
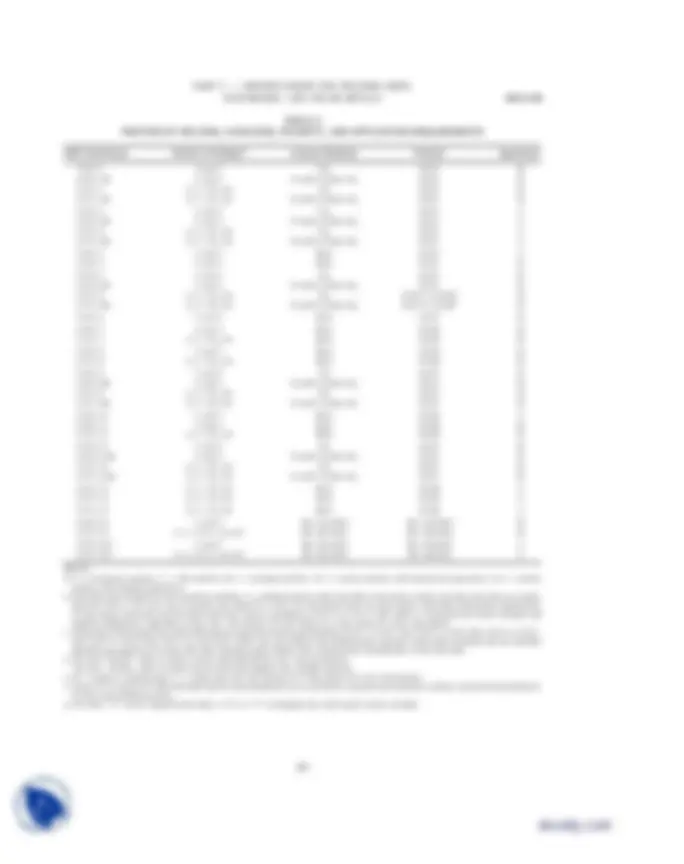
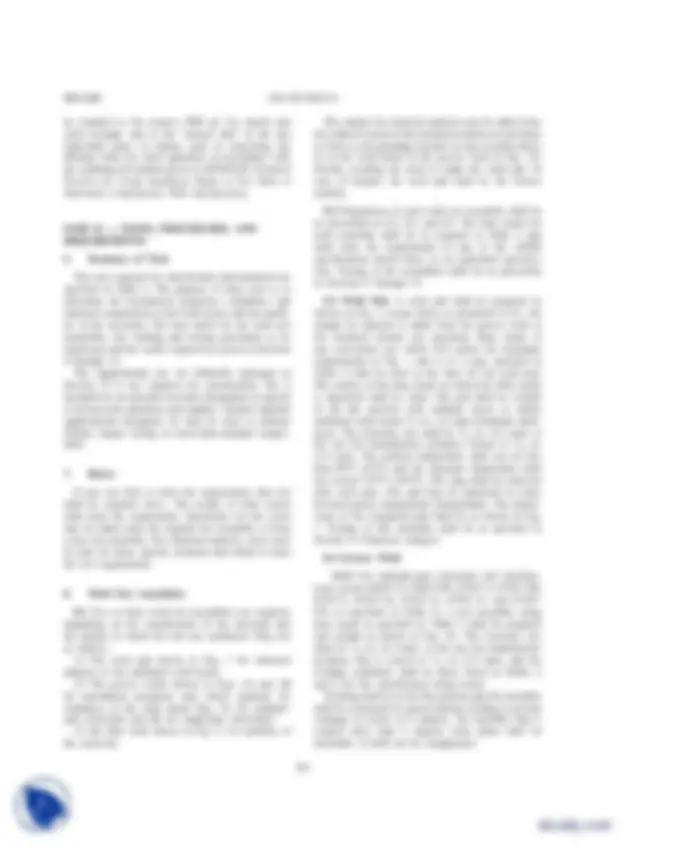
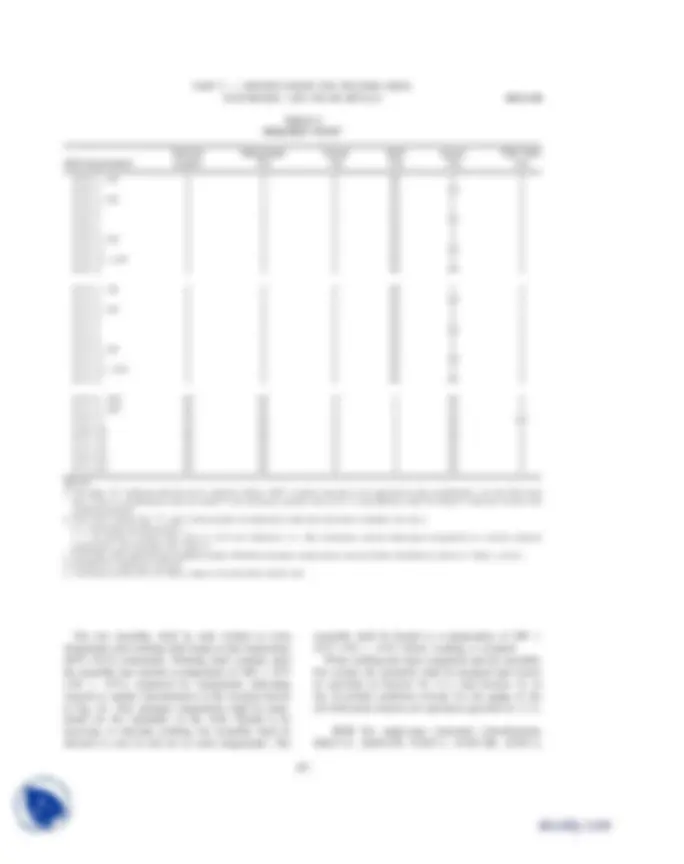
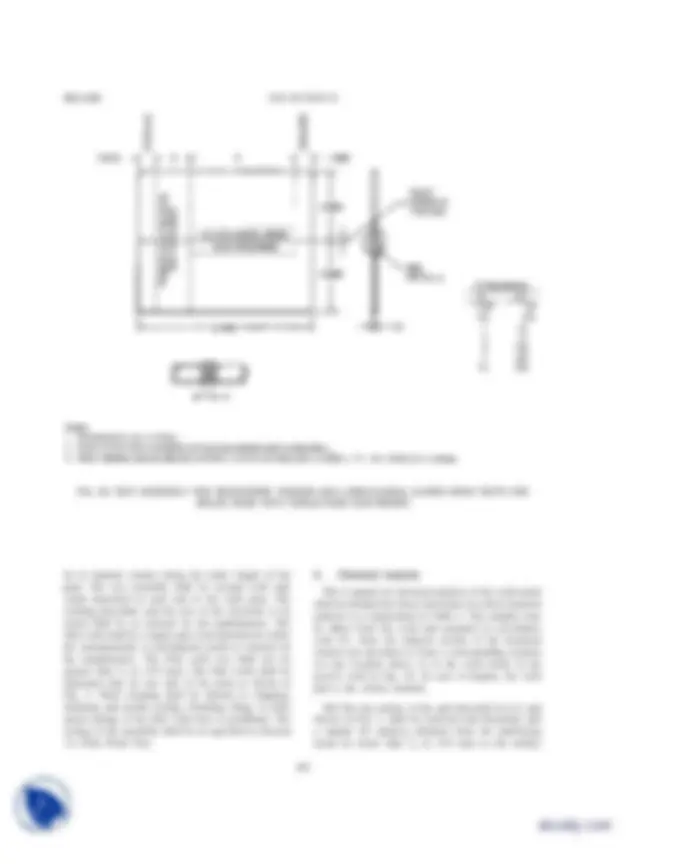
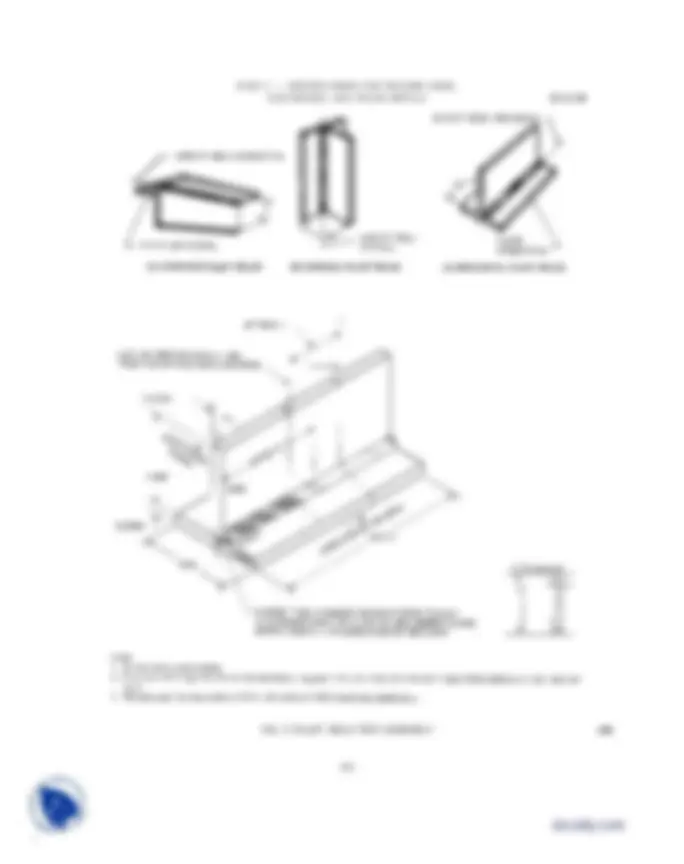
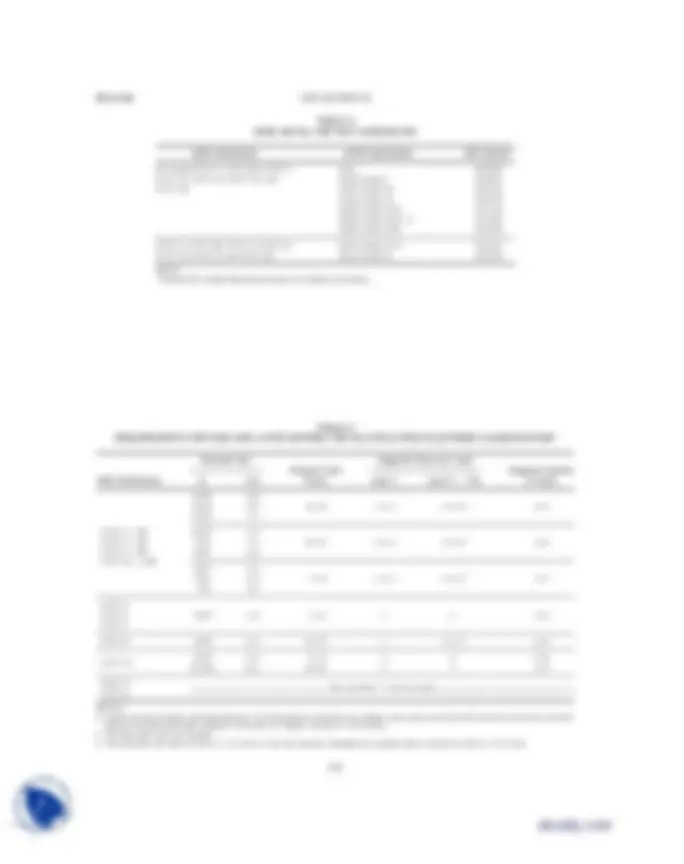
Study with the several resources on Docsity
Earn points by helping other students or get them with a premium plan
Prepare for your exams
Study with the several resources on Docsity
Earn points to download
Earn points by helping other students or get them with a premium plan
Community
Ask the community for help and clear up your study doubts
Discover the best universities in your country according to Docsity users
Free resources
Download our free guides on studying techniques, anxiety management strategies, and thesis advice from Docsity tutors
Dr. Ajitabh Sai delivered this lecture at Baba Farid University of Health Sciences for Mechanical and Materials Engineering Specifications course. It includes: Specification, Carbon, Steel, Electrodes, Flux, Corded, Arc, Welding, Test, Requirements, Procedures
Typology: Exercises
1 / 10
This page cannot be seen from the preview
Don't miss anything!
