources
Download our free guides on studying techniques, anxiety management strategies, and thesis advice from Docsity tutors
Chapter 8: Activity-Based Costing: A Tool to Aid Decision Making
Typology: Exercises
1 / 75
This page cannot be seen from the preview
Don't miss anything!
Solutions Manual, Chapter 8 379
Solutions to Questions
8-1 Activity-based costing differs from tradi- tional costing systems in a number of ways. In activity-based costing, nonmanufacturing as well as manufacturing costs may be assigned to prod- ucts. And, some manufacturing costs—including the costs of idle capacity--may be excluded from product costs. An activity-based costing system typically includes a number of activity cost pools, each of which has its unique measure of activity. These measures of activity often differ from the allocation bases used in traditional costing sys- tems.
8-2 When direct labor is used as an allocation base for overhead, it is implicitly assumed that overhead cost is directly proportional to direct labor. When cost systems were originally devel- oped in the 1800s, this assumption may have been reasonably accurate. However, direct labor has declined in importance over the years while overhead has been increasing. This suggests that there is no longer a direct link between the level of direct labor and overhead. Indeed, when a company automates, direct labor is replaced by machines; a decrease in direct labor is accompa- nied by an increase in overhead. This violates the assumption that overhead cost is directly propor- tional to direct labor. Overhead cost appears to be driven by factors such as product diversity and complexity as well as by volume, for which direct labor has served as a convenient measure.
8-3 Employees may resist activity-based cost- ing because it changes the “rules of the game.” ABC changes some of the key measures, such as product costs, used in making decisions and may affect how individuals are evaluated. Without top management support, employees may have little interest in making these changes. In addition, if top managers continue to make decisions based
on the numbers generated by the traditional cost- ing system, subordinates will quickly conclude that the activity-based costing system can be ig- nored. 8-4 Unit-level activities are performed for each unit that is produced. Batch-level activities are performed for each batch regardless of how many units are in the batch. Product-level activi- ties must be carried out to support a product re- gardless of how many batches are run or units produced. Customer-level activities must be car- ried out to support customers regardless of what products or services they buy. Organization- sustaining activities are carried out regardless of the company’s precise product mix or mix of cus- tomers.
8-5 Organization-sustaining costs, customer- level costs, and the costs of idle capacity should not be assigned to products. These costs repre- sent resources that are not consumed by the products. 8-6 In activity-based costing, costs must first be allocated to activity cost pools and then they are allocated from the activity cost pools to prod- ucts, customers, and other cost objects. 8-7 Since people are often involved in more than one activity, some way must be found to estimate how much time they spend in each ac- tivity. The most practical approach is often to ask employees how they spend their time. It is also possible to ask people to keep records of how they spend their time or observe them as they perform their tasks, but both of these alternatives are costly and it is not obvious that the data would be any better. People who know they are being observed may change how they behave.
380 Managerial Accounting, 12th Edition
8-8 In traditional cost systems, product-level costs are indiscriminately spread across all prod- ucts using direct labor-hours or some other allo- cation base related to volume. As a consequence, high-volume products are assigned the bulk of such costs. If a product is responsible for 40% of the direct labor in a factory, it will be assigned 40% of the manufacturing overhead cost in the factory—including 40% of the product-level costs of low-volume products. In an activity-based cost- ing system, batch-level and product-level costs are assigned more appropriately. This results in shifting product-level costs back to the products that cause them and away from the high-volume products. (A similar effect will be observed with batch-level costs if high-volume products are pro- duced in larger batches than low-volume prod- ucts.)
8-9 Activity rates tell managers the average cost of resources consumed to carry out a par- ticular activity such as processing purchase or- ders. An activity whose average cost is high may be a good candidate for process improvements. Benchmarking can be used to identify which ac- tivities have unusually large costs. If some other organization is able to carry out the activity at a significantly lower cost, it is reasonable to sup- pose that improvement may be possible.
