
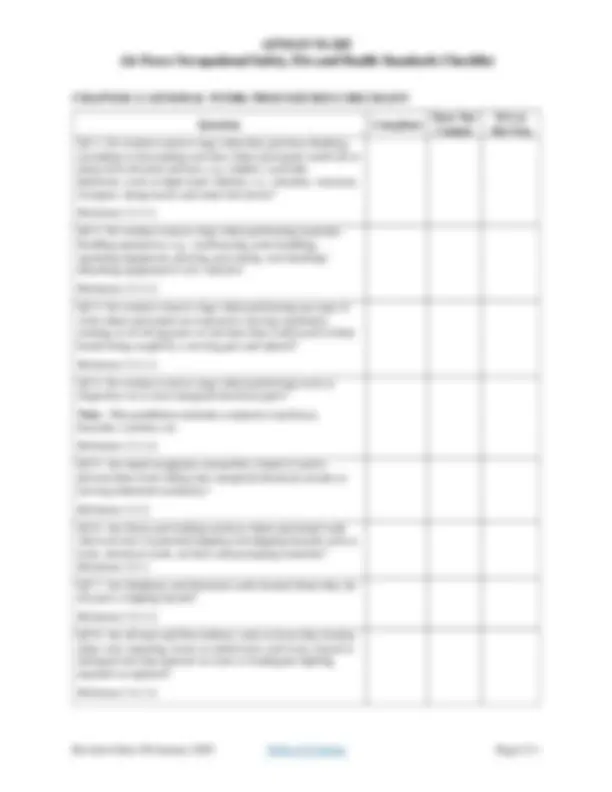
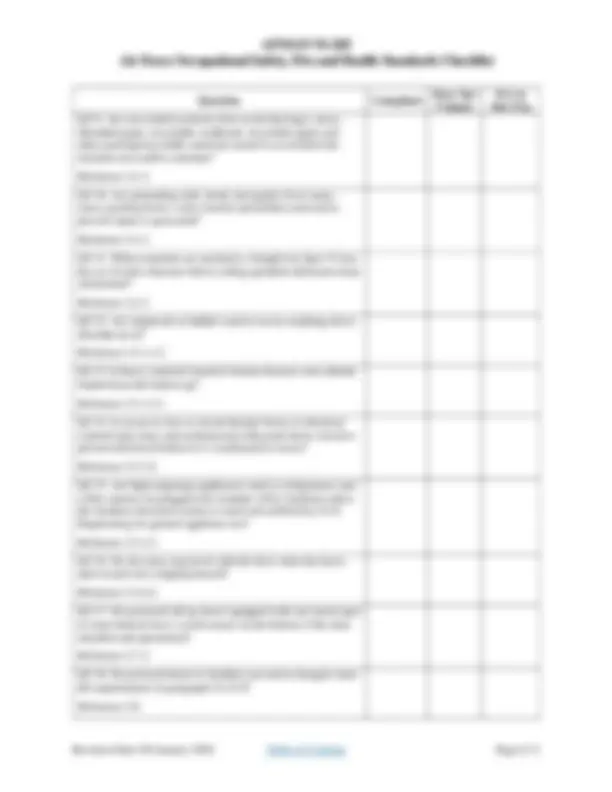
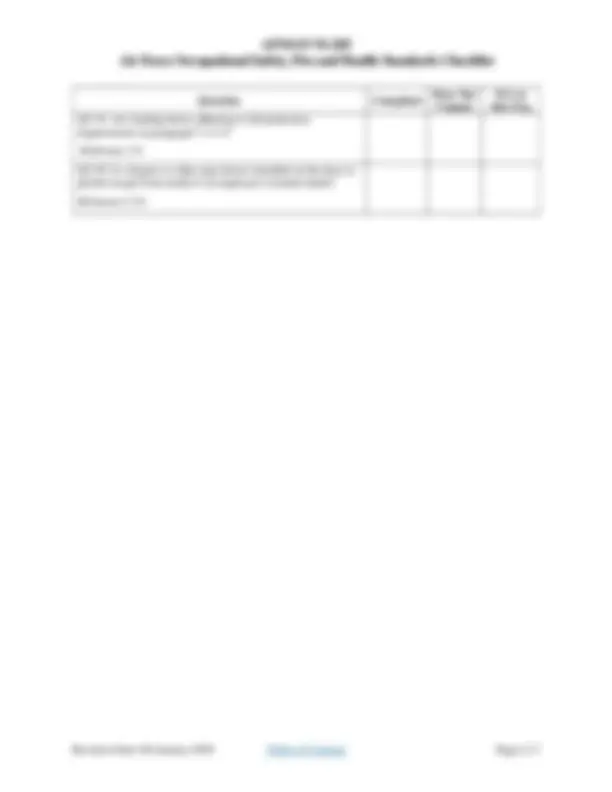

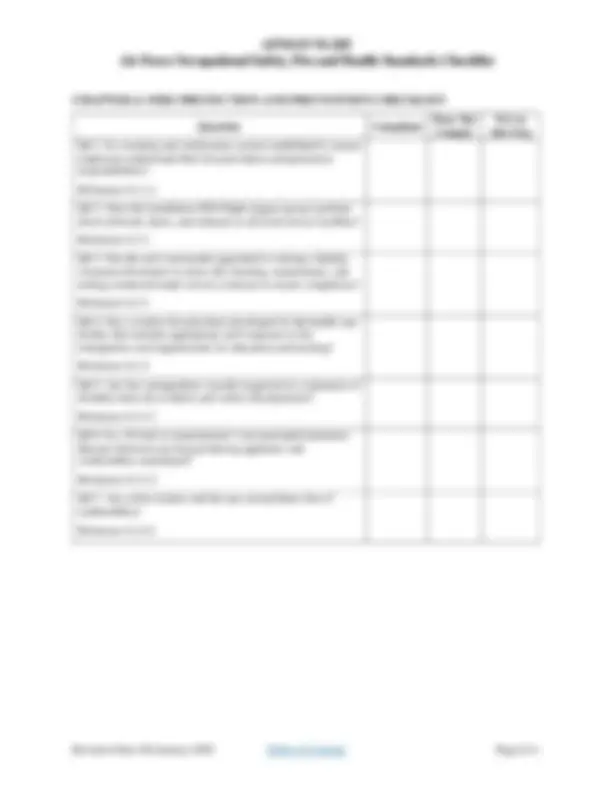
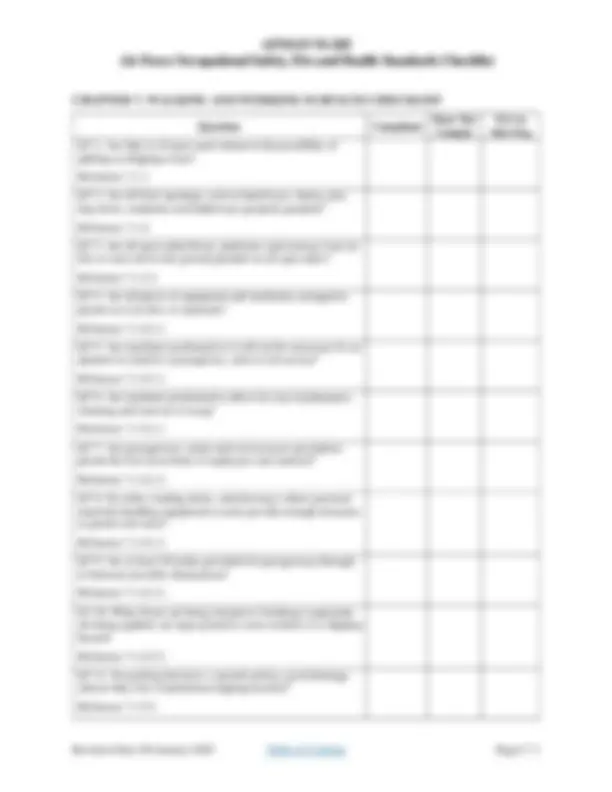
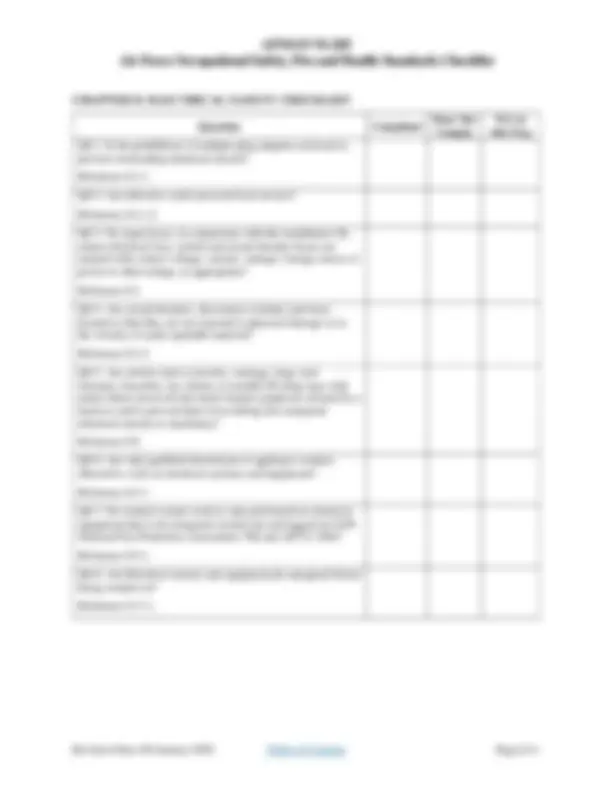
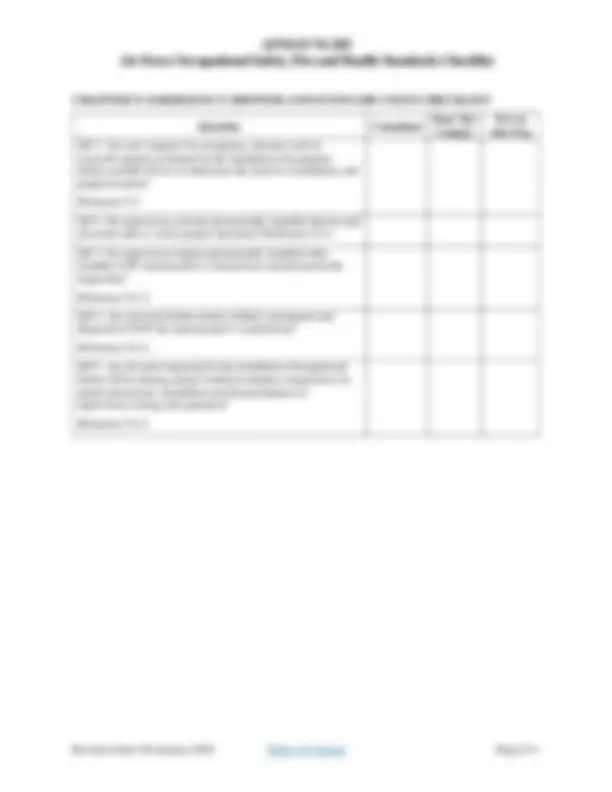
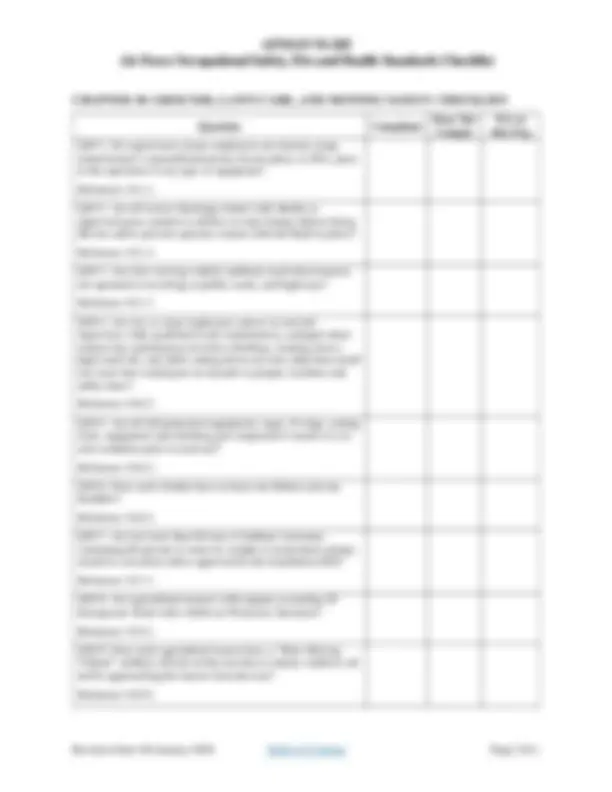
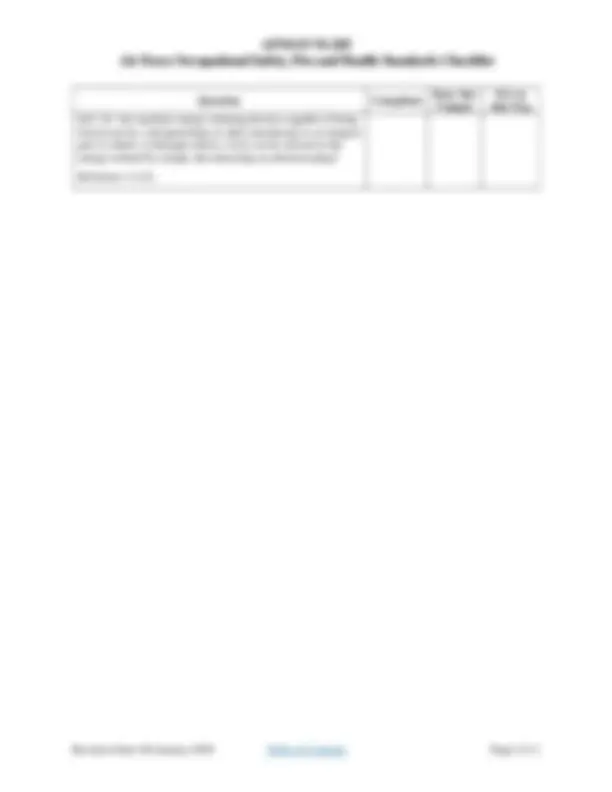
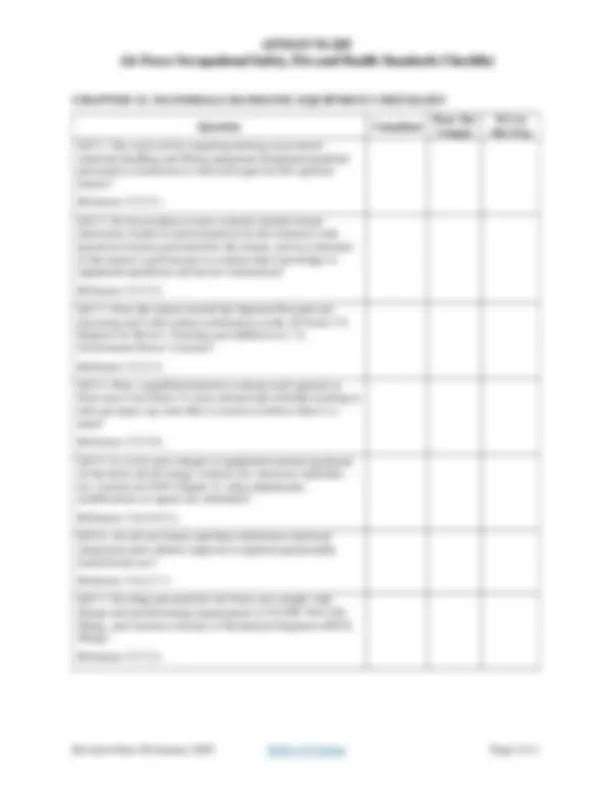
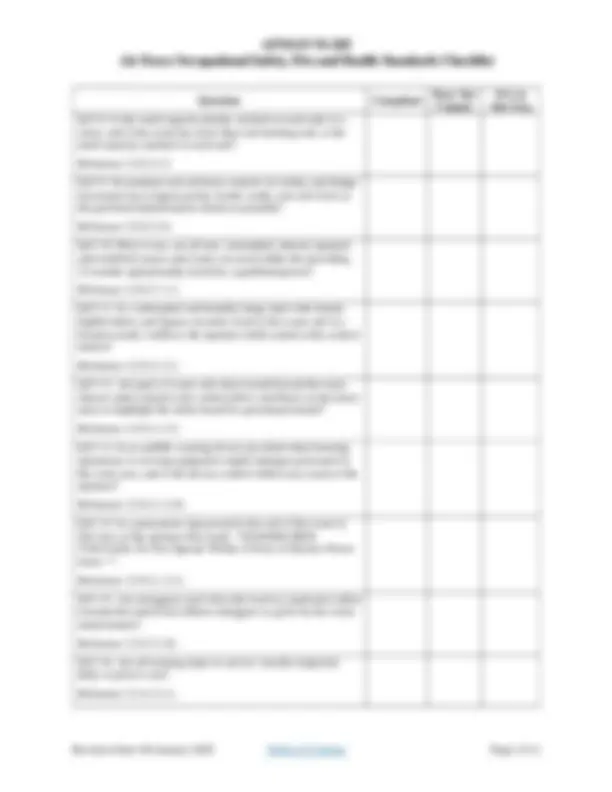
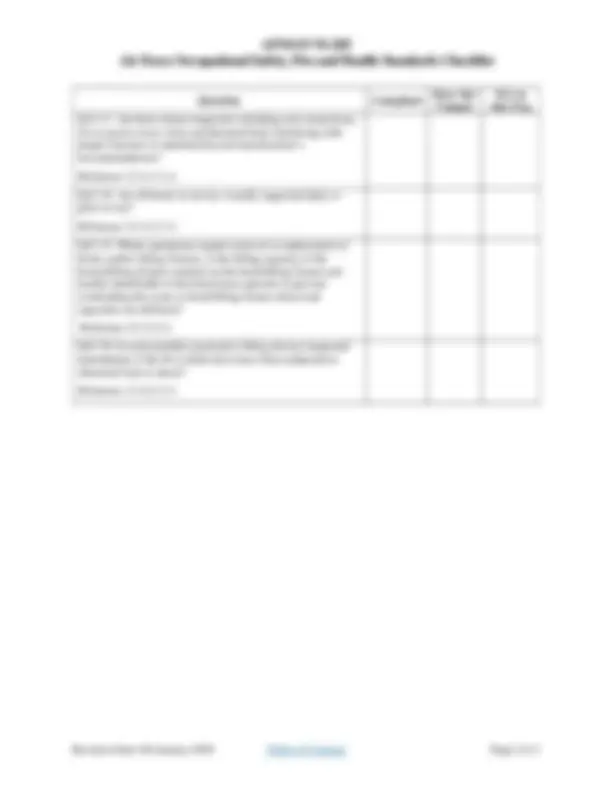
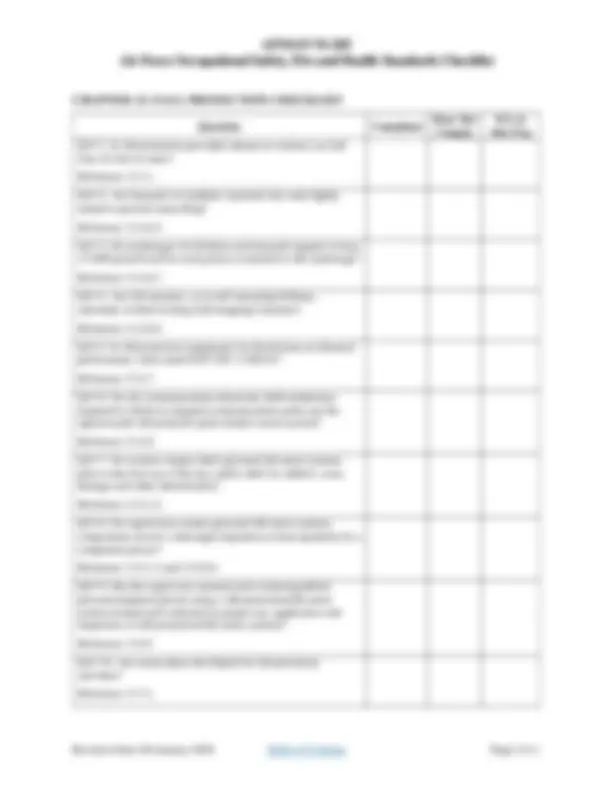
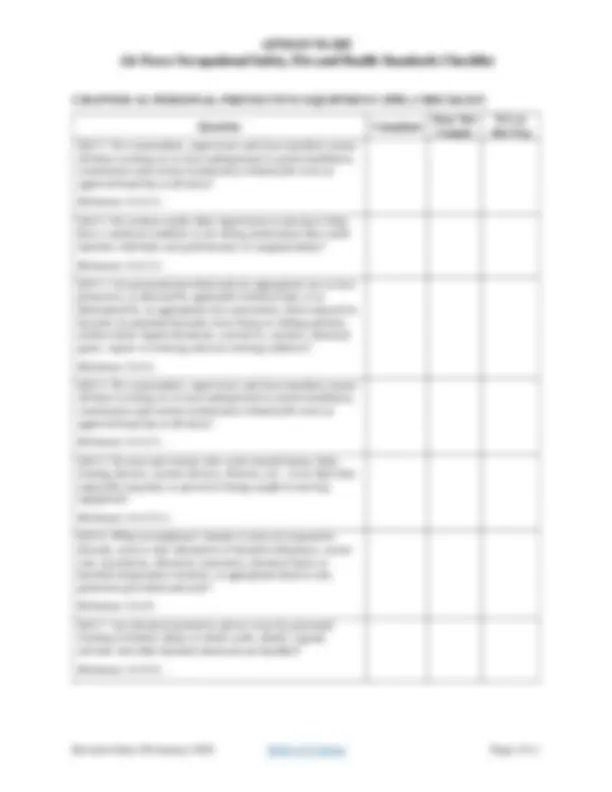
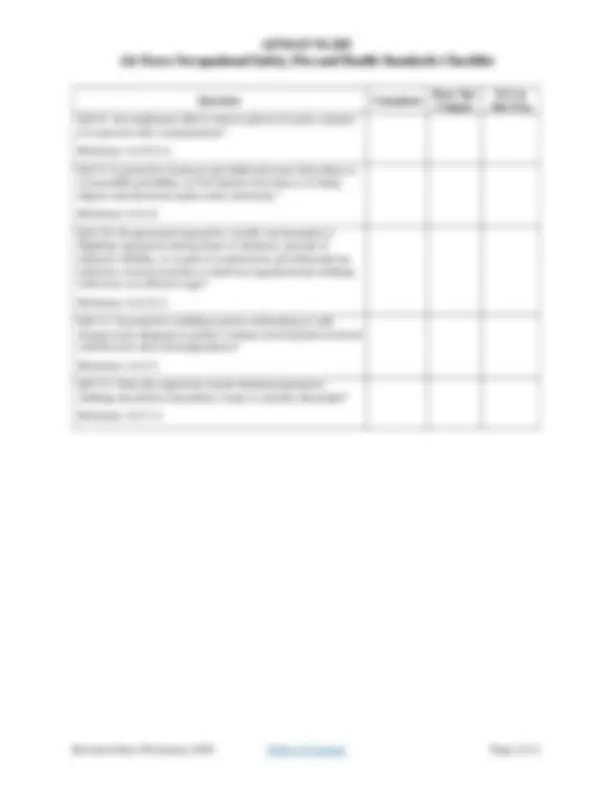
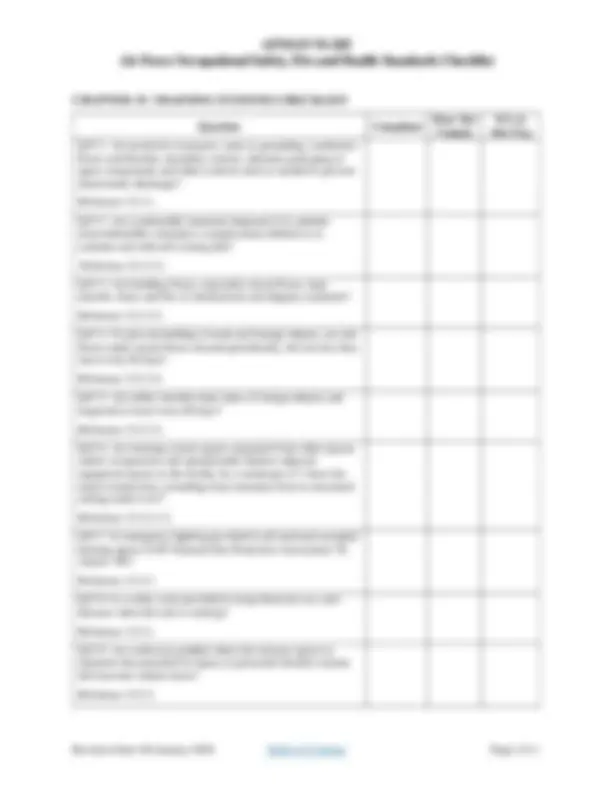
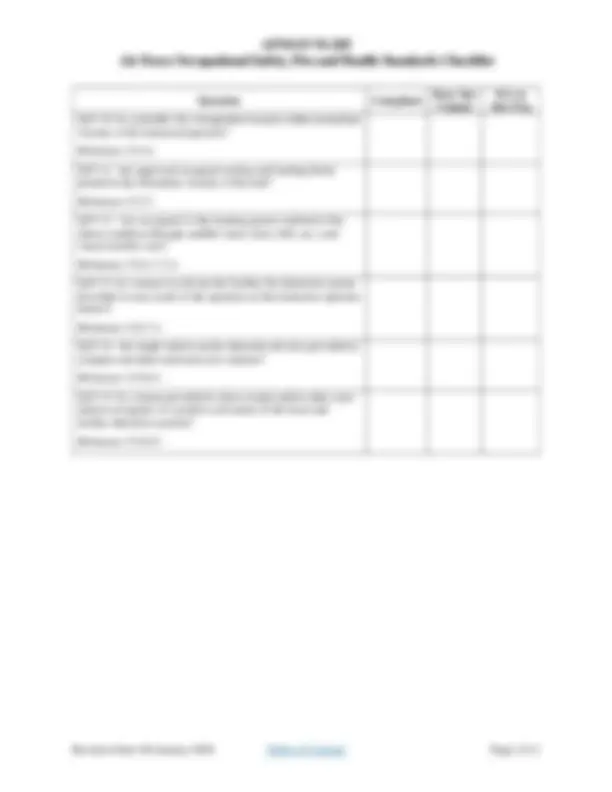
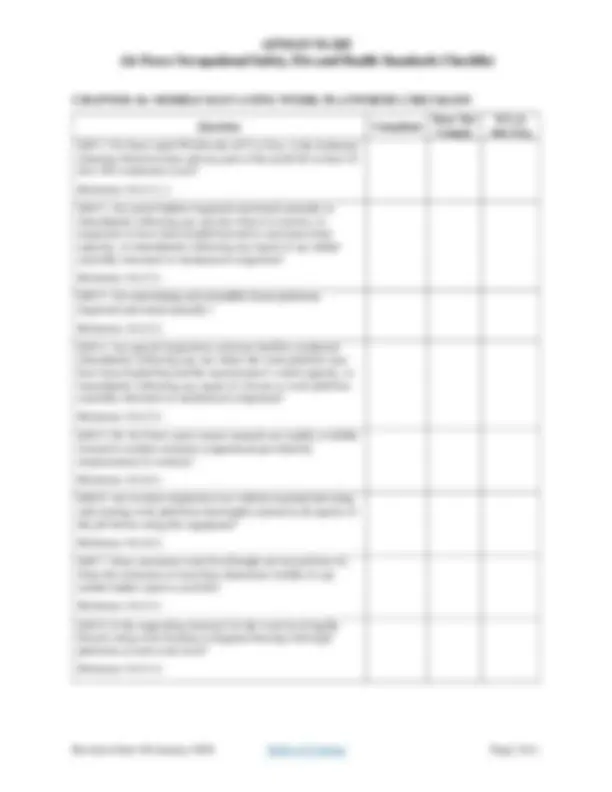
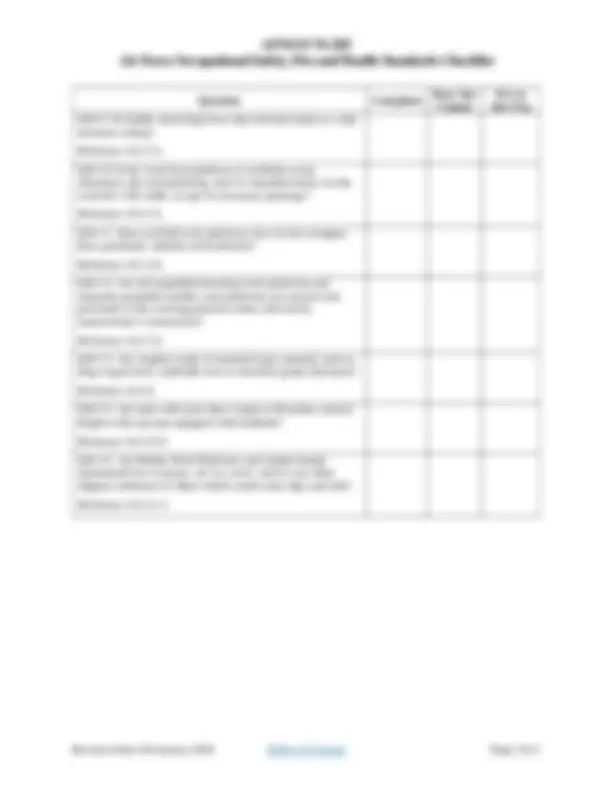
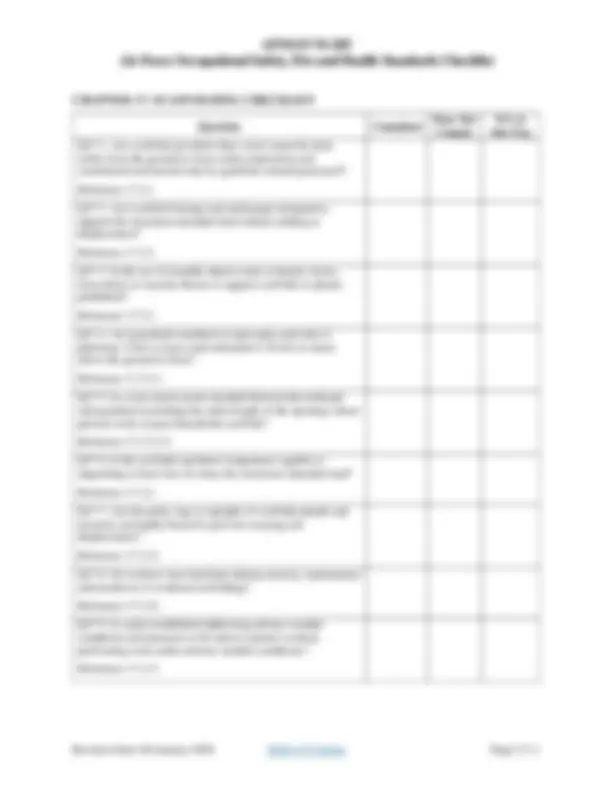
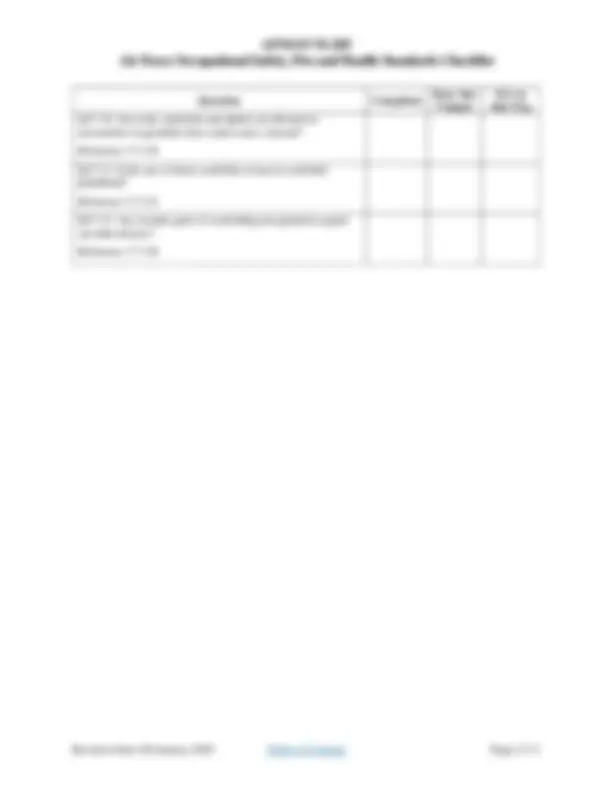
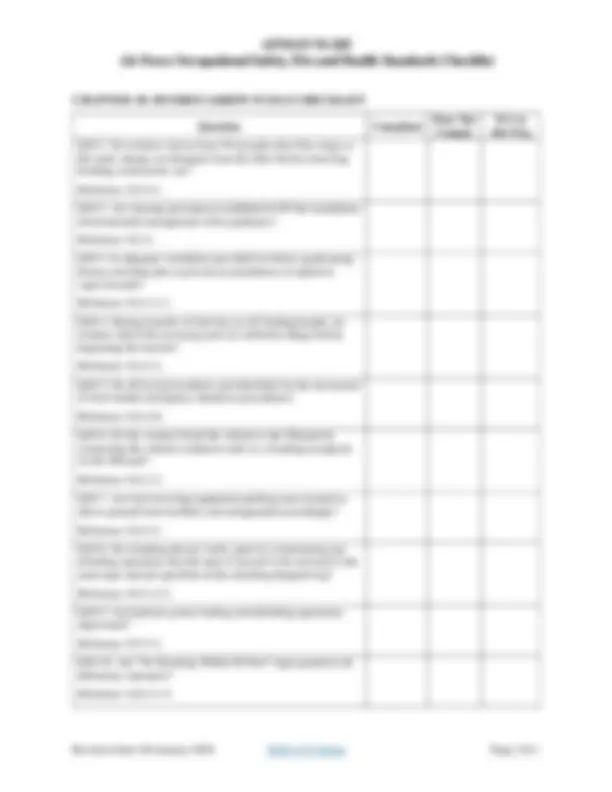
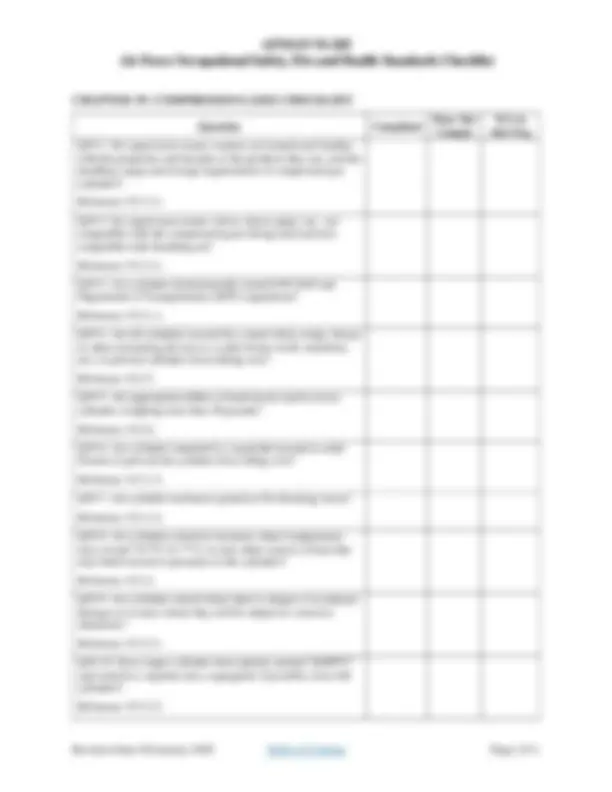
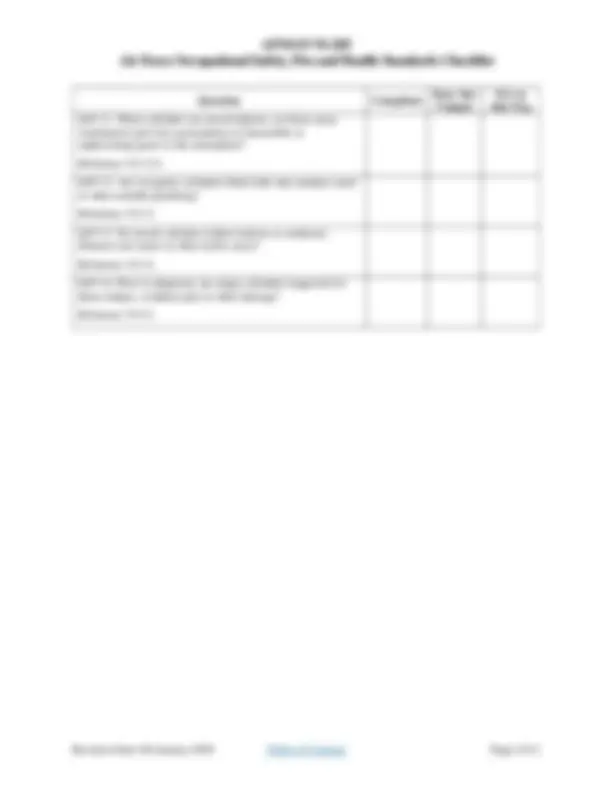
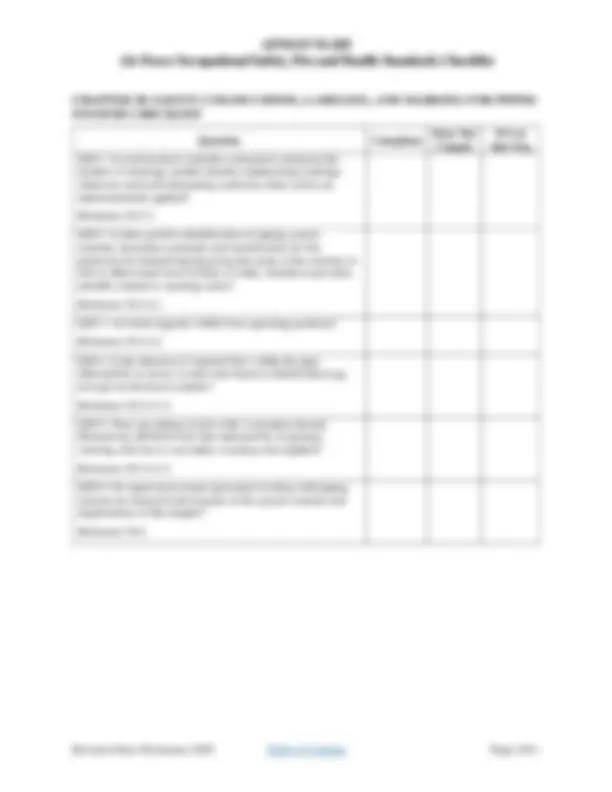
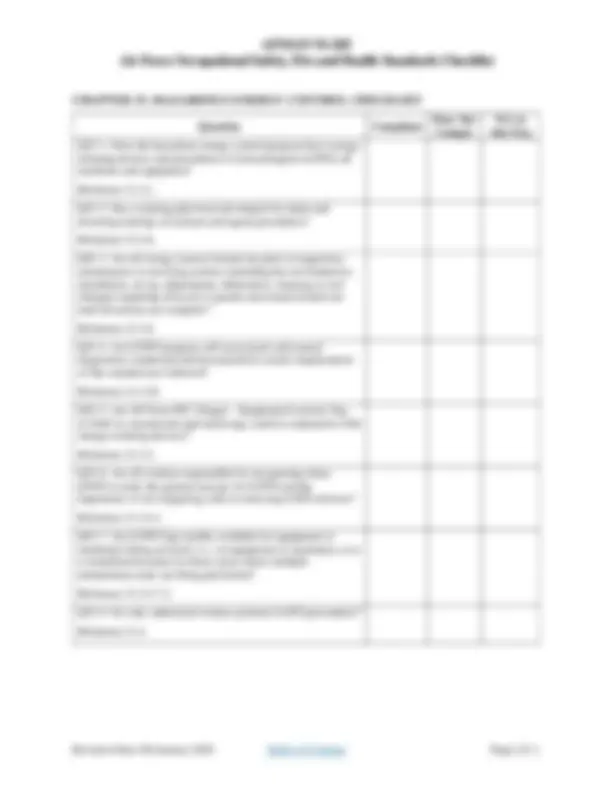
