
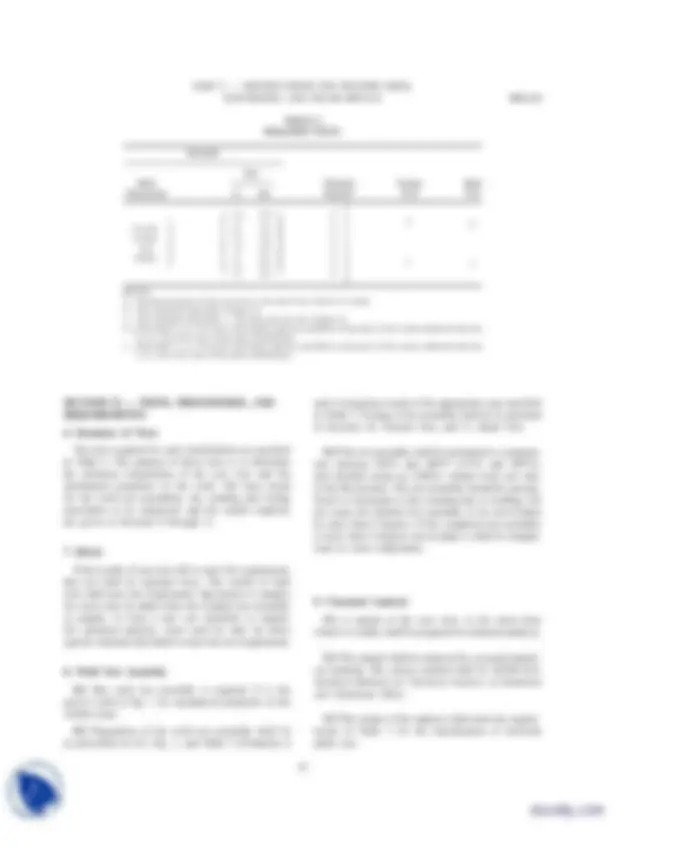
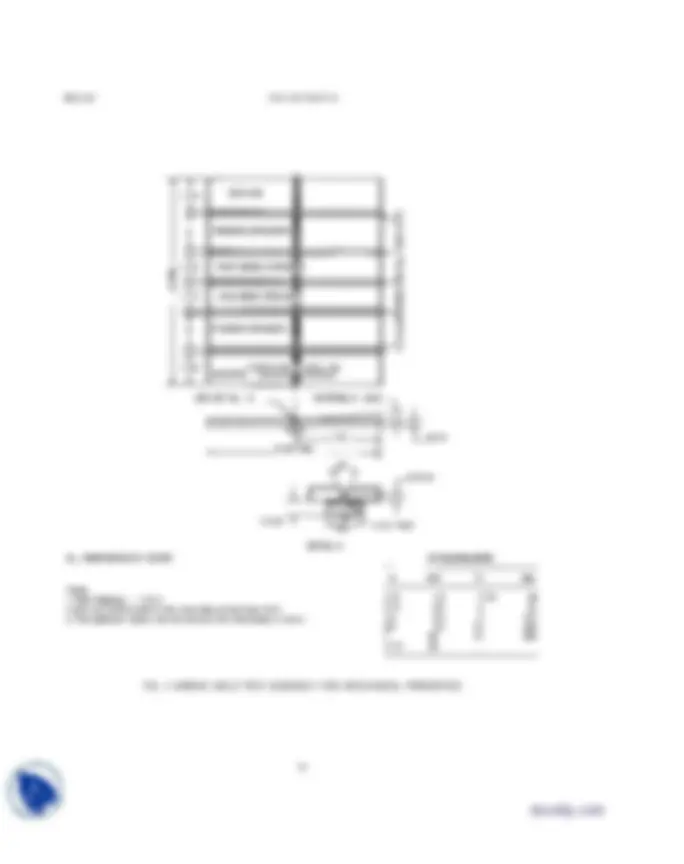
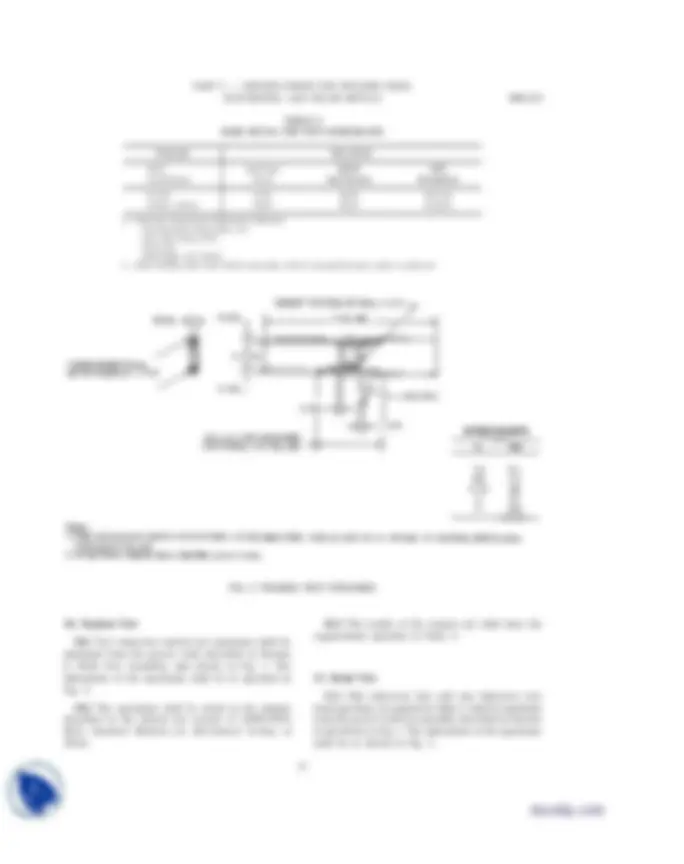
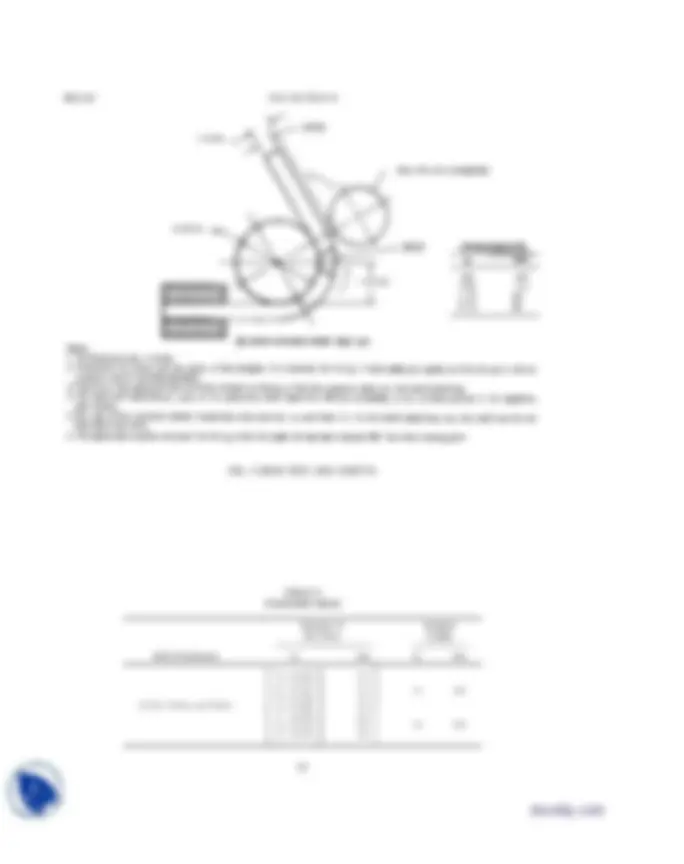
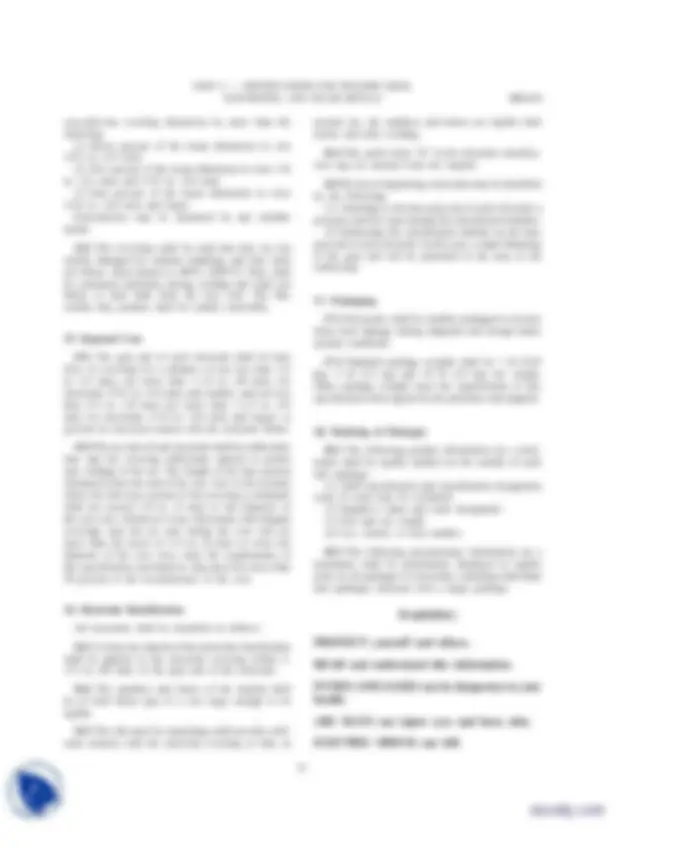
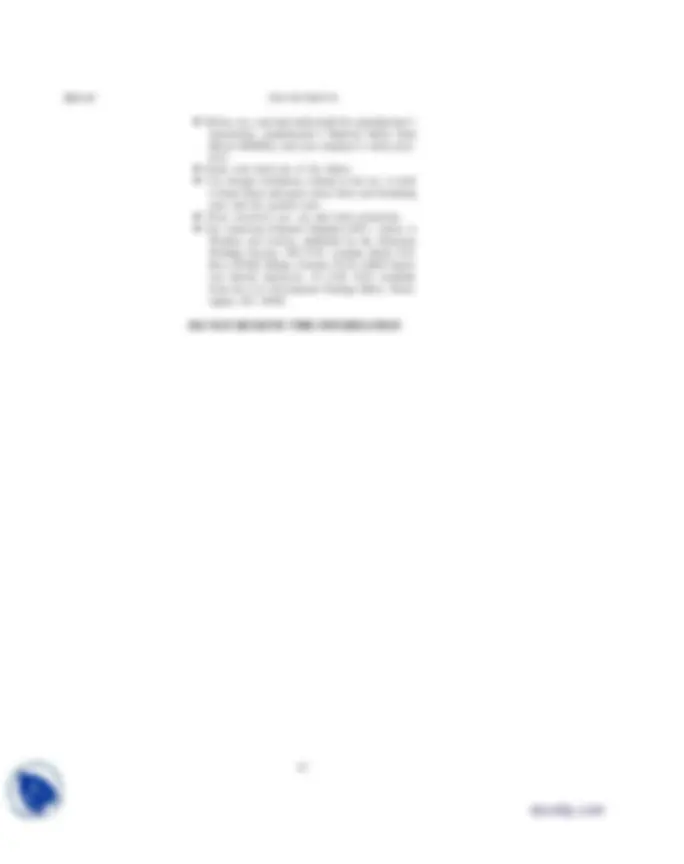
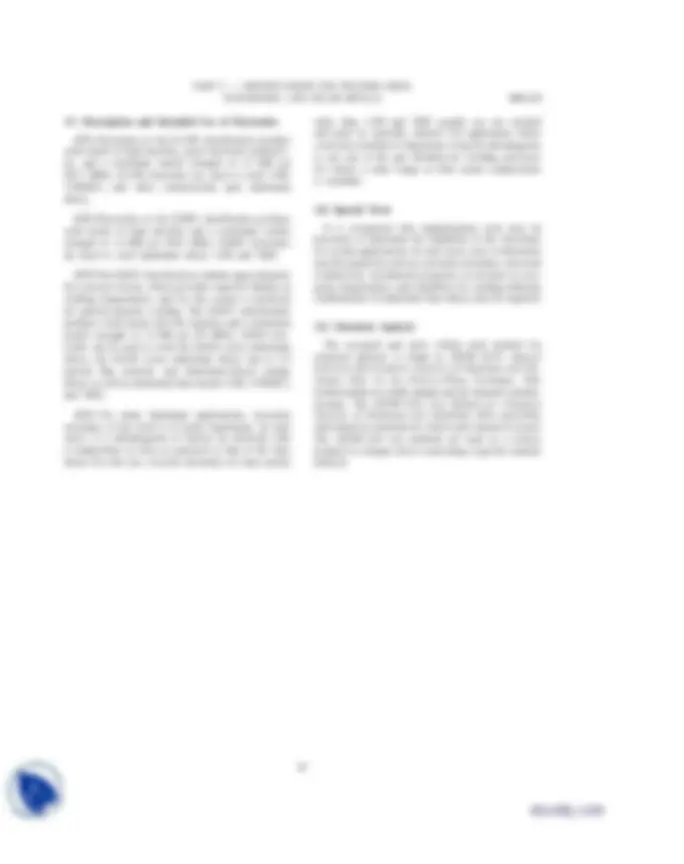
