
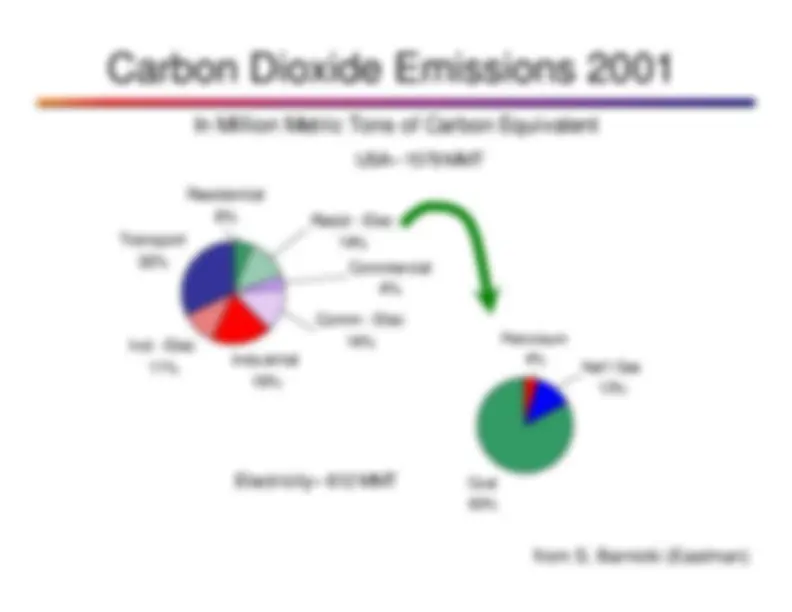
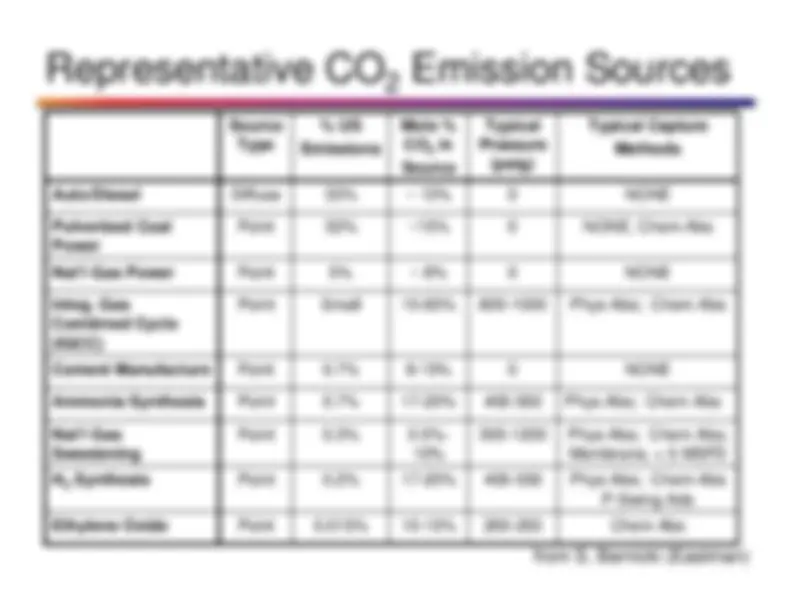

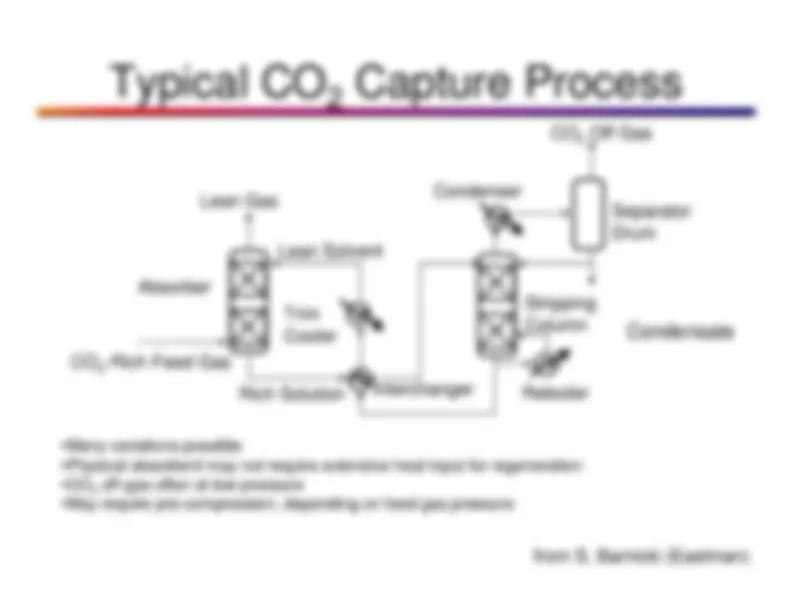
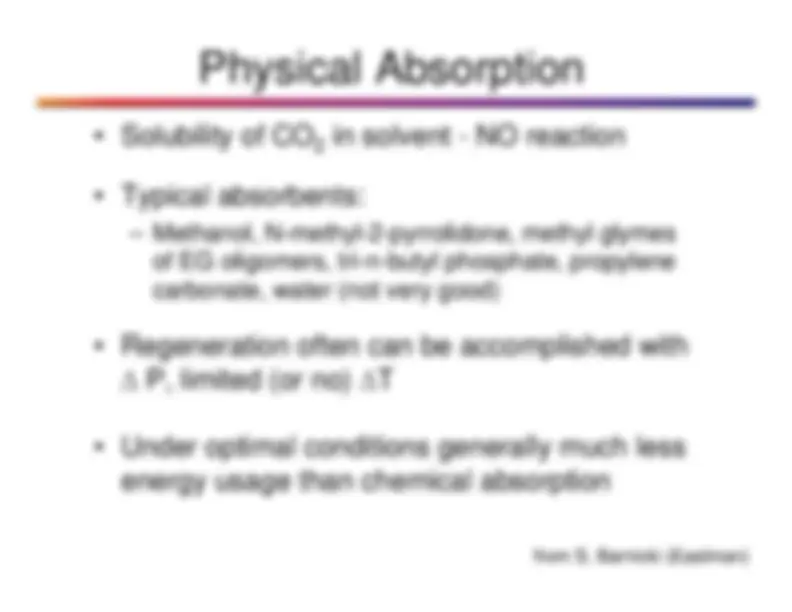
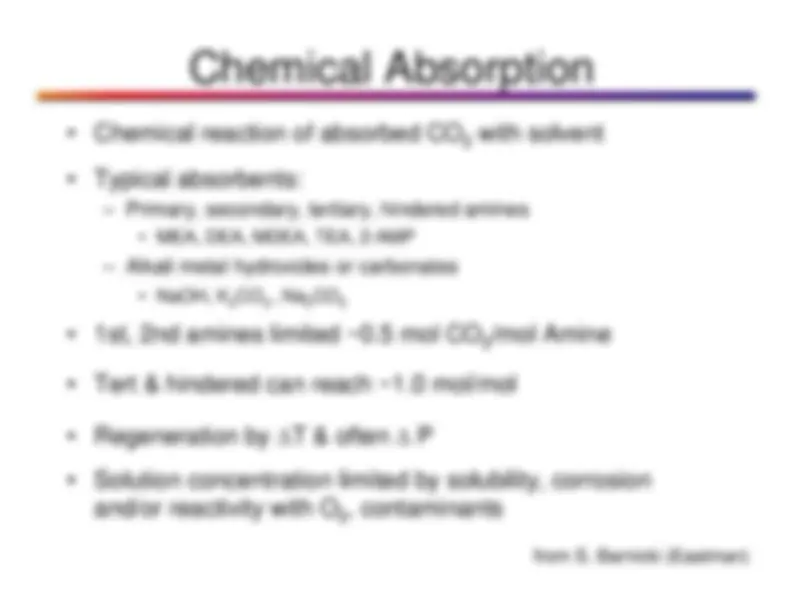
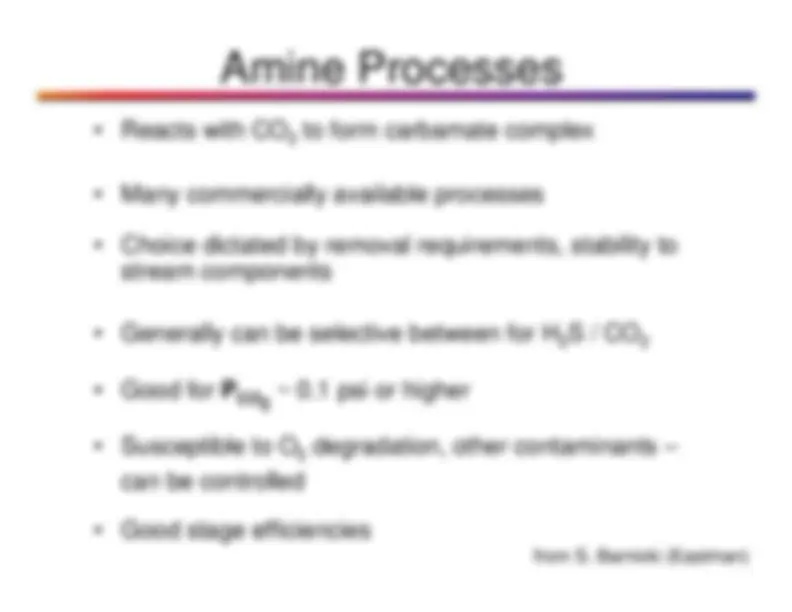
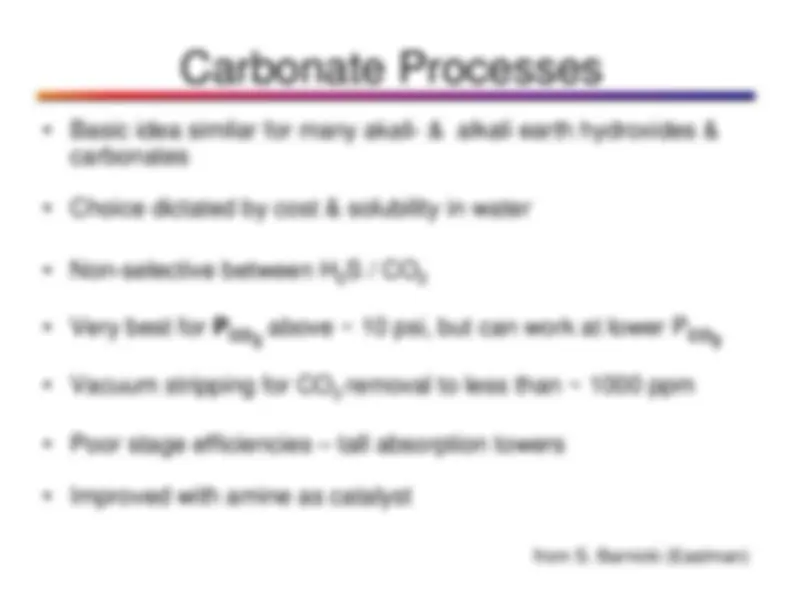
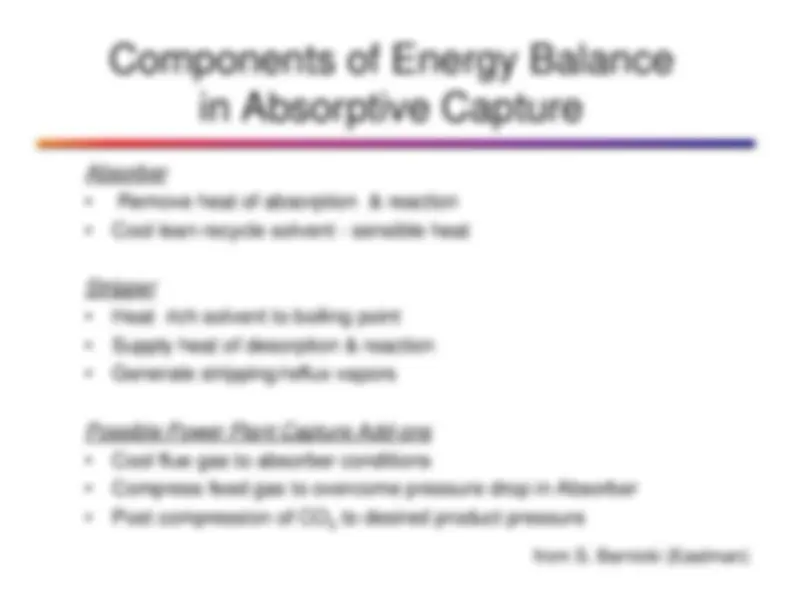
