
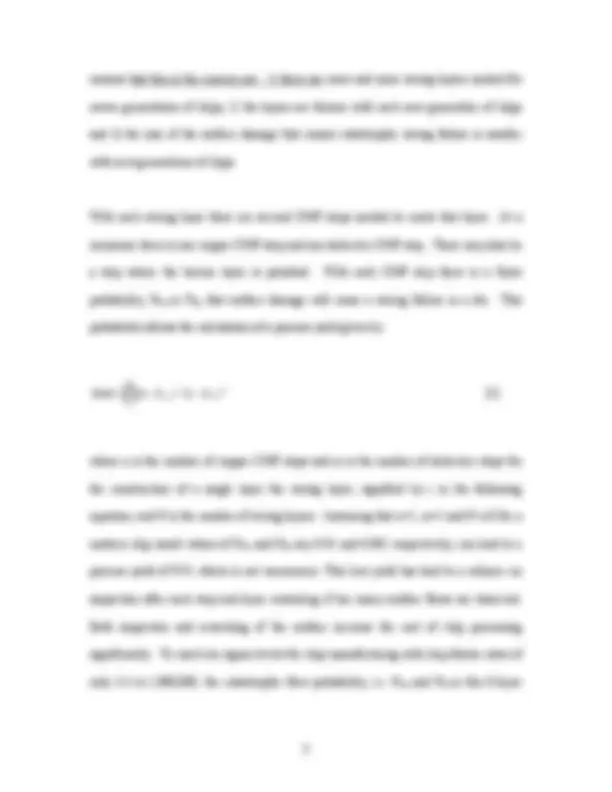
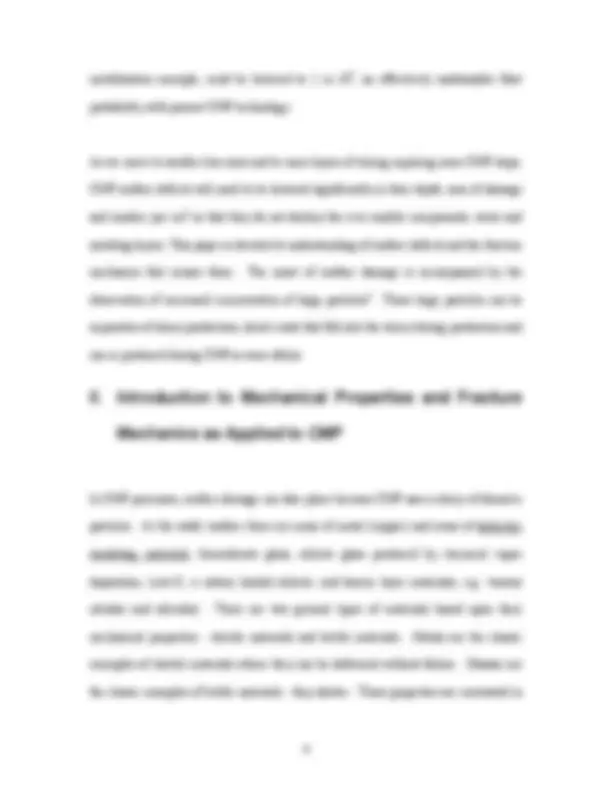
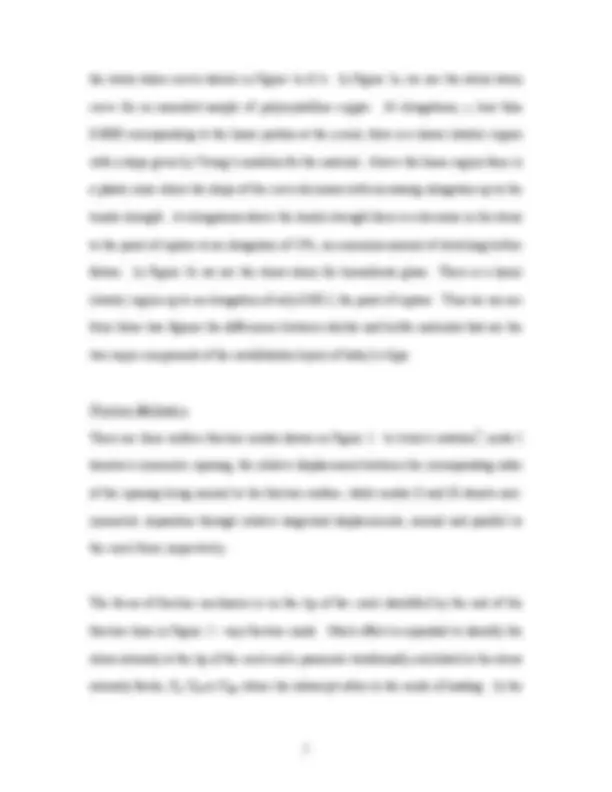
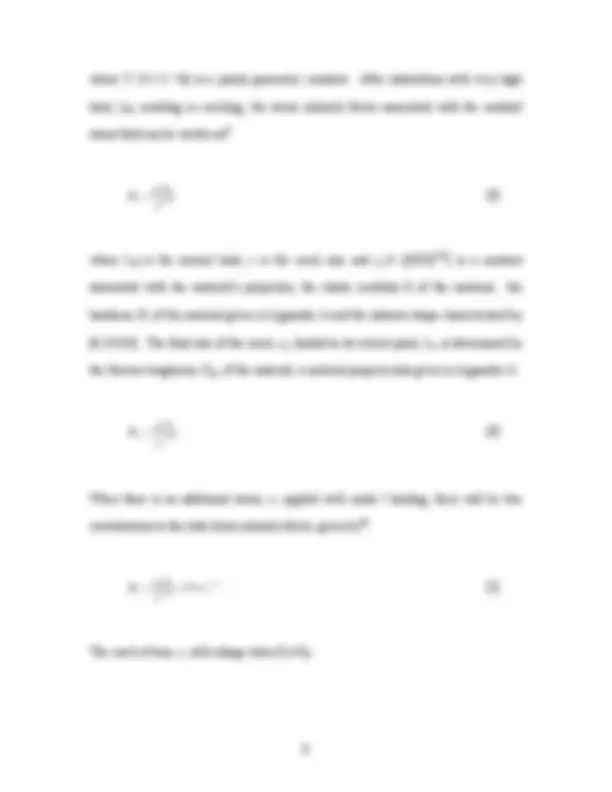
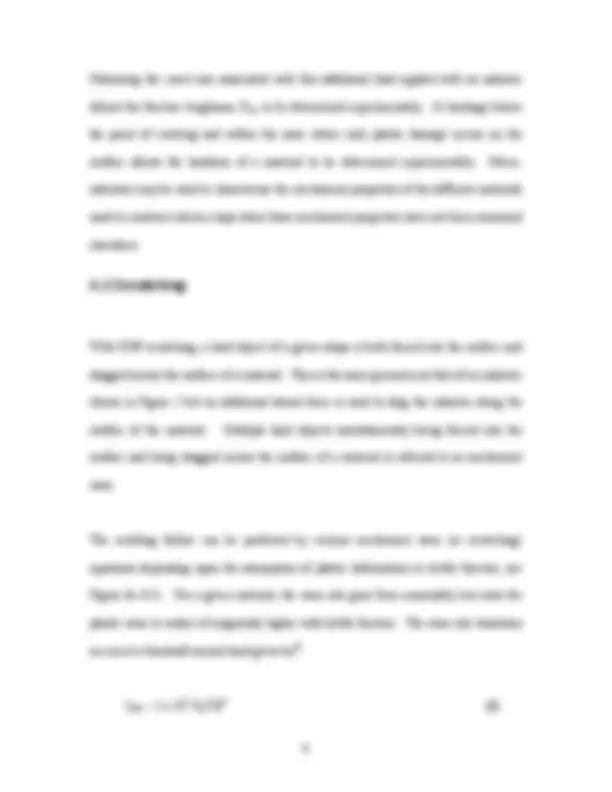
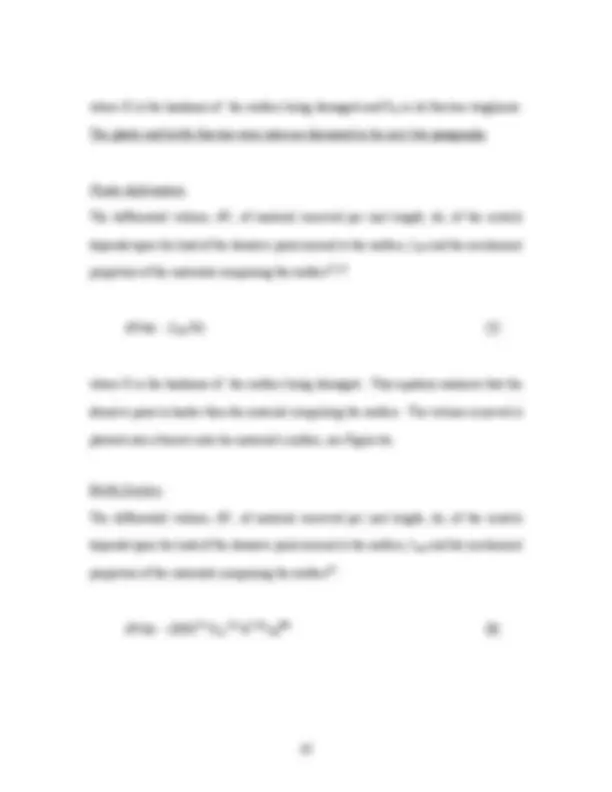
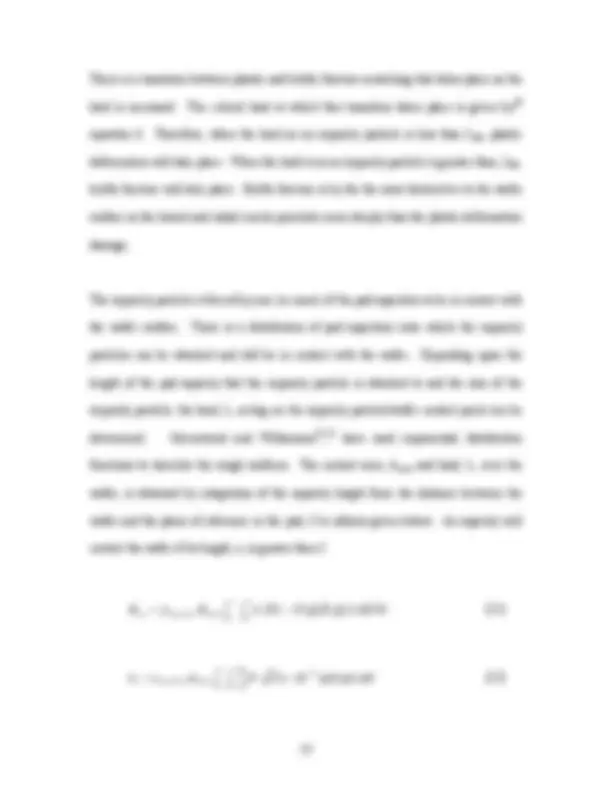
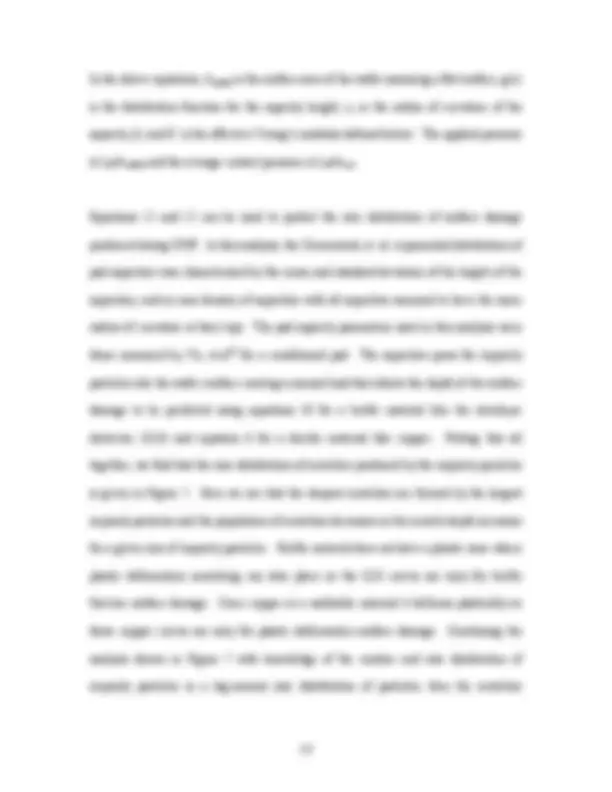
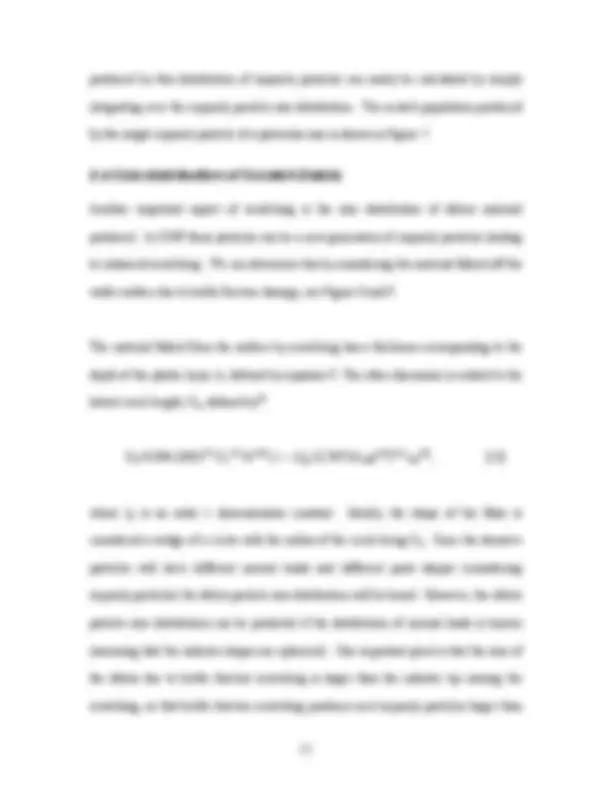
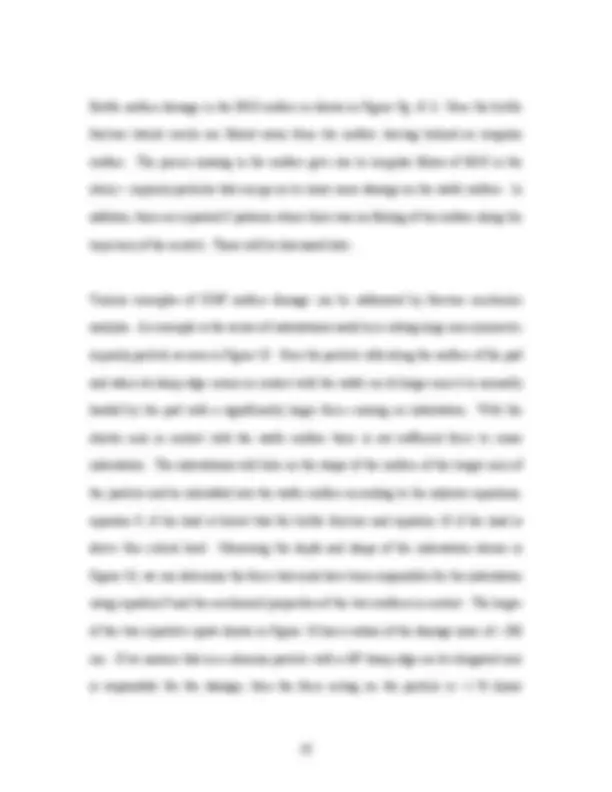
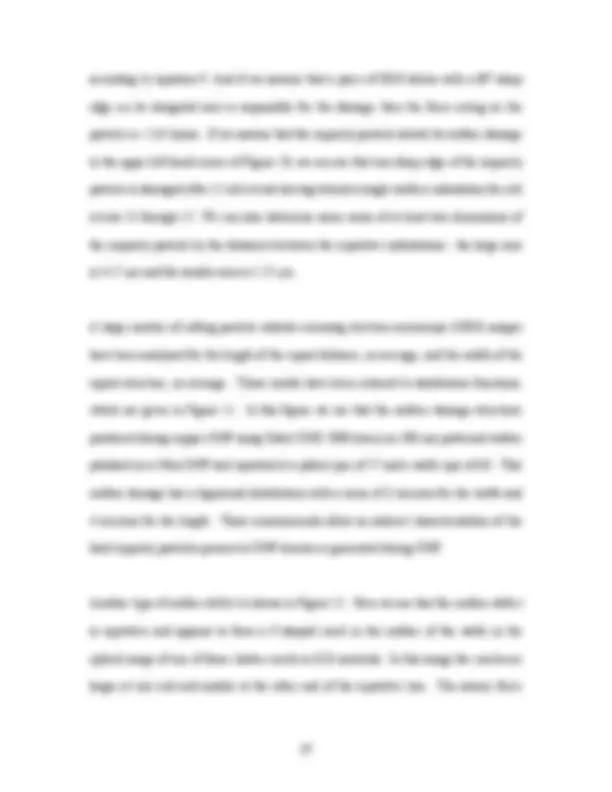
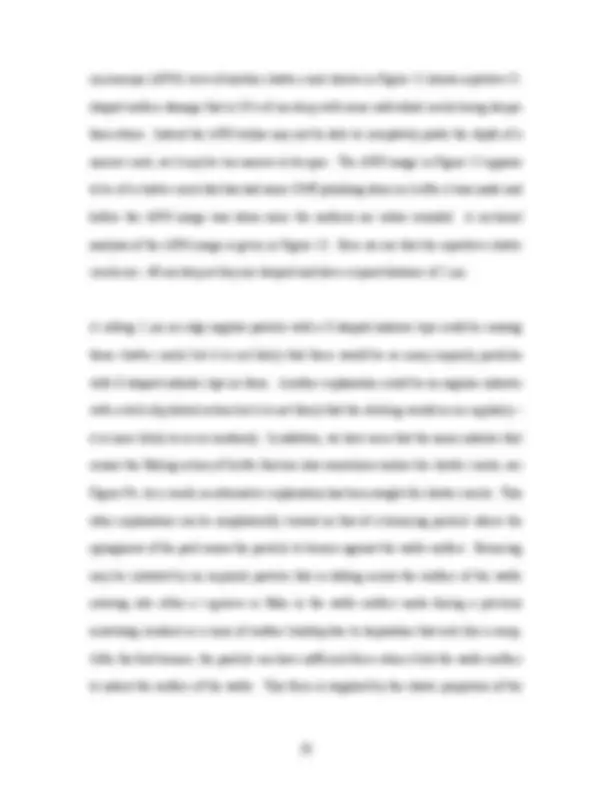


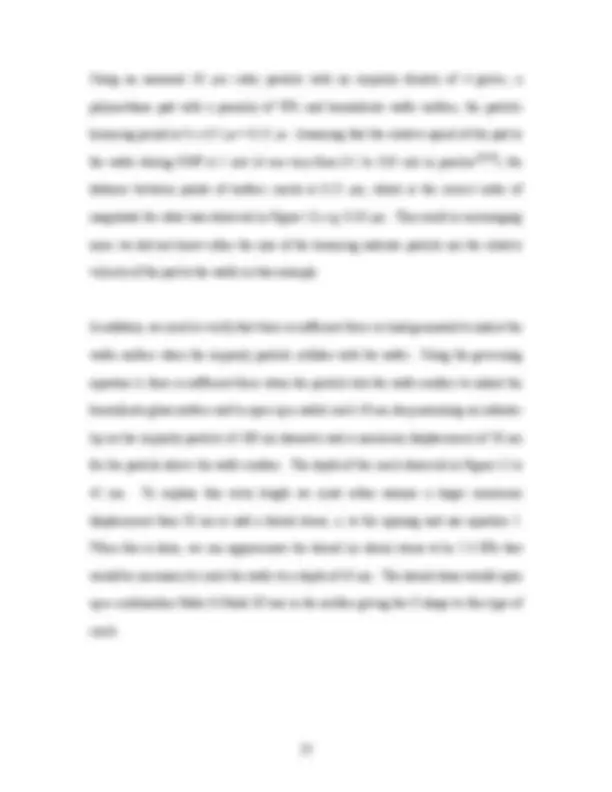
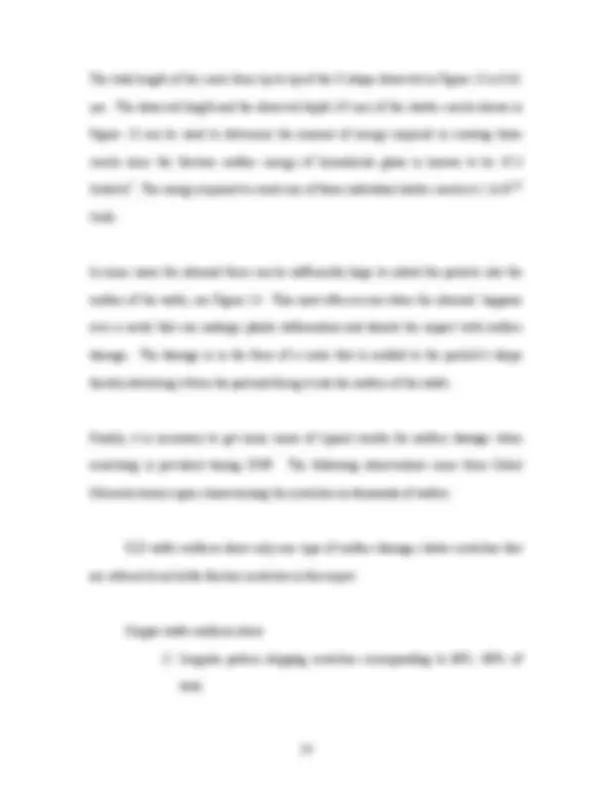
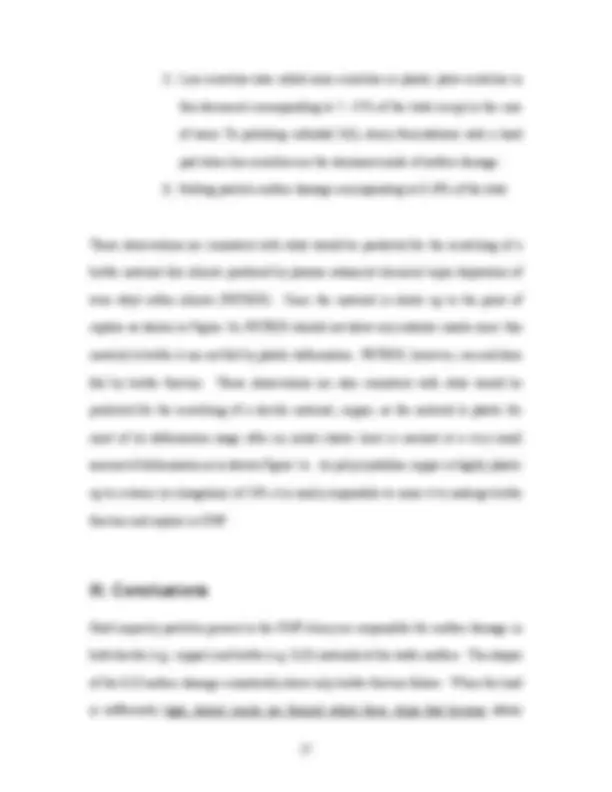
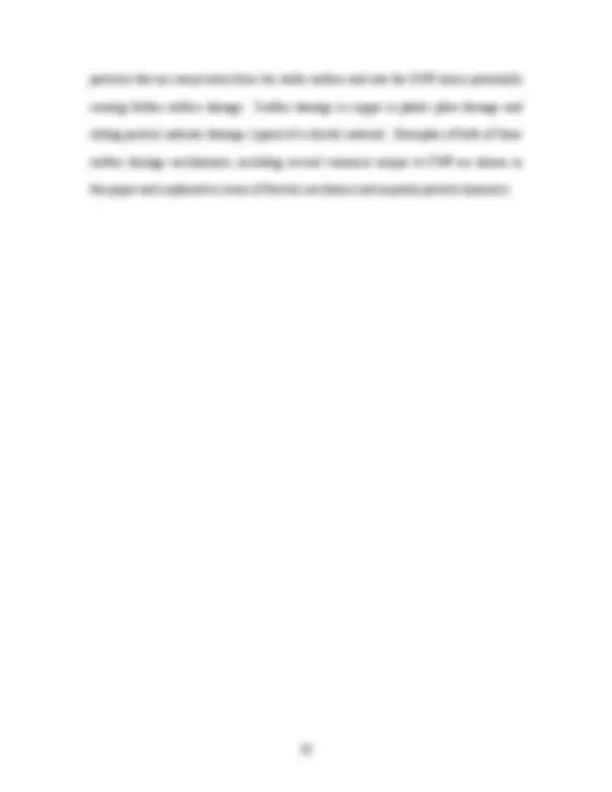
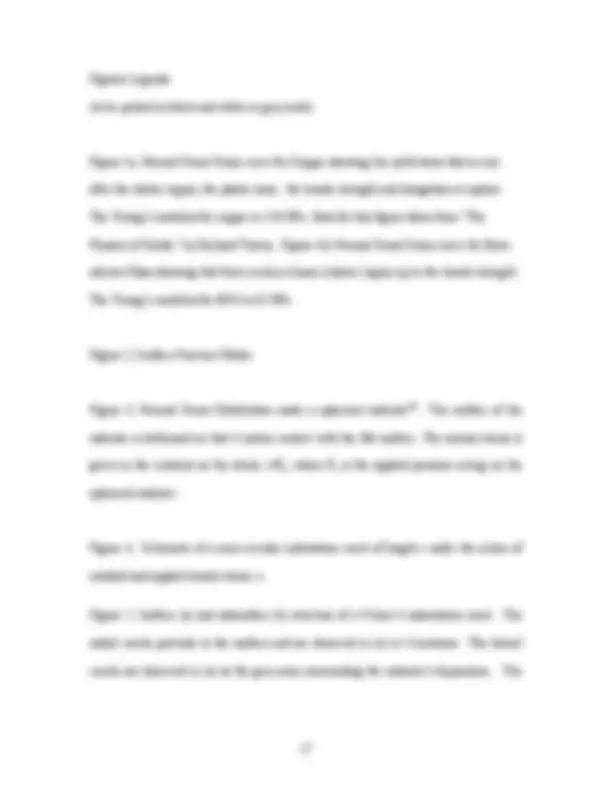
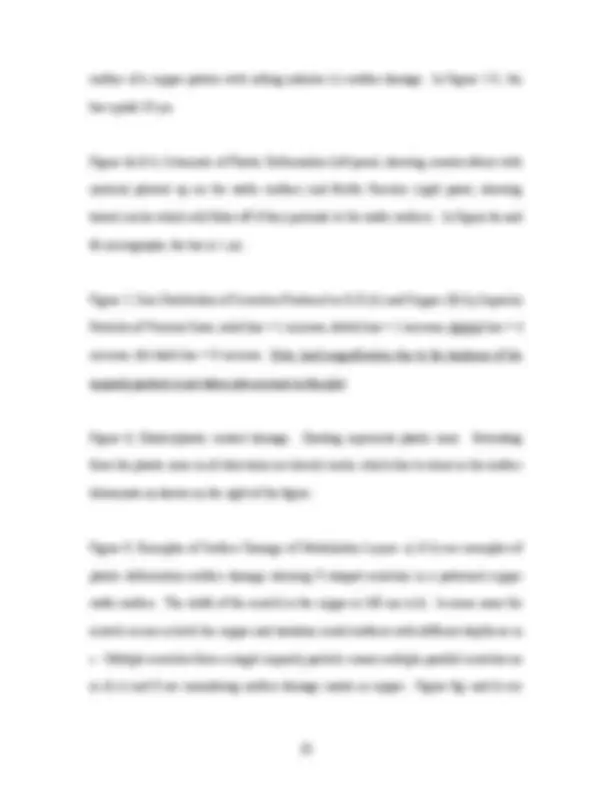
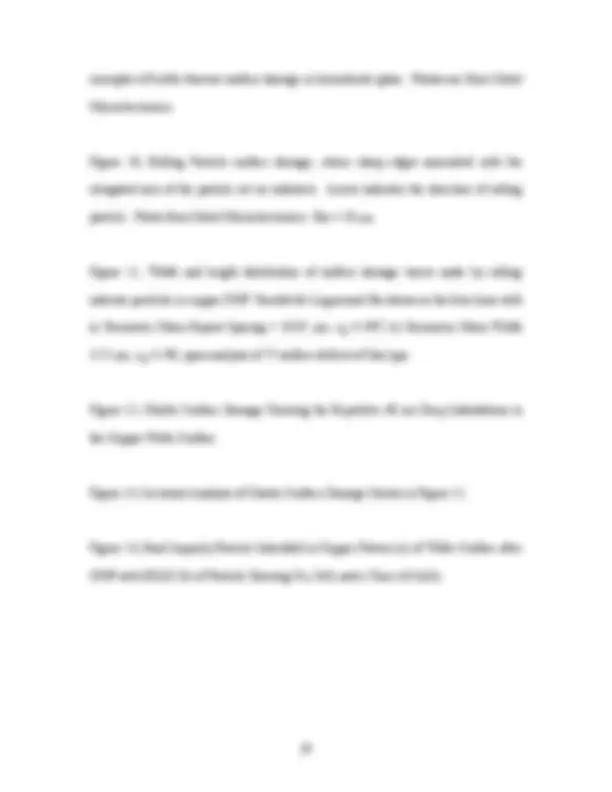
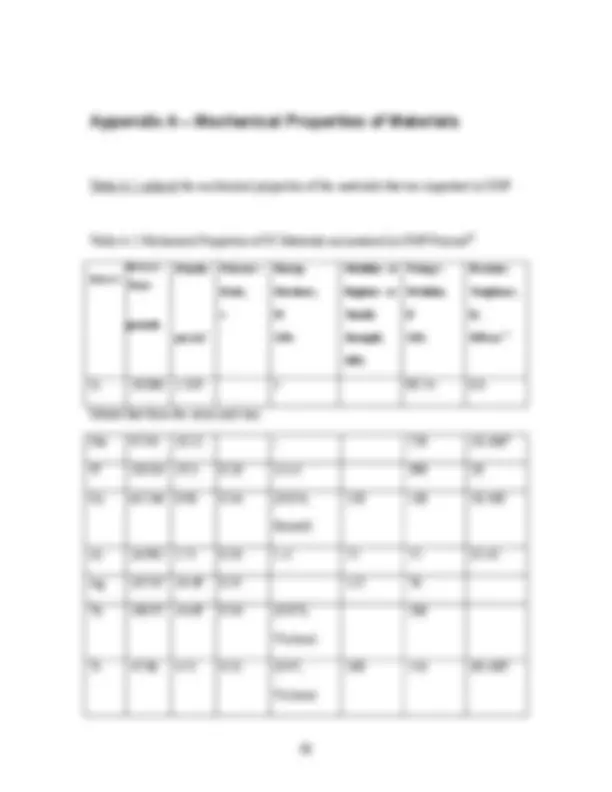
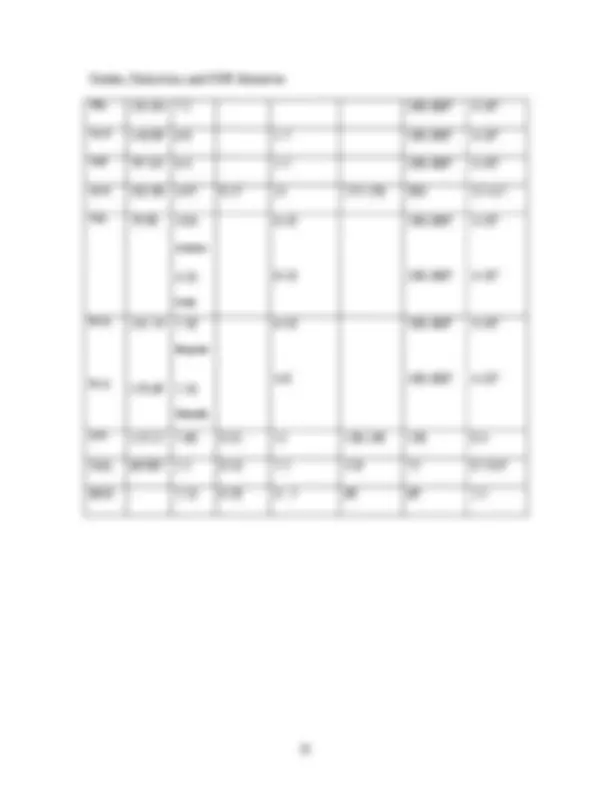
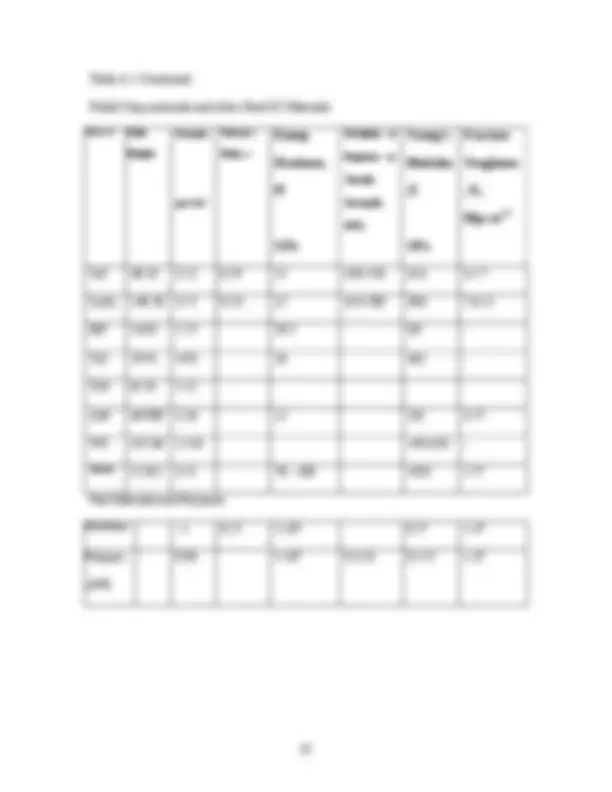
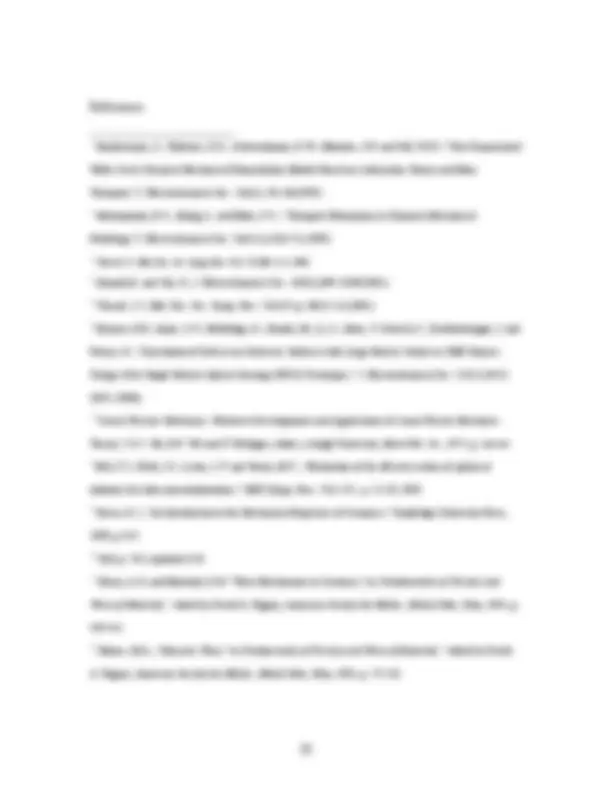
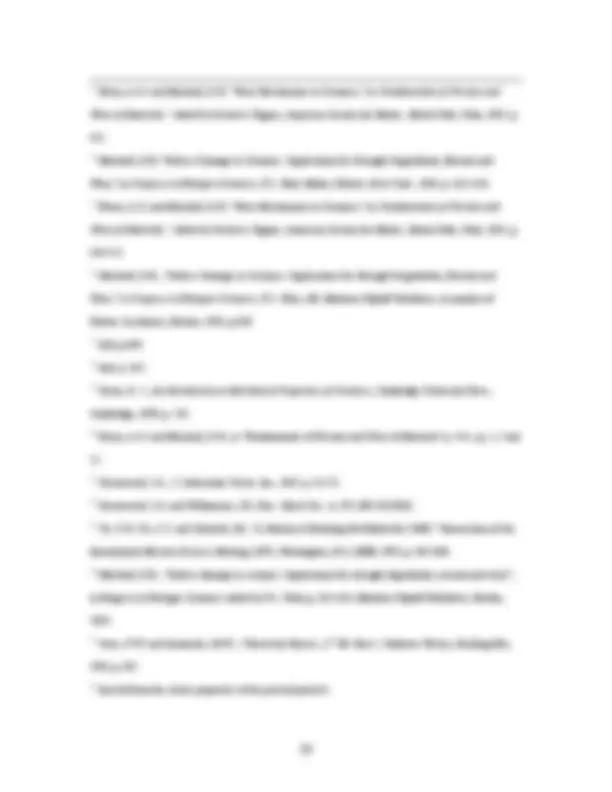
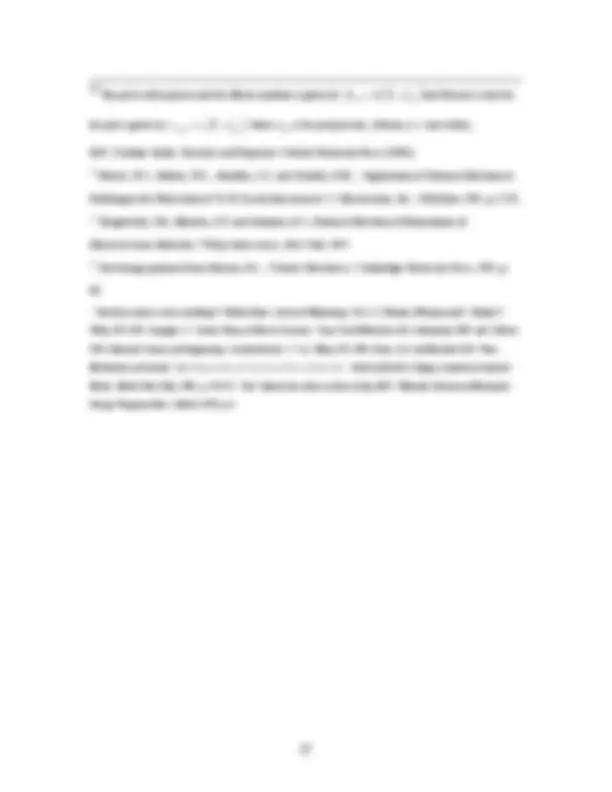
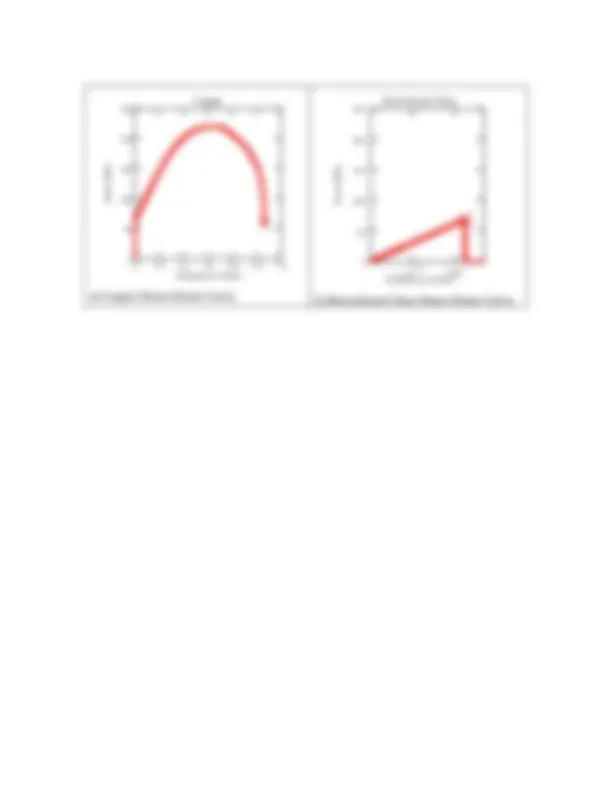
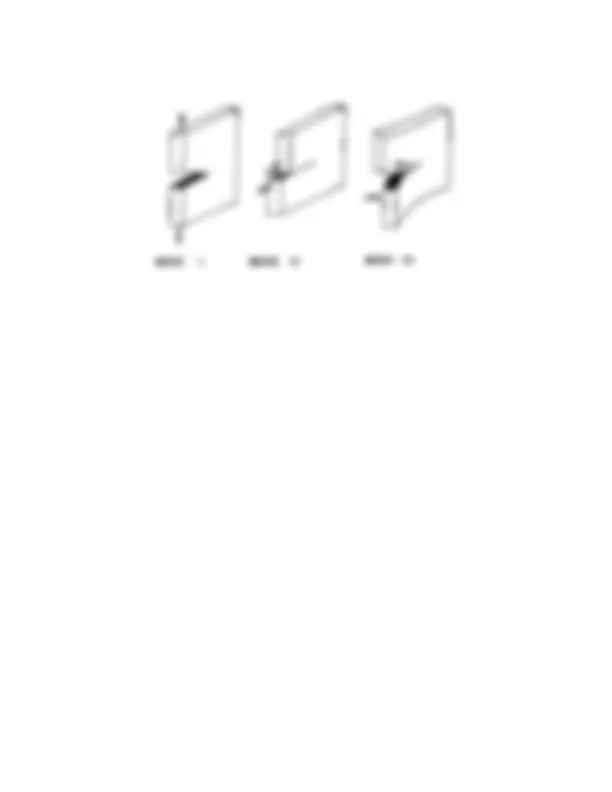
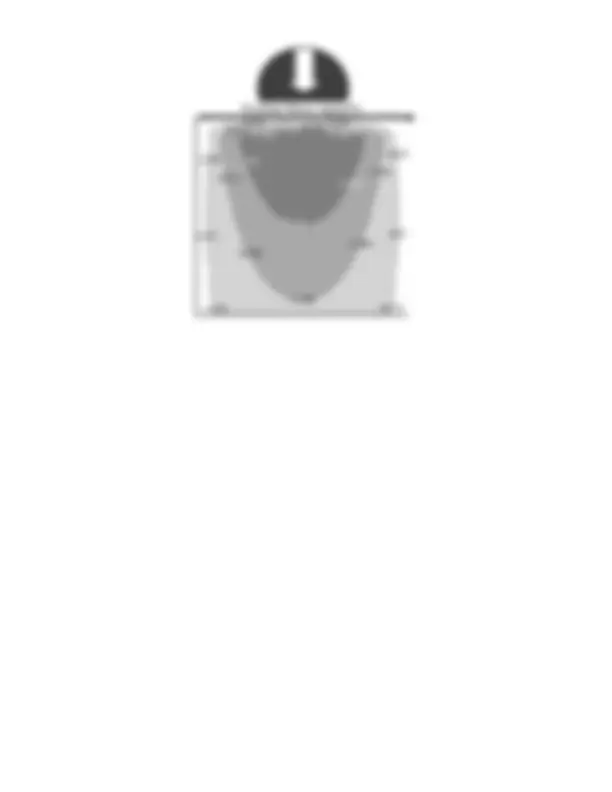
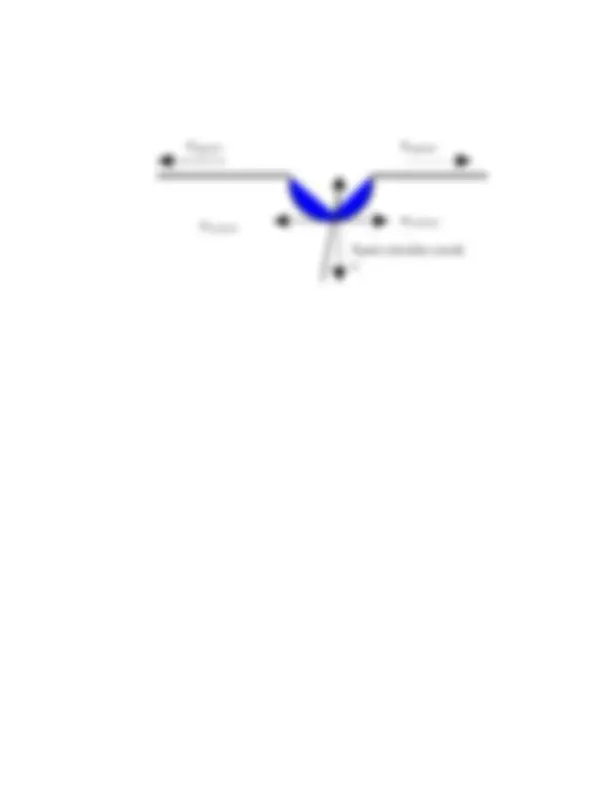
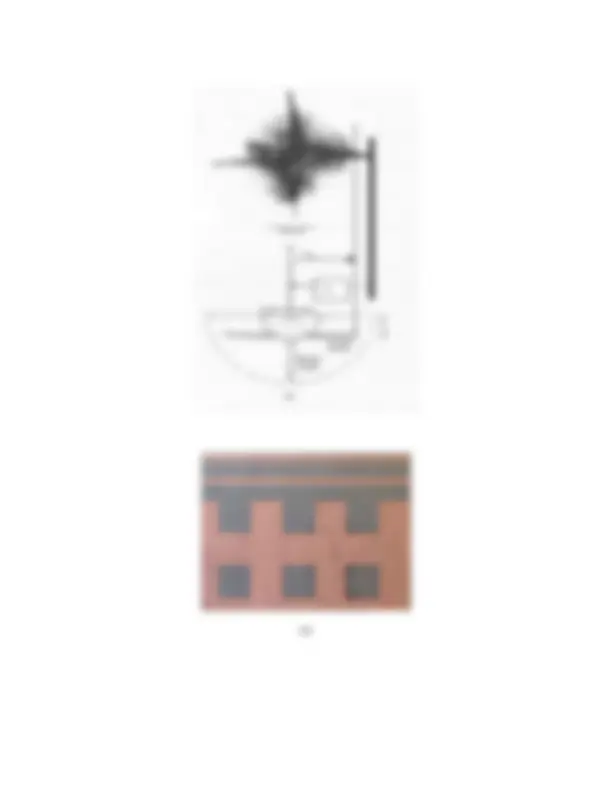
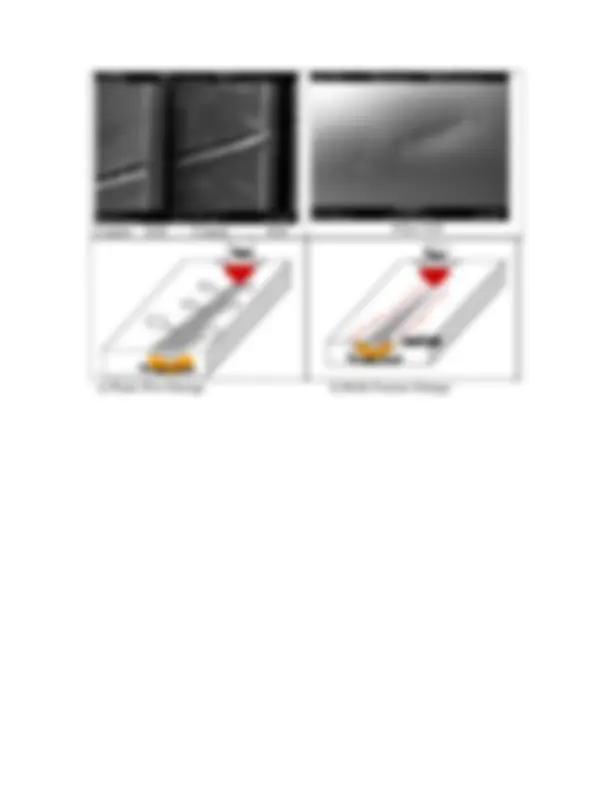
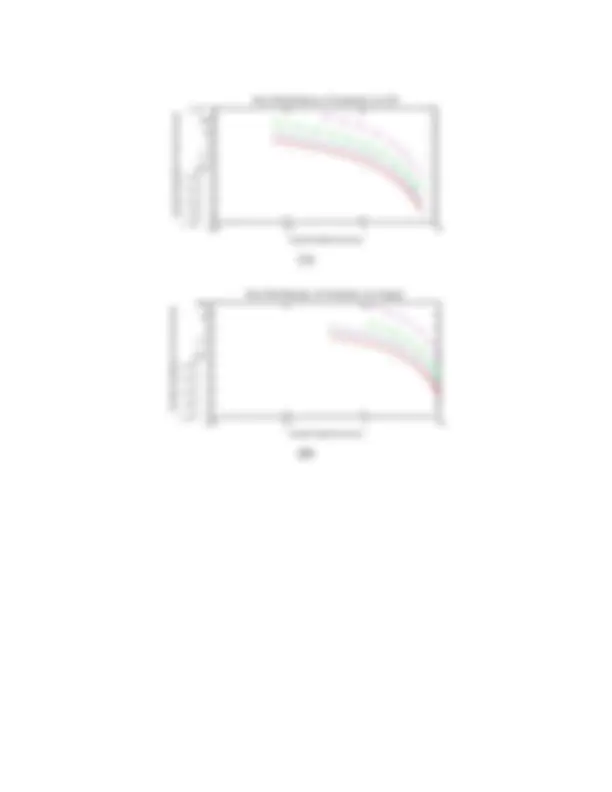
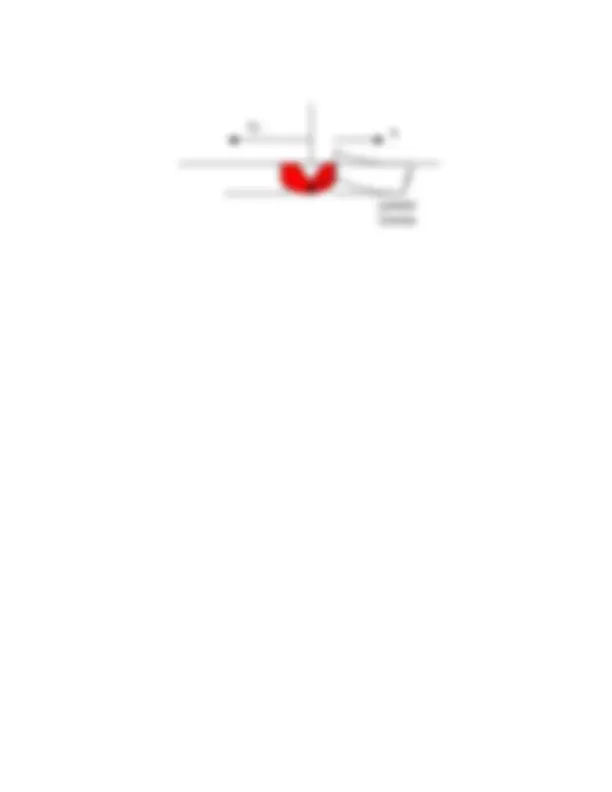
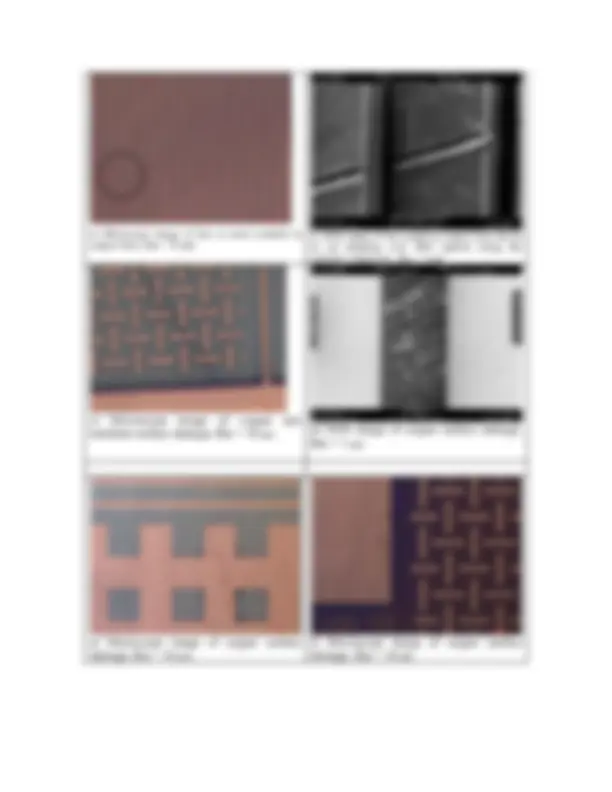
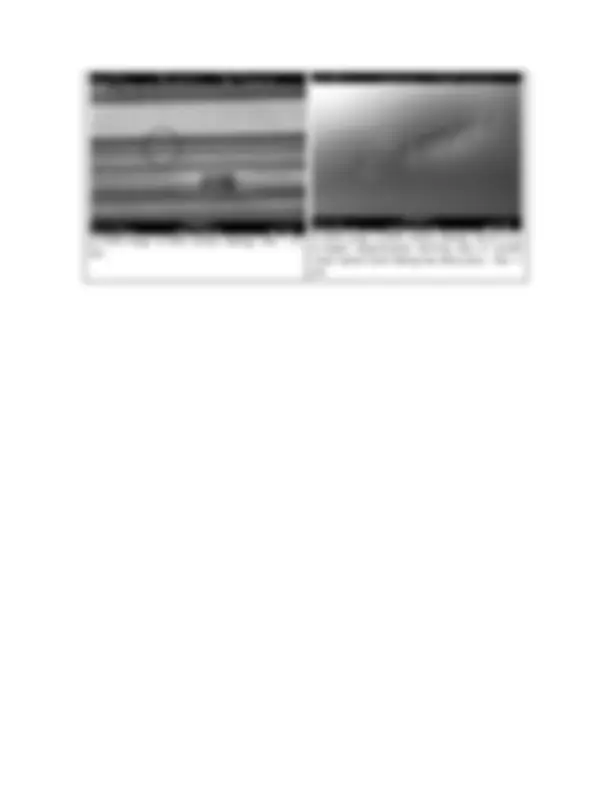
