
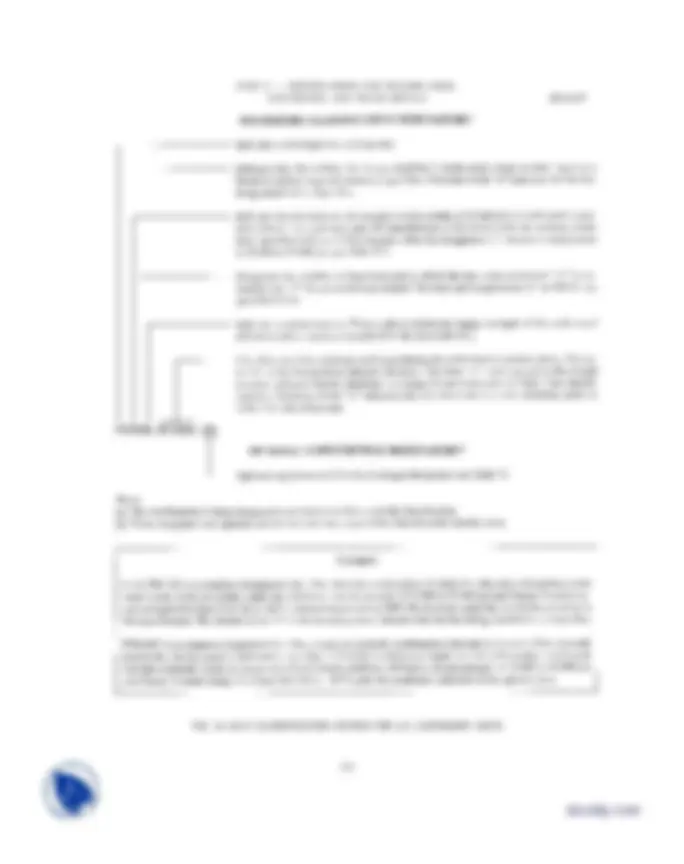
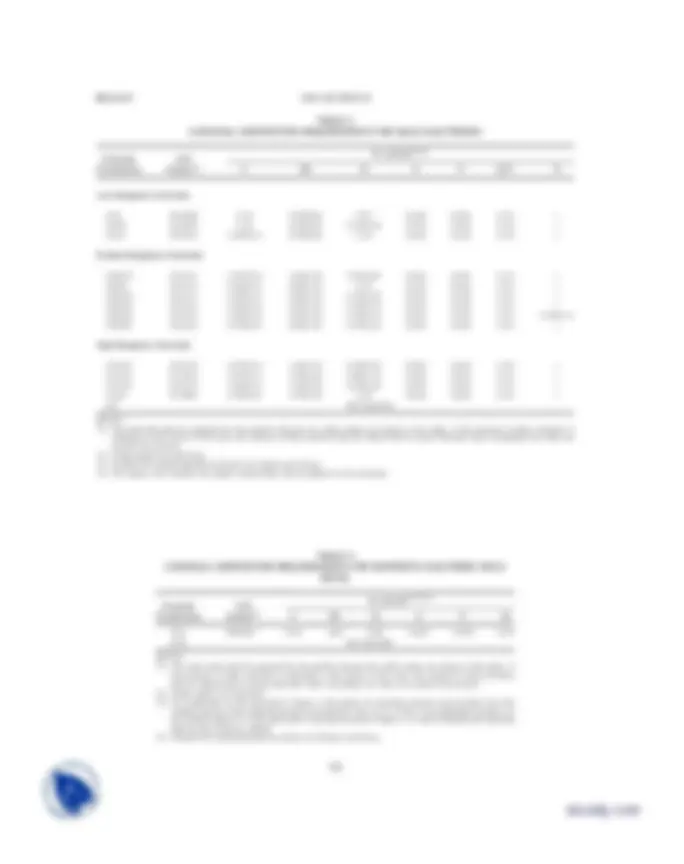
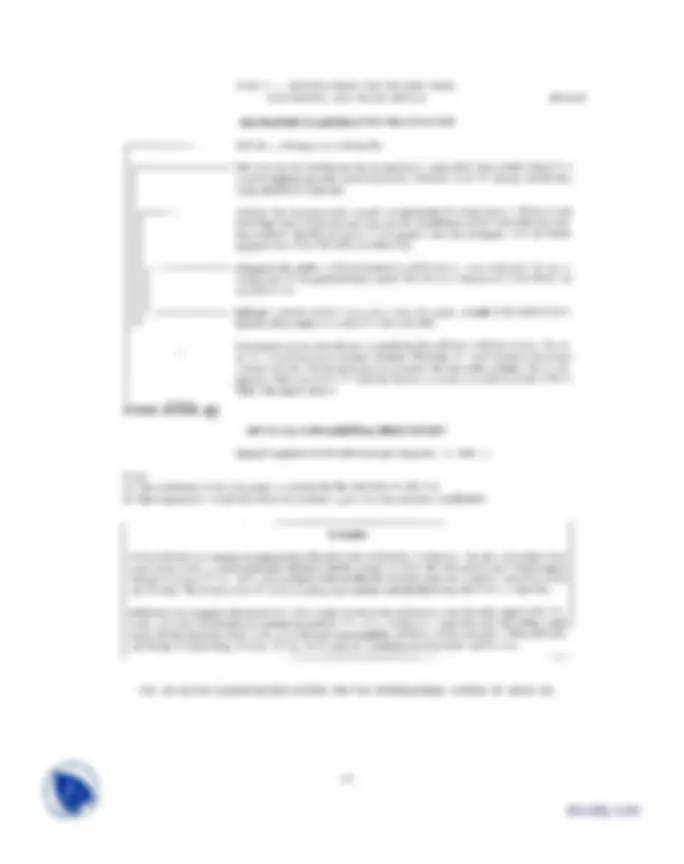
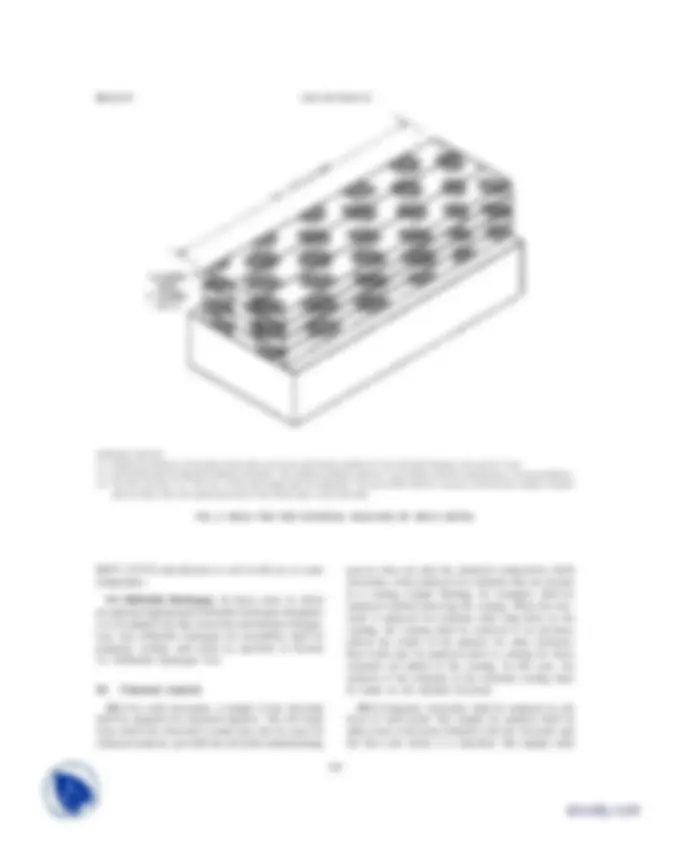
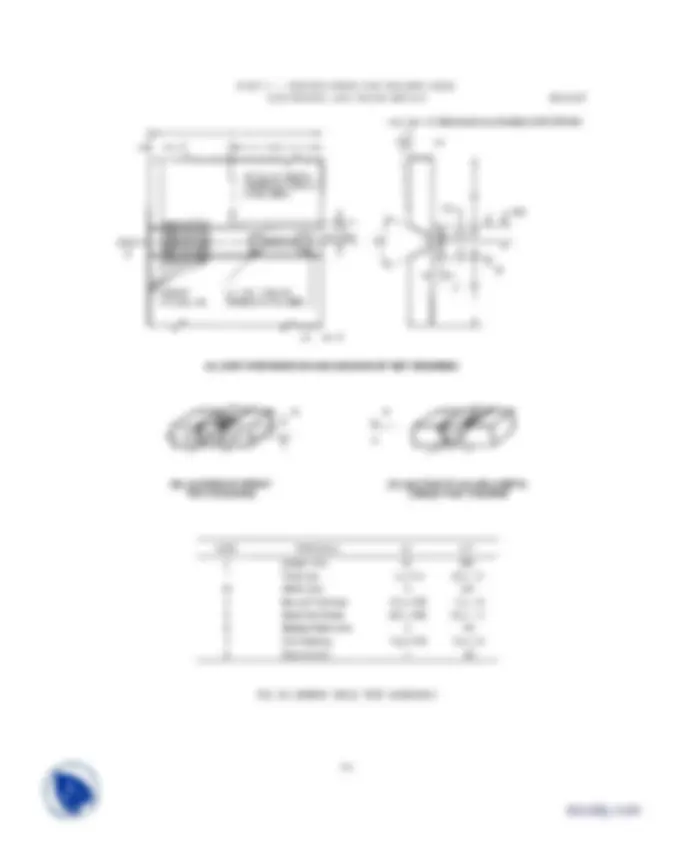
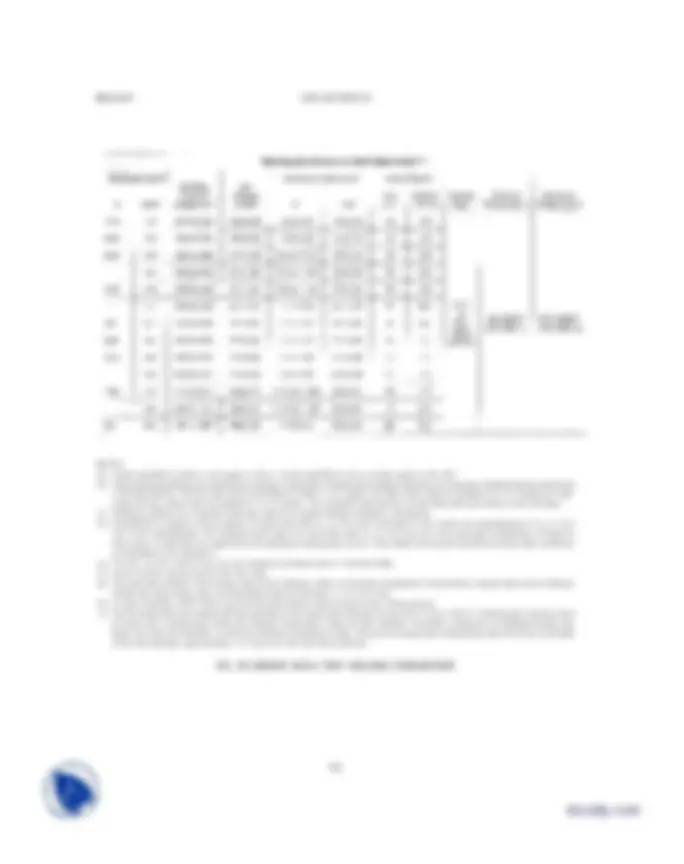
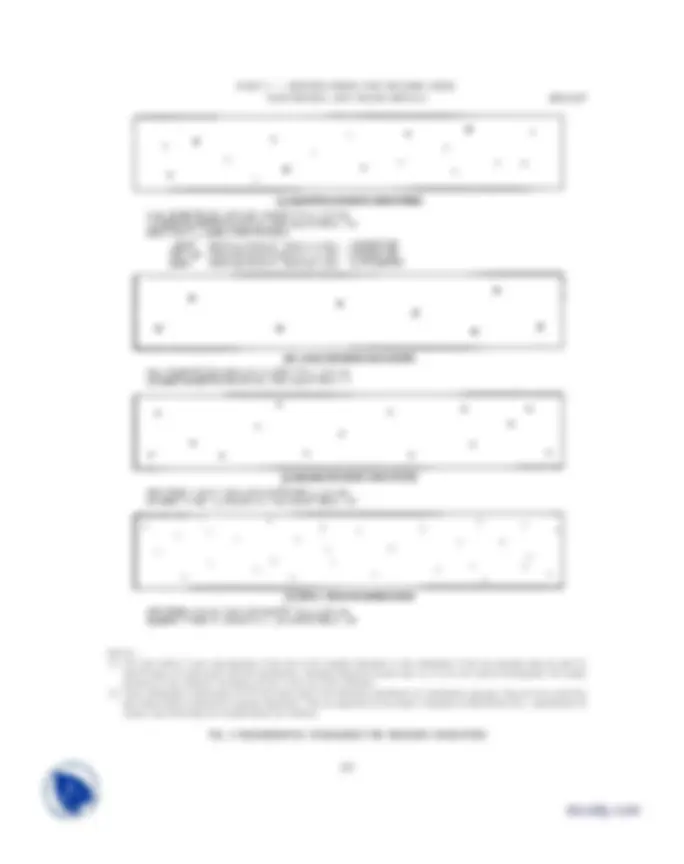
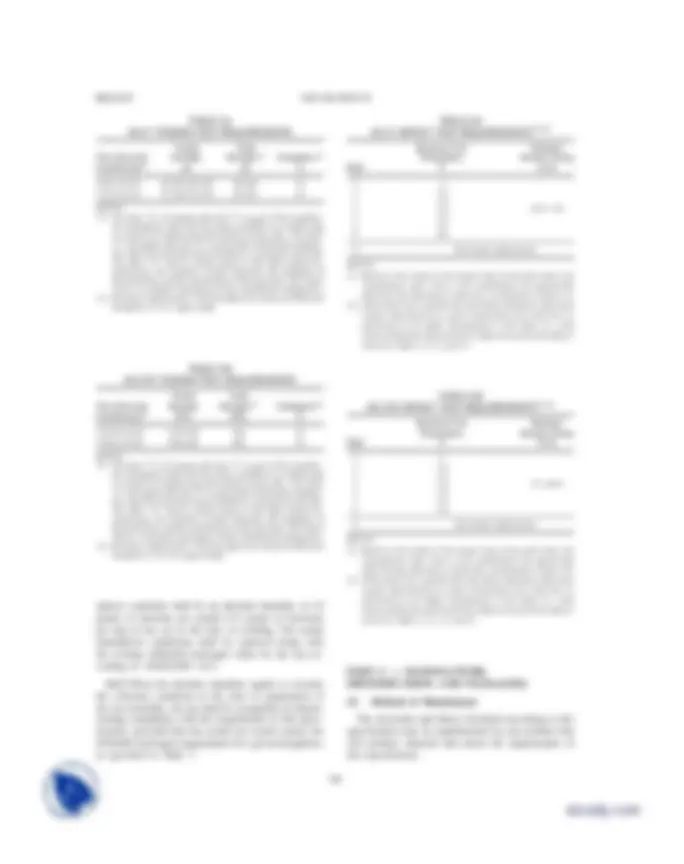
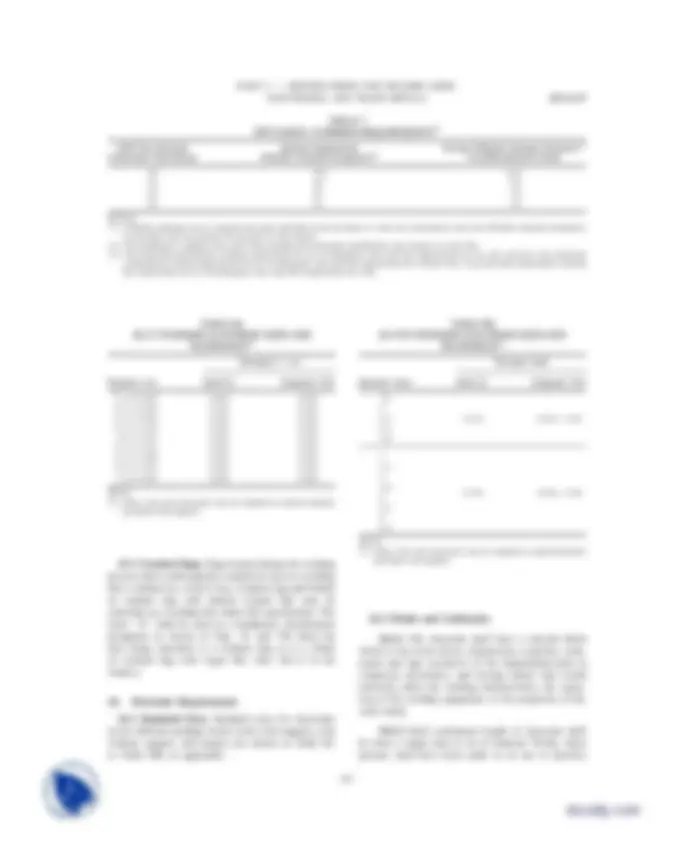
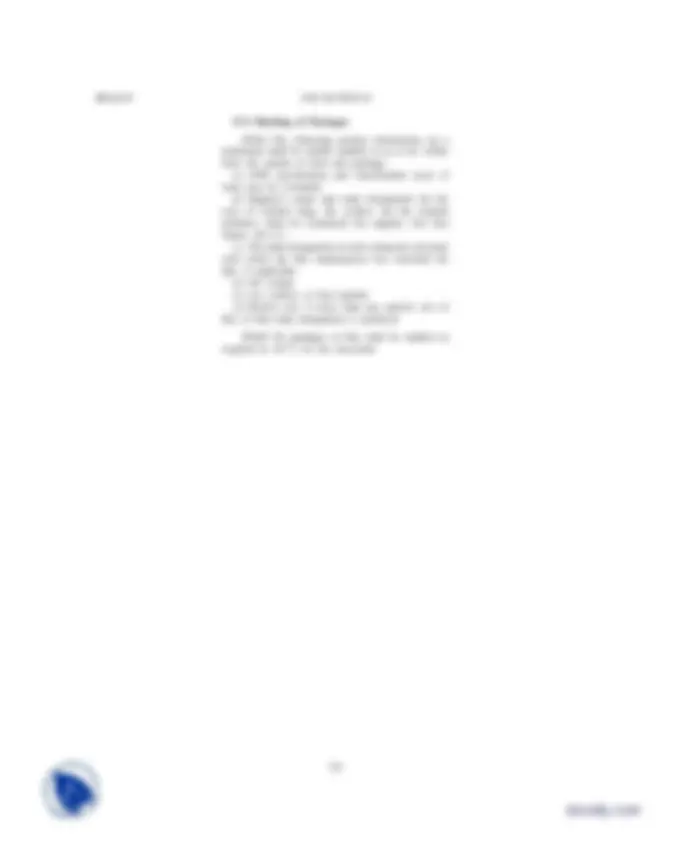
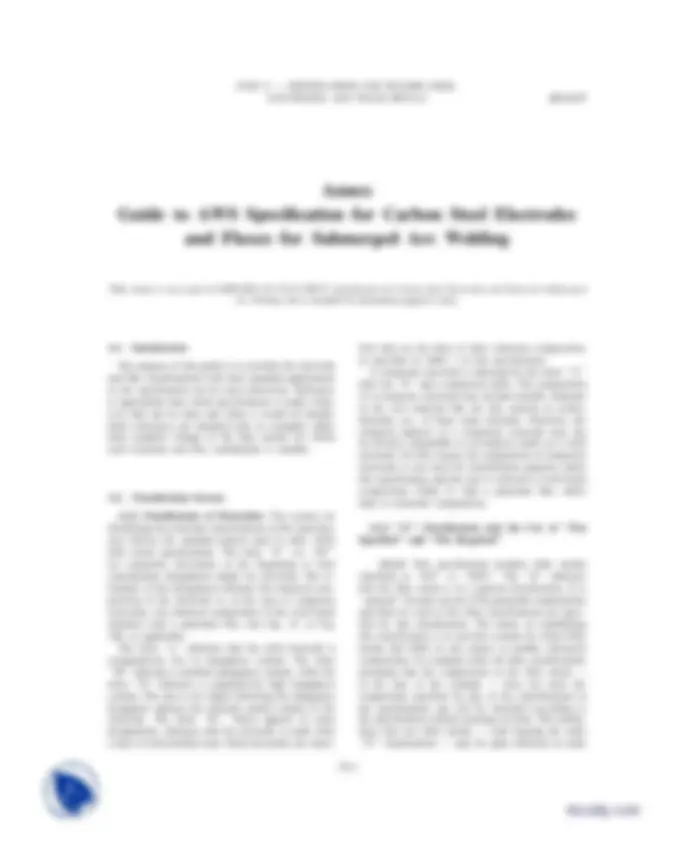
