
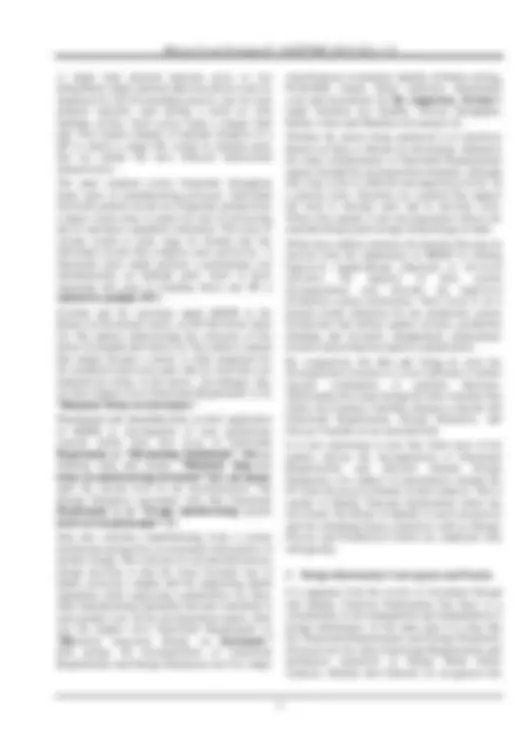
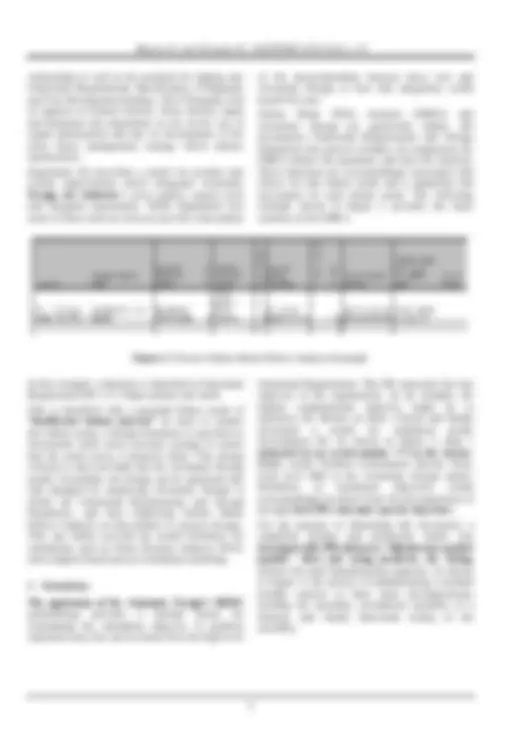
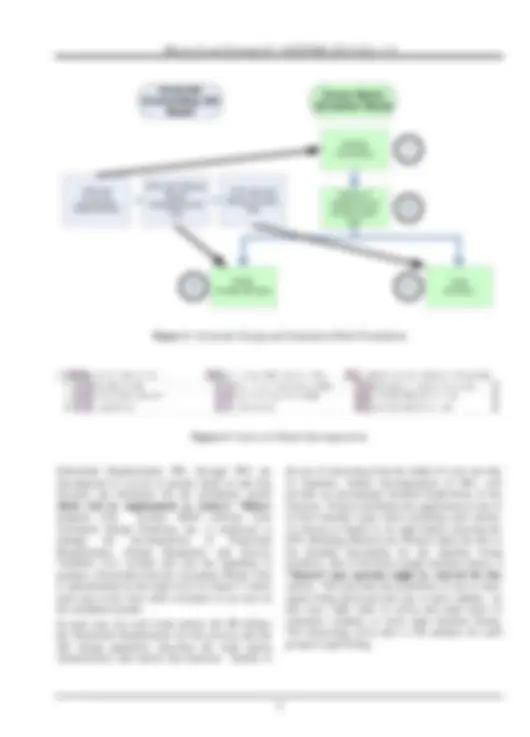
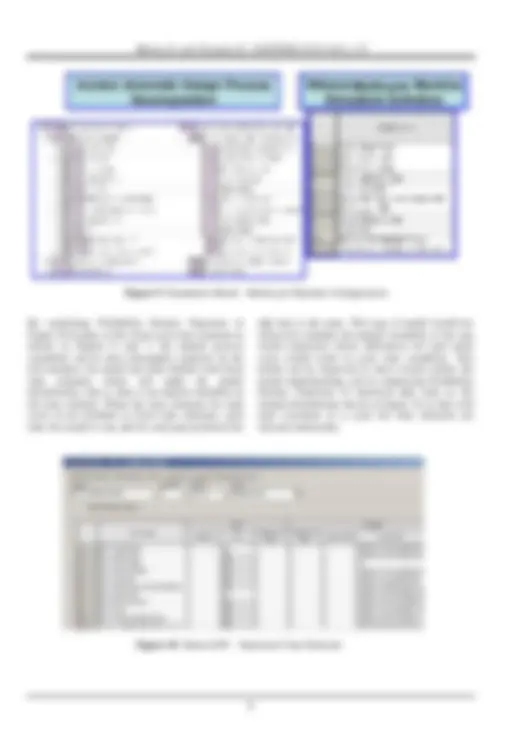
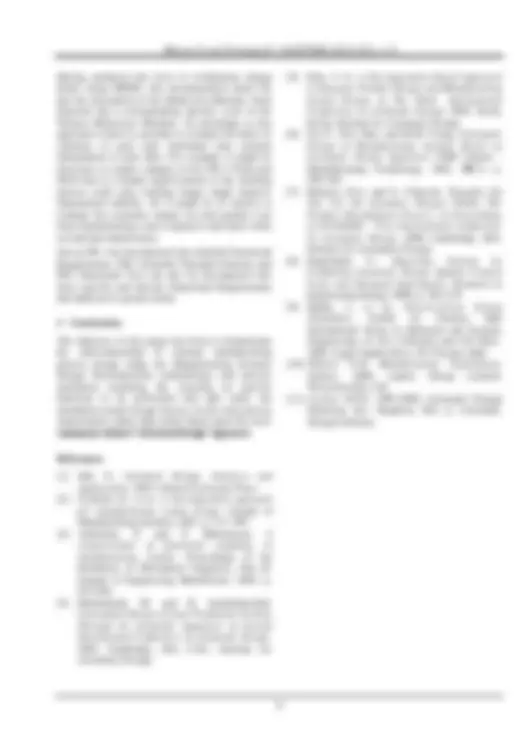
Study with the several resources on Docsity
Earn points by helping other students or get them with a premium plan
Prepare for your exams
Study with the several resources on Docsity
Earn points to download
Earn points by helping other students or get them with a premium plan
Community
Ask the community for help and clear up your study doubts
Discover the best universities in your country according to Docsity users
Free resources
Download our free guides on studying techniques, anxiety management strategies, and thesis advice from Docsity tutors
The application of axiomatic design and manufacturing system decomposition (msdd) in the rational design of process simulation models. The authors, murray and taraman, describe how they employed msdd to define functional requirements and design parameters for manufacturing processes and simulation models as part of the dems program at lawrence technological university. They also explore the relationship between axiomatic design and failure mode effect analysis (fmea) and demonstrate how the interrelationship can be utilized to optimize and risk manage product or process designs. Figures and diagrams to illustrate the concepts.
What you will learn
Typology: Slides
1 / 9
This page cannot be seen from the preview
Don't miss anything!
Murray N.
Lawrence Technological University, Doctor of Engineering in Manufacturing Systems, TRW Automotive LLC, Michigan, U.S.A.
Taraman K.
Lawrence Technological University, Department of Mechanical Engineering, Michigan, U.S.A.
Abstract
Design of computerized process simulation models are often an attempt to mimic workings of an existing manufacturing process with as much precision as feasible so that analysis is optimally useful. This modeling may also be applied to processes that are new and do not have a pre-existing physical example. A methodology from Axiomatic Design called Manufacturing System Design Decomposition (MSDD) is employed to define the functional requirements and the design parameters for the processes which are then employed in the design of the process simulation model. By its very nature, the resultant design is lean since the focus is on the specific functions to be performed necessary to the manufacture of the product at the lowest possible cost. Acclaro DFSS software from Axiomatic Design Solutions, Inc. provides the environment for developing the Axiomatic Design model and Witness software from Lanner Inc. is employed for the simulation environment.
Keywords : Axiomatic Design, Overmold, Process Simulation, MSDD
1 Introduction
A new dual-stage overmolding process for the packaging of automotive electronic crash sensors is being developed in a pilot process at TRW Automotive LLC. This activity has coincided with an initial investigation into the application of Axiomatic Design in the definition of manufacturing Functional Requirements for the development of manufacturing processes and simulation models as a part of the DEMS program at Lawrence Technological University.
Dr. Nam Pyo Suh, in a series of papers and books published beginning in the mid-1980’s culminating in the publication of Axiomatic Design Advances and Applications, proposed a different methodology for solving this problem of analyzing functional requirements and translating them into product or
process design parameters [1]. Analogous to QFD matrices, Dr. Suh proposed four domains to classify the relationship between, what the customer wants, functional requirements of the solution to these wants, design parameters and processes to fabricate the solution. The four defined domains are: Customer Domain, Functional Domain, Design Domain and Process Domain and these are shown in Figure 1. What the customer wants, in axiomatic design terms represents the Customer Domain. Voice of the Customer elements are then translated successively from wants into Functional Requirements, then into the Design Parameters that satisfy the Functional Requirements and then into the process domain which realizes the physicality of the Design Parameters.