1. Scope
This specification prescribes requirements for the
classification of carbon steel electrodes for flux cored
arc welding.
PART A — GENERAL REQUIREMENTS
2. Classification
2.1 The electrodes covered by this specification are
classified according to the following:
(1) The as-welded mechanical properties of the weld
metal, as specified in Table 1
(2) Certain usability characteristics of the electrode
(including the presence or absence of shielding gas),
as specified in Table 2
(3) The positions of welding for which the electrodes
are suitable, as specified in Table 2
2.2 Electrodes classified under one classification shall
not be classified under any other classification in this
specification except for the EXXT-1, EXXT-1M,
EXXT-9, EXXT-9M, EXXT-12, and EXXT-12M classi-
fications. In addition, an electrode classified with 100%
CO 2 shielding gas may also be classified with the “M”
designator. The “M” designator means that the electrode
has been classified with a 75-80% argon/balance CO 2
gas mixture.
2.3 The electrodes classified under this specification
are intended for flux cored arc welding either with or
without an external shielding gas. Electrodes intended
for use without external shielding gas, or with the shielding gas as specified in Table 2, are not prohibited
from use with any other process or shielding gas for
which they are found suitable.
3. Acceptance
Acceptance^1 of the welding electrodes shall be in accordance with the provisions of ANSI/AWS A5.01, Filler Metal Procurement Guidelines.
4. Certification
By affixing the AWS specification and classification designations to the packaging, or the classification designations to the product, the manufacturer certifies that the product meets the requirements of this specifi- cation.^2
5. Units of Measure and Rounding-Off Procedure
5.1 U.S. customary units are the standard units of measure in this specification. The SI units are given as equivalent values to the U.S. customary units. The standard sizes and dimensions in the two systems are not identical and, for this reason, conversion from a standard size or dimension in one system will not always coincide with a standard size or dimension in the other. Suitable conversions, encompassing standard sizes of both, can be made, however, if appropriate tolerances are applied in each case.
5.2 For the purpose of determining conformance with this specification, an observed or calculated value shall
(^1) See Section A3, Acceptance (in the Appendix), for further informa- tion concerning acceptance, testing of the material shipped, and ANSI/AWS A5.01, Filler Metal Procurement Guidelines. (^2) See Section A4, Certification (in the Appendix), for further informa- tion concerning certification and the testing called for to meet this requirement.
Tensile Strength Yield Strength b Percent AWS Classification ksi MPa ksi MPa Elongationc^ Charpy V-Notch Impact Energy d
E7XT-1, -1M d^70 480 58 400 22 20 ft·lbf at 0°F (27 J at −18°C) E7XT-2, -2Me^70 480 Not Specified Not Specified Not Specified E7XT-3e^70 480 Not Specified Not Specified Not Specified E7XT-4 70 480 58 400 22 Not Specified E7XT-5, -5Md^70 480 58 400 22 20 ft·lbf at −20°F (27 J at −29°C) E7XT-6d^70 480 58 400 22 20 ft·lbf at −20°F (27 J at −29°C) E7XT-7 70 480 58 400 22 Not Specified E7XT-8d^70 480 58 400 22 20 ft·lbf at −20°F (27 J at −29°C) E7XT-9, -9Md^70 480 58 400 22 20 ft·lbf at − 20°F (27 J at −29°C) E7XT-10e^70 480 Not Specified Not Specified Not Specified E7XT-11 70 480 58 400 20 Not Specified E7XT-12, -12Md^ 70 to 90 480 to 620 58 400 22 20 ft·lbf at −20°F (27 J at −29°C) E6XT-13e^60 415 Not Specified Not Specified Not Specified E7XT-13e^70 480 Not Specified Not Specified Not Specified E7XT-14e^70 480 Not Specified Not Specified Not Specified E6XT-G 60 415 48 330 22 Not Specified E7XT-G 70 480 58 400 22 Not Specified E6XT-GSe^60 415 Not Specified Not Specified Not Specified E7XT-GSe^70 480 Not Specified Not Specified Not Specified
