
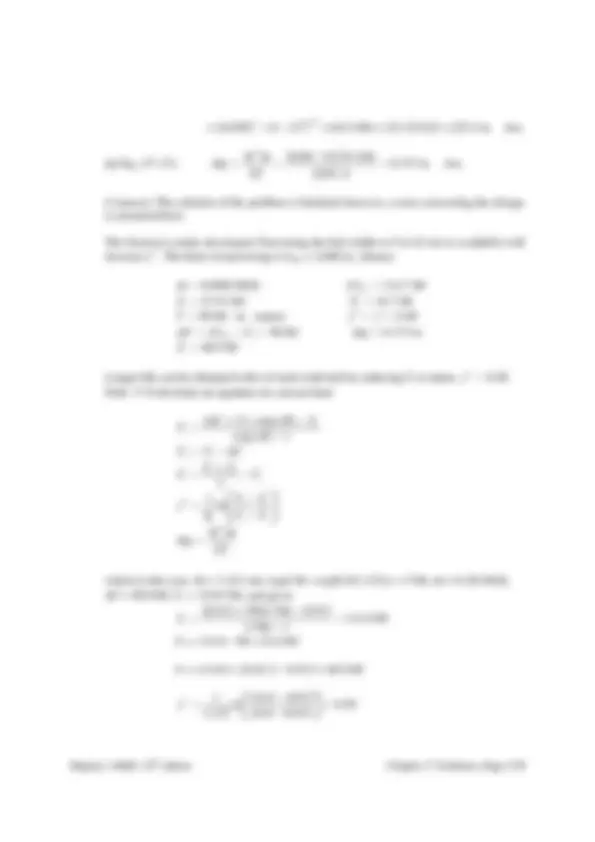
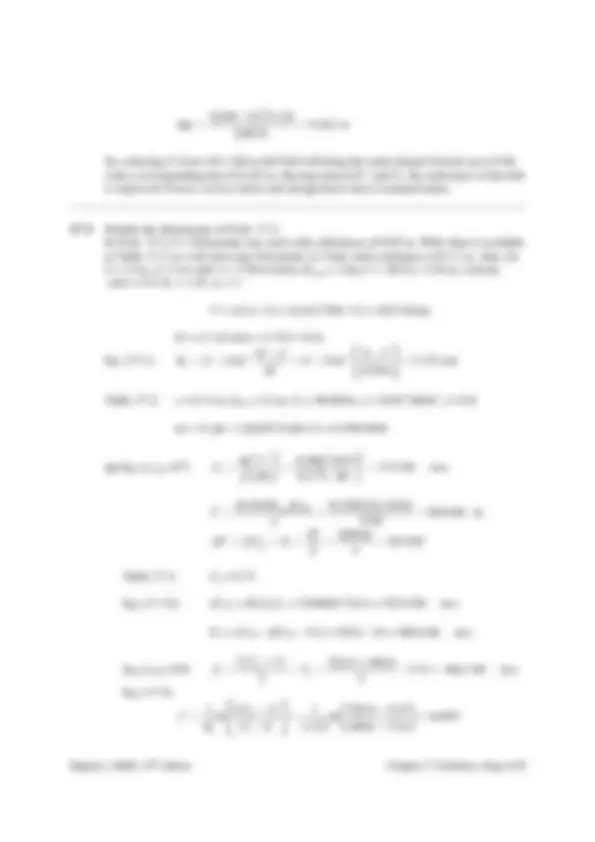
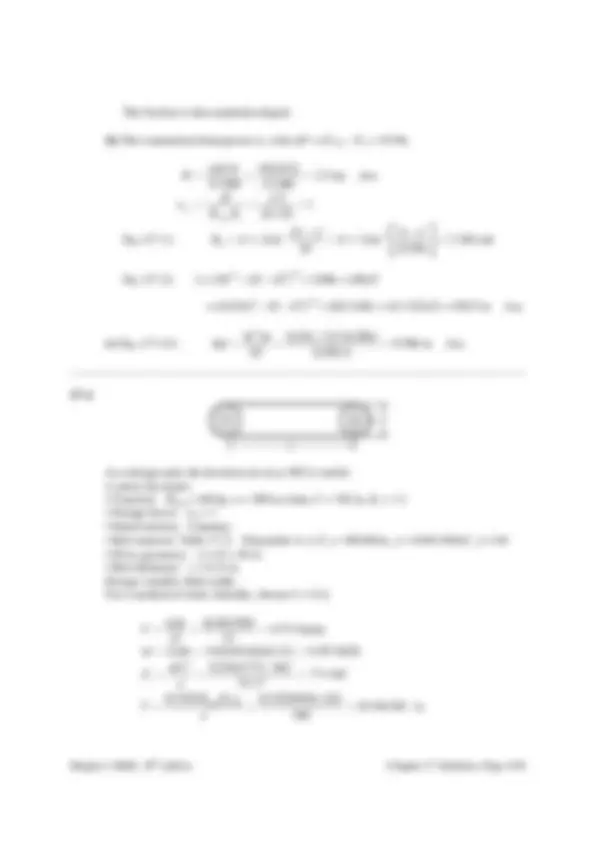
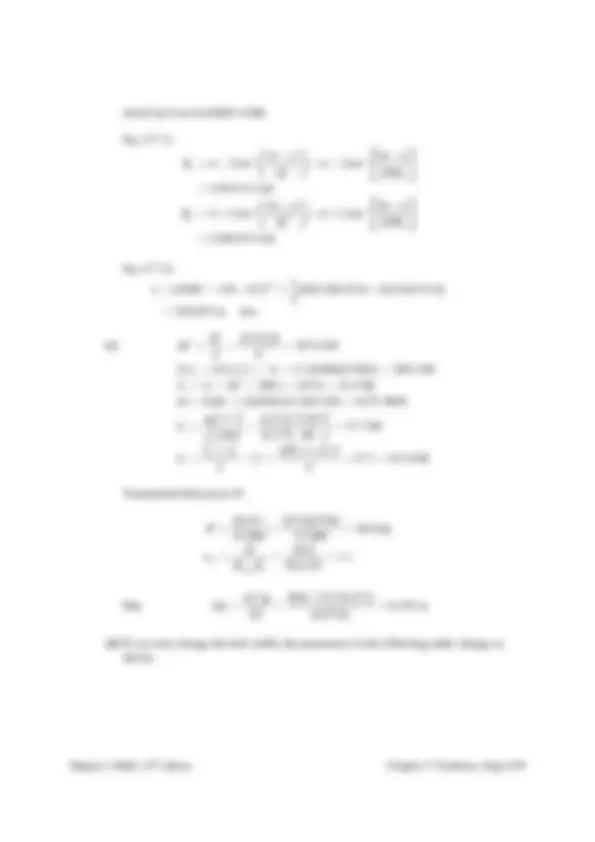
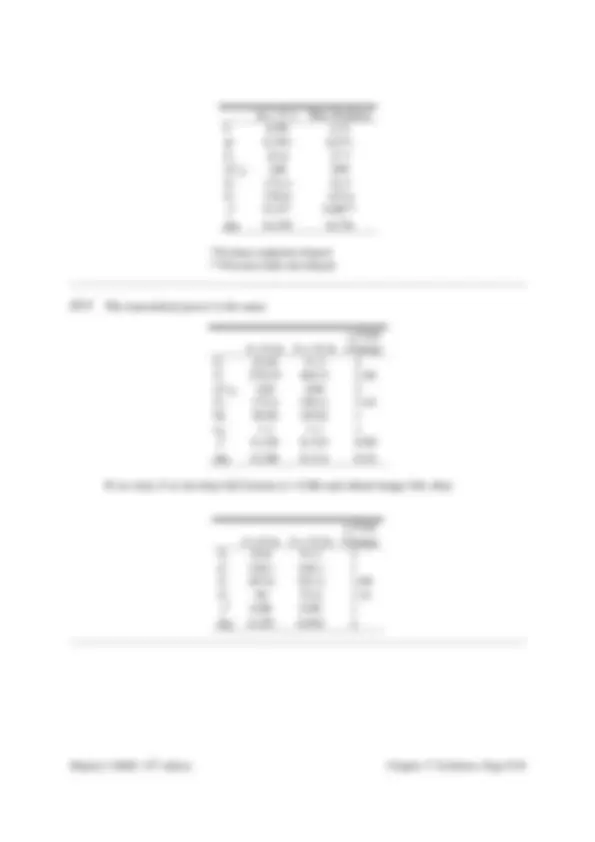
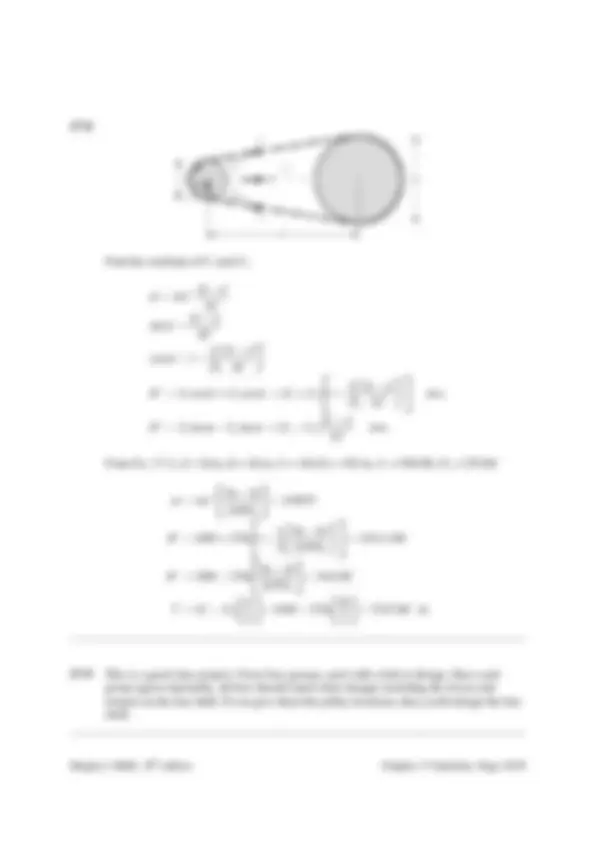
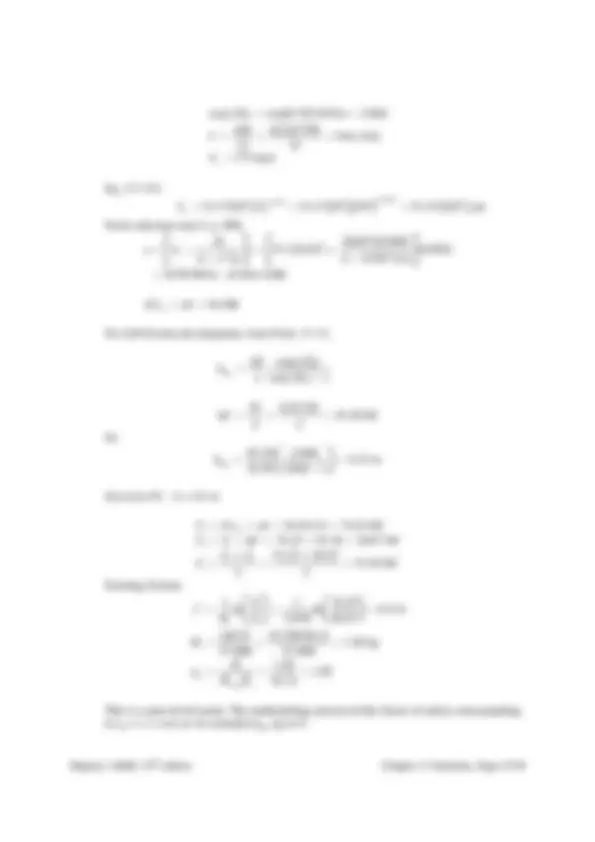
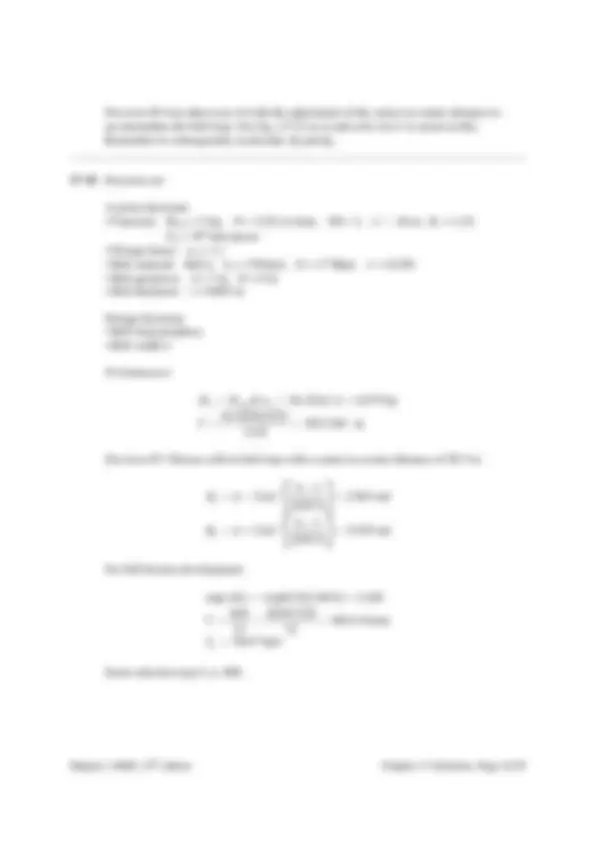
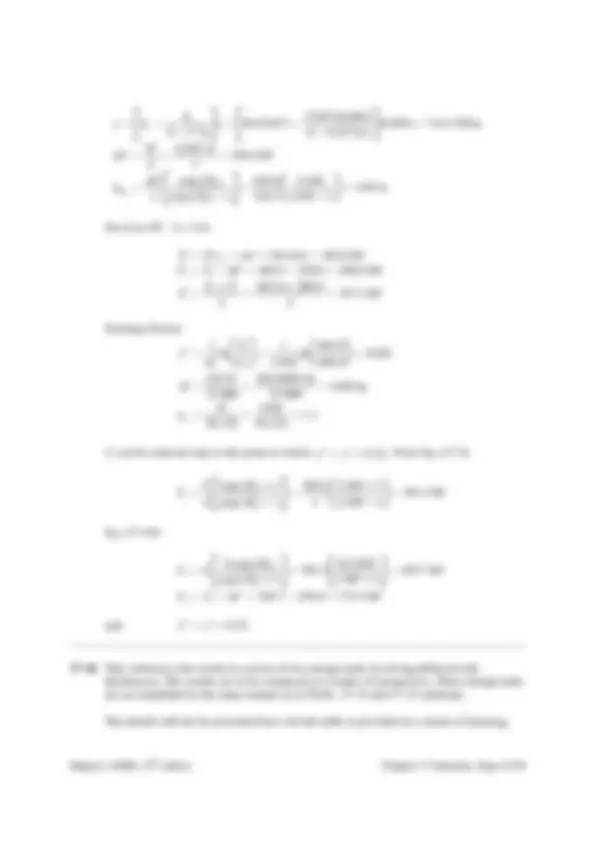
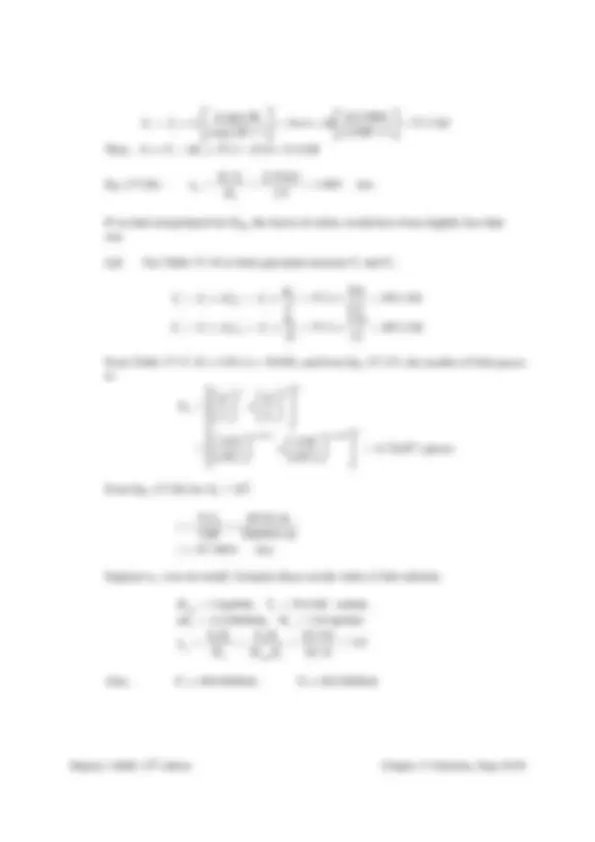
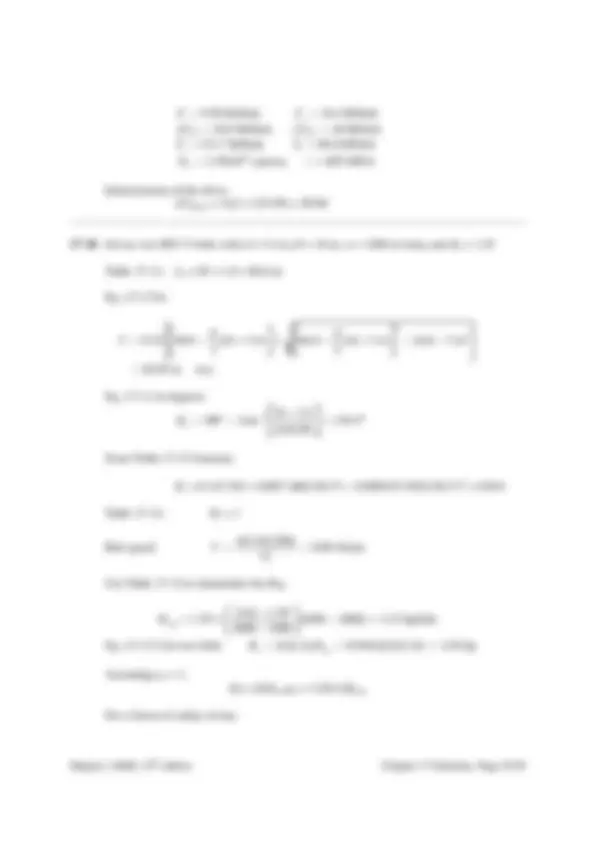
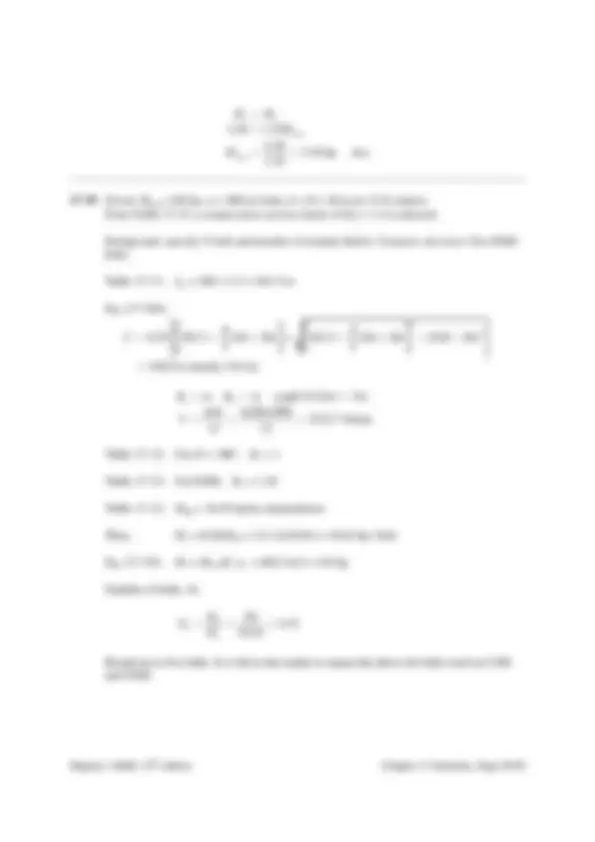
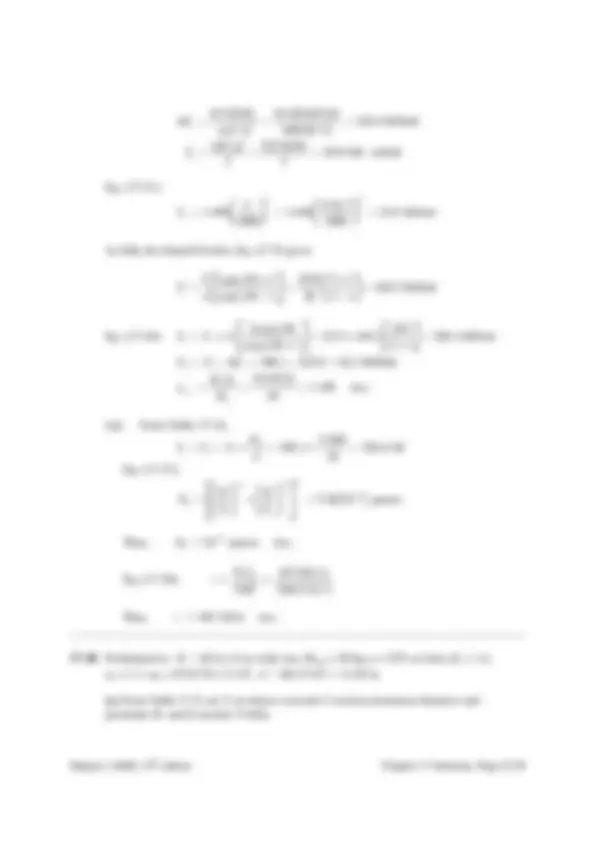
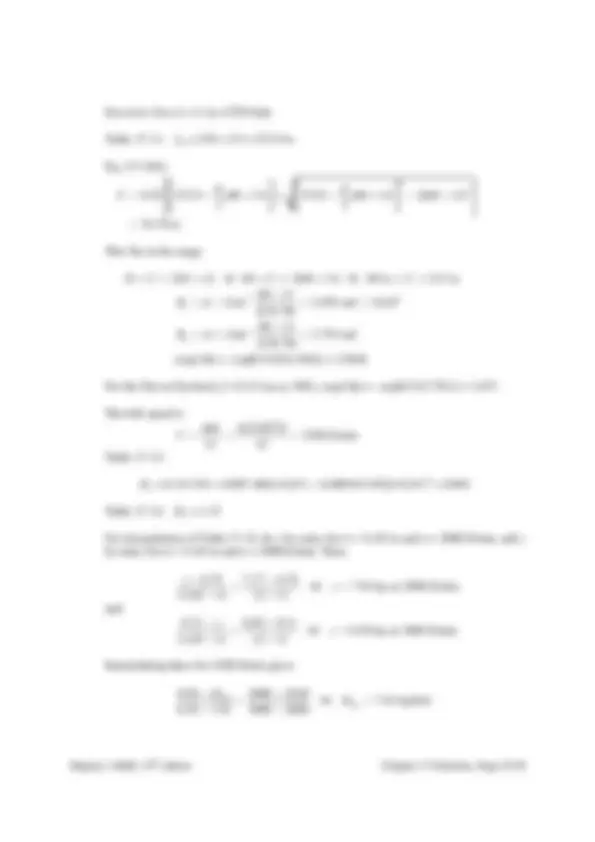