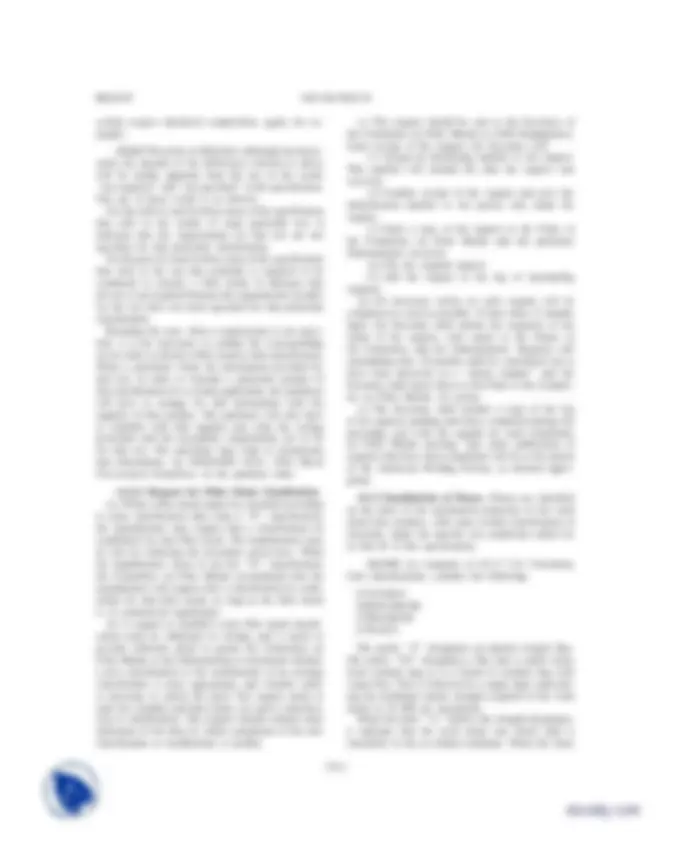
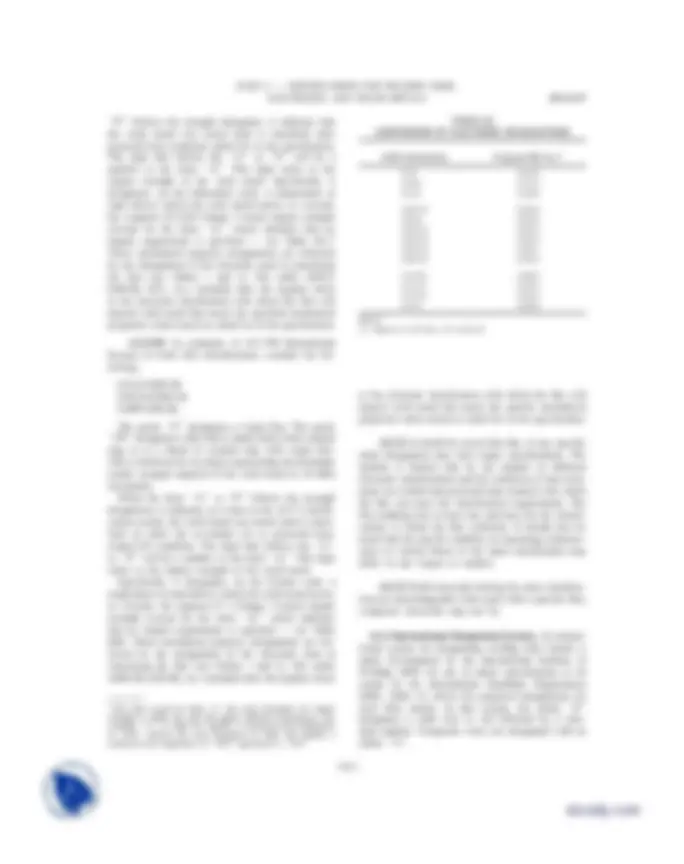
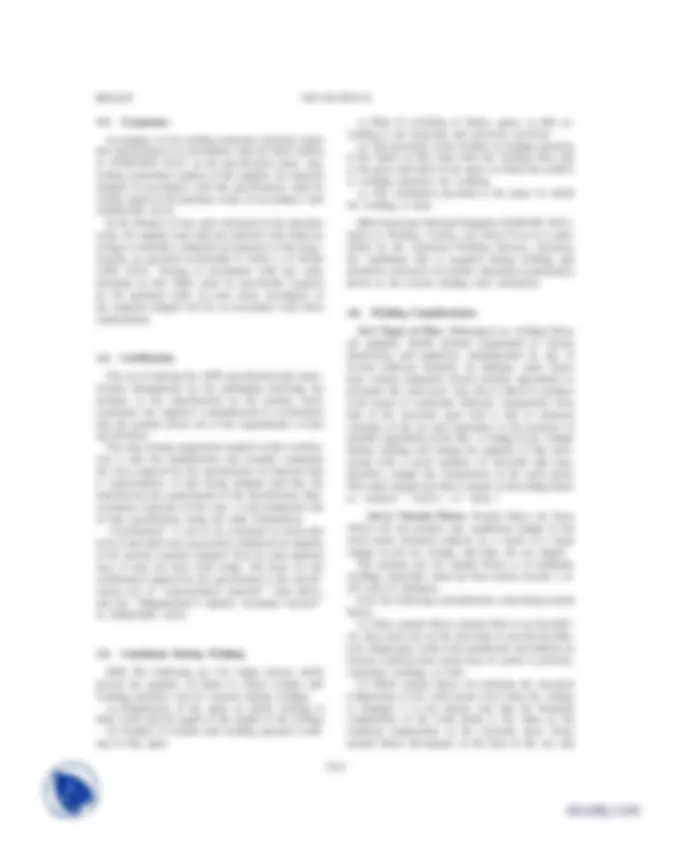
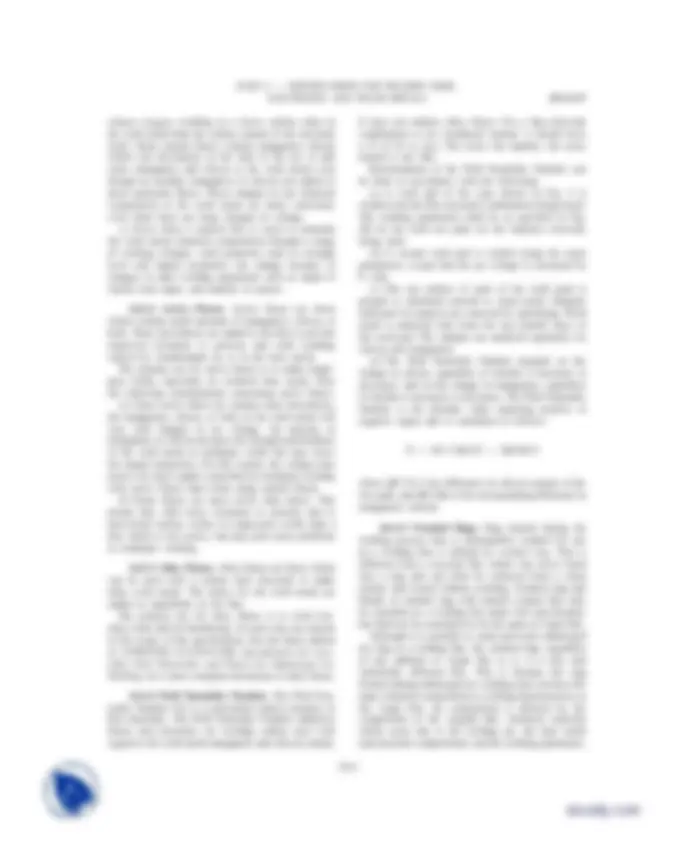
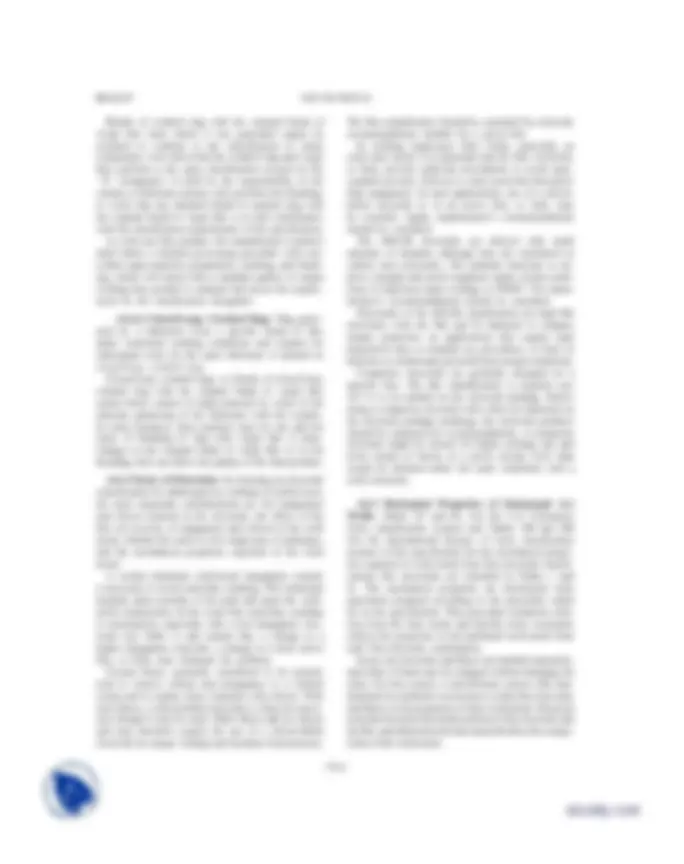
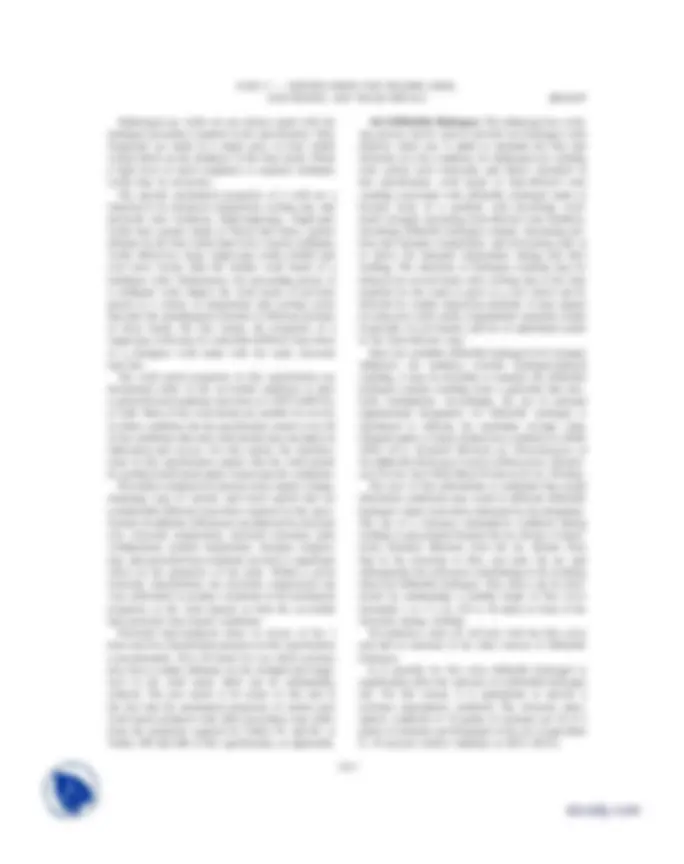
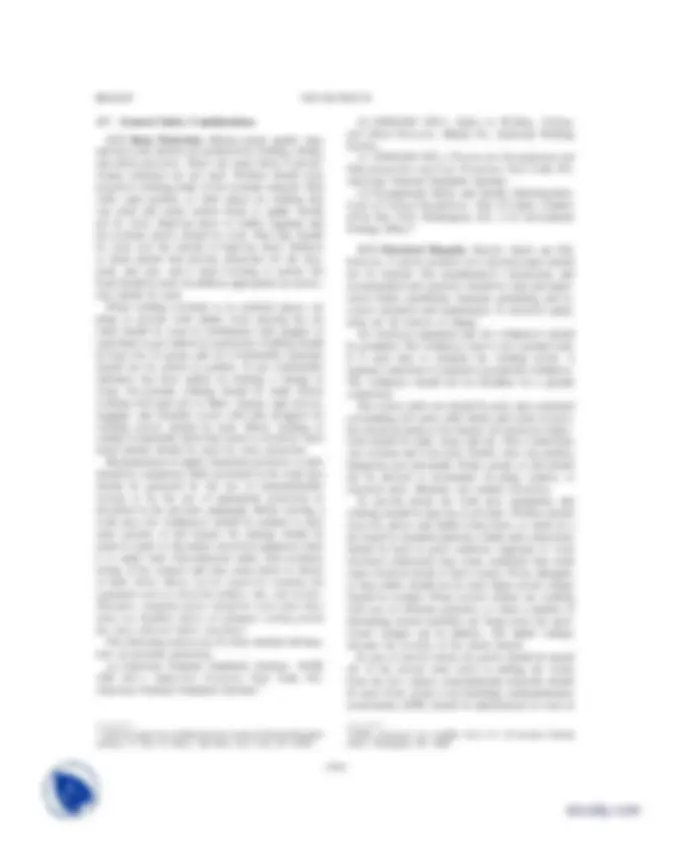
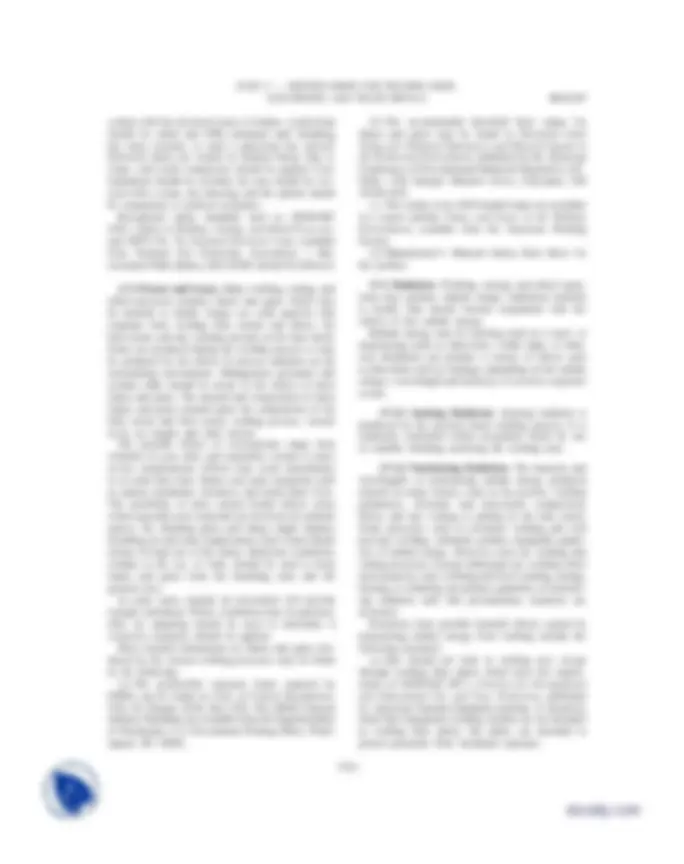
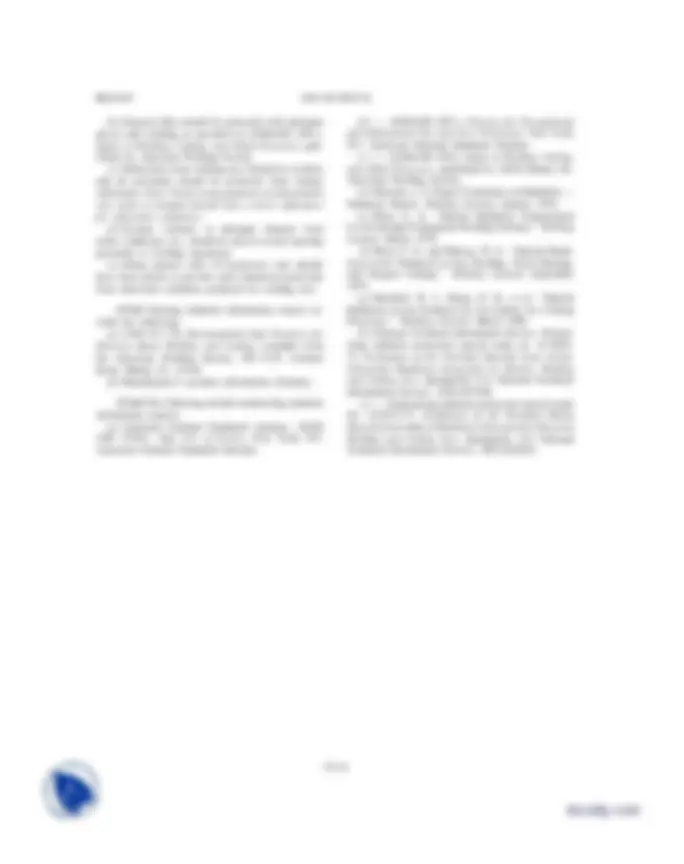
Study with the several resources on Docsity
Earn points by helping other students or get them with a premium plan
Prepare for your exams
Study with the several resources on Docsity
Earn points to download
Earn points by helping other students or get them with a premium plan
Community
Ask the community for help and clear up your study doubts
Discover the best universities in your country according to Docsity users
Free resources
Download our free guides on studying techniques, anxiety management strategies, and thesis advice from Docsity tutors
Dr. Ajitabh Sai delivered this lecture at Baba Farid University of Health Sciences for Mechanical and Materials Engineering Specifications course. It includes: Specification, Carbon, Steel, Electrodes, Fluxes, Submerged, Arc, Welding, Test, Requirements, Procedures
Typology: Exercises
1 / 28
This page cannot be seen from the preview
Don't miss anything!