With this approach, a relationship can be established between the customer want of “reliable safety at minimal cost”, the design and optimization of the manufacturing process and in the end, delivery of a product that provides reliable safety to the consumer at a reasonable cost.
David Cochran and others proposed specific application of functional decomposition and related design parameters to manufacturing system design. Cochran, and his associates described this “Manufacturing System Design Decomposition”, MSDD, approach in a series of published papers [2]. Within the MSDD methodology, the main focus is on the decomposition of functional requirements and the association of design parameters. Other aspects of Axiomatic Design such as the Information Axiom are not explicitly employed. Although Cochran and his associates state that this approach is most suitable for medium to high volume manufacturing enterprises, it is not clear if they contend that this is due to the limited resources available to smaller businesses, or in recognition that by their nature, small enterprises are more intimate with their processes. They suggest that as a practical matter, it is difficult for enterprises to develop manufacturing systems that satisfy their strategic business objectives, quoting Hopp and Sherman’s perspective that too much of the focus in manufacturing development is on the individual process aspects, losing sight of the overall business objectives. For example a CNC milling center may provide a manufacturing capability in replacing an existing manual milling center without being firmly linked to an over-all enterprise strategy which might be to replace machined metal components with plastic injection molded ones. Inherent to this argument is the perspective that business planning must propagate from the top of the organization downwards and not conversely, from the bottom up.
MSDD philosophy dictates that the following four conditions shown in Table 1 must be met in order for
a manufacturing system to satisfy corporate objectives:
Table 1 : RULES OF MSDD [2]
When manufacturing consists of more than a single step, the sequence of the steps involved in the completion of the final product becomes critical and it is by its very nature that this sequence produces functional coupling. As Almstrom and Martensson indicate, with the exception of their paper, this coupling has not been assessed or discussed [3]. Using a case-study example of three connected machining cells, they define a categorization of naturally occurring manufacturing based functional couplings to shed some light on manufacturing coupling as is shown in Table 2.
Table 2 : MANUFACTURING-BASED FUNCTIONAL COUPLINGS [3] 1 Sequence induced couplings 2 Design Parameter-induced sequence 3 Product property constraint 4 Resource integration prompted coupling 5 Multiple DP instances
Ultimately Martensson and Almstrom conclude that uncoupled manufacturing systems do not and can not exist. In their words it is “unthinkable” since there would need to be total independence throughout the sequence of manufacturing process steps. In a sequence of process steps, the FR’s are typically performed in a particular order, i.e., the hole must be drilled before it can be threaded. In another example, surface grinding can only be performed after a metal component is machined on a lathe. The process steps cannot be reversed in order. For a dual-stage overmolding process, molding of the elastomeric material around a nylon substrate would necessitate a specific sequence of molding processes. This sequence is fixed by the nature of the materials and their functions.
CA
CustomerDomain
FR
FunctionalDomain
DP
Physical Domain
PV
Process Domain
What is wanted What it does What is designed How is it made
Figure 1 : Axiomatic Domains
relationship as well as the potential for linking into Functional Requirements Specification, P-Diagrams and Test Development Strategy. The P-Diagram with its analysis of Control Factors, Noise Factors, Input and Response has importance at two levels: use in signal optimization and also in development of the noise factor management strategy which defines optimization.
Englehardt [8] described a model for product and system improvement which integrated Axiomatic Design, the Ishikawa’s seven quality control tools and designed experiments. While Englehardt lists some of these tools, he does not provide a description
of the interrelationship between these tool and Axiomatic Design or how that integration would benefit the user. Failure Mode Effect Analysis (FMEA) and Axiomatic Design are genetically linked. AD decomposes Functional Requirements and Design Parameters into process variables. In comparison, the FMEA defines the parameter and then the function. These functions are correspondingly associated with effects for that failure mode and a quantified risk assessment for each failure mode. The following example shown in Figure 2 provides the basic structure of the FMEA.
Figure 2 : Process Failure Mode Effects Analysis Example
In this example, a function is identified as Functional Requirement FR 1.2.1.5 Inject plastic into mold.
This is identified with a potential failure mode of “Insufficient volume injected”. In order to counter this failure mode, a Design Parameter is specified to incorporate mold cavity pressure sensing to ensure that the mold cavity is properly filled. This design criterion is then fed back into the Axiomatic Design model. Essentially, the design can be optimized and risk managed by employing Axiomatic Design to define the Functional Requirements and Design Parameters, and then employing Failure Mode Effects Analysis on that product or process design,. This can further provide the model definition for simulations such as Finite Element Analysis (FEA) and computer based process simulation modeling.
