
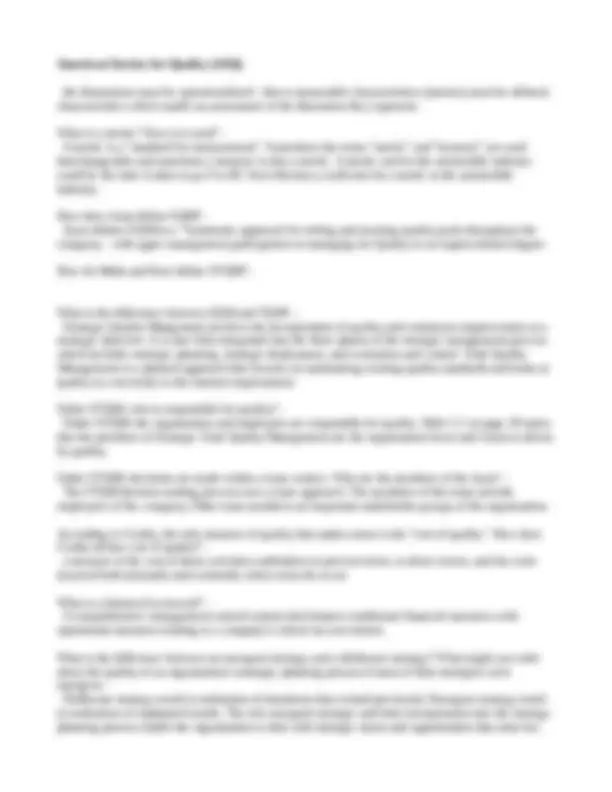
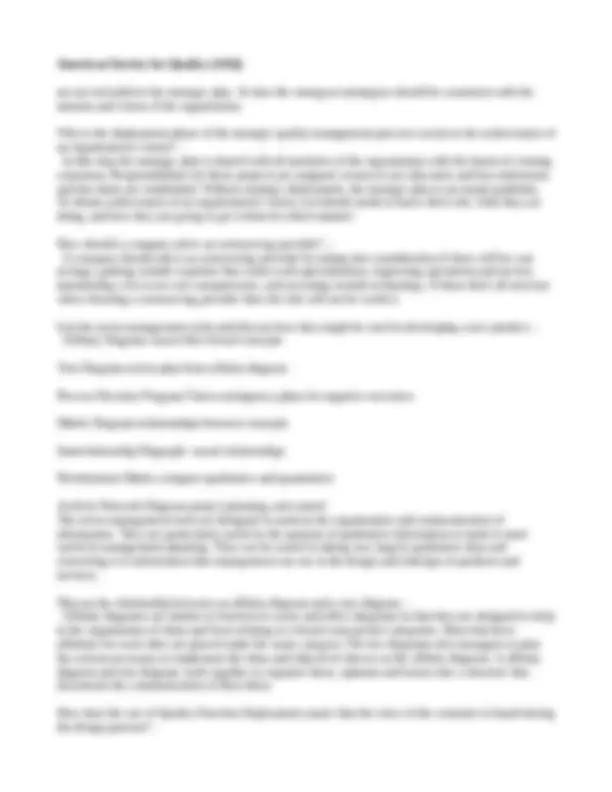
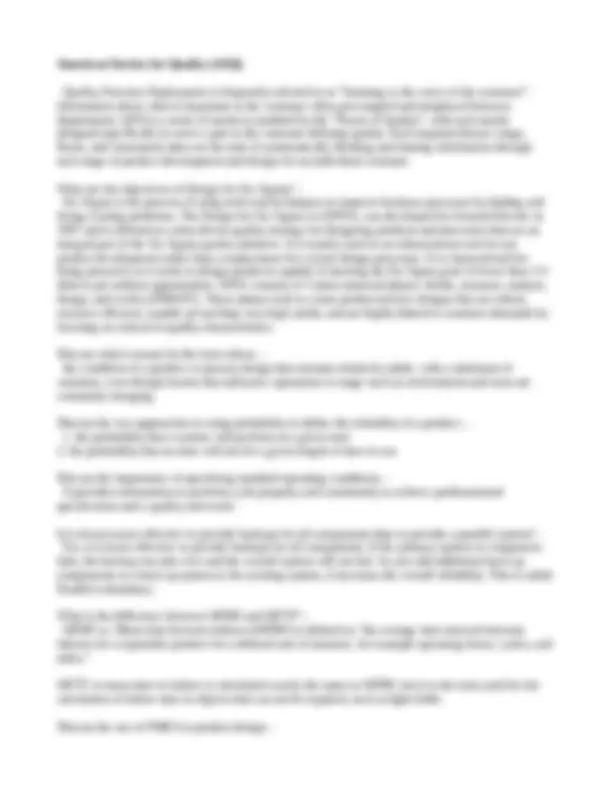
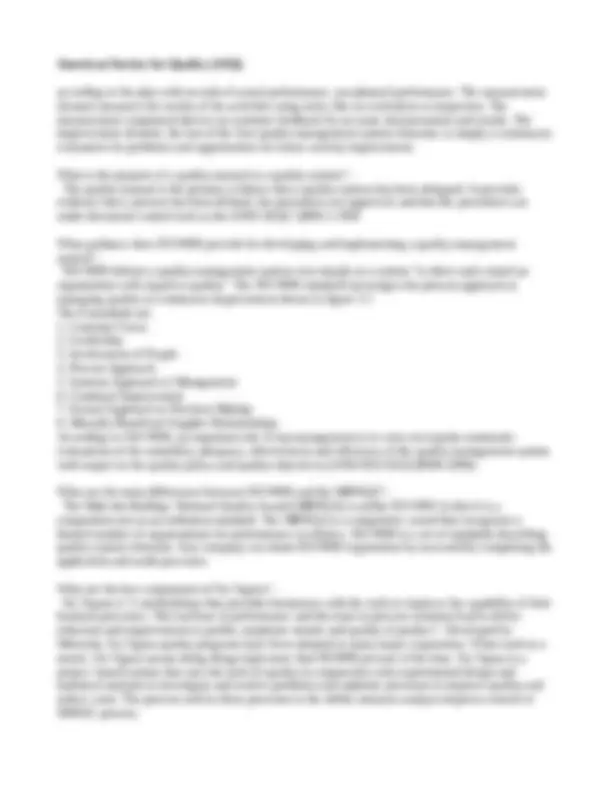
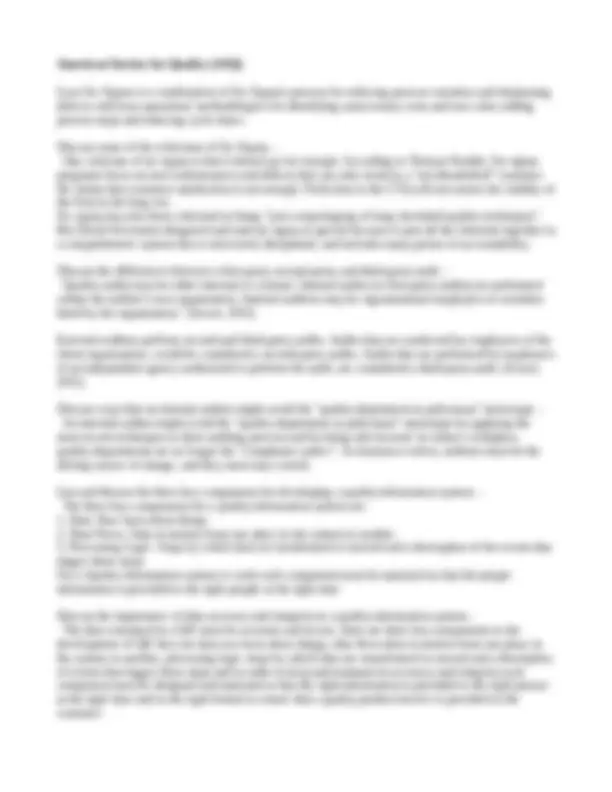
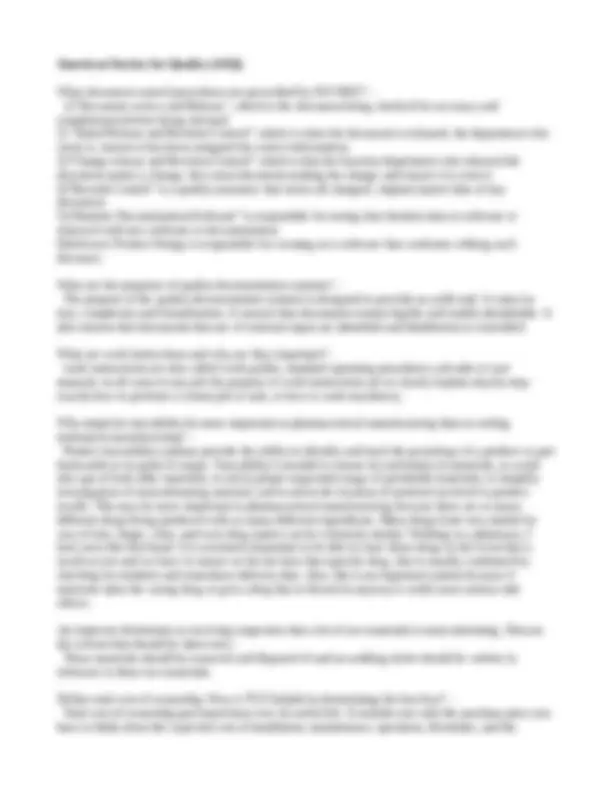
Study with the several resources on Docsity
Earn points by helping other students or get them with a premium plan
Prepare for your exams
Study with the several resources on Docsity
Earn points to download
Earn points by helping other students or get them with a premium plan
Community
Ask the community for help and clear up your study doubts
Discover the best universities in your country according to Docsity users
Free resources
Download our free guides on studying techniques, anxiety management strategies, and thesis advice from Docsity tutors
American Society for Quality (ASQ)
Typology: Exams
1 / 11
This page cannot be seen from the preview
Don't miss anything!
How does the American Society for Quality (ASQ) define quality? - A subjective term for which each person has his or her own definitions. In technical usage, quality can have two meanings. 1) the characteristics of a product or service that bear on its ability to satisfy stated or implied needs. 2) a product or service free of deficiencies. Discuss and distinguish between "internal" and "external" customers - External customers are peopole outside our organization who receive our goods and services. Internal customers are people inside our organization who receive our work services (example - assembly line operation - the station downstream form ours is our internal customer (they are receiving our work)). Describe the three quality revolutions identified by Sower (2011). - The first modern quality revolution occurred in the United States during World War II years, after which it declined in this country until the early 1970s. The second quality revolution occurred in Japan I the 1950s with the work of W/ Edawards Deming, Joseph Juran, and Armand Feigenbaum, and it resulted in Japan's emergence as an economic power. The third quality revolution began in the United States during the early 1970's when the work of Deming, Juran, Feigenbaum, and Phillip Crosby was finally recognized and put into practice in this country. During each of these revolutions , attention was paid to defining just what this "quality" was. Sower states that quality is not just satisfying customers but that it is delighting customers. What does this mean? - He means that when we delight a customer we exceed their expectations which is where competitive advantage can be found. List and briefly describe the eight dimensions of product quality identified by Garvin (1987). - Performance- Product's primary operating characteristics (clock speed; RAM; Hard drive size) Features - Characteristics that supplement basic functioning (Wireless mouse; flat-screen monitor; DVD-RW) Reliability- Probability of a product malfunctioning within a specific time period. (mean time between failures) Conformance-the degree to which a product's design and operating characteristics meet established standards (Underwriter Laboratories labeled; mouse, monitor, keyboard included with CPU) Durability- expected product life (time to technical obsolescence; rated life of monitor) Serviceability- speed, courtesy, competence, and ease of repair (warranty conditions) Aesthetics- how a product looks, feels, sounds, tastes, or smells (computer housing color scheme; keyboard "touch") Perceived Quality- reputation and other indirect measures of quality (brand name; advertising) List and briefly describe the five service quality dimensions identified by Parasuraman et al., 1988). -