(Identical with AWS Specification A5.17/A5.17M-97.)
1. Scope
This specification prescribes requirements for the classification of carbon steel electrodes (both solid and composite) and fluxes for submerged arc welding. This document is the first of the A5.17 specifications which is a combined specification providing for classifi- cation utilizing a system based upon U.S. Customary Units, or utilizing a system based upon the International System of Units (SI). The measurements are not exact equivalents; therefore, each system must be used inde- pendently of the other, without combining values in any way. In selecting rational metric units, ANSI/AWS A1.1, Metric Practice Guide for the Welding Industry, is used where suitable. Tables and figures make use of both U.S. Customary Units and SI Units which, with the application of the specified tolerances, provides for interchangeability of products in both U.S. Custom- ary and SI Units. (a) Paragraphs, tables and figures which carry the suffix letter ‘‘U’’ are applicable only to those products classified to the system based upon U.S. Customary Units under the A5.17 specification. (b) Paragraphs, tables and figures which carry the suffix letter ‘‘M’’ are applicable only to those products classified to the system based upon the International System of Units (SI), under the A5.17M specification. (c) Paragraphs, tables and figures which do not have either the suffix letter ‘‘U’’ or the suffix letter ‘‘M’’are applicable to those products classified under either the U.S. Customary Units System or the International Sys- tem of Units (SI).
353
2. Normative References 2.1 The following ANSI/AWS standards 1 are refer- enced in the mandatory sections of this document: (a) ANSI/AWS A1.1, Metric Practice Guide for the Welding Industry. (b) ANSI/AWS A4.3, Standard Methods for Determi- nation of the Diffusible Hydrogen Content of Marten- sitic, Bainitic, and Ferritic Steel Weld Metal Produced by Arc Welding. (c) ANSI/AWS A5.01, Filler Metal Procurement Guidelines. (d) ANSI/AWS A5.1, Specification for Carbon Steel Electrodes for Shielded Metal Arc Welding. (e) ANSI/AWS B4.0, Standard Methods for Mechan- ical Testing of Welds.
2.2 The following ASTM standards 2 are referenced in the mandatory sections of this document: (a) ASTM A29/A29M, Specification for Steel Bars, Carbon and Alloy, Hot-Wrought and Cold-Finished. (b) ASTM A36/A36M, Specification for Carbon Structural Steel. (c) ASTM A285/A285M, Specification for Pressure Vessel Plates, Carbon Steel, Low- and Intermediate- Tensile Strength.
(^1) AWS standards may be obtained from the American Welding Society, 550 N.W. LeJeune Road, Miami, FL 33126. (^2) ASTM standards can be obtained from ASTM, 100 Barr Harbor Drive, West Conshohocken, PA 19428-2959.
A
SFA-5.17 1998 SECTION II
(d) ASTM A515/A515M, Specification for Pressure Vessel Plates, Carbon Steel, for Intermediate- and Higher-Temperature Service. (e) ASTM A516/A516M, Specification for Pressure Vessel Plates, Carbon Steel, for Moderate- and Lower- Temperature Service. (f) ASTM DS-56, SAE HS-1086, Metals and Alloys in the Unified Numbering System. (g) ASTM E29, Practice for Using Significant Digits in Test Data to Determine Conformance with Specifica- tions. (h) ASTM E142, Method for Controlling Quality of Radiographic Testing. (i) ASTM E350, Test Methods for Chemical Analysis of Carbon Steel, Low Alloy Steel, Silicon Electrical Steel, Ingot Iron and Wrought Iron.
2.3 The following ISO standards 3 are referenced in the mandatory section of this document. (a) ISO 864, Arc Welding — Solid and Tubular Cored Wires which Deposit Carbon and Carbon-Manganese Steel — Dimensions of Wires, Spools, Rims and Coils.
3. Classification
3.1U The welding electrodes and fluxes covered by the A5.17 specification utilize a classification system based upon U.S. Customary Units and are classified according to the following: (a) The mechanical properties of the weld metal obtained with a combination of a particular flux and a particular classification of electrode, as specified in Tables 5U and 6U. (b) The condition of heat treatment in which those properties are obtained, as specified in 9.4 (and shown in Fig. 1U). (c) The chemical composition of the electrode (for solid electrodes) as specified in Table 1, or the weld metal produced with a particular flux (for composite electrodes) as specified in Table 2.
3.1M The welding electrodes and fluxes covered by the A5.17M specification utilize a classification system based upon the International System of Units (SI) and are classified according to the following: (a) The mechanical properties of the weld metal obtained with a combination of a particular flux and a particular classification of electrode, as specified in Tables 5M and 6M.
(^3) ISO standards may be obtained from American National Standards Institute (ANSI), 11 West 42nd St., 13th Floor, New York, NY 10036-8002.
354
(b) The condition of heat treatment in which those properties are obtained, as specified in 9.4 (and shown in Fig. 1M). (c) The chemical composition of the electrode (for solid electrodes) as specified in Table 1, or the weld metal produced with a particular flux (for composite electrodes) as specified in Table 2. 3.2 Solid electrodes classified under one classification shall not be classified under any other classification in this specification, except that solid electrodes meeting the chemical composition requirements of both the EL and EL12 classifications (Table 1) may be given both classifications. Composite electrodes may be classified under more than one classifications when used with different fluxes. Fluxes may be classified under any number of classifications, for weld metal in either or both the as-welded and postweld heat-treated conditions, using different electrode classifications. Flux-electrode combinations may be classified under A5.17 with U.S. Customary Units, A5.17M using the International Sys- tem of Units (SI), or both. Flux-electrode combinations classified under both A5.17 and A5.17M must meet all requirements for classification under each system. The classification systems are shown in Figs. 1U and 1M. 3.3 The electrodes and fluxes classified under this specification are intended for submerged arc welding, but that is not to prohibit their use with any other process for which they are found suitable.
4. Acceptance Acceptance of the electrodes and fluxes shall be in accordance with the provisions of the latest edition of ANSI/AWS A5.01, Filler Metal Procurement Guide- lines (see Annex A3). 5. Certification By affixing the AWS specification and classification designations to the packaging or the classification to the product, the manufacturer certifies that the product meets the requirements of this specification (see Annex A4). 6. Units of Measure and Rounding-Off Procedure 6.1 This specification makes use of both U.S. Custom- ary Units and the International System of Units (SI). The measurements are not exact equivalents; therefore, each system must be used independently of the other
SFA-5.17 1998 SECTION II
TABLE 1 CHEMICAL COMPOSITION REQUIREMENTS FOR SOLID ELECTRODES
wt. percent (1) (2) Electrode UNS Classification Number (3)^ C Mn Si S P Cu (4)^ Ti
Low-Manganese Electrodes
EL8 K01008 0.10 0.25/0.60 0.07 0.030 0.030 0.35 — EL8K K01009 0.10 0.25/0.60 0.10/0.25 0.030 0.030 0.35 — EL12 K01012 0.04/0.14 0.25/0.60 0.10 0.030 0.030 0.35 —
Medium-Manganese Electrodes
EM11K K01111 0.07/0.15 1.00/1.50 0.65/0.85 0.030 0.025 0.35 — EM12 K01112 0.06/0.15 0.80/1.25 0.10 0.030 0.030 0.35 — EM12K K01113 0.05/0.15 0.80/1.25 0.10/0.35 0.030 0.030 0.35 — EM13K K01313 0.06/0.16 0.90/1.40 0.35/0.75 0.030 0.030 0.35 — EM14K K01314 0.06/0.19 0.90/1.40 0.35/0.75 0.025 0.025 0.35 0.03/0. EM15K K01515 0.10/0.20 0.80/1.25 0.10/0.35 0.030 0.030 0.35 —
High-Manganese Electrodes
EH10K K01210 0.07/0.15 1.30/1.70 0.05/0.25 0.025 0.025 0.35 — EH11K K11140 0.07/0.15 1.40/1.85 0.80/1.15 0.030 0.030 0.35 — EH12K K01213 0.06/0.15 1.50/2.00 0.25/0.65 0.025 0.025 0.35 — EH14 K11585 0.10/0.20 1.70/2.20 0.10 0.030 0.030 0.35 — EG Not Specified
NOTES: (1) The electrode shall be analyzed for the specific elements for which values are shown in this table. If the presence of other elements is indicated, in the course of this work, the amount of those elements shall be determined to ensure that their total (excluding iron) does not exceed 0.50 percent. (2) Single values are maximum. (3) SAE/ASTM Unified Numbering System for Metals and Alloys. (4) The copper limit includes any copper coating that may be applied to the electrode.