NOTES: a. Single values are minimums. b. 0.2% offset. c. In 2 in. (50 mm) gage length (see Section 11). In 1 in. (25 mm) gage length for 0.045 in. (1.1 mm) and smaller sizes of EXXT- classification. d. Electrodes with the following optional supplemental designations shall meet the lower temperature impact requirements specified below:
Electrode AWS Classification Designation Charpy V-Notch Impact Requirements E7XT-1, -1M E7XT-1J, -1MJ 20 ft·lbf at −40°F (27 J at −40°C) E7XT-5, -5M E7XT-5J, -5MJ 20 ft·lbf at −40°F (27 J at −40°C) E7XT-6 E7XT-6J 20 ft·lbf at −40°F (27 J at −40°C) E7XT-8 E7XT-8J 20 ft·lbf at −40°F (27 J at −40°C) E7XT-9, -9M E7XT-9J, -9MJ 20 ft·lbf at −40°F (27 J at −40°C) E7XT-12, -12M E7XT-12J, -12MJ 20 ft·lbf at −40°F (27 J at −40°C)
e. These classifications are intended for single pass welding. They are not for multiple pass welding. Only tensile strength is specified and, for this reason, only transverse tension and longitudinal guided bend tests are required (see Table 3).
be rounded to the nearest 1000 psi for tensile and
yield strength, and to the “nearest unit” in the last
right-hand place of figures used in expressing the limiting value for other quantities in accordance with
the rounding-off method given in ASTM E29, Standard
Practice for Using Significant Digits in Test Data to
Determine Conformance With Specifications.
PART B — TESTS, PROCEDURES, AND
REQUIREMENTS
6. Summary of Tests
The tests required for classification determination are
specified in Table 3. The purpose of these tests is to
determine the mechanical properties, soundness, and
chemical composition of the weld metal, and the usabil-
ity of the electrode. The base metal for the weld test
assemblies, the welding and testing procedures to be
employed, and the results required are given in Sections
8 through 14.
The supplemental test for diffusible hydrogen in
Section 15 is not required for classification, but is
included for an optional electrode designation as agreed
to between the purchaser and supplier. Another optional
supplemental designator (J) may be used to indicate
Charpy impact testing at lower-than-standard temper- ature.
7. Retest
If any test fails to meet the requirement, that test
shall be repeated twice. The results of both retests
shall meet the requirement. Specimens for the retest
may be taken from the original test assembly or from
a new test assembly. For chemical analysis, retest need
be only for those specific elements that failed to meet
the test requirements.
8. Weld Test Assemblies
8.1 Two or three weld test assemblies are required,
depending on the classification of the electrode and
the manner in which the tests are conducted. They are
as follows:
(1) The weld pad shown in Fig. 1 for chemical
analysis of the undiluted weld metal
(2) The groove welds shown in Figs. 2A and 2B
for mechanical properties and, where required, for
soundness of the weld metal (Fig. 2A for multiple- pass electrodes and 2B for single-pass electrodes)
(3) the fillet weld shown in Fig. 3, for usability of
the electrode
The sample for chemical analysis may be taken from the reduced section of the fractured tension test specimen or from a corresponding location (or any location above it) in the weld metal in the groove weld in Fig. 2A, thereby avoiding the need to make the weld pad. In case of dispute, the weld pad shall be the referee method.
8.2 Preparation of each weld test assembly shall be as prescribed in 8.3, 8.4, and 8.5. The base metal for each assembly shall be as required in Table 4 and shall meet the requirements of any of the ASTM specifications shown there, or an equivalent specifica- tion. Testing of the assemblies shall be as prescribed in Sections 9 through 14.