3 Simulation
The application of the Axiomatic Design’s MSDD methodology provides a rational means for formulating the simulation objective or problem statement since this can be drawn from the high-level
Functional Requirement. This FR represents the true objective of the organization. As an example, the highest organizational objective might be to maximize the Return on Sales. Carson and Banks developed a model for simulation model development [9]. As shown in Figure 3, Step 1 (indicated by an circled number “1”) in the Carson- Banks model Problem Formulation directly flows from level FR0 in the Axiomatic Design model. Definition of simulation objectives would correspondingly be drawn from the decomposition of the high-level FR’s into more specific objectives. For the purpose of illustrating this discussion, a simplified product and production model was developed with FR0 defined as “Manufacture molded module”. Each part being produced, the Dolog, follows the same manufacturing sequence. As shown in Figure 4, the activity of manufacturing a molded module consists of three main decompositions; molding the assembly, mechanical assembly of a fastener, and finally functional testing of the assembly.
Functional Requirements FR1 through FR3 are decomposed to a level of greater detail as and this becomes the definition for the simulation model which will be implemented in Lanner’s Witness program [10]. Acclaro DFSS software from Axiomatic Design Solutions, Inc. is employed to manage the decomposition of Functional Requirements, Design Parameters and Process Variables [11]. Acclaro also has the capability to produce a flowchart from the Axiomatic Model. This is demonstrated at this high level in Figure 5 where each step in the flow chart correlates to an icon on the simulation model.
In each case, for each work station, the FR defines the Functional Requirement for the process and the DP, design parameter, describes the work station characteristics that satisfy that function. Similar to
the act of traversing from the trunk of a tree out into its branches, further decomposition of FR1, will provide an increasingly detailed break-down of the function. Witness facilitates the application of one of several machine types when modeling each station. As shown in Figure 6, by right-button selecting the DP1_Molding_Station icon, Witness takes the user to the detailed description for the machine being modeled. One of the fairly simple machine classes, a “General” type machine might be selected for this station. This provides the possibility of one or more inputs being processed into one or more outputs. In this case, eight units of nylon and eight units of elastomer combine to form eight finished Dolog. The processing cycle time is 0.6 minutes for each group of eight Dolog.
Problem Formulation
Setting of objectives and overall project plan
Model conceptualization
Data collection
DP0: Cell Stations Design Parameters and Flow
FR0 Cell Functional Requirements
PV0: Cell and Station Process Data
Axiomatic Overmolding Cell Model
Carson-Banks Simulation Model
1
2
3 4
Figure 3 : Axiomatic Design and Simulation Model Postulation
Figure 4 : Top Level Model Decomposition
which provide increased functional specificity and provide a means to identify time, cost and breakdown for each element.
The molding process FR1, has been decomposed, that is, broken down, into increasingly specific sub- components so that the molding process can be examined in greater detail. As shown in Figures 8 and 9, FR1 Mold Sub Assembly can be divided into FR1.1 through FR1.11. These comprise the main activities of the dual shot injection molding process. Further decomposition for FR1.2 and FR1.7 is also possible. For each workstation function in Mold Sub Assembly, we can see both the Design Parameters and the Process variables such as time components allocated to each function. This becomes useful during the progression into simulation model
development since the optimization of the process may focus on cooling time or pack and hold time to increase workstation throughput. What is the source for the time elements in the Process Variable (PV) values? If this is an existing process, it may be as simple as collecting data from the machine itself, or by conducting time and motion studies. New processes, where there is no preexisting empirical world to study represent a different challenge. By decomposing the molding process, those building the simulation model can use standard time data for actions such as opening and closing the press, etc. In this way, information from analogous time elements can be employed to improve simulation model efficacy.
Figure 8 : Decomposition of FR1 - Mold Sub-assemblies
By employing Probability Density Functions in Figure 10 in place of the fixed cycle time elements as shown in Figures 6 and 7, the natural process variability can be more thoroughly explored. In the first instance, the model has been defined with fixed time elements which will make the model deterministic, that is, there is no natural variability in the time element. When the time elements for each cycle in are modeled as fixed time elements, each time the model is run, and for each part produced the
takt time is the same. This type of model would not effectively simulate the natural variability of the real world experience where differences for each mold cycle would result in cycle time variability. This model can be improved to more closely mimic the actual manufacturing cell by employing Probability Density Functions of historical data such as the normal distributions shown in Figure 10 so that with each execution of a cycle the time elements are selected statistically.
Figure 9 : Simulation Model - Multicycle Machine Configuration
Figure 10 : Station DP1 - Statistical Time Elements