TABLE 2 CHEMICAL COMPOSITION REQUIREMENTS FOR COMPOSITE ELECTRODE WELD METAL
wt. percent (1) (2) (3) Electrode UNS Classification Number (4)^ C Mn Si S P Cu EC1 W06041 0.15 1.80 0.90 0.035 0.035 0. ECG Not Specified NOTES: (1) The weld metal shall be analyzed for the specific elements for which values are shown in this table. If the presence of other elements is indicated, in the course of this work, the amount of those elements shall be determined to ensure that their total (excluding iron) does not exceed 0.50 percent. (2) Single values are maximum. (3) As a substitute for the weld pad in Figure 2, the sample for chemical analysis may be taken from the reduced section of the fractured tension test specimen (see 12.1) or from a corresponding location (or any location above it) in the weld metal in the groove weld in Figure 3. In case of dispute, the weld pad shall be the reference method. (4) SAE/ASTM Unified Numbering System for Metals and Alloys.
356
PART C — SPECIFICATIONS FOR WELDING RODS, ELECTRODES, AND FILLER METALS SFA-5.
FIG. 1M A5.17M CLASSIFICATION SYSTEM FOR THE INTERNATIONAL SYSTEM OF UNITS (SI)
357
PART C — SPECIFICATIONS FOR WELDING RODS, ELECTRODES, AND FILLER METALS SFA-5.
the weld test assembly or test specimen(s) or in conduct- ing the test, the test shall be considered invalid, without regard to whether the test was actually completed or whether test results met, or failed to meet, the require- ment. That test shall be repeated, following proper prescribed procedures. In this case, the requirement for doubling the number of test specimens does not apply.
9. Weld Test Assemblies
9.1 Requirements for Classification
9.1.1 Classification of Solid Electrodes. No weld test assembly is required for classification of solid electrodes.
9.1.2 Classification of Composite Electrodes. The chemical analysis of weld metal produced with the composite electrode and a particular flux is required for classification of a composite electrode under this specification. The weld test assembly, shown in Fig. 2, is used to meet this requirement for the classification of composite electrodes. Figure 2 is the weld pad test assembly for chemical analysis of weld metal. As an alternative to the weld pad, the sample for chemical analysis of composite electrode weld metal may be taken from the groove weld in Fig. 3A. Note c to Table 2 allows the sample for chemical analysis in the case of a composite electrode to be taken from the reduced section of the fractured tension test specimen of Fig. 5 or from a corresponding location (or any location above it) in the weld metal in the groove weld in Fig. 3A. In case of dispute, the weld pad shall be the referee method.
9.1.3 Classification of Flux-Electrode Combina- tions. One groove weld test assembly is required for each classification of a flux-solid electrode combination or a flux-composite electrode combination. This is the groove weld in Fig. 3A for mechanical properties and soundness of weld metal.
9.2 Preparation. Preparation of each weld test assem- bly shall be as prescribed in 9.3 and 9.4. The base metal for the weld pad and groove weld assemblies shall be as required in Table 4 corresponding to the tests to be conducted and shall meet the requirements of the appropriate ASTM specification shown in Table 4, or an equivalent specification. Testing of the assem- blies shall be as prescribed in Sections 10 through 13.
9.3 Weld Pad. For composite electrodes only, a weld pad shall be prepared as specified in Fig. 2, except when either alternative in 9.1.2 is selected. Base metal of any convenient size, and of the type specified
359
in Table 4, shall be used as the base metal for the weld pad. The surface of the base metal on which the filler metal is deposited shall be clean. The pad shall be welded in the flat position, three passes per layer, four layers high, using the flux for which classification of the composite electrode is intended. The preheat temperature shall not be less than 60°F [15°C] and the interpass temperature shall not exceed 325°F [165°C]. The slag shall be removed after each pass. The pad may be quenched in water between passes but shall be dry before the start of each pass. Testing of this assembly shall be as specified in Section 10, Chemical Analysis.
9.4 Groove Weld for Mechanical Properties and Soundness. For classification of a flux-electrode combi- nation, a test assembly shall be prepared and welded as specified in Fig. 3A using base metal of the appro- priate type specified in Table 4. Prior to welding, the assembly may be preset so that the welded joint will be sufficiently flat to facilitate removal of the test specimens. As an alternative, restraint or a combination of restraint and presetting may be used to keep the welded joint within 5 degrees of plane. A welded test assembly that is more than 5 degrees out of plane shall be discarded. Straightening of the test assembly is prohibited. Testing shall be as specified in Sections 10 through 13, with the assembly in either the as- welded or the postweld heat-treated condition, according to the classification of the weld metal (See Figs. 1U and 1M). When the tests are to be conducted in each condition (as-welded and postweld heat treated), two such assem- blies, or one single assembly of sufficient length to provide the specimens required for both conditions, shall be prepared. In the latter case, the single assembly shall be cut transverse to the weld into two pieces; one of the pieces shall be tested in the as-welded condition, and the other piece shall be heat treated prior to testing. Any test assembly to be heat treated shall be heat treated at 1150 6 25°F [620 6 15°C] for one hour (−0, +15 minutes). The furnace shall be at a temperature not higher than 600°F [315°C] when the test assembly is placed in it. The heating rate, from that point to the 1150 6 25°F [620 6 15°C] holding temperature, shall not exceed 400°F per hour [220°C per hour]. When the holding time has been completed, the assembly shall be allowed to cool in the furnace to a temperature below 600°F [315°C] at a rate not exceeding 350°F per hour [195°C per hour]. The assembly may be removed from the furnace at any temperature below
SFA-5.17 1998 SECTION II
GENERAL NOTES: (1) Width and thickness of the base-metal plate may be any dimensions suitable for the electrode diameter and current in use. (2) Weld beads shall be deposited without oscillation. The welding conditions shall be in accordance with the manufacturer’s recommendations. (3) The first and last 2 in. [50 mm] of the weld length shall be discarded. The top surface shall be removed, and chemical analysis samples shall be taken from the underlying metal of the fourth layer of the weld pad.
FIG. 2 WELD PAD FOR CHEMICAL ANALYSIS OF WELD METAL
600°F [315°C] and allowed to cool in still air, to room temperature.
9.5 Diffusible Hydrogen. In those cases in which an optional supplemental diffusible hydrogen designator is to be added to the flux-electrode classification designa- tion, four diffusible hydrogen test assemblies shall be prepared, welded, and tested as specified in Section 14, Diffusible Hydrogen Test.
10. Chemical Analysis
10.1 For solid electrodes, a sample of the electrode shall be prepared for chemical analysis. The rod stock from which the electrode is made may also be used for chemical analysis, provided the electrode manufacturing
360
process does not alter the chemical composition. Solid electrodes, when analyzed for elements that are present in a coating (copper flashing, for example), shall be analyzed without removing the coating. When the elec- trode is analyzed for elements other than those in the coating, the coating shall be removed if its presence affects the results of the analysis for other elements. Rod stock may be analyzed prior to coating for those elements not added in the coating. In this case, the analysis of the elements in the electrode coating must be made on the finished electrode. 10.2 Composite electrodes shall be analyzed in the form of weld metal. The sample for analysis shall be taken from weld metal obtained with the electrode and the flux with which it is classified. The sample shall
SFA-5.17 1998 SECTION II
NOTES: (a) Values specified in inches or ipm apply to A5.17. Values specified in mm or mm/sec apply to A5.17M. (b) These welding conditions are intended for machine or automatic welding with straight progression (no weaving). Welding shall be performed in the flat position. The first layer shall be produced in either 1 or 2 passes. All other layers shall be produced in 2 or 3 passes per layer except the last, which shall be produced in 3 or 4 passes. The completed weld shall be at least flush with the surface of the test plate. (c) Welding conditions for composite electrodes shall be as agreed between purchaser and supplier. (d) Classification is based on the properties of weld metal with 5 ⁄ 32 in. [4.0 mm] electrodes or the closest size manufactured, if 5 ⁄ 32 in. [4. mm] is not manufactured. The conditions given above for sizes other than 5 ⁄ 32 in. [4.0 mm] are to be used when classification is based on those sizes, or when they are required for lot acceptance testing under A5.01,Filler Metal Procurement Guidelines (unless other conditions are specified by the purchaser). (e) 4.8 mm, 5.6 mm, and 6.4 mm are not included as standard sizes in ISO 864:1988. (f) Lower currents may be used for the first layer. (g) The electrode extension is the contact tube-to-work distance. When an electrode manufacturer recommends a contact tube-to-work distance outside the range shown, that recommendation shall be followed 61 ⁄ 4 in. [6.5 mm]. (h) In case of dispute, DCEP (direct current-electrode positive) shall be used as the referee current. (i) The first bead shall be produced with the assembly at any temperature between 60 and 325°F [15 to 165°C]. Welding shall continue, bead by bead, until a temperature within the interpass temperature range has been attained. Thereafter, production of subsequent beads may begin only when the assembly is within the interpass temperature range. The point of temperature measurement shall be at the mid-length of the test assembly, approximately 1 in. [25 mm] from the weld centerline.
FIG. 3B GROOVE WELD TEST WELDING PARAMETERS
362
PART C — SPECIFICATIONS FOR WELDING RODS, ELECTRODES, AND FILLER METALS SFA-5.