8.3 Weld Pad. A weld pad shall be prepared as shown in Fig. 1 except when, as permitted in 8.1, the sample for analysis is taken from the groove weld or the fractured tension test specimen. Base metal of any convenient size which will satisfy the minimum requirements of Fig. 1 and is of a type specified in Table 4 shall be used as the base for the weld pad. The surface of the base metal on which the filler metal is deposited shall be clean. The pad shall be welded in the flat position with multiple layers to obtain undiluted weld metal (^1 ⁄ 2 in. [13 mm] minimum thick- ness). The electrode size shall be 3 ⁄ 32 in. (2.4 mm) or the size the manufacturer produces closest to 3 ⁄ 32 in. (2.4 mm). The preheat temperature shall not be less than 60°F (16°C) and the interpass temperature shall not exceed 325°F (163°C). The slag shall be removed after each pass. The pad may be quenched in water between passes (temperature unimportant). The dimen- sions of the completed pad shall be as shown in Fig.
8.4 Groove Weld
8.4.1 For multiple-pass electrodes (all classifica- tions except E6XT-13, E6XT-GS, E7XT-2, E7XT-2M, E7XT-3, E7XT-10, E7XT-13, E7XT-14, and E7XT- GS, as specified in Table 3), a test assembly using base metal as specified in Table 4 shall be prepared and welded as shown in Fig. 2A. The electrode size shall be 3 ⁄ 32 in. (2.4 mm), or the size the manufacturer produces that is closest to 3 ⁄ 32 in. (2.4 mm), and the welding conditions shall be those listed in Tables 2 and 5 for the classification being tested. Welding shall be in the flat position and the assembly shall be restrained (or preset) during welding to prevent warpage in excess of 5 degrees. An assembly that is warped more than 5 degrees from plane shall be discarded. It shall not be straightened.
Chemical Radiographic Tension Bend Impact Fillet Weld AWS Classificationb,c^ Analysis Test Test Test Test Test
EX0T-1, -1M R R R NR R R EX0T-4 R R R NR NR R EX0T-5, -5M R R R NR R R EX0T-6 R R R NR R R EX0T-7 R R R NR NR R EX0T-8 R R R NR R R EX0T-9, -9M R R R NR R R EX0T-11 R R R NR NR R EX0T-12, -12M R R R NR R R EX0T-G R R R NR NR R
EX1T-1, -1M R R R NR R R EX1T-4 R R R NR NR R EX1T-5, -5M R R R NR R R EX1T-6 R R R NR R R EX1T-7 R R R NR NR R EX1T-8 R R R NR R R EX1T-9, -9M R R R NR R R EX1T-11 R R R NR NR R EX1T-12, -12M R R R NR R R EX1T-G R R R NR NR R
EX0T-2, -2M d^ NR NR R e^ R NR R EX1T-2, -2Md^ NR NR R e^ R NR R EX0T-3d^ NR NR R e^ R NR NR EX0T-10d^ NR NR R e^ R NR R EX1T-13d^ NR NR R e^ R NR R EX1T-14d^ NR NR R e^ R NR R EX0T-GSd^ NR NR R e^ R NR R EX1T-GSd^ NR NR R e^ R NR R
NOTES: a. The letter “R” indicates that the test is required. Where “NR” is shown, the test is not required for that classification. For the fillet weld test, EXOT-X classifications shall be tested in the horizontal position and EX1T-X classifications shall be tested in both the vertical and overhead positions. b. The 0 and 1 before the “T” refer to the position of welding for which the electrode is suitable. See A2.2. 0 p horizontal and flat position. 1 p all position (smaller than 3/32 in. (2.4 mm) diameter), i.e., flat, horizontal, vertical (downward progression) or vertical (upward progression), and overhead (see Table 2). c. Electrodes with supplemental toughness and/or diffusible hydrogen requirements may be further identified as shown in Tables 1 and 8. d. Intended for single-pass welding. e. Transverse tension test. All others require all-weld-metal tension test.
