
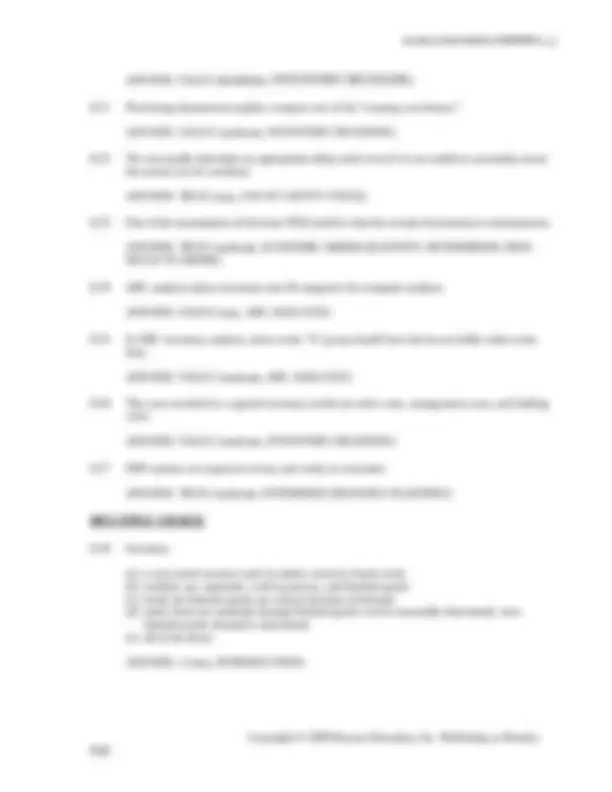
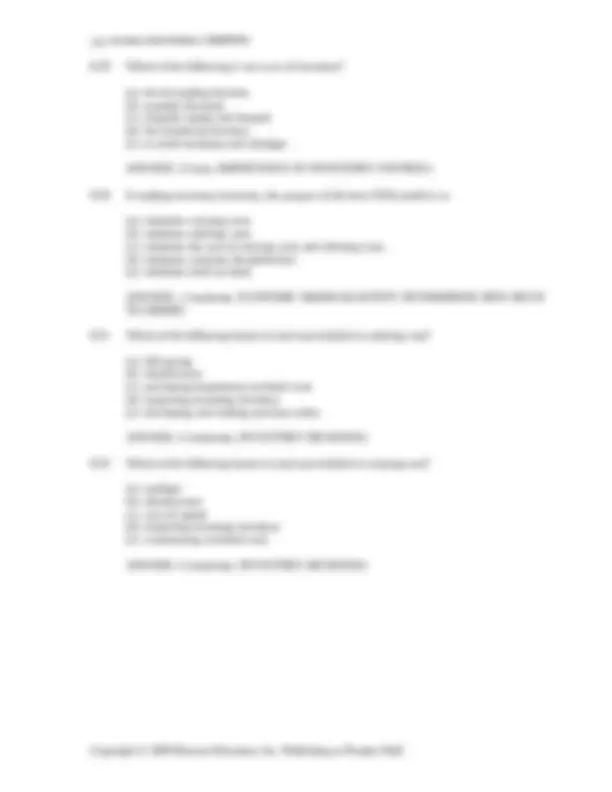
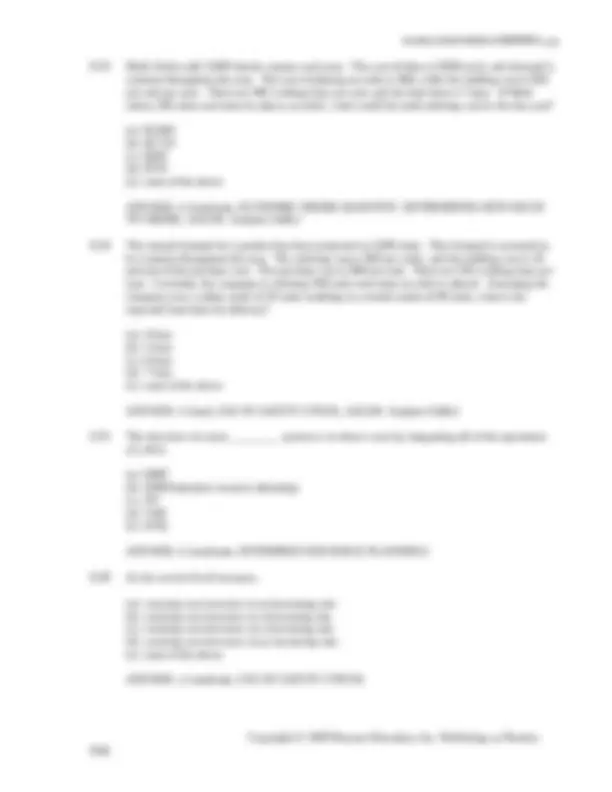
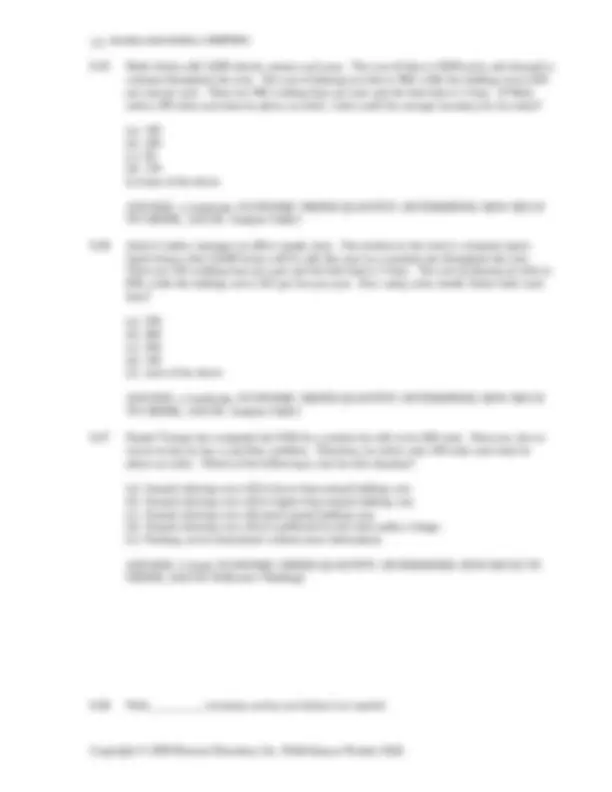
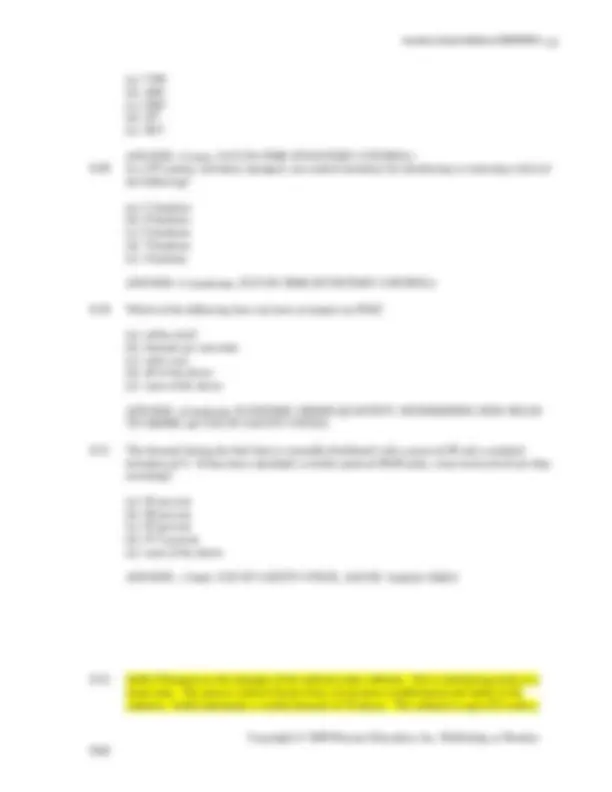
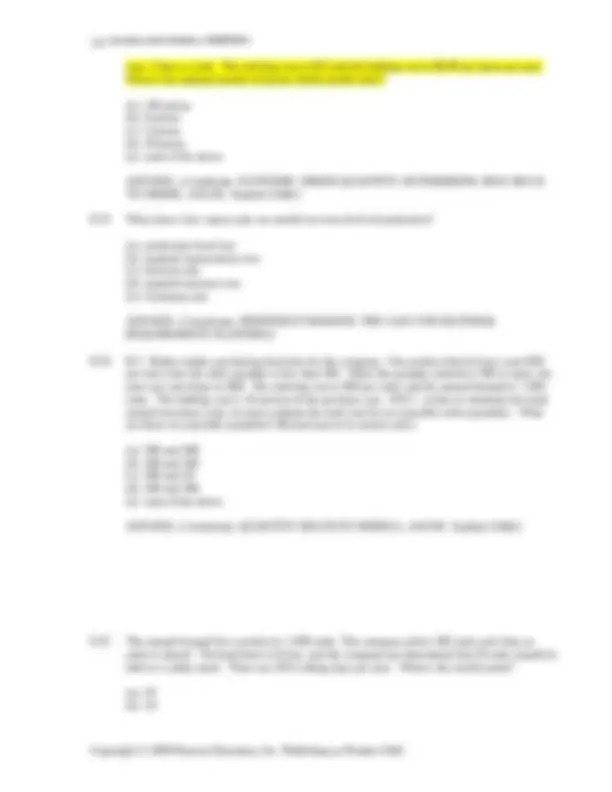
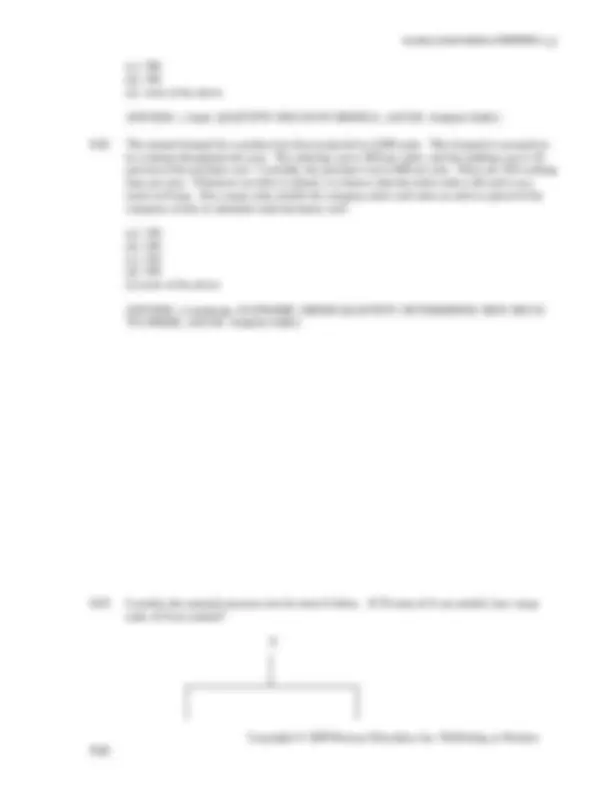
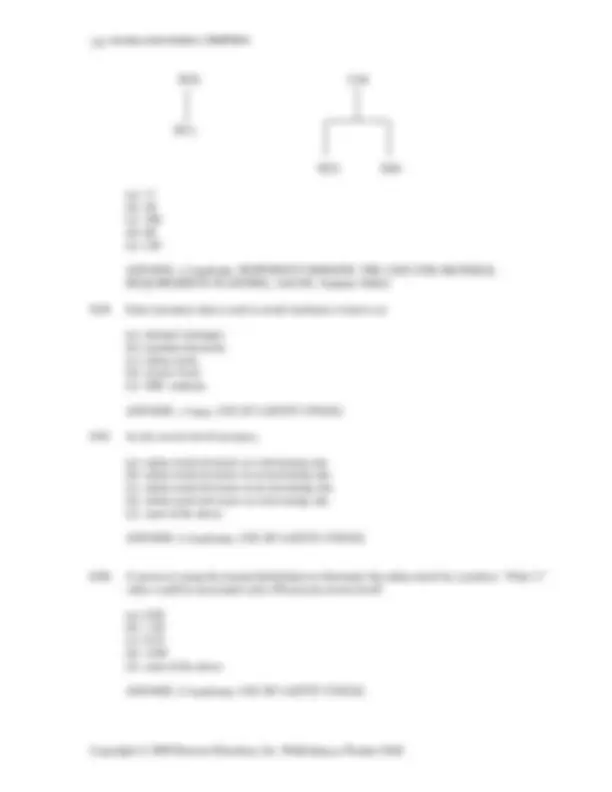
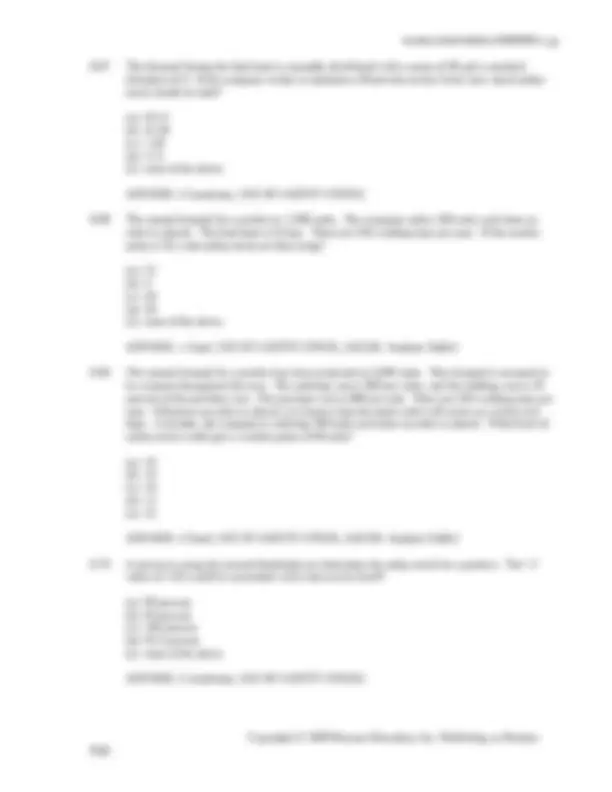

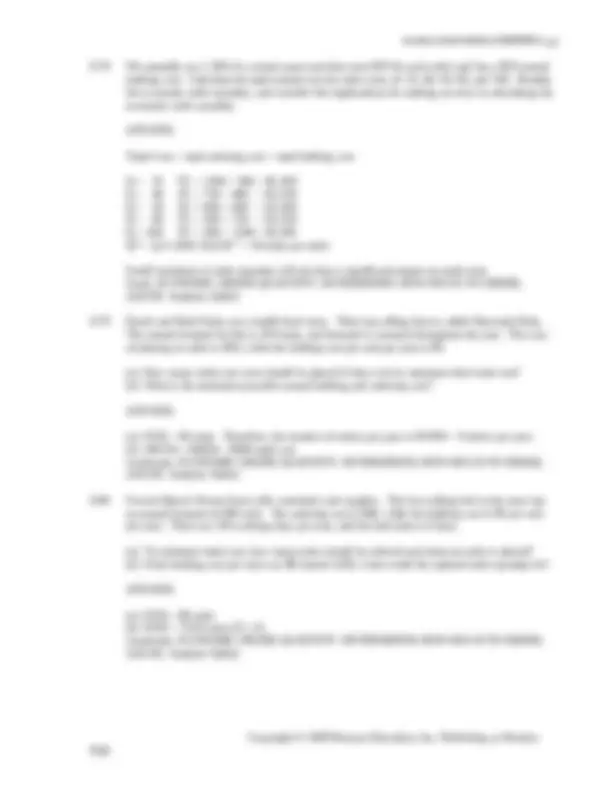
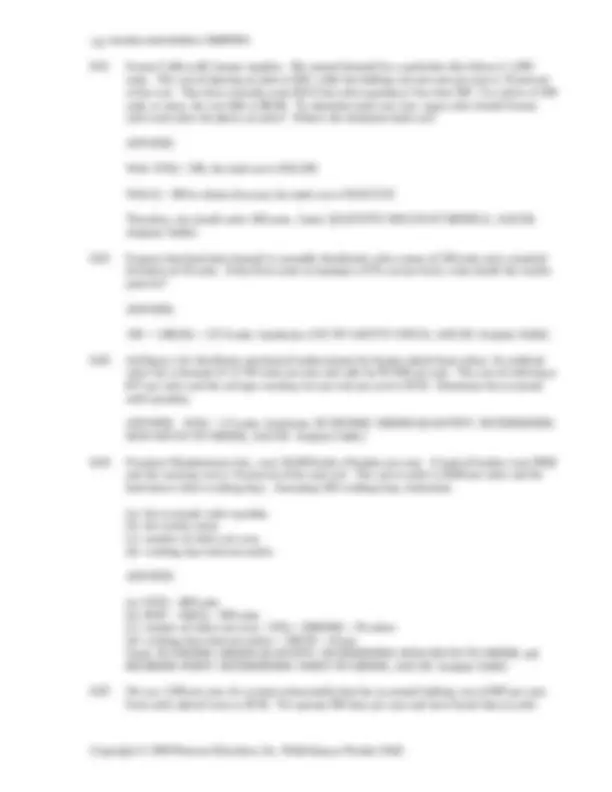
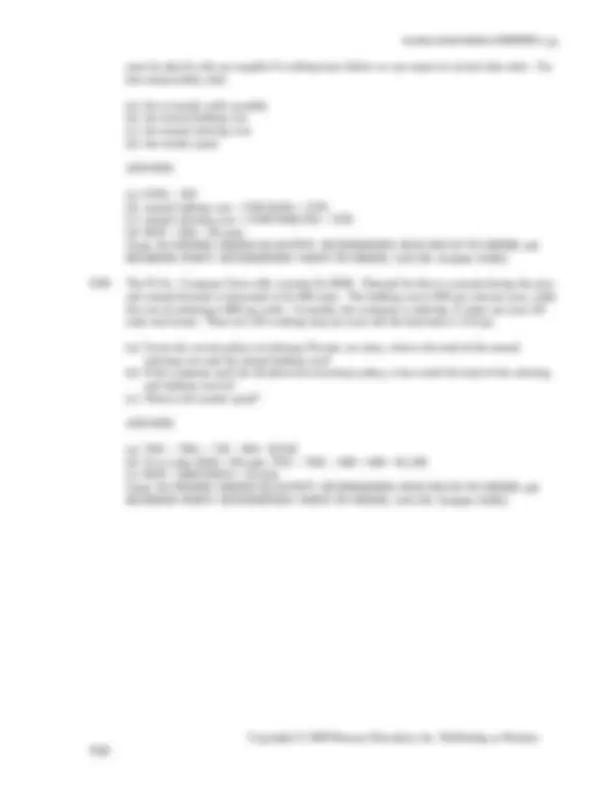
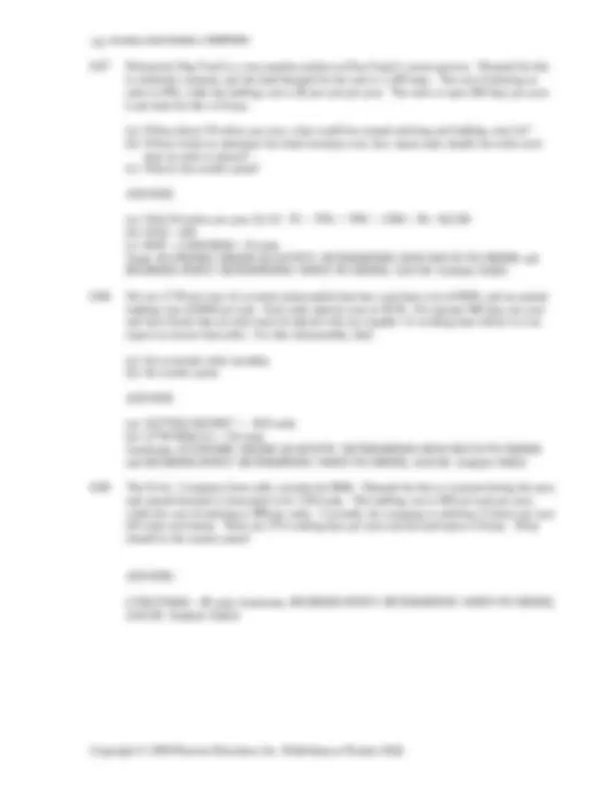
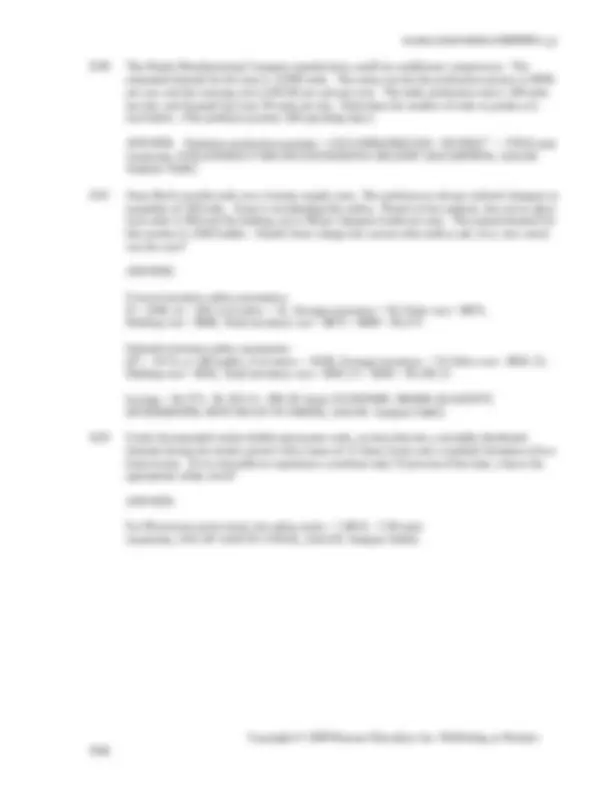
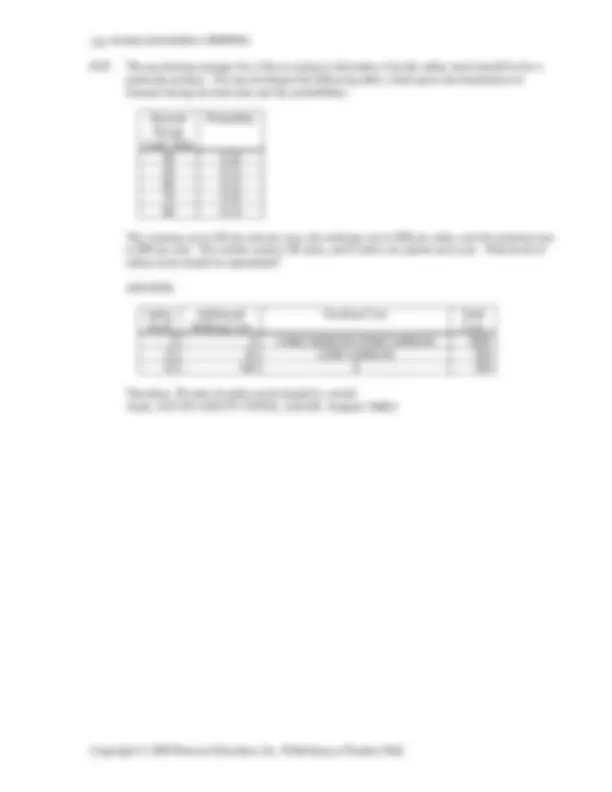
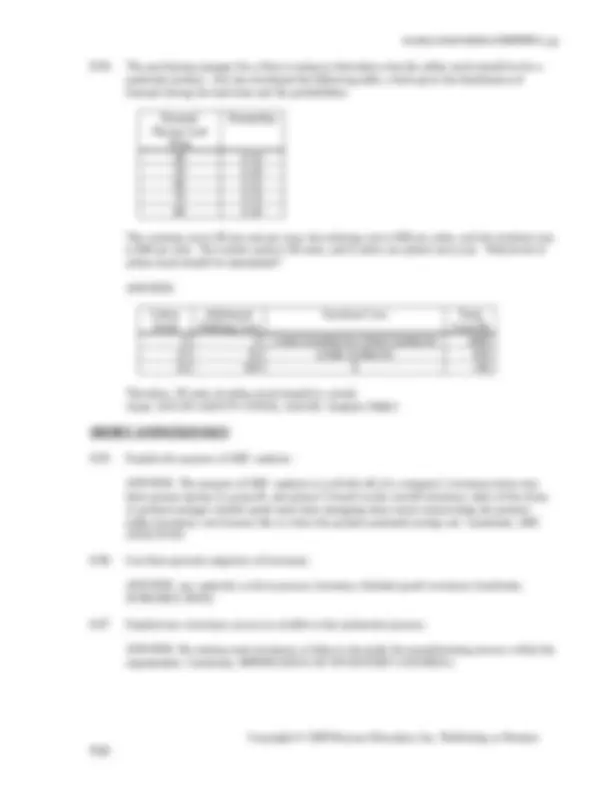
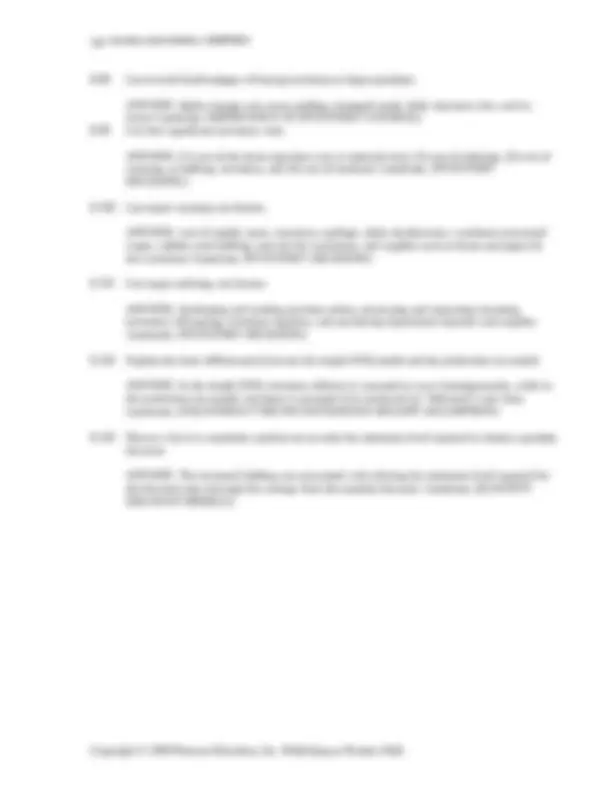
Study with the several resources on Docsity
Earn points by helping other students or get them with a premium plan
Prepare for your exams
Study with the several resources on Docsity
Earn points to download
Earn points by helping other students or get them with a premium plan
Community
Ask the community for help and clear up your study doubts
Discover the best universities in your country according to Docsity users
Free resources
Download our free guides on studying techniques, anxiety management strategies, and thesis advice from Docsity tutors
Material Type: Exam; Class: Accounting for Managers and Investors; Subject: Accounting; University: Florida International University; Term: Spring 2008;
Typology: Exams
1 / 26
This page cannot be seen from the preview
Don't miss anything!
6.1 Inventory is such an expensive asset that it may account for as much as 50 percent of a firm's invested capital. ANSWER: TRUE {moderate, INTRODUCTION} 6.2 The same ratio of marginal loss to the sum of marginal loss and marginal profit is used to solve one-period inventory models for both discrete and continuous probability distributions. ANSWER: TRUE {hard, SINGLE-PERIOD INVENTORY MODELS} 6.3 In the decoupling function, some inventory may be stored between each production process to act as a buffer. ANSWER: TRUE {moderate, IMPORTANCE OF INVENTORY CONTROL} 6.4 Service level is the chance, measured in percent, that there will be a stockout. ANSWER: FALSE {moderate, USE OF SAFETY STOCK} 6.5 A stockout is a situation that occurs when there is no inventory on hand. ANSWER: TRUE {easy, INTRODUCTION} 6.6 The concept of inventory is applicable to both manufacturing and service organizations. ANSWER: TRUE {easy, INTRODUCTION} 6.7 One reason inventory is required is the uneven flow of resources through a company. ANSWER: TRUE {moderate, IMPORTANCE OF INVENTORY CONTROL} 6.8 Inventory is any stored resource that is used to satisfy a current or future need. ANSWER: TRUE {easy, INTRODUCTION} 6.9 Economic order quantity (EOQ) analysis has recently become practical as a consequence of high- speed computers. ANSWER: FALSE {moderate, ECONOMIC ORDER QUANTITY: DETERMINING HOW MUCH TO ORDER} 6.10 Inventory is the common thread that ties all the functions and departments of the organization together. {moderate, INTRODUCTION} ANSWER: FALSE Copyright © 2009 Pearson Education, Inc. Publishing as Prentice Hall. 115
