
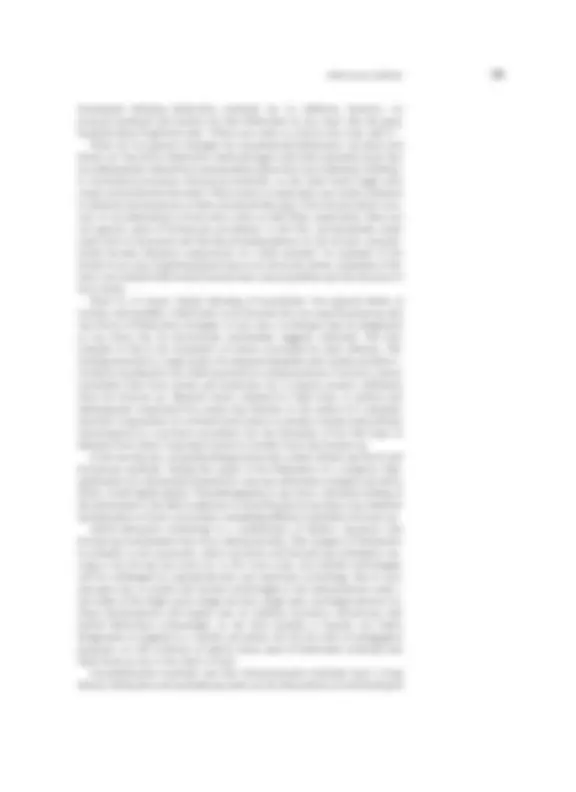
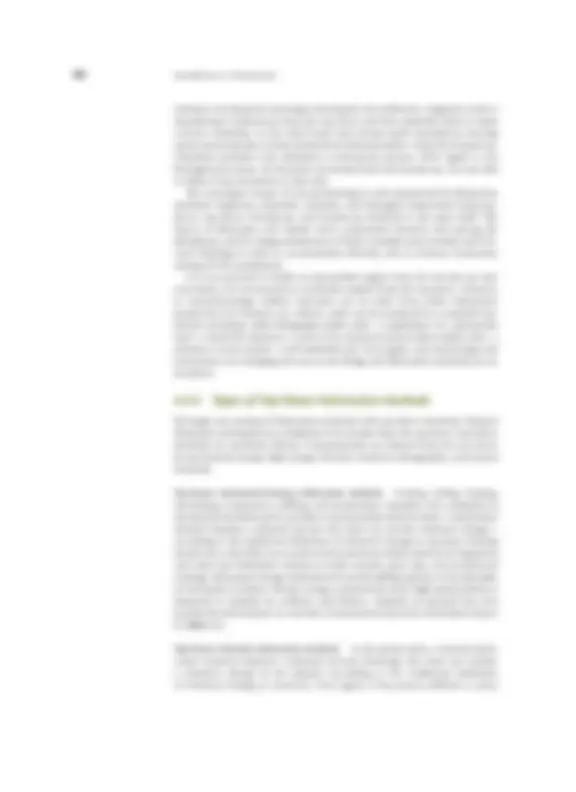
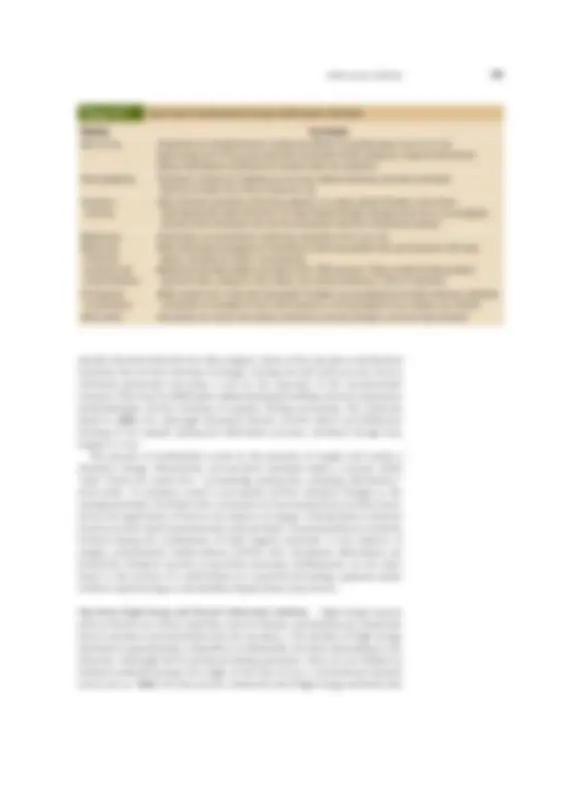
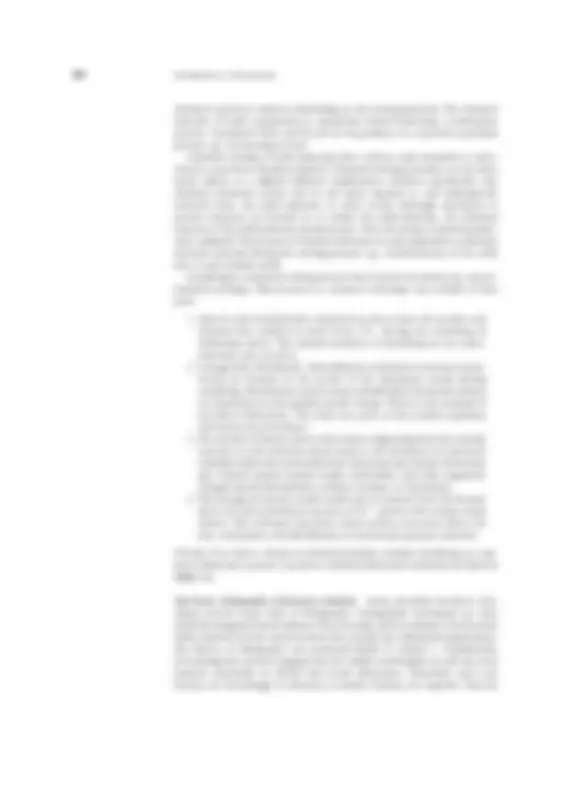
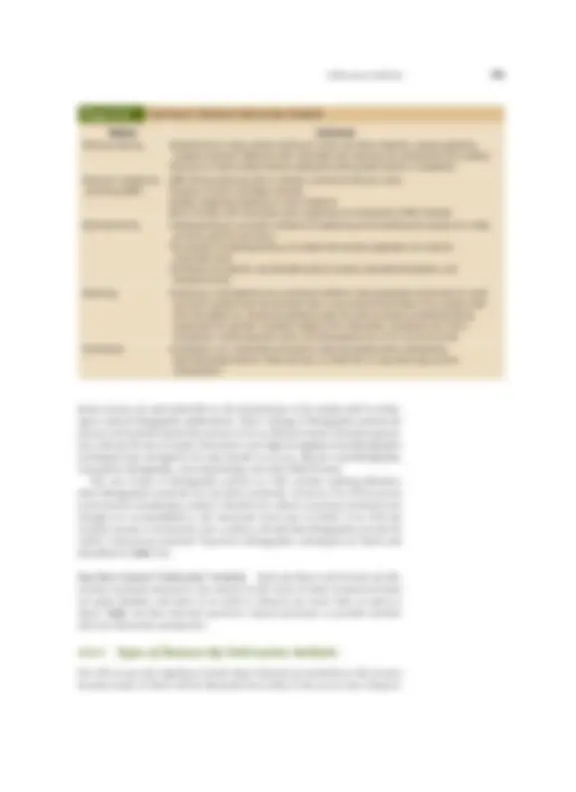
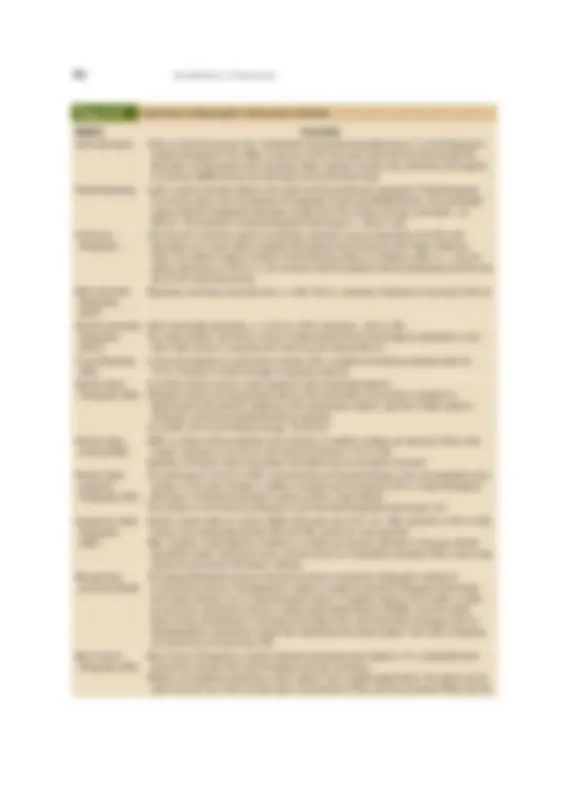
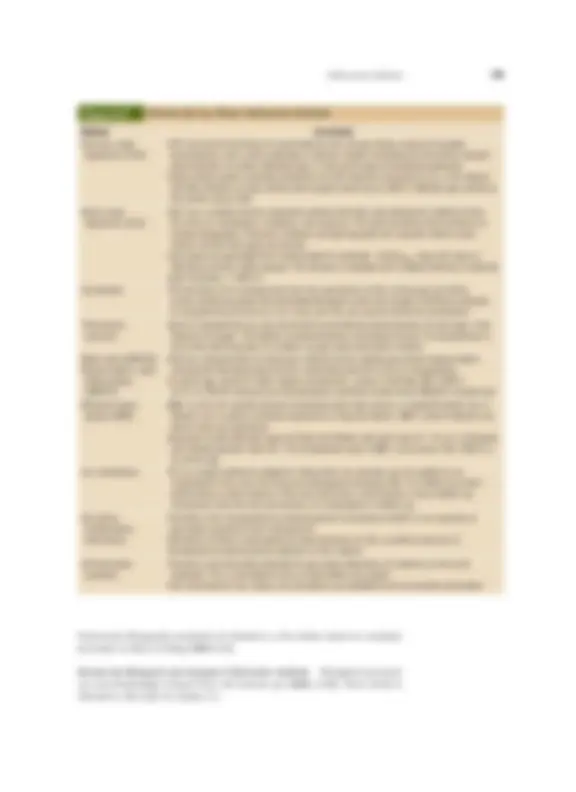
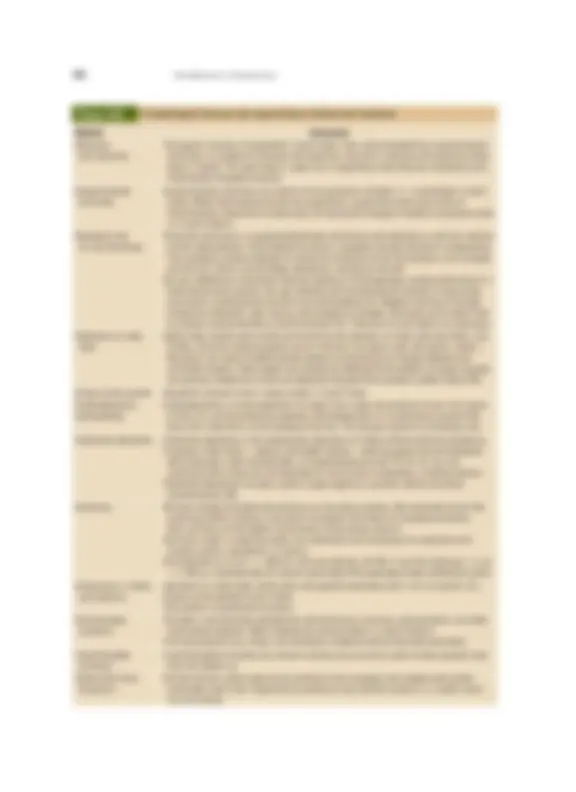
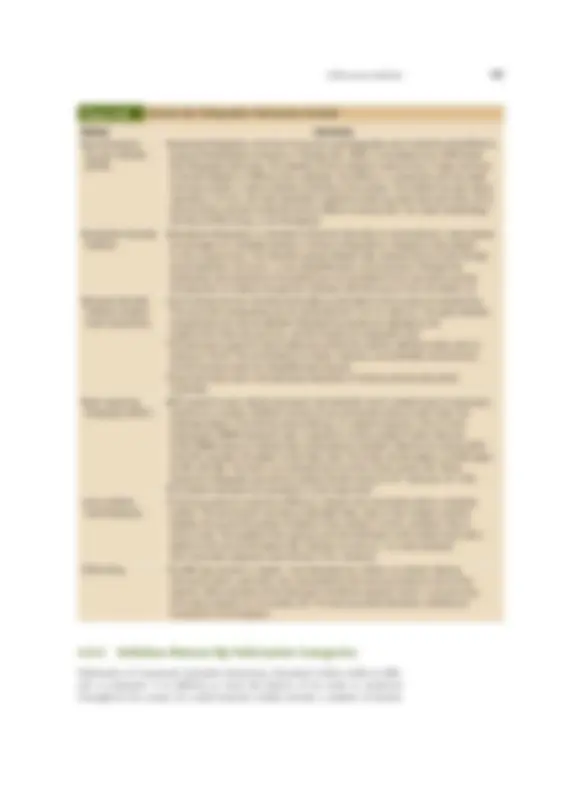
Study with the several resources on Docsity
Earn points by helping other students or get them with a premium plan
Prepare for your exams
Study with the several resources on Docsity
Earn points to download
Earn points by helping other students or get them with a premium plan
Community
Ask the community for help and clear up your study doubts
Discover the best universities in your country according to Docsity users
Free resources
Download our free guides on studying techniques, anxiety management strategies, and thesis advice from Docsity tutors
An overview of fabrication methods used in nanoscience, distinguishing between top-down and bottom-up approaches. Top-down methods employ physical processes to form nanomaterials from bulk materials, while bottom-up methods involve chemical reactions to build materials from the atomic or molecular level. various thermal and chemical fabrication methods, including annealing, electrohydrodynamic atomization, electrospinning, extrusion, and chemical etching.