The test assembly shall be tack welded at room
temperature and welding shall begin at that temperature
(60°F [16°C] minimum). Welding shall continue until
the assembly has reached a temperature of 300 6 25°F
(150 6 14°C), measured by temperature indicating
crayons or surface thermometers at the location shown
in Fig. 2A. This interpass temperature shall be main- tained for the remainder of the weld. Should it be
necessary to interrupt welding, the assembly shall be
allowed to cool in still air at room temperature. The
assembly shall be heated to a temperature of 300 6 25°F (150 6 14°C) before welding is resumed. When welding has been completed and the assembly has cooled, the assembly shall be prepared and tested, as specified in Section 10, 11.1, and Section 13, in the as-welded condition (except for the aging of the all-weld-metal tension test specimen specified in 11.1).
8.4.2 For single-pass electrodes (classifications E6XT-13, E6XT-GS, E7XT-2, E7XT-2M, E7XT-3,
be in intimate contact along the entire length of the
joint. The test assembly shall be secured with tack
welds deposited at each end of the weld joint. The
welding procedure and the size of the electrode to be
tested shall be as selected by the manufacturer. The
fillet weld shall be a single-pass weld deposited in either
the semiautomatic or mechanized mode as selected by
the manufacturer. The fillet weld size shall not be
greater than 3 ⁄ 8 in. (9.5 mm). The fillet weld shall be
deposited only on one side of the joint as shown in
Fig. 3. Weld cleaning shall be limited to chipping,
brushing, and needle scaling. Grinding, filing, or other
metal cutting of the fillet weld face is prohibited. The
testing of the assembly shall be as specified in Section
14, Fillet Weld Test.
9. Chemical Analysis
9.1 A sample for chemical analysis of the weld metal shall be obtained for those electrodes for which chemical analysis is a requirement in Table 3. The samples may be taken from the weld pad prepared in accordance with 8.3, from the reduced section of the fractured tension test specimen or from a corresponding location (or any location above it) in the weld metal in the groove weld in Fig. 2A. In case of dispute, the weld pad is the referee method.
9.2 The top surface of the pad described in 8.3, and shown in Fig. 1, shall be removed and discarded, and a sample for analysis obtained from the underlying metal no closer than 3 ⁄ 8 in. (9.5 mm) to the surface
AWS Classification ASTM Specification UNS Number*
All except E7XT-2, E7XT-2M, E7XT-3, A36, K E7XT-10, E7XT-13, E7XT-14, and A285 Grade C, K E7XT-GS A515 Grade 70, K A516 Grade 70, K A830 Grade 1015, G A830 Grade 1018, or G A830 Grade 1020 G
E7XT-2, E7XT-2M, E7XT-3, E7XT-10, A515 Grade 70 or K E7XT-13, E7XT-14 and E7XT-GS A516 Grade 70 K NOTE: *SAE/ASTM Unified Numbering System for Metals and Alloys.
Electrode Size Suggested Passes per Layer Required Total Suggested Number AWS Classification in. mm Passes Layer 1 Layer 2 — Top of Layers
0.030 0. 0.035 0.9 12–19 1 or 2 2 or 3 b^ 6– 0.045 1.
0.052 1. 1/16 1.6 10–17 1 or 2 2 or 3 b^ 5– 5/64 2.
3/32 2. 7/64 2.8 7–14 1 or 2 2 or 3 b^ 4– 1/8 3.
E7XT-6 3/32 c^ 2.4 7–11 1 2 4– E7XT-
E7XT-8 3/32 c^ 2.4 12–17 1 2 or 3 6–
3/32c^ 2.4 7–11 1 2 4– E7XT- ≤0.045 ≤1.1 18–27 2 3 6–
E6XT-G Not Specified, To Be Recorded E7XT-G
NOTES: a. Actual number of passes, electrode diameter, wire feed speed or amperes, arc voltage, travel speed, and electrode extension (electrical stickout) shall be recorded and made available to the user on request. See A6.2 in the Annex. b. The final layer may be 4 passes. c. The electrode size shall be 3/32 in. (2.4 mm) or the size that the manufacturer produces that is closest to 3/32 in. (2.4 mm).