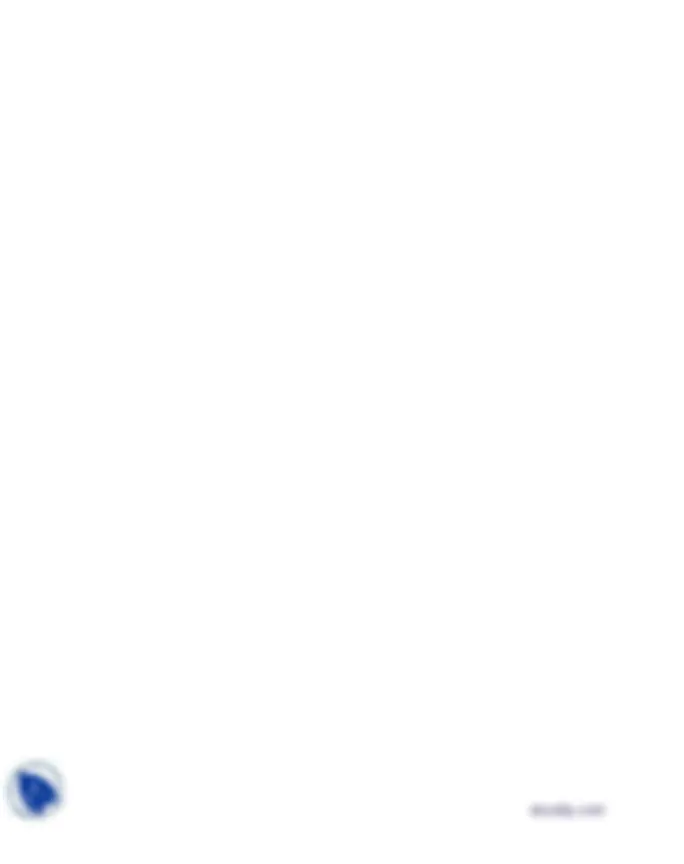
Study with the several resources on Docsity
Earn points by helping other students or get them with a premium plan
Prepare for your exams
Study with the several resources on Docsity
Earn points to download
Earn points by helping other students or get them with a premium plan
Community
Ask the community for help and clear up your study doubts
Discover the best universities in your country according to Docsity users
Free resources
Download our free guides on studying techniques, anxiety management strategies, and thesis advice from Docsity tutors
Dr. Ajitabh Sai delivered this lecture at Baba Farid University of Health Sciences for Mechanical and Materials Engineering Specifications course. It includes: Specification, Aluminium, Alloy, Electrodes, Shield, Metal, Arc, Welding, Test, Requirements, Procedures
Typology: Exercises
1 / 14
This page cannot be seen from the preview
Don't miss anything!