8-10 The activity-based costing approach de- scribed in the chapter is probably unacceptable for external financial reports for two reasons. First, activity-based product costs, as described in this chapter, exclude some manufacturing costs and include some nonmanufacturing costs. Sec- ond, the first-stage allocations are based on in- terviews rather than verifiable, objective data. 8-11 While the reports in Exhibits 8-10 and 8- 11 can yield insights, they should not be used for decision making. These reports give no indication of what costs can actually be adjusted nor is there any indication of who would be responsible for adjusting the costs after a decision has been made. It would be dangerous, for example, to drop a product based solely on a report like the one in Exhibit 8-10. Most of the costs in this re- port do not automatically disappear if a product is dropped; managers must take explicit actions to eliminate resources or to redeploy resources to other uses. Managers may be reluctant to take these actions—particularly if it involves firing or transferring people. The action analysis has the advantage of making it clearer where savings have to come from and hence which managers will have to take action.
382 Managerial Accounting, 12th Edition
Travel
Pickup and Delivery
Customer Service Other Totals Driver and guard wages ......................... $336,000 $378,000 $ 84,000 $ 42,000 $ 840, Vehicle operating expense...................... 202,500 13,500 0 54,000 270, Vehicle depreciation ............................... 105,000 15,000 0 30,000 150, Customer representative salaries and expenses ............................................ 0 0 153,000 27,000 180, Office expenses ..................................... 0 10,000 14,000 16,000 40, Administrative expenses......................... 0 17,000 187,000 136,000 340, Total cost .............................................. $643,500 $433,500 $438,000 $305,000 $1,820,
Each entry in the table is derived by multiplying the total cost for the cost category by the percentage taken from the table below that shows the distribution of resource consumption:
Travel
Pickup and Delivery
Customer Service Other Totals Driver and guard wages ......................... 40% 45% 10% 5% 100% Vehicle operating expense...................... 75% 5% 0% 20% 100% Vehicle depreciation ............................... 70% 10% 0% 20% 100% Customer representative salaries and expenses ............................................ 0% 0% 85% 15% 100% Office expenses ..................................... 0% 25% 35% 40% 100% Administrative expenses......................... 0% 5% 55% 40% 100%
Solutions Manual, Chapter 8 383
Activity Cost Pool
Estimated Overhead Cost Expected Activity Activity Rate Caring for lawn $77,400 180,000 square feet of lawn $0.43 per square foot of lawn Caring for garden beds– low maintenance
$30,000 24,000 square feet of low maintenance beds
$1.25 per square foot of low maintenance beds Caring for garden beds– high maintenance
$57,600 18,000 square feet of high maintenance beds
$3.20 per square foot of high maintenance beds Travel to jobs $4,200 15,000 miles $0.28 per mile Customer billing and service $8,700 30 customers $290 per customer
The activity rate for each activity cost pool is computed by dividing its estimated overhead cost by its expected activity.
