
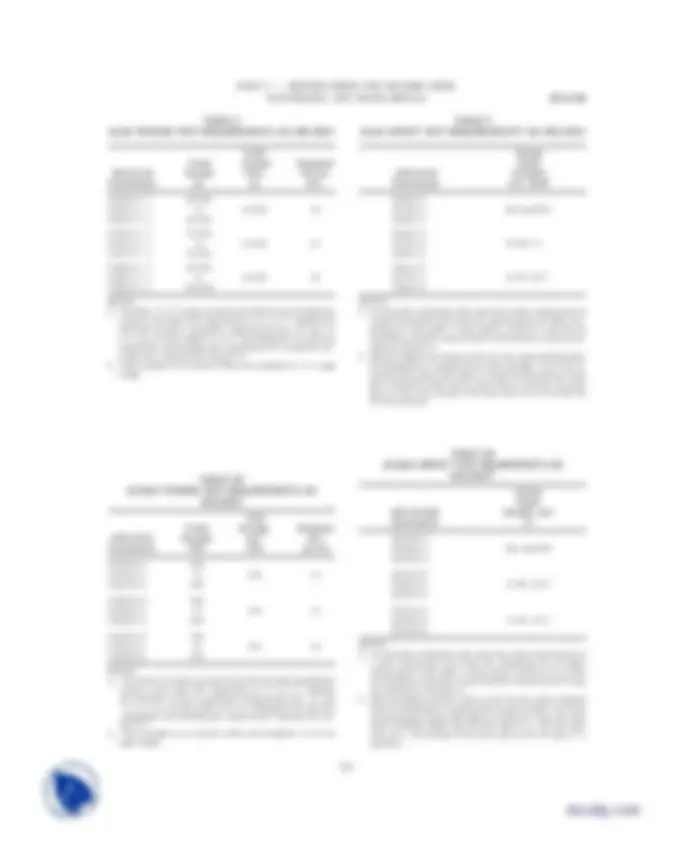
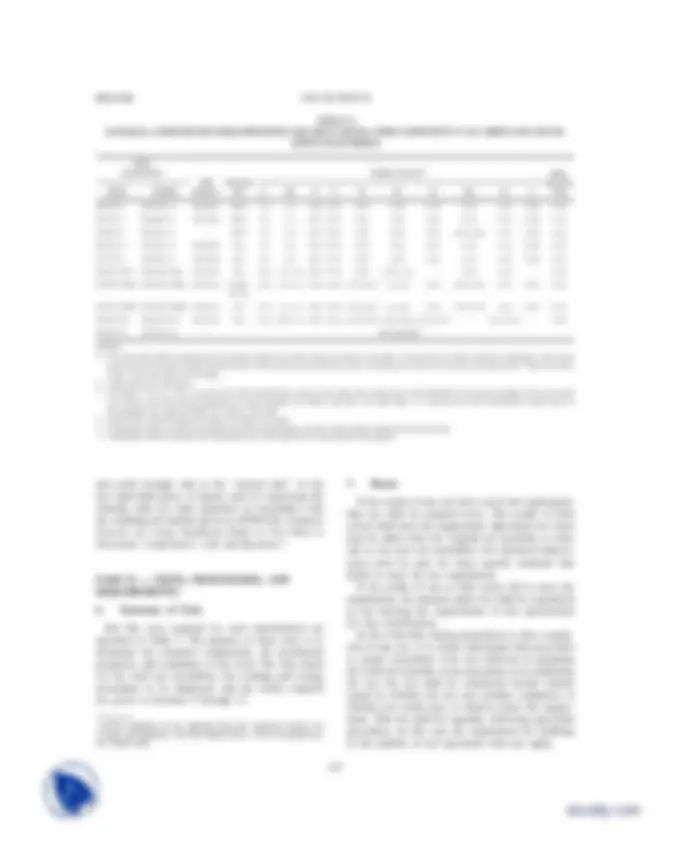
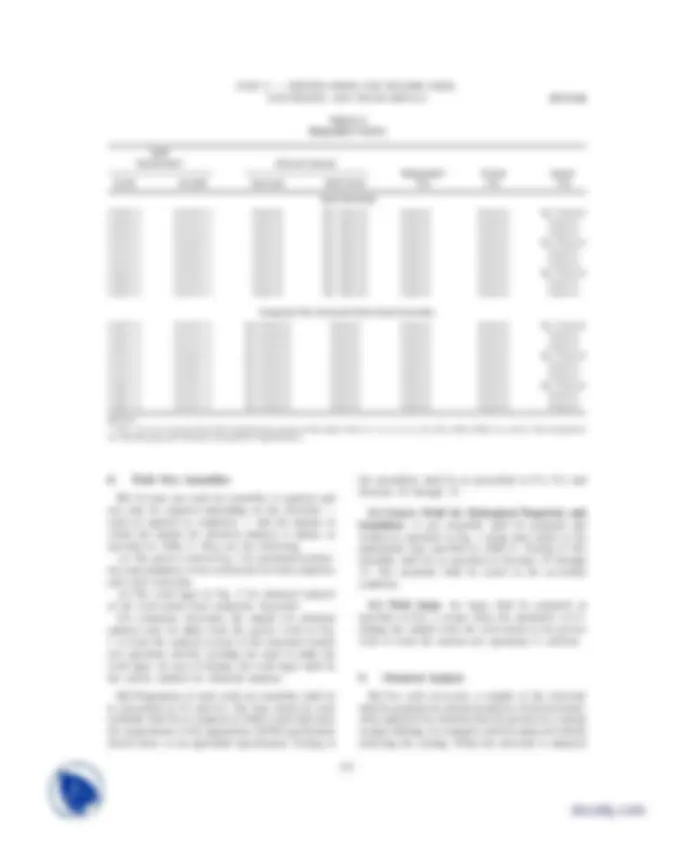
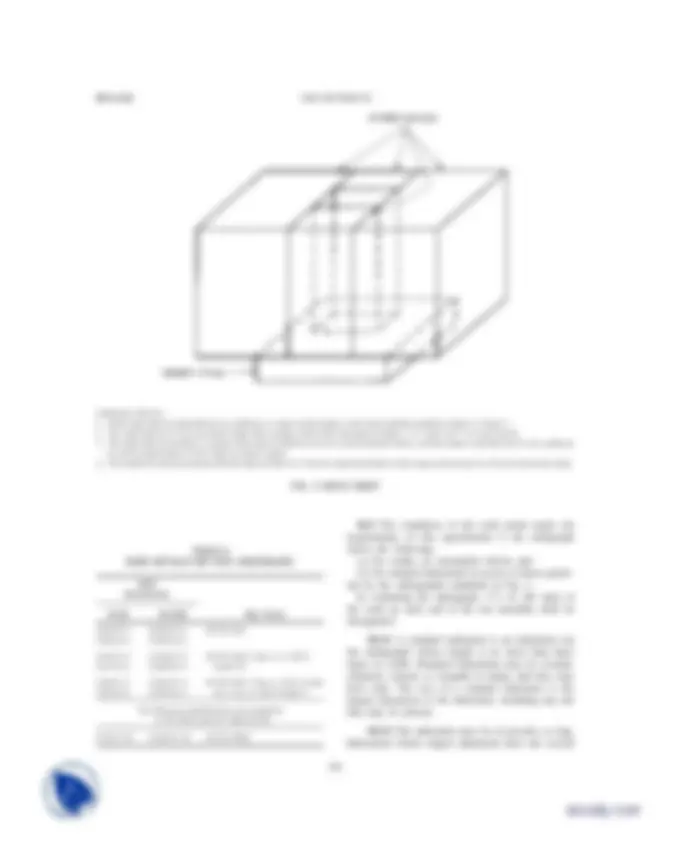
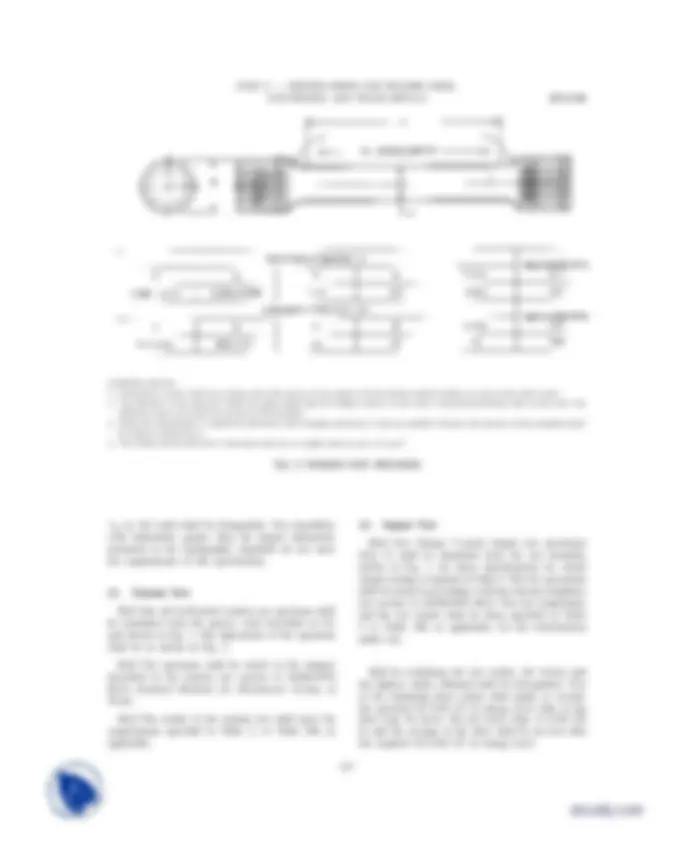
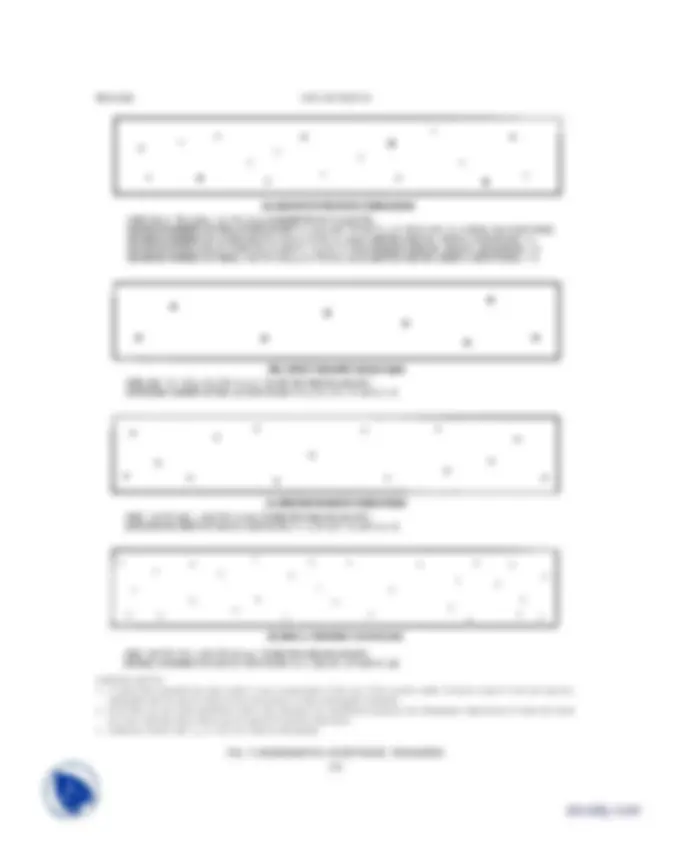
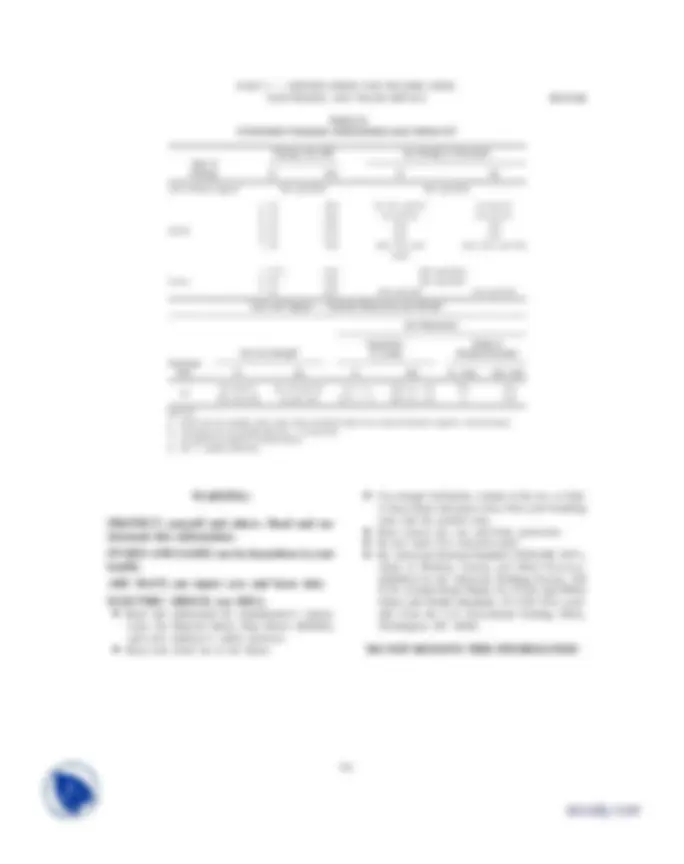
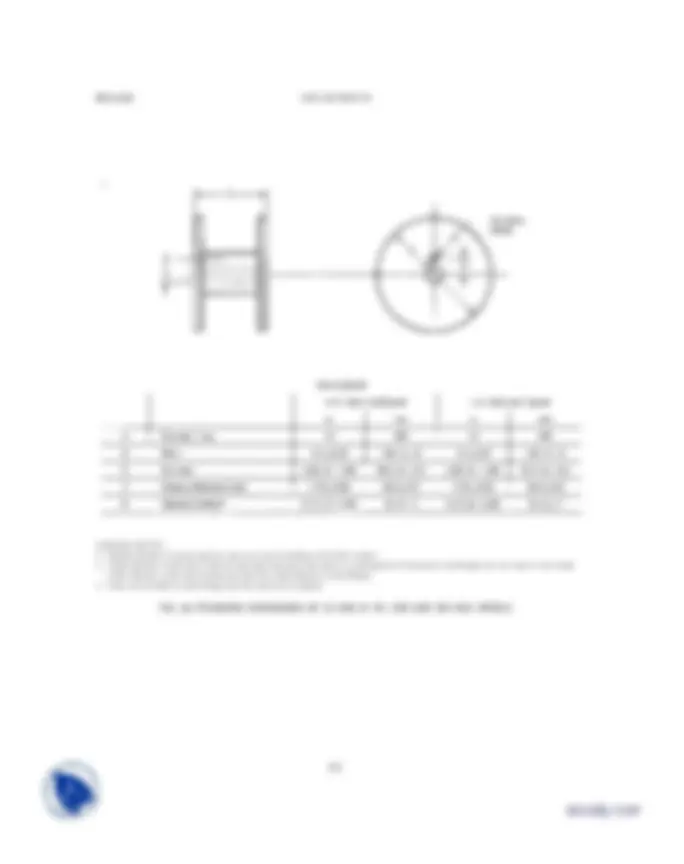
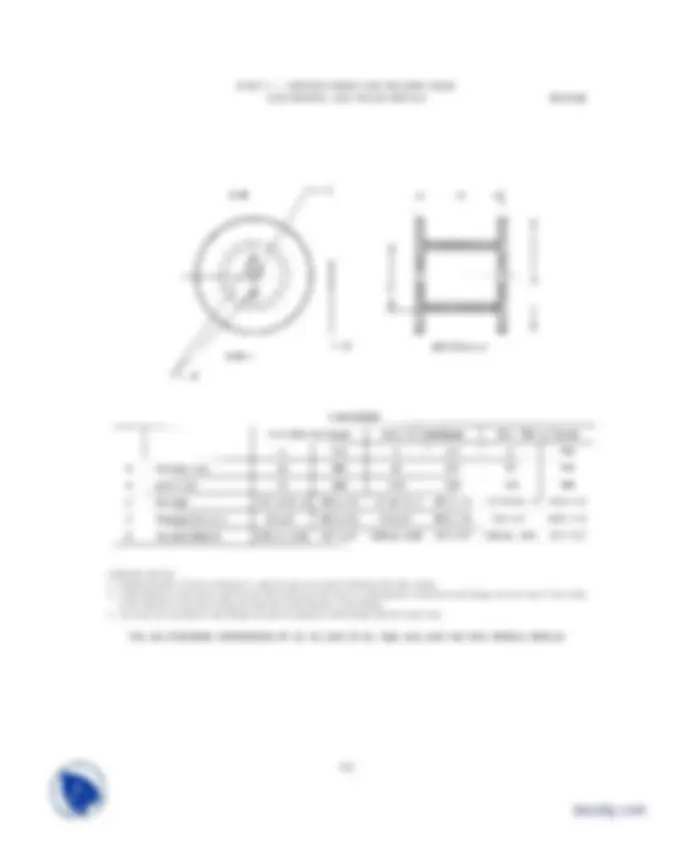
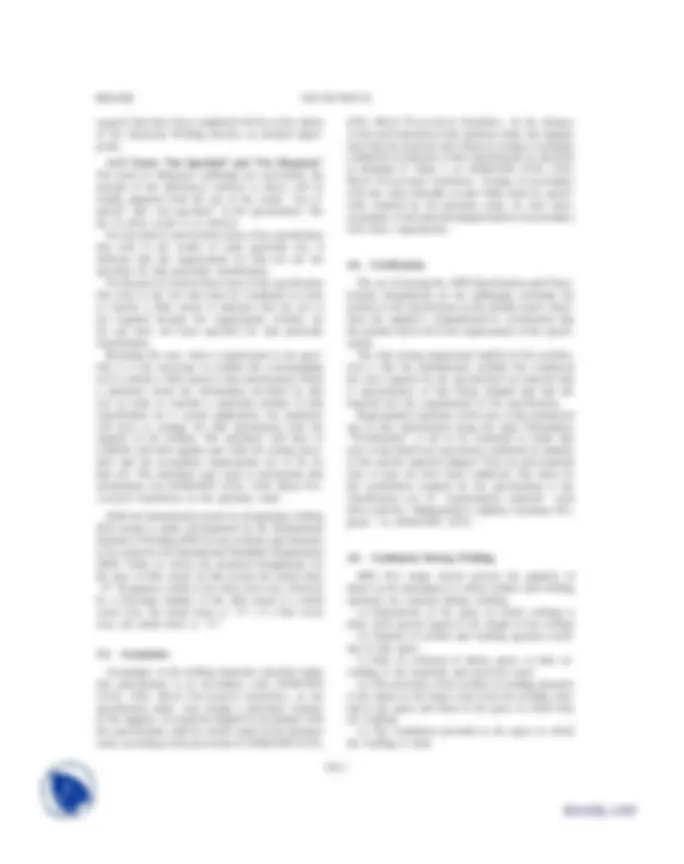