Tangibles - hings you would see and use such as physical facilities, equipment, and appearance of personal. Examples of tangibles are an ATM access, lobby layout, tellers dressed professionally Reliability- Having an ability to perform the promised service dependably and accurately. Examples of reliability are meeting promised deadlines and reassuring problem resolution. Responsiveness- Showing willingness to help customers and provide prompt service. Examples of responsiveness are responding quickly to customer requests; willingness to help customers. Assurance- Having knowledge and courtesy of employees and their ability to inspire confidence and trust. Examples of assurance are trustworthiness; save environments around ATMS; polite behavior of tellers. Empathy- Employees demonstrate sharing and individualized attention the firm provides its customers. Examples of empathy are personal attention to customers; convenient hours. How does knowledge of the dimensions of product and service quality help managers as they work to manage for improved performance? - With knowledge of the dimensions a manager must consider if he needs to make some tradeoffs to improve performance. Distinguish between order qualifiers and order winners. Relate this distinction to the difference between satisfying customers and delighting customers. - Order qualifiers are minimum characteristics that a product or service must have in order to be considered to be of acceptable quality (flashlight that does not provide light would not be considered a quality item under this definition) Order winners are the enhancements that exceed the minimum characteristics (could include enhanced battery life, custom fit to the hand, or enhanced beam focus if it were a flashlight) List and discuss the steps in Shewhart Cycle and the Deming Cycle. - Shewhart cycle - plan, do, check, act this application of statistical methods in mass production makes possible the most efficient use of raw materials and manufacturing processes, and makes possible the highest economic standards of quality for manufactured goods used by us. Deming cycle- plan, do, study, act he wanted to improve the system and not criticize workers, he believed that workers were already doing their best work with resources that were provided. List and briefly describe the two sources of variation. How did Shewhart define the state of statistical control? - Chance causes that are inherent in they system and assignable or special causes that are signs of trouble in the system. Shewhart defined statistical control as the state where there is only chance‐cause (common‐cause) variation. Dr. Sower refers to the process of developing measures and metrics as what? -