What you will learn
Typology: Transcriptions
1 / 17
This page cannot be seen from the preview
Don't miss anything!
178 Introduction to Nanoscience
THREADS
Characterization methods have been presented, addressed, and discussed, albeit without providing significant detail. The catalog nature of chapter 3 is deliberately extended into this chapter, which is the last chapter in the “Nanotools” division of the text. Because reference is made continually to vari- ous kinds of fabrication techniques throughout the text, it is prudent to place introductory material concerning fabrication early in the book. In this way, the student should be able to establish a level of comfort with, perspective on, and understanding of fabrication methods when the subjects emerge
time and time again later in the text. The physics division of the text—chapter 5 through chapter 8— engages the study of nanomaterial properties and phenomena. Please take note that the fabrication methods listed in this chapter are but a few of the multi- tude that actually exist. We have tried to catego- rize in a generic sense the major forms and tried to illustrate the processes with commonly prac- ticed fabrication techniques. Much can be learned about nanomaterials by understanding how they are made.
4.0 FABRICATION OF NANOMATERIALS
4.0.1 Background
180 Introduction to Nanoscience
4.0.2 Types of Top-Down Fabrication Methods
Fabrication Methods 181
TABLE 4.1 Top-Down Mechanical-Energy Fabrication Methods
Method Comments Ball milling Production of nanoparticles by mechanical attrition to produce grain size <5 nm [3] High-energy ball milling uses steel balls to transfer kinetic energy by impact to the sample. Highly polydisperse products and contamination are problems. Rolling/beating Traditional mechanical methods to minimize material thickness and refi ne structure. Gold can be beat into a 50-nm thick fi lm [4]. Extrusion; drawing
High-pressure processes of forcing materials in a plastic phase through a die to form high-aspect ratio parts like wires. Bi metal forced through nanopore alumina is an analogous process at the nanoscale and can be considered a thermal–mechanical process. Mechanical Machining, polishing, grinding, and ultramicrotome
Also known as conventional machining; resolution limit: 5 μm [5] Other techniques analogous to mechanical machining perform the same function with laser beams, focused ion beams, and plasmas. Mechanical grinders/cutters are used to thin TEM samples. These include dimple grinders, diamond saws, ultrasonic disc cutters, and ultramicrotomes (<100 nm sections). Compaction; consolidation
Metal powder ball milled and compacted. Powders are considered to be bulk materials; therefore, compaction of powders to form bulk material is not considered to be a bottom-up method. Atomization Conversion of a liquid into aerosol particles by forcing through a nozzle at high pressure
Fabrication Methods 183
TABLE 4.3 Top-Down High-Energy and Particle Fabrication Methods
Method Comments Arc discharge High-intensity electrical arc discharge directed on a graphite target (anode) + catalyst to produce single-walled carbon nanotubes that accumulate on the cathode Temperature ~4000 K [15,16] Laser ablation High-intensity laser beam directed on a graphite target + catalyst to produce single-walled carbon nanotubes; sample warmed to 1200–1500°C by furnace, laser Sample is collected on water-cooled copper collector [17]. This process can be considered to be a thermal and a high-energy method. Solar energy vaporization
Solar energy focused on graphite target + catalyst to produce single-walled carbon nanotubes Temperature ~3000+K [18] RF sputtering Ion bombardment of metal, oxide, or other material targets to form thin fi lm coatings Usually performed under moderate vacuum (10–3^ torr). Atoms, molecules, and clusters are formed by this process. Ion milling Argon ion plasma is used to subtract material from a surface. The purpose is to clean surface or remove (thin) materials for TEM. No change in the chemical nature of the sample happens during this process. Electron beam evaporation
This is similar to evaporation in Table 4.2 but uses an electron beam source to heat material. Evaporated material condenses on target substrate. High vacuum is required. Thin-layer antirefl ection, scratch-resistant coatings are formed by this technique. Reactive ion etching
