
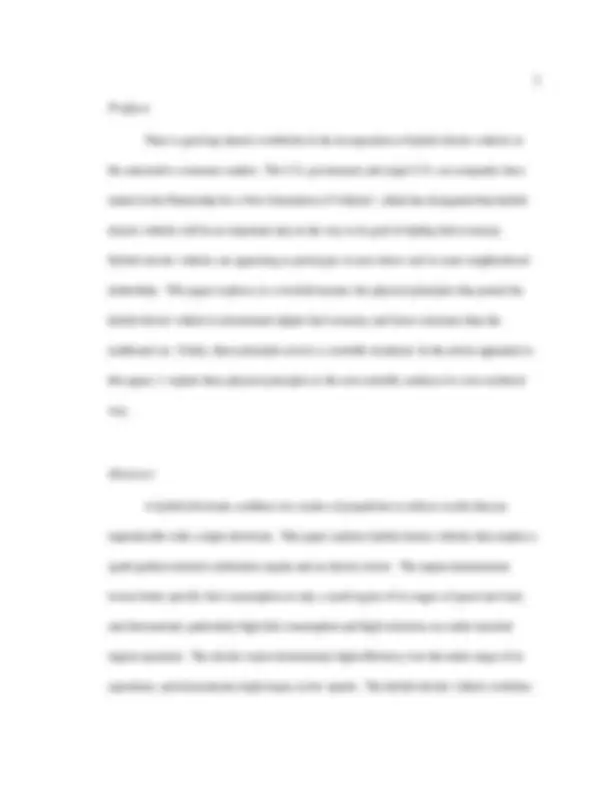
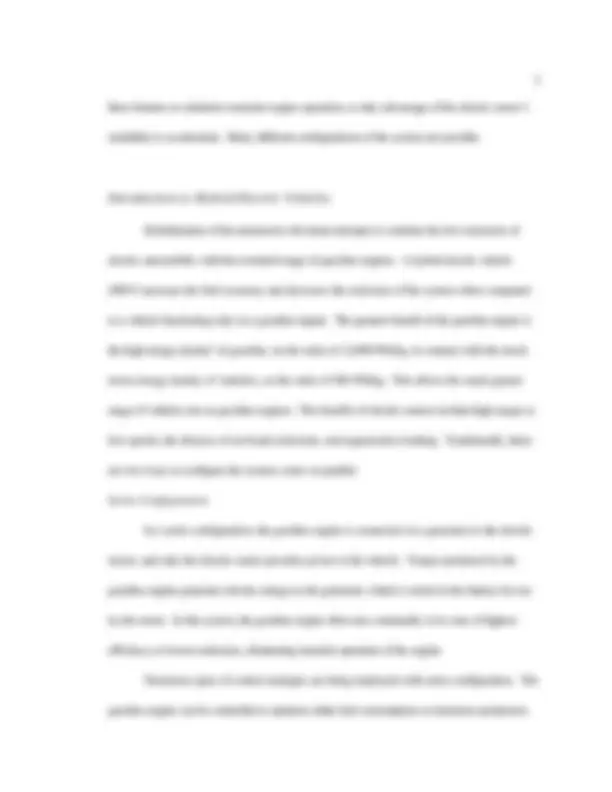
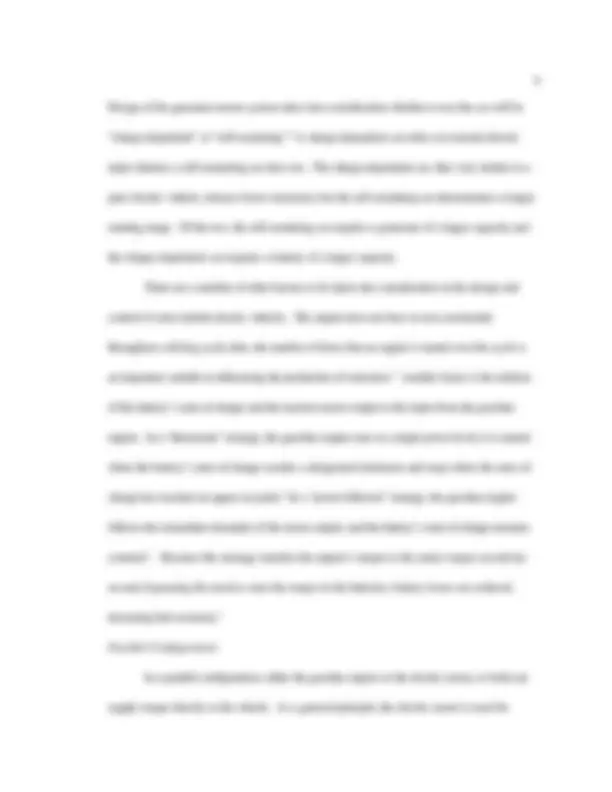
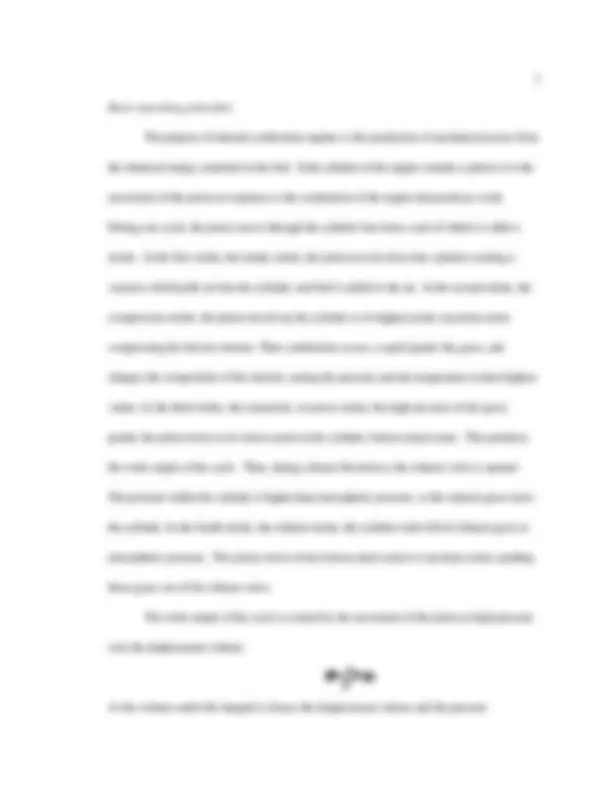
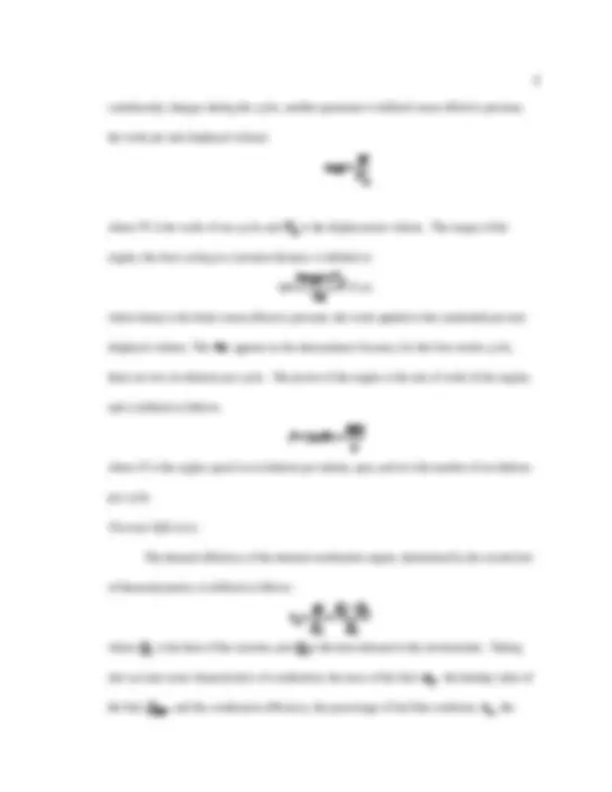
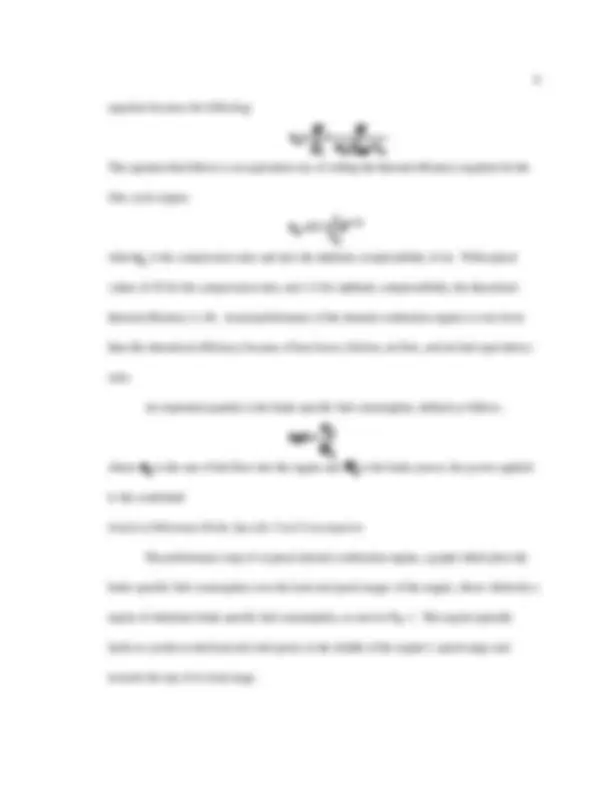
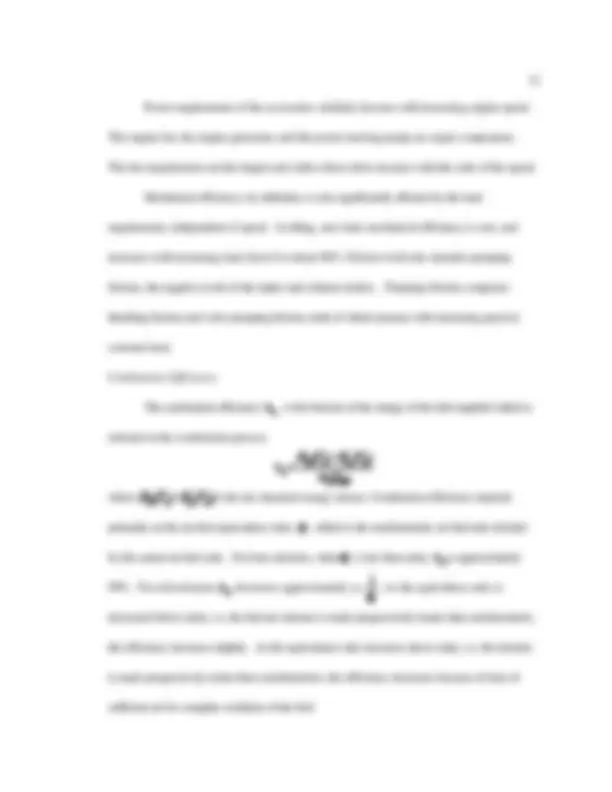
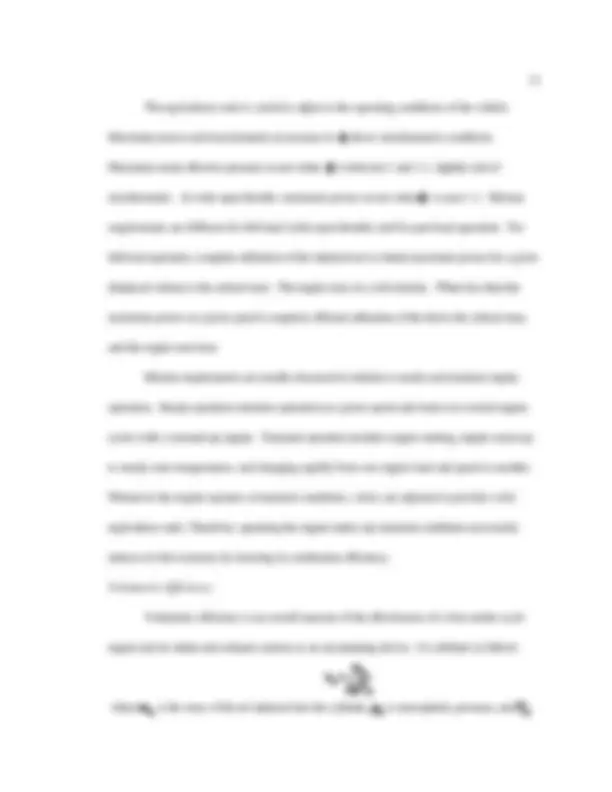
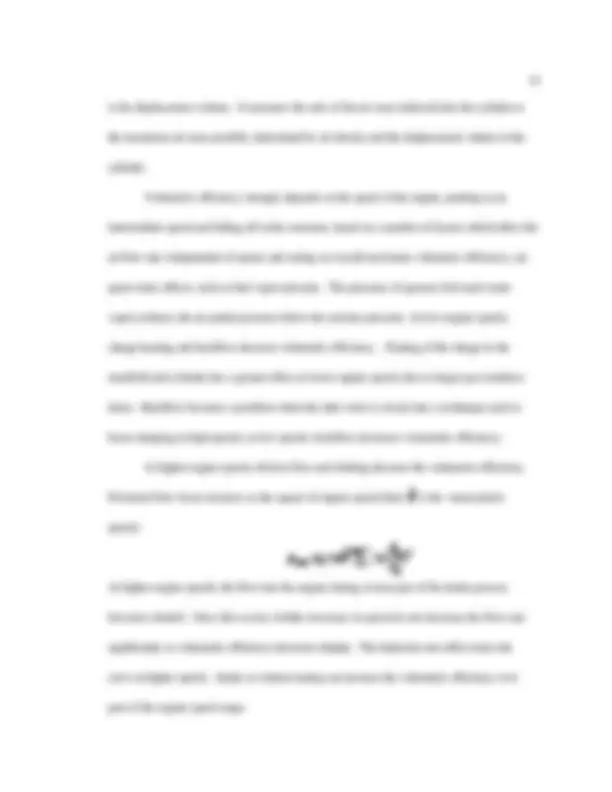
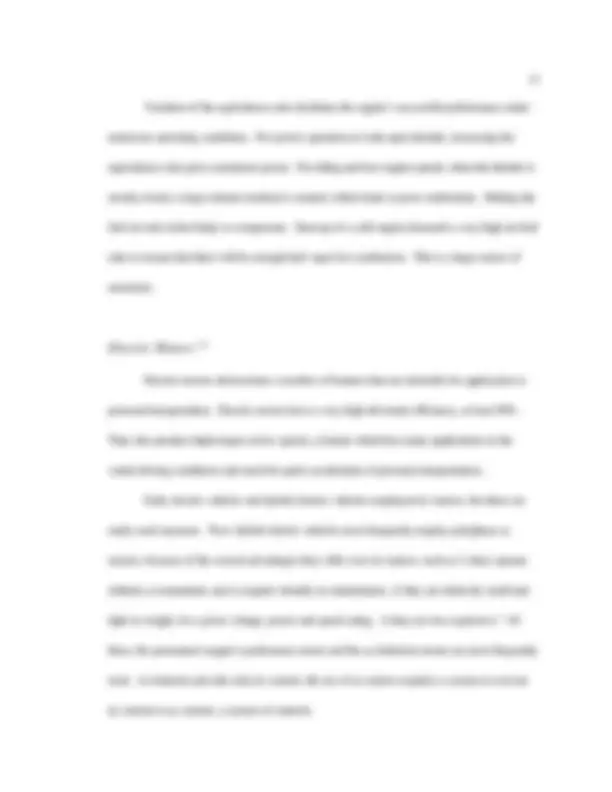
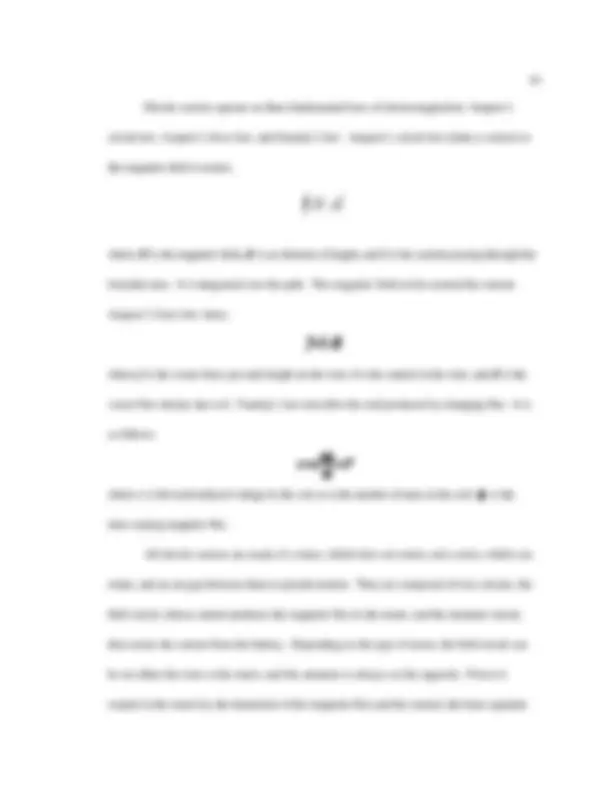
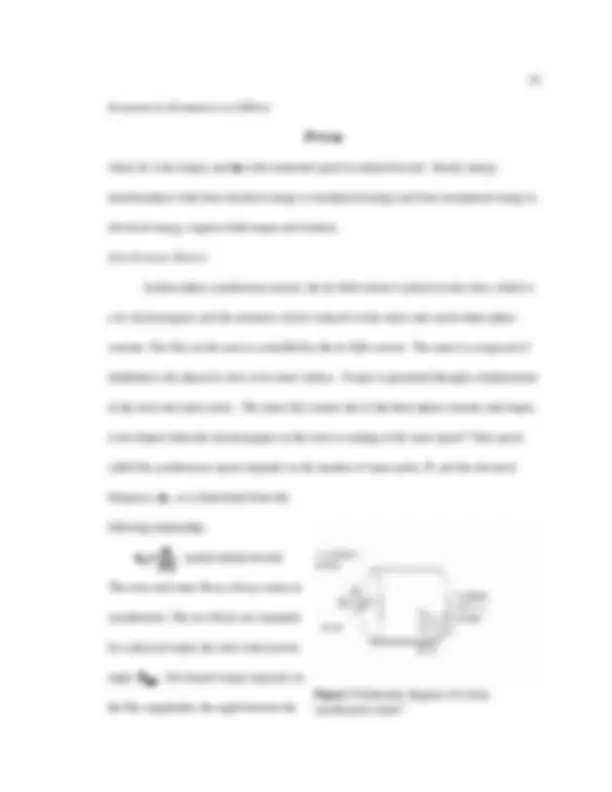
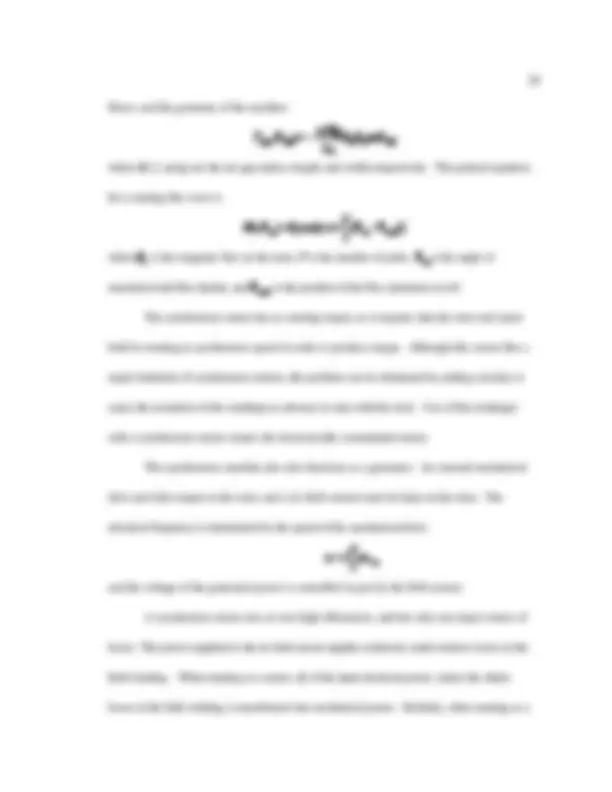
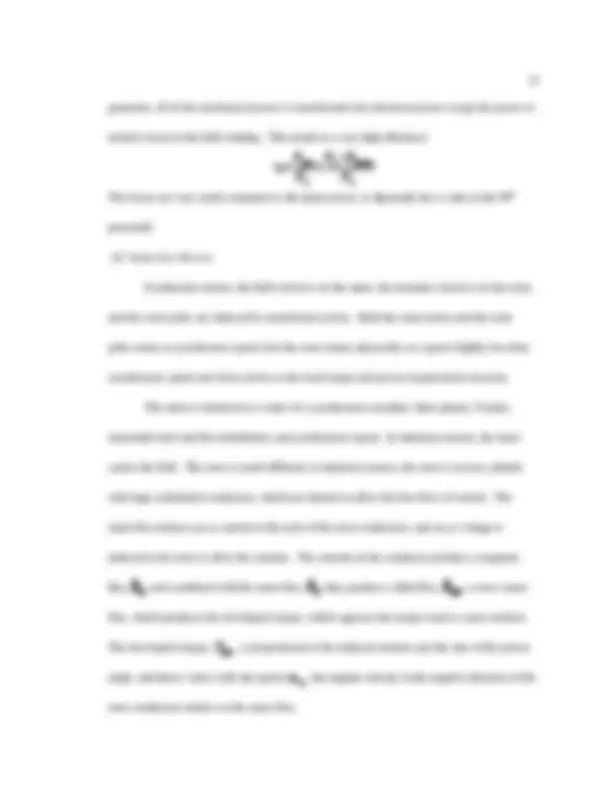
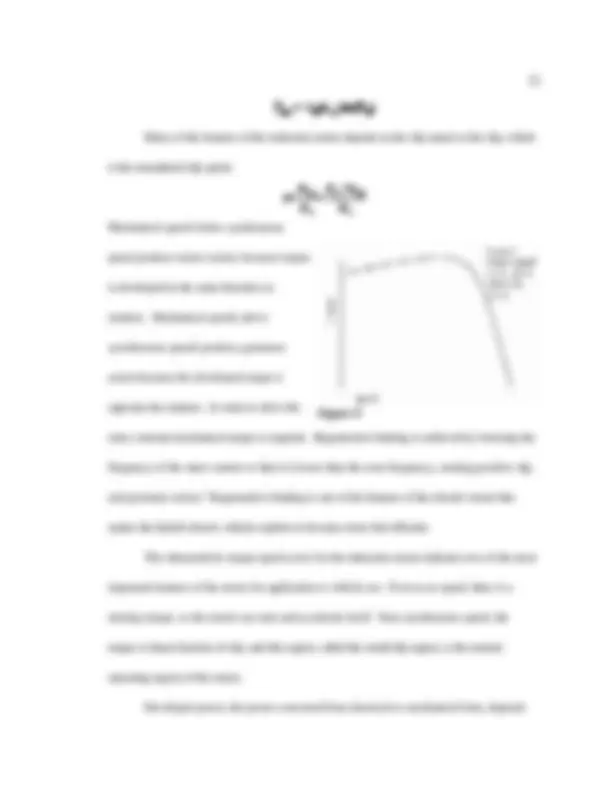
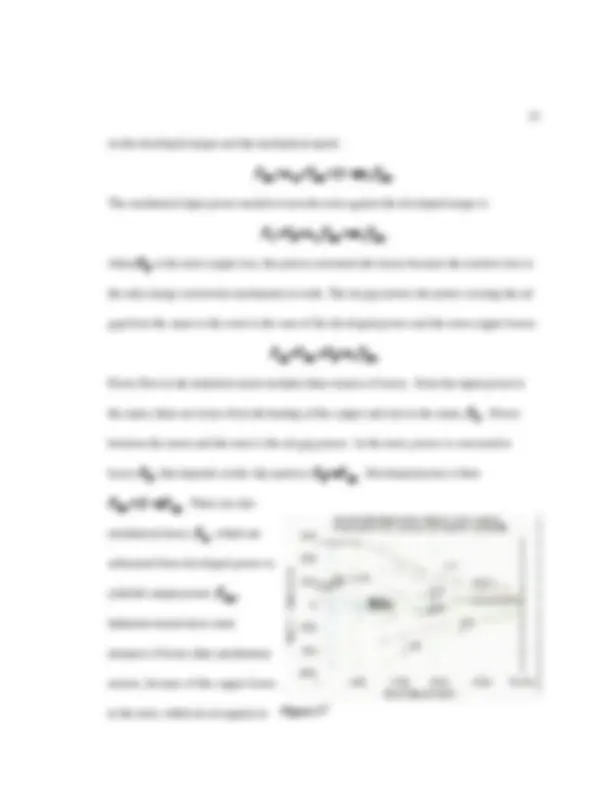
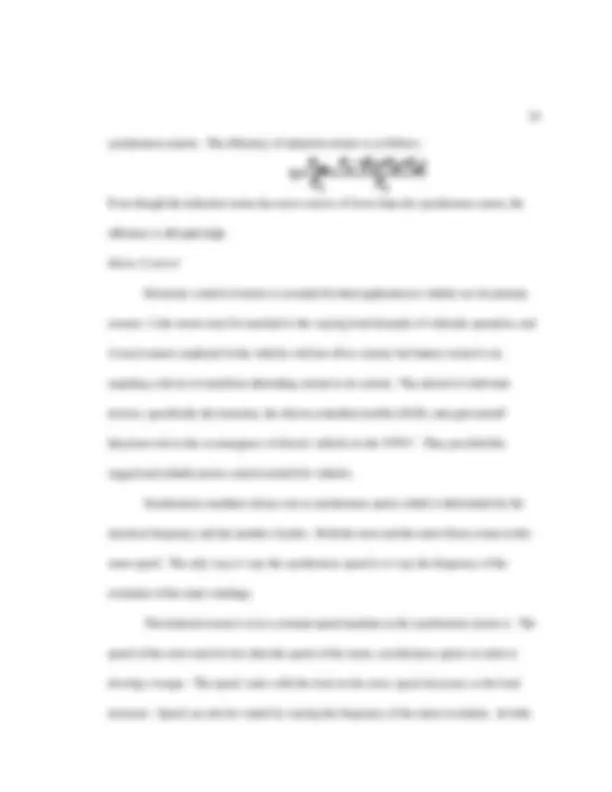
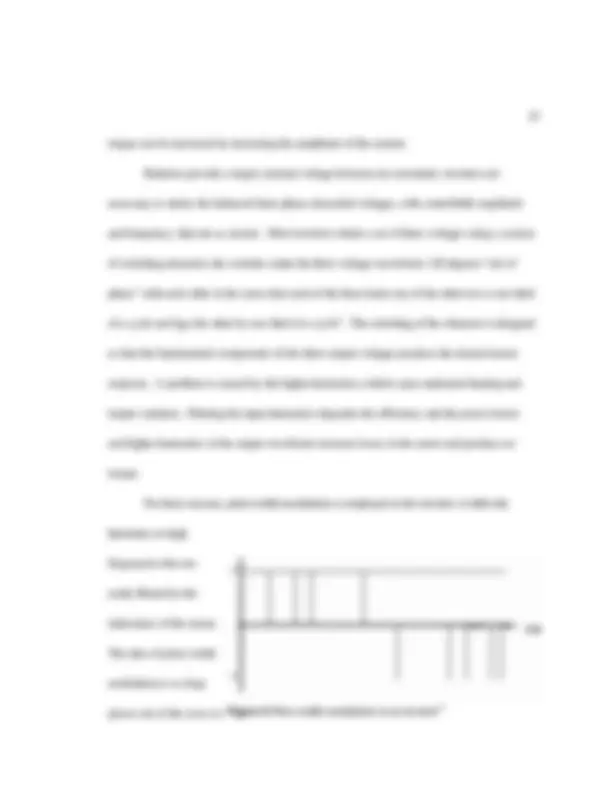
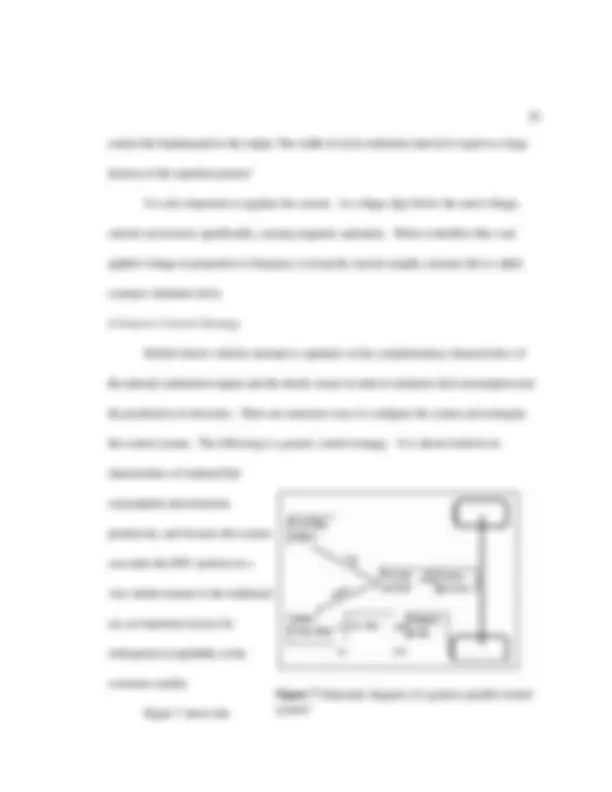
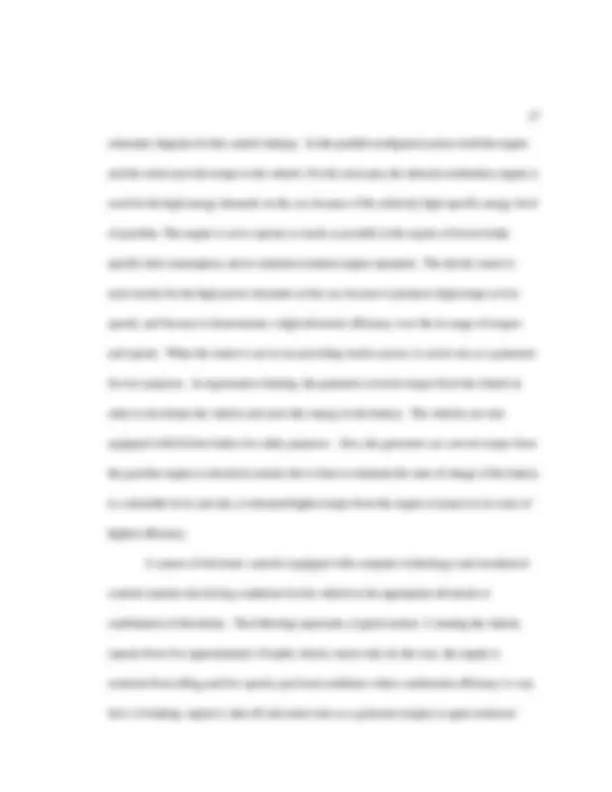
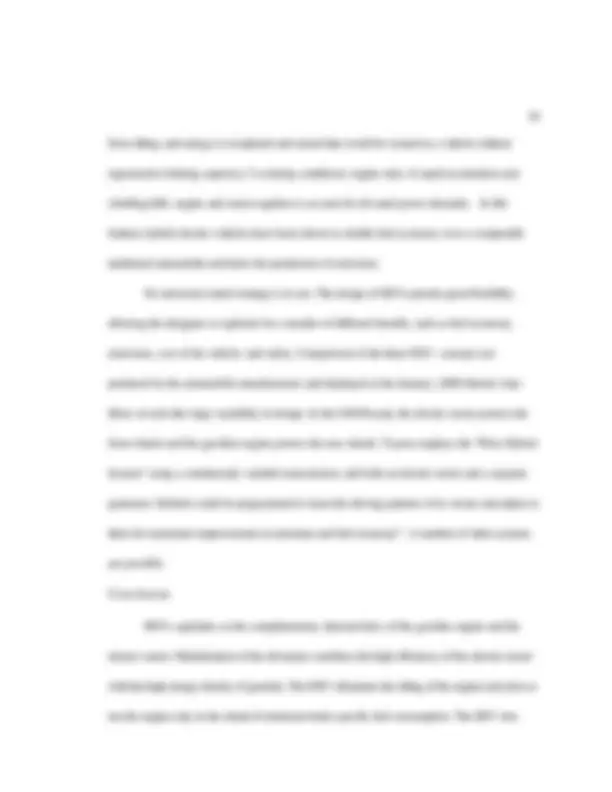
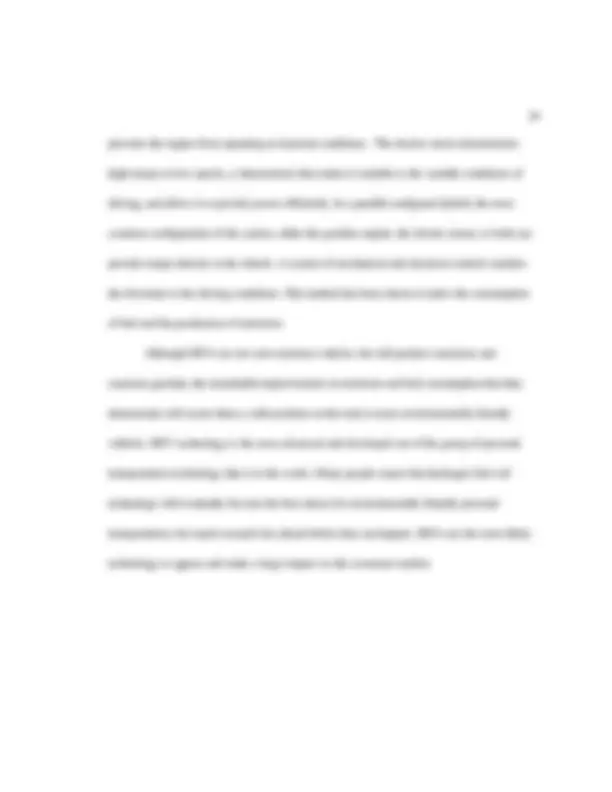
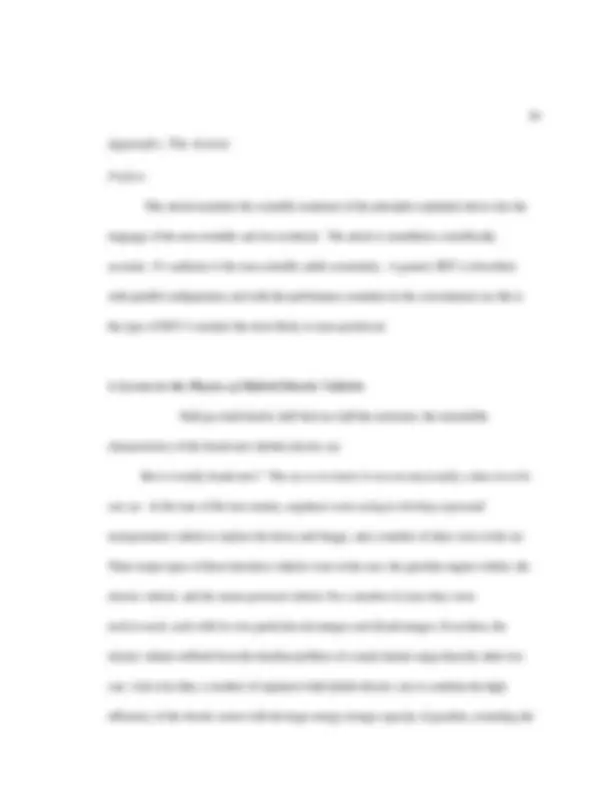
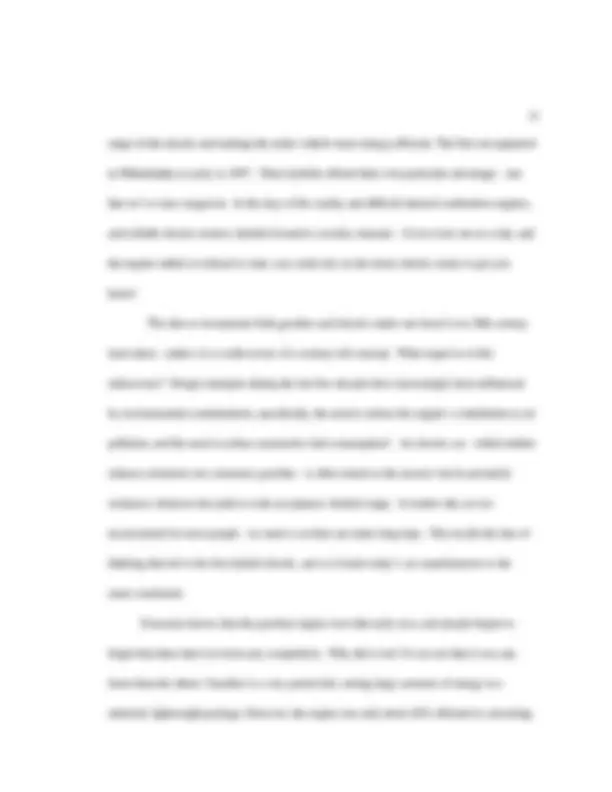
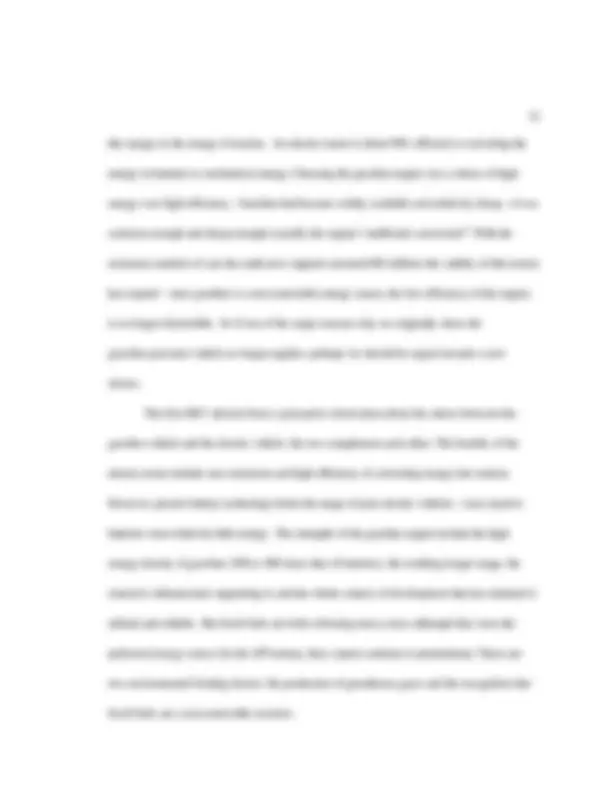
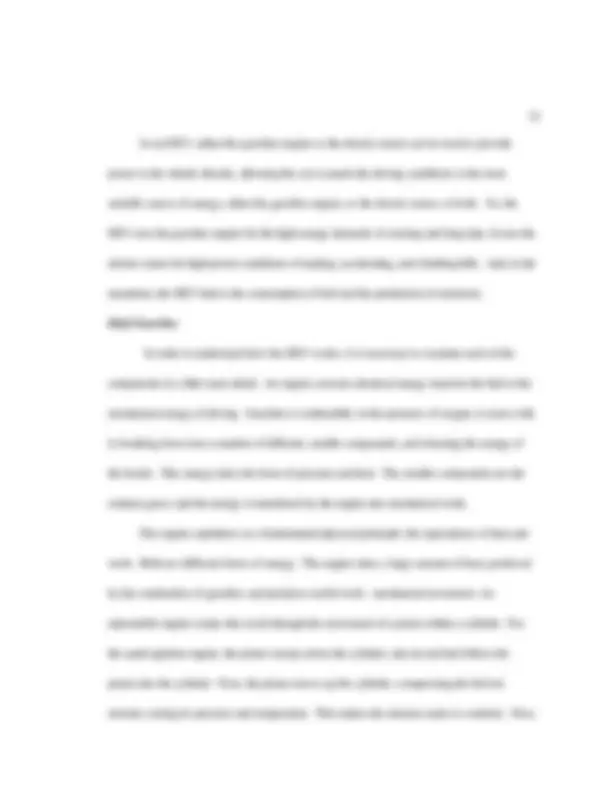
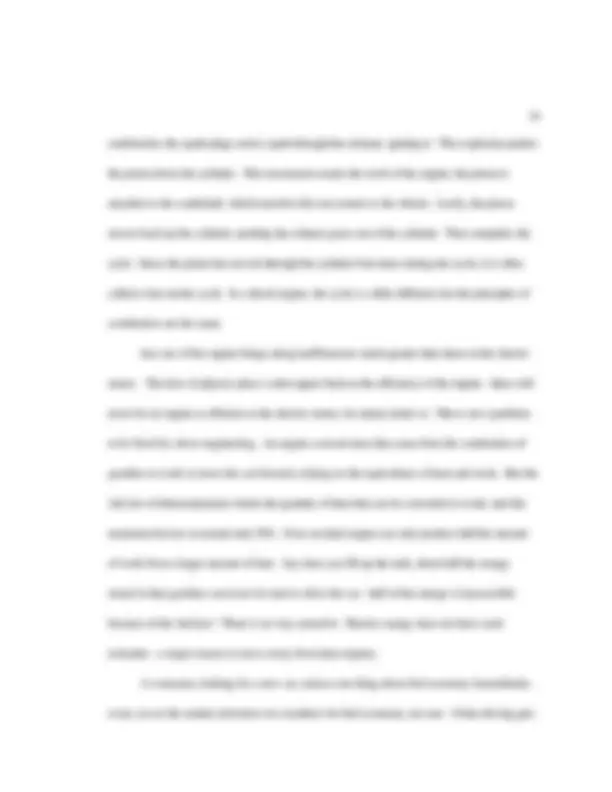
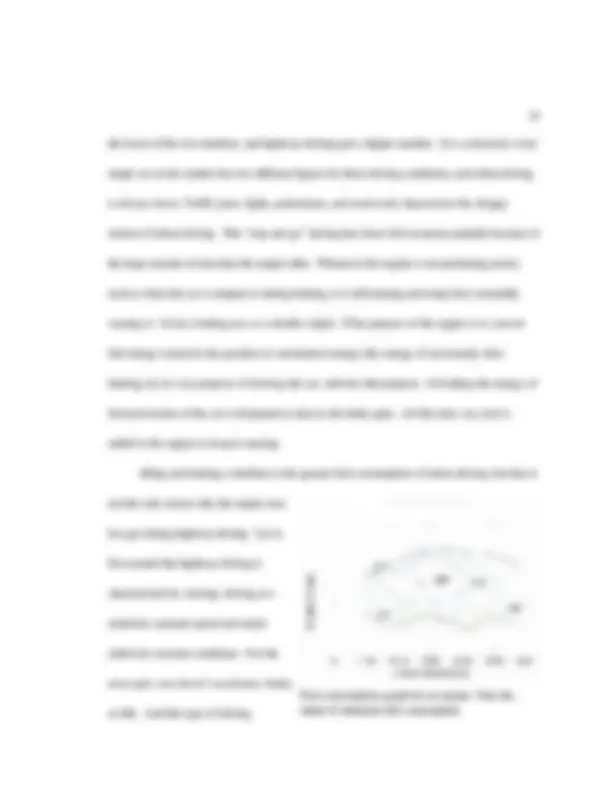
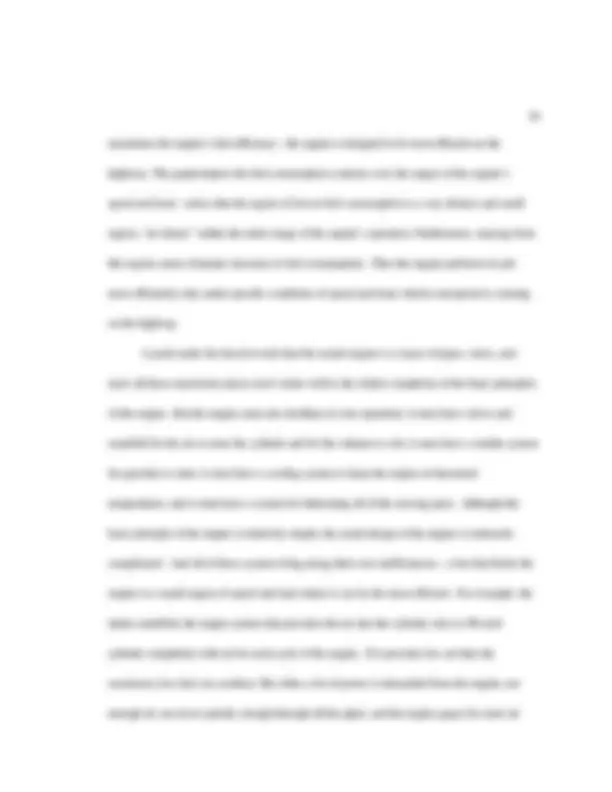
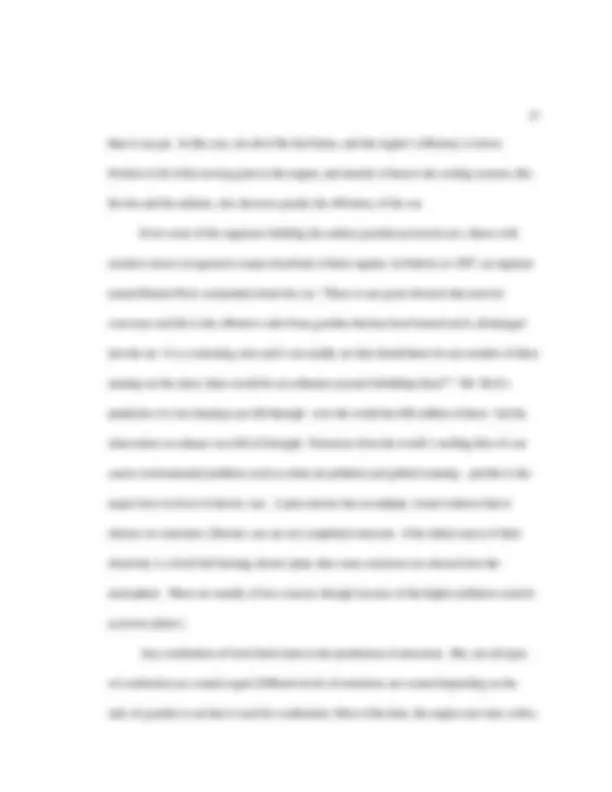
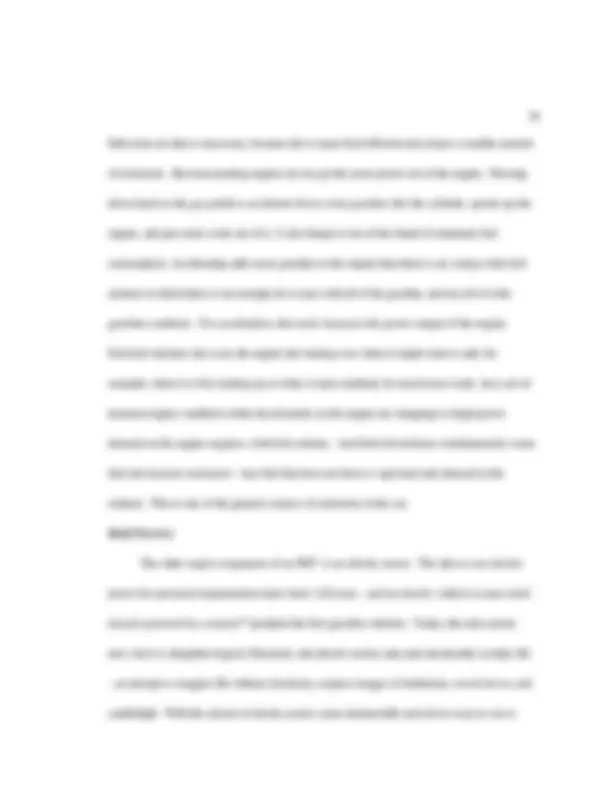