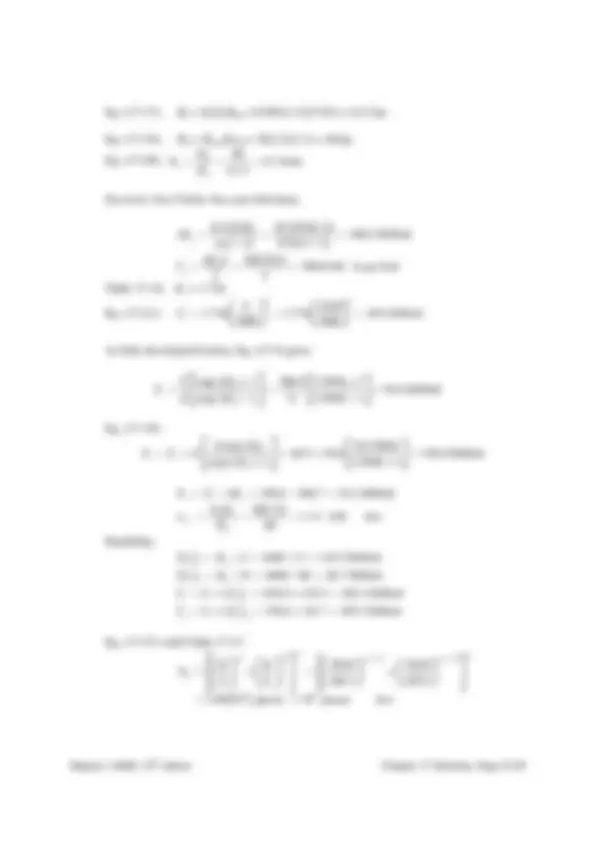
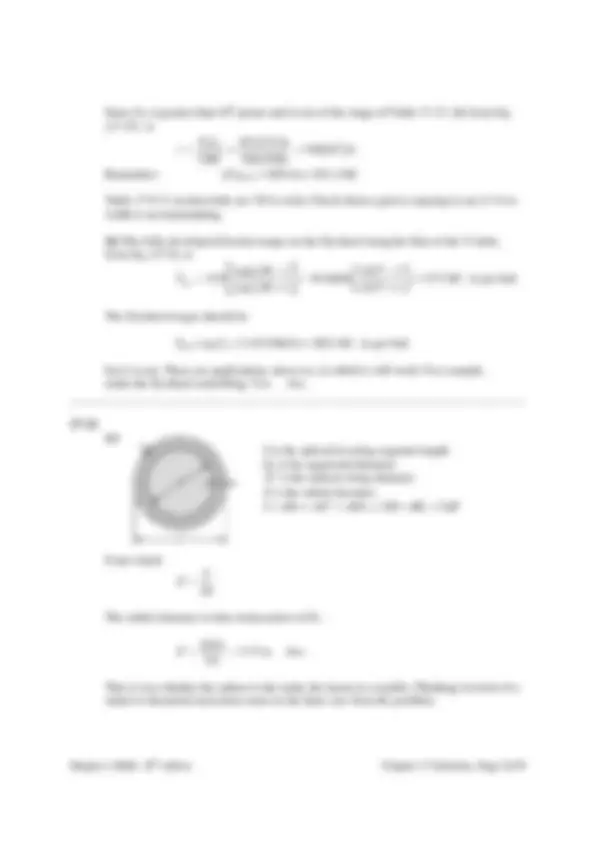
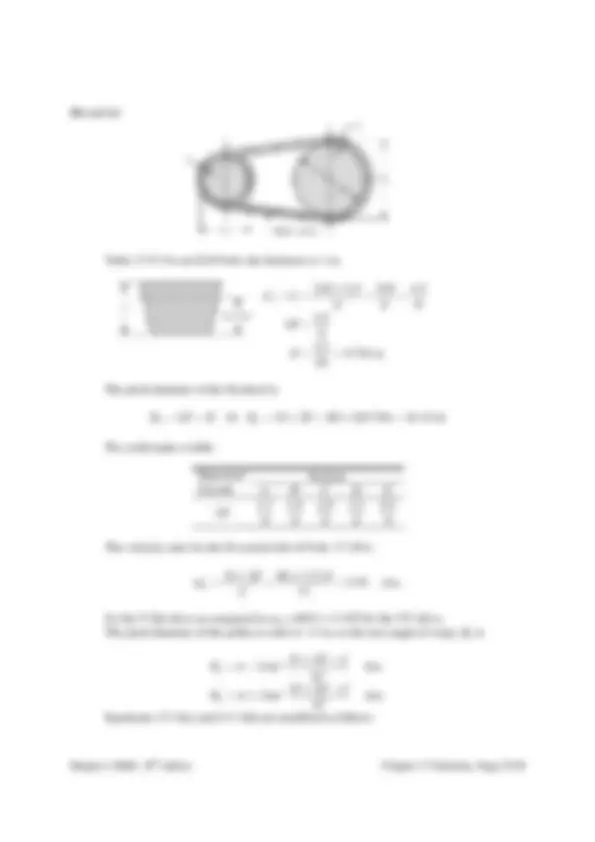
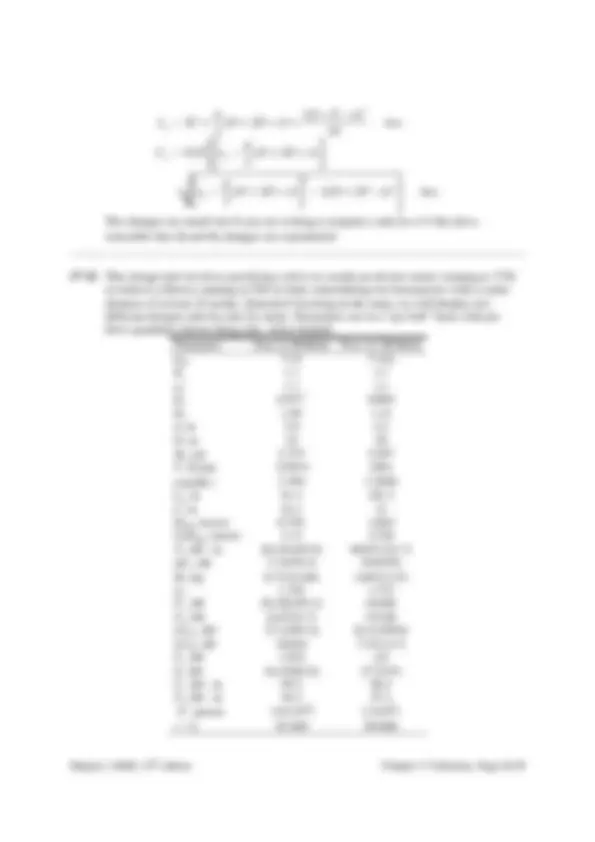
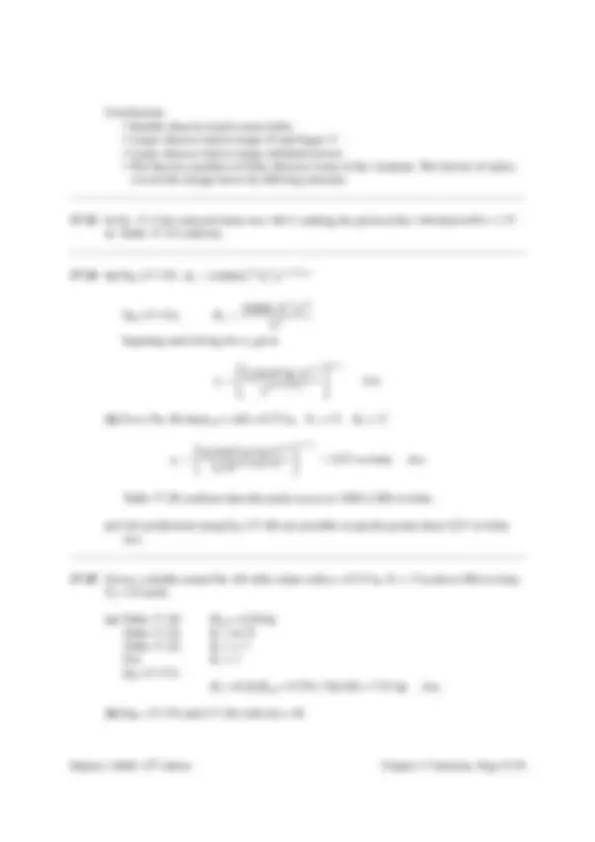
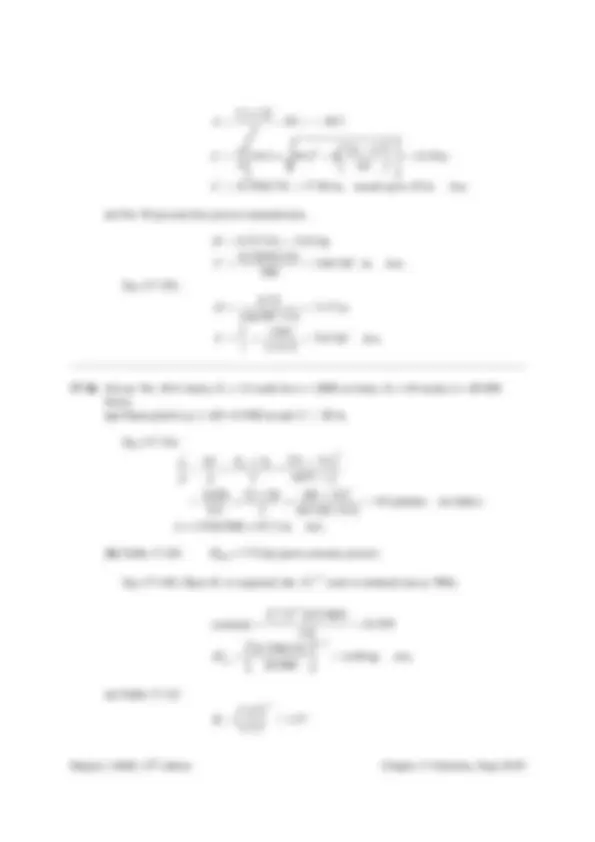
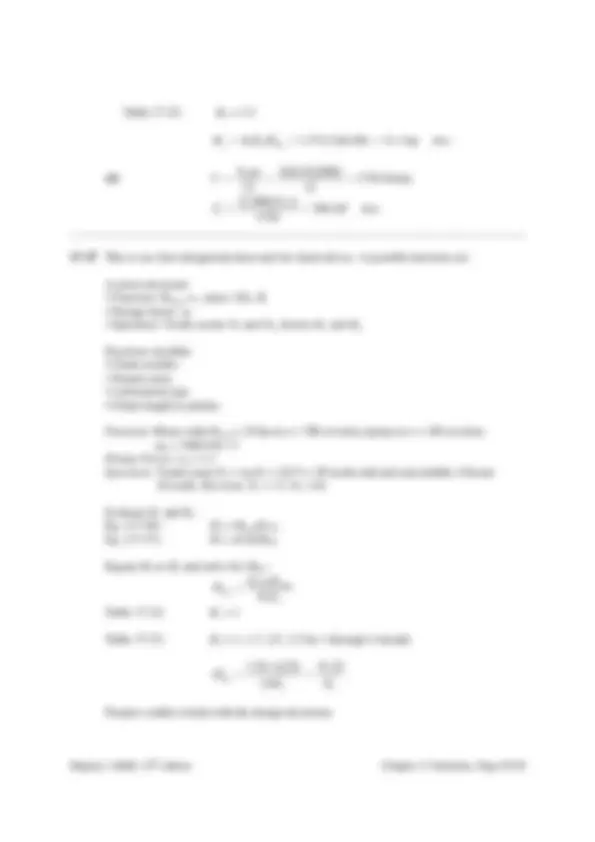
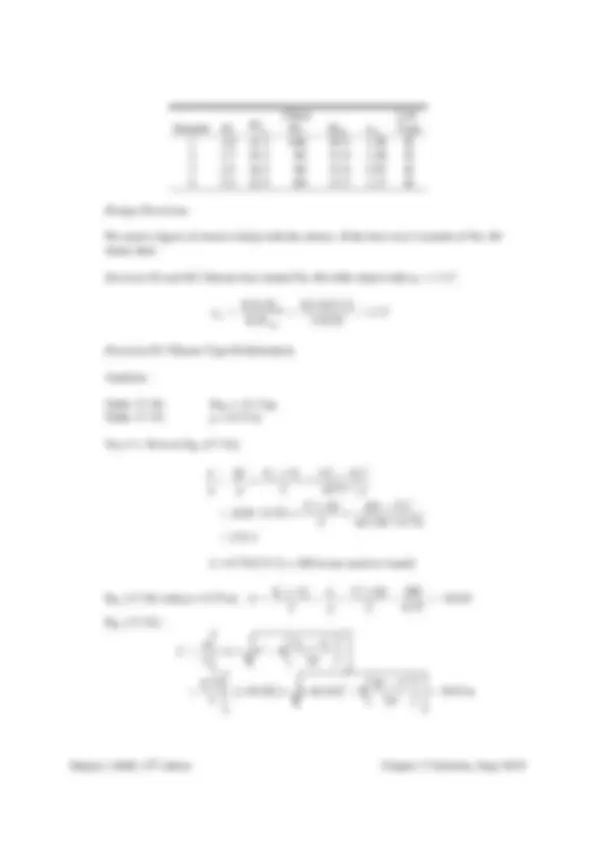
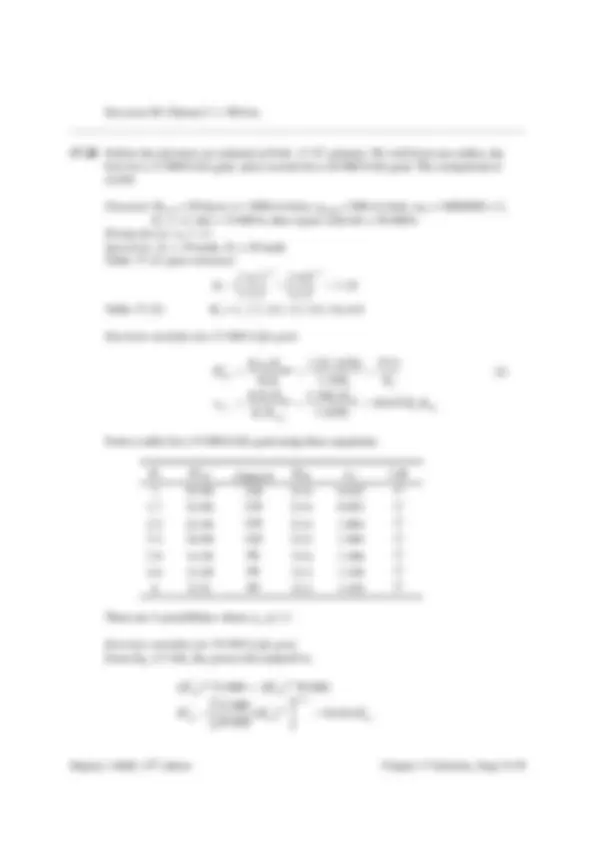
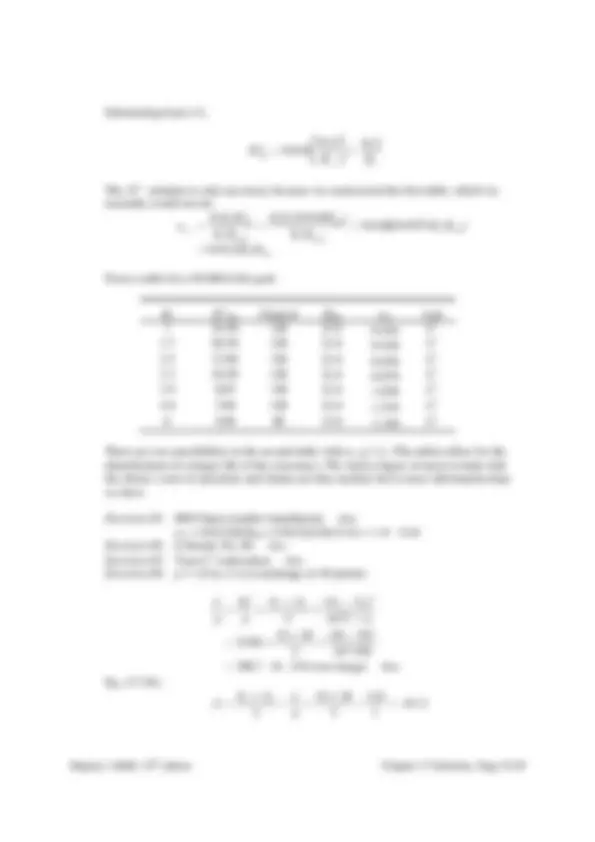
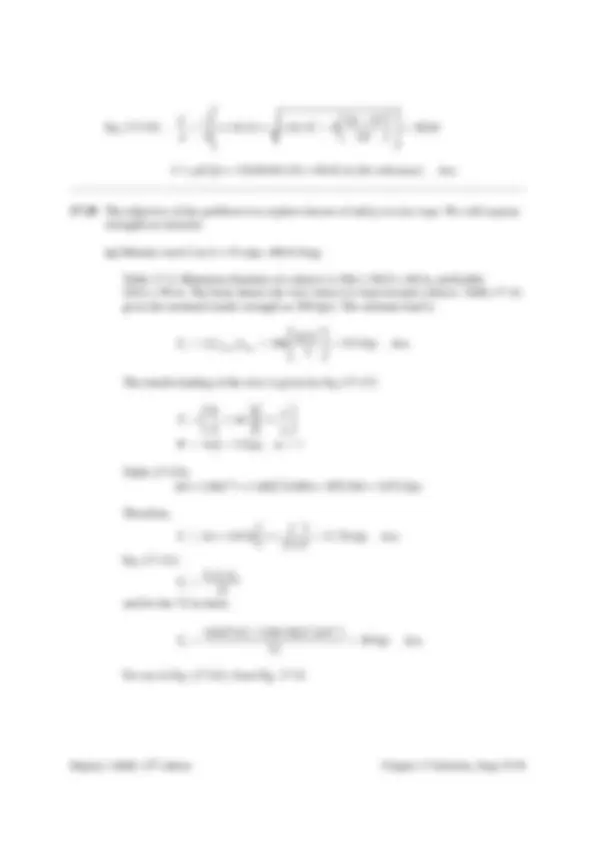
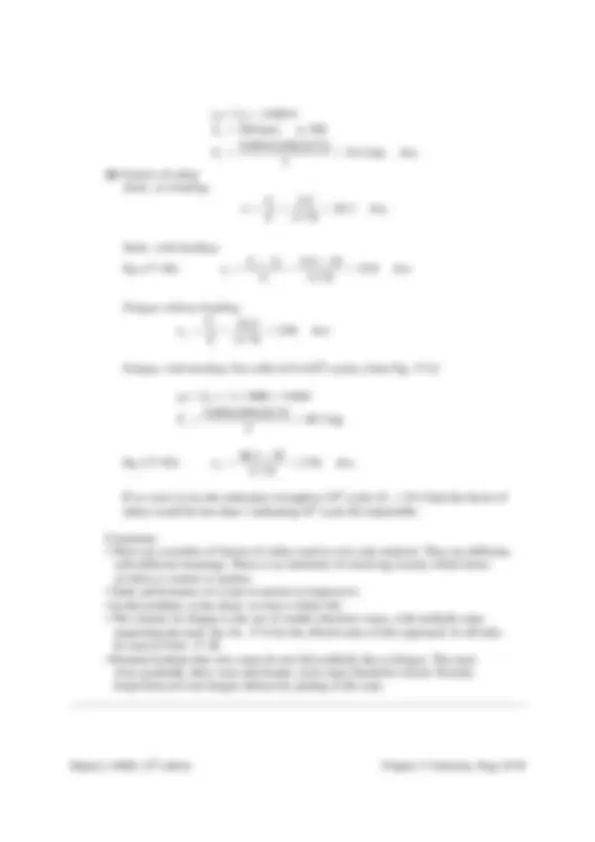
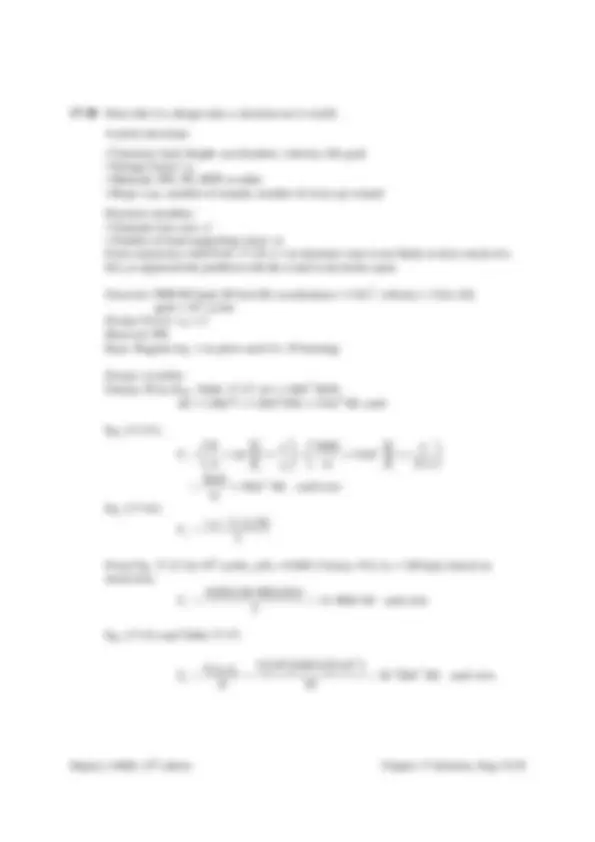
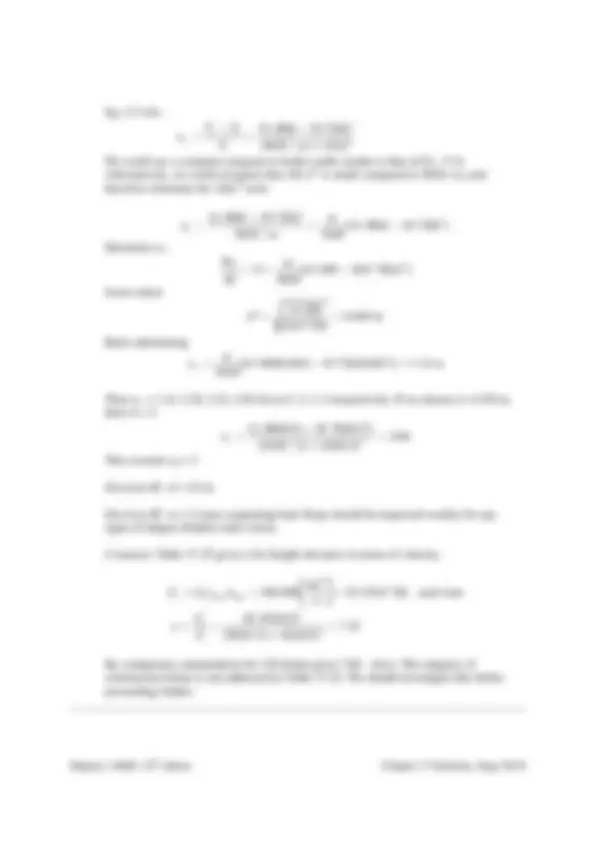