Sensitive materials are etched by reactive chemical species in charged plasma. Chemical change of the etched material takes place during this process. The etching process is guided by maskant materials. Pyrolysis Pyrolysis can also be considered a high-energy method. Application of high-energy source like fi re to bulk hydrocarbon materials (like a steak) in the absence of oxygen creates polyaromatic hydrocarbons (PAHs)—a top-down process (or if considering intermediates—for example, carbon atoms—it can be considered to be a bottom-up process). Pyrolysis of solid refractory nanoscale materials like Si–C–N substrate to form nanotubes at 1500–2200°C is a crossover technique [19]. Large-scale synthesis of multiwalled carbon nanotubes occurs in fl ame environments by burning carbon sources such as methane, ethylene, or benzene. Combustion Combustion can be considered to be a high-energy, thermal, or chemical fabrication method. High-energy sonication
Ultrasonication uses high-energy sound waves to make nanomaterials from bulk materials. The technique is also used to disperse carbon nanotubes in a suitable solvent. The dispersion of bundles of nanotubes into individual tubes is top down. Probe tips are made of titanium, vanadium, and other metals and alloys. Micron- to nanosized residual tip metal is introduced into solutions during the sonication process.
184 Introduction to Nanoscience
186 Introduction to Nanoscience
TABLE 4.5 Top-Down Lithographic Fabrication Methods
Method Comments LIGA techniques LIGA is a German acronym for “Lithographie Galvanoformung Abformung,” a microlithographic method developed in the 1980s. It was one of the fi rst major techniques to demonstrate the fabrication of high-aspect ratio structures. Beam sources include x-ray, ultraviolet, and reactive ion etching. MEMS devices are fabricated using LIGA techniques. Photolithography Light is used to transfer patterns onto light-sensitive photoresist substrates. Photolithography is primarily used in the manufacture of integrated circuits and MEMS devices. The wavelength range of optical lithography techniques ranges from the visible to the near ultraviolet—ca. 300 nm. The resolution of photolithography techniques is ~100 nm [20]. Immersion lithography
Just like with immersion optical microscopy, resolution can be enhanced by 30–40% with application of a liquid medium between the aperture and the sample with higher refractive index. The medium needs to conform to the following criteria: (1) refractive index n > 1, (2) low optical absorption at 193 nm l , (3) immersion fl uid compatible with the photoresist and the lens, and (4) be noncontaminating. Deep ultraviolet lithography (DUV)
Resolution with deep ultraviolet with l = 248–193 nm, resulting in features on the order of 50 nm
Extreme ultraviolet lithography (EUVL)
Short wavelength ultraviolet, l = 13.5 nm. EUVL resolution: ~30 nm [20]. The major problem with EUVL is that all matter absorbs EUV and damage to substrates is very likely. High vacuum is required and mask must be made of Mo–Si. X-ray lithography (XRL)
X-rays are produced by synchrotron sources. XRL is capable of producing features down to 10 nm. Problems include damage to substrate materials. Electron beam lithography (EBL)
An electron beam source is used instead of light to generate patterns. Although e-beams can be generated below a few nanometers, the practical resolution is determined by the electron scattering of the photoresist material. Just like in SEM, electron interaction volumes are generated during exposure. Line width <20 nm and electron energy: 10–50 ke V Electron beam writing (EBW)
EBW is a direct-writing procedure and, therefore, no pattern masters are required. Direct-write e-beam resolution is ca. 20 nm with lateral dimensions <10 nm [20]. Operation of electron beam parameters and patterning are computer controlled. Electron beam projection lithography (EPL)
This technique is similar to TEM in that electrons are focused through a lens and projected onto a surface. In this case, however, a pattern is placed near the aperture. EPL is a high-throughput technique. A diamond membrane is used as stencil mask material. The process is not limited by diffraction as are the photolithographic techniques [21]. Focused ion beam lithography (FIBL)
Utilizes a liquid metal ion source (LMIS) with beam size of 10+ nm. FIBL resolution is 30 nm [20]. There is less backscattering than EBL and FIBL resists are more sensitive. FIBL, however, is restricted by limitations in reliable ion sources, diffi culty in focusing, shorter penetration depth, swelling of resist, and whimsical ion implantation episodes. FIBL is also more expensive and slower that optical methods. Microcontact printing methods
