
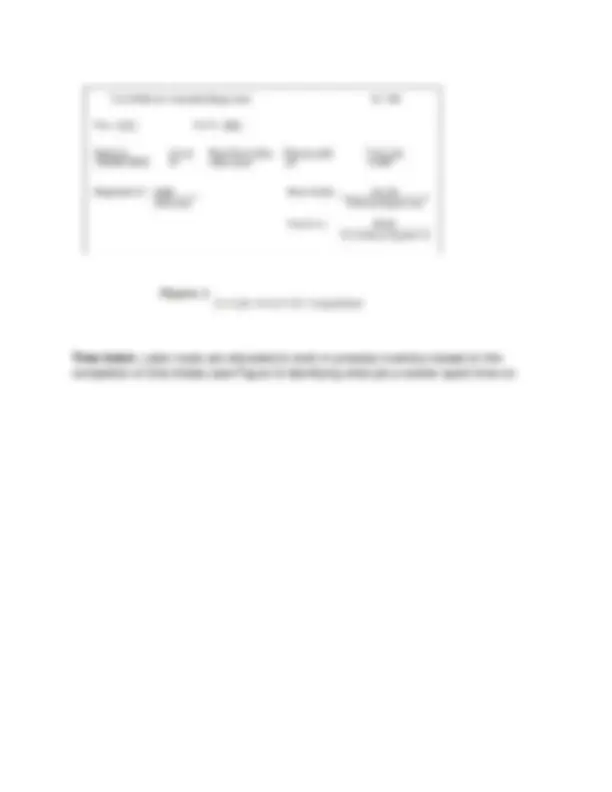
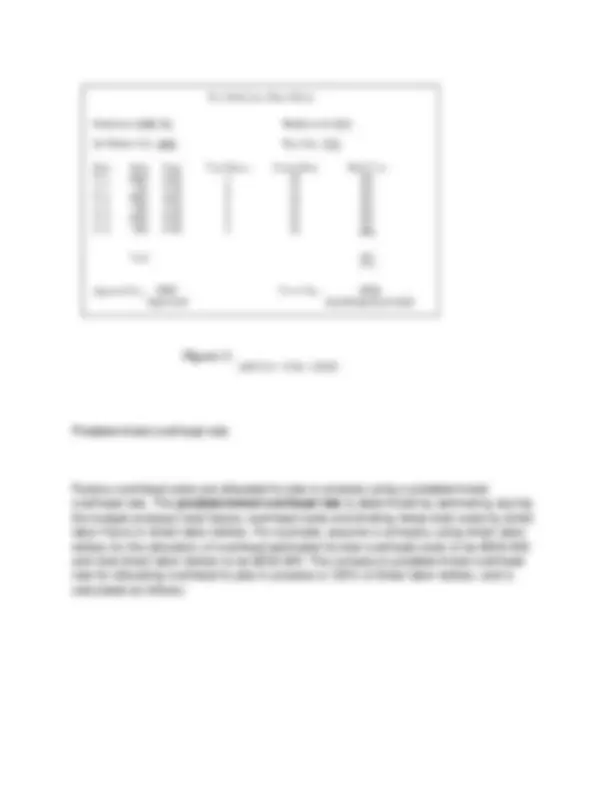

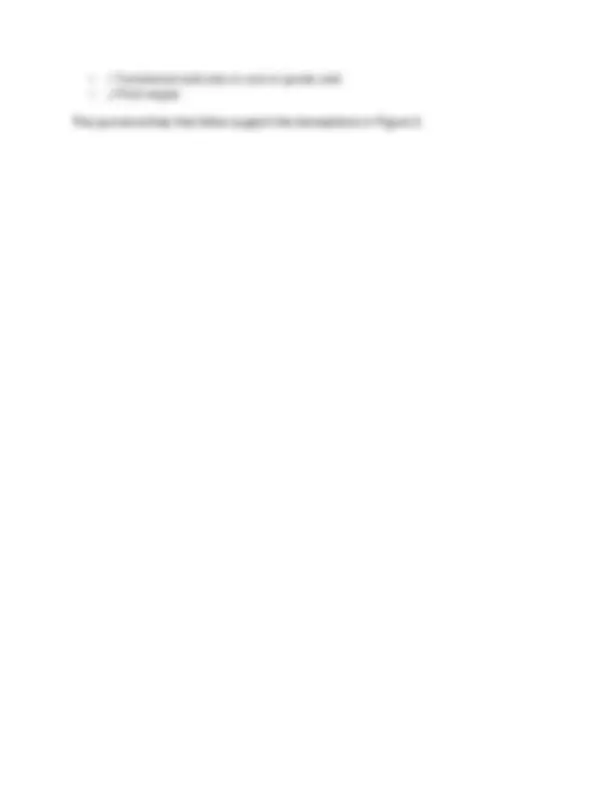
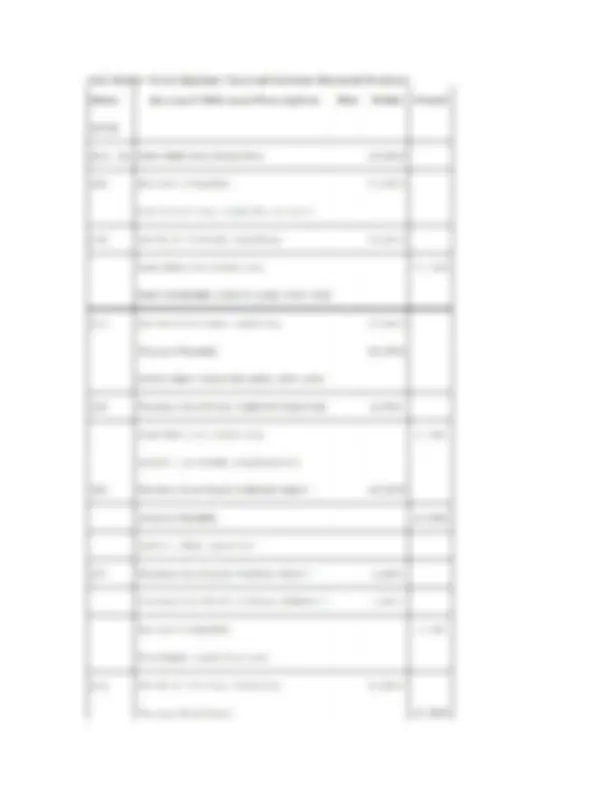
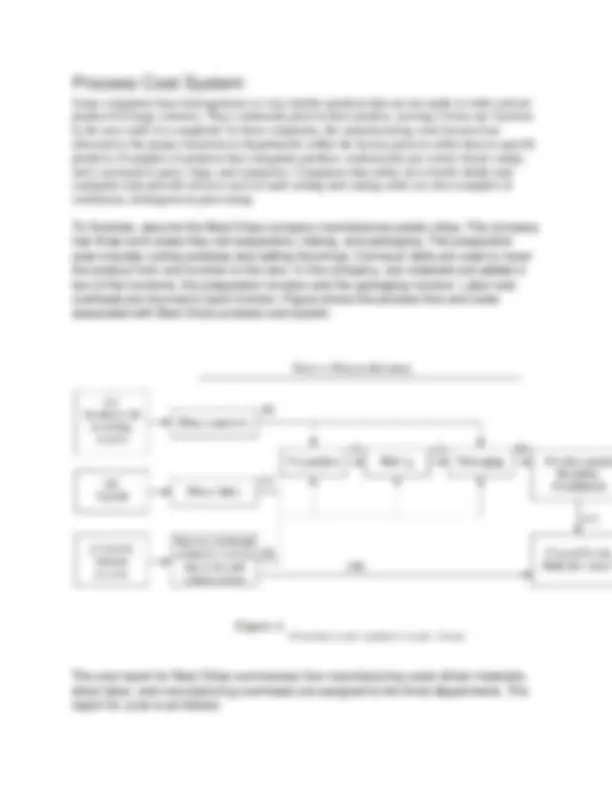
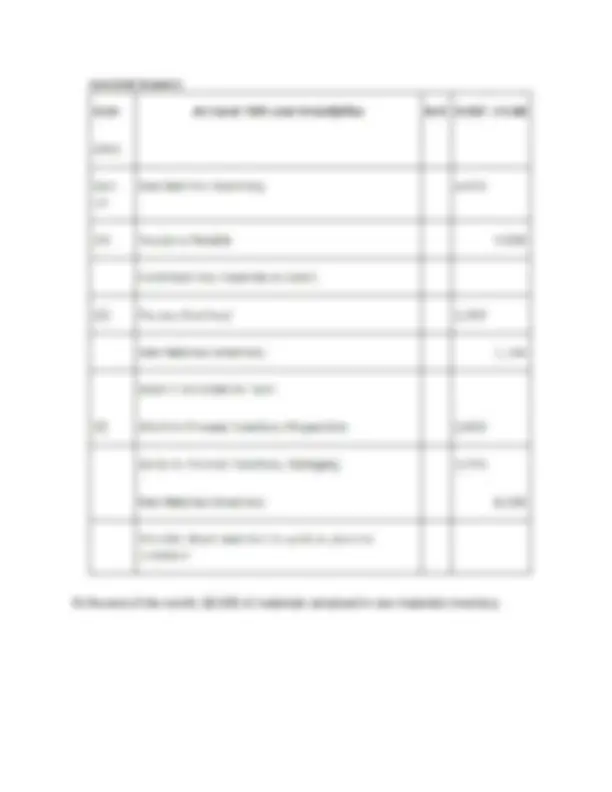
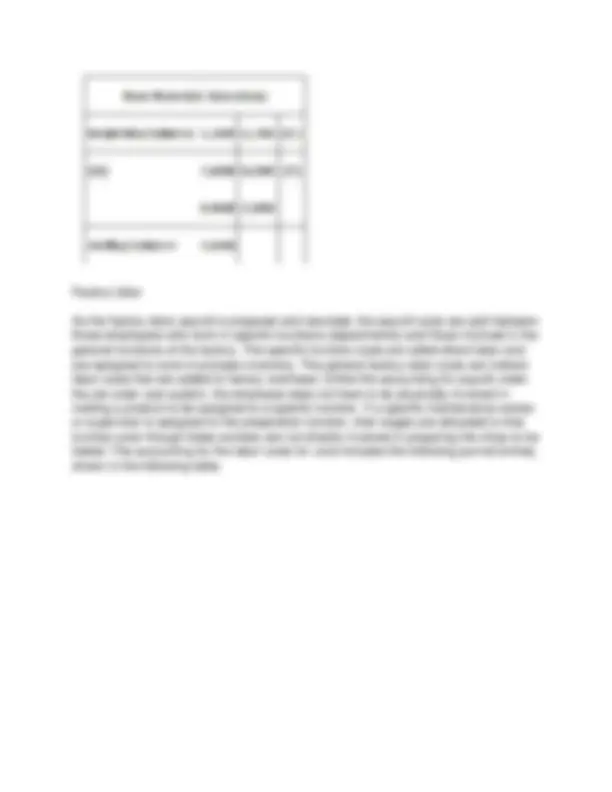

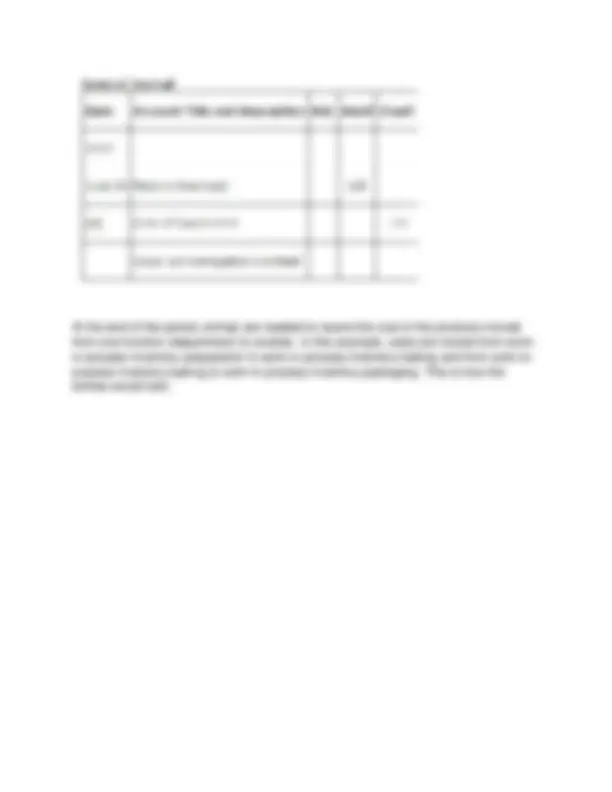