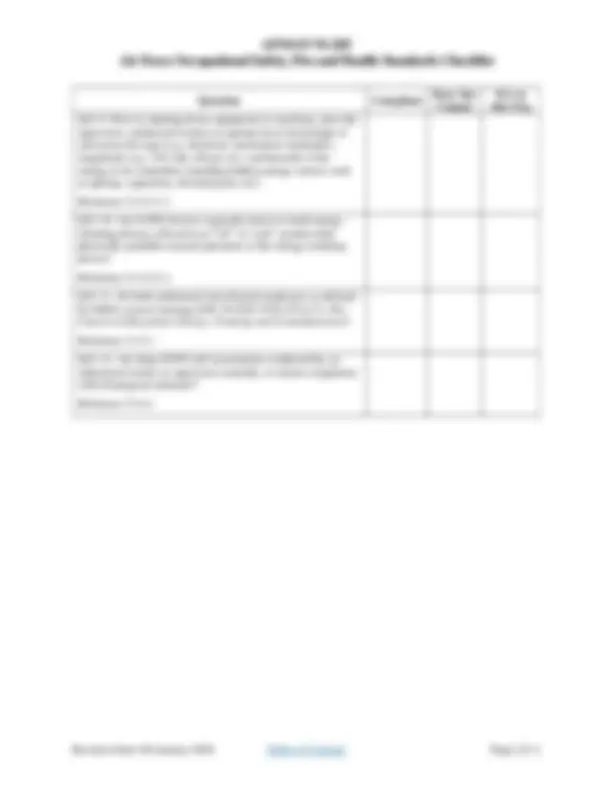
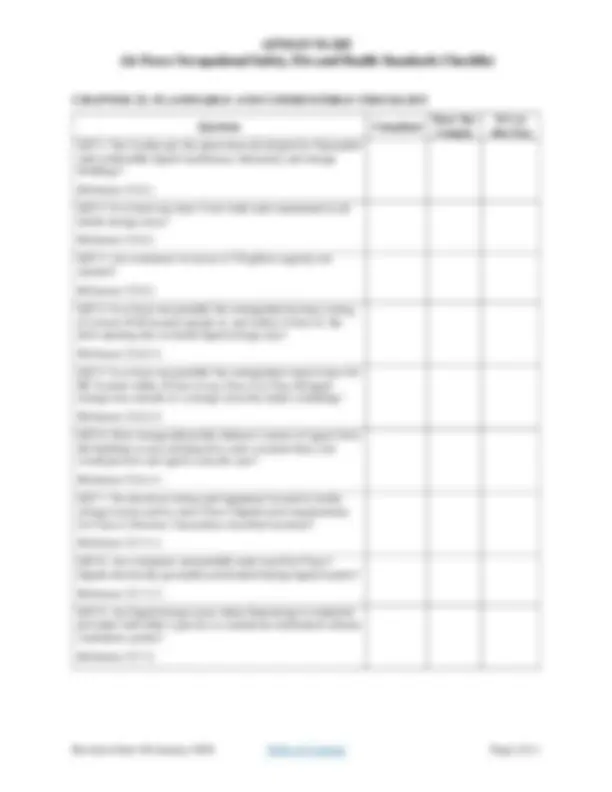
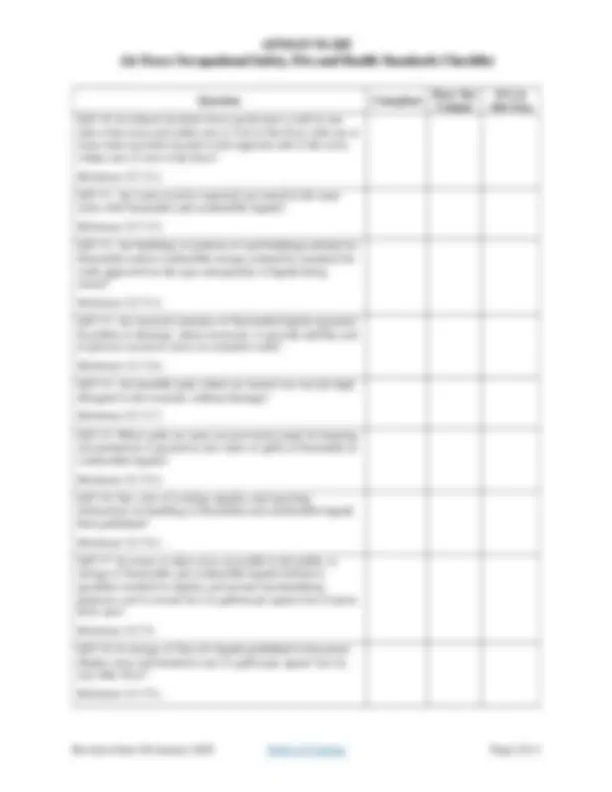
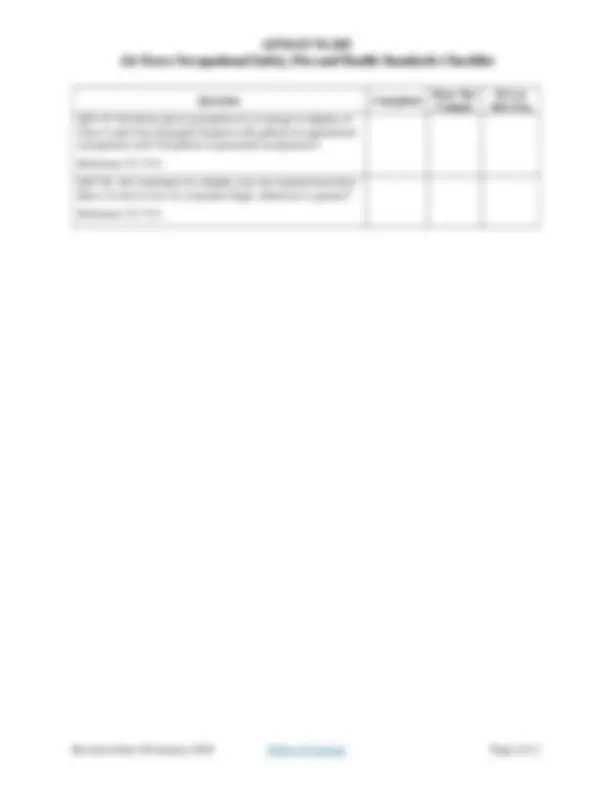
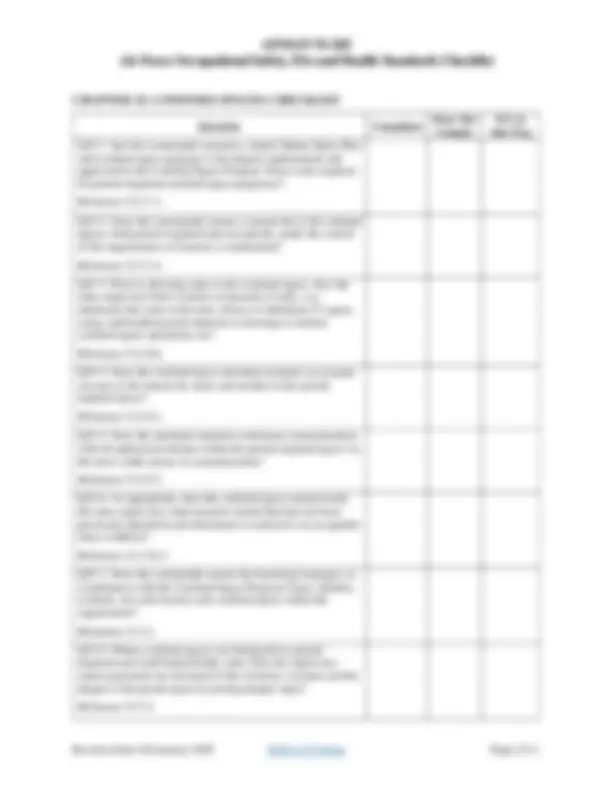
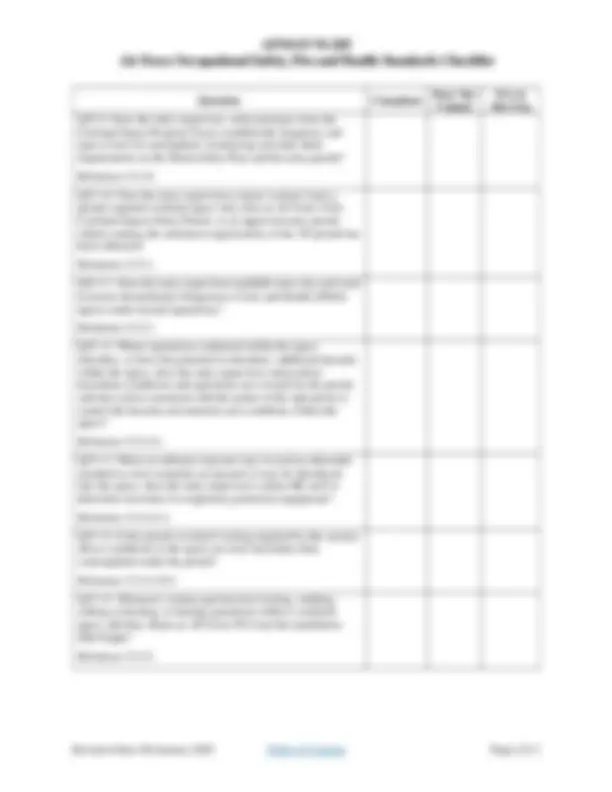
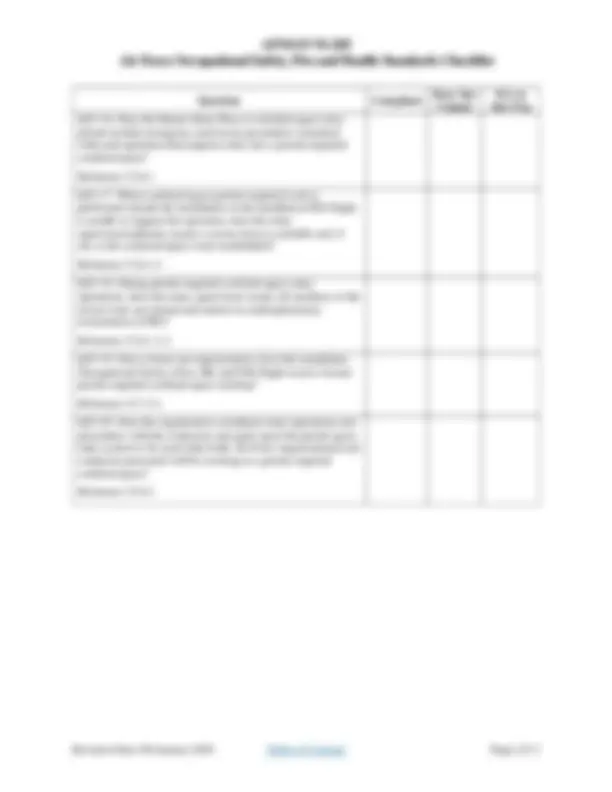
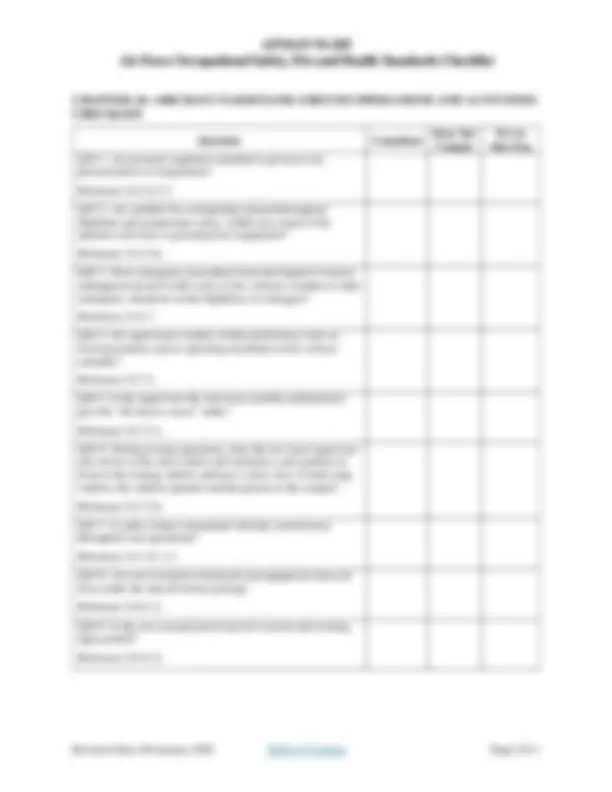
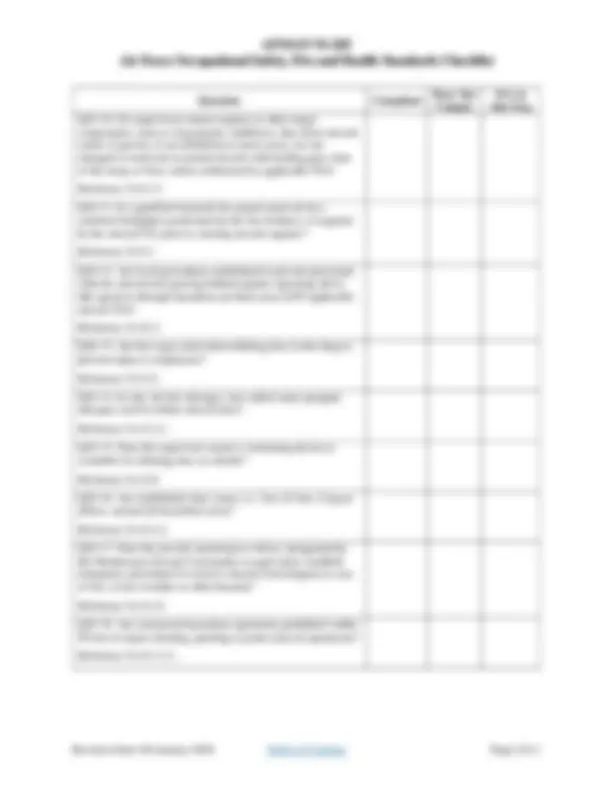
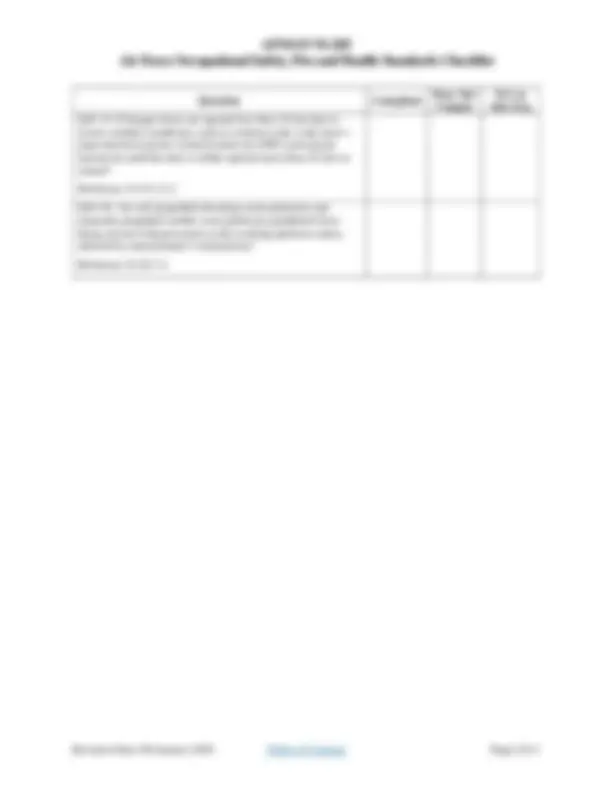
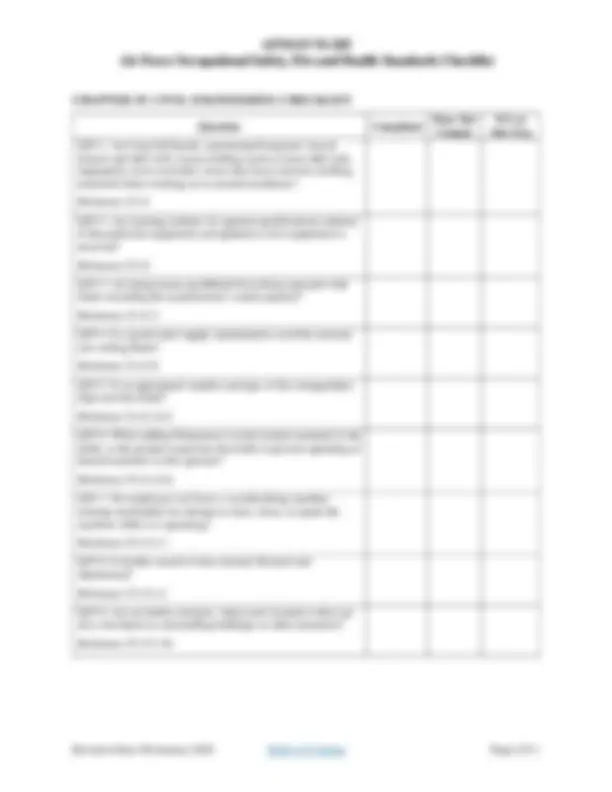
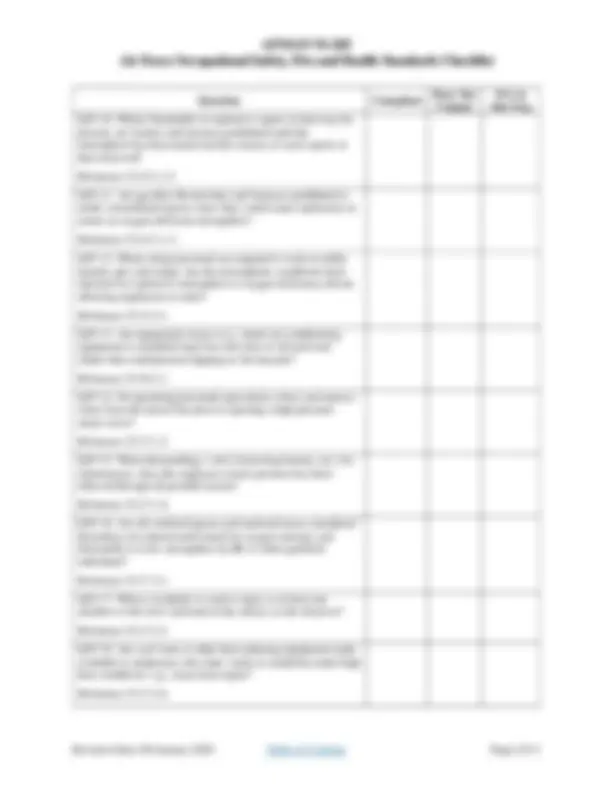
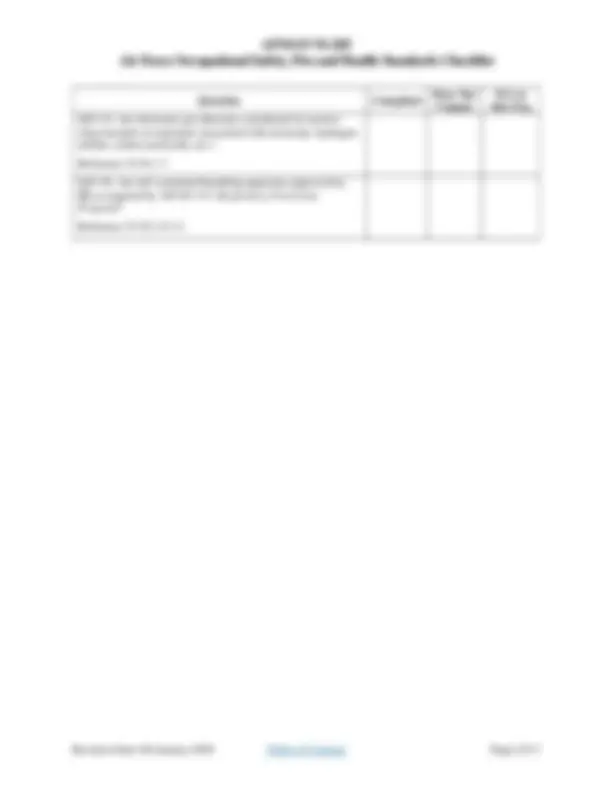
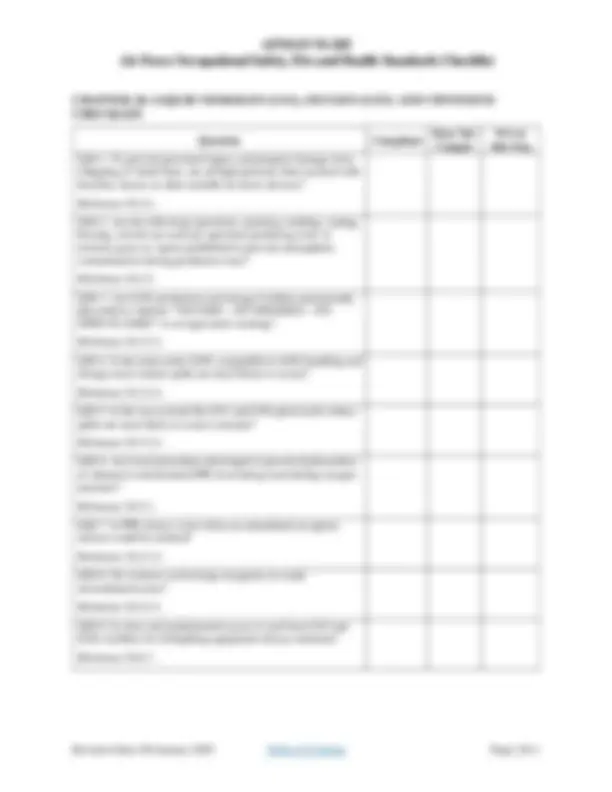
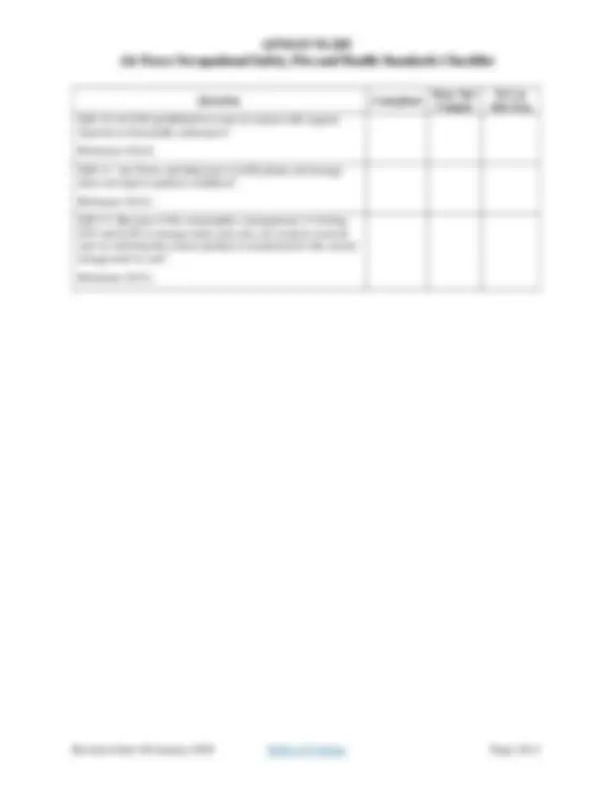
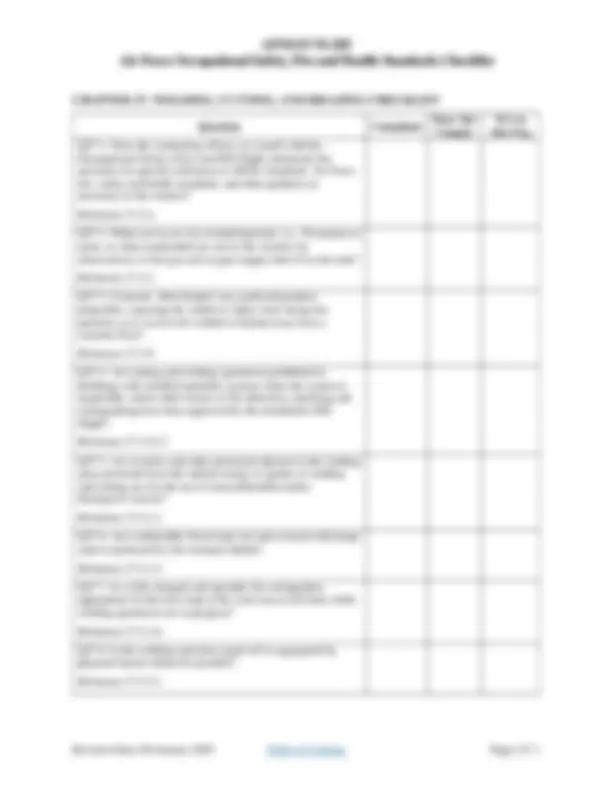
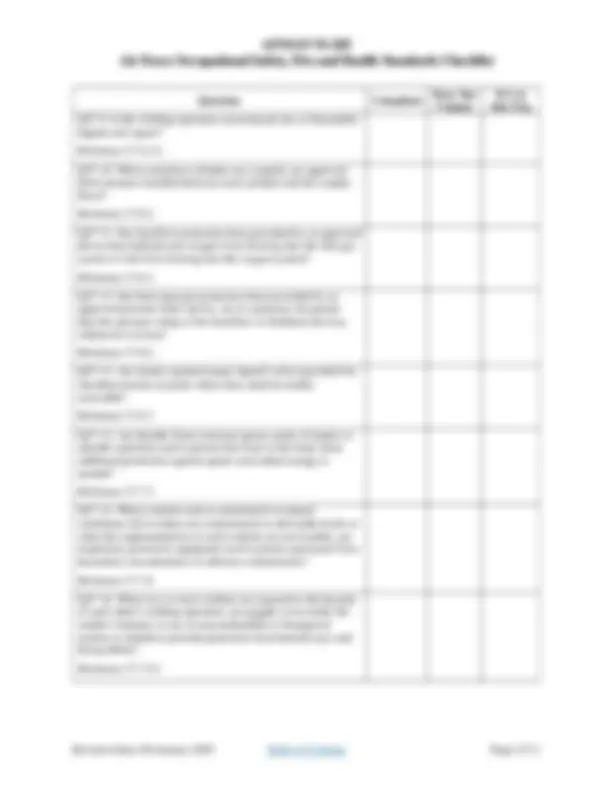
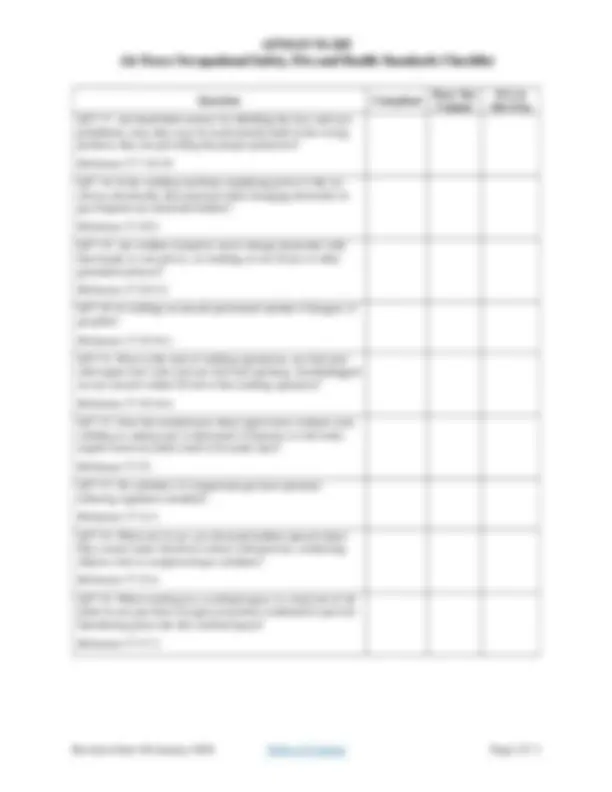
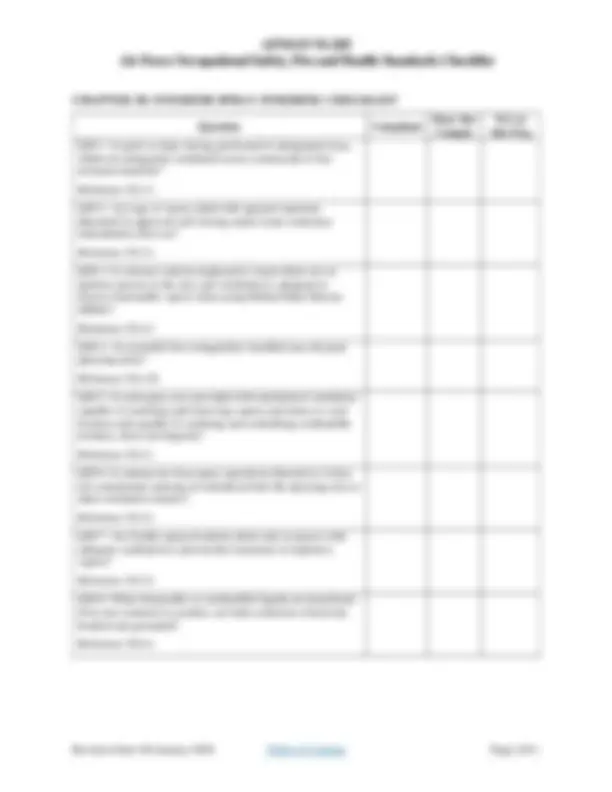
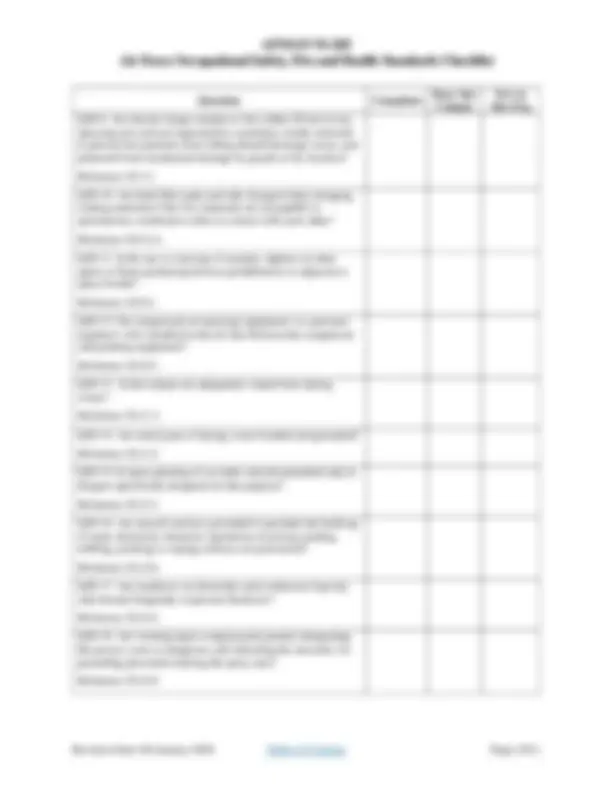
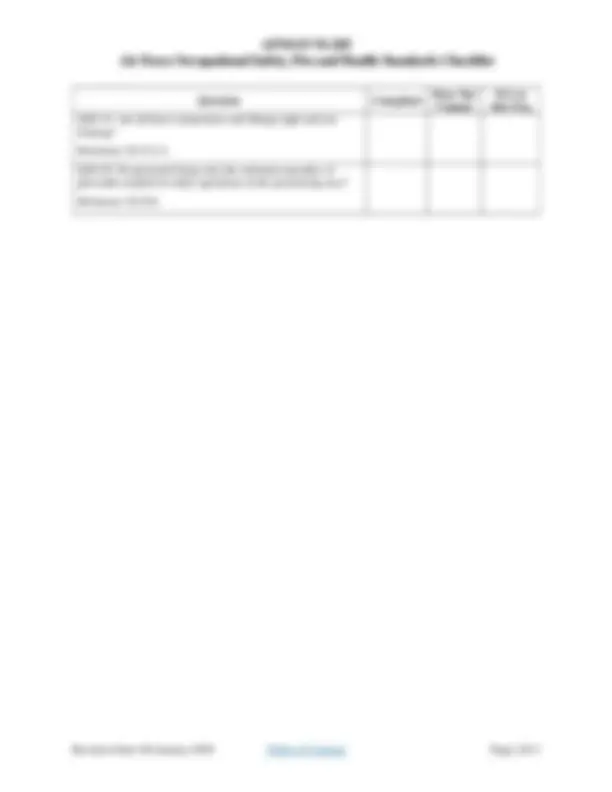

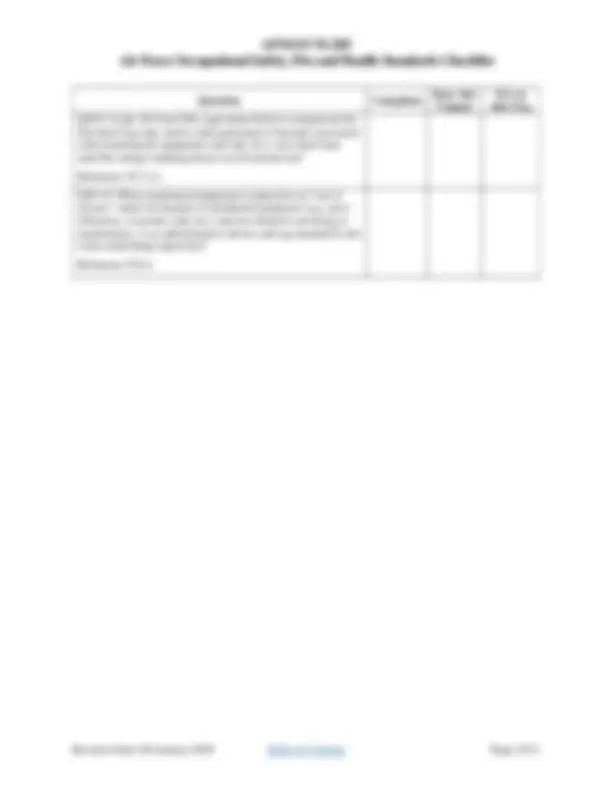
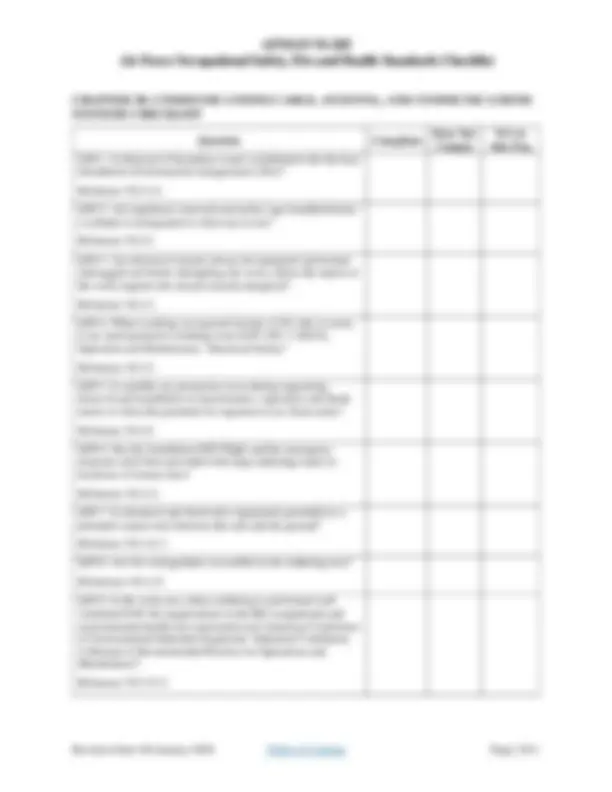
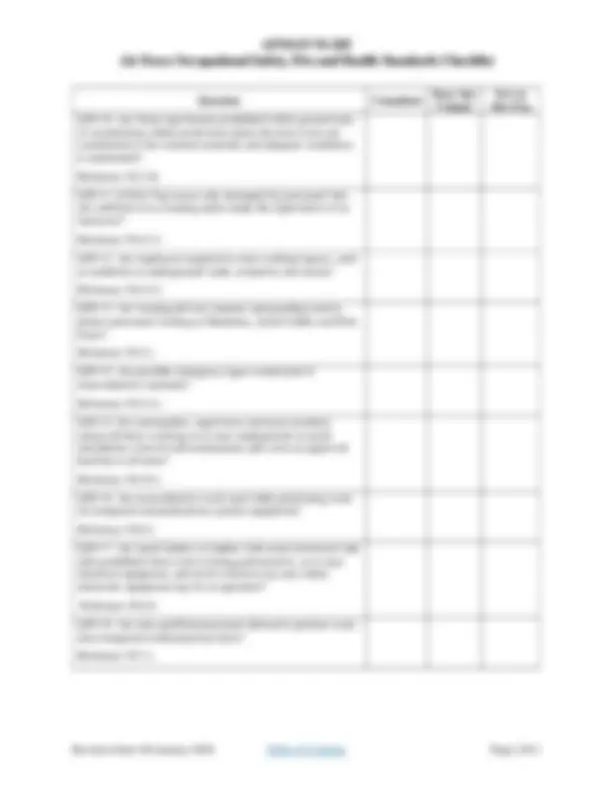
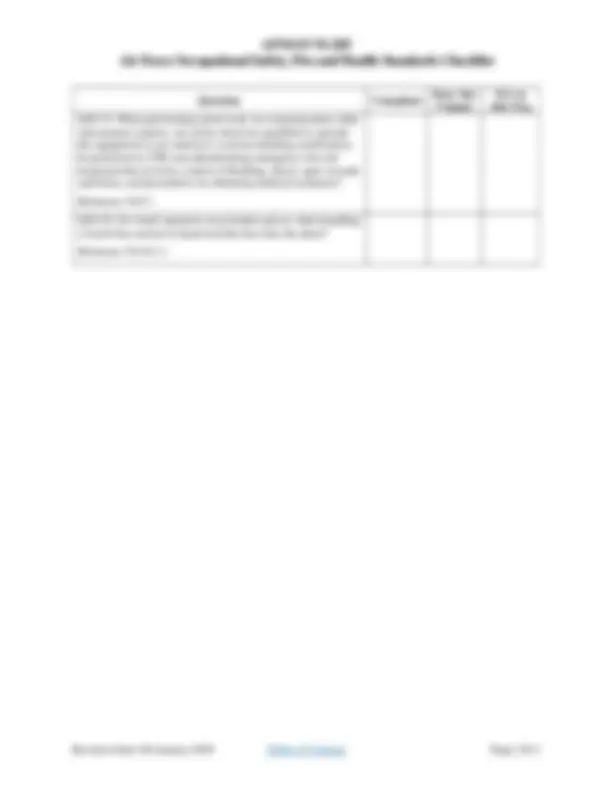
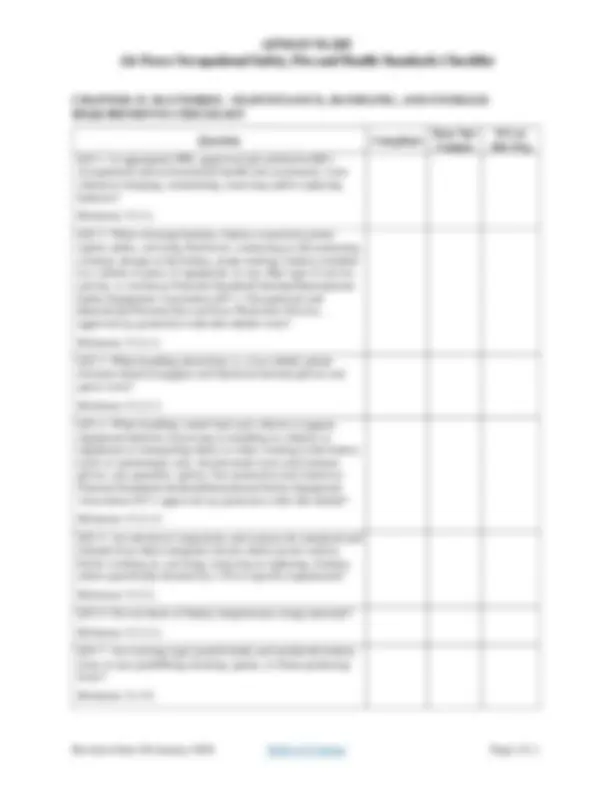
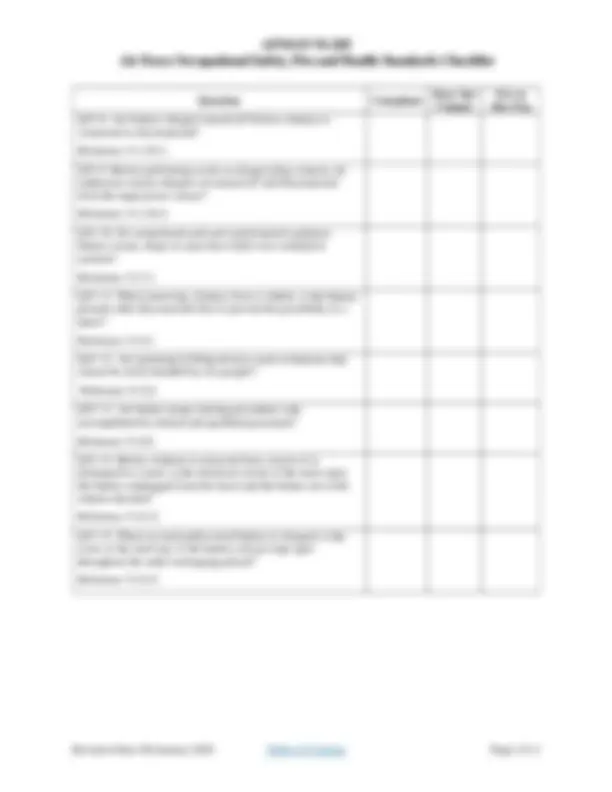