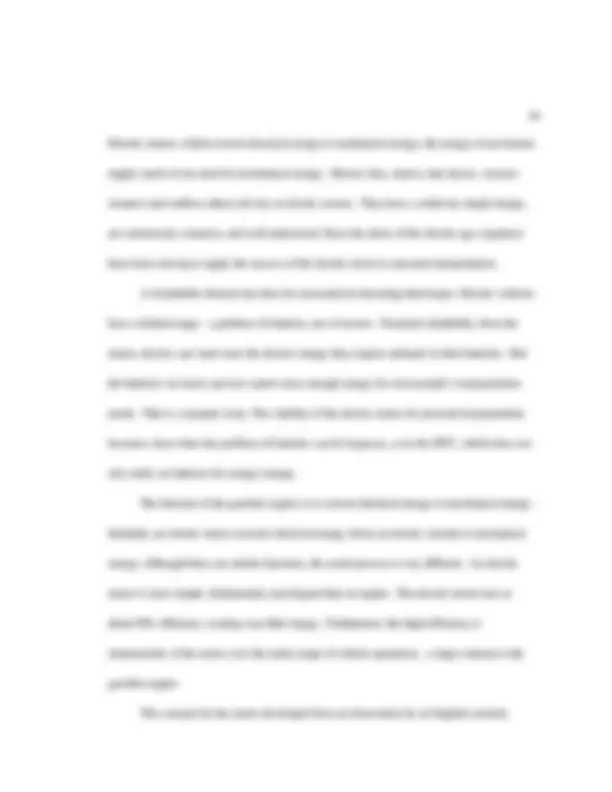
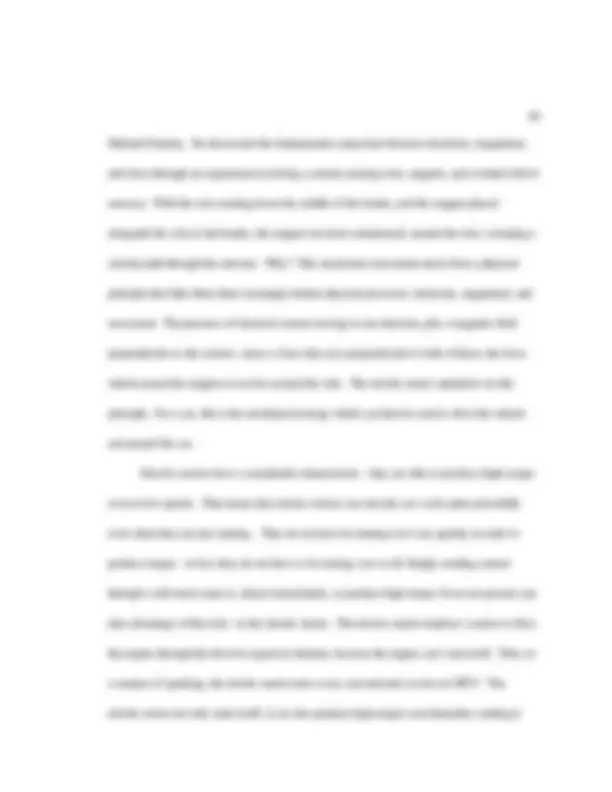
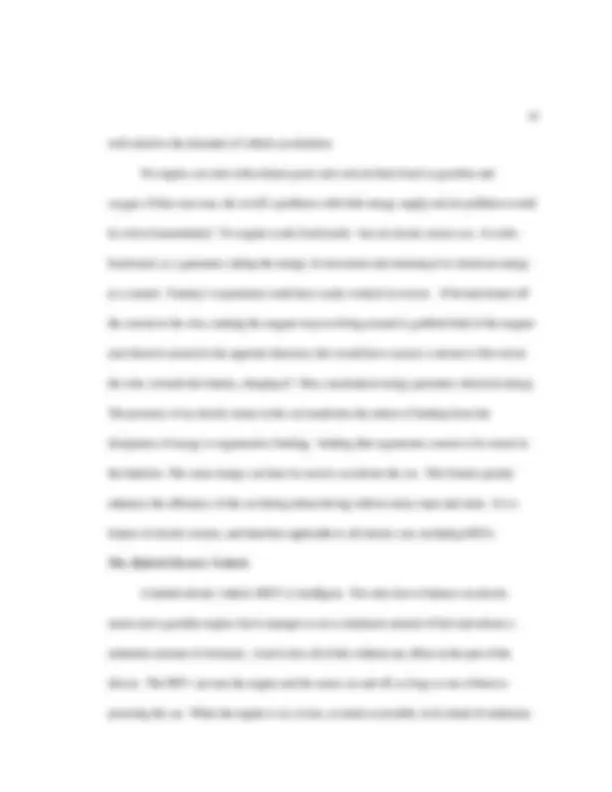
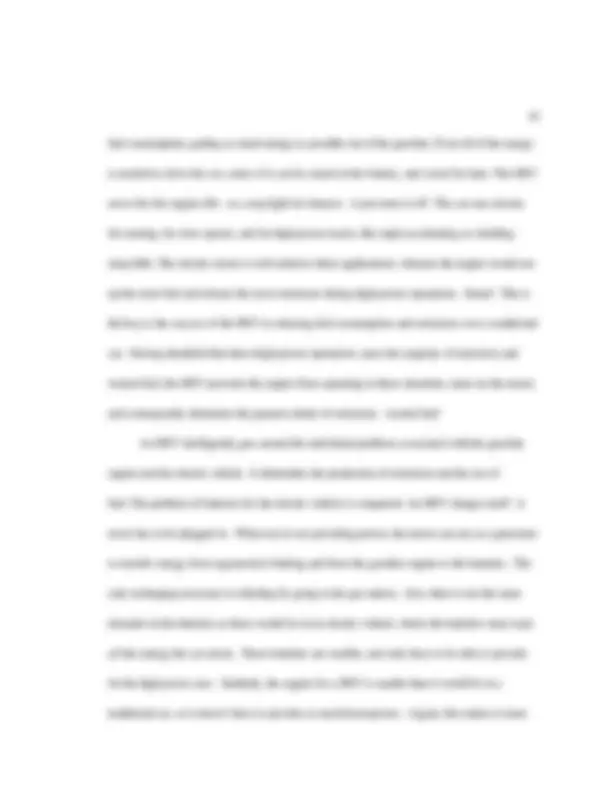
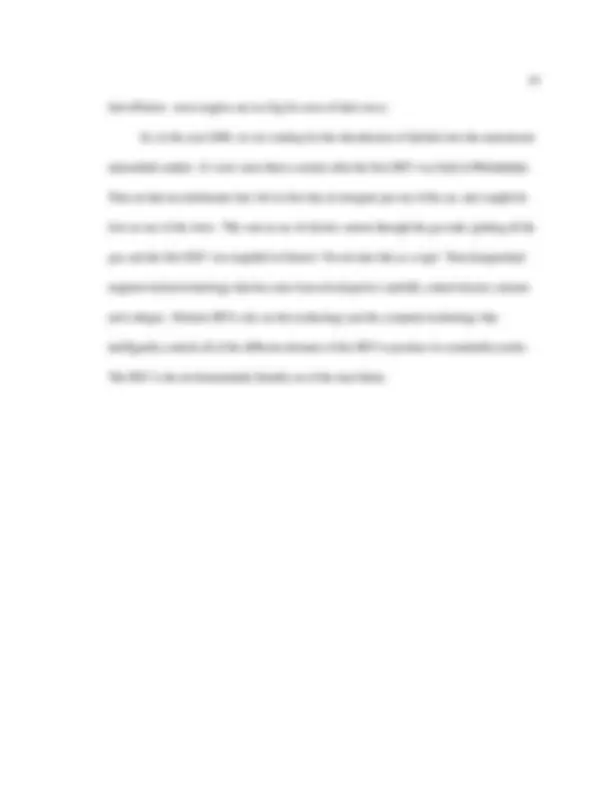
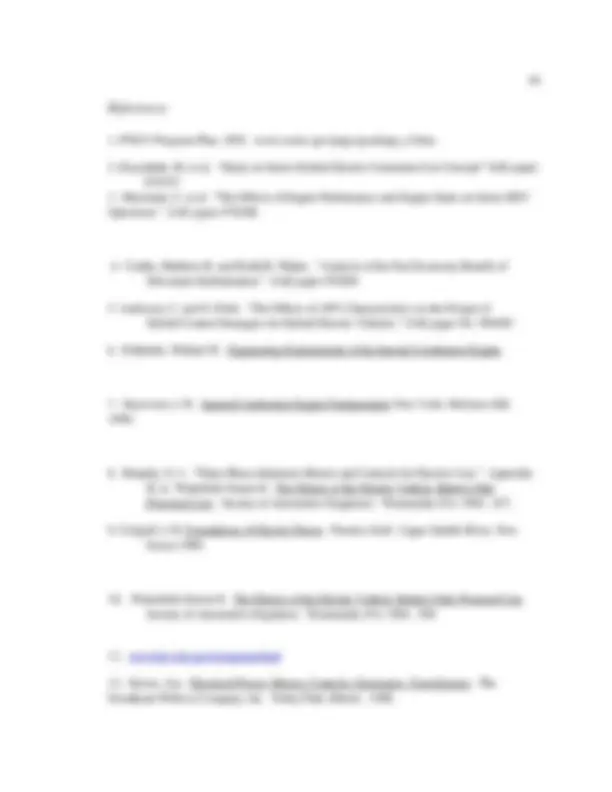
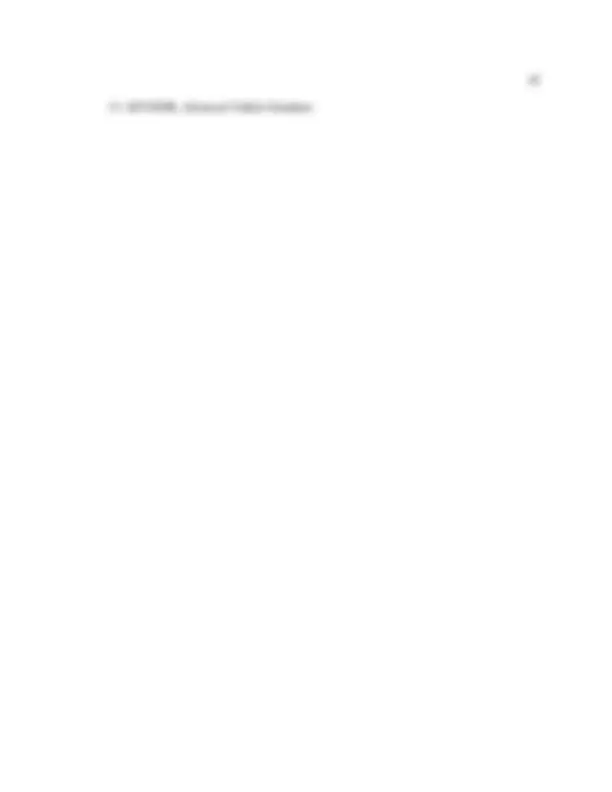
Study with the several resources on Docsity
Earn points by helping other students or get them with a premium plan
Prepare for your exams
Study with the several resources on Docsity
Earn points to download
Earn points by helping other students or get them with a premium plan
Community
Ask the community for help and clear up your study doubts
Discover the best universities in your country according to Docsity users
Free resources
Download our free guides on studying techniques, anxiety management strategies, and thesis advice from Docsity tutors
Material Type: Paper; Class: Physics Research; Subject: Physics; University: William and Mary; Term: Spring 2000;
Typology: Papers
1 / 46
This page cannot be seen from the preview
Don't miss anything!
Karen I. Burke Physics 451- 27 April 2000
these features to minimize transient engine operation, to take advantage of the electric motor’s suitability to acceleration. Many different configurations of the system are possible.