(Identical with AWS Specification A5.3-91)
1. Scope
This specification prescribes requirements for the classification of aluminum and aluminum alloy elec- trodes for shielded metal arc welding.
2. Classification
2.1 The electrodes covered by this specification are classified according to the chemical composition of the core wire as specified in Table 1, and mechanical properties of a groove weld.
2.2 An electrode classified under one classification shall not be classified under any other classification in this specification.
3. Acceptance
Acceptance^1 of the electrode shall be in accordance with the provisions of ANSI /AWS A5.01, Filler Metal Procurement Guidelines.^2
4. Certification
By affixing the AWS specification and classification designations to the packaging, or the classification to
(^1) See A3, Acceptance (in the Appendix), for further information concerning acceptance, testing of the material shipped, and ANSI /AWS A5.01, Filler Metal Procurement Guidelines. (^2) AWS Standards can be obtained from the American Welding Society, 550 N.W. LeJeune Road, P.O. Box 351040, Miami, Florida 33135
53
the product, the manufacturer certifies that the product meets the requirements of this specification.^3
5. Units of Measure and Rounding-Off Procedure 5.1 U.S. Customary Units are the standard units of measure in this specification. The SI Units are given as equivalent values to the U.S. Customary Units. The standard sizes and dimensions in the two systems are not identical, and for this reason conversion from a standard size or dimension in one system will not always coincide with a standard size or dimension in the other. Suitable conversions, encompassing standard sizes of both, can be made, however, if appropriate tolerances are applied in each case.
5.2 For the purpose of determining conformance with this specification, an observed or calculated value shall be rounded to the nearest 1000 psi (7 MPa) for tensile and yield strength, and to the “nearest unit” in the last right-hand place of figures used in expressing the limiting value for other quantities in accordance with the rounding-off method given in ASTM E29, Practice for Using Significant Digits in Test Data to Determine Conformance with Specifications.^4
(^3) See A4, Certification (in the Appendix), for further information concerning certification and the testing called for to meet this requirement. (^4) ASTM Standards can be obtained from the American Society for Testing and Materials, 1916 Race Street, Philadelphia, Pennsylva- nia 19103
SFA-5.3 1998 SECTION II
TABLE 1
CHEMICAL COMPOSITION REQUIREMENTS FOR CORE WIRE (WEIGHT PERCENT)
a,b
Other Elements
AWS
UNS
Classification
Designation
c^
Si
Fe
Cu
Mn
Mg
Zn
Ti
Be
Each
Total
Al
E
A
(d)
(d)
0.05–0.
—
—
99.00 min
e
E
A
0.05–0.
1.0–1.
—
—
Remainder
E
A
4.5–6.
Remainder
NOTES:a. The core wire, or the stock from which it is made, shall be analyzed for the specific elements for which values are shown in this table. If the presence of other elements is indicated in the
course of work, the amount of those elements shall be determined to ensure that they do not exceed the limits specified for “Other Elements.” b. Single values are maximum, except where otherwise specified.c. SAE/ASTM Unified Numbering System for Metals and Alloys. d. Silicon plus iron shall not exceed 0.95 percent.e. The aluminum content for unalloyed aluminum is the difference between 100.00 percent and the sum of all other metallic elements present in amounts of 0.010 percent or more each,expressed to the second decimal before determining the sum.