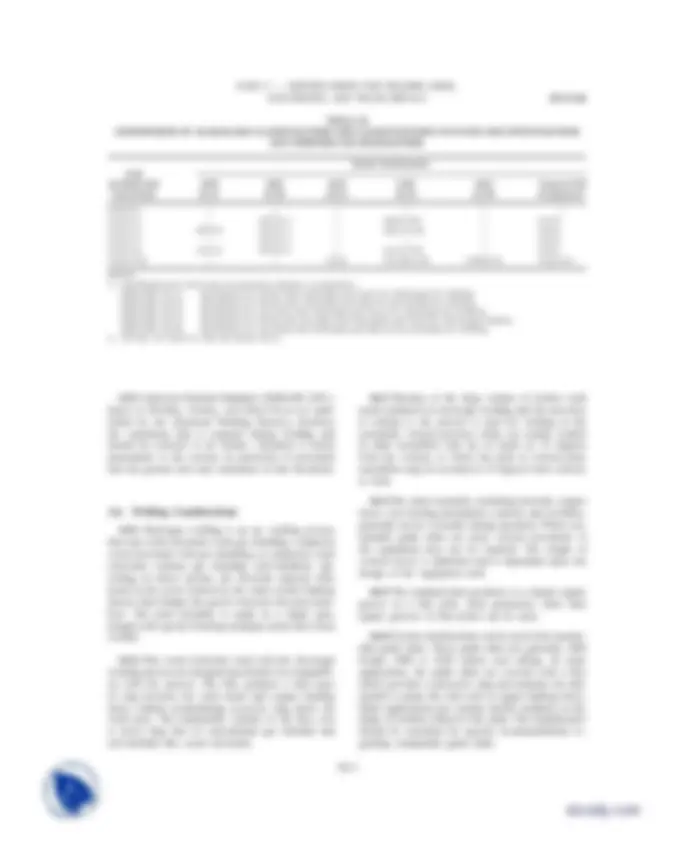
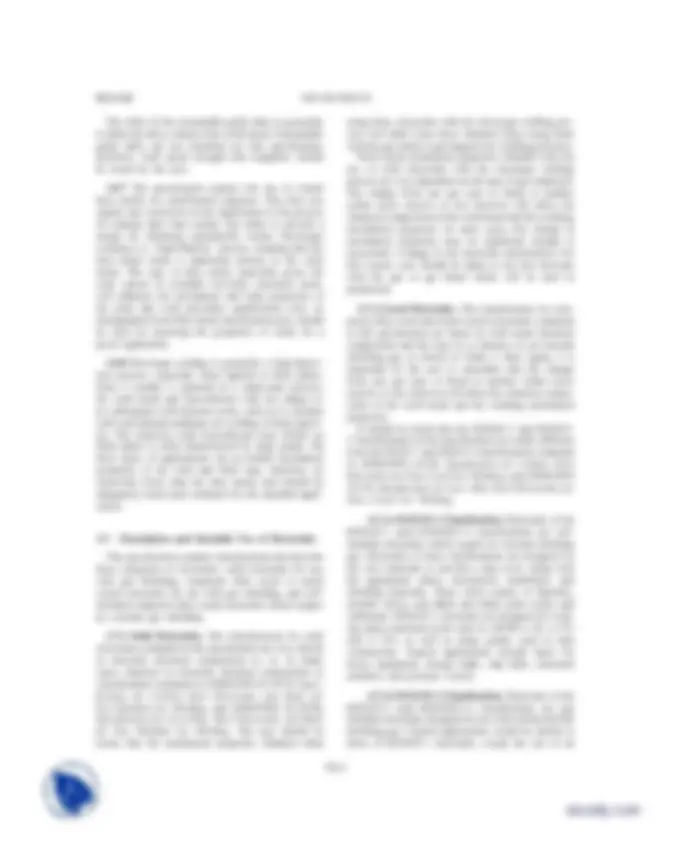
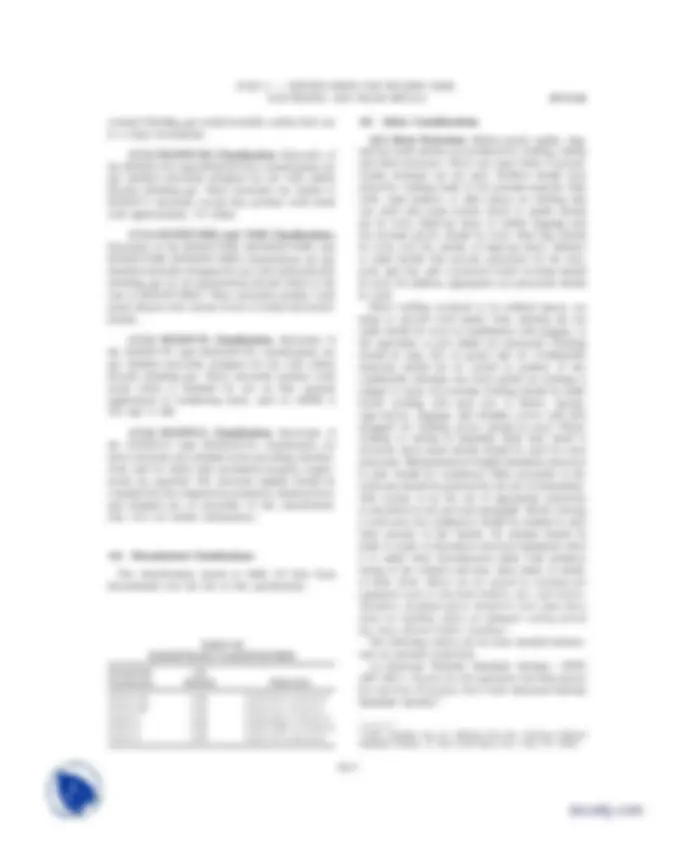
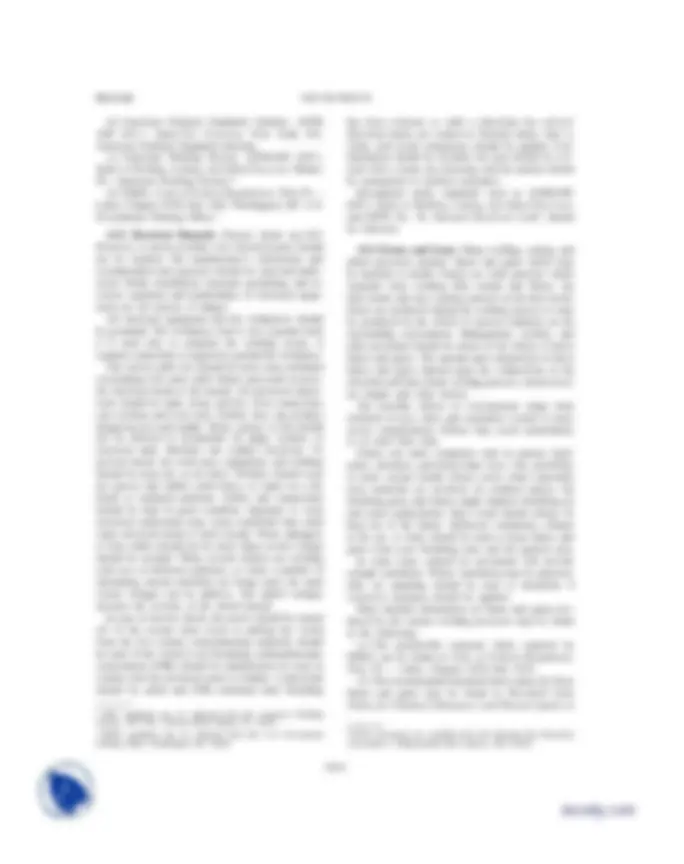
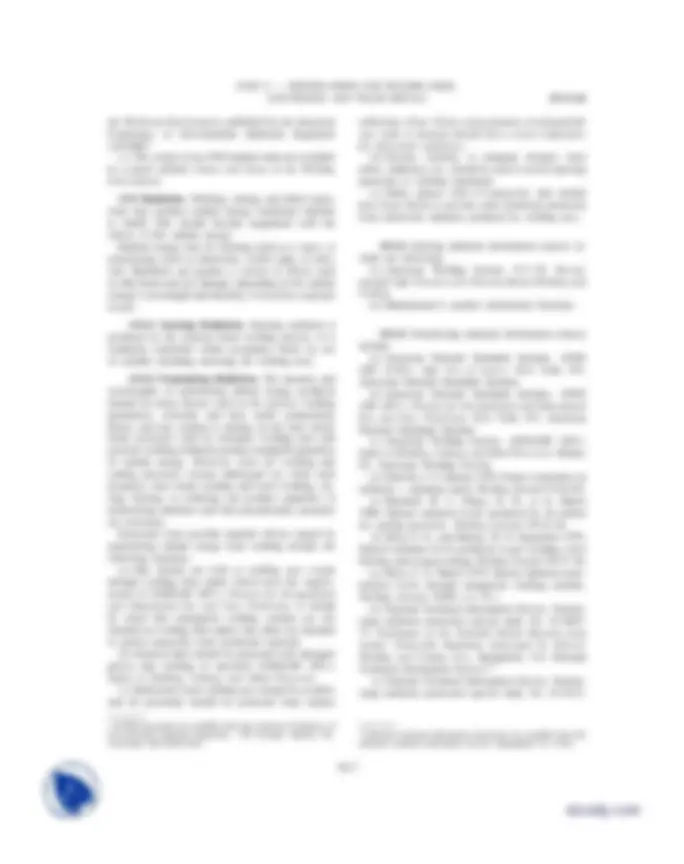
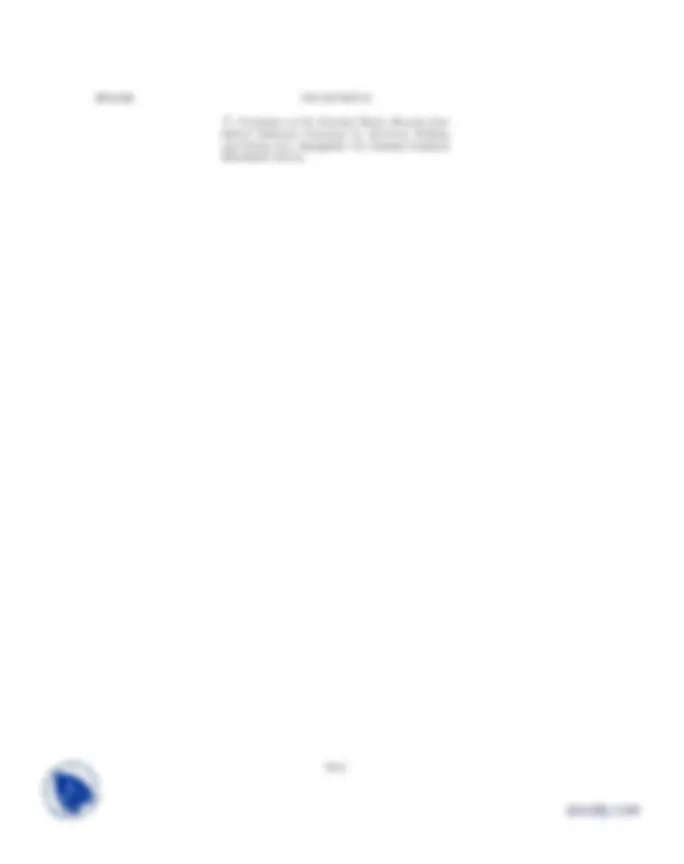
Study with the several resources on Docsity
Earn points by helping other students or get them with a premium plan
Prepare for your exams
Study with the several resources on Docsity
Earn points to download
Earn points by helping other students or get them with a premium plan
Community
Ask the community for help and clear up your study doubts
Discover the best universities in your country according to Docsity users
Free resources
Download our free guides on studying techniques, anxiety management strategies, and thesis advice from Docsity tutors
Specifications for welding rods, electrodes, and filler metals, including tension test requirements, required tests, and classification systems. It also discusses factors affecting fume quantity and nonionizing radiation protection in welding.
Typology: Exercises
1 / 24
This page cannot be seen from the preview
Don't miss anything!
(Identical with AWS Specification A5.26/A5.26M-97.)