TABLE 4 BASE METALS FOR TEST ASSEMBLIES
ASTM Test Assembly Type Specification (1)^ UNS Number (2) Weld Pad for Chemical Analysis Carbon Steel A29 Grade 1015 G A29 Grade 1020 G A36 K A285 Grade A K A285 Grade B K A285 Grade C K A285 Grade D K A515 Grade 70 K A516 Grade 70 K
Groove Weld of Figure 3 Carbon Steel A36 K A285 Grade A K A285 Grade B K A285 Grade C K A285 Grade D K A515 Grade 70 K A516 Grade 70 K
NOTES: (1) Chemically equivalent steel may be used. In case of dispute, ASTM A36 shall be used as the referee steel. (2) As classified in ASTM DS-56, SAE HS-1 Metals and Alloys in the Unified Numbering System.
come from the weld pad in Fig. 2, from the reduced section of the fractured tension test specimen (see 12.1), or from a corresponding location (or any location above it) in the weld metal in the groove weld in Fig. 3A. In case of dispute, the weld pad shall be the referee method. The top surface of the pad described in 9.3 and shown in Fig. 2 shall be removed and discarded, and a sample for analysis shall be obtained from the underlying metal of the fourth layer of the weld pad by any appropriate mechanical means. The sample shall be free of slag. The alternatives to the weld pad outlined above and in 9.1.2 shall be prepared for analysis by any appropriate mechanical means.
10.3 The sample shall be analyzed by accepted analytical methods. The referee method shall be the procedure in the latest edition of ASTM E350, Testing Methods for Chemical Analysis of Carbon Steel, Low- Alloy Steel, Silicon Electrical Steel, Ingot Iron, and Wrought Iron.
10.4 The results of the analysis shall meet the requirements of Table 1 or 2, as applicable, for the classification of electrode under test.
363
11. Radiographic Test 11.1 The groove weld described in 9.4 and shown in Fig. 3A shall be radiographed to evaluate the sound- ness of the weld metal. In preparation for radiography, the backing shall be removed, and both surfaces of the weld shall be machined or ground smooth and flush with the original surfaces of the base metal. Both surfaces of the test assembly, in the area of the weld, shall be smooth enough to avoid difficulty in interpreting the radiograph.
11.2 The weld shall be radiographed in accordance with ASTM E142, Method for Controlling Quality of Radiographic Testing. The quality level of inspection shall be 2-2T.
11.3 The soundness of the weld metal meets the requirements of this specification if the radiograph shows the following: (a) No cracks, no incomplete fusion, and no incom- plete penetration (b) No slag inclusions longer than 5 ⁄ 16 in. [8 mm] or no groups of slag inclusions in line that have an aggregate length greater than 1 in. [25 mm] in a 12 in. [300 mm] length except when the distance between the successive inclusions exceeds 6 times the length of the longest inclusion in the group, and
PART C — SPECIFICATIONS FOR WELDING RODS, ELECTRODES, AND FILLER METALS SFA-5.
NOTES: (1) The chart which is most representative of the size of the rounded indications in the radiograph of the test assembly shall be used for determination of conformance with this specification. Rounded indications smaller than 1 ⁄ 64 in. [0.4 mm] shall be disregarded. The largest dimension of the indication (including any tail) is the size of the indication. (2) These radiographic requirements are for test welds made in the laboratory specifically for classification purposes. They are more restrictive than those usually encountered in general fabrication. They are equivalent to the Grade 1 standards of ANSI/AWS A5.1,Specification for Carbon Steel Electrodes for Shielded Metal Arc Welding.
FIG. 4 RADIOGRAPHIC STANDARDS FOR ROUNDED INDICATION
365
SFA-5.17 1998 SECTION II
TABLE 5U A5.17 TENSION TEST REQUIREMENTS Tensile Yield Flux-Electrode Strength, Strength, (2)^ Elongation, (2) Classification (1)^ psi psi %
F6XX-EXXX 60 000–80 000 48 000 22 F7XX-EXXX 70 000–95 000 58 000 22
NOTES: (1) The letter “S” will appear after the “F” as part of the classifica- tion designation when the flux being classified is a crushed slag or a blend of crushed slag with unused (virgin) flux. The letter “C” will appear after the “E” as part of the classification designa- tion when the electrode being classified is a composite electrode. The letter “X” used in various places in this table stands for, respectively, the condition of heat treatment, the toughness of the weld metal, and the classification of the electrode. See Figure 1U for a complete explanation of the classification designators. (2) Minimum requirements. Yield strength at 0.2 percent offset and elongation in 2 in. gage length.
TABLE 5M A5.17M TENSION TEST REQUIREMENTS Tensile Yield Flux-Electrode Strength, Strength, (2)^ Elongation, (2) Classification (1)^ MPa MPa %
F43XX-EXXX 430–560 330 22 F48XX-EXXX 480–660 400 22
NOTES: (1) The letter “S” will appear after the “F” as part of the classifica- tion designation when the flux being classified is a crushed slag or a blend of crushed slag with unused (virgin) flux. The letter “C” will appear after the “E” as part of the classification designa- tion when the electrode being classified is a composite electrode. The letter “X” used in various places in this table stands for, respectively, the condition of heat treatment, the toughness of the weld metal, and the classification of the electrode. See Figure 1M for a complete explanation of the classification designators. (2) Minimum requirements. Yield strength at 0.2 percent offset and elongation in 51 mm gage length.
spheric condition shall be an absolute humidity of 10 grains of moisture per pound [1.5 grams of moisture per kg] of dry air at the time of welding. The actual atmospheric conditions shall be reported along with the average diffusible hydrogen value for the test ac- cording to ANSI/AWS A4.3.
14.3 When the absolute humidity equals or exceeds the reference condition at the time of preparation of the test assembly, the test shall be acceptable as demon- strating compliance with the requirements of this speci- fication, provided that the actual test results satisfy the diffusible hydrogen requirements for a given designator, as specified in Table 7.
366
TABLE 6U A5.17 IMPACT TEST REQUIREMENTS (1) (2) Maximum Test Minimum Temperature, Average Energy Digit °F Level 0 0 2 − 4 −40 (^) 20 ft · lbf 5 − 6 − 8 − Z No impact requirements NOTES: (1) Based on the results of the impact tests of the weld metal, the manufacturer shall insert in the classification the appropriate digit from the table above (Table 6U), as indicated in Figure 1U. (2) Weld metal from a specific flux-electrode combination that meets impact requirements at a given temperature also meets the re- quirements at all higher temperatures in this table (i.e., weld metal meeting the requirements for digit 5 also meets the require- ments for digits 4, 2, 0, and Z).
TABLE 6M A5.17M IMPACT TEST REQUIREMENTS (1) (2) Maximum Test Minimum Temperature, Average Energy Digit °C Level 0 0 2 − 3 −30 (^) 27 Joules 4 − 5 − 6 − Z No impact requirements NOTES: (1) Based on the results of the impact tests of the weld metal, the manufacturer shall insert in the classification the appropriate digit from the table above (Table 6M), as indicated in Figure 1M. (2) Weld metal from a specific flux-electrode combination that meets impact requirements at a given temperature also meets the re- quirements at all higher temperatures in this table (i.e., weld metal meeting the requirements for digit 5 also meets the require- ments for digits 4, 3, 2, 0 and Z).
15. Method of Manufacture The electrodes and fluxes classified according to this specification may be manufactured by any method that will produce material that meets the requirements of this specification.
SFA-5.17 1998 SECTION II
with the uniform, uninterrupted feeding of the electrode on automatic and semiautomatic equipment.
16.2.3 Core ingredients in composite electrodes shall be distributed with sufficient uniformity throughout the length of the electrode so as not to adversely affect the performance of the electrode or the properties of the weld metal.
16.2.4 A suitable protective coating, such as copper, may be applied to any electrode covered in this specifi- cation.
16.3 Standard Package Forms
16.3.1 Standard package forms are coils with sup- port, coils without support, and drums. Standard package dimensions and weights for each form are given in Table 9. Package forms, sizes and weights other than these shall be as agreed between purchaser and supplier.
16.3.2 The liners in coils with support shall be designed and constructed to prevent distortion of the coil during normal handling and use, and shall be clean and dry enough to maintain the cleanliness of the electrode.
16.3.3 Drums shall be designed and constructed to prevent distortion of the electrode during normal handling and use and shall be clean and dry enough to maintain the cleanliness of the electrode.
16.4 Winding Requirements
16.4.1 The electrode shall be wound so that kinks, waves, sharp bends, or wedging are not encountered, leaving the electrode free to unwind without restriction. The outside end of the electrode (the end with which welding is to begin) shall be identified so it can be readily located and shall be fastened to avoid unwinding.
16.4.2 The cast and helix of the electrode in coils and drums shall be such that the electrode will feed in an uninterrupted manner in automatic and semiautomatic equipment.
16.5 Electrode Identification
16.5.1 The product information and the precaution- ary information required in 16.7 for marking each package shall appear also on each coil and drum.
16.5.2 Coils without support shall be identified by a tag containing this information securely attached to the inside end of the coil.
16.5.3 Coils with support shall have the information securely affixed in a prominent location on the support.
368
16.5.4 Drums shall have the information securely affixed in a prominent location on the side of the drum. 16.6 Packaging. Electrodes shall be suitably pack- aged to ensure against damage during shipment and storage under normal conditions. 16.7 Marking of Packages 16.7.1 The following product information (as a minimum) shall be legibly marked so as to be visible from the outside of each unit package. (a) AWS specification and classification number (year of issue may be excluded) (b) Supplier’s name and trade designation (c) In the case of a composite electrode, the trade designation of the flux (or fluxes) with which its weld metal composition meets the requirements of Table 2 (d) Size and net weight (e) Lot, control or heat number. 16.7.2 The following precautionary information (as a minimum) shall be prominently displayed in legible print on all packages of welding electrodes, including individual unit packages enclosed within a larger package.