6.11 The purpose of the EOQ model is to achieve a balance between the cost of holding inventory and the cost of stockouts. ANSWER: FALSE {easy, ECONOMIC ORDER QUANTITY: DETERMINING HOW MUCH TO ORDER} 6.12 Under the assumptions made to develop the EOQ model, average inventory is one half of the maximum inventory. ANSWER: TRUE {moderate, ECONOMIC ORDER QUANTITY: DETERMINING HOW MUCH TO ORDER} 6.13 The EOQ model is relatively insensitive to minor violations of the basic assumptions. ANSWER: TRUE {moderate, ECONOMIC ORDER QUANTITY: DETERMINING HOW MUCH TO ORDER} 6.14 The production run model is useful when a firm purchases inventory that is delivered over a period of time. ANSWER: TRUE {moderate, EOQ WITHOUT THE INSTANTANEOUS RECEIPT ASSUMPTION} 6.15 The two fundamental decisions that you have to make when controlling inventory are: (1) how much to order, and (2) how much money to spend. ANSWER: FALSE {moderate, INVENTORY DECISIONS} 6.16 The economic order quantity helps one estimate the optimal number of units to purchase with each order. ANSWER: TRUE {easy, ECONOMIC ORDER QUANTITY: DETERMINING HOW MUCH TO ORDER} 6.17 The reorder point occurs during a stockout. ANSWER: FALSE {moderate, REORDER POINT: DETERMINING WHEN TO ORDER} 6.18 Safety stock is ignored when computing the reorder point. ANSWER: FALSE {moderate, USE OF SAFETY STOCK} 6.19 In a quantity discount model, the purchase cost or material cost must be included in the total cost calculation. ANSWER: TRUE {moderate, QUANTITY DISCOUNT MODELS} 6.20 Theft is one of the “ordering cost factors.” Copyright © 2009 Pearson Education, Inc. Publishing as Prentice Hall. 116
6.29 Which of the following is not a use of inventory? (a) the decoupling function (b) quantity discounts (c) irregular supply and demand (d) the translucent function (e) to avoid stockouts and shortages ANSWER: d {easy, IMPORTANCE OF INVENTORY CONTROL} 6.30 In making inventory decisions, the purpose of the basic EOQ model is to (a) minimize carrying costs. (b) minimize ordering costs. (c) minimize the sum of carrying costs and ordering costs. (d) minimize customer dissatisfaction. (e) minimize stock on hand. ANSWER: c {moderate, ECONOMIC ORDER QUANTITY: DETERMINING HOW MUCH TO ORDER} 6.31 Which of the following factors is (are) not included in ordering cost? (a) bill paying (b) obsolescence (c) purchasing department overhead costs (d) inspecting incoming inventory (e) developing and sending purchase orders ANSWER: b {moderate, INVENTORY DECISIONS} 6.32 Which of the following factors is (are) not included in carrying cost? (a) spoilage (b) obsolescence (c) cost of capital (d) inspecting incoming inventory (e) warehousing overhead costs ANSWER: d {moderate, INVENTORY DECISIONS} Copyright © 2009 Pearson Education, Inc. Publishing as Prentice Hall. 118