1. Scope
This specification prescribes requirements for the classification of carbon and low-alloy steel electrodes for electrogas welding. It covers solid and composite (flux cored and metal cored) electrodes used with external gas shielding, and composite (self-shielded flux cored) electrodes used without external shielding.
2. Classification
2.1 The solid electrodes covered by this specification are classified according to the chemical composition of the electrode, as specified in Table 1 and the mechanical properties of the weld metal as specified in Tables 2 and 3.
2.2 The composite (flux cored and metal cored) electrodes covered by this specification are classified according to the need for external shielding gas (Table
2.3 Electrodes classified under one classification shall not be classified under any other classification in this specification, except as specifically permitted by Note (a) to Table 3.
2.4 The electrodes classified under this specification are intended for electrogas welding, but that is not to prohibit their use with any other process for which they are found suitable.
549
3. Acceptance Acceptance 1 of the electrodes shall be in accordance with the provisions of ANSI/AWS A5.01, Filler Metal Procurement Guidelines^2. 4. Certification By affixing the AWS Specification and Classification designations to the packaging, or the classification to the product, the manufacturer certifies that the product meets the requirements of this specification. 3 5. Units of Measure and Rounding-Off Procedure 5.1 This specification makes use of both U.S. Custom- ary Units and the International System of Units (SI). The measurements are not exact equivalents; therefore each system must be used independently of the other without combining in any way. The specification with the designation A5.26 uses U.S. Customary units. The specification A5.26M uses SI units. The latter are shown in appropriate columns in tables or within brackets [] when used in the text.
5.2 For the purpose of determining conformance with this specification, an observed or calculated value shall be rounded to the nearest 1000 psi [10 MPa] for tensile
(^1) See Section A3 (in the Annex) for further information concerning acceptance, testing of the material shipped, and ANSI/AWS A5.01, Filler Metal Procurement Guidelines. (^2) AWS standards can be obtained from the American Welding Society, 550 N.W. LeJeune Road, Miami, FL 33126. (^3) See Section A4 (in the Annex) for further information concerning certification and the testing called for to meet this requirement.
A
SFA-5.26 1998 SECTION II
TABLE 1
CHEMICAL COMPOSITION REQUIREMENTS FOR SOLID ELECTRODES
AWS
Weight, Percent
a,b
Other
Classifica-
UNS
Elements,
tion
c^
Number
d^
C^
Mn
S^
P
Si
Ni
Mo
Cu
e^
Ti
Zr
Al
Total
EGXXS-
K
0.07–0.
0.90–1.
0.30–0.
—
—
—
—
—
EGXXS-
K
0.90–1.
0.40–0.
—
—
0.05–0.
0.02–0.
0.05–0.
EGXXS-
K
0.06–0.
0.90–1.
0.45–0.
—
—
—
—
—
EGXXS-
K
0.07–0.
0.90–1.
0.30–0.
—
—
—
—
0.50–0.
EGXXS-
K
0.06–0.
1.40–1.
0.80–1.
—
—
—
—
—
EGXXS-D
K
0.07–0.
1.60–2.
0.50–0.
0.40–0.
—
—
—
EGXXS-G
—
Not Specified
f
NOTES:a.
The filler metal shall be analyzed for the specific elements for which values are shown in this table. If the presence of other elements is indicated, in the course of this work, the amountof those elements shall be determined to ensure that their total (excluding iron) does not exceed the limit specified for “Other Elements, Total” in the last column of the table. b. Single values are maximums. c. The letters “XX” as used in the AWS classification column of this table refer respectively to the designator for tensile strength of the weld metals (see Tables 2 and 2M) and the designatorfor impact strength (see Tables 3 and 3M). d. SAE/ASTM Unified Numbering System for Metals and Alloys. e. The copper limit includes copper that may be applied as a coating on the electrode.f. Composition shall be reported; the requirements are those agreed to by the purchaser and the supplier.
550
SFA-5.26 1998 SECTION II
TABLE 4 CHEMICAL COMPOSITION REQUIREMENTS FOR WELD METAL FROM COMPOSITE FLUX CORED AND METAL CORED ELECTRODES
AWS Classificationc^ Weight, Percenta,b^ Other UNS Shielding Elements, A5.26 A5.26M Numberd^ Gas C Mn P S Si Ni Cr Mo Cu V Total
EG6XT-1 EG43XT-1 W06301 None (e) 1.7 0.03 0.03 0.50 0.30 0.20 0.35 0.35 0.08 0. EG7XT-1 EG48XT-1 W07301 None (e) 1.7 0.03 0.03 0.50 0.30 0.20 0.35 0.35 0.08 0. EG8XT-1 EG55XT-1 — None (e) 1.8 0.03 0.03 0.90 0.30 0.20 0.25–0.65 0.35 0.08 0. EG6XT-2 EG43XT-2 W06302 CO 2 (e) 2.0 0.03 0.03 0.90 0.30 0.20 0.35 0.35 0.08 0. EG7XT-2 EG48XT-2 W07302 CO 2 (e) 2.0 0.03 0.03 0.90 0.30 0.20 0.35 0.35 0.08 0. EGXXT-Ni1 EGXXXT-Ni1 W21033 CO 2 0.10 1.0–1.8 0.03 0.03 0.50 0.70–1.10 — 0.30 0.35 — 0. EGXXT-NM1 EGXXXT-NM1 W22334 Ar/CO 2 0.12 1.0–2.0 0.02 0.03 0.15–0.50 1.5–2.0 0.20 0.40–0.65 0.35 0.05 0. or CO 2 EGXXT-NM2 EGXXXT-NM2 W22333 CO 2 0.12 1.1–2.1 0.03 0.03 0.20–0.60 1.1–2.0 0.20 0.10–0.35 0.35 0.05 0. EGXXT-W EGXXXT-W W20131 CO 2 0.12 0.50–1.3 0.03 0.03 0.30–0.80 0.40–0.80 0.45–0.70 — 0.30–0.75 — 0. EGXXT-G EGXXXT-G — Not Specifiedf
NOTES: a. The weld metal shall be analyzed for the specific elements for which values are shown in this table. If the presence of other elements is indicated, in the course of this work, the amount of those elements shall be determined to ensure that their total (excluding iron) does not exceed the limit specified for “Other Elements, Total” in the last column of this table. b. Single values are maximums. c. The letters “XX” or “XXX” as used in the AWS classification column in this table refer respectively to the designator(s) for tensile strength of the weld metal (see Tables 2 and 2M) and the designator for impact strength (see Tables 3 and 3M). The single letter “X” as used in the AWS classification column refers to the designator for impact strength (see Tables 3 and 3M). d. SAE/ASTM Unified Numbering System for Metals and Alloys. e. Composition range of carbon not specified for these classifications, but the amount shall be determined and reported. f. Composition shall be reported; the requirements are those agreed to by the purchaser and supplier.
and yield strength, and to the ‘‘nearest unit’’ in the last right-hand place of figures used in expressing the limiting value for other quantities in accordance with the rounding-off method given in ASTM E29, Standard Practice for Using Significant Digits in Test Data to Determine Conformance with Specifications.^4
6. Summary of Tests
6.1 The tests required for each classification are specified in Table 5. The purpose of these tests is to determine the chemical composition, the mechanical properties, and soundness of the weld. The base metal for the weld test assemblies, the welding and testing procedures to be employed, and the results required are given in Sections 8 through 12.
(^4) ASTM standards can be obtained from the American Society for Testing and Materials, 100 Barr Harbor Drive, West Conshohocken, PA 19428-2959.
552
7. Retest If the results of any test fail to meet the requirement, that test shall be repeated twice. The results of both retests shall meet the requirement. Specimens for retest may be taken from the original test assembly or from one or two new test assemblies. For chemical analysis, retest need be only for those specific elements that failed to meet the test requirement. If the results of one or both retests fail to meet the requirement, the material under test shall be considered as not meeting the requirements of this specification for that classification. In the event that, during preparation or after comple- tion of any test, it is clearly determined that prescribed or proper procedures were not followed in preparing the weld test assembly or test specimens or in conducting the test, the test shall be considered invalid without regard to whether the test was actually completed, or whether test results met, or failed to meet, the require- ment. That test shall be repeated, following prescribed procedures. In this case the requirement for doubling of the number of test specimens does not apply.