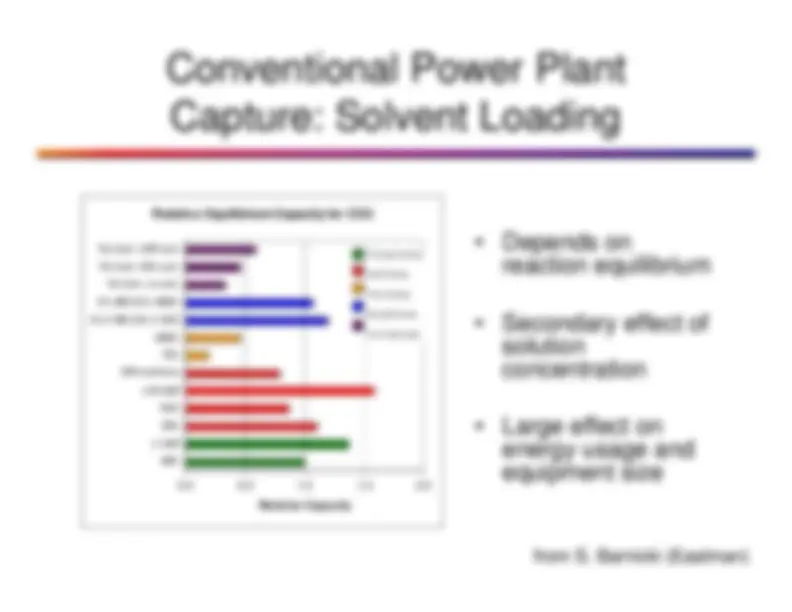
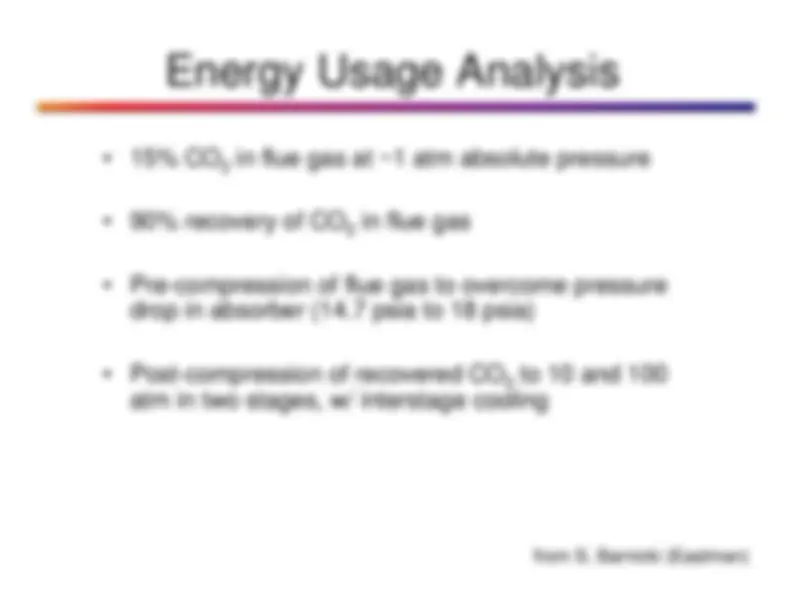
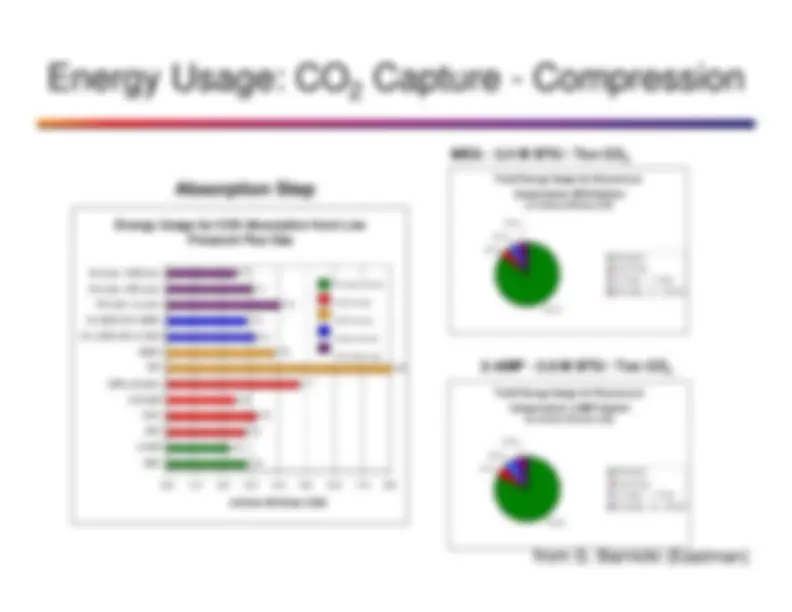
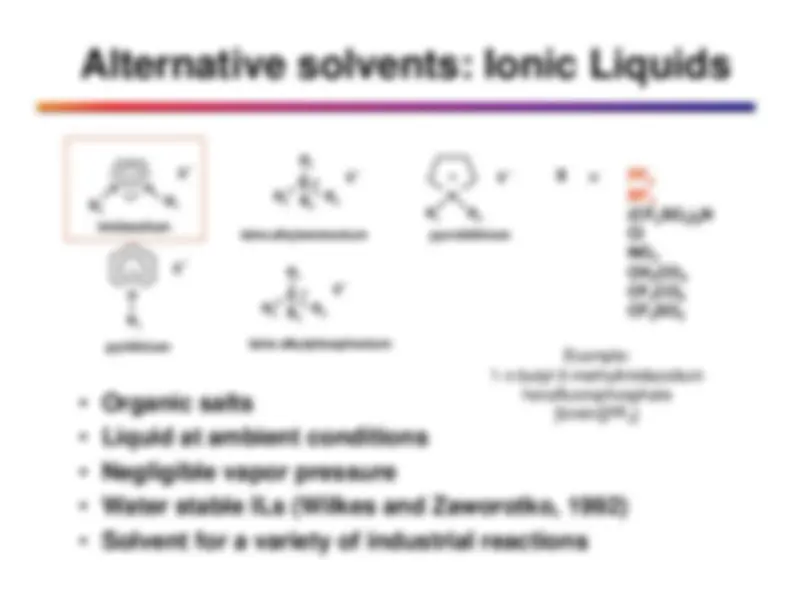
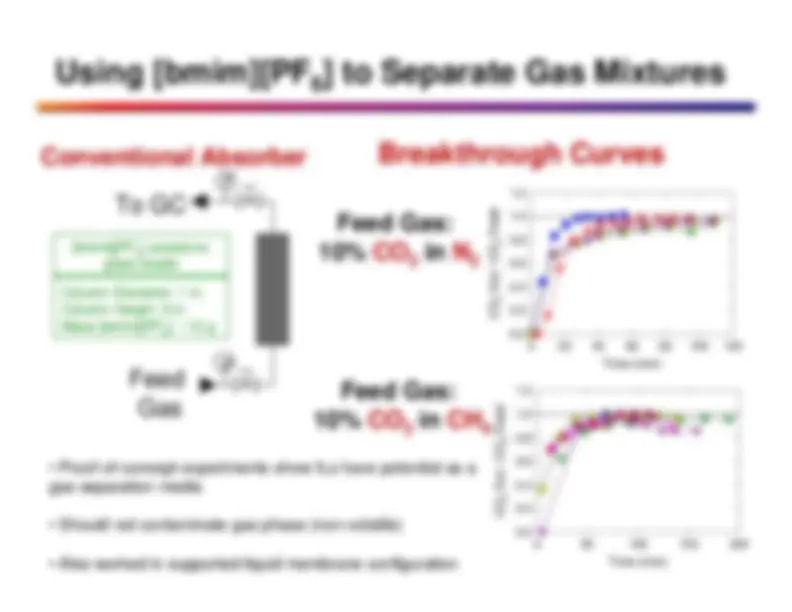
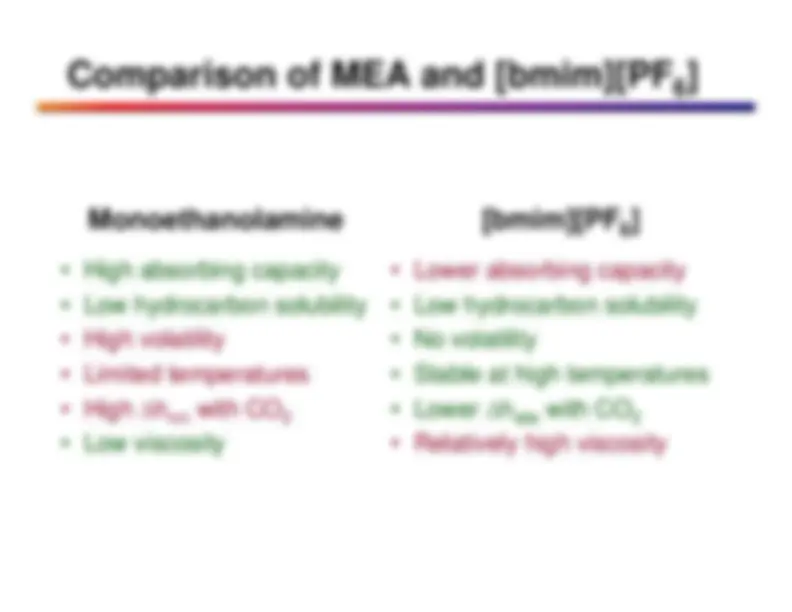
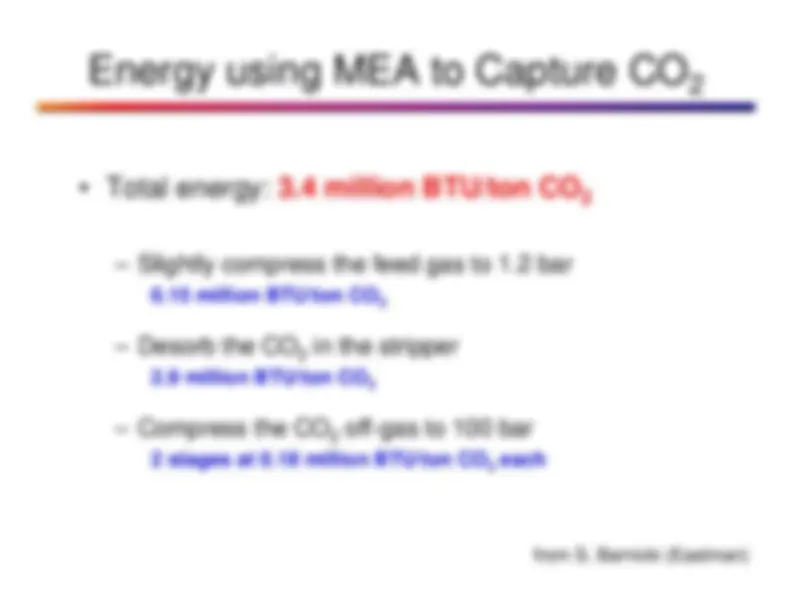