6.33 Mark Achin sells 3,600 electric motors each year. The cost of these is $200 each, and demand is constant throughout the year. The cost of placing an order is $40, while the holding cost is $ per unit per year. There are 360 working days per year and the lead-time is 5 days. If Mark orders 200 units each time he places an order, what would his total ordering cost be for the year? (a) $2, (b) $2, (c) $ (d) $ (e) none of the above ANSWER: d {moderate, ECONOMIC ORDER QUANTITY: DETERMINING HOW MUCH TO ORDER, AACSB: Analytic Skills} 6.34 The annual demand for a product has been projected at 2,000 units. This demand is assumed to be constant throughout the year. The ordering cost is $20 per order, and the holding cost is 20 percent of the purchase cost. The purchase cost is $40 per unit. There are 250 working days per year. Currently, the company is ordering 500 units each time an order is placed. Assuming the company uses a safety stock of 20 units resulting in a reorder point of 60 units, what is the expected lead-time for delivery? (a) 4 days (b) 5 days (c) 6 days (d) 7 days (e) none of the above ANSWER: b {hard, USE OF SAFETY STOCK, AACSB: Analytic Skills} 6.35 The objective of a (an) _________ system is to reduce costs by integrating all of the operations of a firm. (a) MRP (b) ERP(Enterprise resource planning) (c) JIT (d) VMI (e) EOQ ANSWER: b {moderate, ENTERPRISE RESOURCE PLANNING} 6.36 As the service level increases, (a) carrying cost increases at an increasing rate. (b) carrying cost increases at a decreasing rate. (c) carrying cost decreases at a decreasing rate. (d) carrying cost decreases at an increasing rate. (e) none of the above ANSWER: a {moderate, USE OF SAFETY STOCK} Copyright © 2009 Pearson Education, Inc. Publishing as Prentice Hall. 119
6.41 Which of the following is not a potential drawback of an ERP system? (a) Training employees on the use of the new software can be expensive. (b) The software is costly to customize. (c) The software is expensive to buy. (d) The implementation may require a company to change its normal operations. (e) It does not incorporate inventory control decisions. ANSWER: e {easy, ENTERPRISE RESOURCE PLANNING} 6.42 Sensitivity analysis of EOQ refers to (a) the attitude of top management toward the use of the EOQ model. (b) analysis of how much the EOQ will change if different input values are used. (c) an assessment of the impact of obsolescence upon the EOQ. (d) a study of the impact of storing incompatible products in the same warehouse. (e) analysis of the impact of stock shortages on customers or on production. ANSWER: b {moderate, ECONOMIC ORDER QUANTITY: DETERMINING HOW MUCH TO ORDER} 6.43 Which of the following is not a benefit of a well-developed ERP system? (a) It is relatively inexpensive to customize. (b) It can integrate all of the operations of a firm. (c) It can reduce transaction costs. (d) It