are not included in the strategic plan. At time the emergent sstrategies should be consistent with the mission and vision of the organization. Why is the deployment phase of the strategic quality management process crucial to the achievement of an organization's vision? - In this step the strategic plan is shared with all members of the organization with the intent of creating consensus. Responsibilities for these projects are assigned, resources are allocated, and key milestones and due dates are established. Without strategic deployment, the strategic plan is an empty guideline. To obtain achievement of an organization's vision, everybody needs to know their role, what they are doing, and how they are going to get it done/in which manner. How should a company select an outsourcing provider? - A company should select an outsourcing provider by taking into consideration if there will be cost savings, gaining outside expertise that comes with specialization, improving operations and service, maintaining a focus on core competencies, and accessing outside technology. If these don't all increase when choosing a outsourcing provider then the risk will not be worth it. List the seven management tools and discuss how they might be used in developing a new product. - Affinity Diagram-cause/effect broad concepts Tree Diagram-action plan from affinity diagram Process Decision Program Chart-contingency plans for negative outcomes Matrix Diagram-relationships between concepts Interrelationship Diagraph- causal relationships Prioritization Matrix-compare qualitative and quantitative Activity Network Diagram-project planning and control The seven management tools are designed to assist in the organization and communication of information. They are particularly useful in the analysis of qualitative information to make it more useful in management planning. They can be useful in taking raw, largely qualitative data and converting it to information that management can use in the design and redesign of products and services. Discuss the relationship between an affinity diagram and a tree diagram. - Affinity diagrams are similar in function to cause-and-effect diagrams in that they are designed to help in the organization of ideas and facts relating to a broad concept into categories. Ideas that have affinities for each other are placed under the same category. The tree diagrams aloe managers to plan the actions necessary to implement the ideas and objectives shown on the affinity diagram. A affinity diagram and tree diagram work together to organize ideas, opinions and issues into a structure that documents the communication of their ideas. How does the use of Quality Function Deployment assure that the voice of the customer is heard during the design process? -
Quality Function Deployment is frequently referred to as "listening to the voice of the customer". Information about what is important to the customer often gets tangled and misplaced between departments. QFD is a series of matrices modeled by the "House of Quality", with each matrix designed specifically to serve a part in the customer defining quality. Each segment (house wings, floors, attic basement) takes on the task of systematically dividing and sharing information through each stage of product development and design for an individual customer. What