Solutions Manual, Chapter 8 385
Sales ($1,650 per standard model glider × 10 stand- ard model gliders + $2,300 per custom designed glider × 2 custom designed gliders) ...................... $21, Costs: Direct materials ($462 per standard model glider × 10 standard model gliders + $576 per custom designed glider × 2 custom designed gliders) ..... $5, Direct labor ($19 per direct labor-hour × 28.5 direct labor-hours per standard model glider × 10 standard model gliders + $19 per direct labor- hour × 32 direct labor-hours per custom designed glider × 2 custom designed gliders).................... 6, Supporting manufacturing ($18 per direct labor- hour × 28.5 direct labor-hours per standard mod- el glider × 10 standard model gliders + $18 per direct labor-hour × 32 direct labor-hours per cus- tom designed glider × 2 custom designed gliders) ........................................................................ 6, Order processing ($192 per order × 3 orders) ....... 576 Custom designing ($261 per custom design × 2 custom designs) ................................................ 522 Customer service ($426 per customer × 1 customer) ...................................................... 426 20, Customer margin .................................................... $ 891
386 Managerial Accounting, 12th Edition
Sales (80 clubs × $48 per club) ............................ $3,840. Green costs: Direct materials (80 clubs × $25.40 per club) ...... $2,032.00 2,032. Green margin ...................................................... 1,808. Yellow costs: Direct labor (80 clubs × 0.3 hour per club × $21.50 per hour) ............................................. 516. Indirect labor ..................................................... 90. Marketing expenses ........................................... 540.20 1,146. Yellow margin...................................................... 661. Red costs: Factory equipment depreciation .......................... 106. Factory administration ........................................ 262. Selling and administrative wages and salaries ...... 436. Selling and administrative depreciation................ 30.00 834. Red margin ......................................................... ($ 173.00)
While not required in the problem, the conventional ABC analysis would be:
Sales (80 clubs × $48 per club) ............................ $3,840. Costs: Direct materials ................................................. $2,032. Direct labor ....................................................... 516. Volume related overhead ................................... 283. Batch processing overhead ................................ 53. Order processing overhead ................................ 118. Customer service overhead ................................ 1,010.00 4,013. Customer margin ................................................. ($ 173.00)
388 Managerial Accounting, 12th Edition
Exercise 8-7 (continued)
Manufacturing overhead is assigned to the two products as follows: Deluxe Product:
Activity Cost Pool
(a) Activity Rate
(b) Activity
(a) × (b) ABC Cost Supporting direct labor .......... $3 per DLH 8,000 DLHs $24, Batch setups ......................... $240 per setup 200 setups 48, Safety testing ........................ $800 per test 80 tests 64, Total..................................... $136, Standard Product:
Activity Cost Pool
(a) Activity Rate
(b) Activity
(a) × (b) ABC Cost Supporting direct labor .......... $3 per DLH 42,000 DLHs $126, Batch setups ......................... $240 per setup 50 setups 12, Safety testing ........................ $800 per test 20 tests 16, Total..................................... $154,
Activity-based costing unit product costs are computed as follows: Deluxe Standard Direct materials ................................................... $60.00 $45. Direct labor ......................................................... 9.60 7. Manufacturing overhead ($136,000 ÷ 10, units; $154,000 ÷ 70,000 units) ........................ 13.60 2. Unit product cost................................................. $83.20 $54.
Solutions Manual, Chapter 8 389
Activity
Activity Classification
Examples of Activity Measures a. Materials are moved from the receiving dock to the assembly area by a mate- rial-handling crew
Batch-level
Number of materials moves; time spent mov- ing materials b. Direct labor workers as- semble various products Unit-level Time spent assembling products c. Diversity training is provid- ed to all employees in the company
Organiza- tion- sustaining
Number of employees taking diversity training; Time spent in training d. A product is designed by a cross-functional team Product- level
Number of new products designed; time spent developing new products e. Equipment is set up to process a batch Batch-level Number of batches run; time spent setting up f. A customer is billed for all products delivered during the month
Customer- level
Number of customer bills prepared; time spent preparing bills
Notes:
Solutions Manual, Chapter 8 391
Exercise 8-9 (continued)
Rims Posts Direct materials ................................... $17.00 $10. Direct labor: $16 per DLH × 0.40 DLHs per unit..... 6. $16 per DLH × 0.20 DLHs per unit..... 3. Overhead: $288,000 ÷ 20,000 units ................... 14. $201,600 ÷ 80,000 units ................... 2. Unit cost ............................................. $37.80 $15.