can increase speed of information. (e) It can increase accuracy of information. ANSWER: a {moderate, ENTERPRISE RESOURCE PLANNING} 6.44 The annual demand for a product has been projected at 2,000 units. This demand is assumed to be constant throughout the year. The ordering cost is $20 per order, and the holding cost is 20 percent of the purchase cost. Currently, the purchase cost is $40 per unit. There are 250 working days per year. Whenever an order is placed, it is known that the entire order will arrive on a truck in 6 days. Currently, the company is ordering 500 units each time an order is placed. What is the total holding cost for the year using this policy? (a) $ (b) $2, (c) $4, (d) $8, (e) none of the above ANSWER: b {moderate, ECONOMIC ORDER QUANTITY: DETERMINING HOW MUCH TO ORDER, AACSB: Analytic Skills} Copyright © 2009 Pearson Education, Inc. Publishing as Prentice Hall. 121
6.45 Mark Achin sells 3,600 electric motors each year. The cost of these is $200 each, and demand is constant throughout the year. The cost of placing an order is $40, while the holding cost is $ per unit per year. There are 360 working days per year and the lead-time is 5 days. If Mark orders 200 units each time he places an order, what would his average inventory be (in units)? (a) 100 (b) 200 (c) 60 (d) 120 (e) none of the above ANSWER: a {moderate, ECONOMIC ORDER QUANTITY: DETERMINING HOW MUCH TO ORDER, AACSB: Analytic Skills} 6.46 Andre Candess manages an office supply store. One product in the store is computer paper. Andre knows that 10,000 boxes will be sold this year at a constant rate throughout the year. There are 250 working days per year and the lead-time is 3 days. The cost of placing an order is $30, while the holding cost is $15 per box per year. How many units should Andre order each time? (a) 200 (b) 400 (c) 500 (d) 100 (e) none of the above ANSWER: a {moderate, ECONOMIC ORDER QUANTITY: DETERMINING HOW MUCH TO ORDER, AACSB: Analytic Skills} 6.47 Daniel Trumpe has computed the EOQ for a product he sells to be 400 units. However, due to recent events he has a cash flow problem. Therefore, he orders only 100 units each time he places an order. Which of the following is true for this situation? (a) Annual ordering cost will be lower than annual holding cost. (b) Annual ordering cost will be higher than annual holding cost. (c) Annual ordering cost will equal annual holding cost. (d) Annual ordering cost will be unaffected by the order policy change. (e) Nothing can be determined without more information. ANSWER: b {hard, ECONOMIC ORDER QUANTITY: DETERMINING HOW MUCH TO ORDER, AACSB: Reflective Thinking} 6.48 With _________, inventory arrives just before it is needed. Copyright © 2009 Pearson Education, Inc. Publishing as Prentice Hall. 122