The George Whitesides group at Harvard University invented the lithographic method of microcontact printing. A topographical master is created by standard lithographic techniques that employ electron, ion, or electromagnetic beams. A negative replica of the master is made by pouring an elastomeric polymer, usually polydimethylsiloxane (PDMS), over the master. Upon curing, the elastomer is removed and coated with a self-assembled monolayer such as hexadecanethiol. Application of gold then reproduces the master pattern. Sub-100 nm features are possible by this technique [20]. Nano-imprint lithography (NIL)
Nano-imprint lithography is used to fabricate nanometer-scale patterns. It is a straightforward economical process with high throughput and high resolution. Patterns are created by stamping a resist material with a prefabricated stamp. The stamp can be used over and over. There are two types: thermoplastic (TNIL) [22,23] and photo (PNIL) [22,23]
Fabrication Methods 187
Method Comments
Nanosphere lithography (NSL)
NSL is used to fabricate nanometer-scale patterns. It is a straightforward economical process with high throughput and high resolution. It is diffi cult to categorize this technique as top down or bottom up. Micron-scale latex spheres are often used as the template material. The interstices are nanoscale in size. NSL utilizes nanospherical materials in close-packed confi guration as a mask to aid in the fabrication of periodic particle arrays (PPAs). Polymer nanospheres (diameter <300 nm) are in a single or double layer over insulator, semiconductor, metal, inorganic ion insulator, or organic π-electron semiconductor materials. Depending on the sphere diameter, nanoscale facets on the order of 22 nm are easily formed [24]. Scanning AFM nanostencil
An evaporated particle beam source is focused through a hole in an AFM cantilever. The procedure is good for metal deposition. This technique combines the ability to pattern a surface simultaneously with the ability to image the surface with the same cantilever. It is diffi cult to classify this technique as top down or bottom up (e.g., as it is for the thermal evaporation technique discussed before).
Scanning probe nanolithographies
There exist several forms of scanning probe nanolithographies. Some impart mechanical stress via the probe tip to a sensitized surface, followed by a chemical treatment; others apply an STM current to a substrate to create dangling bonds that react further to produce nanofeatures. These methods can be considered as top down in that nanofacets and features are produced from a solid bulk substrate. 2-Photon polymerization
Photopolymerization causes polymer to solidify to form three-dimensional image. Resolution of ~120 nm, although the laser l is 780 nm [25]. This is, in the clearest sense of the term, a top-down process.
TABLE 4. (CONTD.)
TABLE 4.6 Top-Down Natural Fabrication Methods
Method Comments Erosion Conversion of macroscopic mineral-based materials into micro- and nanoparticles.
Etching Etching of silicate rocks by carbonic acid from the environment contributes to erosion. Hydrolysis The decomposition of organic (and inorganic) matter by hydrolysis is a common way to make nanomaterials in the natural world. Volcanic activity Formation of fl y ash and other materials by volcanic activity. The dispersion of volcanic byproducts is mostly airborne. Volcanic by-products contribute to the formation of clays like montmorillonite (a nanostructured material discussed in chapter 13).
Forest and brush fi res
Formation of combustion gases, nanometer scale PAHs, amorphous carbons, and particulates
Solar activity Radiation degradation of bulk synthetic, inorganic, and organic materials
Pressure and temperature
Formation of diamond crystallites from pressure and temperature processes applied to bulk materials; application to bulk carbon deposits (coal) Biological decomposition
Decomposition is a process that begins at the bulk, micro-, or nanoscale level and terminates at the nano, molecular, or atomic level. Biological decomposition is mitigated by bacterial and other life forms in addition to inorganic natural processes.
Digestion Reduction of bulk biological materials into nanometer and subnanometer scale components by the action of acids and hydrolysis; the formation of nitrogenous wastes is a bottom-up procedure, so to speak.