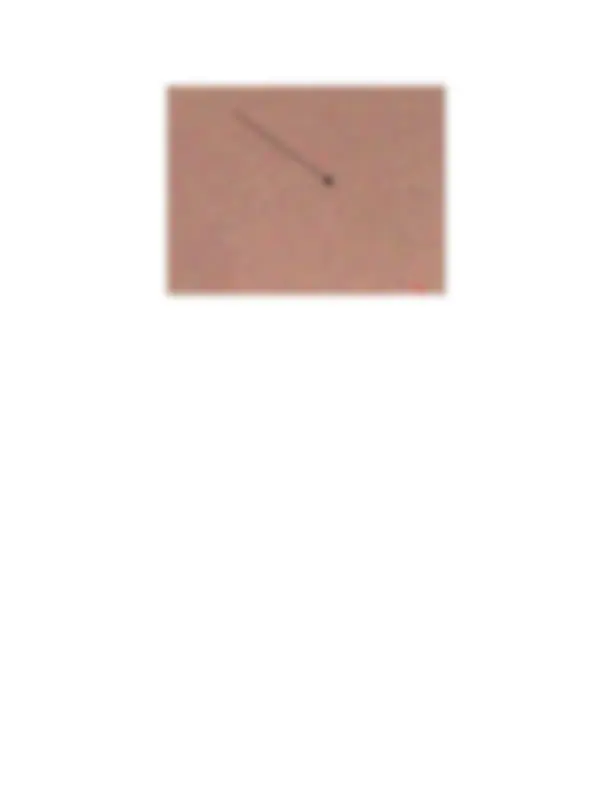
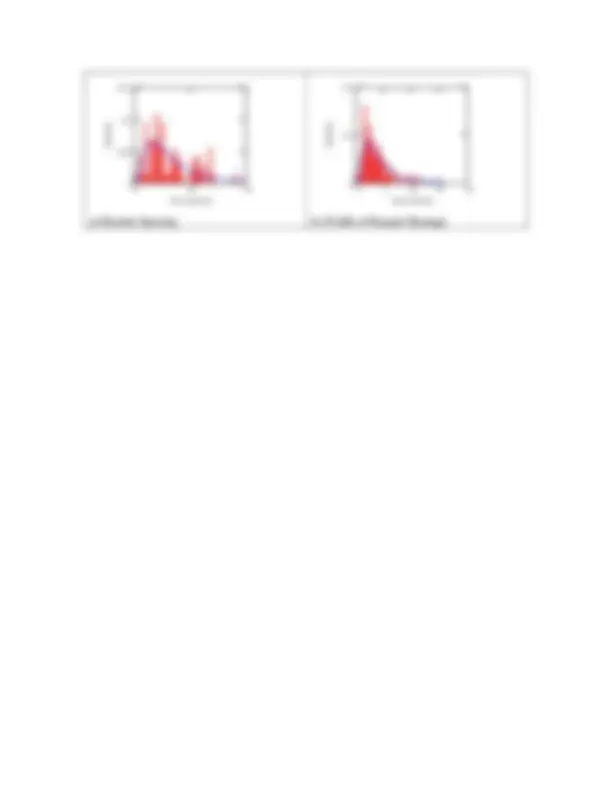
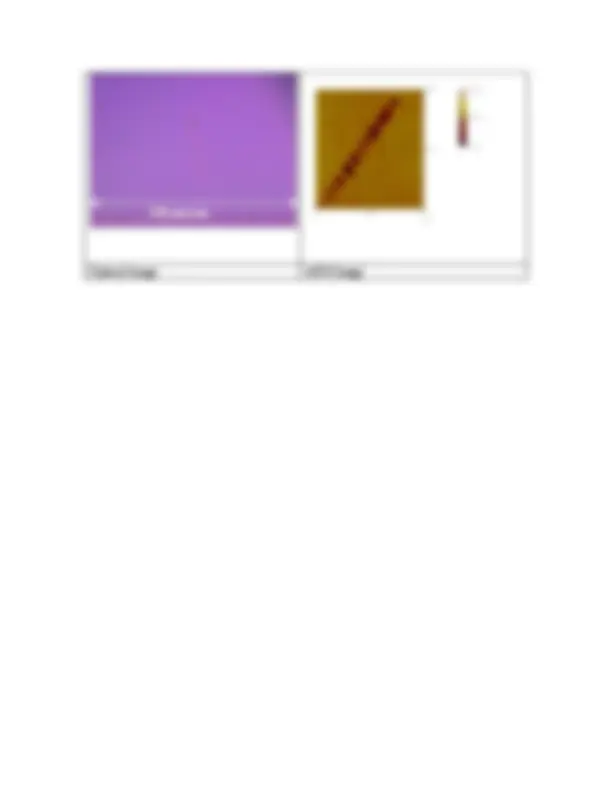
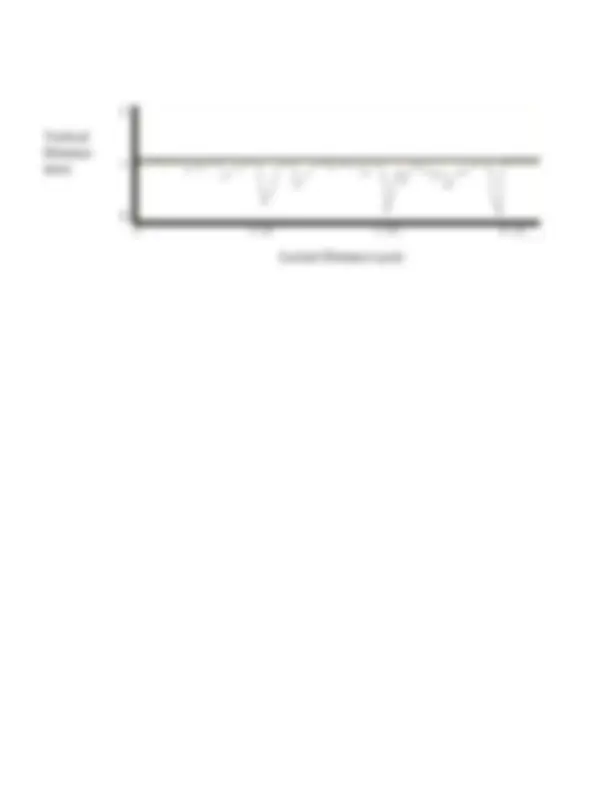
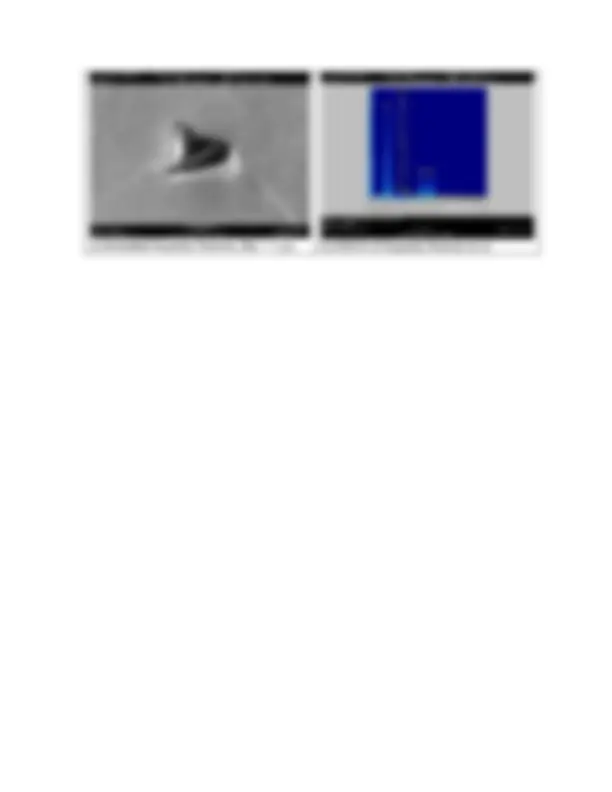
Study with the several resources on Docsity
Earn points by helping other students or get them with a premium plan
Prepare for your exams
Study with the several resources on Docsity
Earn points to download
Earn points by helping other students or get them with a premium plan
Community
Ask the community for help and clear up your study doubts
Discover the best universities in your country according to Docsity users
Free resources
Download our free guides on studying techniques, anxiety management strategies, and thesis advice from Docsity tutors
An in-depth analysis of the mechanical properties and fracture mechanics of materials used in the manufacture of multilayer interconnects on silicon chips, focusing on surface damage caused during CMP. It discusses chatter marks, surface flaking in interlayer dielectric material, and rolling indenter and plastic plow lines in copper on the wafer surface. The document also explains the importance of reducing surface damage to reach six sigma levels in chip manufacturing.
What you will learn
Typology: Study notes
1 / 50
This page cannot be seen from the preview
Don't miss anything!
Terry A. Ring₤, Paul Feeney, David Boldridge, Jaishankar Kasthurirangan, Shoutian Li, and James A. Dirksen