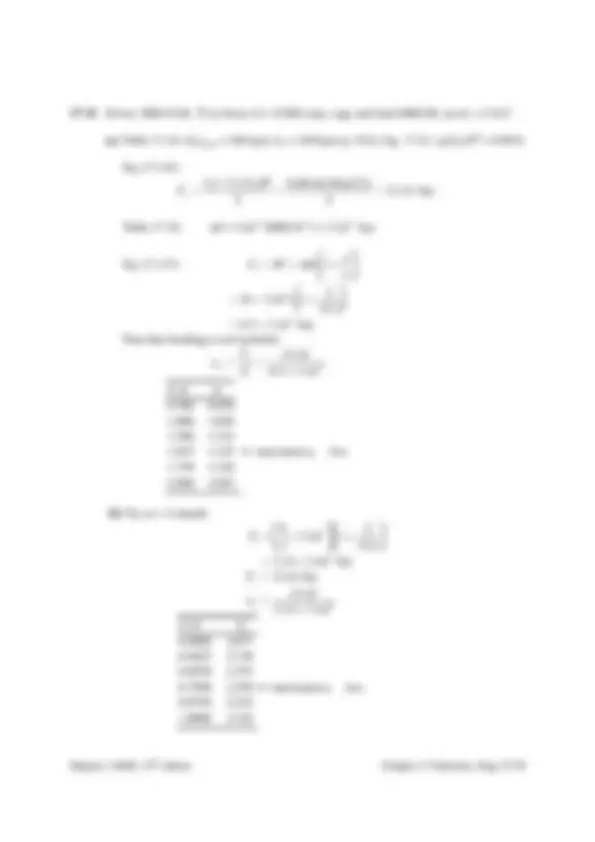
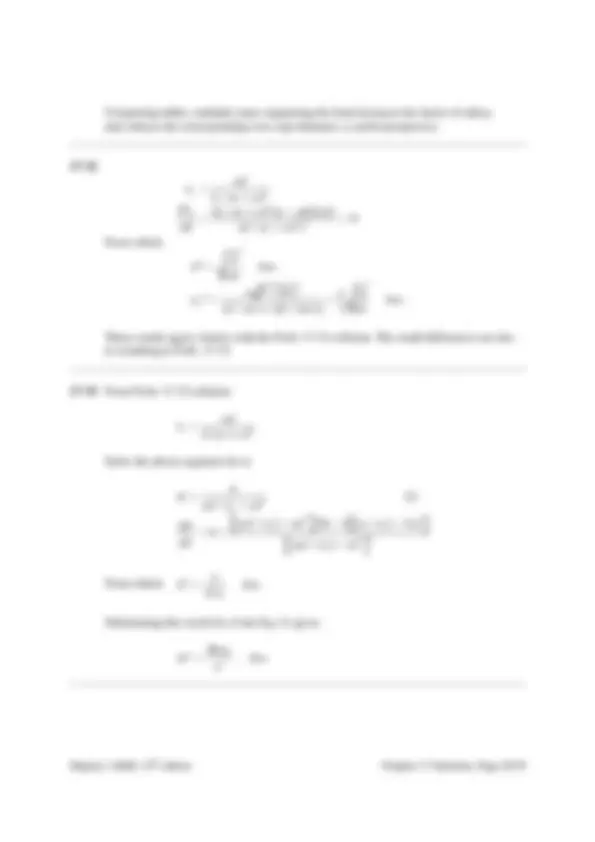
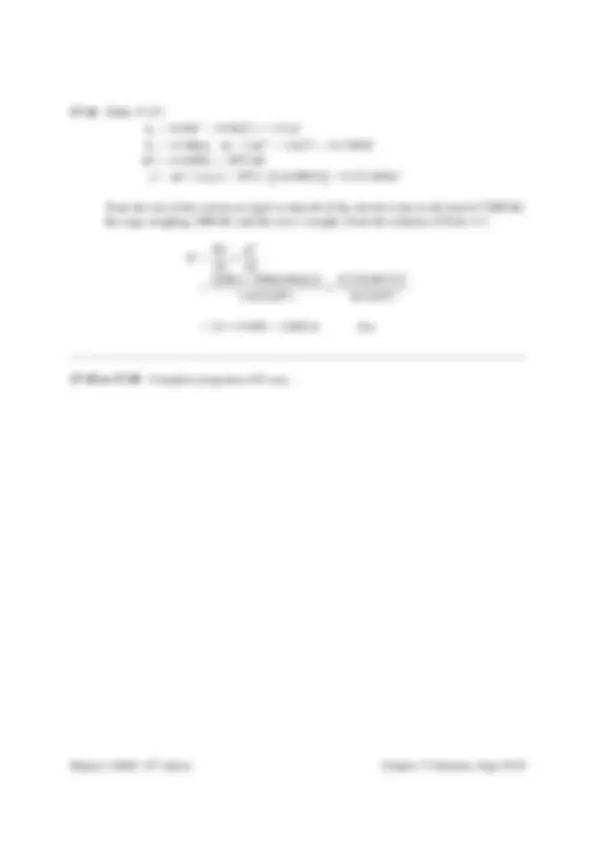
Study with the several resources on Docsity
Earn points by helping other students or get them with a premium plan
Prepare for your exams
Study with the several resources on Docsity
Earn points to download
Earn points by helping other students or get them with a premium plan
Community
Ask the community for help and clear up your study doubts
Discover the best universities in your country according to Docsity users
Free resources