392 Managerial Accounting, 12th Edition
Teller wages ............................... $150, Assistant branch manager salary .. $70, Branch manager salary ................ $85,
Distribution of Resource Consumption Across Activities
Opening Accounts
Processing Deposits and Withdrawals
Processing Other Customer Transactions
Other Activities Totals Teller wages ............................... 0% 75% 15% 10% 100% Assistant branch manager salary .. 10% 15% 25% 50% 100% Branch manager salary ................ 0% 0% 20% 80% 100%
Opening Accounts
Processing Deposits and Withdrawals
Processing Other Customer Transactions
Other Activities Totals Teller wages ................................ $ 0 $112,500 $22,500 $ 15,000 $150, Assistant branch manager salary... 7,000 10,500 17,500 35,000 70, Branch manager salary................. 0 0 17,000 68,000 85, Total cost .................................... $7,000 $123,000 $57,000 $118,000 $305,
Teller wages are $150,000 and 75% of the tellers’ time is spent processing deposits and withdrawals: $150,000 × 75% = $112, Other entries in the table are similarly determined.
394 Managerial Accounting, 12th Edition
Activity Cost Pool
(a) Activity Rate
(b) Activity
(a) × (b) ABC Cost Order size ........... R 17.60 per direct labor-hour 150 direct labor-hours R 2, Customer orders .. R 360.00 per customer order 1 customer order 360 Product testing .... R 79.00 per product testing hour 18 product testing hours 1, Selling ................. R 1,494.00 per sales call 3 sales calls 4, Total ................... R 8,
According to these calculations, the total overhead cost of the order is R 8,904.
Solutions Manual, Chapter 8 395
Order Size
Customer Orders
Product Testing Selling Total Total activity for the order ........ 150 1 18 3 direct labor- hours
customer order
product testing hours
sales calls
Manufacturing overhead: Indirect labor ........................ R 1,440 R 231 R 648 R 0 R 2, Factory depreciation .............. 1,050 0 324 0 1, Factory utilities...................... 30 0 18 0 48 Factory administration ........... 0 46 432 36 514 Selling and administrative: Wages and salaries ............... 120 72 0 2,895 3, Depreciation ......................... 0 11 0 108 119 Taxes and insurance.............. 0 0 0 147 147 Selling expenses.................... 0 0 0 1,296 1, Total overhead cost ................. R 2,640 R 360 R 1,422 R 4,482 R 8,
Example: R 9.60 per direct labor-hour × 150 direct labor-hours = R 1,
According to these calculations, the overhead cost of the order was R 8,904. This agrees with the com- putations in Exercise 8-12.
Solutions Manual, Chapter 8 397
Activity Level a. The purchasing department orders the specific color of paint specified by the customer from the company’s supplier .... Batch-level
b. A steering wheel is installed in a golf cart .. Unit-level c. An outside attorney draws up a new ge- neric sales contract for the company lim- iting Green Glider’s liability in the case of accidents that involve its golf carts ......... Organization-sustaining
d. The company’s paint shop makes a stencil for a customer’s logo ............................. Batch-level
e. A sales representative visits an old cus- tomer to check on how the company’s golf carts are working out and to try to make a new sale.................................... Customer-level f. The accounts receivable department pre- pares the bill for a completed order ........ Batch-level g. Electricity is used to heat and light the factory and the administrative offices ...... Organization-sustaining
h. A golf cart is painted ................................ Unit-level
i. The company’s engineer modifies the de- sign of a model to eliminate a potential safety problem ...................................... Product-level j. The marketing department has a cata- logue printed and then mails them to golf course managers ............................. Customer-level
k. Completed golf carts are each tested on the company’s test track ........................ Unit-level
l. A new model golf cart is shipped to the leading golfing trade magazine to be evaluated for the magazine’s annual rat- ing of golf carts ..................................... Product-level
398 Managerial Accounting, 12th Edition
Customer Margin—ABC Analysis Sales (2,400 seats × $137.95 per seat) ............. $331, Costs: Direct materials ($112 per seat × 2,400 seats) .. $268, Direct labor ($14.40 per seat × 2,400 seats) ..... 34, Supporting direct labor ($12 per DLH × 0. DLH per seat × 2,400 seats) .......................... 23, Batch processing ($96 per batch × 4 batches)... 384 Order processing ($284 per order × 1 order)..... 284 Customer service overhead ($2,620 per cus- tomer × 1 customer) ..................................... 2,620 329, Customer margin ............................................... $ 1,