Hybridization of the automotive drivetrain attempts to combine the low emissions of electric automobiles with the extended range of gasoline engines. A hybrid electric vehicle (HEV) increases the fuel economy and decreases the emissions of the system when compared to a vehicle functioning only on a gasoline engine. The greatest benefit of the gasoline engine is the high energy density^2 of gasoline, on the order of 12,000 Wh/kg, in contrast with the much lower energy density of batteries, on the order of 500 Wh/kg. This allows the much greater range of vehicles run on gasoline engines. The benefits of electric motors include high torque at low speeds, the absence of on-board emissions, and regenerative braking. Traditionally, there are two ways to configure the system, series or parallel.
In a series configuration, the gasoline engine is connected via a generator to the electric motor, and only the electric motor provides power to the wheels. Torque produced by the gasoline engine generates electric energy in the generator, which is stored in the battery for use by the motor. In this system, the gasoline engine often runs continually in its zone of highest efficiency or lowest emissions, eliminating transient operation of the engine. Numerous types of control strategies are being employed with series configuration. The gasoline engine can be controlled to optimize either fuel consumption or emissions production.
Design of the generator-motor system takes into consideration whether or not the car will be “charge-dependent” or “self-sustaining.”^2 A charge-dependent car relies on external electric input whereas a self-sustaining car does not. The charge-dependent car, thus very similar to a pure electric vehicle, releases fewer emissions; but the self-sustaining car demonstrates a longer running range. Of the two, the self-sustaining car requires a generator of a larger capacity and the charge-dependent car requires a battery of a larger capacity. There are a number of other factors to be taken into consideration in the design and control of series hybrid electric vehicles. The engine does not have to run consistently throughout a driving cycle; thus, the number of times that an engine is started over the cycle is an important variable in influencing the production of emissions.^3 Another factor is the relation of the battery’s state-of-charge and the traction motor output to the input from the gasoline engine. In a “thermostat” strategy, the gasoline engine runs at a single power level; it is started when the battery’s state-of-charge reaches a designated minimum and stops when the state-of- charge has reached an upper set point.