are the objectives of Design for Six Sigma? - Six Sigma is the process of using tools and techniques to improve business processes by finding and fixing existing problems. The Design for Six Sigma or (DFSS), was developed by General Electric in 1997 and is defined as a data driven quality strategy for designing products and processes that are an integral part of the Six Sigma quality initiative. It is mainly used as an enhancement tool for not product development rather than a replacement for current design processes. It is characterized for being proactive as it seeks to design products capable of meeting the Six Sigma goal of fewer than 3. defects per million opportunities. DFSS consists of 5 interconnected phases: define, measure, analyze, design, and verify (DMADV). These phases seek to create product/service designs that are robust, resource efficient, capable pf reaching very high yields, and are highly linked to customer demands by focusing on critical-to-quality characteristics. Discuss what is meant by the term robust. - the condition of a product or process design that remains relatively stable, with a minimum of variation, even though factors that influence operations or usage such as environment and wear are constantly changing. Discuss the two approaches to using probability to define the reliability of a product. -
important for superiors to take the extra effort to focus on their creativity and bring it out of them. It is very important for those hiring to review their skills. What are some ways to stimulate creativity within an organization? - There are so many ways to stimulate creativity according to our lesson book Robinson and Stern gives some elements. Alignment involve good communication by management they need to know the key goal and objectives of the organization are and hold employees accountable for their activities. Senior management is responsibility for alignment by effective communication, establishment of a responsive and equitable reward and recognition system. Idea programs sponsored by the organization are one way to encourage self initiated activity. Self -initiated activity must be supported and promoted by senior management by allowing freedom and autonomy in decisions about work, encouraging risk taking, and tolerance on nonconformity. We know that their is many ways to encourage creativity by also encouraging risk taking, providing adequate resources. Why might creative projects benefit from some period of unofficial status? - Unofficial activity recognizes that good ideas sometimes are killed in their infancy because they are made official too soon. When a project is unofficial it is not subject to budgets, timelines, or review by management. That gives the originator of the idea the freedom to develop it. What is meant by alignment? Of what importance is it to a creative organization? - Alignment refers to how well the interests and actions of each employee contribute to attainment of organizational goals. This is necessary for employees to understand which direction to channel their creativity. What does it mean to be a risk-tolerant organization? How does that relate to the level of creative that is likely to develop in an organization? - A risk