PART C — SPECIFICATIONS FOR WELDING RODS, ELECTRODES, AND FILLER METALS SFA-5.
TABLE 5 REQUIRED TESTS
AWS Classification Chemical Analysis Radiographic Tension Impact A5.26 A5.26M Electrode Weld Metal Test Test Test Solid Electrodes* EG6ZS-X EG43ZS-X Required Not Required Required Required Not Required EG60S-X EG432S-X Required Not Required Required Required Required EG62S-X EG433S-X Required Not Required Required Required Required EG7ZS-X EG48ZS-X Required Not Required Required Required Not Required EG70S-X EG482S-X Required Not Required Required Required Required EG72S-X EG483S-X Required Not Required Required Required Required EG8ZS-X EG55ZS-X Required Not Required Required Required Not Required EG80S-X EG552S-X Required Not Required Required Required Required EG82S-X EG553S-X Required Not Required Required Required Required
Composite Flux Cored and Metal Cored Electrodes EG6ZT-X EG43ZT-X Not Required Required Required Required Not Required EG60T-X EG432T-X Not Required Required Required Required Required EG62T-X EG433T-X Not Required Required Required Required Required EG7ZT-X EG48ZT-X Not Required Required Required Required Not Required EG70T-X EG482T-X Not Required Required Required Required Required EG72T-X EG483T-X Not Required Required Required Required Required EG8ZT-X EG55ZT-X Not Required Required Required Required Not Required EG80T-X EG552T-X Not Required Required Required Required Required EG82T-X EG553T-X Not Required Required Required Required Required
NOTES:
8. Weld Test Assemblies
8.1 At least one weld test assembly is required, and two may be required (depending on the electrode — solid as opposed to composite — and the manner in which the sample for chemical analysis is taken), as specified in Table 5. They are the following: (a) The groove weld in Fig. 1 for mechanical proper- ties and soundness of the weld metal for both composite and solid electrodes (b) The weld ingot in Fig. 2 for chemical analysis of the weld metal from composite electrodes For composite electrodes, the sample for chemical analysis may be taken from the groove weld in Fig. 1 or from the reduced section of the fractured tension test specimen, thereby avoiding the need to make the weld ingot. In case of dispute, the weld ingot shall be the referee method for chemical analysis.
8.2 Preparation of each weld test assembly shall be as prescribed in 8.3 and 8.4. The base metal for each assembly shall be as required in Table 6 and shall meet the requirements of the appropriate ASTM specification shown there, or an equivalent specification. Testing of
553
the assemblies shall be as prescribed in 9.2, 9.3, and Sections 10 through 12.
8.3 Groove Weld for Mechanical Properties and Soundness. A test assembly shall be prepared and welded as specified in Fig. 1 using base metal of the appropriate type specified in Table 6. Testing of this assembly shall be as specified in Sections 10 through
8.4 Weld Ingot. An ingot shall be prepared as specified in Fig. 2 except when the alternative in 8. (taking the sample from the weld metal in the groove weld or from the tension test specimen) is selected.
9. Chemical Analysis 9.1 For solid electrodes , a sample of the electrode shall be prepared for chemical analysis. Solid electrodes, when analyzed for elements that are present in a coating (copper flashing, for example), shall be analyzed without removing the coating. When the electrode is analyzed
PART C — SPECIFICATIONS FOR WELDING RODS, ELECTRODES, AND FILLER METALS SFA-5.
GENERAL NOTES: a. Weld test assembly shall be welded in the vertical position with upward progression. b. Fixturing of the test assembly shall be based on the manufacturer’s recommendations. Water-cooled copper shoes shall be used except when using consumable guide tubes. For welding with consumable guide tubes, follow the manufacturer’s recommendations regarding the use of water-cooled shoes. When using water cooling, the outgoing water temperature shall not exceed 180°F [80°C] near the exit point. c. If the manufacturer does not make the electrode size specified, the nearest size may be used. For sizes other than that shown, the manufacturer’s recommended procedure shall be used. d. Either wire feed speed or current shall be used as a control setting based on the design of the equipment. e. Welding shall begin with the assembly at room temperature, 65°F [18°C] minimum. No external heat shall be applied during welding. Starting and run-off tabs are not required if the test assembly without weld tabs is sufficient to provide the required test specimens. f. The weld shall be completed in one pass. g. A postweld heat treatment shall not be applied to the test assembly. h. Single V-groove joint is optional for CO 2 gas shielded classifications only. In case of dispute, the square groove assembly is the referee method. Root opening, R, for single-V groove is 5 ⁄ 32 in. [4 mm].
FIG. 1 GROOVE WELD TEST ASSEMBLY FOR MECHANICAL PROPERTIES AND SOUNDNESS (CONT’D)
Fig. 1 is used, the sample shall be prepared by any suitable mechanical means. The sample from the groove weld shall be taken at least 2 in. [50 mm] from both the start and crater ends of the weld.
9.3 The sample shall be analyzed by accepted analyti- cal methods. The referee method shall be ASTM Stan- dard Method E350, Chemical Analysis of Carbon Steel, Low-Alloy Steel, Silicon Electrical Steel, Ingot Iron and Wrought Iron.
9.4 The results of the analysis shall meet the require- ments of Table 1 for solid electrodes and Table 4 for composite electrodes, for the classification of electrode under test.
555
10. Radiographic Test 10.1 The groove weld described in 8.3 and shown in Fig. 1 shall be radiographed to evaluate the soundness of the weld metal. In preparation for radiography, both surfaces of the weld may be machined or ground smooth and flush with the original surfaces of the base metal or with a uniform reinforcement not exceeding (^3) ⁄ 32 in. [2.5 mm]. Both surfaces of the test assembly, in the area of the weld, shall be smooth enough to avoid difficulty in interpreting the radiograph.
10.2 The weld shall be radiographed in accordance with ASTM E142, Standard Method for Controlling Quality of Radiographic Testing. The quality level of inspection shall be 2-2T.
SFA-5.26 1998 SECTION II
GENERAL NOTES:
FIG. 2 WELD INGOT
TABLE 6 BASE METALS FOR TEST ASSEMBLIES
AWS Classification
A5.26 A5.26M Base Metal
EG6XT-X EG43XT-X ASTM A EG6XS-X EG43XS-X
EG7XT-X EF48XT-X ASTM A242 Type 2, or A EG7XS-X EG48XS-X Grade 50
EG8XT-X EG55XT-X ASTM A537 Class 2, A572 Grade EG8XS-X EG55XS-X 60 or 65, or A633 Grade E
The following classifications are exceptions to the above general requirements:
EGXXT-W EGXXXT-W ASTM A
556
10.3 The soundness of the weld metal meets the requirements of this specification if the radiograph shows the following: (a) No cracks, no incomplete fusion, and (b) No rounded indications in excess of those permit- ted by the radiographic standards in Fig. 4. In evaluating the radiograph, 2- 1 ⁄ 2 in. [65 mm] of the weld on each end of the test assembly shall be disregarded.
10.3.1 A rounded indication is an indication (on the radiograph) whose length is no more than three times its width. Rounded indications may be circular, elliptical, conical, or irregular in shape, and they may have tails. The size of a rounded indication is the largest dimension of the indication, including any tail that may be present.
10.3.2 The indication may be of porosity or slag. Indications whose largest dimension does not exceed
SFA-5.26 1998 SECTION II
GENERAL NOTES:
FIG. 4 RADIOGRAPHIC ACCEPTANCE STANDARDS 558
PART C — SPECIFICATIONS FOR WELDING RODS, ELECTRODES, AND FILLER METALS SFA-5.