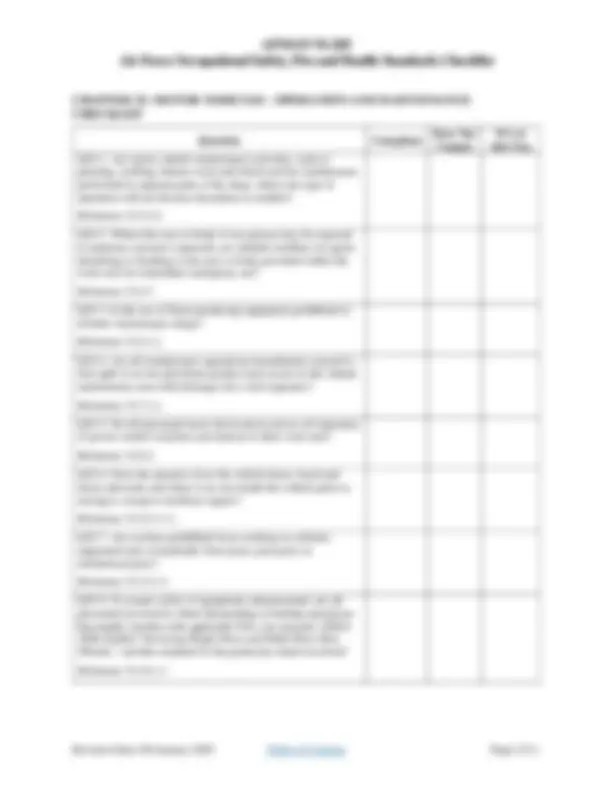
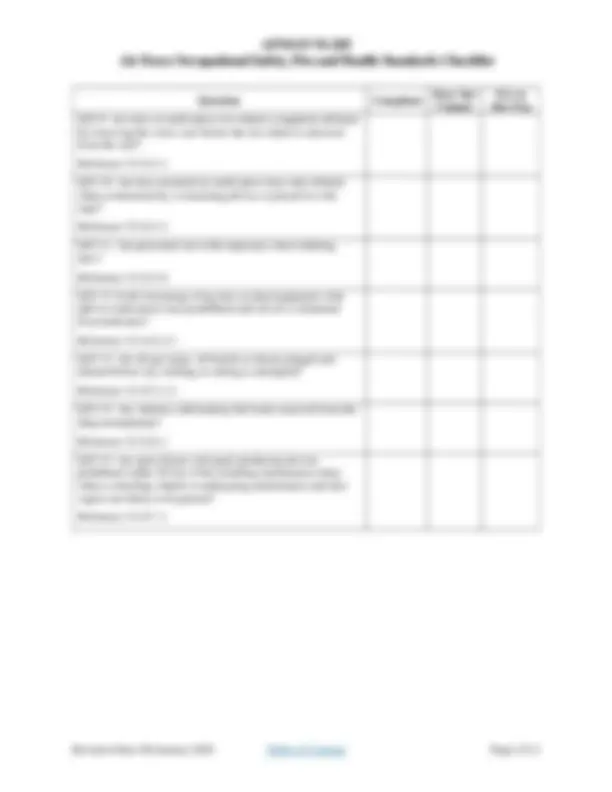
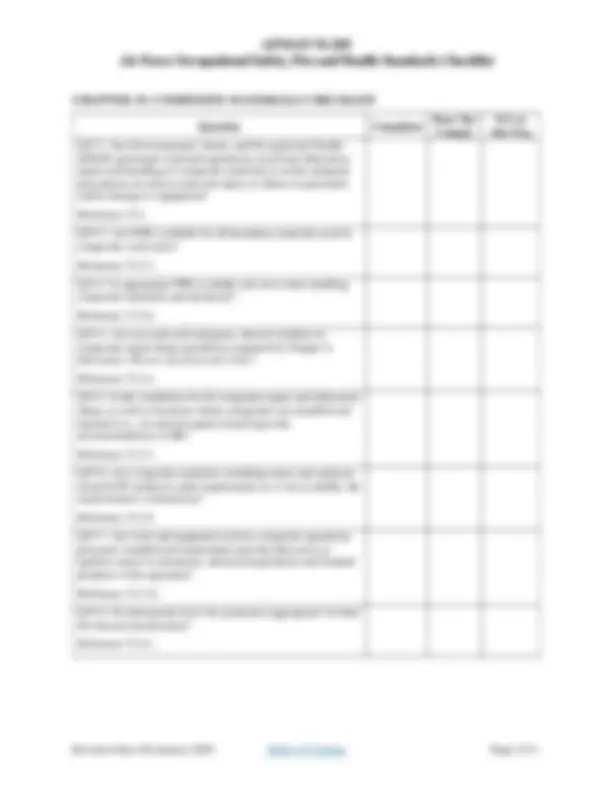
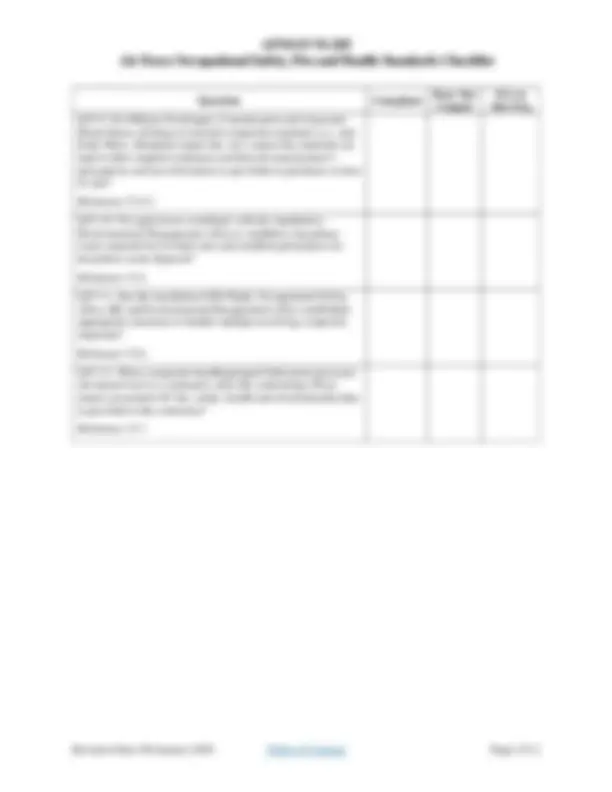
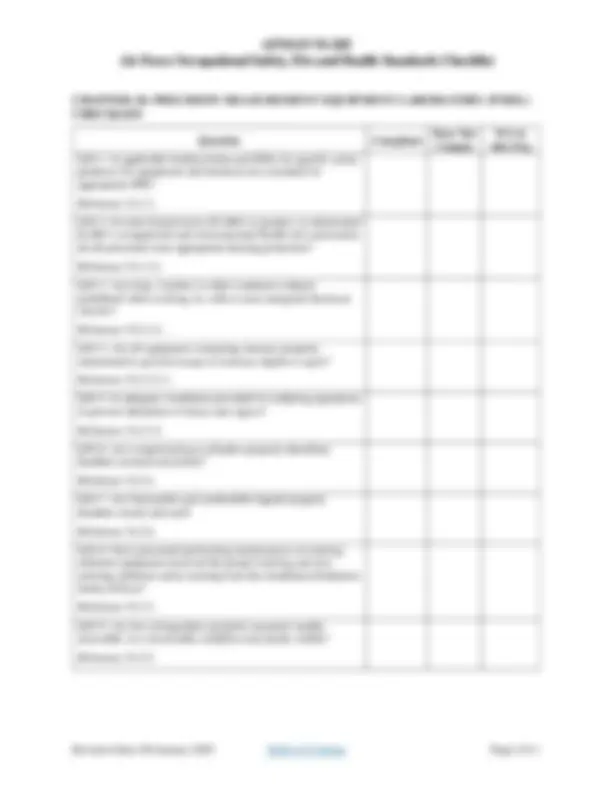
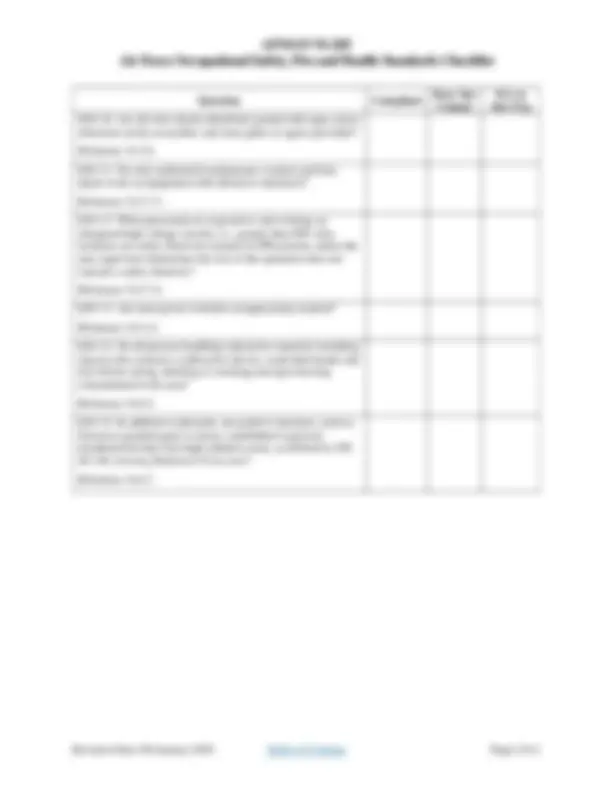
Study with the several resources on Docsity
Earn points by helping other students or get them with a premium plan
Prepare for your exams
Study with the several resources on Docsity
Earn points to download
Earn points by helping other students or get them with a premium plan
Community
Ask the community for help and clear up your study doubts
Discover the best universities in your country according to Docsity users
Free resources
Download our free guides on studying techniques, anxiety management strategies, and thesis advice from Docsity tutors
A checklist for safety and health requirements in NDI shops and equipment maintenance, including ventilation, electrical systems, fall protection, training, confined spaces, welding operations, and handling of hazardous materials. It refers to various guidelines and regulations such as UFC 4-024-01, ACGIH’s Industrial Ventilation, AFI 48-145, and OSHA standards.