Cabot Microelectronics Corporation 870 Commons Drive Aurora, IL 60504
and
₤Chemical Engineering Department
University of Utah 50 S. Central Campus Drive, MEB Salt Lake City, UT 84112
This work reviews the mechanical properties and fracture mechanics of materials important in the manufacture of multilayer interconnects on silicon chips in order to understand surface damage caused during chemical mechanical polishing (CMP). It
gives an explanation for chatter marks, surface flaking in interlayer dielectric material (ILD) and rolling indenter and plastic plow lines in copper on the wafer surface during CMP of silicon chips.
Chemical mechanical planarization is also called chemical mechanical polishing (CMP). These terms evoke the combination of chemical and mechanical aspects in the polishing and planarization of silicon chips. There have been several papers over the years that discuss the chemical dissolution^1 ,^2 of surfaces being polished and there has been less work on the mechanical wear^3 ,^4 ,^5 of a surface being polished until more recently. There have not been many papers that discuss the mechanical aspects of scratching and surface damage in CMP.
CMP is used multiple times during the production of today’s silicon chips as there are multiple layers of wiring required to connect the more than one billion transistors per square centimeter in a modern silicon chip to the outside world. CMP uses a suspension of abrasive particles as the contacting medium between a polymeric pad and the wafer surface. In addition to material selective removal at the wafer surface, CMP is used to produce flat wafer surfaces that allow small features to be in focus during photolithography. CMP slurries, if not very carefully produced to eliminate impurity particles, have the propensity to cause surface damage to the wafer. Surface damage can be trivial or it can be catastrophic as when a wire line or dielectric layer is cut by a scratch. Surface damage during CMP is a major concern of chip manufacturers. The
metallization example, must be lowered to 1 in 10^7 , an effectively unattainable flaw probability with present CMP technology.
As we move to smaller line sizes and to more layers of wiring requiring more CMP steps, CMP surface defects will need to be lowered significantly in their depth, area of damage and number per cm^2 so that they do not destroy the ever smaller components, wires and insulting layers. This paper is devoted to understanding of surface defects and the fracture mechanics that causes them. The onset of surface damage is accompanied by the observation of increased concentration of large particles^6. These large particles can be impurities of slurry production, dried crusts that fall into the slurry during production and use or produced during CMP as wear debris.