NOTES:
FIG. 5 CHARPY V-NOTCH IMPACT TEST SPECIMEN
13. Method of Manufacture
The electrodes classified according to this specifica- tion may be manufactured by any method that will produce material that meets the requirements of this specification.
14. Standard Sizes
Standard sizes for electrodes in the different package forms (coils with support, coils without support, spools and drums) are shown in Table 7.
15. Finish and Uniformity
15.1 All electrodes shall have a smooth finish that is free from slivers, depressions, scratches, scale, seams or laps (exclusive of the longitudinal joint in composite electrodes), and foreign matter that would adversely
559
affect the welding characteristics, the operation of the welding equipment, or the properties of the weld metal.
15.2 Each continuous length of electrode shall be from a single lot of material, and welds, when present, shall have been made so as not to interfere with the uniform, uninterrupted feeding of the electrode on automatic equipment.
15.3 The core ingredients in composite electrodes shall be distributed with sufficient uniformity throughout the length of the electrode so as not to adversely affect the performance of the electrode or the properties of the weld metal.
15.4 A suitable protective coating may be applied to any of the electrodes in this specification.
16. Standard Package Forms 16.1 Standard package forms are coils with support, coils without support, spools, and drums. Standard
PART C — SPECIFICATIONS FOR WELDING RODS, ELECTRODES, AND FILLER METALS SFA-5.
TABLE 8 STANDARD PACKAGE DIMENSIONS AND WEIGHTS a
Package Size OD d^ Net Weight of Electrode b Type of Package in. mm lb kg Coils without support Not specified c^ Not specified c
12 300 25, 30, and 35^ 10 and 15 14 360 50 and 60 20 and 25 Spools ^22 560 250 24 610 300 150 30 760 600, 750, and 250, 350, and 450 1000
^15 1 ⁄^2 400 Not specified^ c Drums (^) 20 500 Not specified c 23 600 300 and 600 150 and 300 Coils with Support — Standard Dimensions and Weight a
Coil Dimensions
Inside Dia. Width of Coil Net Weightb^ of Lining Wound Electrodes Electrode Size lb kg in. mm in., max. mm, max.
All 60 and 75^ 20, 25 and 30^12 6 1 ⁄^8 300 +3, −10^4 5 ⁄^8 150 and 200 75 and 100 231 ⁄ 2 6 1 ⁄ 4 600 +3, −10 5 125 NOTES: a. Sizes and net weights other than those specified shall be as agreed between supplier and purchaser. b. Tolerance on net weight shall be 6 10 percent. c. As agreed by supplier and purchaser. d. OD p outside diameter.
O Read and understand the manufacturer’s instruc- tions, the Material Safety Data Sheets (MSDSs), and your employer’s safety practices. O Keep your head out of the fumes.
561
O Use enough ventilation, exhaust at the arc, or both, to keep fumes and gases away from your breathing zone and the general area. O Wear correct eye, ear, and body protection. O Do not touch live electrical parts. O See American National Standard ANSI/ASC Z49.1, Safety in Welding, Cutting, and Allied Processes, published by the American Welding Society, 550 N.W. LeJeune Road, Miami, FL 33126; and OSHA Safety and Health Standards, 29 CFR 1910 , avail- able from the U.S. Government Printing Office, Washington, DC 20402.
SFA-5.26 1998 SECTION II
GENERAL NOTES:
FIG. 6A STANDARD DIMENSIONS OF 12 AND 14 IN. [300 AND 350 MM] SPOOLS
562
SFA-5.26 1998 SECTION II
(This Annex is not a part of ANSI/AWS A5.26/A5.26M-97, Specification for Carbon and Low-Alloy Steel Electrodes for Electro- gas Welding , but is included for information purposes only.)
A1. Introduction
The purpose of this annex is to correlate the electrode classifications with their intended applications so the specification can be used effectively. Reference to appro- priate base metal specifications is made whenever that can be done and when it would be helpful. Such references are intended only as examples rather than complete listings of the base metals for which each filler metal is suitable.
A2. Classification System
A2.1 The system for identifying the electrode classi- fications in this specification follows the standard pattern used in other AWS filler metal specifications (see Fig. A1). The letters ‘‘EG’’ at the beginning of each classification designation shows that the electrode is intended for use with the electrogas welding process. In the case of the designations for A5.26, this is followed by a single digit (6, 7, or 8) representing the minimum tensile strength of the weld metal in units of 10 000 psi. For the designations of A5.26M, the ‘‘EG’’ is followed by two digits (43, 48, or 55) representing the minimum tensile strength in units of 10 MPa (see Table 2M). The digit that follows is a number or the letter ‘‘Z.’’ The number designates the temperature at which (and/ or above which) the weld metal meets or exceeds the required 20 ft·lbf [27 J] Charpy V-notch impact strength. The letter ‘‘Z’’ indicates that no impact strength require- ment is specified.
564
The next letter, either S or T, indicates that the electrode is solid (S) or composite (flux cored or metal cored) (T). The designator (digits or letters) following the hyphen in the classification indicates the chemical composition (of weld metal for the composite electrodes and of the electrode itself for solid electrodes) and the type or absence of shielding gas required in the case of composite electrodes only.
A2.2 ‘‘G’’ Classification
A2.2.1 This specification includes filler metals classified as EGXXT-G or EGXXS-G. The last ‘‘G’’ indicates that the filler metal is of a general classifica- tion. It is ‘‘general’’ because not all of the particular requirements specified for each of the other classifica- tions are specified for this classification. The intent in establishing this classification is to provide a means by which filler metals that differ in one respect or another (chemical composition, for example) from all other classifications (meaning that the composition of the filler metal, in the case of the example, does not meet the composition specified for any of the classifications in the specification) can still be classified according to the specification. The purpose is to allow a useful filler metal — one that otherwise would have to await a revision of the specification — to be classified immediately, under the existing specification. This means, then, that two filler metals, each bearing the same ‘‘G’’ classification, may be quite different in some certain respect (chemical composition, again, for example).
PART C — SPECIFICATIONS FOR WELDING RODS, ELECTRODES, AND FILLER METALS SFA-5.
FIG. A1 CLASSIFICATION SYSTEM
A2.2.2 Request for Filler Metal Classification (a) When a filler metal cannot be classified according to some classification other than a ‘‘G’’ classification, the manufacturer may request that a classification be established for that filler metal. The manufacturer may do this by following the procedure given here. When the manufacturer elects to use the ‘‘G’’ classification, the Committee on Filler Metals recommends that the manufacturer still request that a classification be estab- lished for that filler metal, as long as the filler metal is of commercial significance. (b) A request to establish a new filler metal classifi- cation must be a written request and it needs to provide sufficient detail to permit the Committee on Filler Metals or the Subcommittee to determine whether the new classification or the modification of an existing classification is more appropriate to satisfy the need. The request needs to state the variables and their limits for such a classification or modification. The request should contain some indication of the time by which completion of the new classification or modification is needed. (c) The request should be sent to the Secretary of the Committee on Filler Metals at AWS headquarters. Upon receipt of the request, the Secretary will:
(1) Assign an identifying number to the request. This number will include the date the request was received. (2) Confirm receipt of the request and give the identification number to the person who made the request. (3) Send a copy of the request to the Chairman of the Committee on Filler Metals and the Chairman of the particular Subcommittee involved. (4) File the original request. (5) Add the request to the log of outstanding requests. (d) All necessary action on each request will be completed as soon as possible. If more than 12 months lapse, the Secretary shall inform the requestor of the status of the request, with copies to the Chairmen of the Committee and of the Subcommittee. Requests still outstanding after 18 months shall be considered not to have been answered in a ‘‘timely manner’’ and the Secretary shall report these to the Chairman of the Committee on Filler Metals for action. (e) The Secretary shall include a copy of the log of all requests pending and those completed during the preceding year with the agenda for each Committee on Filler Metals meeting. Any other publication of
PART C — SPECIFICATIONS FOR WELDING RODS, ELECTRODES, AND FILLER METALS SFA-5.