54
SFA-5.3 1998 SECTION II
FIG. 1 GROOVE WELD TEST ASSEMBLY FOR MECHANICAL PROPERTIES
56
PART C — SPECIFICATIONS FOR WELDING RODS, ELECTRODES, AND FILLER METALS SFA-5.
TABLE 3 BASE METAL FOR TEST ASSEMBLIES
Electrode Base Metal AWS Aluminum ASTM UNS Classification Alloy a^ Specification Designation E1100 1100 B209 A E3003, E4043 3003 b^ B209 A a. Aluminum Association Registration Numbers. The Aluminum Association, Inc. 900 19th Street, N.W. Suite 300 Washington, DC 20006 b. When welding 3003 with E4043 electrodes, 3003-0 (annealed temper) plate is preferred.
FIG. 2 TENSION TEST SPECIMEN
10. Tension Test
10.1 Two transverse tension test specimens shall be machined from the groove weld described in Section 8, Weld Test Assembly, and shown in Fig. 1. The dimensions of the specimens shall be as specified in Fig. 2.
10.2 The specimens shall be tested in the manner described in the tension test section of ANSI /AWS B4.0, Standard Methods for Mechanical Testing of Welds.
57
10.3 The results of the tension test shall meet the requirements specified in Table 4.
11. Bend Test 11.1 One transverse face and one transverse root bend specimen, as required in Table 2, shall be machined from the groove weld test assembly described in Section 8 and shown in Fig. 1. The dimensions of the specimens shall be as shown in Fig. 3.
PART C — SPECIFICATIONS FOR WELDING RODS, ELECTRODES, AND FILLER METALS SFA-5.
FIG. 4 BEND TEST JIGS
59
SFA-5.3 1998 SECTION II
FIG. 4 BEND TEST JIGS (CONT’D)
TABLE 5 STANDARD SIZES
Diameter of Standard Core Wire, Lengths
AWS Classification in. mm in. mm (^3) ⁄ 32 (0.094) 2. (^1) ⁄ 8 (0.125) 3. (^5) ⁄ 14 350 32 (0.156)^ 4. E1100, E3003, and E4043 3 ⁄ 16 (0.188) 4.
(^1) ⁄ 4 (0.250) 6. (^5) ⁄ 16 (0.312) 8.0 18 450 (^3) ⁄ 8 (0.375) 9.
60
SFA-5.3 1998 SECTION II
O Before use, read and understand the manufacturer’s instructions, manufacturer’s Material Safety Data Sheets (MSDSs), and your employer’s safety prac- tices. O Keep your head out of the fumes. O Use enough ventilation, exhaust at the arc, or both to keep fumes and gases away from your breathing zone and the general area. O Wear corrective eye, ear and body protection. O See American National Standard Z49.1, Safety in Welding and Cutting, published by the American Welding Society, 550 N.W. LeJeune Road, P.O. Box 351040, Miami, Florida 33135; OSHA Safety and Health Standards, 29 CFR 1910 , available from the U.S. Government Printing Office, Wash- ington, DC 20402
62
PART C — SPECIFICATIONS FOR WELDING RODS, ELECTRODES, AND FILLER METALS SFA-5.
(This Appendix is not a part of ANSI /AWS A5.3-91, Specification for Aluminum and Aluminum Alloy Electrodes for Shielded Metal Arc Welding, but is included for information purposes only.)
A1. Introduction
The purpose of this guide is to correlate the electrode classifications with their intended applications so the specification can be used effectively. Reference to appro- priate base metal specifications is made whenever that can be done and when it would be helpful. Such references are intended only as examples rather than complete listings of the materials for which each filler metal is suitable.
A2. Classification System
The system for identifying the electrode classifications in this specification follows the standard pattern used in other AWS filler metal specifications. The letter E at the beginning of each classification designation stands for electrode. The numerical portion of the designation in this specification conforms to the Aluminum Associa- tion registration for the composition of the core wire used in the electrode.