In CMP processes, surface damage can take place because CMP uses a slurry of abrasive particles. At the wafer surface there are areas of metal (copper) and areas of dielectric insulating materials, (borosilicate glass, silicate glass produced by chemical vapor deposition, Low-K, a carbon loaded silicate; and barrier layer materials, e.g. various nitrides and silicides). There are two general types of materials based upon their mechanical properties - ductile materials and brittle materials. Metals are the classic examples of ductile materials where they can be deformed without failure. Glasses are the classic examples of brittle materials - they shatter. These properties are contrasted in
the stress strain curves shown in Figure 1a & b. In Figure 1a, we see the stress strain curve for an annealed sample of polycrystalline copper. At elongations, ε, less than 0.0008 corresponding to the linear portion at the y-axis, there is a linear (elastic) region with a slope given by Young’s modulus for the material. Above the linear region there is a plastic zone where the slope of the curve decreases with increasing elongation up to the tensile strength. At elongations above the tensile strength there is a decrease in the stress to the point of rupture at an elongation of 53%, an enormous amount of stretching before failure. In Figure 1b we see the stress strain for borosilicate glass. There is a linear (elastic) region up to an elongation of only 0.0012, the point of rupture. Thus we can see from these two figures the differences between ductile and brittle materials that are the two major components of the metallization layers of today’s chips.