TABLE A COMPARISONS OF A5.26/A5.26M CLASSIFICATIONS AND CLASSIFICATIONS IN OTHER AWS SPECIFICATIONS AND PROPOSED ISO DESIGNATIONS
Similar Classifications a AWS A5.26/A5.26M AWS AWS AWS AWS AWS Proposed ISO Classification A5.17 A5.18 A5.23 A5.25 A5.28 Designations b
EGXXS-1 — — — — — — EGXXS-2 — ER70S-2 — EM5K-EW — S EGXXS-3 EM13K ER70S-3 — EM13K-EW — S EGXXS-5 — ER70S-5 — — — S EGXXS-6 EH11K ER70S-6 — EH11K-EW — S EGXXS-D2 — — EA3K EH10Mo-EW ER80S-D2 S3020-A
NOTES: a. Classifications are similar but not necessarily identical in composition. ANSI/AWS A5.17 Specification for Carbon Steel Electrodes and Fluxes for Submerged Arc Welding ANSI/AWS A5.18 Specification for Carbon Steel Electrodes and Rods for Gas Shielded Arc Welding ANSI/AWS A5.23 Specification for Low-Alloy Steel Electrodes and Fluxes for Submerged Arc Welding ANSI/AWS A5.25 Specification for Carbon and Low-Alloy Steel Electrodes and Fluxes for Electroslag Welding ANSI/AWS A5.28 Specification for Low-Alloy Steel Electrodes and Rods for Gas Shielding Arc Welding b. IIW Doc. XII-1232-91 (also see Section A2.5).
A5.2 American National Standard ANSI/ASC Z49.1, Safety in Welding, Cutting, and Allied Processes (pub- lished by the American Welding Society), discusses the ventilation that is required during welding and should be referred to for details. Attention is drawn particularly to the section on protection of personnel and the general area and ventilation in that document.
A6. Welding Considerations
A6.1 Electrogas welding is an arc welding process that uses solid electrodes with gas shielding, composite cored electrodes with gas shielding, or composite cored electrodes without gas shielding (self-shielded). Op- erating on direct current, the electrode deposits filler metal in the cavity formed by the water-cooled backing shoe(s) that bridges the groove between the joint mem- bers. The joint normally is made in a single pass, though with special fixturing multipass joints have been welded.
A6.2 Flux cored electrodes used with the electrogas welding process are designed specifically for compatibil- ity with the process. The flux produces a thin layer of slag between the weld metal and copper backing shoes without accumulating excessive slag above the weld pool. The nonmetallic content of the flux core is lower than that of conventional gas shielded and self-shielded flux cored electrodes.
A6.3 Because of the large volume of molten weld metal produced in electrogas welding and the necessity to contain it, the process is used for welding in the essentially vertical position. Joints are readily welded in plate assemblies that are as much as 15 degrees from the vertical, or where the joint in vertical plate assemblies may be as much as 15 degrees from vertical, or both.
A6.4 The entire assembly, including electrode, copper shoes, wire-feeding mechanism, controls, and oscillator, generally moves vertically during operation. When con- sumable guide tubes are used, vertical movement of the equipment may not be required. The length of vertical travel is unlimited and is dependent upon the design of the equipment used.
A6.5 The standard joint geometry is a simple square groove in a butt joint. Joint geometries other than square grooves in butt joints can be used.
A6.6 Certain classifications can be used with consum- able guide tubes. These guide tubes are generally AISI Grades 1008 to 1020 carbon steel tubing. In some applications, the guide tubes are covered with a flux which provides a protective slag and insulates the tube should it contact the side wall or copper backing shoes. Other applications use ceramic fusible insulators in the shape of washers affixed to the tubes. The manufacturer should be consulted for specific recommendations re- garding consumable guide tubes.
SFA-5.26 1998 SECTION II
The effect of the consumable guide tubes is generally to dilute the alloy content of the weld metal. Consumable guide tubes are not classified per this specification; therefore, weld metal strength and toughness should be tested by the user.
A6.7 The specification requires the use of certain base metals for classification purposes. This does not signify any restriction on the application of the process for joining other base metals, but rather to provide a means for obtaining reproducible results. Electrogas welding is a ‘‘high-dilution’’ process, meaning that the base metal forms a significant portion of the weld metal. The type of base metal, especially given the wide variety of available low-alloy structural steels, will influence the mechanical and other properties of the joint and weld procedure qualification tests, as distinguished from filler metal classification tests, should be used for assessing the properties of welds for a given application.
A6.8 Electrogas welding is generally a high-deposi- tion process, especially when applied to thick plates. Since it usually is operated as a single-pass process, the weld metal and heat-affected zone are subject to no subsequent weld thermal cycles, such as is common with conventional multipass arc welding of thick materi- als. The relatively wide heat-affected zone (HAZ) on thick plates is often characterized by large grains. On these types of applications, the as-welded mechanical properties of the weld and HAZ may, therefore, be somewhat lower than the base metal, and should be adequately tested and evaluated for the intended appli- cation.
A7. Description and Intended Use of Electrodes
This specification contains classifications that describe three categories of electrodes: solid electrodes for use with gas shielding, composite (flux cored or metal cored) electrodes for use with gas shielding, and self- shielded composite (flux cored) electrodes which require no external gas shielding.
A7.1 Solid Electrodes. The classifications for solid electrodes contained in this specification are very similar in electrode chemical composition to, or, in many cases, identical in electrode chemical composition to classifications contained in ANSI/AWS A5.18-93, Speci- fication for Carbon Steel Electrodes and Rods for Gas Shielded Arc Welding , and ANSI/AWS A5.28-96, Specification for Low-Alloy Steel Electrodes and Rods for Gas Shielded Arc Welding. The user should be aware that the mechanical properties obtained when
using these electrodes with the electrogas welding pro- cess will differ from those obtained when using them with the gas metal or gas tungsten arc welding processes. Weld metal mechanical properties obtained with the use of solid electrodes with the electrogas welding process are very dependent on the type of gas employed. The change from one gas type or blend to another (either more reactive or less reactive) will affect the chemical composition of the weld metal and the resulting mechanical properties. In some cases, this change in mechanical properties may be significant enough to necessitate a change in the electrode classification. For this reason, care should be taken to test the electrode with the gas or gas blend which will be used in production.
A7.2 Cored Electrodes. The classifications for com- posite (flux cored and metal cored) electrodes contained in this specification are based on weld metal chemical composition and the type of, or absence of, an external shielding gas, as shown in Table 4. Once again, it is important for the user to remember that the change from one gas type or blend to another (either more reactive or less reactive) will affect the chemical compo- sition of the weld metal and the resulting mechanical properties. It should be noted that the EGXXT-1 and EGXXT- 2 classifications in this specification are totally different from the EXXT-1 and EXXT-2 classifications contained in ANSI/AWS A5.20, Specification for Carbon Steel Electrodes for Flux Cored Arc Welding , and ANSI/AWS A5.29, Specification for Low Alloy Steel Electrodes for Flux Cored Arc Welding.
A7.2.1 EGXXT-1 Classification. Electrodes of the EGXXT-1 (and EGXXXT-1) classifications are self- shielded electrodes which require no external shielding gas. Electrodes of these classifications are designed for the core materials to provide a slag cover, along with the appropriate alloys, deoxidizers, denitrifiers, and shielding materials. These often consist of fluorides, metallic alloys, and alkali and alkali earth oxides and carbonates. EGXXT-1 electrodes are designed for weld- ing many structural steels such as ASTM A 36, A 572 and A 515, as well as many grades used in ship construction. Typical applications include bases for heavy equipment, storage tanks, ship hulls, structural members and pressure vessels.
A7.2.2 EGXXT-2 Classification. Electrodes of the EGXXT-2 (and EGXXXT-2) classifications are gas shielded electrodes designed for use with carbon dioxide shielding gas. Typical applications would be similar to those of EGXXT-1 electrodes, except the use of an