A3. Acceptance
Acceptance of all welding materials classified under this specification is in accordance with ANSI /AWS A5.01, Filler Metal Procurement Guidelines, as the specification states. Any testing a purchaser requires of the supplier, for material shipped in accordance with this Specification, shall be clearly stated in the purchase order, according to the provisions of ANSI /AWS A5.01. In the absence of any such statement in the purchase order, the supplier may ship the material with whatever testing normally is performed on material of that classi-
63
fication, as specified in Schedule F, Table 1, of ANSI /AWS A5.01. Testing in accordance with any other Schedule in that Table must be specifically re- quired by the purchase order. In such cases, acceptance of the material shipped shall be in accordance with those requirements.
A4. Certification The act of placing the AWS specification and classi- fication designations on the packaging enclosing the product, or the classification on the product itself, constitutes the supplier’s (manufacturer’s) certification that the product meets all of the requirements of the specification. The only testing requirement implicit in this certifica- tion is that the manufacturer has actually conducted the tests required by the specification on material that is representative of that being shipped and that material met the requirements of the specification. Representative material, in this case, is any production run of that classification using the same formulation. “Certification” is not to be construed to mean that tests of any kind were necessarily conducted on samples of the specific material shipped. Tests on such material may or may not have been conducted. The basis for the certification required by the specification is the classification test of “representative material” cited above, and the “Manu- facturer’s Quality Assurance Program” in ANSI /AWS A5.01.
PART C — SPECIFICATIONS FOR WELDING RODS, ELECTRODES, AND FILLER METALS SFA-5.
A7. Description and Intended Use of Electrodes
A7.1 Electrodes of the E1100 classification produce weld metal of high ductility, good electrical conductiv- ity, and a minimum tensile strength of 12 000 psi (82.7 MPa). E1100 electrodes are used to weld 1100, 1350(EC), and other commercially pure aluminum alloys.
A7.2 Electrodes of the E3003 classification produce weld metal of high ductility and a minimum tensile strength of 14 000 psi (96.5 MPa). E3003 electrodes are used to weld aluminum alloys 1100 and 3003.
A7.3 The E4043 classification contains approximately five percent silicon, which provides superior fluidity at welding temperatures, and for this reason is preferred for general purpose welding. The E4043 classification produces weld metal with fair ductility and a minimum tensile strength of 14 000 psi (97 MPa). E4043 elec- trodes can be used to weld the 6XXX series aluminum alloys, the 5XXX series aluminum alloys (up to 2. percent Mg content), and aluminum-silicon casting alloys, as well as aluminum base metals 1100, 1350(EC), and 3003.
A7.4 For many aluminum applications, corrosion resistance of the weld is of prime importance. In such cases, it is advantageous to choose an electrode with a composition as close as practical to that of the base metal. For this use, covered electrodes for base metals
65
other than 1100 and 3003 usually are not stocked and must be specially ordered. For application where corrosion resistance is important, it may be advantageous to use one of the gas shielded arc welding processes for which a wider range of filler metal compositions is available.
A8. Special Tests It is recognized that supplementary tests may be necessary to determine the suitability of the electrodes for certain applications. In such cases, tests to determine specific properties such as corrosion resistance, electrical conductivity, mechanical properties at elevated or cryo- genic temperatures, and suitability for welding different combinations of aluminum base alloys may be required.
A9. Chemical Analysis The accepted and most widely used method for chemical analysis is found in ASTM E227, Optical Emission Spectrometric Analysis of Aluminum and Alu- minum Alloy by the Point-to-Plane Technique. This method analyzes a bulk sample and all elements simulta- neously. The ASTM E34, Test Method for Chemical Analysis of Aluminum and Aluminum Alloy prescribes individual test methods for which each element is tested. The ASTM E34 test methods are used as a referee method if a dispute arises concerning a specific element analysis.