^4 In a “power-follower” strategy, the gasoline engine follows the immediate demands of the motor output, and the battery’s state-of-charge remains constant^5. Because this strategy matches the engine’s torque to the motor torque second-by- second, bypassing the need to store the torque in the batteries, battery losses are reduced, increasing fuel economy.^4
In a parallel configuration, either the gasoline engine or the electric motor, or both can supply torque directly to the wheels. As a general principle, the electric motor is used for
produce large variations in emissions production and fuel economy.^4 The parallel configuration is being most commonly chosen by automobile manufacturers. The operation of parallel hybrids more closely resembles the operation of traditional cars than does the operation of series hybrids, thus rendering them more appealing to the consumer. Also, the parallel hybrid has been shown to be 4% more fuel efficient than the series hybrid, primarily because the gasoline engine supplies power directly to the wheels, converting from mechanical power to electrical power and back again, as occurs in the series hybrid.^4
The design and success of the hybrid electric vehicle depends on certain characteristics of the internal combustion engine. The internal combustion engine demonstrates highest fuel efficiency and lowest emissions when it is run at cruising conditions in a small domain of its torque-speed curve. Also, the engine’s fuel efficiency is limited to a theoretical maximum of around 60% by the 2nd^ law of thermodynamics. This analysis is made for the four-stroke (Otto cycle) spark-ignition engine, the most commonly used for automobiles today. Some hybrid electric vehicles will use diesel engines, and these have not been treated extensively in this paper. Like spark-ignition engines, diesel engines also operate most efficiently in a small region of their torque and speed curves - the characteristic of engines that most justifies the hybridization of the drivetrain. Most of the analysis applies equally; however, diesel engines have a slightly different thermodynamic cycle.
Basic operating principles The purpose of internal combustion engines is the production of mechanical power from the chemical energy contained in the fuel. Each cylinder of the engine contains a piston; it is the movement of the piston in response to the combustion of the engine that produces work. During one cycle, the piston moves through the cylinder four times, each of which is called a stroke. In the first stroke, the intake stroke, the piston travels down the cylinder creating a vacuum, which pulls air into the cylinder, and fuel is added to the air. In the second stroke, the compression stroke, the piston travels up the cylinder to its highest point, top dead center, compressing the fuel-air mixture. Then combustion occurs; a spark ignites the gases, and changes the composition of the mixture, raising the pressure and the temperature to their highest values. In the third stroke, the expansion, or power stroke, the high pressure of the gases pushes the piston down to its lowest point in the cylinder, bottom dead center. This produces the work output of the cycle. Then, during exhaust blowdown, the exhaust valve is opened. The pressure within the cylinder is higher than atmospheric pressure, so the exhaust gases leave the cylinder. In the fourth stroke, the exhaust stroke, the cylinder starts full of exhaust gases at atmospheric pressure. The piston moves from bottom dead center to top dead center, pushing those gases out of the exhaust valve. The work output of the cycle is created by the movement of the piston at high pressure over the displacement volume.