Download our free guides on studying techniques, anxiety management strategies, and thesis advice from Docsity tutors
Chapter 17 Exercise problems solved for Shigley's Mechanical Engineering Design 10th Edition, by Michael A. Latcha, PhD. ME 486 Oakland University (OU)
Typology: Lecture notes
1 / 39
This page cannot be seen from the preview
Don't miss anything!
th
17-1 Begin with Eq. (17-10),
1
2 exp( )
exp( ) 1
c i
f F F F f
θ
θ
Introduce Eq. (17-9):
1
1
exp( ) 1 2 exp( ) 2 exp( )
exp( ) 1 exp( ) 1 exp( ) 1
exp( )
exp( ) 1
c c
c
f f T f F F d F f f d f
f F F F f
θ θ θ
θ θ θ
θ
θ
Now add and subtract
exp( )
exp( ) 1
c
f F f
θ
θ
1
exp( ) exp( ) exp( )
exp( ) 1 exp( ) 1 exp( ) 1
exp( ) exp( ) ( ) exp( ) 1 exp( ) 1
exp( ) ( ) exp( ) 1 exp( ) 1
( ) exp( )
ex
c c c
c c c
c c
c c
f f f F F F F F f f f
f f F F F F f f
f F F F f f
F F f F
θ θ θ
θ θ θ
θ θ
θ θ
θ
θ θ
θ
p( ) 1
f θ −
From Ex. 17-2: θ d = 3_._ 037 rad, ∆ F = 664 lbf, exp( f θ ) = exp[0_._ 80(3_._ 037)] = 11_._ 35, and
Fc = 73_._ 4 lbf.
1
2 1
1
2
802 lbf (11.35 1)
802 664 138 lbf
73.4 396.6 lbf 2
ln ln 0.. 3.037 138 73.
i
c
d c
f Ans θ F F
17-2 Given: F-1 Polyamide, b = 6 in, d = 2 in with n = 1750 rev/min, H nom = 2 hp, C = 9(12) =
108 in, velocity ratio = 0.5, Ks = 1.25, nd = 1
th
V = π d n / 12 = π (2)(1750) / 12 = 916.3 ft/min
D = d / vel ratio = 2 / 0.5 = 4 in
Eq. (17-1):
2sin 2sin 3.123 rad 2 2(108)
d
D d
θ π π
Table 17-2: t = 0.05 in, d min = 1.0 in, Fa = 35 lbf/in, γ = 0.035 lbf/in
3 , f = 0.
w = 12 γ bt = 12(0.035)6(0.05) = 0.126 lbf/ft
(a) Eq. ( e ), p. 877:
2 2 0.126 916. 0.913 lbf. 60 32.17 60
c
F Ans g
w
90.0 lbf · in 1750
2 2(90.0) 90.0 lbf 2
nom s d
a
H K n T n
T F F F d
Table 17-4: Cp = 0.
Eq. (17-12): ( F 1 ) a = bFaCpCv = 6(35)(0_._ 70)(1) = 147 lbf Ans.