year, 5 days a week. The ordering cost is $15 and the holding cost is $0.40 per pizza per year. What is the optimal number of pizzas Judith should order? (a) 184 pizzas (b) 9 pizzas (c) 5 pizzas (d) 28 pizzas (e) none of the above ANSWER: a {moderate, ECONOMIC ORDER QUANTITY: DETERMINING HOW MUCH TO ORDER, AACSB: Analytic Skills} 6.53 What shows how many units are needed at every level of production? (a) production level tree (b) material requirements tree (c) decision tree (d) material structure tree (e) Christmas tree ANSWER: d {moderate, DEPENDENT DEMAND: THE CASE FOR MATERIAL REQUIREMENTS PLANNING} 6.54 R.C. Barker makes purchasing decisions for his company. One product that he buys costs $ per unit when the order quantity is less than 500. When the quantity ordered is 500 or more, the price per unit drops to $48. The ordering cost is $30 per order and the annual demand is 7, units. The holding cost is 10 percent of the purchase cost. If R.C. wishes to minimize his total annual inventory costs, he must evaluate the total cost for two possible order quantities. What are these two possible quantities? (Round answer to nearest unit.) (a) 300 and 306 (b) 300 and 500 (c) 306 and 50 (d) 200 and 306 (e) none of the above ANSWER: b {moderate, QUANTITY DISCOUNT MODELS, AACSB: Analytic Skills} 6.55 The annual demand for a product is 1,000 units. The company orders 200 units each time an order is placed. The lead-time is 6 days, and the company has determined that 20 units should be held as a safety stock. There are 250 working days per year. What is the reorder point? (a) 20 (b) 24 Copyright © 2009 Pearson Education, Inc. Publishing as Prentice Hall. 124
(c) 44 (d) 120 (e) none of the above ANSWER: c {moderate, USE OF SAFETY STOCK, AACSB: Analytic Skills} 6.56 The annual demand for a product has been projected at 2,000 units. This demand is assumed to be constant throughout the year. The ordering cost is $20 per order, and the holding cost is 20 percent of the purchase cost. Currently, the purchase cost is $40 per unit. There are 250 working days per year. Whenever an order is placed, it is known that the entire order will arrive on a truck in 6 days. Currently, the company is ordering 500 units each time an order is placed. What is the reorder point under the current policy? (a) 48 (b) 100 (c) 6 (d) 24 (e) none of the above ANSWER: a {moderate, REORDER POINT: DETERMING WHEN TO ORDER, AACSB: Analytic Skills} 6.57 Andre Candess manages an office supply store. One product in the store is computer paper. Andre knows that 10,000 boxes will be sold this year at a constant rate throughout the year. There are 250 working days per year and the lead-time is 3 days. The cost of placing an order is $30, while the holding cost is $15 per box per year. If Andre orders 500 boxes each time he orders from his supplier, what would his total annual inventory cost be (holding cost plus ordering cost)? (a) $3, (b) $4, (c) $3, (d) $3, (e) none of the above ANSWER: b {moderate, ECONOMIC ORDER QUANTITY: DETERMINING HOW MUCH TO ORDER, AACSB: Analytic Skills} 6.58 Rolf Steps