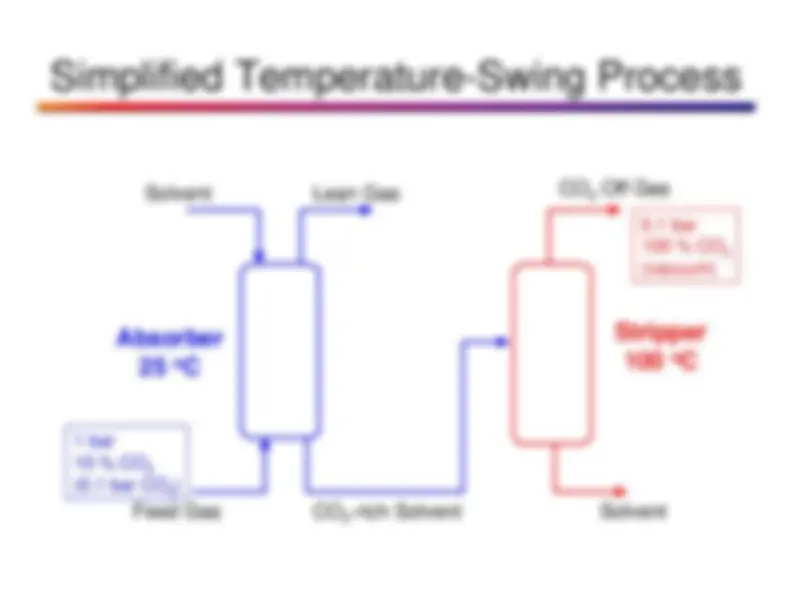
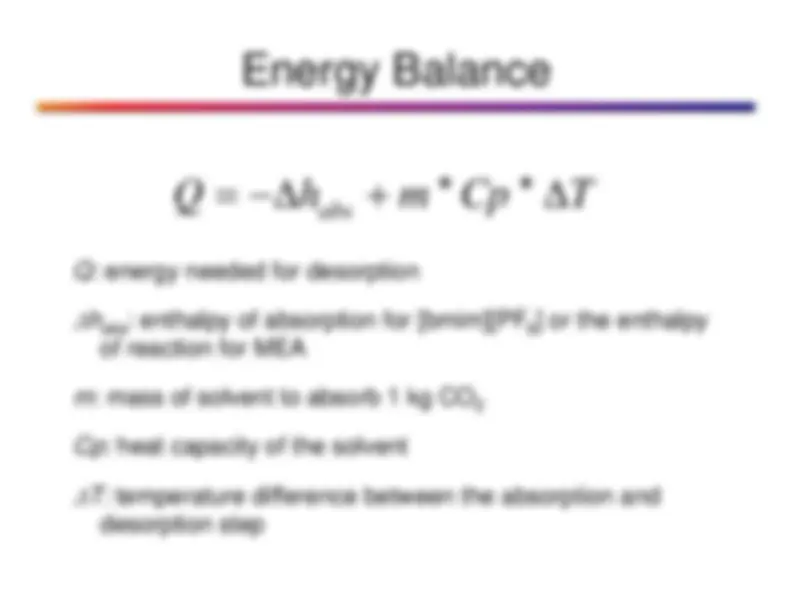
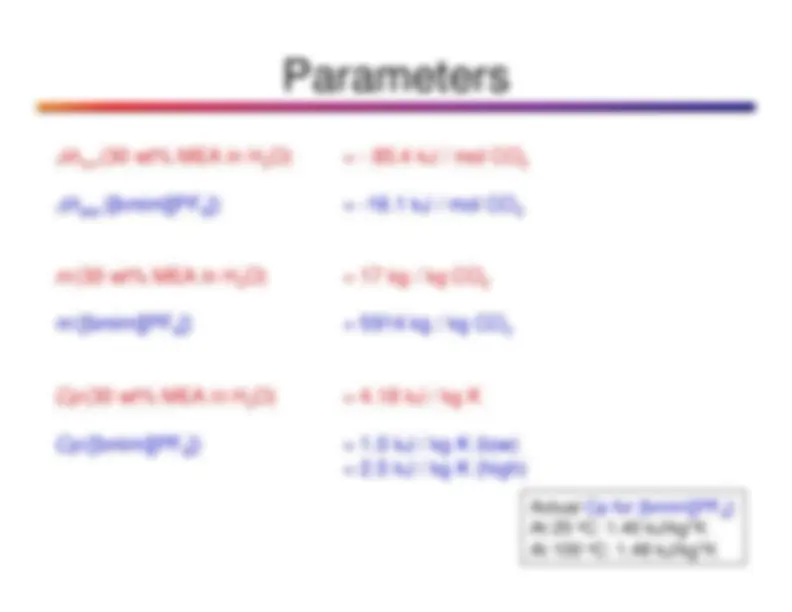
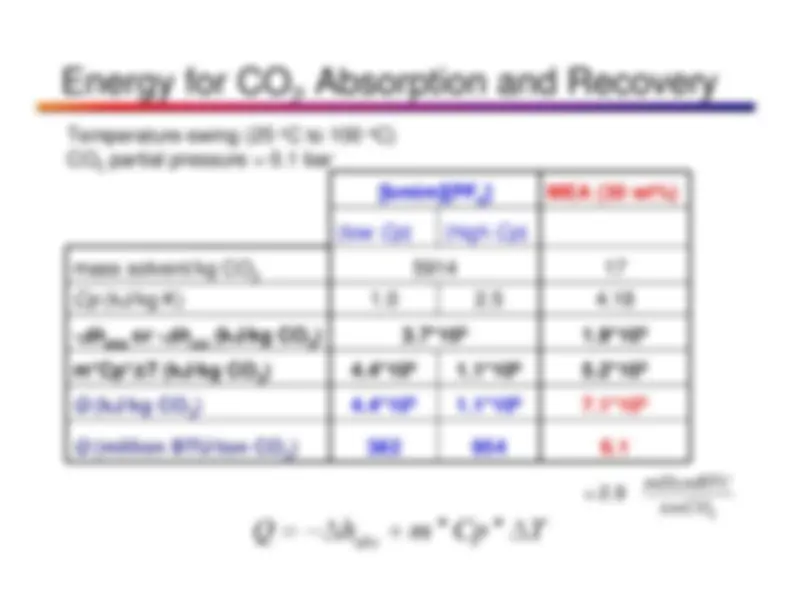
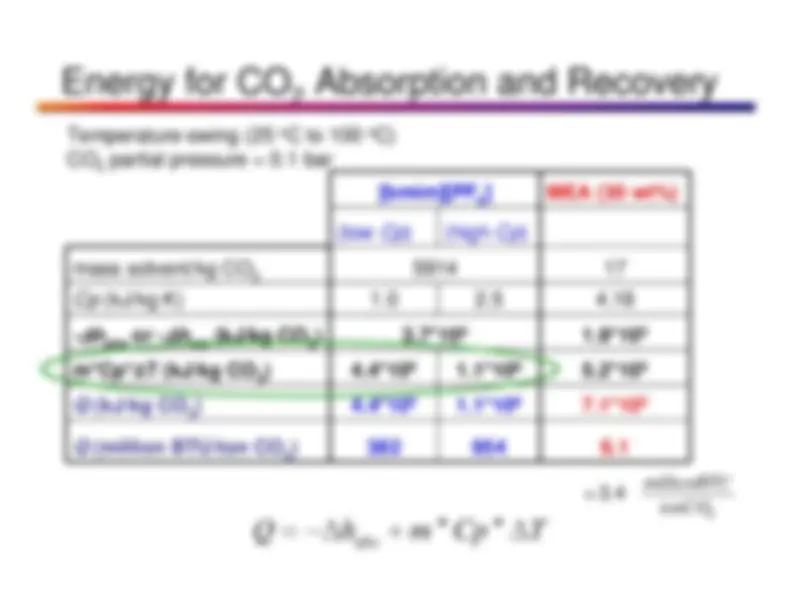
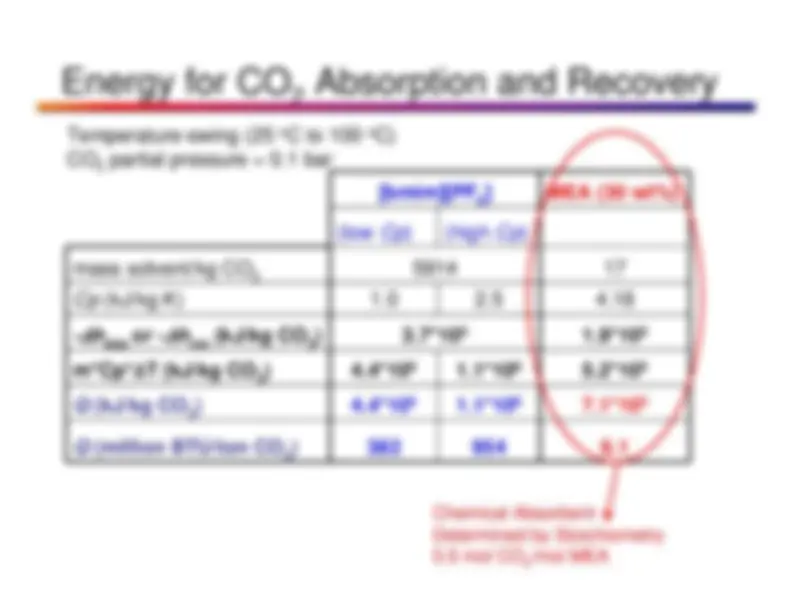
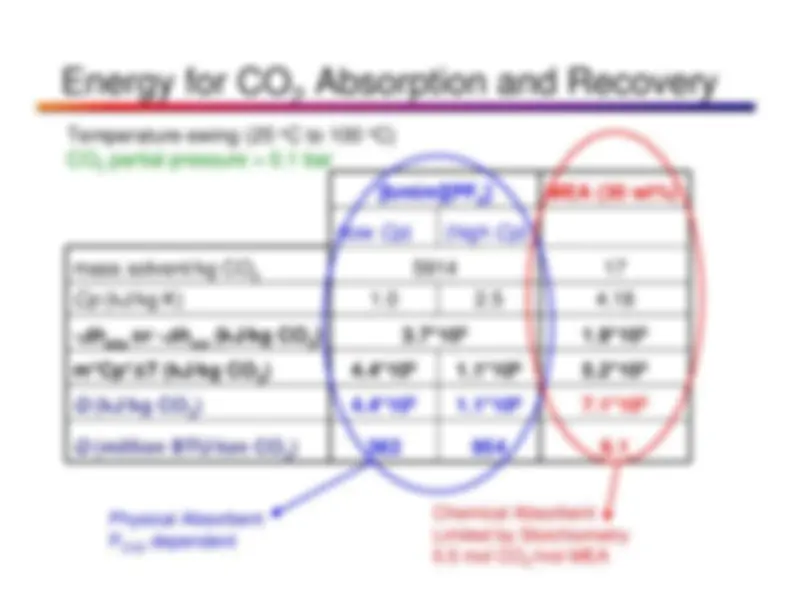
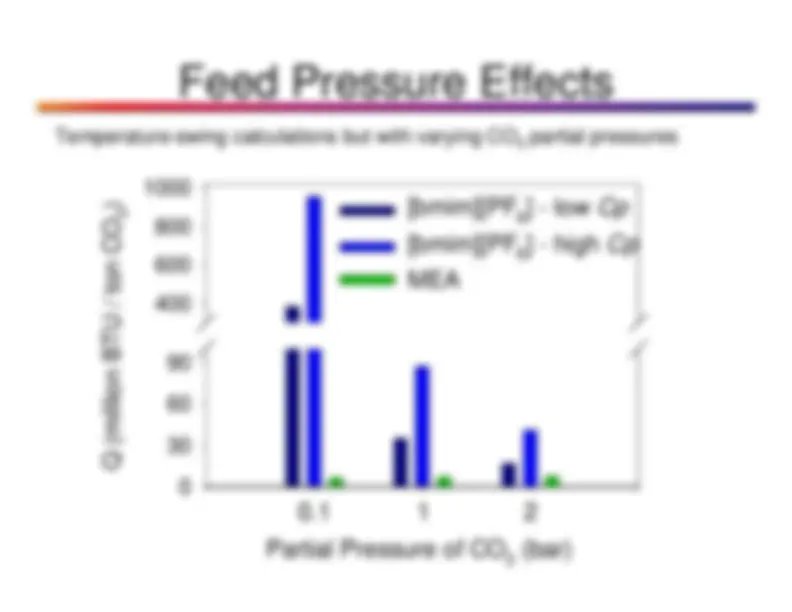