F 2 = ( F 1 ) a − [( F 1 ) a − F 2 ] = 147 − 90 = 57 lbf Ans.
Do not use Eq. (17-9) because we do not yet know f ′
Eq. ( i ), p. 878:
0.913 101.1 lbf. 2 2
a i c
F F Ans
Using Eq. (17-7) solved for f ′ (see step 8, p.888),
1
2
ln ln 0. 3.123 57 0.
a c
d c
f θ F F
The friction is thus underdeveloped.
(b) The transmitted horsepower is, with ∆ F = ( F 1 ) a − F 2 = 90 lbf,
Eq. (j), p. 879:
2.5 hp. 33 000 33 000
H Ans
nom
f s s
n H K
Eq. (17-1):
2sin 2sin 3.160 rad 2 2(108)
D
D d
θ π π
Eq. (17-2): L = [4 C
2 − ( D − d )
2 ]
1/
th
2 3 108 / 12 0. dip 0.222 in 2(68.9)
So, reducing Fi from 101.1 lbf to 68.9 lbf will bring the undeveloped friction up to 0.50,
with a corresponding dip of 0.222 in. Having reduced F 1 and F 2 , the endurance of the belt
is improved. Power, service factor and design factor have remained intact.
17-3 Double the dimensions of Prob. 17-2.
In Prob. 17-2, F-1 Polyamide was used with a thickness of 0.05 in. With what is available
in Table 17-2 we will select the Polyamide A-2 belt with a thickness of 0.11 in. Also, let
b = 12 in, d = 4 in with n = 1750 rev/min, H nom = 2 hp, C = 18(12) = 216 in, velocity
ratio = 0.5, Ks = 1.25, nd = 1.
V = π d n / 12 = π (4)(1750) / 12 = 1833 ft/min
D = d / vel ratio = 4 / 0.5 = 8 in
Eq. (17-1):
2sin 2sin 3.123 rad 2 2(216)
d
D d
θ π π
Table 17-2: t = 0.11 in, d min = 2.4 in, Fa = 60 lbf/in, γ = 0.037 lbf/in
3 , f = 0.
w = 12 γ bt = 12(0.037)12(0.11) = 0.586 lbf/ft
(a) Eq. ( e ), p. 877:
2 2 0.586 1833 17.0 lbf. 60 32.17 60
c
F Ans g
w
90.0 lbf · in 1750
2 2(90.0) 45.0 lbf 4
nom s d
a
H K n T n
T F F F d
Table 17-4: Cp = 0.
Eq. (17-12): ( F 1 ) a = bFaCpCv = 12(60)(0_._ 73)(1) = 525.6 lbf Ans.
F 2 = ( F 1 ) a − [( F 1 ) a − F 2 ] = 525.6 − 45 = 480.6 lbf Ans.
Eq. ( i ), p. 878:
17.0 486.1 lbf. 2 2
a i c
F F Ans
Eq. (17-9):
1
2
ln ln 0. 3.123 480.6 17.
a c
d c
f θ F F
Shigley’s MED, 10
th edition
The friction is thus un
(b) The transmitted horsepower is,
f s
H Ans
n H K
Eq. (17-1):
Eq. (17-2): L =
(c) Eq. (17-13):
As a design task, the decision set on p. 8
A priori decisions:
Design variable: Belt width.
Use a method of trials. Initially
2 2
nom
12 12(0.042)(6)(0.13) 0.393 lbf/ft
c
dn V
bt
g
H K n T n
π π
γ
w
w
Chapter 17
The friction is thus underdeveloped.
The transmitted horsepower is, with ∆ F = ( F 1 ) a − F 2 = 45 lbf,
nom
2.5 hp. 33 000 33 000
1
s 2(1.25)
H Ans
2sin 2sin 3.160 rad 2 2(216)
D
D d
θ π π
2 − ( D − d )
2 ]
1/
2 − (8 − 4)
2 ]
1/
2 2 3 3(216 / 12) (0.586) dip 0.586 in. (^2) i 2(486.1)
w
the decision set on p. 885 is useful.
= 60 hp, n = 380 rev/min, C = 192 in, Ks = 1_._ 1
= 1
Catenary
. Table 17-2: Polyamide A-3, Fa = 100 lbf/in, γ = 0.042 lbf/in
= D = 48 in
= 0_._ 13 in
ign variable: Belt width.
Use a method of trials. Initially, choose b = 6 in
2 2
nom
4775 ft/min 12 12
12 12(0.042)(6)(0.13) 0.393 lbf/ft
77.4 lbf
10 946 lbf · in 380
H K n s d
n
π π = = =
Chapter 17 Solutions, Page 5/
2sin 2sin 3.160 rad 2 2(216)
(3.123)]/2 = 450_._ 9 in Ans.
dip 0.586 in Ans.
= 0.042 lbf/in
3 , f = 0.
10 946 lbf · in
th
17-5 From the last equation given in the problem statement,
0 2
0 2
0 2
0 2
exp 1 2 / [ ( ) ]
1 exp 1 ( )
exp exp 1 ( )
1 2 exp
exp 1
f T d a a b
f d a a b
f f d a a b
T f b a a d f
φ
φ
φ φ
φ
φ
But 2 T/d = 33 000 Hd/V. Thus,
1 33 000 exp
... exp 1
H d f b Q E D a a V f
φ
φ
17-6 Refer to Ex. 17-1 on p. 882 for the values used below.
(a) The maximum torque prior to slip is,
63 025 (^) nom 63 025(15)(1.25)(1.1) 742.8 lbf · in. 1750
H K n s d T Ans n
The corresponding initial tension, from Eq. (17-9), is,
exp( ) 1 742.8 11.17 1 148.1 lbf. exp( ) 1 6 11.17 1
i
T f F Ans d f
θ
θ
(b) See Prob. 17-4 statement. The final relation can be written
min (^2)
2
1 33 000^ exp
(12 / 32.174)( / 60) [exp 1]
4.13 in.
a
a p
H f b F C C t V V f
Ans
θ
γ θ
v
This is the minimum belt width since the belt is at the point of slip. The design must
th
round up to an available width.
Eq. (17-1):
1 1
1 1
2sin 2sin 2 2(96)
3.016 511 rad
2sin 2sin 2 2(96)
3.266 674 rad
d
D
D d
D d
θ π π
θ π π
− −
− −
Eq. (17-2):
230.074 in.
Ans
(c)
247.6 lbf 6
d
1 1
2 1
2 2
1 2
( ) 4.13(100)(0.70)(1) 289.1 lbf
289.1 247.6 41.5 lbf
12 12(0.042)4.13(0.130) 0.271 lbf/ft
17.7 lbf 60 32.17 60
17.7 147.6 lb 2 2
a a p
c
i c
F bF C C F
bt
g
γ
v
w
w
f
Transmitted belt power H
nom
20.6 hp 33 000 33 000
15(1.25)
fs s
n H K
Dip:
2 2 3 3(96 / 12)^ 0. 0.176 in (^2) i 2(147.6)
dip F
w
( d ) If you only change the belt width, the parameters in the following table change as
shown.
Shigley’s MED, 10
th edition
Find the resultant of F
1
1 2 1 2
1 2 1 2
sin 2
sin 2
cos 1 2 2
cos cos ( ) 1.
sin sin ( ).
x
y
D d
D d
R F F F F Ans
R F F F F Ans
α
α
α
α α
α α
From Ex. 17-2, d = 16 in,
1 2
sin 2.
(940 276) 1 1214.4 lbf
(940 276) 34.6 lbf
( ) (940 276) 5312 lbf · in
x
y
α
− = =
17-9 This is a good class project. Form four groups, each with a belt to design. Once each
group agrees internally, all four should report their designs including the forces and
torques on the line shaft. If you give them the pulley locations, they could
shaft.
Chapter 17
F 1 and F 2 :
2
2
1 2 1 2
1 2 1 2
cos cos ( ) 1. 2 2
sin sin ( ). 2
D d
D d
D d
D d R F F F F Ans C
D d R F F F F Ans C
α α
α α
= 16 in, D = 36 in, C = 16(12) = 192 in, F 1 = 940 lbf,
1 o
2
1 2
sin 2. 2(192)
(940 276) 1 1214.4 lbf 2 2(192)
(940 276) 34.6 lbf 2(192)
( ) (940 276) 5312 lbf · in 2 2
d T F F
This is a good class project. Form four groups, each with a belt to design. Once each
group agrees internally, all four should report their designs including the forces and
torques on the line shaft. If you give them the pulley locations, they could
Chapter 17 Solutions, Page 10/
R F cos F cos ( F F ) 1 Ans.
= 940 lbf, F 2 = 276 lbf
( ) (940 276) 5312 lbf · in
This is a good class project. Form four groups, each with a belt to design. Once each
group agrees internally, all four should report their designs including the forces and
torques on the line shaft. If you give them the pulley locations, they could design the line
th
17-10 If you have the students implement a computer program, the design problem selections
may differ, and the students will be able to explore them. For Ks = 1_._ 25, nd = 1_._ 1, d = 14
in and D = 28 in, a polyamide A-5 belt, 8 inches wide, will do ( b min = 6_._ 58 in)
17-11 An efficiency of less than unity lowers the output for a given input. Since the object of
the drive is the output, the efficiency must be incorporated such that the belt’s capacity is
increased. The design power would thus be expressed as
nom . eff
s d d
H K n H = Ans
17-12 Some perspective on the size of Fc can be obtained from
2 2 12
c
V bt V F g g
γ = (^) =
w
An approximate comparison of non-metal and metal belts is presented in the table below.