is the production manager for a local manufacturing firm. This company produces staplers and other items. The holding cost is $2 per unit per year. The cost of setting up the production line for this is $25. There are 200 working days per year. The production rate for this product is 80 per day. If the production order quantity is 200 units, what was the daily demand (rounded to the nearest whole unit)? (a) 6 units Copyright © 2009 Pearson Education, Inc. Publishing as Prentice Hall. 125
(c) 500 (d) 200 (e) none of the above ANSWER: c {hard, QUANTITY DISCOUNT MODELS, AACSB: Analytic Skills} 6.62 The annual demand for a product has been projected at 2,000 units. This demand is assumed to be constant throughout the year. The ordering cost is $20 per order, and the holding cost is 20 percent of the purchase cost. Currently, the purchase cost is $40 per unit. There are 250 working days per year. Whenever an order is placed, it is known that the entire order will arrive on a truck in 6 days. How many units should the company order each time an order is placed if the company wishes to minimize total inventory cost? (a) 100 (b) 200 (c) 250 (d) 500 (e) none of the above ANSWER: a {moderate, ECONOMIC ORDER QUANTITY: DETERMINING HOW MUCH TO ORDER, AACSB: Analytic Skills} 6.63 Consider the material structure tree for item A below. If 20 units of A are needed, how many units of D are needed? A Copyright © 2009 Pearson Education, Inc. Publishing as Prentice Hall. 127
(a) 11 (b) 30 (c) 160 (d) 60 (e) 220 ANSWER: e {moderate, DEPENDENT DEMAND: THE CASE FOR MATERIAL REQUIREMENTS PLANNING, AACSB: Analytic Skills} 6.64 Extra inventory that is used to avoid stockouts is known as (a) planned shortages. (b) quantity discounts. (c) safety stock. (d) service level. (e) ABC analysis. ANSWER: c {easy, USE OF SAFETY STOCK} 6.65 As the service level increases, (a) safety stock increases at a decreasing rate. (b) safety stock increases at an increasing rate. (c) safety stock decreases at an increasing rate. (d) safety stock decreases at a decreasing rate. (e) none of the above ANSWER: b {moderate, USE OF SAFETY STOCK} 6.66 A person is using the normal distribution to determine the safety stock for a product. What "z" value would be associated with a 90 percent service level? (a) 0. (b) 1. (c) 0. (d) 0. (e) none of the above ANSWER: b {moderate, USE OF SAFETY STOCK} Copyright © 2009 Pearson Education, Inc. Publishing as Prentice Hall. 128
6.71 A person is using the normal distribution to determine the safety stock for a product. The "z" value of 2.33 would be associated with what service level? (a) 95 percent (b) 97.5 percent (c) 98 percent (d) 99 percent (e) none of the above ANSWER: d {moderate, USE OF SAFETY STOCK} Copyright © 2009 Pearson Education, Inc. Publishing as Prentice Hall. 130