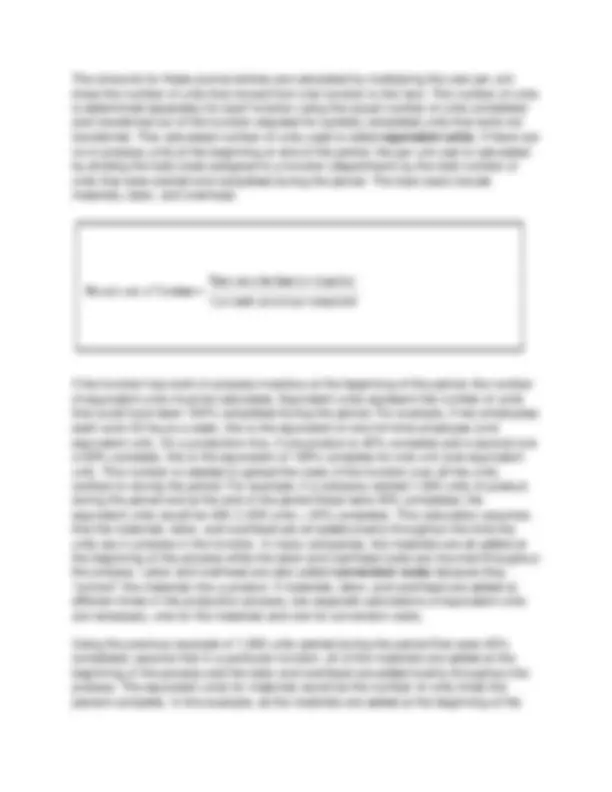

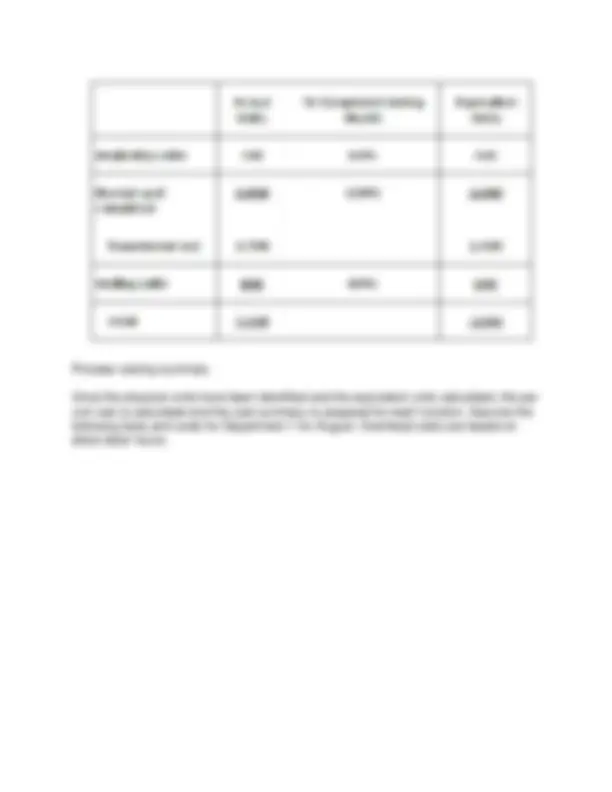


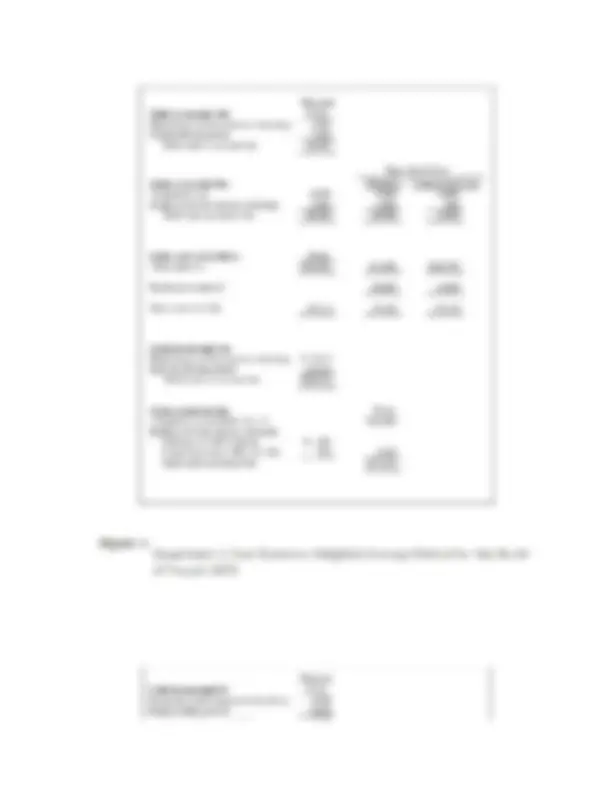

Study with the several resources on Docsity
Earn points by helping other students or get them with a premium plan
Prepare for your exams
Study with the several resources on Docsity
Earn points to download
Earn points by helping other students or get them with a premium plan
Community
Ask the community for help and clear up your study doubts
Discover the best universities in your country according to Docsity users
Free resources
Download our free guides on studying techniques, anxiety management strategies, and thesis advice from Docsity tutors
The two traditional cost accounting systems used in manufacturing environments: job order cost system and process cost system. The job order cost system tracks costs by job, including materials, labor, and overhead, while the process cost system allocates overhead based on activity levels. Both systems help managers determine total production costs.