Non-metal Metal
γ, lbf/in
3 0.04 0.
b , in 5.00 1.
t , in 0.20 0.
The ratio w / wm is
m^ 12(0.28)(1)(0.005)
w
w
The second contribution to Fc is the belt peripheral velocity which tends to be low in
metal belts used in instrument, printer, plotter and similar drives. The velocity ratio
squared influences any Fc / ( Fc ) m ratio.
It is common for engineers to treat Fc as negligible compared to other tensions in the
belting problem. However, when developing a computer code, one should include Fc.
17-13 Eq. (17-8):
1 2 1 1
exp( ) 1 exp( ) 1 ( ) exp( ) exp( )
c
f f F F F F F F f f
θ θ
θ θ
Assuming negligible centrifugal force and setting F 1 = ab from step 3, p. 889,
min
exp( ) (1) exp( ) 1
F f b a f
θ
θ
th
exp( ) exp[0.35(3.010)] 2.
916.3 ft/s 12 12
175 kpsi
d
y
f
dn V
θ
π π
Eq. (17-15):
6 0.407 6 6 0.407 3 S (^) y 14.17 10 N (^) p 14.17 10 10 51.212 10 psi
− − = = =
From selection step 3, p. 889,
6 3 2 2
1
16.50 lbf/in of belt width
f
a
Et a S t d
F ab b
ν
For full friction development, from Prob. 17-13,
min
exp( )
exp( ) 1
45.38 lbf 2
d
d
F f b a f
d
θ
θ
So
min
4.23 in 16.50 2.868 1
b
Decision #1 : b = 4_._ 5 in
1 1
2 1
1 2
( ) 16.5(4.5) 74.25 lbf
74.25 45.38 28.87 lbf
51.56 lbf 2 2
a
i
F F ab
Existing friction
1
2
nom
ln ln 0. 3.010 28.
1.26 hp 33 000 33 000
1(1.2)
d
t
t fs s
f F
n H K
θ
This is a non-trivial point. The methodology preserved the factor of safety corresponding
to nd = 1_._ 1 even as we rounded b min up to b.
th
Decision #2 was taken care of with the adjustment of the center-to-center distance to
accommodate the belt loop. Use Eq. (17-2) as is and solve for C to assist in this.
Remember to subsequently recalculate θ d and θ D.
17-15 Decision set:
A priori decisions
Np = 10
6 belt passes
Design decisions
Preliminaries :
nom 5(1.25)(1.1)^ 6.875 hp
63 025(6.875) 385.2 lbf · in 1125
H (^) d H K ns d
Decision #1 : Choose a 60-in belt loop with a center-to-center distance of 20.3 in.
1
1
2sin 2.845 rad 2(20.3)
2sin 3.438 rad 2(20.3)
d
D
θ π
θ π
−
−
For full friction development:
exp( ) exp[0.32(2.845)] 2.
883.6 ft/min 12 12
56.67 kpsi
d
f
f
dn V
θ
π π
From selection step 3, p. 889,
th
Five groups of students could each be assigned a belt thickness. You can form a table
from their results or use the table given here.
t , in
0.002 0.003 0.005 0.008 0.
b 4.000 3.500 4.000 1.500 1.
CD 20.300 20.300 20.300 18.700 20.
a 109.700 131.900 110.900 194.900 221.
d 3.000 3.000 3.000 5.000 6.
D 9.000 9.000 9.000 15.000 18.
Fi 310.600 333.300 315.200 215.300 268.
F 1 439.000 461.700 443.600 292.300 332.
F 2 182.200 209.000 186.800 138.200 204.
nf s 1.100 1.100 1.100 1.100 1.
L 60.000 60.000 60.000 70.000 80.
f ′ 0.309 0.285 0.304 0.288 0.
Fi 301.200 301.200 301.200 195.700 166.
F 1 429.600 429.600 429.600 272.700 230.
F 2 172.800 172.800 172.800 118.700 102.
f 0.320 0.320 0.320 0.320 0.
The first three thicknesses result in the same adjusted Fi , F 1 and F 2 (why?). We have no
figure of merit, but the costs of the belt and pulleys are about the same for these three
thicknesses. Since the same power is transmitted and the belts are widening, belt forces
are lessening.
17-17 This is a design task. The decision variables would be belt length and belt section, which
could be combined into one, such as B90. The number of belts is not an issue.
We have no figure of merit, which is not practical in a text for this application. It is
suggested that you gather sheave dimensions and costs and V-belt costs from a principal
vendor and construct a figure of merit based on the costs. Here is one trial.
Preliminaries : For a single V-belt drive with H nom = 3 hp, n = 3100 rev/min, D = 12 in,
and d = 6_._ 2 in, choose a B90 belt, Ks = 1_._ 3 and nd = 1. From Table 17-10, select a
circumference of 90 in. From Table 17-11, add 1.8 in giving
Lp = 90 + 1_._ 8 = 91_._ 8 in
Eq. (17-16 b ):
2 2 0.25 91.8 (12 6.2) 91.8 (12 6.2) 2(12 6.2) 2 2
31.47 in
π π
th
2sin 2.9570 rad 2(31.47)
θ (^) d π
exp( ) exp[0.5123(2.9570)] 4.
5031.8 ft/min 12 12
f d
dn V
θ
π π
Table 17-13:
Angle θ θ (^) d (2.957 rad) 169. π π
The footnote regression equation of Table 17-13 gives K 1 without interpolation:
2 = 0_._ 9767
The design power is
Hd = H nom Ksnd = 3(1_._ 3)(1) = 3_._ 9 hp
From Table 17-14 for B90, K 2 = 1. From Table 17-12 take a marginal entry of H tab = 4,
although extrapolation would give a slightly lower H tab.
Eq. (17-17): Ha = K 1 K 2 H tab = 0_._ 9767(1)(4) = 3_._ 91 hp
The allowable ∆ Fa is given by
25.6 lbf ( / 2) 3100(6.2 / 2)
a a
n d
The allowable torque Ta is
79.4 lbf · in 2 2
a a
F d T
From Table 17-16, Kc = 0_._ 965. Thus, Eq. (17-21) gives,
2 2
0.965 24.4 lbf 1000 1000
c c
At incipient slip, Eq. (17-9) provides:
exp( ) 1 79.4 4.5489 1 20.0 lbf exp( ) 1 6.2 4.5489 1
i
T f F d f
θ
θ
Eq. (17-10):
th
1 2
1 2 10
9.99 lbf/belt, 24.4 lbf/belt
( ) 92.9 lbf/belt, ( ) 48 lbf/belt
133.7 lbf/belt, 88.8 lbf/belt
2.39(10 ) passes, 605 600 h
i c
b b
P
N t
Initial tension of the drive:
( Fi )drive = NbFi = 2(9_._ 99) = 20 lbf
17-18 Given: two B85 V-belts with d = 5_._ 4 in, D = 16 in, n = 1200 rev/min, and Ks = 1_._ 25
Table 17-11: Lp = 85 + 1_._ 8 = 86_._ 8 in
Eq. (17-17 b ):
2 2 0.25 86.8 (16 5.4) 86.8 (16 5.4) 2(16 5.4) 2 2
26.05 in.
Ans
π π
Eq. (17-1) in degrees:
180 2sin 156. 2(26.05)
θ (^) d
From Table 17-13 footnote:
2 = 0_._ 944
Table 17-14: K 2 = 1
Belt speed:
1696 ft/min 12
π = =
Use Table 17-12 to interpolate for H tab_._
Eq. (17-17) for two belts: H (^) a = K K N H 1 2 b tab = 0.944(1)(2)(2.31) =4.36 hp
Assuming nd = 1,
Hd = KsH nom nd = 1_._ 25(1) H nom
For a factor of safety of one,
tab
1.59 (1696 1000) 2.31 hp/belt 2000 1000
th
nom
nom
3.49 hp.
H a Hd
H Ans
17-19 Given: H nom = 60 hp, n = 400 rev/min, d = D = 26 in on 12 ft centers.
From Table 17-15, a conservative service factor of KS = 1_._ 4 is selected.
Design task: specify V-belt and number of strands (belts). Tentative decision : Use D
belts.
Table 17-11: Lp = 360 + 3_._ 3 = 363_._ 3 in
Eq. (17-16 b ):
2 2 0.25 363.3 (26 26) 363.3 (26 26) 2(26 26) 2 2
140.8 in (nearly 144 in)
π π
, , exp[0.5123 ] 5.0,
2722.7 ft/min 12 12
d D
dn V
θ π θ π π
π π
Table 17-13: For θ = 180°, K 1 = 1
Table 17-14: For D360, K 2 = 1_._ 10
Table 17-12: H tab = 16_._ 94 hp by interpolation
Thus, Ha = K 1 K 2 H tab = 1(1_._ 1)(16_._ 94) = 18_._ 63 hp / belt
Eq. (17-19): Hd = H nom Ks nd = 60(1_._ 4)(1) = 84 hp
Number of belts, Nb
d b a
Round up to five belts. It is left to the reader to repeat the above for belts such as C
and E360.