Fracture Mechanics There are three surface fracture modes shown in Figure 2. In Irwin’s notation^7 , mode I denotes a symmetric opening, the relative displacement between the corresponding sides of the opening being normal to the fracture surface, while modes II and III denote anti- symmetric separation through relative tangential displacements, normal and parallel to the crack front, respectively.
The focus of fracture mechanics is on the tip of the crack identified by the end of the fracture lines in Figure 2 – any fracture mode. Much effort is expended to identify the stress intensity at the tip of the crack and a parameter traditionally calculated is the stress intensity factor, KI, KII or KIII, where the subscript refers to the mode of loading. In the
The normal load, LN, needed to cause plastic deformation (without cracking) is a measure of the materials hardness, H. The hardness has several definitions depending upon the shape of the indenter. If the indenter is a sphere HB =LN/(πd*δ) where d is the diameter of the indentation and δ is its depth for Brinnell hardness and HM= LN/(πdM^2 ) for Meyer Hardness where dM is the diameter of the dent. If the indenter is a square pyramid, the Vicker’s Hardness is HV= 1.8454 LN /a 2 , where a is the corner-to-corner diagonal distance of the square mark in the surface, see Figure 5a. If the indenter is an elongated pyramid, the Knoop Hardness is HK=14.2 L (^) N/D^2 where D is the maximum dimension of the indenter mark in the surface.
With even larger forces applied to the indenter, the surface fractures forms a semi- circular or radial cracks into the surface directly under the point of the indenter, see Figure 4 and 5. The radial cracks, of size c (also CR in Figure 4), has a half-circle shape under the indenter protruding to a distance c away from the point of contact along the surface of the material in opposite directions.
A crack at the surface intensifies any stress, σ, placed upon the sample. The stress intensity factor, KI, for a small surface flaw of size c is given by:
K (^) I = Y σ c [2]
where Y [=1.12 √π] is a purely geometric constant. After indentation with very high load, LN, resulting in cracking, the stress intensity factor associated with the residual stress field can be written as^9
K (^) I = χ c 3 L / 2 N [3]
where LN is the normal load, c is the crack size and χ [= β(E/H) 1/2^ ] is a constant associated with the material’s properties, the elastic modulus E of the material, the hardness, H, of the material given in Appendix A and the indenter shape characterized by β[~0.016]. The final size of the crack, co , loaded to its critical point, Lc, is determined by the fracture toughness, KIc, of the material, a material property also given in Appendix A.