Fabrication Methods 189
TABLE 4.7 Bottom-Up Gas-Phase Fabrication Methods
Method Comments Chemical vapor deposition (CVD)
CVD involves the formation of nanomaterials from the gas phase, usually at elevated temperatures, onto a solid substrate or catalyst. Carbon nanotubes are formed by catalytic decomposition of carbon feedstock gas in inert carrier gas at elevated temperature. Single-walled carbon nanotube production by CVD requires nanoscale Fe, Co, or Ni catalyst plus Mo activator on high surface area support (alumina) at >650°C. Methane gas serves as the carbon source [26]. Atomic layer deposition (ALD)
ALD is an incredibly precise sequential surface chemistry layer deposition method to form thin fi lms on conductors, insulators, and ceramics. The layer formed by ALD conforms to surface topography. Precursor materials are kept separate until required. Atomic scale control pinhole-free layers are formed. Al 203 layers are generated from hydroxylated Si substrate + Al(CH 3 ) (^) 3(g), then H 2 O vapor is applied to remove methyl groups. The process is repeated until a target thickness is attained. Layer thickness: 1–500 nm Combustion The formation of Si nanoparticles from the combustion of SiH 4 (silane gas) and other silicon-containing gases like hexamethyldisiloxane under low-oxygen conditions produces Si nanoparticles as small as 2 nm. Al 2 O 3 and TiO 2 can also be formed by combustion. Thermolysis; pyrolysis
Solid Si nanoparticles can also be formed by the thermal decomposition of silane gas in the absence of oxygen. The bottom-up decomposition of ferrocene to form Fe nanoparticles is one of the best examples of a bottom-up gas-phase fabrication method. Metal oxide (MOCVD) Organometallic vapor phase epitaxy (OMVPE)
Chemical characteristics of precursor materials utilize reactive gas-phase-organometallic compounds that decompose to form nanometer-scale thin fi lms or nanoparticles. H 2 carrier gas, group III metal–organic compounds + group V hydrides 500–1500°C at 15- to 750-torr pressure are representative conditions under which MOCVD is performed. Molecular beam epitaxy (MBE)
MBE is a thin fi lm growth process conducted under high vacuum. A heated Knudsen cell or effusion cell is used to introduce reactants by molecular beams. MBE is able to deposit one atomic layer per application. Examples include alternate layers of GaAs and AlGaAs with each layer of 1.13 nm in thickness and InGaAs quantum dots [27]. The temperature used in MBE is commonly 750–1050°C in H 2 carrier gas. Ion implantation This is a tough method to categorize. Nanovoids, for example, can be created by ion implantation of Cu ions into silica and subsequent annealing [28]. It is bottom-up action performed on a bulk material. If the ions come from a bulk source, it has a bottom up component. Once the ions are formed, ion implantation is bottom up. Gas phase condensation; thermolysis
Formation of Fe nanoparticles by decomposition of ferrocene at 200°C is an example of gas-phase process to form nanoscale Fe. Formation of lithium nanoclusters by decomposition of LiN 3 is another example [7]. Temperature at decomposition depends on the material. Solid template synthesis
Provides a solid template substrate for gas-phase deposition of materials on the solid substrate. This is considered to be a mixed bottom-up system. Final nanomaterial size, shape, and orientation are predetermined by template parameters.
190 Introduction to Nanoscience
TABLE 4.8 Nonbiological Bottom-Up Liquid-Phase Fabrication Methods
Method Comments Molecular self-assembly
This generic process is supported in liquid media. From some perspectives, supramolecular chemistry is a subset of molecular self-assembly. Almost all molecular self-assembly takes place in liquids. The liquid plays a major role in supporting intermolecular interactions and intermediate metastable species. Supramolecular chemistry
Supramolecular chemistry, for reasons to be explained in chapter 11, is conducted in liquid media. Weak intermolecular forces are supported in liquids that allow many kinds of intermolecular interactions to take place. All signifi cant biological metabolic processes occur in a liquid medium. Nucleation and sol–gel processes
Precursor chemicals in a supersaturated state combine by self-assembly or chemical reaction to form seed particles. Thermodynamics drives a nucleation process that forms nanoparticles. The nucleation process depends on prevailing conditions of pH, temperature, ionic strength, and time [5]. Due to van der Waals attractions, colloids are formed. Sol–gel methods are irreversible chemical reactions of homogeneous solutions that result in a three-dimensional polymer. Sol–gel methods yield nanostructured materials of high purity and uniform nanostructures formed at low temperatures [5]. Negative replicas of colloidal hierarchical structures, upon drying, yield aerogels or xerogels. Such gels can be back-filled to produce nanocomposites or hybrid materials [5]. These are all pure bottom-up processes. Reduction of metal salts