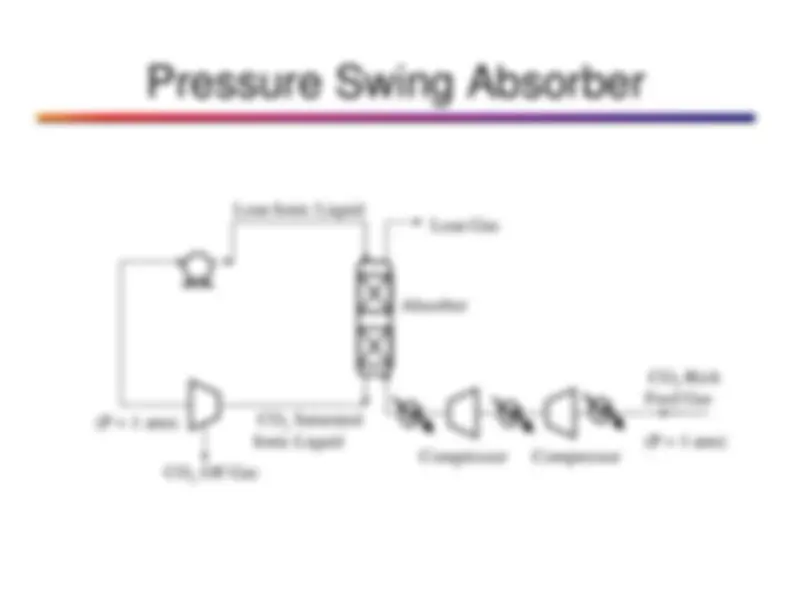
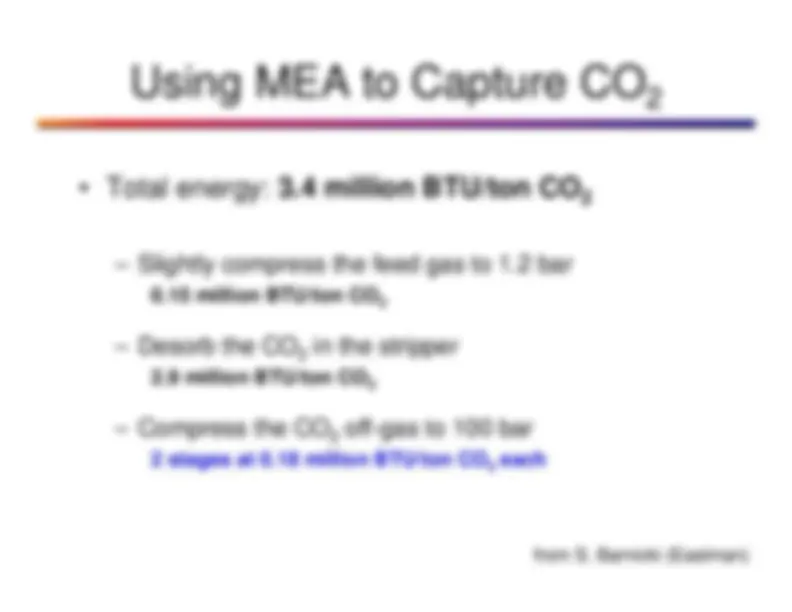
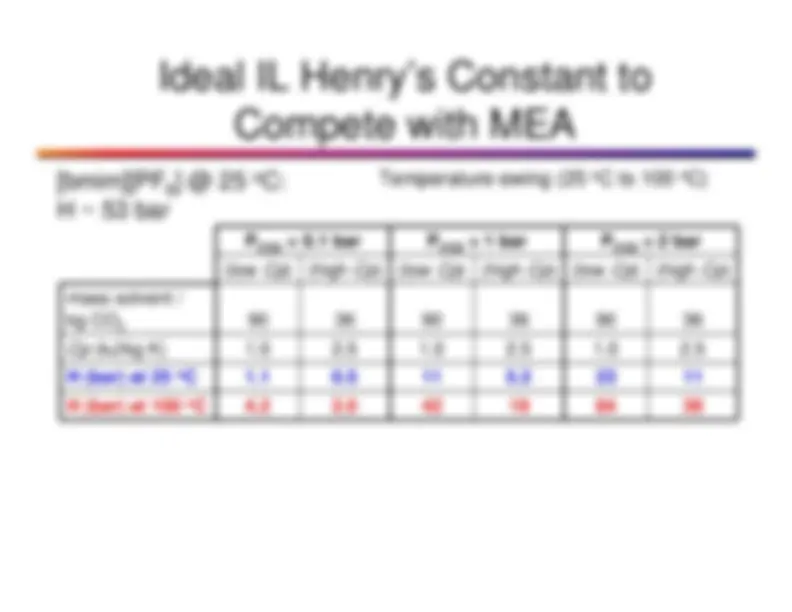
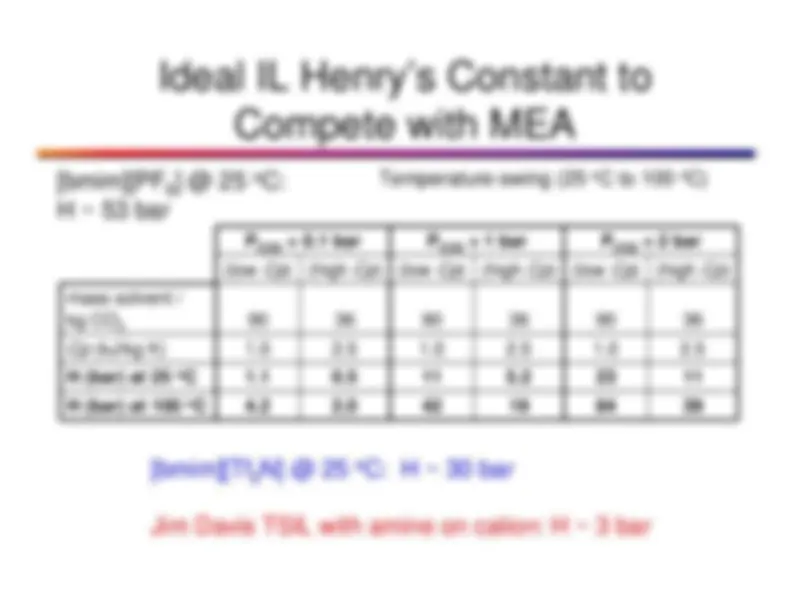
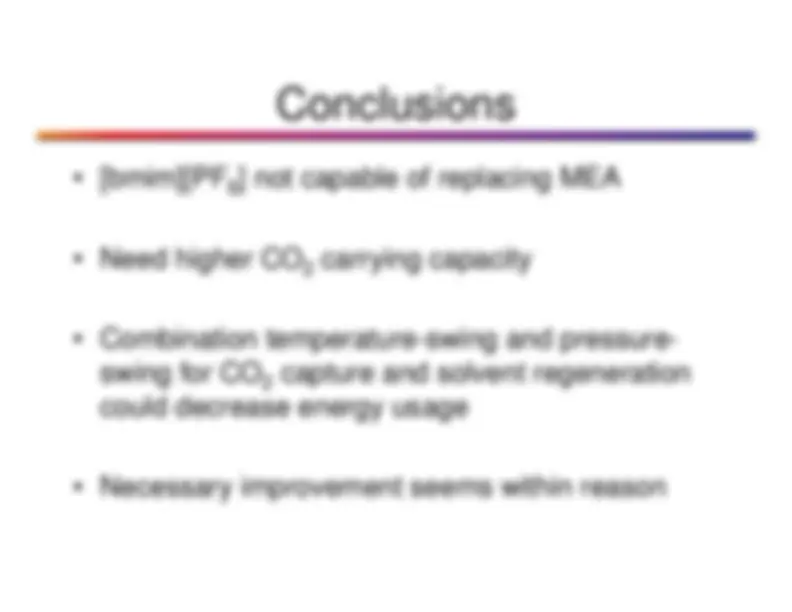
Study with the several resources on Docsity
Earn points by helping other students or get them with a premium plan
Prepare for your exams
Study with the several resources on Docsity
Earn points to download
Earn points by helping other students or get them with a premium plan
Community
Ask the community for help and clear up your study doubts
Discover the best universities in your country according to Docsity users
Free resources
Download our free guides on studying techniques, anxiety management strategies, and thesis advice from Docsity tutors
An overview of aluminum production processes and their associated co2 emissions. It also covers various co2 capture methods, including membrane separation, adsorption, and chemical absorption, and discusses their energy usage and efficiency. Data on co2 emissions from different sources and the percentage of us emissions, as well as typical pressures and capture methods for each source.
Typology: Study notes
1 / 37
This page cannot be seen from the preview
Don't miss anything!