KIc = (^) c^ χ o 3 L / c 2 [4]
When there is an additional stress, σ, applied with mode I loading, there will be two contributions to the total stress intensity factor, given by^10 :
3 / 2 Y c^1 /^2 c K (^) I = χ^ LN + σ. [5]
The crack of size, c, will enlarge when KI>KIc.
where H is the hardness of the surface being damaged and KIc is its fracture toughness. The plastic and brittle fracture wear rates are discussed in the next two paragraphs.
Plastic deformation The differential volume, dV, of material removed per unit length, dx, of the scratch depends upon the load of the abrasive point normal to the surface, LN, and the mechanical properties of the materials comprising the surface^12 ,^13 :
dV/dx ∼ (LN /H) [7]
where H is the hardness of the surface being damaged. This equation assumes that the abrasive point is harder than the material comprising the surface. The volume removed is plowed into a furrow onto the material’s surface, see Figure 6a.
Brittle fracture The differential volume, dV, of material removed per unit length, dx, of the scratch depends upon the load of the abrasive point normal to the surface, LN, and the mechanical properties of the materials comprising the surface^14 :
dV/dx ∼ (E/H) 4/5^ K1c-1/2^ H-5/8^ LN9/8^ [8]
where E is Young’s modulus of elasticity, H is the hardness, K1c [=2 E γf ] is the fracture toughness and γf is the surface energy for fracture. All of these material properties are for the surface being damaged as this equation assumes that the abrasive point is harder than the material comprising the surface. The volume removed in this case consists of the surface furrow as well as large pieces of the surface material being dislodged from the surface out to the point where the lateral cracks reach the surface, see Figure 6b. The above equations are consistent with experimental measurements for scratching wear and particle erosion within the limits of experimental accuracy^15 and can be used to determine
To determine the depth distribution of the scratches due to both abrasive and impurity particles, we consider each of these scratching particles to be attached to the tip of an asperity or if larger than an asperity to be pressed into the pad. Since we have a distribution of particle sizes for both the abrasive particles and the impurity particles and we have a distribution of forces caused by the height distribution of asperities on which the particles will reside, this gives a complicated scratch depth distribution. If in addition, the impurity particles are not spherical but angular, we will also have an additional distribution to consider – the distribution of radii of curvature for the point of
There is a transition between plastic and brittle fracture scratching that takes place as the load is increased. The critical load at which this transition takes place is given by 20 equation 6. Therefore, when the load on an impurity particle is less than LNc, plastic deformation will take place. When the load is on an impurity particle is greater than, LNc, brittle fracture will take place. Brittle fracture is by far the most destructive to the wafer surface as the lateral and radial cracks penetrate more deeply than the plastic deformation damage.
The impurity particle is forced by one (or more) of the pad asperities to be in contact with the wafer surface. There is a distribution of pad asperities onto which the impurity particles can be attached and still be in contact with the wafer. Depending upon the length of the pad asperity that the impurity particle is attached to and the size of the impurity particle, the load, L, acting on the impurity particle/wafer contact point can be determined. Greenwood and Williamson 21 ,^22 have used exponential distribution functions to describe the rough surfaces. The contact area, Acon , and load, L, over the wafer, is obtained by integration of the asperity height from the distance between the wafer and the plane of reference in the pad, δ to infinity given below. An asperity will contact the wafer if its length, z, is greater than δ.
In the above equations, Awafer is the surface area of the wafer assuming a flat surface, g(x) is the distribution function for the asperity height, z, or the radius of curvature of the asperity, β, and E’ is the effective Young’s modulus defined below. The applied pressure is L (^) N/Awafer and the average contact pressure is LN/Acon.
Equations 11 and 12 can be used to predict the size distribution of surface damage produced during CMP. In this analysis, the Greenwood, et. al. exponential distribution of pad asperities was characterized by the mean and standard deviation of the length of the asperities, and an area density of asperities with all asperities assumed to have the same radius of curvature at their tips. The pad asperity parameters used in this analysis were those measured by Yu, et.al^23 for a conditioned pad. The asperities press the impurity particles into the wafer surface creating a normal load that allows the depth of the surface damage to be predicted using equations 10 for a brittle material like the interlayer dielectric (ILD) and equation 6 for a ductile material like copper. Putting this all together, we find that the size distribution of scratches produced by the impurity particles is given in Figure 7. Here we see that the deepest scratches are formed by the largest impurity particles and the population of scratches decreases as the scratch depth increases for a given size of impurity particles. Brittle material does not have a plastic zone where plastic deformation scratching can take place so the ILD curves are only for brittle fracture surface damage. Since copper is a malleable material it deforms plastically so these copper curves are only for plastic deformation surface damage. Combining the analysis shown in Figure 7 with knowledge of the number and size distribution of impurity particles in a log-normal size distribution of particles, then the scratches
the original indenter that are likely to go on to make even large scratches quickly propelling the number and size of surface defects to high levels.
The surface of the wafer during the fabrication of any of the multiplayer interconnection layers has areas of metal and areas of dielectric exposed to the CMP slurry. The thickness of the layer and the width of a region of metal or dielectric are on the order of 100 nm in size with modern chips. Surface damage during CMP can cut through the thickness or the width of these features and cause the components that they represent to fail. For this reason, understanding and controlling surface damage during CMP is important.
V-shaped plastic deformation scratches in copper have been observed on wafer surfaces in cases with high levels of scratching, see Figure 9a, b and c. The size of the V is on the order of 100’s of nanometers in width. Since this is larger than the size of the abrasive particles, it is assumed that this is due to an impurity particle being normally loaded and dragged along the wafer surface. Furthermore as the impurity particle is dragged across the surface the depth of the V is different when the surface changes from tantalum to copper and vice versa. A plastic deformation scratch will form in a material when the stress imposed by the indenter is greater than the hardness of the material. In the case of copper this is 0.874 GPa and in the case for tantalum this is 0.873 GPa using data from
Appendix A. Noting that the ILD in Figure 9a & b is borosilicate glass (BSG), we know that the applied stress that caused the scratch in the copper layer but not in the BSG layer is > 0.874 GPa, (the hardness of copper and < 5 GPa the hardness of BSG).
If a single impurity particle is large, hard and has multiple points of contact with the wafer surface it can be loaded with sufficient force by many pad asperities to cause multiple indenter points to be dragged across the surface simultaneously giving multiple parallel scratches as shown in Figure 9d. Each of the indenter points can be treated with the scratching equations presented in Section II.3, however, to apply these equations we would need to know how the load developed by the pad is distributed over the back of the impurity particle and the specific geometry of the hard points of contact with the wafer surface. This load redistribution will be specific to each of these very large impurity particles. This makes a simple analysis of the resulting scratching difficult. Another possible explanation of the multiple parallel scratches shown in Figure 9d are that a series of pores, similar size, has been produced in the deposited metal layer possibly associated with previous scratches at the underlying layer surface. During CMP these pores are uncovered leaving them open after a certain amount of removal.
Other types of copper plastic surface damage are shown in Figure 9e & f where a random pattern of an irregular particle rolling across the copper surface is shown. In Figure 9e, the particle makes indentations as the particle rolls but the tips are broken during rolling altering the shape of the indentation marks as it rolls along. Figure 9f, shows an example of a plowing-rolling action of an impurity particle on a copper surface.
according to equation 9. And if we assume that a piece of BSG debris with a 60º sharp edge on its elongated axis is responsible for the damage, then the force acting on the particle is ~2.65 dynes. If we assume that the impurity particle started its surface damage in the upper left hand corner of Figure 10, we can see that one sharp edge of the impurity particle is damaged after 12 roll events leaving behind a single surface indentation for roll events 13 through 15. We can also determine some sense of at least two dimensions of the impurity particle by the distances between the repetitive indentations - the large axis is 4.17 μm and the smaller axis is 1.25 μm.
A large number of rolling particle indenter scanning electron microscope (SEM) images have been analyzed for the length of the repeat distance, on average, and the width of the repeat structure, on average. These results have been reduced to distribution functions, which are given in Figure 11. In this figure we see that the surface damage structures produced during copper CMP using Cabot CMC 5000 slurry on 200 mm patterned wafers polished on a Mira CMP tool operated at a platen rpm of 57 and a wafer rpm of 63. This surface damage has a lognormal distribution with a mean of 3 microns for the width and 4 microns for the length. These measurements allow an indirect characterization of the hard impurity particles present in CMP slurries or generated during CMP.
Another type of surface defect is shown in Figure 12. Here we see that the surface defect is repetitive and appears to form a C-shaped crack in the surface of the wafer in the optical image of one of these chatter cracks in ILD materials. In this image the cracks are larger at one end and smaller at the other end of the repetitive line. The atomic force
microscope (AFM) view of another chatter crack shown in Figure 12 shows repetitive C- shaped surface damage that is 10’s of nm deep with some individual cracks being deeper than others. Indeed the AFM stylus may not be able to completely probe the depth of a narrow crack, as it may be too narrow at its apex. The AFM image in Figure 12 appears to be of a chatter crack that has had some CMP polishing done on it after it was made and before the AFM image was taken since the surfaces are rather rounded. A sectional analysis of the AFM image is given in Figure 13. Here we see that the repetitive chatter cracks are ~40 nm deep at they are deepest and have a repeat distance of 2 μm.
A rolling 2 μm on edge angular particle with a C-shaped indenter tips could be causing these chatter cracks but it is not likely that there would be so many impurity particles with C-shaped indenter tips on them. Another explanation could be an angular indenter with a stick slip lateral action but it is not likely that the sticking would occur regularly – it is more likely to occur randomly. In addition, we have seen that the same indenter that causes the flaking action of brittle fracture also sometimes makes the chatter cracks, see Figure 9h. As a result, an alternative explanation has been sought for chatter cracks. This other explanation can be simplistically viewed as that of a bouncing particle where the springiness of the pad causes the particle to bounce against the wafer surface. Bouncing may be initiated by an impurity particle that is sliding across the surface of the wafer entering into either a v-groove or flake in the wafer surface made during a previous scratching incident or a zone of surface buildup due to deposition that acts like a ramp. After the first bounce, the particle can have sufficient force when it hits the wafer surface to indent the surface of the wafer. This force is supplied by the elastic properties of the