As the volume under the integral is always the displacement volume and the pressure
equation becomes the following:
The equation that follows is an equivalent way of writing the thermal efficiency equation for the Otto cycle engine:
where is the compression ratio and is the adiabatic compressibility of air. With typical values of 10 for the compression ratio, and 1.4 for adiabatic compressibility, the theoretical thermal efficiency is .60. Actual performance of the internal combustion engine is even lower than this theoretical efficiency because of heat losses, friction, air flow, and air-fuel equivalence ratio. An important quantity is the brake specific fuel consumption, defined as follows:
where is the rate of fuel flow into the engine and is the brake power, the power applied to the crankshaft.
The performance map of a typical internal combustion engine, a graph which plots the brake specific fuel consumption over the load and speed ranges of the engine, shows distinctly a region of minimum brake specific fuel consumption, as seen in Fig. 1. This region typically lands at a point at mid-load and mid-speed, in the middle of the engine’s speed range and towards the top of its load range.
Figure 1 Graph of brake specific fuel consumption showing the “island” of minimum consumption^13
These map characteristics can be understood in terms of variations in volumetric efficiency, fuel conversion efficiency, and mechanical efficiency as the equivalence ratio and the importance of heat losses and friction change. Starting at the minimum bsfc point, increasing speed at constant load increases bsfc due primarily to the increasing friction mep at higher speeds, which decreases mechanical efficiency. While gross indicated fuel conversion efficiency increases as speed increases, friction increases dominate. Decreasing speed at constant load increases bsfc due primarily to the increasing importance of heat transfer per cycle (which decreases gross indicated fuel conversion efficiency). Friction decreases, increasing mechanical efficiency, but this is secondary. Any mixture enrichment required to maintain a sufficiently repeatable combustion process at low engine speeds contributes too. Increasing load at constant speed from the minimum bsfc island increases bsfc due to the mixture enrichment required to increase torque as the engine becomes increasingly air-flow limited. Decreasing load at constant speed increases bsfc due to the increased magnitude of friction (due to increased pumping work), the increased relative importance of friction, and increasing importance of heat transfer.^5
Power requirements of the accessories similarly increase with increasing engine speed. The engine fan, the engine generator, and the power-steering pump are major components. The fan requirements are the largest and with a direct drive increase with the cube of the speed. Mechanical efficiency, by definition, is also significantly affected by the load requirements, independent of speed. At idling, zero load, mechanical efficiency is zero, and increases with increasing load, from 0 to about 90%. Friction work also includes pumping friction, the negative work of the intake and exhaust strokes. Pumping friction comprises throttling friction and valve pumping friction, both of which increase with increasing speed at constant load.
The combustion efficiency is the fraction of the energy of the fuel supplied which is released in the combustion process.
where is the net chemical energy release. Combustion efficiency depends primarily on the air-fuel equivalence ratio, , which is the stoichiometric air-fuel ratio divided by the actual air-fuel ratio. For lean mixtures, when is less than unity, is approximately 98%. For rich mixtures, decreases approximately as. As the equivalence ratio is decreased below unity, i.e. the fuel-air mixture is made progressively leaner than stoichiometric, the efficiency increases slightly. As the equivalence ratio increases above unity, i.e. the mixture is made progressively richer than stoichiometric, the efficiency decreases because of lack of sufficient air for complete oxidation of the fuel.
The equivalence ratio is varied to adjust to the operating conditions of the vehicle. Maximum power and load demands an increase in above stoichiometric conditions. Maximum mean effective pressure occurs when is between 1 and 1.1, slightly rich of stoichiometric. At wide-open throttle, maximum power occurs when is near 1.1. Mixture requirements are different for full-load (wide-open throttle) and for part-load operation. For full-load operation, complete utilization of the inducted air to obtain maximum power for a given displaced volume is the critical issue. The engine runs on a rich mixture. When less than the maximum power at a given speed is required, efficient utilization of the fuel is the critical issue, and the engine runs lean. Mixture requirements are usually discussed in relation to steady and transient engine operation. Steady operation includes operation at a given speed and load over several engine cycles with a warmed-up engine. Transient operation includes engine starting, engine warm-up to steady state temperatures, and changing rapidly from one engine load and speed to another. Whenever the engine operates at transient conditions, valves are adjusted to provide a rich equivalence ratio. Therefore, operating the engine under any transient conditions necessarily reduces its fuel economy by lowering its combustion efficiency.
Volumetric efficiency is an overall measure of the effectiveness of a four-stroke cycle engine and its intake and exhaust systems as an air-pumping device. It is defined as follows
where is the mass of the air inducted into the cylinder, is atmospheric pressure, and
Heat Transfer The internal combustion engine operates at extremely high temperatures in the cylinder. High engine temperatures are necessary to produce high work output. Heat transfer occurs between the working fluid, the walls of the intake system, combustion chamber, and exhaust system, and to the coolant. Three modes of heat transfer play a role in the engine: conduction, convection, and radiation, although radiation is negligible. The magnitude of heat transfer affects the engine’s specific power and efficiency. As you increase heat transfer per a unit of fuel, the gas temperatures and pressure in the cylinder decrease, decreasing the work output, and the fuel efficiency decreases. At lower engine speeds, a longer amount of time elapses per cycle, allowing greater heat transfer. The relative importance of heat transfer is greatest at low speeds and loads. If the engine remains at a certain speed, as you lower the load, you decrease the maximum temperatures in the cylinder, decreasing the work load. The rate of heat transfer also decreases, but, the relative importance of the heat transfer to the work load increases. Heat transfer depends on a number of variables, including engine size, equivalence ratio, speed, load, brake mean effective pressure, spark timing, compression ratio, and materials. Of these, speed and load have the greatest effect. The peak heat flux in an SI engine
leaned out or enriched from this value. However, as a fraction of the fuel’s chemical energy,
mixtures. Emissions
Figure 2 Emissions in the engine as a function of equivalence ratio^6
The combustion of fuel in the engine necessarily produces emissions. The most harmful by-products of the combustion process are hydrocarbons, carbon monoxide, oxides of nitrogen, sulfur, and solid carbon particulates. The major causes of emissions are non- stoichiometric combustion, dissociation of nitrogen, and impurities in the fuel and air.^6 Hybrid electric vehicles reduce emissions by reducing both the amount of fuel used and by reducing the amount of time that the engine burns fuel via non-stoichiometric combustion. The production of emissions is also a strong function of the operating conditions of the engine; and hybrid electric vehicles permit less variation in the operating conditions of the engine while often optimizing those conditions for the minimization of the release of emissions. The production of both hydrocarbon emissions and carbon monoxide emissions depends greatly on the equivalence ratio, , as shown in Figure 2. Fuel-rich air-fuel ratio does not have enough oxygen to react with all the carbon and hydrogen, and emissions increase above stoichiometric values. The engine runs on a rich air-fuel ratio during engine startup, to ensure that the engine starts, and during rapid acceleration under load, to demand the highest power out of the engine. The production of nitrogen oxides is a function of temperature in the cylinder, and peaks when the equivalence ratio is slightly lean of stoichiometric.
Electric motors operate on three fundamental laws of electromagnetism: Ampere’s circuit law, Ampere’s force law, and Faraday’s law. Ampere’s circuit law relates a current to the magnetic field it creates,
where H is the magnetic field, dl is an element of length, and I is the current passing through the bounded area. It is integrated over the path. The magnetic field circles around the current. Ampere’s force law states,
where f is the vector force per unit length on the wire, I is the current in the wire, and B is the vector flux density due to I. Faraday’s law describes the emf produced by changing flux. It is as follows:
where v is the total induced voltage in the coil, n is the number of turns in the coil, is the time-varying magnetic flux. All electric motors are made of a stator, which does not rotate, and a rotor, which can rotate, and an air gap between them to permit motion. They are composed of two circuits, the field circuit, whose current produces the magnetic flux in the motor, and the armature circuit, that carries the current from the battery. Depending on the type of motor, the field circuit can be on either the rotor or the stator, and the armature is always on the opposite. Power is created in the motor by the interaction of the magnetic flux and the current; the basic equation
Figure 3 Schematic diagram of a basic synchronous motor^9
for power in all motors is as follows:
where is the torque, and is the rotational speed in radians/second. Steady energy transformation, both from electrical energy to mechanical energy and from mechanical energy to electrical energy, requires both torque and rotation.
In three-phase synchronous motors, the dc field current is placed on the rotor, which is a dc electromagnet, and the armature circuit is placed on the stator and carries three-phase currents. The flux on the rotor is controlled by the dc field current. The stator is composed of distributed coils placed in slots on its inner surface. Torque is generated through a displacement in the rotor and stator poles. The stator flux rotates due to the three-phase currents and torque is developed when the electromagnet on the rotor is rotating at the same speed.^8 That speed, called the synchronous speed, depends on the number of stator poles, P , and the electrical frequency, , as is determined from the following relationship: spatial radians/second The rotor and stator fluxes always rotate in synchronism. The two fluxes are separated by a physical angle, the rotor-stator power angle,. Developed torque depends on the flux magnitudes, the angle between the