What you will learn
Typology: Lecture notes
1 / 69
This page cannot be seen from the preview
Don't miss anything!
Revision Date: 08 January 2020 Page | i
The checklists contained herein is created by AFSEC/SEGS to assist Air Force personnel in meeting the requirements of AFMAN 91-203. Where appropriate, MAJCOMs, FOAs, DRUs, local safety offices and shop supervisors may download a copy of this checklist to add local or shop specific requirements. NOTE: Reference the checklist revision number to ensure you are using the most current.
Table of Contents .......................................................................................................................................... 1
CHAPTER 2: GENERAL WORK PROCEDURES CHECKLIST........................................................... 2-
CHAPTER 3: WEATHER SAFETY CHECKLIST .................................................................................. 3-
CHAPTER 4: SERVICES OPERATIONS CHECKLIST......................................................................... 4-
CHAPTER 5: NDI AND OIL ANALYSIS CHECKLIST ........................................................................ 5-
CHAPTER 6: FIRE PROTECTION AND PREVENTION CHECKLIST ............................................... 6-
CHAPTER 7: WALKING AND WORKING SURFACES CHECKLIST ............................................... 7-
CHAPTER 8: ELECTRICAL SAFETY CHECKLIST ............................................................................. 8-
CHAPTER 9: EMERGENCY SHOWER AND EYEWASH UNITS CHECKLIST ................................ 9-
CHAPTER 10: GROUNDS, LAWN CARE, AND MOWING SAFETY CHECKLIST ....................... 10-
CHAPTER 11: HAND TOOLS AND PORTABLE POWER TOOLS CHECKLIST ............................ 11-
CHAPTER 12: MATERIALS HANDLING EQUIPMENT CHECKLIST ............................................ 12-
CHAPTER 13: FALL PROTECTION CHECKLIST.............................................................................. 13-
CHAPTER 14: PERSONAL PROTECTIVE EQUIPMENT (PPE) CHECKLIST ................................. 14-