tolerant organization is one that encourages risk-taking in order to spur creativity. They create an environment where workers can benefit from their mistakes as well as their successes. Open communication is encouraged between employees. Unofficial activity is accepted and encouraged while allowing freedom and autonomy in decisions about work, encouraging risk taking, providing adequate resources (especially time) and tolerance of nonconformity By opening up and allowing creativity to happen, the organization can rise through the levels on the divided line from learning, to hands on experience, to mathematical understanding, and finally to insight where new products or processes are created. How does one reconcile the definition of quality as meeting customer needs in cases where customers cannot articulate those needs? - There is certainly a need for creativity within the framework of continuous incremental improvement. But if we apply the definition of quality as "meeting customer needs" one need not be elderly to have experienced radical breakthrough improvements that redefined "customer needs". List and discuss the key elements of a quality management system - There are four key elements of a quality management system; planning, performance, measurement, and improvement. The planning element designates responsibility, accountability, and ownership of the activities that occur during the plan. It also defines who the customer and other constituents are, as well as their requirements. The performance element ensures that the activities should be executed
according to the plan with records of actual performance, not planned performance. The measurement element measures the results of the activities using tools, like an evaluation or inspection. The measurement component thrives on customer feedback for accurate measurements and results. The improvement element, the last of the four quality management system elements, is simply a continuous evaluation for problems and opportunities for future activity improvement. What is the purpose of a quality manual in a quality system? - The quality manual is the primary evidence that a quality system has been designed. It provides evidence that a process has been defined, the procedures are approved, and that the procedures are under document control such as the ANSI/ASQC Q900-1- What guidance does ISO 9000 provide for developing and implementing a quality management system? - ISO 9000 defines a quality management system very simply as a system "to direct and control an organization with regard to quality." The ISO 9000 standard encourages the process approach to managing quality as continuous improvement shown in figure 5. The 8 standards are:
What document control procedures are prescribed by ISO 9001? - 1)"Document review and Release", which is the document being checked for accuracy and completeness before being released.
expected cost of the equipment. TCO determine the initial delivered and installed cost of the equipment. You have to estimate all the cost associated with the operation of the equipment during its lifetime, routine maintenance and mean cost of repair and labor requirement. List and discuss the four major factors in supplier selection. -