Transport32%^ CommercialInd - ElecIndustrial11%19%
4% Residential6%^
Resid - Elec14% Comm - Elec14%
In Million Metric Tons of Carbon EquivalentIndustrial – Non-Electricity / Non-Steam Cement Production^
Ammonia Synthesis
Lime Production & Use
CO2 from natural Gas
Hydrogen Production
Aluminum Production
Soda Ash Production & Use
Ethylene Oxide^
Other Chemical Processes
from S. Barnicki (Eastman)
Source^ % USType^ Emissions
Mole %^ TypicalCO^ inPressure^2 (psig)^ Source
Typical Capture^ Methods
Auto/Diesel^
Diffuse^ 33%
~ 13%^
0
NONE
Pulverized CoalPower
Point^ 32%
~15%^
0 NONE, Chem Abs
Nat’l Gas Power
Point^
5%^ ~ 8%
0
NONE
Integ. GasCombined Cycle(IGCC)
Point^ Small
15-65%^
800-1000^ Phys Abs; Chem Abs
Cement Manufacture
Point^
0.7%^ 9-15%
0
NONE
Ammonia Synthesis
Point^
0.7%^ 17-20%
400-550^ Phys Abs; Chem Abs
Nat’l GasSweetening
Point^ 0.3%
0.5%-10%
300-1200^ Phys Abs; Chem Abs;Membrane, < 5 MSFD
H^ Synthesis^2
Point^ 0.2%
17-20%^
400-550^ Phys Abs; Chem Abs
P-Swing Ads
Ethylene Oxide
Point^
0.015%^ 10-15%
200-^
Chem Abs from S. Barnicki (Eastman)
-^ Rankine Cycle - 25-30% efficiency•^ Energy in very LPsteam is lost -condensed w/o energyrecovery•^ Difficult to controlpollution•^ Flue gas at lowpressure ~1 atm HP SteamHP Turbine^ Very LP Steam Combustor /Steam Drum
HP Generator LP Turbine LP Generator Fuel:Pulv. CoalNat'l GasPetroleum Inter-changer^ CondensateCondenser^ PostTreatment 10-20%ExcessAir
Flue Gas Blower
3 %from S. Barnicki (Eastman)
Conventional Methods for CO
Capture (^2) membrane
from S. Barnicki (Eastman)
Lean Gas
COOff Gas^2 CondenserSeparatorDrum StrippingColumn Reboiler
Absorber
TrimCoolerInterchanger Lean Solvent Rich Solution CO-Rich Feed Gas^2 •Many variations possible •Physical absorbent may not require extensive heat input for regeneration •CO^ off-gas often at low pressure^2 •May require pre-compression, depending on feed gas pressure
from S. Barnicki (Eastman)
-^ Chemical reaction of absorbed CO
with solvent 2
-^ Typical absorbents:^ – Primary, secondary, tertiary, hindered amines^ •^ MEA, DEA, MDEA, TEA, 2-AMP^ – Alkali metal hydroxides or carbonates^ •^ NaOH, K
CO, Na^ CO 23 23
-^ 1st, 2nd amines limited ~0.5 mol CO
/mol Amine 2
-^ Tert & hindered can reach ~1.0 mol/mol •^ Regeneration by
∆T & often
∆^ P
-^ Solution concentration limited by solubility, corrosionand/or reactivity with O
, contaminants 2
from S. Barnicki (Eastman)
CO^2
-^ Can reach very low outlet P
CO^2
CO^2
-^ Loading proportional to P
CO^2
-^ Cannot reach very low outletPi.e., usually 0.1-2%, butCO^2 some can reach ppm levels MeOH, 0°C^ MeOH, 0°C20wt% DEA, 50 °C20wt% DEA, 50 °C above Liquid, atm CO2 P CO, vol/vol absorbent^2
from S. Barnicki (Eastman)
-^ Reacts with CO
to form carbamate complex 2
-^ Many commercially available processes •^ Choice dictated by removal requirements, stability tostream components •^ Generally can be selective between for H
S / CO 22
-^ Good for
P ~ 0.1 psi or higher CO^2
-^ Susceptible to O
degradation, other contaminants – 2 can be controlled • Good stage efficiencies
from S. Barnicki (Eastman)
-^ Basic idea similar for many akali- & alkali earth hydroxides &carbonates •^ Choice dictated by cost & solubility in water •^ Non-selective between H
S / CO 2 2
-^ Very best for
P^ above ~ 10 psi, but can work at lower P CO^2
CO^2
-^ Vacuum stripping for CO
removal to less than ~ 1000 ppm 2
-^ Poor stage efficiencies – tall absorption towers •^ Improved with amine as catalyst
from S. Barnicki (Eastman)
2-AMP(hindered)MEA (Prim)
(tert)MDEADEA (sec) TEA (tert)2NaHCO3Na2CO3 to
MeOH2KCO3K2CO3 to(Physical)
2-AMP(hindered)MEA (Prim)
(tert)MDEADEA (sec) TEA (tert)2NaHCO3Na2CO3 to
2KCO3MeOHK2CO3 to(Physical)
(^22) (Kcal/gmole CO(Kcal/gmole COHeat of Reaction Heat of Reaction
from S. Barnicki (Eastman)
-^ Primary Amines
-^ Secondary Amines
-^ Tertiary Amines
-^ Hindered Amines
-^ Mixed Amines
-^ Hot Potassium Carbonate
-^ Ionic Liquids
from S. Barnicki (Eastman)
in flue gas 2
-^ Pre-compression of flue gas to overcome pressuredrop in absorber (14.7 psia to 18 psia) •^ Post-compression of recovered CO
to 10 and 100 2
atm in two stages, w/ interstage cooling
from S. Barnicki (Eastman)
Energy Usage: CO
Capture - Compression 2^ MEA - 3.4 M BTU / Ton CO
2 Total Energy Usage for Recovery &Compression: MEA System3.4 million BTU/ton CO2 5.2%5.2%4.5%^ 85.1%
Absorption Feed Compr 1st stage - 1- 10 atm 2nd stage - 10 - 100 atm
Energy Usage for CO2 Absorption from LowPressure Flue Gas
4.7 2.5 3.2 2.8 2.3 2.
2.5^ 3.1^ 4.0^ 2.9^ 3.2^ 3. 0.0^ 1.0^ 2.0^ 3.0^ 4.
5.0^ 6.0^ 7.0^ 8. Pot Carb- AMP activPot Carb- DEA activPot Carb- no activ6% MEA/24% MDEA3% 2-MPz/30% 2-BAEMDEATEADIPA/sulfolane2-iPrAMPDGADEA2-AMPMEA^ million BTU/ton CO
P rimary A mines2nd A minesTert A minesM ixed A minesP o t Carbo nate Absorption Step
Total Energy Usage for Recovery &Compression: 2-AMP System2.8 million BTU/ton CO2 6.3%6.3%5.5%^ 81.8%
Absorption Feed Compr 1st stage - 1- 10 atm 2nd stage - 10 - 100 atm 2-AMP - 2.8 M BTU / Ton CO
2 from S. Barnicki (Eastman)