CHAPTER 15: TRAINING SYSTEMS CHECKLIST ........................................................................... 15-
CHAPTER 16: MOBILE ELEVATING WORK PLATFORMS CHECKLIST ..................................... 16-
CHAPTER 17: SCAFFOLDING CHECKLIST ...................................................................................... 17-
CHAPTER 18: HYDROCARBON FUELS CHECKLIST ..................................................................... 18-
CHAPTER 19: COMPRESSED GASES CHECKLIST ......................................................................... 19-
CHAPTER 20: SAFETY COLOR CODING, LABELING, AND MARKING FOR PIPING SYSTEMS CHECKLIST............................................................................................................................................ 20-
CHAPTER 21: HAZARDOUS ENERGY CONTROL CHECKLIST .................................................... 21-
CHAPTER 22: FLAMMABLE AND COMBUSTIBLE CHECKLIST.................................................. 22-
CHAPTER 23: CONFINED SPACES CHECKLIST ............................................................................. 23-
CHAPTER 24: AIRCRAFT FLIGHTLINE GROUND OPERATIONS AND ACTIVITIES CHECKLIST ................................................................................................................................................................. 24-
CHAPTER 25: CIVIL ENGINEERING CHECKLIST........................................................................... 25-
CHAPTER 26: LIQUID NITROGEN (LN2), OXYGEN (LOX) AND CRYOGENS CHECKLIST .... 26-
CHAPTER 27: WELDING, CUTTING, AND BRAZING CHECKLIST .............................................. 27-
Revision Date: 08 January 2020 Page | ii
Question Compliant Does NotComply this Org^ N/A to
Q2-9. Are non-soiled excelsior (fine wood shavings), straw, shredded paper, recyclable cardboard, recyclable paper and other packing/recyclable materials stored in an isolated fire- resistant area and/or container?
Reference 2.4.3.
Q2-10. Are protruding nails, brads and staples from crates, cases, packing boxes, casks, boards and lumber removed to prevent injury to personnel?