Typology: Exams
1 / 26
This page cannot be seen from the preview
Don't miss anything!
The two basic types of manufacturing processes are the job order approach, where each order is customized, and mass production, where the product is always the same. To accompany these procedures are the two traditional types of cost accounting systems: job order cost system and process cost system. The information captured by these cost accounting systems aids managers in determining total production costs. The job order cost system is used when products are made based on specific customer orders. Each product produced is considered a job. Costs are tracked by job. Services rendered can also be considered a job. For example, service companies consider the creation of a financial plan by a certified financial planner, or of an estate plan by an attorney, unique jobs. The job order cost system must capture and track by job the costs of producing each job, which includes materials, labor, and overhead in a manufacturing environment. To track data, the following documents are used: Job cost sheet. This is used to track the job number; customer information; job information (date started, completed, and shipped); individual cost information for materials used, labor, and overhead; and a total job cost summary. See Figure 1.
Materials requisition form. To assure that materials costs are properly allocated to jobs in process, a materials requisition form (see Figure 2) is usually completed as materials are taken from the raw materials inventory and added to work‐in‐process.
Predetermined overhead rate Factory overhead costs are allocated to jobs in process using a predetermined overhead rate. The predetermined overhead rate is determined by estimating (during the budget process) total factory overhead costs and dividing these total costs by direct labor hours or direct labor dollars. For example, assume a company using direct labor dollars for the allocation of overhead estimated its total overhead costs to be $300, and total direct labor dollars to be $250,000. The company's predetermined overhead rate for allocating overhead to jobs in process is 120% of direct labor dollars, and is calculated as follows:
If direct labor costs are $20,000 for the month, overhead of $24,000 ($20,000 × 120%) would be allocated to work‐in‐process inventory. Factory overhead would be allocated to individual jobs based on the portion of the $20,000 direct labor cost that is assigned to each job. If job number 45 had $9,000 in direct labor cost for the month, factory overhead of $10,800 ($9,000 × 120%) would also be allocated to the job. Once a job is completed, the total costs assigned to the job are transferred from work‐ in‐process inventory to finished goods inventory. Once the job is sold and delivered, the job costs are transferred from finished goods inventory to cost of goods sold. Figure 4 summarizes the flow of costs in a job order cost system and Figure 5 summarizes the journal entries required given the flow of costs in Figure 4. The ending balances in the three inventory accounts would be reported as inventories on the balance sheet and cost of goods sold would be reported on the income statement.
The factory overhead account (see Figure 5) has a balance which indicates the amount of overhead applied to work‐in‐process inventory is different from the actual overhead incurred. When there is a debit balance in the factory overhead account, it is called under‐applied overhead meaning not enough overhead was allocated to jobs. If the balance in the factory overhead account was a credit, the overhead would be over‐ applied, meaning too much overhead was allocated to jobs. Factory overhead must be zero at the end of the year. Most companies transfer the balance in factory overhead to cost of goods sold. An alternative method, although more complex, is to allocate the under‐ or over‐applied balance among the work‐in‐process inventory, finished goods inventory, and cost of goods sold accounts. The $2,600 account balance in factory overhead in Figure 5 is relatively small. To zero out the account balance and transfer it to cost of goods sold, the entry would be: Key: A Purchased raw materials B Direct material requisition to be used on jobs C Direct labor payroll based on time ticket D Indirect materials used E Indirect labor payroll F Other overhead costs incurred G Overhead applied to jobs (direct labor dollars ¥ 80% predetermined overhead rate) H Transfer completed jobs to finished goods inventory
I Transferred sold jobs to cost of goods sold J Paid wages The journal entries that follow support the transactions in Figure 5.