Noble metal clusters and colloids are formed by the reduction of metal salts like HAuCl 4 and H 2 PtCl 6. Common reducing agents come in the form of organic salts like sodium citrate— Na3C 6 H 5 O7. By means of phase transfer reactions (consisting of an interface between two immiscible liquids), metal clusters and colloids are stabilized by the addition of organic ligands. For example, phosphine or thiols are adsorbed onto gold-55 to produce a stable cluster [29]. Single-crystal growth Nucleation process to form single crystals in liquid media Electrodeposition Electroplating
Electrodeposition is direct deposition of metals from metal salt solutions to form thin layers or fi lms on a solid conducting substrate. Electrodeposition is an electrolytic process that forms thin metal fi lms on the cathode of the cell. The process conforms to Faraday’s law. Electroless deposition Electroless deposition is the autocatalytic deposition of metals without electrical assistance. It requires metal cation + catalytic (activated) surface + reducing agents like formaldehyde, alkali diboranes, alkali borohydrides, or hypophosphorous acid. Pt, Ni, Co, Au, and numerous other metals can be deposited on many kinds of substrates, including plastics. Electroless deposition has been used to create negative or positive replicas of porous nanostructures [30]. Anodizing We have already characterized anodizing as a top-down process. We mentioned earlier that anodizing method contains a top-down component (formation of scalloped structure). Here, we focus on the bottom-up formation of the porous alumina. Aluminum metal is made the anode in an electrolytic cell consisting of a polyprotic acid (usually sulfuric, phosphoric, or oxalic). Pore diameter of <5 nm → >200 nm; with pore density: 20–80+% and fi lm thickness: <1 μm → > 100 μm. Anodized titanium several nanometers thick generates bright interference colors. Electrolysis in molten salt solutions
Utilization of molten alkali halide salts with graphite electrodes with 3- to 5-A current [31] Erosion at the cathode to form tubes The product is transferred to toluene. Solid template synthesis
Provides a solid template substrate for electrochemical, chemical, polymerization, and other liquid-phase reactions. Most methods are accomplished in a liquid medium. Final nanomaterial size, shape, and orientation predetermined by template parameters. Liquid template synthesis
Liquid templates (micelles and reverse micelles) are commonly used to make quantum dots from the bottom up. Supercritical fl uid expansion
Solvent removal under hypercritical conditions forms aerogels and xerogels that contain nanometer-sized voids. Supercritical conditions imply that the medium is in neither liquid nor solid phase.
192 Introduction to Nanoscience
TABLE 4.10 Bottom-Up Biological and Inorganic Fabrication Methods
Method Comments Protein synthesis Formation of proteins from precursor amino acids by elaborate process of protein synthesis Transfer RNA transports amino acids to ribosomal RNA and link with peptide bonds. Nucleic acid synthesis Synthesis of nucleic material (RNA, DNA) from sugars, phosphate, and nuclides (adenosine, guanine, cytosine, and thymine) from the bottom up The processes of mitosis and meiosis are template (replication) methods. Membrane synthesis Bottom-up agglomeration of lipids, phospholipids to form organized membrane structures that make life possible Inorganic biological structures
Mother of pearl (nacre) 95% Inorganic aragonite (platelets 200–500 nm thick) + organic biopolymer Deformable nanograins [38] Crystal formation methods
Nucleation depends on P, T, concentration, and composition. Flaws reduce surface energy by nucleation. Direction of growth depends on nanostructure.
4.0.5 The Nano Perspective
Fabrication Methods 193
4.1 TOP-D OWN FABRICATION
TABLE 4.11 The Nanostructure of Tendons
Structural component Dimensions Description/function Amino acids (^) <1-nm The building blocks of proteins Collagen 1.5-nm Diameter Primary structure polypeptide (the protein of connective tissue) Triple-helix coil (tropocollagen) 1.5-nm Diameter; 300 nm length
Three polypeptide strands form a cooperative quaternary structure. Microfi brils Subfi bril Fibril
<4-nm Diameter 10–20-nm Diameter 50–500-nm Diameter Connective tissue called^ endomysium^ based on collagen subunits that surround muscle fi brils Fascicle 50–300 μm Bundle of muscle fi brils (~10) surrounded by perimysium (connective tissue) [40]. The endo-, peri-, and epimysia converge to form the tendon. Tendon 10–50 cm Attachment of muscle to bone support structure Provides fl exibility and strength