6.72 Rolf Steps is the production manager for a local manufacturing firm. This company produces staplers and other items. The annual demand for a particular stapler is 1,600 units. The holding cost is $2 per unit per year. The cost of setting up the production line is $25. There are 200 working days per year. The production rate for this product is 80 per day. If Rolf decided to produce 200 units each time he started production of the stapler, what would his maximum inventory level be? (a) 200 (b) 180 (c) 100 (d) 90 (e) none of the above ANSWER: b {hard, EOQ WITHOUT THE INSTANTANEOUS RECEIPT ASSUMPTION, AACSB: Analytic Skills} 6.73 In the ABC analysis of inventory, the A group items (a) are critical to the functioning of the organization. (b) are the most expensive class of items. (c) typically account for over 70 percent of the company's business in dollars. (d) typically account for about 10 percent of a company's inventory items. (e) all of the above ANSWER: e {moderate, ABC ANALYSIS} 6.74 With an annual demand of 2,400 units, daily demand of 10 units, and daily production rate of 40 units, a company has determined that each production run will be for 200 units. If production starts when the inventory level is at zero, how many units would actually be in the warehouse at the end of the first day of production? (Round answer to nearest unit.) (a) 12 (b) 20 (c) 30 (d) 40 (e) none of the above ANSWER: c {moderate, EOQ WITHOUT THE INSTANTANEOUS RECEIPT ASSUMPTION, AACSB: Analytic Skills} Copyright © 2009 Pearson Education, Inc. Publishing as Prentice Hall. 131
6.78 We annually use 1,200 of a certain spare part that costs $25 for each order and has a $24 annual holding cost. Calculate the total annual cost for order sizes of: 25, 40, 50, 60, and 100. Identify the economic order quantity, and consider the implications for making an error in calculating the economic order quantity. ANSWER: Total Cost = total ordering cost + total holding cost Q = 25 TC = 1200 + 300 = $1, Q = 40 TC = 750 + 480 = $1, Q = 50 TC = 600 + 600 = $1, Q = 60 TC = 500 + 720 = $1, Q = 100 TC = 300 + 1200 = $1, Q* = [(2×1200×25)/24]1/2^ = 50 units per order Small variations in order quantity will not have a significant impact on total costs. {hard, ECONOMIC ORDER QUANTITY: DETERMINING HOW MUCH TO ORDER, AACSB: Analytic Skills} 6.79 David and Beth Sheba run a health food store. Their top selling item is called Heavenly Kelp. The annual demand for this is 810 units, and demand is constant throughout the year. The cost of placing an order is $20, while the holding cost per unit per year is $4. (a) How many orders per year should be placed if they wish to minimize their total cost? (b) What is the minimum possible annual holding and ordering cost? ANSWER: (a) EOQ = 90 units. Therefore, the number of orders per year is 810/90 = 9 orders per year. (b) (90/2)4 + 9($20) = $360 total cost {moderate, ECONOMIC ORDER QUANTITY: DETERMINING HOW MUCH TO ORDER, AACSB: Analytic Skills} 6.80 Everett Mann's Dream Store sells waterbeds and supplies. The best selling