Reference 2.4.3.
Q2-11. When materials are stacked to a height less than 15 feet, has an 18-inch clearance below ceiling sprinkler deflectors been maintained?
Reference 2.4.5.
Q2-12. Are stepstools or ladders used to access anything above shoulder level?
Reference 2.5.1.1.2.
Q2-13. Is heavy material stored in bottom drawers and cabinets loaded from the bottom up?
Reference 2.5.1.2.1.
Q2-14. Is access to fuse or circuit breaker boxes or electrical controls kept clear and unobstructed with panel doors closed to prevent electrical flashover if a malfunction occurs?
Reference 2.5.2.2.
Q2-15. Are high amperage appliances such as refrigerators and coffee makers not plugged into modular office furniture unless the furniture electrical system is rated and certified by Civil Engineering for general appliance use?
Reference 2.5.2.3.
Q2-16. Do elevators stop level with the floor when the doors open to prevent a tripping hazard?
Reference 2.5.6.2.
Q2-17. Do powered roll-up doors equipped with one touch open or close buttons have a crush sensor on the bottom of the door installed and operational?
Reference 2.7.2.
Q2-18. Do powered doors in facilities not used as hangers meet the requirements in paragraph 24.14.8?
Reference 2.8.
Question Compliant Does NotComply this Org^ N/A to
Q2-19. Are loading docks adhering to fall protection requirements in paragraph 7.1.5.4?
Reference 2.9.
Q2-20. Is a bypass or other type device installed on the door to permit escape from inside if an employee is locked inside?
Reference 2.10.
Question Compliant
Does Not Comply
N/A to this Org Q4-1. Is machinery producing potentially hazardous noise/vibration levels identified and control measure initiated IAW BE’s occupational and environmental health risk assessment guidance? Reference 4.2.4.
Q4-2. Are hazardous and flammable materials stored IAW Chapter 22 requirements? Reference 4.2.5. Q4-3. Are floors in dry cleaning rooms fire resistant and covered with solvent resistant materials? Reference 4.2.6.
Q4-4. Is grease cleaned from burners and ranges as needed to prevent fires? Reference 4.3.2.1. Q4-5. Do workers unplug heat producing appliances such as irons and coffee makers when cleaning or not in use? Reference 4.3.2.2. Q4-6. Are microwave ovens cleaned daily? Reference 4.3.2.3. Q4-7. Are broken microwave doors removed from service so personnel will not be exposed to microwave energy exposure? Reference 4.3.2.3.
Q4-8. Are all movable parts on equipment properly guarded? Reference 4.4.2.2. Q4-9. Are knives and cutting attachments safeguarded when not in use? Reference 4.4.2.3. Q4-10. Are hood filters over grease vapor producing activities washed at least daily? Reference 4.4.2.4.
Question Compliant
Does Not Comply
N/A to this Org Q5-1. Is TO 33B- 1 - 1, Nondestructive Inspection Methods, Basic Theory, used when conducting NDI analysis? Reference 5.1.1. Q5-2. Are surface area exhaust ventilation evaluations conducted at least annually? Reference 5.2.6.1. Q5-3. Do areas that may require an evaluation for adequate ventilation include cleaning areas, penetrant tanks, remover tanks, penetrant inspection viewing booths, stationary magnetic particle units, film processing rooms and the oil analysis program work area meet requirements of UFC 4-024-01, ACGIH’s Industrial Ventilation: A Manual of Recommended Practice for Operations and Maintenance, and AFI 48-145, Occupational and Environmental Health Program? Reference 5.2.6.2. Q5-4. Are waste cleaning rags and towels removed from the lab at the end of each shift? Reference 5.3.2.
Q5-5. Does the NDI shop contact the installation FES Flight prior to operating equipment which utilizes black lights, X-rays, ultraviolet and/or infrared rays? Reference 5.4.
Question Compliant
Does Not Comply
N/A to this Org Q7-1. Are drip or oil pans used whenever the possibility of spilling or dripping exists? Reference 7.1.1. Q7-2. Are all floor openings, such as hatchways, chutes, pits, trap doors, manholes and ladderways properly guarded? Reference 7.1.4. Q7-3. Are all open-sided floors, platforms and runways four (4) feet or more above the ground guarded on all open sides? Reference 7.1.5.3. Q7-4. Are all pieces of equipment and machinery arranged to permit an even flow of materials? Reference 7.1.8.1.1. Q7-5. Are machines positioned so it will not be necessary for an operator to stand in a passageway, aisle or exit access? Reference 7.1.8.1.1. Q7-6. Are machines positioned to allow for easy maintenance, cleaning and removal of scrap? Reference 7.1.8.1.1.
Q7-7. Are passageways, aisles and exit accesses provided to permit the free movement of employees and material? Reference 7.1.8.1.2. Q7-8. Do aisles, loading docks, and doorways where powered materials handling equipment is used, provide enough clearance to permit safe turns? Reference 7.1.8.1.3. Q7-9. Are at least 18 inches provided for passageways through or between movable obstructions? Reference 7.1.8.1.4.
Q7-10. When floors are being cleaned or finishing compounds are being applied, are signs posted to warn workers of a slipping hazard? Reference 7.1.8.2.3. Q7-11. Do parking lots have a smooth surface, good drainage and are they free of pedestrian tripping hazards? Reference 7.1.9.1.
Question Compliant Does NotComply this Org^ N/A to
Q7-12. Are entrances and exits free of obstructions that block a driver’s or pedestrian’s view of traffic?
Reference 7.1.9.1.
Q7-13. Do workers ensure materials are not stored, left under or piled against buildings, doors, exits or stairways?
Reference 7.1.9.3.1.
Q7-14. Are poisonous or toxic plants prohibited for landscaping unless approved by the installation medical services?
Reference 7.1.9.3.2.
Q7-15. Are trees and bushes adjacent to walkways trimmed to permit a clear path for pedestrians?
Reference 7.1.9.3.2.
Q7-16. Is all construction work clearly identified by signs that can be read from at least 50 feet, in addition to barriers marked with reflective materials?
Reference 7.1.9.4.
Q7-17. Are fixed stairs and ramps designed and built to carry a load of 5 times the normal live load anticipated, but not less than a 1,000 pound moving concentrated load?
Reference 7.2.2.
Q7-18. Are fixed stairs (not part of the exit access) installed at angles to the horizontal of 30 to 50 degrees?
Reference 7.2.4.
Q7-19. When the doors or gates open directly onto a stairway, is the available width of the landing not less than 20 inches?
Reference 7.2.6.
Q7-20. Is every flight of fixed industrial stairs with four (4) or more risers equipped with standard guardrails or standard handrails?
Reference 7.2.11.
Q7-21. Are slippery surfaces replaced or made safe by coating them with nonslip surface materials?
Reference 7.2.14.3.
Q7-22. Is adequate illumination provided when using ladders?
Reference 7.3.1.5.
Question Compliant
Does Not Comply
N/A to this Org Q8-1. Is the prohibition of multiple plug adapters enforced to prevent overloading electrical circuits? Reference 8.2.1. Q8-2. Are defective cords removed from service? Reference 8.4.1.2. Q8-3. Do supervisors, in conjunction with the installation CE, ensure electrical fuse, switch and circuit-breaker boxes are marked with correct voltage, current, wattage, foreign source of power or other ratings, as appropriate? Reference 8.5. Q8-4. Are circuit breakers, disconnect switches and fuses located so that they are not exposed to physical damage or in the vicinity of easily ignitable material? Reference 8.5.2. Q8-5. Are articles such as jewelry, earrings, rings, hair fasteners, bracelets, key chains or metallic ID (dog) tags with metal chains removed and metal framed eyeglasses secured by a band or cord to prevent them from falling into energized electrical circuits or machinery? Reference 8.8. Q8-6. Are only qualified electricians or appliance workers allowed to work on electrical systems and equipment? Reference 8.9.1. Q8-7. Do workers ensure work is only performed on electrical equipment that is de-energized, locked out and tagged out IAW National Fire Protection Association 70E and AFI 32-1064? Reference 8.9.1. Q8-8. Are Electrical circuits and equipment de-energized before being worked on? Reference 8.17.1.
Question Compliant
Does Not Comply
N/A to this Org Q9-1. Are new requests for emergency showers and /or eyewash stations evaluated by the installation Occupation Safety and BE offices to determine the need for installation and proper location? Reference 9.3.
Q9-2. Do supervisors activate permanently installed shower and eyewash units to verify proper operation? Reference 9.4.1.
Q9-3. Do supervisors inspect permanently installed units monthly IAW manufacturer’s instructions and document the inspection? Reference 9.4.2. Q9-4. Are eyewash bottles tested, refilled, maintained and disposed of IAW the manufacturer’s instructions? Reference 9.4.4. Q9-5. Are all units inspected by the installation Occupational Safety Office during annual facility/workplace inspections for proper placement, installation and documentation of supervisory testing and operation? Reference 9.4.5.
Question Compliant Does NotComply this Org^ N/A to
Q10-10. Are sickle-bar mower blades positioned on the high side of the slope so the pull of gravity will not cause the tractor to turn over?
Reference 10.9.8.
Q10-11. Are riders prohibited on tractors, the draw bar or towed equipment except when specifically designed for such use?
Reference 10.9.9.
Q10-12. If a tractor is parked on an incline; is the engine turned off, with the gear shift placed in the park position (or the lowest gear if standard transmission), and the wheels braked and blocked?
Reference 10.9.9.3.
Question Compliant
Does Not Comply
N/A to this Org Q11-1. Do supervisors and employees frequently inspect all hand tools used in the operations under their supervision, and are defective tools immediately removed from service? Reference 11.2.1.3. Q11-2. Do employees carrying hand tools while on ladders, scaffolds, platforms or work stands use carrying bags, i.e., shoulder bags or backpacks, or tool belts for tools that are not in use? Reference 11.2.1.4. Q11-3. Are workers not allowed to drop tools from elevated surfaces, or throw tools back and forth to each other? Reference 11.2.1.4. Q11-4. Are screwdrivers not used as a prying tool, punch, wedge, chisel, punch bar, nail puller or be struck with a hammer? Reference 11.2.2.1. Q11-5. Are hook-bill knives, utility knives or other similar extremely sharp knives, when not in use, stored in a holder or sheath? Reference 11.2.2.7. Q11-6. Are all portable electric tools with exposed metal parts grounded IAW the National Electrical Code to prevent electric shock? Reference 11.2.3.5.
Q11-7. Is the motor START switch on machines protected against accidental or inadvertent operation? Reference 11.4.1.1. Q11-8. Are anti-kickback dogs and fingers or safety hold-down wheels installed when ripping material? Reference 11.4.3.1. Q11-9. Are anti-kickback dogs and fingers inspected before each use and kept sharp to maintain their holding power? Reference 11.4.3.1.
Question Compliant
Does Not Comply
N/A to this Org Q12-1. Has each activity requiring training on powered materials handling and lifting equipment designated qualified personnel as instructors to train and supervise the operator trainee? Reference 12.3.3.1.
Q12-2. Do lesson plans (course content) include formal instruction, hands-on demonstrations by the instructor with practical exercises performed by the trainee, and an evaluation of the trainee’s performance to confirm their knowledge of equipment operations and service instructions? Reference 12.3.3.2. Q12-3. Does the trainee furnish the Operator Records and Licensing staff with written certification on the AF Form 171, Request for Driver’s Training and Addition to U. S. Government Driver’s License? Reference 12.3.3.3. Q12-4. Does a qualified instructor evaluate each operator at least once every three (3) years and provide refresher training in relevant topics any time there is reason to believe there is a need? Reference 12.3.3.6.
Q12-5. Is a lock and a danger or equipment lockout tag placed on the hoist and all energy controls (air, electrical, hydraulic, etc.) locked out IAW Chapter 21 when adjustments, modifications or repairs are scheduled? Reference 12.6.3.6.5.1. Q12-6. Are all new hoists and those which have had load- suspension parts altered, replaced or repaired operationally tested before use? Reference 12.6.3.7.1. Q12-7. Do slings procured for Air Force use comply with design and manufacturing requirements in 29 CFR 1910.184, Slings, and American Society of Mechanical Engineers B30.9, Slings? Reference 12.7.2.1.
Question Compliant Does NotComply this Org^ N/A to
Q12-8. Is the rated capacity plainly marked on each side of a crane, and if the crane has more than one hoisting unit, is the rated capacity marked on each unit?
Reference 12.8.2.2.2.
Q12-9. Do pendant and cab hoist controls for trolley and bridge movement use compass points (north, south, east and west) as the preferred identification wherever possible?
Reference 12.8.2.2.6.
Q12-10. Prior to use, are all new, reinstalled, altered, repaired and modified cranes and cranes not used within the preceding 12 months operationally tested by a qualified person?
Reference 12.8.2.7.1.1.
Q12-11. Is a substantial and durable rating chart with clearly legible letters and figures securely fixed to the crane cab in a location easily visible to the operator while seated at the control station?
Reference 12.9.2.1.2.1.
Q12-12. Are parts of crane cabs that extend beyond the main chassis when rotated color coded yellow and black on the lower areas to highlight the strike hazard to ground personnel?
Reference 12.9.2.1.2.5.
Q12-13. Is an audible warning device provided when hoisting operations or moving equipment might endanger personnel in the work area, and is the device control within easy reach of the operator?
Reference 12.9.2.1.2.10.
Q12-14. Is a permanent sign posted in the cab of the crane in full view of the operator that reads: “DANGER HIGH VOLTAGE, Do Not Operate Within 10 Feet of Electric Power Lines.”?
Reference 12.9.2.1.2.11.
Q12-15. Are outriggers used when the load at a particular radius exceeds the rated load without outriggers as given by the crane manufacturer?
Reference 12.9.2.3.24.
Q12-16. Are all running ropes in service visually inspected daily or prior to use?
Reference 12.11.2.2.1.