Some companies have homogeneous or very similar products that are not made to order and are produced in large volumes. They continually process their product, moving it from one function to the next until it is completed. In these companies, the manufacturing costs incurred are allocated to the proper functions or departments within the factory process rather than to specific products. Examples of products that companies produce continuously are cereal, bread, candy, steel, automotive parts, chips, and computers. Companies that refine oil or bottle drinks and companies that provide services such as mail sorting and catalog order are also examples of continuous, homogeneous processing. To illustrate, assume the Best Chips company manufactures potato chips. The company has three work areas they call preparation, baking, and packaging. The preparation area includes cutting potatoes and adding flavorings. Conveyor belts are used to move the product from one function to the next. In this company, raw materials are added in two of the functions: the preparation function and the packaging function. Labor and overhead are incurred in each function. Figure shows the process flow and costs associated with Best Chip's process cost system. The cost report for Best Chips summarizes how manufacturing costs (direct materials, direct labor, and manufacturing overhead) are assigned to the three departments. The report for June is as follows:
The raw materials are assigned based on material requisition forms, the labor based on time tickets, and the overhead based on predetermined overhead rates based on direct labor dollars. The journal entries to record these transactions are made prior to the period end entries that transfer the amounts from one work‐in‐process inventory
At the end of the month, $2,000 of materials remained in raw materials inventory.
Factory labor As the factory labor payroll is prepared and recorded, the payroll costs are split between those employees who work in specific functions (departments) and those involved in the general functions of the factory. The specific function costs are called direct labor and are assigned to work‐in‐process inventory. The general factory labor costs are indirect labor costs that are added to factory overhead. Unlike the accounting for payroll under the job order cost system, the employee does not have to be physically involved in making a product to be assigned to a specific function. If a specific maintenance worker or supervisor is assigned to the preparation function, their wages are allocated to that function even though these workers are not directly involved in preparing the chips to be baked. The accounting for the labor costs for June includes the following journal entries, shown in the following table.
Factory overhead In a process company, factory overhead represents those costs not directly assigned to one function. For example, the depreciation expense of a machine used solely by the preparation function would be assigned to work‐in‐process inventory for the preparation department while depreciation expense for the plant (the factory building) would be assigned to factory overhead as all functions occupy the plant. The journal entries that follow illustrate the accounting for general overhead costs.
At the end of the period, the factory overhead account has a credit balance of ($125). This is called overapplied overhead and an entry would be made at the end of the period to move it to cost of goods sold, or alternatively, to allocate the difference to work‐in‐process inventories, finished goods inventory, and cost of goods sold. After recording this entry, the balance in the factory overhead account is zero.
When the packaging function (department) completes its work, the product is ready to be sold. The costs of the completed products are then transferred from work‐in‐process inventory‐packaging to finished goods inventory. This transfer also requires a journal entry.
The amounts for these journal entries are calculated by multiplying the cost per unit times the number of units that moved from one function to the next. The number of units is determined separately for each function using the actual number of units completed and transferred out of the function adjusted for partially completed units that were not transferred. This calculated number of units used is called equivalent units. If there are no in‐process units at the beginning or end of the period, the per unit cost is calculated by dividing the total costs assigned to a function (department) by the total number of units that were started and completed during the period. The total costs include materials, labor, and overhead. If the function has work‐in‐process inventory at the beginning of the period, the number of equivalent units must be calculated. Equivalent units represent the number of units that could have been 100% completed during the period. For example, if two employees each work 20 hours a week, this is the equivalent of one full‐time employee (one equivalent unit). On a production line, if one product is 40% complete and a second one is 60% complete, this is the equivalent of 100% complete for one unit (one equivalent unit). This number is needed to spread the costs of the function over all the units worked on during the period. For example, if a company started 1,000 units of product during the period and at the end of the period these were 40% completed, the equivalent units would be 400 (1,000 units × 40% complete). This calculation assumes that the materials, labor, and overhead are all added evenly throughout the time the units are in process in the function. In many companies, the materials are all added at the beginning of the process while the labor and overhead costs are incurred throughout the process. Labor and overhead are also called conversion costs because they “convert” the materials into a product. If materials, labor, and overhead are added at different times in the production process, two separate calculations of equivalent units are necessary, one for the materials and one for conversion costs. Using the previous example of 1,000 units started during the period that were 40% completed, assume that in a particular function, all of the materials are added at the beginning of the process and the labor and overhead are added evenly throughout the process. The equivalent units for materials would be the number of units times the percent complete. In this example, all the materials are added at the beginning of the