O Before use, read, and understand the manufacturer’s instructions, Material Safety Data Sheets (MSDSs), and your employer’s safety practices. O Keep your head out of the fumes. O Use enough ventilation, exhaust at the arc, or both, to keep fumes and gases away from your breathing zone and the general area. O Wear correct eye, ear, and body protection. O Do not touch live electrical parts. O See American National Standard ANSI/ASC Z49.1, Safety in Welding, Cutting, and Allied Processes, published by the American Welding Society, 550 N.W. LeJeune Road, Miami, FL 33126; and OSHA Safety and Health Standards, 29 CFR 1910 , avail- able from the U.S. Government Printing Office, Washington, DC 20402.
PART C — SPECIFICATIONS FOR WELDING RODS, ELECTRODES, AND FILLER METALS SFA-5.
TABLE 9 STANDARD DIMENSIONS AND WEIGHTS (1) (2)
Width of Outside Net Weight Inside Diameter Coil, Diameter Electrode Size(3)^ of Coil (4)^ of Liner Max. of Coil, Max.
in. mm lb kg in. mm in. mm in. mm (^25 2 1) ⁄ 50 2 171 ⁄^2 (^1) ⁄ 16 – (^1) ⁄ 4 12 6 1 ⁄ 8 or or (^60 45) ⁄ 65 8 17
12 15 1.6–6.4 20 300 + 15, −0 (5) (5) 25 30
100 (^3) ⁄ 32 – (^1) ⁄ 4 150 (5) 5 31 1 ⁄ (^2) 200
45 2.4–6.4 70 610 6 10 130 800 90 100
Coils with Support
Coils without Support 1 ⁄ 16 – 1 ⁄ 4 1.6–6.4 As agreed between purchaser and supplier
Drums 1 ⁄ 16 – 1 ⁄ 4 1.6–6.4 As agreed between purchaser and supplier
NOTES: (1) Values specified in “in.” or “lb” apply to A5.17. Values specificed in “mm” or “kg” apply to A5.17M. (2) Other dimensions and weights may be supplied as agreed between purchaser and supplier. (3) The range is inclusive. (4) Net weights shall not vary more than 6 10 percent. (5) This dimension shall be agreed between purchaser and supplier.
17. Flux Requirements
17.1 Form and Particle Size. Flux shall be granular in form and shall be capable of flowing freely through the flux feeding tubes, valves, and nozzles of standard submerged arc welding equipment. Particle size is not specified here, but, when it is addressed, it shall be a matter of agreement between the purchaser and the supplier.
17.2 Usability. The flux shall permit the production of uniform, well-shaped beads that merge smoothly with each other and the base metal. Undercut, if any, shall not be so deep or so widespread that a subsequent bead will not remove it.
369
17.3 Packaging
17.3.1 Flux shall be suitably packaged to ensure against damage during shipment.
17.3.2 Flux, in its original unopened container, shall withstand storage under normal conditions for at least six months without damage to its welding characteristics or the properties of the weld. Heating of the flux to assure dryness may be necessary when the very best properties (of which the materials are capable) are required. For specific recommendations, consult the manufacturer.
PART C — SPECIFICATIONS FOR WELDING RODS, ELECTRODES, AND FILLER METALS SFA-5.
(This Annex is not a part of ANSI/AWS A5.17/A5.17M-97, Specification for Carbon Steel Electrodes and Fluxes for Submerged Arc Welding, but is included for information purposes only).
A1. Introduction
The purpose of this guide is to correlate the electrode and flux classifications with their intended applications so the specification can be used effectively. Reference to appropriate base metal specifications is made when- ever that can be done and when it would be helpful. Such references are intended only as examples rather than complete listings of the base metals for which each electrode and flux combination is suitable.
A2. Classification System
A2.1 Classification of Electrodes. The system for identifying the electrode classifications in this specifica- tion follows the standard pattern used in other AWS filler metal specifications. The letter ‘‘E’’ (or ‘‘EC’’ for composite electrodes) at the beginning of each classification designation stands for electrode. The re- mainder of the designation indicates the chemical com- position of the electrode or, in the case of composite electrodes, the chemical composition of the weld metal obtained with a particular flux. See Fig. 1U or Fig. 1M, as applicable. The letter ‘‘L’’ indicates that the solid electrode is comparatively low in manganese content. The letter ‘‘M’’ indicates a medium manganese content, while the letter ‘‘H’’ indicates a comparatively high manganese content. The one or two digits following the manganese designator indicate the nominal carbon content of the electrode. The letter ‘‘K,’’ which appears in some designations, indicates that the electrode is made from a heat of silicon-killed steel. Solid electrodes are classi-
fied only on the basis of their chemical composition, as specified in Table 1 of this specification. A composite electrode is indicated by the letter ‘‘C’’ after the ‘‘E’’ and a numerical suffix. The composition of a composite electrode may include metallic elements in the core material that are also present as oxides, fluorides, etc., of those same elements. Therefore, the chemical analysis of a composite electrode may not be directly comparable to an analysis made on a solid electrode. For this reason, the composition of composite electrodes is not used for classification purposes under this specification, and the user is referred to weld metal composition (Table 2) with a particular flux, rather than to electrode composition.
A2.2 ‘‘G’’ Classification and the Use of ‘‘Not Specified’’ and ‘‘Not Required’’
A2.2.1 This specification includes filler metals classified as ‘‘EG’’ or ‘‘ECG.’’ The ‘‘G’’ indicates that the filler metal is of a general classification. It is ‘‘general’’ because not all of the particular requirements specified for each of the other classifications are speci- fied for this classification. The intent, in establishing this classification, is to provide a means by which filler metals that differ in one respect or another (chemical composition, for example) from all other classifications (meaning that the composition of the filler metal — in the case of the example — does not meet the composition specified for any of the classifications in the specification) can still be classified according to the specification without awaiting revision. This means, then, that two filler metals — each bearing the same ‘‘G’’ classification — may be quite different in some
SFA-5.17 1998 SECTION II
certain respect (chemical composition, again, for ex- ample).
A2.2.2 The point of difference (although not neces- sarily the amount of the difference) referred to above will be readily apparent from the use of the words ‘‘not required’’ and ‘‘not specified’’ in the specification. The use of these words is as follows: Not Specified is used in those areas of the specification that refer to the results of some particular test. It indicates that the requirements for that test are not specified for that particular classification. Not Required is used in those areas of the specification that refer to the test that normally is required to be conducted to classify a filler metal. It indicates that the test is not required because the requirements (results) for the test have not been specified for that particular classification. Restating the case, when a requirement is not speci- fied, it is not necessary to conduct the corresponding test in order to classify a filler metal to that classification. When a purchaser wants the information provided by that test, in order to consider a particular product of that classification for a certain application, the purchaser will have to arrange for that information with the supplier of that product. The purchaser will also have to establish with that supplier just what the testing procedure and the acceptance requirements are to be for that test. The purchaser may want to incorporate that information, via ANSI/AWS A5.01, Filler Metal Procurement Guidelines, in the purchase order.
A2.2.3 Request for Filler Metal Classification (a) When a filler metal cannot be classified according to some classification other than a ‘‘G’’ classification, the manufacturer may request that a classification be established for that filler metal. The manufacturer may do this by following the procedure given here. When the manufacturer elects to use the ‘‘G’’ classification, the Committee on Filler Metals recommends that the manufacturer still request that a classification be estab- lished for that filler metal, as long as the filler metal is of commercial significance. (b) A request to establish a new filler metal classifi- cation must be submitted in writing, and it needs to provide sufficient detail to permit the Committee on Filler Metals or the Subcommittee to determine whether a new classification or the modification of an existing classification is more appropriate, and whether either is necessary to satisfy the need. The request needs to state the variables and their limits, for such a classifica- tion or modification. The request should contain some indication of the time by which completion of the new classification or modification is needed.
(c) The request should be sent to the Secretary of the Committee on Filler Metals at AWS Headquarters. Upon receipt of the request, the Secretary will: (1) Assign an identifying number to the request. This number will include the date the request was received. (2) Confirm receipt of the request and give the identification number to the person who made the request. (3) Send a copy of the request to the Chair of the Committee on Filler Metals and the particular Subcommittee involved. (4) File the original request. (5) Add the request to the log of outstanding requests. (d) All necessary action on each request will be completed as soon as possible. If more than 12 months lapse, the Secretary shall inform the requestor of the status of the request, with copies to the Chairs of the Committee and the Subcommittee. Requests still outstanding after 18 months shall be considered not to have been answered in a ‘‘timely manner’’ and the Secretary shall report these to the Chair of the Commit- tee on Filler Metals, for action. (e) The Secretary shall include a copy of the log of all requests pending and those completed during the preceding year with the agenda for each Committee on Filler Metals meeting. Any other publication of requests that have been completed will be at the option of the American Welding Society, as deemed appro- priate. A2.3 Classification of Fluxes. Fluxes are classified on the basis of the mechanical properties of the weld metal they produce, with some certain classification of electrode, under the specific test conditions called for in Part B of this specification. A2.3.1U As examples of A5.17 U.S. Customary Unit classifications, consider the following: F7A2-EH FS6A0-EM13K F7P6-EM12K F7P4-EC The prefix ‘‘F’’ designates an unused (virgin) flux. The prefix ‘‘FS’’ designates a flux that is made solely from crushed slag or is a blend of crushed slag with virgin flux. This is followed by a single digit represent- ing the minimum tensile strength required of the weld metal in 10 000 psi increments. When the letter ‘‘A’’ follows the strength designator, it indicates that the weld metal was tested (and is classified) in the as-welded condition. When the letter