bed in the store has an annual demand of 400 units. The ordering cost is $40, while the holding cost is $5 per unit per year. There are 250 working days per year, and the lead-time is 6 days. (a) To minimize total cost, how many units should be ordered each time an order is placed? (b) If the holding cost per unit was $6 instead of $5, what would the optimal order quantity be? ANSWER: (a) EOQ = 80 units (b) EOQ = 73.03 units if Ch=6. {moderate, ECONOMIC ORDER QUANTITY: DETERMINING HOW MUCH TO ORDER, AACSB: Analytic Skills} Copyright © 2009 Pearson Education, Inc. Publishing as Prentice Hall. 133
6.81 Ivonne Callen sells beauty supplies. Her annual demand for a particular skin lotion is 1, units. The cost of placing an order is $20, while the holding cost per unit per year is 10 percent of the cost. This item currently costs $10 if the order quantity is less than 300. For orders of 300 units or more, the cost falls to $9.80. To minimize total cost, how many units should Ivonne order each time she places an order? What is the minimum total cost? ANSWER: With EOQ = 200, the total cost is $10,200. With Q = 300 to obtain discount, the total cost is $10,013.67. Therefore, she should order 300 units. {hard, QUANTITY DISCOUNT MODELS, AACSB: Analytic Skills} 6.82 Suppose that lead-time demand is normally distributed with a mean of 100 units and a standard deviation of 20 units. If the firm wants to maintain a 97% service level, what should the reorder point be? ANSWER: 100 + 1.88(20) = 137.6 units {moderate, USE OF SAFETY STOCK, AACSB: Analytic Skills} 6.83 ArtOrgan, Ltd. distributes mechanical replacements for human mitral heart valves. Its artificial valve has a demand of 12,765 units per year and sells for $7,900 per unit. The cost of ordering is $75 per order and the average carrying cost per unit per year is $150. Determine the economic order quantity. ANSWER: EOQ = 113 units {moderate, ECONOMIC ORDER QUANTITY: DETERMINING HOW MUCH TO ORDER, AACSB: Analytic Skills} 6.84 Furniture Manufacturers Inc., uses 20,000 loads of lumber per year. A load of lumber costs $ and the carrying cost is 10 percent of the unit cost. The cost to order is $200 per order and the lead-time is three working days. Assuming 200 working days, determine: (a) the economic order quantity (b) the reorder point (c) number of orders per year (d) working days between orders ANSWER: (a) EOQ = 400 units (b) ROP = 100(3) = 300 units (c) number of orders per year = D/Q = 2000/400 = 50 orders (d) working days between orders = 200/50 = 4 days {hard, ECONOMIC ORDER QUANTITY: DETERMINING HOW MUCH TO ORDER and REORDER POINT: DETERMINING WHEN TO ORDER, AACSB: Analytic Skills} 6.85 We use 1,500 per year of a certain subassembly that has an annual holding cost of $45 per unit. Each order placed costs us $150. We operate 300 days per year and have found that an order Copyright © 2009 Pearson Education, Inc. Publishing as Prentice Hall. 134